超声波检测中的波形识别
在役支柱瓷绝缘子超声波检测波形分析
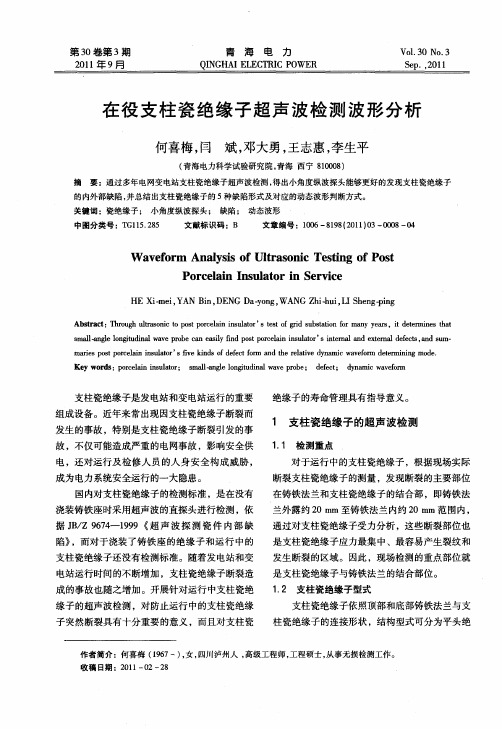
W a e o m a y i o t a o i si g o o t v f r An lss fUl s n c Te t fP s r n P r e an I s lt r i e vc o c l i n u a o S r ie n
HE Xime , - i YAN B n, ENG Da y n , i D -o g WANG h - u , IS e g p n Z i i L h n - ig h
Ab t a t h o g l a o i o p s p r ean i s l tr S ts f d s b tt n f rma y y a s t d tr n s t a s r c :T r u h u t s n c t o t o c l i n u ao ’ e t r o u sai o n e r ,i ee mi e h t o
子 突然 断裂具 有 十分重 要 的意义 ,而且 对 支柱瓷
通过对支柱瓷绝缘子受力分析 ,这些断裂部位也
是 支柱 瓷绝 缘子 应力最 集 中 、最 容易 产生 裂纹 和 发 生 断裂 的区域 。 因此 ,现 场检 测 的重点部 位就
是支柱瓷绝缘子与铸铁法兰的结合部位。
12 支柱 瓷绝缘 子型 式 .
第 3 卷第 3期 0 21年 9 01 月
青 海 电 力 Q N H IE E T I O R I G A L C R C P WE
V 13 . 0 . O No 3
S p., 01 e 2 1
在 役 支柱 瓷绝 缘 子 超 声 波 检 测 波 形分 析
何喜梅 , 斌 , 闫 邓大勇 , 王志惠 , 李生平
/ \
/
A
\
自动焊对接焊缝超声波探伤中变形波的识别
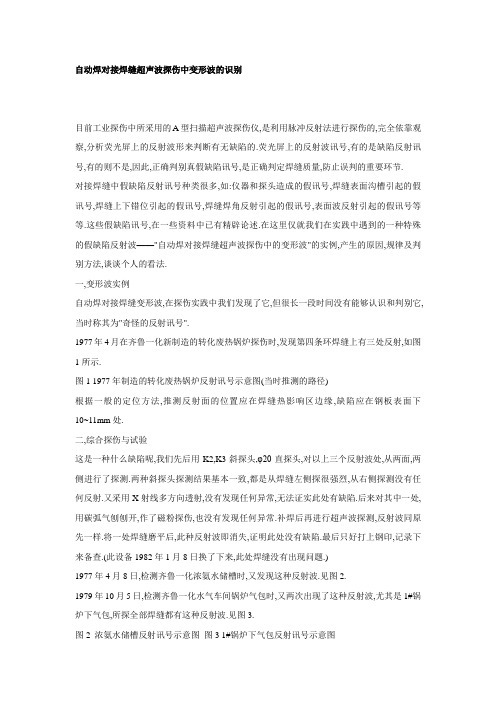
自动焊对接焊缝超声波探伤中变形波的识别目前工业探伤中所采用的A型扫描超声波探伤仪,是利用脉冲反射法进行探伤的,完全依靠观察,分析荧光屏上的反射波形来判断有无缺陷的.荧光屏上的反射波讯号,有的是缺陷反射讯号,有的则不是,因此,正确判别真假缺陷讯号,是正确判定焊缝质量,防止误判的重要环节.对接焊缝中假缺陷反射讯号种类很多,如:仪器和探头造成的假讯号,焊缝表面沟槽引起的假讯号,焊缝上下错位引起的假讯号,焊缝焊角反射引起的假讯号,表面波反射引起的假讯号等等.这些假缺陷讯号,在一些资料中已有精辟论述.在这里仅就我们在实践中遇到的一种特殊的假缺陷反射波——"自动焊对接焊缝超声波探伤中的变形波"的实例,产生的原因,规律及判别方法,谈谈个人的看法.一,变形波实例自动焊对接焊缝变形波,在探伤实践中我们发现了它,但很长一段时间没有能够认识和判别它,当时称其为"奇怪的反射讯号".1977年4月在齐鲁一化新制造的转化废热锅炉探伤时,发现第四条环焊缝上有三处反射,如图1所示.图1 1977年制造的转化废热锅炉反射讯号示意图(当时推测的路径)根据一般的定位方法,推测反射面的位置应在焊缝热影响区边缘,缺陷应在钢板表面下10~11mm处.二,综合探伤与试验这是一种什么缺陷呢,我们先后用K2,K3斜探头,φ20直探头,对以上三个反射波处,从两面,两侧进行了探测.两种斜探头探测结果基本一致,都是从焊缝左侧探很强烈,从右侧探测没有任何反射.又采用X射线多方向透射,没有发现任何异常,无法证实此处有缺陷.后来对其中一处,用碳弧气刨刨开,作了磁粉探伤,也没有发现任何异常.补焊后再进行超声波探测,反射波同原先一样.将一处焊缝磨平后,此种反射波即消失,证明此处没有缺陷.最后只好打上钢印,记录下来备查.(此设备1982年1月8日换了下来,此处焊缝没有出现问题.)1977年4月8日,检测齐鲁一化浓氨水储槽时,又发现这种反射波.