1700热连轧机毕业设计论文
毕业设计(论文)-热轧带钢车间的翻卷机设计[管理资料]
![毕业设计(论文)-热轧带钢车间的翻卷机设计[管理资料]](https://img.taocdn.com/s3/m/7f8817bac850ad02df80411c.png)
摘要本次设计的翻卷机是热轧带钢车间的设备之一,它虽然没有轧钢机那样的重要,但是也是必不可少的,其作用就是把由卷曲机完成的钢卷成品送到成品收集链上,大大的减少了人工劳力。
本设计选用了气压装置和缓冲装置作辅助动力的翻卷机,在翻卷机结构设计上由运输辊道作为辅助的结构形式。
整体具有结构简单,整体尺寸适中,维修方便,造价较低的优点。
在本设计中主要对翻卷机进行了结构设计和理论计算,并着重对传动机构做了详细的分析设计。
关键词:翻卷机、辊道、结构设计、理论计算AbstractThe machine is a device designed for hot rolled strip steel plant, although it is not important as rolling mill, but it is also essential . Its role is to transport the coil from the crimping machine to collection which greatly reduced the manual labor. I use a pneumatic and buffer device as a auxiliary power of rolled machine in this design. The transport roller are used as a secondary structure in rolled machine structural design. This machine has a simple structure ,moderate size ,low cost advantages and it is easilytofix up. Rolled machine structural design and calculation are mainly content in this design,this designe focus on the detailed analysis of transmission structural.Keywords: rolled machine, roller, structural design, calculation前言时光飞逝,转眼已是毕业设计时间,这是大学时光结束的标志,也是对大学四年最好的诠释。
武钢1700mm热连轧机降低轧辊消耗的实践

武钢1700mm 热连轧机降低轧辊消耗的实践唐本立,陈 刚(武钢热轧带钢厂湖北武汉430083)摘 要:轧辊消耗指标是热连轧机主要技术经济指标之一,对比分析找出武钢1700mm 热连轧机轧辊消耗高的原因,通过开展有针对性的课题攻关,把研究成果运用到生产实践中,获得降低轧辊消耗的明显效果。
关键词:轧辊消耗;改造辊径;综合利用;控制剥落中图分类号:TG 333.17 文献标识码:B 文章编号:1008-4371(2004)01-0025-04Practice on R eduction of R oll Consumption of 1700mmContinuous H ot R olling Mill in WISCOT ANG Ben -li ,CHE N G ang(The H ot R olling S trip M ill of WISC O Wuhan Hubei 430083,China )Abstract :The roll consum ption is one of the critical im portant technical and economic indica 2tors for the continuous hot rolling mill in WISC O have been achieved in reduction of the roll con 2sum ption by way of scientific research in light of the technical problems and application of results of the scientific study in the production.K eyw ords :roll consum ption ;revam p of roll diameter ;com prehensive utilization ;control on peeling off收稿日期:2003-09-02作者简介:唐本立(1954- ),男,湖北仙桃市人,高级工程师. 轧辊消耗指标是热连轧机的主要技术经济指标之一。
热轧带钢技术论文(2)

热轧带钢技术论文(2)热轧带钢技术论文篇二热轧带钢轧后控制冷却技术的发展及比较摘要:本文对国内外热轧带钢轧后控制冷却技术从20世纪20年代到现在的发展做了介绍,同时对不同控制冷却方式进行了比较。
关键词:热轧带钢,控制冷却,喷水冷却,层流冷却,水幕冷却,超快速冷却UFC。
控制轧制和控制冷却技术已发展成为现代轧钢技术的一项重要工艺。
近年来,随着市场对热轧带钢的需求量增大,对钢材的质量要求也越来越高,不仅要求有很好的表面质量,对钢材的组织力学性能更是提出了更高的要求。
热轧带钢卷取温度的控制是整个热轧生产成品的最后一个环节,为了获得所需要的微观组织形态和力学性能,要求实现快速有效的轧后冷却,使得钢材冷却过程中的温度控制要求更严格。
轧后冷却是控制热轧带钢最终机械性能和板形质量的一个关键环节,这已成为全世界业内研究人员的共识。
控制冷却技术是从对控制冷却工艺及有关理论的系统研究、控制冷却系统、控制冷却装置三方面逐步发展起来的。
1.国内外轧后控制冷却的发展90年代,欧美各国也相继在现有设备改造、新技术的引进、全面生产跟踪、管理系统自动化等诸多方面做了大量的工作。
苏联伊里奇-日丹诺夫1700mm热带钢轧机层流冷却装置,采用了一种新型的“管套管”喷嘴,内管输送压缩空气,外管送水,形成细雾化的水汽混合物喷柱,实现了在线水-空冷却。
