转炉煤气干法净化回收技术
转炉一次烟气干法净化与煤气回收系统设备技术规范-最新国标

转炉一次烟气干法净化与煤气回收系统设备技术规范1 范围本标准规定了转炉一次烟气干法净化与煤气回收系统中主要机械设备的技术规范。
本标准适用于转炉一次烟气干法净化与煤气回收系统主要机械设备的制作、安装、试车及系统排放等功能测试。
2 规范性引用文件下列文件中的内容通过文中的规范性引用而构成本文件必不可少的条款。
其中,注日期的引用文件,仅该日期对应的版本适用于本文件;不注日期的引用文件,其最新版本(包括所有的修改单)适用于本文件。
GB/T 9115 对焊钢制管法兰GB/T 9124 钢制管法兰 技术条件GBT 12221-2005 金属阀门结构长度GB/T 13927 工业阀门 压力试验GB/T 13931 电除尘器性能测试方法GB/T 15605 粉尘防爆、泄压指南GB/T 16845 除尘器GB/T 16157 固定污染源排气中颗粒物测定与气态污染物采样方法GB/T 24917-2010 眼镜阀GB/T 37400.1 重型机械通用技术条件 产品检验GB/T 37400.3 重型机械通用技术条件 焊接件GB/T 37400.10 重型机械通用技术条件 装配GB/T 37400.11 重型机械通用技术条件 配管GB/T 37400.12 重型机械通用技术条件 涂装GB/T 37400.13 重型机械通用技术条件 包装GB/T 40514-2021 电除尘器GB 50231 机械设备安装工程施工及验收通用规范GB 50236 现场设备、工业管道焊接工程施工规范GB 50275 压缩机、风机、泵安装工程施工及验收规范GB/T 50387 冶金机械液压、润滑和气动设备工程安装验收规范GB 51135-2015 转炉煤气净化及回收工程技术规范JB/T 322 环境保护产品技术要求JB/T 8536 电除尘器机械安装技术条件JB/T 5900 电除尘器JB/T 6407 电除尘器调试、运行、维修安全技术规范JB/T 8527-2015 金属密封蝶阀JB/T 11312-2012 转炉煤气干法净化用圆筒型电除器JB/T 12627 转炉煤气干法除尘系统用杯形阀JC/T358--2021 水泥工业用电除尘器YB/T4917-2021 转炉炼钢一次烟气颗粒物测定技术规范3 术语和定义下列术语和定义适用于本文件。
转炉煤气干法LT净化回收技术的应用及防爆措施

转炉煤气干法LT净化回收技术的应用及防爆措施概述炼钢厂在生产过程中会产生大量的转炉煤气,其中含有大量的有害物质,如一氧化碳、二氧化碳等,对环境造成威胁。
为了减少煤气对环境的影响,炼钢厂引入了转炉煤气干法LT净化回收技术。
技术原理转炉煤气干法LT净化回收技术是一种先将煤气进行除尘、水分脱除等处理后,采用催化剂进行低温净化,在净化完成后再进行回收利用的技术。
该技术的主要原理是:将煤气进行过滤处理,去除其中的杂质和水分,再通过特制的催化剂进行净化处理,使其中的有毒有害物质转化为无害化合物,最后再将净化后得到的煤气进行回收利用。