见图2.1979年10月5日,检测齐鲁一化水气车间锅炉气包时,又两次出现了这种反射波,尤其是1#锅炉下气包,所探全部焊缝都有这种反射波.见图3.图2 浓氨水储槽反射讯号示意图图3 1#锅炉下气包反射讯号示意图以上三次检测发现的反射波现象,都发生在自动焊对接焊缝区.1983年淄博客车厂,在探测液化石油气槽车自动焊对接焊缝时,也发现了这种变形波反射.据了解胜利炼油厂也曾多次发现这种变形波反射.三,变形波产生的原因经分析和研究,发现这种波形是焊缝表面形状引起的变形纵波反射.由超声波的性质可知,当超声波束倾斜传播,遇到异形界面时,在反射和折射过程中,都可能产生变形波.但是,为什么在焊缝探伤中,一般情况下荧光屏上不出现变形纵波反射讯号呢这可从超声波在焊缝中传播的路径得到解释.由反射定律可求得:变形定律反射角: βL=arcsin(CL/Cs×sinβs)(1)横波入射角: βs= arc sin(Cs/CL×sinβL) (2)因为纵波声速约为横波的两倍,可知变形纵波反射角将大大地大于横波入射角.我们所用探头的角度,是在第一临界角和第二临界角之间,计算可知此时变形纵波,将沿工件表面传播或超出工件表面,所以一般情况下,荧光屏上不会出现变形纵波反射讯号.但在特殊情况下,尤其是在成形很有规律的自动焊对接焊缝中,有时就会出现变形纵波.观察自动焊焊缝表面成型,大致有以下几种形式.如图4所示.平缓圆弧形(小区率) 棱角形表面(如2M16二段冷却分析器)突陡圆弧形(大曲率) 类半圆形表面图4 自动焊焊缝表面的几种成型形式在这几种成型的焊缝中,都不会象在平板中那样,按原来的折射角进行传播,而要改变传播方向.到达焊缝弧面后,反射角度将变小,并随弧面曲率变化而变化,当反射角小到一定程度时,变形纵波将在焊缝或板材内传播,便有可能返回探头,显示到荧光屏上.让我们来分析一下图4中几种焊缝表面成形,找出超声波束在其中传播的规律.图中L表示纵波波束, S表示横波波束,βs表示横波入射角,βL表示变形纵波反射角.βs/表示横波反射角.首先,让我们来看看第种焊缝成形,这种焊缝成形是比较理想的,由于焊缝表面平缓,超声波束入射后反射角改变很小,变形纵波不会出现在工件中,也就不会在荧光屏上出现变形纵波反射讯号.第种焊缝成形,表面呈棱角状,与入射波束有较好的垂直性,其中大部分能量被反射回探头.(这是一种特殊情形,其检测方法与判别将在另外的文章中讨论).焊缝表面与工件表面呈一定的角度,横波声束到达其表面后,有可能产生变形纵波,但这种变形纵波只能在工件中向前传播,不能返回被探头接受,所以荧光屏上不会出现变形纵波反射讯号.第种焊缝成形,表面余高很大,呈圆弧形.入射波位置不同,波束传播规律也不相同.图中表示的是两种极限位置的传播规律,其1是探头推到最前沿的传播规律,其2是一次波束能达到的最后位置.从图中分析可以看出,在这种焊缝中会出现变形纵波,但由于圆弧形焊缝的反射规律,变形波不会被探头接受,所以荧光屏上也不会出现变形波讯号.最后,让我们来分析第种焊缝成形,这种焊缝边缘陡直,表面又比较平缓,类似半个椭圆形,其断面外形很像压力容器碟形封头的剖面.焊缝与母材交界处呈一小圆弧形,当入射横波达到小圆弧面时,便有变形纵波产生,变形纵波可以到达焊缝上表面反射回来,被探头接受显示在荧光屏上.因为纵波声速约等于横波声速的两倍,在相同的时间里,纵波所走的路程也约等于横波所走路程的两倍.因为荧光屏水平扫描线的比例是按横波声束调节的,所以变形纵波的回波在荧光屏上显示的数字,不是它走的真实路程,而仅等于它的1/2.在这里所谓的纵波路程,仅指变形纵波在焊缝中走的路程.返回探头是经焊缝下表面,再次变为横波而被接受的.若变形纵波所走路程以L表示,工件厚度用δ表示,则L≈δ,这段路程显示在荧光屏上仅为1/2δ.如果按原横波入射方向的三角关系推算(这是错误的!),就会误认为反射面所在的位置,是在焊缝热影响区之内(当时所推测的缺陷位置),如图2~4所示.