在供水量不变的条件下,解决了厚度5-10mm带钢冷却不足问题。
日本钢厂针对冷却设备存在的问题再次进行改造,使卷取温度的精度大幅度提高。
截止1994年,对于厚度2.4mm,卷取温度550℃的普碳钢,99%的热轧带钢卷取温度可控制在士20℃以内。
日本水岛厂热带钢轧机冷却设备进行了一系列改造,流量控制阀采用了响应时间仅为0.5秒,使用寿命超过75万次后仍不漏水的活塞阀,设计出I/D=28(过去为20)的新喷嘴,确定喷嘴最佳安装高度,从而提高了冷却能力,提高了冷却精度,尽管末架精轧机出口温度有波动,卷取温度仍控制在10℃目标范围内。
1700-热带刚的精轧设计论文

1 轧钢机选择1.1 轧钢机选择的原则1.2 轧钢机机架布置及数目的确定1.2.1 精轧前立轧机(FE)1.2.2 精轧机组(F1~F7)2 典型产品压下规程设计2.1 概述2.2 各道次出口厚度及压下量的确定2.2.1 粗轧机的压下量分配原则.2.2 精轧机的压下量分配原则2.2.3 综合分析2.3 轧机咬入的校核2.4 确定轧制速度制度2.4.1 粗轧机速度制度2.4.2 精轧机速度制度2.4.3 加减速度的选择2.5 确定轧制温度制度2.5.1 粗轧各道次温度确定2.5.2 精轧各道次温度确定2.6 力能参数的计算2.6.1 轧制力的计算和空载辊缝的设定2.6.2 轧制力矩的计算2.6.3 附加摩擦力矩的计算2.6.4 空转力矩的计算2.6.5 动力矩的计算2.7 层流冷却对温度的控制及大致的冷却速率的确定参考文献致谢板带钢是钢铁产品的主要品种之一,广泛应用于工业,农业,交通运输和建筑业。
宽带钢在我国国民经济中的发展中需求量很大。
世界各国近年来都在注重研制和使用连铸连轧等新技术和新设备来生产板带钢。
本设计是年产300万吨的热轧板带钢车间工艺设计。
产品规格为:(2.0~10.0)×(700~1600)mm。
所用钢种为:普碳钢、合金结构钢、不锈钢(约含25%)。
论文主要内容包括:轧制机的选择,典型产品工艺计算。
关键词:轧钢机,典型产品,轧制力,各道次温度,轧制速度,力矩计算。
1 轧钢机选择1.1 轧钢机选择的原则轧钢机是完成金属轧制变形的主要设备,是代表车间生产技术水平、区别于其它车间类型的关键。
因此,轧钢车间选择的是否合理对车间生产具有非常重要的作用。
轧钢机选择的主要依据是:车间生产的钢材的钢种,成品品种和规格,生产规模的大小以及由此而确定的产品生产工艺过程。
对轧钢车间工艺设计而言,轧钢机选择的内容是:确定轧机的结构型式,确定其主要参数,选用轧机机架数即布置形式。
在选择轧钢机时,一般要注意,考虑下列原则:(1)在满足产品方案的前提下,使轧机组成合理,布置紧凑;(2)有较高的生产率和设备利用系数;(3)保证获得良好的产品,并考虑到生产新产品的可能;(4)有利于轧机的机械化,自动化的实现,有助于工人的劳动条件改善;(5)轧机结构型式先进合理,制造容易,操作简单,维修方便;(6)备品备件更换容易,并利于实现备品备件的标准化;(7)有良好的综合经济技术指标。
本科毕业论文---年产500万吨热连轧带钢车间设计说明书

内蒙古科技大学本科生毕业设计说明书(毕业论文)题目:设计年产量500万吨热连轧带钢车间,计算产品SPHD,规格2.0×1800mm,占年产量15%学生姓名:学号:专业:材料成型及控制工程班级:11级成型3班指导教师:李慧琴教授年产500万吨热连轧带钢车间摘要本文以包钢稀土钢板材公司2250热连轧带钢车间为依据,在包头地区建立一个热连轧带钢车间,根据设计任务书要求,本车间设计年产量热轧钢卷500万t;钢种有普碳钢,优质钢和低合金钢;产品规格为1.2~25.4×830~2130mm。
设计内容主要包括:产品方案,工艺流程,设备选择及生产能力计算,车间平面布置,环境保护等。
本车间采用常规半连轧工艺。
板坯全部采用连铸坯。
为减少坯料规格,简化轧制程序,采用定宽压力机。
为提高产品质量,精轧机各架全采用CVC轧机。
采用CAD绘制车间平面布置图。
关键词:热轧带钢;半连续;轧制温度;轧制压力;轧制速度。
Annual output of 5 million tons of strip steel workshopAbstractIn Baotou rare earth steel company on the basis of 2250 continuous strip steel workshop in the Baotou region to establish a continuous strip steel workshop, according to the design specification requirements, this workshop design annual production of 5 million t hot rolled steel coils; Steel grade of carbon-steel, high-quality steel and low alloy steel; Product specification is 1.2 ~ 25.4 x 830 ~ 2130 mm.Design content mainly includes: product scheme, process flow, equipment selection, calculation of production capacity, the workshop layout, environmental protection, etc.This workshop USES conventional half and rolling process. The slab are all made of casting billet. To reduce billet specifications, simplify the process of rolling, adopt fixed width press. In order to improve the quality of our products and finishing mill adopts the frame of CVC mill.Using CAD drawing workshop