此种净化方式是比传统的高温净化的方式更加环保,且更加节能。
应用情况转炉煤气干法LT净化回收技术目前已经在国内多家炼钢厂得到了广泛应用,其净化效果得到了良好的验证。
它不仅可以降低污染排放,而且可以提高资源利用率,收益显著。
在使用过程中,需要做好相关的防爆措施,以确保工作安全。
防爆措施作为一种较为安全的净化方式,转炉煤气干法LT净化回收技术在实际使用过程中也需要做好相应的防爆措施。
具体可采取以下措施:1.操作人员必须接受专业的培训,熟练掌握操作技能及相关安全规范。
2.对设备进行定期检查维护,确保设备处于良好的工作状态,减少设备故障以及为防止事故的发生留下隐患。
3.在压力较高的部位加装爆炸防护装置,防止在操作过程中因煤气燃爆出现安全事故。
4.注意防火措施,在操作现场设立消防设施,在操作过程中严格控制火源,尽可能避免火花等潜在火源的出现。
通过加强设备维修保养,并加强操作人员的安全意识,可帮助工作人员避免由于设备故障或操作不当导致的事故发生。
结论转炉煤气干法LT净化回收技术是一种环保且高效的煤气净化方式,已经在国内多家炼钢厂得到了操纵和推广。
在此技术的应用过程中,我们需要加强设备维修保养,注重安全教育培训,在操作现场设立消防设备,注意防火措施等,可实现安全可靠的运转。
虽然转炉煤气干法LT技术已经得到了广泛应用,但我们还需要进行更深入的研究以优化该技术,并进一步推广和应用。
转炉干法除尘系统煤气回收的分析与研究

转炉干法除尘系统煤气回收的分析与研究随着经济和社会的发展,钢铁生产已经成为许多国家不可或缺的行业之一。
炼钢过程中,转炉炼钢是一个非常重要的工艺流程。
然而,炼钢过程中释放出大量的烟尘和废气,给环境造成了很大的污染。
因此,对炼钢生产过程中的污染治理工作是非常重要的。
本文将对转炉干法除尘系统煤气回收的分析与研究进行探讨。
一、转炉干法除尘系统的原理在炼钢废气治理中,转炉干法除尘系统是一种常用的治理方法。
该系统的主要原理是利用机械力和离心力将煤气中的粉尘和颗粒物脱除出来。
该系统通常由除尘器、旋风分离器、旋转式喷淋器、出水口等部分组成。
其主体部分是除尘器,其工作原理如下:废气从除尘器的进气管进入除尘器内部,在进入过程中经过了预处理段的净化。
落下的颗粒物通过旋风分离系统,沉下到料斗中。
此时废气已经分离了一定量的颗粒物,在旋风分离器内,煤气受到离心作用,使其速度降低,并将其中的颗粒物和粉尘分离出来。
随后,煤气流入旋转式唧筒中。
在这里,水通过压力喷嘴和旋转式喷淋器进行喷淋,与废气发生接触,使煤气中的颗粒物和粉尘被溶解并冲入水面中。
在煤气净化的过程中收集的毒物也被波浪冲走。
最后,净化后的废气通过排气管排放或再利用。
整个除尘系统的操作过程大大降低了煤气中污染物的浓度,达到了保护环境和节约能源的效果。
1、处理效率高:煤气经过除尘器的物理吸附、静电吸附与旋风分离,将微小的颗粒粉尘从煤气中分离出来,使其浓度和体积大大降低,达到高效的净化效果。
2、应用广泛:该系统不仅适用于钢铁、建筑等重工业中的烟雾净化,还适用于煤矿,化工等其他制造业中的废气净化。