四,产生变形纵波反射的临界条件通过以上分析可知,只有当焊缝剖面呈边缘陡直,表面较平缓的半椭圆形时,才可能出现变形纵波反射讯号.当变形纵波接近垂直于焊缝上表面时,反射回探头的能量较大,就出现变形纵波反射.参见图5. 图5 纵波变形波反射条件示意图由反射定律可知:sinβL:sinβS/=CL:CS……………………………………………………………………………………又从图5中可知<β=<βL+<βS/ 则<βL=<β-<βS/从式可知:sin(β-βS/):sinβS/= CL:CS……………………………………………………根据三角函数的"和差公式":sin(β-βS/)= sinβcosβS/-cosβsinβS/………………………………………………………式可为:(sinβcosβS/-cosβsinβS/)/sinβS/= CL/CS………………………………………又根据三角函数关系:ctgβS/= cosβS// sinβS/……………………………………………………式可为:sinβctgβS/-cosβ= CL/CS ……………………………………………………………ctgβS/=(CL/CS+ cosβ)÷sinββS/=arc ctg[(CL/CS+ cosβ) ÷sinβ] ………………………………………………………………在中厚工件(δ=12~40mm)探伤中,常选用K=2的探头,K2探头折射角β=63.26/,代入式计算可得βS/=21.36/.即当选用K2探头探伤时,如果能满足βS/=21.36/或稍大,稍小于21.36/时,变形纵波便垂直于(或接近垂直于)焊缝表面,此时变形纵波产生强烈的反射,荧光屏上将出现变形纵波讯号.所以βS/=21.36/是产生这种变形纵波的临界角度.此时焊缝的焊角处表面小圆弧的圆心位置,可按以下方法求得.在△OBC中,tg(90.-β+βS/)=OC/(BE/2)OC=(BE/2)tg(90.-β+βS/)…………………………………………………………式中BE可近似地看作是焊缝宽度,OC可近似地看作是焊缝表面小圆弧的圆心O到焊缝表面的距离.当选用K=2探头时,OC≈0.5585BE.此时小圆弧半径为:R=OB=BC/[cos(90.-β+βS/)]≈0.76BE.在中厚焊缝中,常采用X型坡口,此时BE≈δ(工件厚度).可以看出,当小圆弧的圆心O处于焊缝中部附近,或略靠上,略靠下时,亦即小圆弧的半径在0.68~0.76倍工件厚度时,就可能出现变形纵波反射.此值即产生这种变形纵波的临界半径.小结1,从以上事例和分析不难看出,焊缝中此种变形纵波反射,常出现在自动焊缝中,其焊缝表面形状为表面较平缓,焊角处呈一小圆弧形.当自动焊中出现类似图1~3中反射波时,要注意观察分析焊缝表面形状,分析是否产生变形纵波.2,产生这种变形纵波反射的临界角度βS/=21.36/~24.7/,焊角小圆弧临界半径R=0.68~0.76δ.测量临界半径可用万能型规,将焊缝表面形状取下来,作图求出.3,表面形状的观察分析,临界条件的测量计算,是分析产生变形纵波反射的条件.除了以上观察,测量,计算,分析外,还应该采用多种方法的综合检测,有条件时可将焊缝磨平,然后检验验证,以得到确无缺陷的可靠结论.《化工设备检验》1989年第1期发表。
浅析锻件超声波探伤中缺陷波和伪缺陷波的识别

浅析锻件超声波探伤中缺陷波和伪缺陷波的识别发表时间:2018-05-25T15:29:14.550Z 来源:《基层建设》2018年第6期作者:解斌[导读] 摘要:锻件经常用于承受应力复杂、冲击震动、重负荷载等类型的零部件中,其一旦出现问题,将造成严重后果。
沈阳铸锻工业有限公司检测中心辽宁沈阳 110142摘要:锻件经常用于承受应力复杂、冲击震动、重负荷载等类型的零部件中,其一旦出现问题,将造成严重后果。