layout.Key words:Hot rolled strip steel workshop design; Semi-continuous; Rolling temperature; The rolling pressure; The speed of rolling目录摘要 (I)Abstract (II)第一章国内外热轧带钢发展概况及在包头地区新建热轧带钢厂可行性与必要性分析 (1)1.1 国内外热连轧带钢的发展概况 (1)1.1.1热连轧技术 (1)1.1.2我国热连轧技术的发展 (1)1.1.3我国热连轧带钢生产现状 (2)1.2 在包头地区新建热连轧带钢厂的可行性和必要性 (3)1.2.1可行性分析 (3)1.2.2必要性分析 (6)2.3社会及经济效果评价 (6)2.4可行性研究结论与建议 (6)第二章产品方案及金属平衡表的编制 (8)2.1产品方案的主要内容 (8)2.2在编制产品方案时应该注意的问题 (8)2.3产品大纲 (9)2.4产品规格 (9)2.5金属平衡表的编制 (11)第三章生产车间工艺流程的确定 (13)3.1 生产工艺流程制定的依据 (13)3.2热连轧带钢生产工艺流程的制定 (14)3.3热连轧生产工艺流程简述 (14)3.3.1原料准备 (16)3.3.2板坯加热及设备组成 (17)3.3.3调宽 (19)3.3.4.粗轧机组 (19)3.3.5.精轧机组 (20)3.3.6工作辊窜辊系统简介 (21)3.3.7轧后冷却和卷取 (24)3.3.7钢板的标志与包装 (25)3.3.8钢板的质量检验 (25)3.4车间布置形式 (25)3.4.1轧机布置形式 (25)3.4.2轧制方法 (26)3.4.3轧钢机数目的确定 (27)3.5.3轧机主要技术参数的确定 (28)3.6轧机选择 (29)3.6.1粗轧机组: (29)3.6.2精轧机组: (30)第四章轧制规程设计 (32)4.1 Q195的产品技术要求 (32)4.2热连轧轧制规程简述 (33)4.3坯料尺寸选择 (33)4.4道次选择确定 (33)4.5粗轧机组压下量分配 (34)4.6精轧机组的压下量分配 (36)4.7校核咬入能力 (37)4.8确定各道的轧制速度 (37)4.9确定轧件在各道次中的轧制时间 (39)4.9.1粗轧 (39)4.9.2精轧 (41)4.10轧制温度的确定 (44)4.10.1粗轧 (44)4.10.2精轧 (45)第五章轧制进程图,生产能力的核算 (47)5.1 典型产品的工作图表 (47)5.2 产品小时产量计算 (48)5.3 平均小时产量计算 (48)5.4 年计划实际工作小时数 (49)5.5 年产量计算 (50)第六章力能参数计算 (51)6.1 轧制压力计算 (51)6.1.1 粗轧 (51)6.1.2精轧 (60)6.2电机能力校核 (62)6.2.1 R1电机能力校核 (64)6.2.2 R2电机能力校核 (64)6.2.3精轧机电机能力校核 (65)6.3轧辊强度校核 (65)6.3.1二辊粗轧机轧辊校核 (67)轧辊校核 (67)6.3.2四辊粗轧机的R26.3.3F1~F4精轧机强度校核 (68)6.3.4 F5~F7精轧机强度校核 (68)第七章辅助设备的选择 (70)7.1 加热设备 (70)7.1.1 入炉设备 (70)7.1.2 出炉设备 (71)7.2 加热炉选择 (72)7.2.1 炉型确定 (72)7.2.2 炉子尺寸的确定 (72)7.3 起重运输设备的选择 (73)7.3.1 起重机 (73)7.3.2 辊道的选用 (74)7.4 除鳞设备的选择 (76)7.5 保温装置的选择 (78)7.6 剪切设备的选择 (78)7.7 层流冷却设备的选择 (79)7.8 卷取设备的选择 (79)7.9 平整分卷机组 (80)7.9.1 钢卷准备区设备 (81)7.9.2 平整机前后设备 (81)第八章车间平面布置 (84)8.1 平面布置的原则 (84)8.2 金属流程线的确定 (84)8.3 设备间距的确定 (85)8.3.1 加热炉间距离 (85)8.3.2 加热炉到轧机的距离 (85)8.3.3 柱间距离的确定 (85)8.3.4 其它设备之间的距离 (85)8.4 仓库面积的确定 (86)8.4.1 原料仓库面积的计算 (86)8.4.2成品仓库面积的计算 (87)8.5 车间运输量的确定 (87)第九章劳动组织及车间经济技术指标 (89)9.1 车间技术经济指标 (89)9.1.1 金属消耗 (89)9.1.2 其它消耗 (89)9.2 综合技术经 (90)第十章环境保护与综合利用 (92)10.1 环保对车间设计的要求 (92)10.2 环保的内容与对策 (92)参考文献 (94)第一章国内外热轧带钢发展概况及在包头地区新建热轧带钢厂可行性与必要性分析1.1 国内外热连轧带钢的发展概况1.1.1热连轧技术在工业现代化进程中国,钢铁行业一直处于基础产业的地位,在国民经济中所起的作用很重要,是衡量一个国家的工业、农业、国防和科学技术的四个现代化水平的标志。
1700热连轧机毕业设计论文

1700热连轧机毕业设计论文1绪论1.1热连轧生产的国内外发展概况热轧宽带钢轧机的发展已有70多年的历史,第一套热连轧机于1926年诞生于美国。
汽车工业、建筑工业、交通运输业等的发展,使得热轧机冷轧薄钢板的需求量不断增长,从而促进热轧宽带钢轧机的建设获得了迅速和稳定的发展。
促进热轧宽带钢轧机及工艺技术发展的主要因素是:要求其生产能力不断提高,从而钢卷质量不断增大和轧制速度不断提高,同时提出扩大产品品种的要求;要求产品的尺寸精度和性能不断提高;受1973年中东石油危机的冲击而转向注意开发节约能源技术;进入20世纪80年代中期更加注重产品质量的提高,并对板形质量及带钢凸度和平直度提出更高的质量要求。
热轧宽带钢轧机的热轧板卷,不仅可以供薄板和中板直接使用,还可以作为下道工序冷轧、焊管、冷弯型钢的原料。
带钢热连轧机从50年代起,在世界范围内已成为带钢生产的主要形式。
目前世界上1000mm以上的热轧机和带卷轧机有200余套。
带钢热连轧机具有轧制速度高、产量高、自动化程度高的特点,轧制速度50年代为10~12 m/s,70年代已达18 ~ 30 m/s,产品规格也由生产厚度为2 ~8mm,宽度小于2000mm的成卷带钢扩大到生产厚度1.2 ~20mm,宽度2500mm的带钢。