3、维护简单:转炉干法除尘系统的维护操作相对比较简单,易于维护。
4、技术成熟:该系统的技术已经相对成熟,大部分钢铁企业已经普及了该除尘系统,也具备了一定的经济效益。
三、煤气回收技术的分析在钢铁生产中,煤气是非常宝贵的资源。
随着技术的不断革新,将废气回收并再利用,已成为炼钢业的一种新技术。
科技成果——转炉煤气干法回收技术
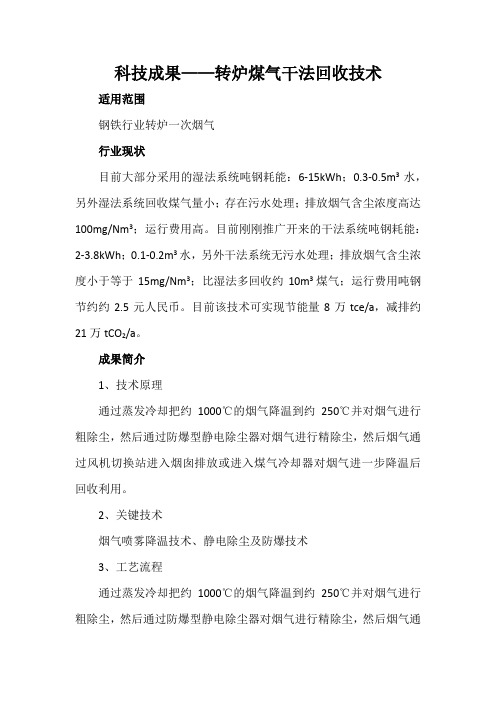
科技成果——转炉煤气干法回收技术适用范围钢铁行业转炉一次烟气行业现状目前大部分采用的湿法系统吨钢耗能:6-15kWh;0.3-0.5m3水,另外湿法系统回收煤气量小;存在污水处理;排放烟气含尘浓度高达100mg/Nm3;运行费用高。
目前刚刚推广开来的干法系统吨钢耗能:2-3.8kWh;0.1-0.2m3水,另外干法系统无污水处理;排放烟气含尘浓度小于等于15mg/Nm3;比湿法多回收约10m3煤气;运行费用吨钢节约约2.5元人民币。
目前该技术可实现节能量8万tce/a,减排约21万tCO2/a。
成果简介1、技术原理通过蒸发冷却把约1000℃的烟气降温到约250℃并对烟气进行粗除尘,然后通过防爆型静电除尘器对烟气进行精除尘,然后烟气通过风机切换站进入烟囱排放或进入煤气冷却器对烟气进一步降温后回收利用。
2、关键技术烟气喷雾降温技术、静电除尘及防爆技术3、工艺流程通过蒸发冷却把约1000℃的烟气降温到约250℃并对烟气进行粗除尘,然后通过防爆型静电除尘器对烟气进行精除尘,然后烟气通过风机切换站进入烟囱排放或进入煤气冷却器对烟气进一步降温后回收利用。
工艺流程见图1所示。
图1 工艺流程图主要技术指标1、放散烟气含尘量小于15mg/Nm3;2、回收煤气含尘量小于10mg/Nm3。
技术水平该技术与传统湿法技术相比即节能又环保,被认定为转炉一次烟气处理的发展方向,目前已得到了广泛应用,共计约100多套。
典型案例典型案例1:信钢建设规模:3台65t转炉;技改内容:信钢为新建3套65t转炉配套3套转炉一次烟气干法净化回收系统;主要设备:蒸发冷却器、静电除尘器、风机、切换站煤气冷却器及烟囱等。
节能技改投资额约5300万,建设期约24个月,节能量:与传统湿法相比吨钢节能约5kgce。
年节能经济效益不低于1200万元,投资回收期不到5年。
典型案例2:攀钢建设规模:3台220t转炉;技改内容:攀钢西昌为新建3套220t炼钢转炉配套3套转炉一次烟气干法净化回收系统;主要设备:蒸发冷却器、静电除尘器、风机、切换站煤气冷却器及烟囱等。
转炉煤气干法净化回收技术应用及防爆措施

转炉煤气干法净化回收技术应用及防爆措施引言随着工业化进程的加速,煤炭等化石能源的使用量也在不断增加。
然而,煤气作为燃料,在燃烧过程中产生的废气中含有大量的有害物质,对环境和人体健康造成了严重的危害。
因此,净化和回收转炉煤气成为了一项重要的任务。
本文将介绍转炉煤气干法净化回收技术的应用和相关的防爆措施。
转炉煤气干法净化回收技术的原理转炉煤气干法净化回收技术是通过一系列的物理和化学过程,将转炉煤气中的有害物质去除,并回收其中的燃料成分。