基于此,文章介绍了锻件超声波探伤中关于缺陷波和伪缺陷波的识别方法,希望能够为锻件生产提供一定的指导,达到对锻件探伤的目的。
关键词:锻件超声波探伤;缺陷波;伪缺陷波;识别引言近年来,锻件在石油化工、兵器、航天、能源、机械、冶金等行业获得广泛应用,逐渐成为这些行业生产过程中的重要设备。
如果锻件质量出现问题,会严重影响这些行业的发展。
因此,应用超声波探伤并找出反射波的规律,识别其中的缺陷波和伪缺陷波显得尤为必要。
1识别锻件缺陷波和伪缺陷波的重要性锻件常应用于承受重负载荷、冲击振动以及复杂应力等类型零部件中。
这些零件损坏或者是失效以后会引发严重后果,轻则影响到系统功能,重则可能会危及到工作人员的生命安全,并给相关产业带来巨大的经济损失。
因此,保证锻件质量需要正确识别锻件超声波探伤中的缺陷波以及伪缺波,以此来指导锻件的生产。
超声波探伤是一种检查接焊缝内部缺陷的方法,具有灵敏度高、检测速度快并且使用方便等优点,可以有效检测出锻件的质量问题。
2缺陷波识别方法2.1根据缺陷特征分析缺陷性质对于平面状缺陷,可以从不同方向进行探测,根据缺陷回波高度的差异识别缺陷波。
在垂直于缺陷方向探测,缺陷回波高,在平行于缺陷方向探测,缺陷回波低,甚至无缺陷回波。
一般来说裂纹、夹层、折叠等属于这种缺陷。
对于点状缺陷从不同方向探测,缺陷回波无明显变化。
一般包括点状夹渣和密集气孔以及单个气孔。
点状夹渣和气孔的缺陷回波波形稳定,高度较低,从任何方向探测,反射波的高度差别不大,但稍一移动探头就消失。
超声波检测的波形分析

超声波检测的波形分析
一、超声波检测的原理
超声波检测是指利用超声波声压快速变化,来探测物体的材质和结构,及其缺陷,并做出相应的表示的检测方法和技术。
它是一种高频超声技术,它通过使用高频超声耦合到结构中,集中和分散发生,并通过给定的传感
器接受,来探测结构的材质、结构、缺陷种类及其大小等信息。
1、超声波检测中,有四类主要波形:A波形、B波形、C波形、D波形,它们分别代表的是不同的信号及特征,不同的波形通常被用来表示以
下特征:A波形表示表面引起的弹性驻波;B波形表示表面和内部引起的
弹性驻波;C波形表示表面的热驻波;D波形表示表面和内部的热驻波。
2、超声波检测波形分析还可以用来识别缺陷。
通过波形可以分析出
缺陷的大小、位置、形态等信息。
在对缺陷的测量时,波形的极值上或者
下限位置就可以用来确定缺陷的位置,通过计算波形的极值点的高度可以
得出缺陷的大小。
3、超声波检测还可以用来比较和对比不同样品的测量结果,这就需
要将不同样品的测量数据全部行拟合,以得到最佳的拟合曲线。
课件描述超声波探伤仪的原理及波形显示图
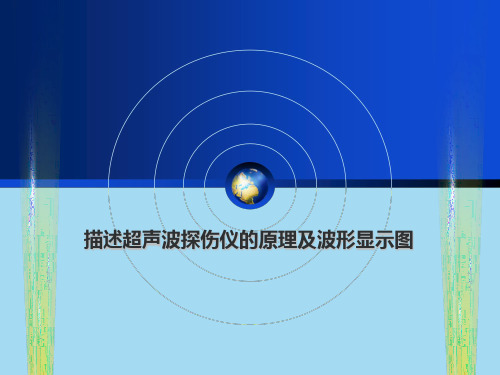
二、探伤仪检测螺栓孔及伤损的波形显示
左图为探伤仪在钢轨推行 时,探头声束角度的发出:
右图为探头声束发射角度在 钢轨上的示意图:
G探头
I探头
H探头
下图红色虚线内为螺栓孔在荧光屏上面出现的波形显示图:
其余探头的波形 显示图
下图为螺孔斜裂纹及波形显示图:
受螺栓孔阻挡无法探测
三、焊缝探伤仪0°探头探测伤损的波形显示
描述超声波探伤仪的原理及波形显示图
钢轨探伤仪 探头 钢轨
一、超声波探伤的原理
超声波探伤是探伤仪利用超声能透入钢轨材质的深处,超声波声
束由探头发出通至钢轨内部遇到缺陷与钢轨底面时分别产生反射 波,在荧光屏上形成波形显示(波束与缺陷越接近横向垂直时, 反射效果越好,波形显示越明显,反之纵向时,显示效果越弱), 从而判断缺陷的位置与大小。 探头又称换能器,由电能激励压电晶片产生机械振动,从而产生机械 能,发出声束。
请看下面左侧的图片,分析一下会有波形显示吗?
注意:波束与缺陷越接近垂直时,反射效果
越好,波形显示越明显。
下图为上图的波形显示图:
Байду номын сангаас
所以当伤损缺陷与声束同向 而不垂直时,探伤仪对伤损 缺陷的检出能力是最差的!