带卷重量的加大和作业率的提高,使现有的带钢热连轧机年产量达350 ~600万t,最大卷重也由15t增加到70t。
坯料尺寸及重量加大,要求设置更多的工作机座,过去的粗轧机组和精轧机组的工作机座分别为2~4架和5~6架,现已分别增加到4 ~ 6架和7~8架,轧机尺寸也相应增加。
现代的带钢热连轧机除了采用厚度自动控制外,还实现了电子计算机控制,从而大大提高了自动化水平,改善了产品质量,带钢厚度公差不超过±0.5mm,宽度公差不超过0.5 ~1.0mm,并具有良好的板形。
90年代以来,钢铁生产短流程迅速开发和推广,薄板坯(或中厚板坯)连铸连轧工艺的出现,正在改变着传统的热连轧机市场。
1700热连轧机轧辊温度场及热凸度研究

收稿日期:2007204220基金项目:国家自然科学基金资助项目(50534020)・作者简介:郭忠峰(1978-),男,辽宁沈阳人,东北大学博士研究生;李长生(1964-),男,黑龙江七台河人,东北大学教授;刘相华(1953-),男,黑龙江双鸭山人,东北大学教授,博士生导师・第29卷第4期2008年4月东北大学学报(自然科学版)Journal of Northeastern University (Natural Science )Vol 129,No.4Apr.20081700热连轧机轧辊温度场及热凸度研究郭忠峰,徐建忠,李长生,刘相华(东北大学轧制技术及连轧自动化国家重点实验室,辽宁沈阳 110004)摘 要:研究了国内某1700热连轧机轧辊温度场有限差分模型及热凸度模型,采用C ++语言编制离线仿真程序,计算某一轧制周期工作辊温度场及热凸度,得到轧制过程不同时刻工作辊表面温度及热变形情况・F2,F3和F4轧辊上表面在轧制结束后最高温度分别为58.1,73.1和81.2℃;表面最大变形量(半径方向)分别为193.979,275.259和333.433μm ・对CVC 轧辊而言,轧辊表面温度分布及热变形变化明显受到轧辊横移的影响・将程序计算得到的轧辊表面温度与实测值比较,两者吻合较好,表明轧辊温度场模型及热凸度模型具有较高的计算精度・关 键 词:热连轧机;轧辊;轧制周期;温度场;热凸度中图分类号:TG 335.11 文献标识码:A 文章编号:100523026(2008)0420517204T emperature Field and Therm al Crow n of Work R olls on 1700H ot Strip MillGU O Zhong 2f eng ,X U Jian 2z hong ,L I Chang 2sheng ,L IU Xiang 2hua(The State K ey Laboratory of Rolling and Automation ,Northeastern University ,Shenyang 110004,China.Correspondent :GUO Zhong 2feng ,E 2mail :zf -guo @ )Abstract :The FDM (finite difference method )model of temperature field and thermal crown of work roll on 1700hot strip mill (HSM )was studied.The off 2line simulation program was compiled by C ++language and the temperature field and thermal crown were calculated according to the rolling schedule ,thus obtaining roll surface temperature and thermal deformation at different moments.The maximum surface temperatures of the work rolls F2,F3and F4are about 58.1,73.1and 81.2℃and relevant maximum radial deformations are about 193.979,275.259and 333.433μm respectively.The surface temperature distribution and thermal deformation were both affected obviously by roll shift.The computed and measured roll surface temperature were comparatively in good agreement with each other ,and the fact showed that the computed roll temperature field and thermal crown model are quite accurate.K ey w ords :HSM ;roll ;rolling schedule ;temperature field ;thermal crown在热轧带钢生产中,工作辊热凸度是影响带钢板形重要因素之一・为提高带钢质量,必须对工作辊热凸度进行准确计算及预报・轧辊温度场的计算是求解轧辊热凸度的前提,对于轧辊温度场的求解,主要有解析法[1]、有限元法[2-5]、有限条元法[6]及有限差分法[7-10]・解析法大都采用傅立叶变换和分离变量法对导热微分方程进行求解,需做大量假设,一般只能解决比较简单的传热问题;有限元和有限条元法计算量大,很难满足现场设备和实时预测控制的要求;有限差分法计算简便快捷,在满足工程要求的计算精度下,计算速度快,计算也较稳定・因此在工程上一般采用差分法求解工作辊温度场问题・本文研究了国内某1700热连轧机工作辊温度场及热凸度数学模型,综合考虑影响轧辊温度场的各种边界条件,采用等效法计算轧辊节点热量变化,进而确定轧辊温度场・编制了离线仿真程序,计算了某一轧制周期工作辊温度场及热凸度,得到了轧制过程不同时刻工作辊表面温度分布及热变形情况・1 轧辊温度场及热凸度模型1.1 