主要的净化过程包括吸附、过滤和冷凝等。
吸附过程吸附是将废气中的有害物质吸附到吸附剂表面上的过程。
常用的吸附剂有活性炭和分子筛等。
当煤气通过吸附床时,有害物质会被吸附剂吸附,并在其表面积聚。
吸附剂可以重复使用,只需要定期进行再生处理,将吸附在上面的有害物质去除。
过滤过程过滤是利用滤料的孔隙、表面和作用力等原理,将煤气中的颗粒物、微粒和液滴等固体和液体物质从气体中分离的过程。
常用的过滤材料有陶瓷滤板、玻璃纤维滤料等。
过滤过程可以有效地去除煤气中的颗粒物,提高其净化效果。
冷凝过程冷凝是通过降低煤气温度,使其中的水蒸气和有机物质凝结成液体,从而将其分离出来。
冷凝过程常用的设备有冷却器和冷凝器等。
通过控制冷凝温度和冷凝速度,可以有效地去除煤气中的水分和有机物质。
转炉煤气干法净化回收技术的应用转炉煤气干法净化回收技术在钢铁、化工、电力等行业都有广泛的应用。
钢铁行业在钢铁生产过程中,转炉煤气是一种重要的燃料和能源,同时也是高浓度有害物质的主要来源。
通过应用转炉煤气干法净化回收技术,可以将转炉煤气中的有害物质净化去除,提高环境保护和生产效率。
化工行业在化工生产过程中,转炉煤气是一种重要的燃料和原料。
然而,转炉煤气中含有大量的有机物质和硫化物等有害物质,对生产设备和环境造成了严重的腐蚀和污染。
通过应用转炉煤气干法净化回收技术,可以将转炉煤气中的有害物质净化去除,提高生产安全和产品质量。
转炉干法除尘系统煤气回收的分析与研究
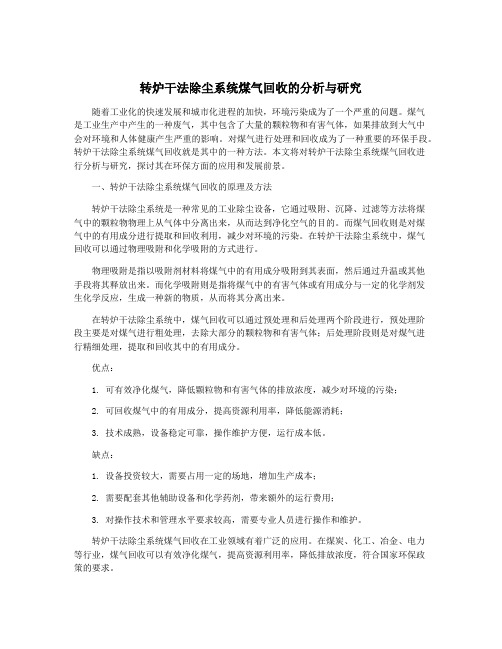
转炉干法除尘系统煤气回收的分析与研究随着工业化的快速发展和城市化进程的加快,环境污染成为了一个严重的问题。
煤气是工业生产中产生的一种废气,其中包含了大量的颗粒物和有害气体,如果排放到大气中会对环境和人体健康产生严重的影响。
对煤气进行处理和回收成为了一种重要的环保手段。
转炉干法除尘系统煤气回收就是其中的一种方法。
本文将对转炉干法除尘系统煤气回收进行分析与研究,探讨其在环保方面的应用和发展前景。
一、转炉干法除尘系统煤气回收的原理及方法转炉干法除尘系统是一种常见的工业除尘设备,它通过吸附、沉降、过滤等方法将煤气中的颗粒物物理上从气体中分离出来,从而达到净化空气的目的。
而煤气回收则是对煤气中的有用成分进行提取和回收利用,减少对环境的污染。
在转炉干法除尘系统中,煤气回收可以通过物理吸附和化学吸附的方式进行。
物理吸附是指以吸附剂材料将煤气中的有用成分吸附到其表面,然后通过升温或其他手段将其释放出来。
而化学吸附则是指将煤气中的有害气体或有用成分与一定的化学剂发生化学反应,生成一种新的物质,从而将其分离出来。
在转炉干法除尘系统中,煤气回收可以通过预处理和后处理两个阶段进行,预处理阶段主要是对煤气进行粗处理,去除大部分的颗粒物和有害气体;后处理阶段则是对煤气进行精细处理,提取和回收其中的有用成分。