五、伤损实例图
六、超声波探伤的优、缺点
优点:
u 不破坏工件内部; u 检出能力强; u 显示效果佳等等。
由于钢轨焊缝中伤损不同角度发展的多样性,所以为了更 好的发现伤损缺陷,设计院把探头里的晶片按角度也设计 为很多种,如0°、37°、45°、70°等分别应用在探伤仪中。
这里重点讲解0°探头遇见伤损的波形显示。
当伤损位于钢轨中部时,如下图及其示意图:
下图为上述图片的波形显示图:
基桩超声波检测特殊情况的判定及处理

基桩超声波检测特殊情况的判定及处理常见特殊情况的判定和处理检测数据异常1.管斜:在检测过程中,难免会碰到声测管弯管的情况,管斜对我们的检测结果有较大的影响,容易造成对缺陷的错判或漏判,下面我们来看看管斜如何处理。
如下图所示:直接从波形上观察,感觉该剖面在42米以下存在大范围缺陷。
但通过观察PSD的变化及声速声幅曲线的变化,我们发现,PSD并无强烈变化,且声速声幅呈趋势性渐变,应为声测管偏斜,需进行管斜修正。
在管斜起始位置按住鼠标右键,沿管斜趋势方向拖动,到结束出松开鼠标,在声速曲线附近会标示出一条黑线。
点击顶部菜单的工具栏,点击确认管斜修正。
此时观察右边的深度声速曲线,可以发现已根据刚才的操作进行了管斜修正处理,该剖面42米以下并未存在缺陷。
2.同一根桩,各剖面相差很大:在检测过程中,有时会出现这种情况,举个例子,三管的桩,测完发现,2-3面与1-2 1-3面的声速声幅差距很大。
从一般情况来看,一根桩浇注不太可能出现整桩某个面或某几个面比其它面在波速和波幅上都差别很大的情况,出现此种情况,还是应该检查是否检测中传感器在同一深度,从上图上可以推测,1号管探头与2号3号管不在同一深度。
3. 桩身波速较均匀,但波速偏低,波幅不均匀:在检测过程中,有时会出现这种情况,举个例子,一根桩的波速比较均匀,但是都比正常值偏低。
声幅存在一定的不均匀离散。
如下图:后经过几番询问,才最终了解,此桩检测龄期只有4天,且为水下灌注桩。
由此可见,一定要按照规范要求的时间去进行检测,龄期不够或太短的检测数据,容易造成误判或者漏判。
检测数据分析及判断计算透射法检测数据1、声速计算声时测量分辨力超声波仪器声时测量分辨力(采样间隔),精密测量时仪器的声时测量采样间隔应优于或等于0.5 μs。
若仪器的采样间隔设定大于1.0 μs 时,声时测读精度下降;大于2.0 μs 时,将严重影响对小缺陷的判定能力。
•系统测量误差•它包括仪器测量系统的延迟时间t0、声测管及耦合水层声时修正值t′、两声测管的外壁净距测量引起的相对误差等。
超声波检测中的波形识别

实践经验超声检测中的波形识别与缺陷定性吴德新,杨小林(中国人民解放军空军第一航空学院,信阳 464000)IDENTIFICATION OF WAVEFORMS AN D DEFECTS IN U LTRASONIC INSPECTIONWU De 2xin ,YANG Xiao 2lin(The First Aeronautical Institute of the Chinese PLA Air Force ,Xinyang 464000,China ) 中图分类号:TG 115.28 文献标识码:B 文章编号:100026656(2002)0720312203 超声检测技术中对缺陷评定的三大关键内容是缺陷的定位、定量和定性。
缺陷定位与定量方法已较成熟,而对缺陷定性仍存在许多实际困难。
目前,在原位检测中应用最广泛的是A 型超声脉冲反射式检测仪,根据其示波屏显示的缺陷回波静态波形与动态波形,再结合具体产品或材料特点和制造工艺等来评估缺陷的性质。
缺陷的超声波反射特性取决于缺陷的取向和几何形状、相对超声波传播方向的长度和厚度、缺陷的表面粗糙度、缺陷内含物以及缺陷性质等,还与所用超声检测系统特性有关,因此,超声检测中获得缺陷的超声响应是一个综合响应。
如何观察波形并把反映缺陷性质的有用信息从综合响应中分离出来,这对缺陷的定性评定尤为重要。
1 脉冲干扰噪声的识别与波形分析1.1 脉冲噪声的来源在超声波探伤中,脉冲干扰噪声的来源很广泛。
首先是检测仪器,质量较差的仪器工作时性能不稳定,自身会产生脉冲干扰噪声。
在超声波探伤现场,如果电源的输出不稳定将会干扰检测仪器,引起脉冲噪声。
多种仪器(如探伤仪、示波屏、频谱仪和计算机等)组合或同一地点多台不同检测仪器联机运行(如超声与涡流组合探伤)时,仪器之间也会互相干扰而产生脉冲噪声。