轧辊温度场模型轧辊温度场是一个三维非稳态系统,随着轧制过程的进行,轧辊轴向、径向和周向的温度都要发生变化,考虑到轧辊的回转周期与热凸度对轧制条件变化的响应时间相比为二阶小,所以可忽略轧辊在圆周方向的温度变化,这样就将复杂的三维温度场问题简化为二维问题・同时为简化计算还忽略了轧辊与带钢之间摩擦热和带钢的变形热・对于横移式轧辊,因左右温度场不对称,为了研究整个轧辊温度场,采用简化二维模型对工作辊全长进行单元划分,如图1所示・忽略轧辊周向温度变化,辊身轴向及径向都均匀划分,辊身轴向划分20个单元,径向划分8层单元,左右两端辊颈沿轴向分别划分3个单元・在轧制过程中,工作辊表面圆周的不同部分处于不同的热交换状态,热带钢、冷却水、空气、轧辊轴承组成复合外部环境,为便于简化计算,可用一个等效环境去代替・图2为轧辊在轧制过程中边界条件示意图・图1 工作辊单元划分Fig.1 E lement division of work roll图2 工作辊边界条件Fig.2 Boundary conditions of work roll(a )—工作辊径向边界条件;(b )—工作辊轴向边界条件・假设轧辊表面节点的边界条件有n 种,在单位时间内每种边界条件下流入此节点所在单元体的热量可用式(1)表示:Q 1=h 1A T 1-h 1A T ,Q 2=h 2A T 2-h 2A T ,…Q n =h n A T n -h n A T ・(1)式中,Q i (i =1,2,…,n )为在第i 种边界条件作用下,表面节点i 所在单元体在单位时间内热量增量,J /s ;h i 为在第i 种边界条件作用下,表面节点i 所在单元体与外界条件等效热交换系数,J /(s ・mm 2・℃);A 为表面节点i 所在单元体与外界条件接触单元面积,mm 2;T i 为在第i 种边界条件外部介质温度,℃;T 为表面节点所在单元体温度,℃・815东北大学学报(自然科学版) 第29卷那么,在这种边界条件作用下,节点所在单元单位时间内所吸收的热量为Q=Q1+Q2+…+Q n・(2)将式(1)代入式(2),得Q=A・6n i=1h i t i-T6n i=1h i・(3)轧辊表面节点单元热量增量确定后,与相邻节点间的热量传递采用热传导处理,得到当前节点最后的热量增量h f・各节点单元在单位时间内的热量增量确定后,可根据下式计算节点网格的温度增量,进而得到轧辊温度场:t1=t c+t d,t d=h f×t s/c c・(4)式中,t1为节点最终温度,℃;t c为节点当前温度,℃;t d为节点温度变化量,℃;t s为时间步长, s;c c为节点热容,J/℃・1.2 轧辊热凸度模型由于轧辊内部存在不均匀温度场,使得辊身轴向产生不均匀热膨胀,进而形成工作辊热变形・轧制过程中轧辊表面热变形为u(R)=2(1+υ)βR∫R(t R-t R0)r d r=(1+υ)βΔ t R R・(5)式中,Δ t R为轧辊断面内的平均上升温度,℃;β为轧辊材质线膨胀系数,mm/℃;υ为泊松比; t R为轧辊当前表面温度,℃;t R0为轧辊原始温度,℃・2 计算实例在确定轧辊温度场及热凸度基本模型后,用C++语言编制了轧辊温度场及热凸度离线模拟计算程序・现以国内某1700热轧带钢厂某一轧制周期为例,对F2~F4CVC工作辊温度场及热凸度进行离线模拟分析・在计算中,主要的热传输参数及温度初始值取下列各值:各机架轧辊与空气热交换系数取值0.003W/(mm2・℃);各机架轧辊辊颈与轧辊轴承间热交换系数取值0.002W/(mm2・℃);各机架轧辊初始温度,轴承初始温度,环境初始温度均取值25℃・在此轧制周期中,共轧制194卷带钢,其宽度变化范围为1140~1255mm,如图3所示・图4为F2~F4上辊轧制末了表面温度变化情况及F2上辊表面温度测量值・由图4可知,轧辊轴向温度的分布并不相对于轧辊中心线对称,这是由于在轧制过程中,CVC轧辊为满足板形控制要求而不断横移,导致轧辊表面左右两侧温度差别显著・F2,F3和F4轧辊上表面在轧制结束后表面的最高温度分别为58.1,73.1和81.2℃・F2轧辊上表面在轧制结束后的最高温度较低的另一个主要原因为工艺要求F2在轧制过程中甩架次数较多(轧制194块中有28块发生甩架)・图3 带钢宽度的变化Fig.3 Variation of strip width图4 F2~F4轧辊(上辊)表面温度变化Fig.4 Variation of roll surface temperature ofF2~F4(top roll)在轧制周期结束后,即将各架轧辊抽出,进行空冷・轧辊抽出后,清除轧辊表面粘附物,采用高精度测温笔测量轧辊表面温度・测量起点为轧辊驱动侧端部,测量方向由驱动侧至操作侧,辊身均匀划分32份・从轧辊下机开始,空冷24h,每隔2 h测量一次,每次测量三组数据,然后对其取平均值・通过对比F2轧辊上表面程序计算得到的温度与实测温度可知,轧辊中心温度曲线吻合较好;而在轧辊边部,测量得到的温度明显高于程序计算得到的数值,这可能因为在空冷过程中,轧辊中部热量向轧辊边部传递的结果・图5为F2~F4上辊轧制末了轧辊轴向热变形情况・由图5可知,各机架轧辊表面轴向热变形曲线明显不对称于轧辊中心线・轧辊上表面在轧制结束后表面的最大变形量(半径方向)偏离了轧辊中部,其值分别为1931979,2751259和3331433μm・915第4期 郭忠峰等:1700热连轧机轧辊温度场及热凸度研究图5 F2~F4轧辊(上辊)热变形变化Fig.5 Variation of thermal shape of F2~F4(top roll)3 结 论1)建立了热带钢轧机工作辊温度场差分模型,计算了某一轧制周期工作辊温度场及热凸度・工作辊表面温度计算值与实测值吻合良好,说明所建立的模型具有较高精度,可满足在线预报要求・2)对CVC轧辊而言,轧辊表面温度分布及热变形变化,明显受到轧辊横移的影响・在整个轧制过程中,轧辊表面热变形变化与轧制节奏密切相关・参考文献:[1]Tseng A A,Tong S X,Raudensky M.Thermal expansionand crown evaluations in rolling processes[J].S teelResearch,1996,67(5):188-199.