此外,强烈的机械振动与冲击也会导致脉冲干扰噪声的产生[1]。
1.2 脉冲噪声的特征分析(1)偶然性 在超声波探伤中出现的脉冲噪声收稿日期:2001201225无规则可循,不可重复,具有强烈的偶然性。
钢管超声波检测时缺陷波形的识别
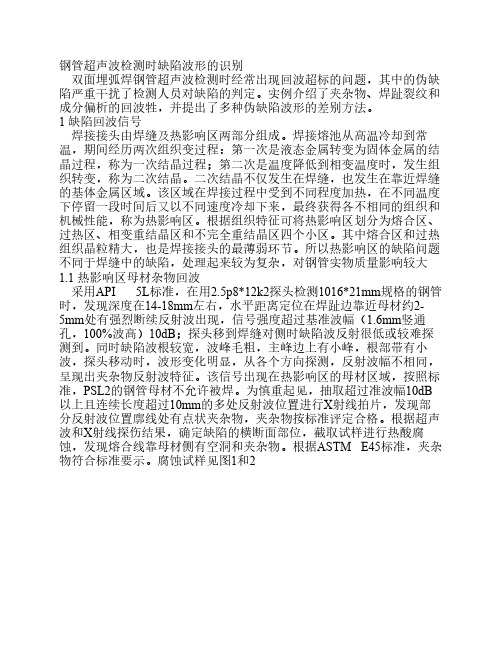
钢管超声波检测时缺陷波形的识别双面埋弧焊钢管超声波检测时经常出现回波超标的问题,其中的伪缺陷严重干扰了检测人员对缺陷的判定。
实例介绍了夹杂物、焊趾裂纹和成分偏析的回波牲,并提出了多种伪缺陷波形的差别方法。
1 缺陷回波信号焊接接头由焊缝及热影响区两部分组成。
焊接熔池从高温冷却到常温,期间经历两次组织变过程:第一次是液态金属转变为固体金属的结晶过程,称为一次结晶过程;第二次是温度降低到相变温度时,发生组织转变,称为二次结晶。
二次结晶不仅发生在焊缝,也发生在靠近焊缝的基体金属区域。
该区域在焊接过程中受到不同程度加热,在不同温度下停留一段时间后又以不同速度冷却下来,最终获得各不相同的组织和机械性能,称为热影响区。
根据组织特征可将热影响区划分为熔合区、过热区、相变重结晶区和不完全重结晶区四个小区。
其中熔合区和过热组织晶粒精大,也是焊接接头的最薄弱环节。
所以热影响区的缺陷问题不同于焊缝中的缺陷,处理起来较为复杂,对钢管实物质量影响较大1.1 热影响区母材杂物回波采用API 5L标准,在用2.5p8*12k2探头检测1016*21mm规格的钢管时,发现深度在14-18mm左右,水平距离定位在焊趾边靠近母材约2-5mm处有强烈断续反射波出现,信号强度超过基准波幅(1.6mm竖通孔,100%波高)10dB;探头移到焊缝对侧时缺陷波反射很低或较难探测到。
同时缺陷波根较宽,波峰毛粗,主峰边上有小峰,根部带有小波,探头移动时,波形变化明显,从各个方向探测,反射波幅不相同,呈现出夹杂物反射波特征。
该信号出现在热影响区的母材区域,按照标准,PSL2的钢管母材不允许被焊。
为慎重起见,抽取超过准波幅10dB 以上且连续长度超过10mm的多处反射波位置进行X射线拍片,发现部分反射波位置廓线处有点状夹杂物,夹杂物按标准评定合格。
根据超声波和X射线探伤结果,确定缺陷的横断面部位,截取试样进行热酸腐蚀,发现熔合线靠母材侧有空洞和夹杂物。
- 1、下载文档前请自行甄别文档内容的完整性,平台不提供额外的编辑、内容补充、找答案等附加服务。
- 2、"仅部分预览"的文档,不可在线预览部分如存在完整性等问题,可反馈申请退款(可完整预览的文档不适用该条件!)。
- 3、如文档侵犯您的权益,请联系客服反馈,我们会尽快为您处理(人工客服工作时间:9:00-18:30)。
实践经验超声检测中的波形识别与缺陷定性吴德新,杨小林(中国人民解放军空军第一航空学院,信阳 464000)IDENTIFICATION OF WAVEFORMS AN D DEFECTS IN U LTRASONIC INSPECTIONWU De 2xin ,YANG Xiao 2lin(The First Aeronautical Institute of the Chinese PLA Air Force ,Xinyang 464000,China ) 中图分类号:TG 115.28 文献标识码:B 文章编号:100026656(2002)0720312203 超声检测技术中对缺陷评定的三大关键内容是缺陷的定位、定量和定性。
缺陷定位与定量方法已较成熟,而对缺陷定性仍存在许多实际困难。
目前,在原位检测中应用最广泛的是A 型超声脉冲反射式检测仪,根据其示波屏显示的缺陷回波静态波形与动态波形,再结合具体产品或材料特点和制造工艺等来评估缺陷的性质。
缺陷的超声波反射特性取决于缺陷的取向和几何形状、相对超声波传播方向的长度和厚度、缺陷的表面粗糙度、缺陷内含物以及缺陷性质等,还与所用超声检测系统特性有关,因此,超声检测中获得缺陷的超声响应是一个综合响应。
如何观察波形并把反映缺陷性质的有用信息从综合响应中分离出来,这对缺陷的定性评定尤为重要。
1 脉冲干扰噪声的识别与波形分析1.1 脉冲噪声的来源在超声波探伤中,脉冲干扰噪声的来源很广泛。
首先是检测仪器,质量较差的仪器工作时性能不稳定,自身会产生脉冲干扰噪声。
在超声波探伤现场,如果电源的输出不稳定将会干扰检测仪器,引起脉冲噪声。
多种仪器(如探伤仪、示波屏、频谱仪和计算机等)组合或同一地点多台不同检测仪器联机运行(如超声与涡流组合探伤)时,仪器之间也会互相干扰而产生脉冲噪声。
此外,强烈的机械振动与冲击也会导致脉冲干扰噪声的产生[1]。
1.2 脉冲噪声的特征分析(1)偶然性 在超声波探伤中出现的脉冲噪声收稿日期:2001201225无规则可循,不可重复,具有强烈的偶然性。
由于脉冲噪声的产生原因多种多样,因此其出现的时间间隔数量、幅度及频率等均随机变化且多种多样。
(2)满幅性 超声波探伤仪示波屏上的脉冲噪声幅度很大,常达饱和状态。
图1为水浸法探伤中出现的电脉冲干扰噪声。
其中S 为工件的界面回波,P 1~P 4为饱和脉冲噪声,n 1和n 2属脉冲噪声,但其来源可能与饱和脉冲噪声不同。
图1 探伤仪示波屏上的脉冲干扰噪声(3)单峰性 超声波探伤中的缺陷回波信号是由多次反射波组成的。
但在实践中发现,示波屏上观察到的波形实质是这些反射波的包络,而脉冲噪声则是孤立的单峰。
因此,各脉冲噪声之间不能形成缺陷波F 那样的包络(图2)。
(4)频率范围广 采用傅里叶变换方法,将超声波探伤信号进行离散化处理,可得到离散频谱x (k )=∑N -1n =0x (n )wkn N 0≤k ≤n -1 将上式用于图1所示的原始信号,可得图3所示的频谱。
由此可见,脉冲噪声频率分布很广,不只是一个中心频率,产生的机理不同,就有不同的中心・213・第24卷第7期2002年7月无损检测ND TVol.24 No.7J uly 2002图2 缺陷回波与脉冲噪声的波形区别图3 图1所示信号的频谱频率与带宽。
2 波型转换噪声干扰的识别超声波在奥氏体不锈钢或其它粗晶材料中传播时,粗大晶粒的界面会使声波发生散射,并引起波型转换,从而在荧光屏上产生杂乱的草状波,称为噪声。
噪声波幅随晶粒尺寸增长而升高。
材料中的缺陷反射波往往会湮没于噪声杂波中而无法分辨,导致细小缺陷的检测受到限制。
噪声电平是衡量晶粒度大小的指标,其测量方法是,首先使增益为最大值,抑制为零位,将声程与被探工件的底面回波达到80%基准波高度,用公式求得工件的噪声电平。
由材料晶粒度的大小判断波形中晶粒散射而产生的波型转换噪声,进而判断草状杂波[2]。
3 不同被检材料中不同缺陷的波形分析3.1 铸钢件铸件内部普遍为不致密枝晶,其结构组织不均匀且晶粒粗大,声波在晶界面和不均匀结构处会产生散射,示波屏上往往产生杂乱无章的丛状回波。
由于铸件形状复杂,往往在示波屏上产生外轮廓直射或迟到回波,使杂波与缺陷波难以分辨。
由于铸件产生缺陷的位置有一定的规律性和重复性,因此可对易产生缺陷的重点部位作针对性探伤。
铸件探伤常用脉冲回波反射法。
工件无缺陷时出现底波次数多,且波幅呈指数衰减,各底波间隔大致相等(图4a );当工件有疏松等缺陷时,散射等因(a )(b )(c )图4 铸件多次脉冲反射法检测波形素使声能衰减而底波反射次数减少(图4b );若工件内部有大面积缺陷(如疏松、夹杂和气孔等)则底波消失,只出现杂波(图4c )。
(1)气孔 有单个、密集和链状等球状或椭圆形气孔,表面光滑。
波形特征是反射波峰高,面陡峭,敏感性强,波峰单一,根部清晰,对底波影响不大。
探头移动时,单个气孔为一个较稳定的单脉冲波(图5a ),链状气孔会产生连续不断的缺陷波(图5b ),密集气孔则为数个缺陷波(图5c )。
(a )(b )(c )图5 气孔波形(2)夹渣 典型特征是带有棱角,回波较弱,不同方位探测回波变化较大。
(3)缩孔 密集缩孔呈树枝状,中心缩孔呈管状。
波形特征是一波多峰,幅度高,对底波有明显影响。
(4)冷裂纹 脆性断口表面较光;塑性断口表面粗糙。
回波特征是回波较高,对底波影响明显,移动探头时波形此起彼伏,变化较大。
3.2 锻钢件(1)残余缩孔 呈连续或断续条状,回波反射较强。
探头移动时多个回波此起彼伏,圆周方向探测均能发现,严重时影响底波。
(2)夹杂 呈连串状,回波呈丛状(图6a ),波幅一般较低,但有一两个较高的波,探头移动时此起彼落,显得杂乱,可与白点缺陷波形(图6b )相比较。
(a )(b )图6 锻件夹杂及白点波形示意图・313・(3)孔性裂纹和冷裂纹 形状是撕裂状断口,脆性较光,塑性较粗糙。
回波呈丛状,底部较宽,波峰清晰有分枝,缺陷波对底波有明显影响。
降低灵敏度,缺陷波下降速度比底波慢。
(4)疏松 疏松对声波有显著吸收和散射作用,使底波显著降低,甚至消失。