[2]陈宝官,陈先霖・用有限元法预测板带轧机工作辊热变形[J]・钢铁,1991,26(8):40-44・(Chen Bao2guan,Chen Xian2lin.Prediction of work rollthermal deformation with finite element method on hot stripmill[J].Iron and S teel,1991,26(8):40-44.)[3]Li C S,Liu X H,Wang G D.Three2dimensional FEManalysis of work roll temperature field in hot strip rolling[J].M aterials Science and Technology,2002,18(10):1147-1150.[4]包仲南・带钢连轧机工作辊瞬态温度场的有限元仿真[J]・北京科技大学学报,1991,21(1):60-63・(Bao Zhong2nan.Imitation of instantaneous temperature fieldof work roll in hot strip mill by finite element method[J].Journal of U niversity of Science and Technology Beiji ng,1991,21(1):60-63.)[5]孔祥伟,徐建忠,龚殿尧,等・采用平辊实现自由程序轧制最优横移方案新方法[J]・东北大学学报:自然科学版,2002,23(12:1166-1169・(K ong Xiang2wei,Xu Jian2zhong,G ong Dian2yao,et al.Optimum shift scheme of SFR realized by adopting flat roll[J].Journal of Northeastern U niversity:N at ural Science,2002,23(12):1166-1169.)[6]李俊洪,连家创,岳晓丽・热带钢连轧机工作辊温度场和热凸度预报模型[J]・钢铁研究学报,2003,15(6):25-28・(Li J un2hong,Lian Jia2chuang,Yue Xiao2li.Predictionmodel of temperature field and crown of work roll for hotstrip mill[J].Journal of Iron and S teel Research,2003,15(6):25-28.)[7]Lenard J G.Predictive capabilities of a thermal model of flatrolling[J].Steel Research,1989,60(9):403-406.[8]Atack P A,Robinson I S.Control of thermal camber byspray cooling when hot rolling aluminum[J].Iron M aki ngand S teel M aki ng,1996,23(1):69-73.[9]Vladimr B G.Application of coolflex model for analysis ofwork roll thermal condition in hot strip mills[J].Iron andS teel Engi neer,1997(11):38-45.[10]Yang L P,Peng Y,Liu H M.Two2dimensional transienttemperature field of finish rolling section in hot tandem rolling[J].Journal of Iron and S teel Research,2004,11(4):29-33.(上接第503页)[5]Tolle G,Polastre J,Szewczyk R,et al.Design of anapplication2cooperative management system for wireless sensor networks[C]∥Proceedings of the2nd European Workshop on Wireless Sensor Networks.Istanbul:IEEE Press,2005:121-132.[6]Wang Y,Martonosi M,Peh L S.A new scheme on linkquality prediction and its applications to metric based routing[C]∥Proceedings of the3rd International Conference onEmbedded Networked Sensor Systems.San Diego:ACM Press,2005:288-289.[7]张希元,赵海,孙佩刚,等・WebitOS内核的实现机制及性能分析[J]・东北大学学报:自然科学版,2006,27(4):394-397・(Zhang Xi2yuan,Zhao Hai,Sun Pei2gang,et al.Realization mechanism and performance of WebitOS kernel[J].Journal of Northeastern U niversity:N at ural Science,2006,27(4): 394-397.)[8]张文彤,董伟・SPSS统计分析高级教程[M]・北京:高等教育出版社,2004:70-115・(Zhang Wen2tong,Dong Wei.Advanced tutorial for statistical analysis using SPSS[M].Beijing:High Education Press, 2004:70-115.)025东北大学学报(自然科学版) 第29卷。
1700mm热连轧机组的生产设备与生产技术分析
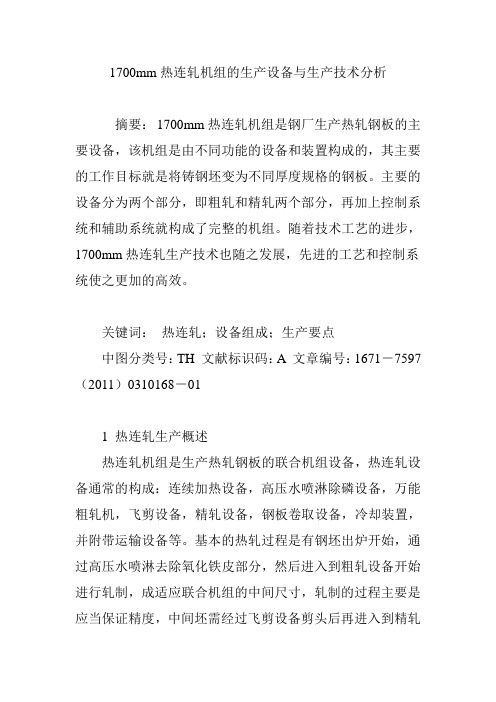
1700mm热连轧机组的生产设备与生产技术分析摘要:1700mm热连轧机组是钢厂生产热轧钢板的主要设备,该机组是由不同功能的设备和装置构成的,其主要的工作目标就是将铸钢坯变为不同厚度规格的钢板。
主要的设备分为两个部分,即粗轧和精轧两个部分,再加上控制系统和辅助系统就构成了完整的机组。
随着技术工艺的进步,1700mm热连轧生产技术也随之发展,先进的工艺和控制系统使之更加的高效。
关键词:热连轧;设备组成;生产要点中图分类号:TH 文献标识码:A 文章编号:1671-7597(2011)0310168-011 热连轧生产概述热连轧机组是生产热轧钢板的联合机组设备,热连轧设备通常的构成:连续加热设备,高压水喷淋除磷设备,万能粗轧机,飞剪设备,精轧设备,钢板卷取设备,冷却装置,并附带运输设备等。
基本的热轧过程是有钢坯出炉开始,通过高压水喷淋去除氧化铁皮部分,然后进入到粗轧设备开始进行轧制,成适应联合机组的中间尺寸,轧制的过程主要是应当保证精度,中间坯需经过飞剪设备剪头后再进入到精轧设备中,一次轧制成需要的规格然后再进行卷取,且中间都需要进行二次除鳞。
热轧机目前已经进入了全线自动化的阶段,并且采用厚度自动控制、弯辊系统等新兴技术。
九十年代末期,连轧设备广泛的应用在薄钢板的轧制加工中,从炼钢到轧制钢板形成了一个连贯的自动化生产流程,形成了短流程、低能耗、高效率的生产线。
目前正向着热轧复合板技术发展,并成功的轧制了不锈钢复合卷板。
2 1700mm热连轧机组的设备组成下面就某钢厂的1700mm热连轧机组为例具体说明热连轧机组的设备构成。
1)基本组成。
某钢厂的1700mm热连轧机组主要构成有:四台步进梁式加热炉,粗轧机三台,立辊轧机三台,高速飞剪一台,七机架精轧机组,配套冷却设备,卷取机三台,钢卷检查装置一套,自动打捆机和喷号系统及步进梁运卷系统。
这些设备构成了一条完整的热连轧机组,从加热到轧制到成品运输构成了一个完整的成产线。
- 1、下载文档前请自行甄别文档内容的完整性,平台不提供额外的编辑、内容补充、找答案等附加服务。
- 2、"仅部分预览"的文档,不可在线预览部分如存在完整性等问题,可反馈申请退款(可完整预览的文档不适用该条件!)。
- 3、如文档侵犯您的权益,请联系客服反馈,我们会尽快为您处理(人工客服工作时间:9:00-18:30)。
1700热连轧机毕业设计论文1绪论1.1热连轧生产的国内外发展概况热轧宽带钢轧机的发展已有70多年的历史,第一套热连轧机于1926年诞生于美国。
汽车工业、建筑工业、交通运输业等的发展,使得热轧机冷轧薄钢板的需求量不断增长,从而促进热轧宽带钢轧机的建设获得了迅速和稳定的发展。
促进热轧宽带钢轧机及工艺技术发展的主要因素是:要求其生产能力不断提高,从而钢卷质量不断增大和轧制速度不断提高,同时提出扩大产品品种的要求;要求产品的尺寸精度和性能不断提高;受1973年中东石油危机的冲击而转向注意开发节约能源技术;进入20世纪80年代中期更加注重产品质量的提高,并对板形质量及带钢凸度和平直度提出更高的质量要求。
热轧宽带钢轧机的热轧板卷,不仅可以供薄板和中板直接使用,还可以作为下道工序冷轧、焊管、冷弯型钢的原料。
带钢热连轧机从50年代起,在世界范围内已成为带钢生产的主要形式。
目前世界上1000mm以上的热轧机和带卷轧机有200余套。
带钢热连轧机具有轧制速度高、产量高、自动化程度高的特点,轧制速度50年代为10~12 m/s,70年代已达18 ~ 30 m/s,产品规格也由生产厚度为2 ~8mm,宽度小于2000mm的成卷带钢扩大到生产厚度1.2 ~20mm,宽度2500mm的带钢。
带卷重量的加大和作业率的提高,使现有的带钢热连轧机年产量达350 ~600万t,最大卷重也由15t增加到70t。
坯料尺寸及重量加大,要求设置更多的工作机座,过去的粗轧机组和精轧机组的工作机座分别为2~4架和5~6架,现已分别增加到4 ~ 6架和7~8架,轧机尺寸也相应增加。
现代的带钢热连轧机除了采用厚度自动控制外,还实现了电子计算机控制,从而大大提高了自动化水平,改善了产品质量,带钢厚度公差不超过±0.5mm,宽度公差不超过0.5 ~1.0mm,并具有良好的板形。
90年代以来,钢铁生产短流程迅速开发和推广,薄板坯(或中厚板坯)连铸连轧工艺的出现,正在改变着传统的热连轧机市场。
自1987年7月第一套薄板坯连铸连轧生产线在美国纽柯公司投产以来,到1997年已建成和拟建的有33套。
连铸连轧技术是将钢的凝固成型与变形两个工序衔接起来,将连铸坯在热状态下继续送入精轧机组,直接轧制成带卷产品。
[1,14-16]1.2 热连轧在轧钢生产中的作用及其发展情况连轧机使用原料厚度150 — 350mm的板坯或连铸坯。
在连续式加热炉中,将板坯加热到轧制温度后,先在粗轧机组的立辊除鳞机座破除板坯表层的氧化铁皮。
经粗轧机组各工作机座后,轧制成厚度为25—60mm的长带坯。
经过切头飞剪切去带坯端头,送入具有6 — 7座四辊式连轧机的精轧机组中,轧成成品厚度的带钢。
经冷却到550—650℃后,卷成钢卷,用链式运输机送往热轧卷材仓库存放。
冷却至常温后,由精整工段的横切机组或纵切机组经开卷、矫直、平整及剪切后,切成定尺长度的热轧钢板或窄带钢卷,供应工业生产需要。
热连轧机可分为:连续式、半连续式、四分之三连续式等。
连续式热带钢轧机,除立辊机座外,共有11~13个工作机座,均为不可逆式轧机。
各机座均进行一道次轧制。
根据车间设备组成及主电机功率的不同,轧机年产量约在200~600万吨之间。
半连续式热带钢轧机,除立辊除鳞机及一台二辊不可逆式轧机外,用一台可逆式四辊轧机反复轧制,进行几道次压下,轧成带坯送往精轧机组,精轧后卷成钢卷。
共有7~9个工作机座。
轧机年产量根据设备能力不同,约在100~250万吨之间。
六十年代后出现的四分之三连续式热带钢轧机的粗轧机组,采用一台四辊式或二辊式可逆轧机来代替3台四辊式不可逆轧机,其余轧制设备与连续式相同,这样可以减少设备重量,缩短车间长度,减少建设投资。
车间年产量与连续式热带钢轧机相同。
2.高速线材轧机的发展 1) 近年来,高速线材生产取得巨大进步,主要表现在生产率显著提高。
2) 产品规格范围增大,钢种增多。
3) 产品精度有所提高,一般均能达到士O.lmm。
4) 低温轧制、控轧挖冷、热装热送等技术的采用节约了能源,提高了成品率和产品性能。
5) 全连续无扭轧制避免了产品扭曲轧制产生的应力,提高了产量质量。