严重疏松有时无缺陷波出现,移动探头有时出现波幅很低的不稳定蠕动波形。
提高灵敏度,会出现一些微弱而杂乱的波形,但无底波,其波形特征见图7。
(5)白点 波形往往呈密集形状,白点斑点内有锯齿状小裂纹。
超声波探伤时,在中心部位出现林状波形,其波形显示很清晰,尖锐。
降低灵敏度,缺陷波仍然显得高而清晰。
密集白点对超声波反射影响强烈,对底波影响大,出现在锻件的大截面段,其波形呈根部清晰的林状间波(图8)。
图7 疏松波形图8 白点波形 3.3 轧制钢棒(1)缩孔 冒口端条状分布,多出现在碳结构钢中,对底波有明显影响,圆周方向探测能发现。
(2)内部裂纹 多出现在高速钢中,寒冷季节比高温季节易出现,圆周方向探测波形变化较大,对底波影响明显。
3.4 对接钢焊缝(1)凝固性裂纹 呈星状,出现在焊道的起弧、收弧部位和热影响区,多出现在表面。
(2)冷却裂纹 呈折线状,端部较细,淬硬性好的钢材中易产生,由残余应力偏大和金属内部组织偏硬引起,回波较高,波峰较宽,多峰(图9)。
(a )(b ) 图9 裂纹波形(3)裂纹 (层状撕裂)多产生在尺寸较厚的T型焊缝或角焊缝上,回波特征同上。
(4)未焊透 呈线状或条状,一般在焊缝中部和根部,是垂直于钢板的面状缺陷,波形见图10。
图10 未焊透波形图11 焊缝中的夹渣波形(5)未熔合 包括坡口和层间未熔合,片状缺陷类似裂纹,但表面比裂纹光滑。
探头折射角合适时回波较高,从焊道两侧探时,反射幅度不同。
(6)夹渣 包括点状夹渣(点渣)和条状夹渣(条渣),夹渣带有一定棱角,条渣呈条状连续或断续分布。
点渣回波有方向性,与气孔不同,条渣多呈锯齿状,反射率偏低,根部较宽,好像树枝一样,主干旁边有小枝峰(图11)。
(7)气孔 呈空心球状,单个气孔回波(图12a )幅度不高,波形稳定;密集气孔常出现一簇反射回波(图12b ),从不同方位探测,回波幅度变化不大。
(a )(b ) 图12 气孔波形4 波形信号的判断方法4.1 分布状态判断法分布状态判断法是根据缺陷的分布状态和几何位置判断其性质。
在现役飞机超声检测中,多采用该方法对缺陷进行定性。
白点多出现在锻件大截面段的偏析带上,群集分布。
未焊透必在焊缝的根部。
4.2 回波个数判断法把缺陷分为单个或多个,以便确定其危害程度。
4.3 回波高度判断法最大回波高度可作为判断缺陷性质的依据,如超声波对裂纹较敏感,探测面合适时其回波较高,反射强烈。
铸件中的疏松和锻件中的粗晶不可能有较高回波。
4.4 回波根部判断法根据回波的宽度或其根部特征来对缺陷性质及种类进行判断。
气孔、点渣、白点和脆性断口的冷裂纹根部较干净,铸件上的缩孔、焊缝上的条渣和塑性断口的裂纹则为多峰,根部也带有小波。
(下转第316页)・413・为防止生锈,用宽20mm 、厚2mm 和0.5mm 的不锈钢扁钢,<12mm 不锈钢管,四块20mm ×20mm ×6mm 钢块以及棘轮,小钢丝绳和紧箍。
1.3 构造以<377mm 管为例,探伤专用架形状如图3。
图31.凹槽2.不锈钢管3.棘轮4.钢块取两条厚2mm ,长300mm 扁钢,弯成与<377mm 管外弧相贴切。
取四块20mm ×20mm ×6mm 钢块,中间钻<6mm 孔,垂直焊在扁钢的两端。
为使射线束中心穿过管的圆心并有一定的倾斜角度,根据透照焦距和射线机的大小,按图2和图3在实际钢管上量出垂直不锈钢管的长度,按图3进行焊接,用小钢丝绳和棘轮将探伤架固定在管子上。
取200mm 长扁钢一条,弯成与射线机机身相贴切,焊在与管子平行的两条不锈钢管位置上,另取厚0.5mm 扁钢将射线机机身用紧箍固定在探伤架一端。
制作两个凹槽,焊在另一端的两条不锈钢管上,将射线机底端手柄固定在上面,探伤架制成。
2 应用和局限透照方式采用双壁单影,先划分好焊缝探伤等份,射线机固定在探伤架上,探伤架固定在管子上,射线机窗口的中心对准有效透照范围焊缝中心的对称位置,这时射线束中心就穿过管子的圆心,可以进行透照。
拍完第一张片,松开棘轮,探伤架转动一定角度至另一张拍片位置,拉紧棘轮,使探伤架固定,进行第二次拍照。
用此探伤架对某地供热500多米埋地管线的76道焊缝拍摄500多张片,取得预想的效果。
由于各种规格管子的弧度不一样,所以一个探伤架只适合一种规格的管子,这是该探伤架的局限。
3 结束语用此探伤专用架在大径管焊缝探伤时,透照完一张底片,然后移动到另一个位置进行第二次透照的时间,一般≯3min ,大大节省探伤时间,工作效率得到了提高。