我国线材产量已居世界前茅,这批“高线”轧机全部投产后,我国不仅在产量上将成为线材1.3实习车间车间概况术在鞍钢,我们了解到现代化连续式热带钢轧机,主要用于轧制厚度为1~20mm的带钢。
最近15年,热连轧技术有了很大的进步,在热轧带钢轧机布置形式的发展方面。
总结起来,主要有6种形式:第一种是典型的传统热带钢连轧机组。
这种机组通常是2架粗轧机,7架精轧机,两个地下卷取机,年总产量350×550万吨,生产线的总长度有400×500m,有些新建的机组装备了定宽压力机(SP)。
这类轧机采用的铸坯厚度通常200×250衄。
特点是产量高,自动化程度高,轧制速度高(20M/s以上)、产品性能好。
第二种是紧凑型的热连轧机,通常机组的组成为1架粗轧机,1台中间热卷箱,5×6架精轧机,1×2个地下卷取机,生产线长度约300m,年产量约200×300万吨。
采用的铸坯厚度200衄左右,比较少,生产比较灵活,由于使用热卷箱温度条件较好,可以不用升速轧制(轧制速度14M/s)。
第三种是新型的炉卷轧机机组,常采用1台粗轧机,1台炉卷轧机,1 x2台地下卷取机,产量约100万吨,其中有的生产线可以生产中板也可以生产热轧板卷,主要用于不锈钢生产,投资较小,灵活,合多品种。
1三座加热炉 2高压水除鳞箱 3粗轧除鳞 4粗轧前大立棍图1.1 1700设备及工艺流程2方案设计2.1线材生产对扎钢的要求:线材轧机是专门用于轧制盘条(即线材)的轧机。
线材是型材中断面尺寸最小的产品,从坯料轧成成品,总延伸系数大,轧件在每架轧机上往往只轧一道次,故线材轧机是热轧型材中机架数目最多、分工最细的轧机。
通常认为直径范围在5.5—20mm的线材在高速线材轧机上生产,直径在16—60mm的线材多用小型线材联合机组生产成棒卷。
目前现代化的连续式线材轧机一般由21~28架轧机组成,分为粗轧机组、中轧机组和精轧机组,中轧机组有时还分为一中轧、二中轧两组。
线材轧机的结构和布置方式一直朝着高速、连续、无扭、单线、组合结构、机械化、自动化的方向发展。
由巴西圣保罗Viliares设备公司为巴西贝戈尔一内拉钢铁厂建造的世界上速度最高的线材轧机----贝戈尔一内拉的新单线线材轧机。
1.小型、线材轧制技术的发展方向高速、连续轧制是20 世纪中期工业发达国家提出的线材和小型材轧制技术的发展方向。
小型和线材轧机的产品均为小断面, 重量轻, 只有提高轧制速度才能提高小时产量。
高速轧制 20 世纪中期, 线材轧机的最高轧制速度只有30m/ s。
经济学家从成本构成的角度分析指出, 如果轧制速度提高1 倍, 虽然设备造价也提高1 倍,但冶金企业仍会因人工投入的相对减少而盈利。
在这个方针指引下, 许多轧机制造商研制了具有更高速度的轧机, 直至最终诞生了高速线材轧机,开创了线材生产的新时代。
之后, 提高轧制速度仍是人们追求的主要目标。
因为高速轧制不仅可以提高生产效率, 而且轧制时可使用更大断面的连铸坯。
时至今日, 最高实用轧制速度已达 120m/ s, 小型轧机速度也提高了1 倍。
1990 年投产的巴西Belgo 厂棒线材轧机, 生产φ5.5mm 线材的保证速度为120m/ s, 最高速度达140m/ s,φ16mm 大盘卷轧制速度可达26.4m/ s。
直条棒材生产时轧制速度往往受冷床限制, 西马克公司曾提出小规格直条棒材轧制速度最大允许为41m/ s。
提高速度需要更多投入, 用经济法则可权衡在某一时期或许会有暂时的最高经济速度, 但“高速轧制”无疑是线材、小型轧机发展中的追求。
1.2连续轧制通过对小型、线材轧机诸多布置形式和工艺特点比较后, 得出横列式、顺列式、布棋式、半连续式都不如连续式更能适应小型与线材轧制的要求。
细长的轧件温降快, 轧制时间是关键。
以前曾提出过极限轧制时间, 即限定总轧制时间和成品道次的轧制时间。
总轧制时间限制总温降;成品道次的轧制时间限定轧件头尾温差。
活套轧制、穿梭轧制, 造成轧制时间长、温降大、轧件头尾温差大, 不利于轧制时间的控制。
而连续式轧制不仅轧制时间短, 而且可以减少轧件头尾温差, 理论上可以实现各机座的恒温轧制, 从而在工艺上取消了对坯料重量的限制,这是横列、顺列、布棋、半连续式布置做不到的。
连续式轧机操作最简便, 用人最少, 轧机效率最高。
由于多年来追求高速、连续轧制, 因而小型和线材轧机得到迅速发展, 同时也促进了轧钢技术进步。
2.2 F7精轧机的总体结构和传动方案综合分析因为F7机架轧制速度高,而且精轧机组主电机功率不是很大,考虑到成本和维修费用,故不能采用减速机减速传动。
齿轮座起分配扭矩的作用,它的可能的替代形式是采用双电机驱动,由于精轧机轧制压下量较小,轧制力和力矩也较小,应用齿轮座分配力矩齿轮座的尺寸不太大,制造和维修比较容易,所以成本比双电机要低。
压下系统采用电动压下装置电动双压下装置:这是较旧式轧机上的一种电动压下装置,该压下装置具有粗调与精调两个压下系统。
个系统分别有各自的电动机和减速器。
平衡装置采用液压式平衡平衡装置类型有弹簧式、重锤式和液压式等。
由于精轧机组需要经常换辊,而且弹簧式装置换辊时需人工拆装弹簧,费力、费时,故不采用弹簧式平衡。
重锤式工作可靠,维修方便,但设备重量大,轧机的基础结构较复杂。
由于四辊热轧要平衡的重量很大,使得设备重量会更大,故也不采用。
液压式平衡装置结构紧凑,与其它平衡方式比较,使用方便,易操作,能改变油缸压力,而且可以使上辊不受压下螺丝的约束而上下移动,所有这些都有利于换辊操作。
故采用液压式平衡最合适。
1 支撑辊2 工作辊3支撑辊 4 连接轴支座 5 连接轴 6 齿轮机座 8电动机图2.1传动装置示意图3 主电机容量的选择3.1轧制力的计算3.1.1主要参数的选择1、轧制规程F 7精轧机:板坯断面 240×1600mm 2 重240kg轧制速度 12 m/s原料断面 2.9×1550 mm 2成品断面 2.5×1500 mm 2轧制温度t =860℃轧制钢种 Q2352、工作辊直径选择由文献[1,79]咬入条件确定最小工作辊直径αcos 11-∆≥h D (3.1)式中: α——最大咬入角,它和轧辊与轧件间的摩擦系数有关,h ∆——最大轧制厚度差,10h h h -=∆,已知h ∆=0.4mm 。
52.7042cos 14.0cos 11=︒-=-∆≥mm h D αmm 考虑安全性及其他因素,取1D =730 mm 。