优点:1. 可有效净化煤气,降低颗粒物和有害气体的排放浓度,减少对环境的污染;2. 可回收煤气中的有用成分,提高资源利用率,降低能源消耗;3. 技术成熟,设备稳定可靠,操作维护方便,运行成本低。
缺点:1. 设备投资较大,需要占用一定的场地,增加生产成本;2. 需要配套其他辅助设备和化学药剂,带来额外的运行费用;3. 对操作技术和管理水平要求较高,需要专业人员进行操作和维护。
转炉干法除尘系统煤气回收在工业领域有着广泛的应用。
在煤炭、化工、冶金、电力等行业,煤气回收可以有效净化煤气,提高资源利用率,降低排放浓度,符合国家环保政策的要求。
转炉煤气干法(LT)净化回收技术在转炉的应用
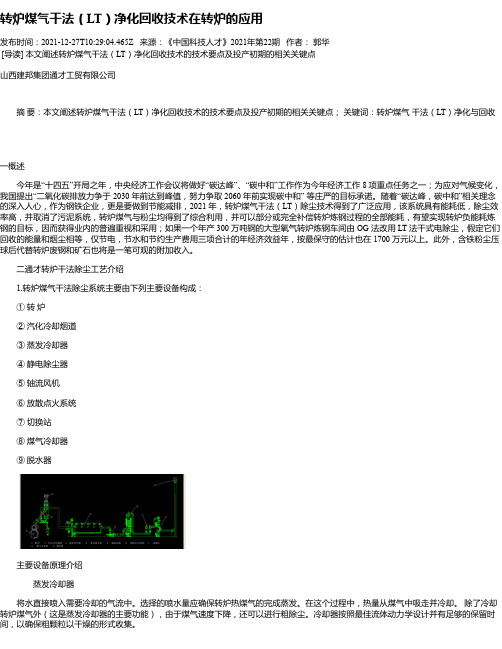
转炉煤气干法(LT)净化回收技术在转炉的应用发布时间:2021-12-27T10:29:04.465Z 来源:《中国科技人才》2021年第22期作者:郭华[导读] 本文阐述转炉煤气干法(LT)净化回收技术的技术要点及投产初期的相关关键点山西建邦集团通才工贸有限公司摘要:本文阐述转炉煤气干法(LT)净化回收技术的技术要点及投产初期的相关关键点;关键词:转炉煤气干法(LT)净化与回收一概述今年是“十四五”开局之年,中央经济工作会议将做好“碳达峰”、“碳中和”工作作为今年经济工作 8 项重点任务之一;为应对气候变化,我国提出“二氧化碳排放力争于 2030 年前达到峰值,努力争取 2060 年前实现碳中和” 等庄严的目标承诺。
随着“碳达峰,碳中和”相关理念的深入人心,作为钢铁企业,更是要做到节能减排,2021 年,转炉煤气干法(LT)除尘技术得到了广泛应用,该系统具有能耗低,除尘效率高,并取消了污泥系统,转炉煤气与粉尘均得到了综合利用,并可以部分或完全补偿转炉炼钢过程的全部能耗,有望实现转炉负能耗炼钢的目标,因而获得业内的普遍重视和采用;如果一个年产 300 万吨钢的大型氧气转炉炼钢车间由 OG 法改用 LT 法干式电除尘,假定它们回收的能量和烟尘相等,仅节电,节水和节约生产费用三项合计的年经济效益年,按最保守的估计也在 1700 万元以上。
此外,含铁粉尘压球后代替转炉废钢和矿石也将是一笔可观的附加收入。
二通才转炉干法除尘工艺介绍1.转炉煤气干法除尘系统主要由下列主要设备构成:①转炉②汽化冷却烟道③蒸发冷却器④静电除尘器⑤轴流风机⑥放散点火系统⑦切换站⑧煤气冷却器⑨脱水器主要设备原理介绍蒸发冷却器将水直接喷入需要冷却的气流中。
选择的喷水量应确保转炉热煤气的完成蒸发。
在这个过程中,热量从煤气中吸走并冷却。
除了冷却转炉煤气外(这是蒸发冷却器的主要功能),由于煤气速度下降,还可以进行粗除尘。
冷却器按照最佳流体动力学设计并有足够的保留时间,以确保粗颗粒以干燥的形式收集。
转炉干法除尘系统煤气回收的分析与研究
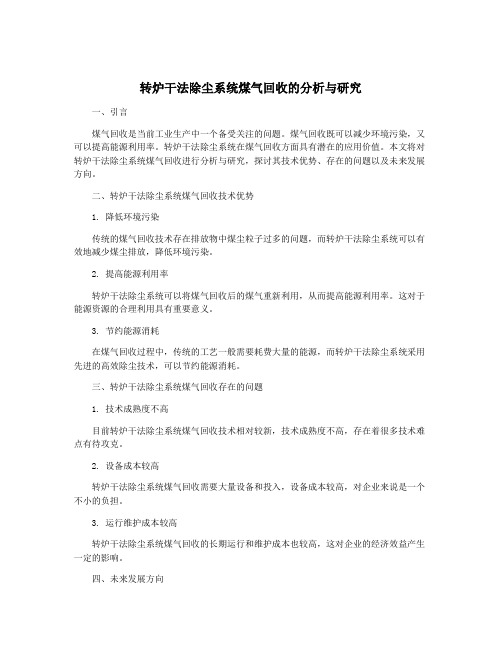
转炉干法除尘系统煤气回收的分析与研究一、引言煤气回收是当前工业生产中一个备受关注的问题。
煤气回收既可以减少环境污染,又可以提高能源利用率。
转炉干法除尘系统在煤气回收方面具有潜在的应用价值。
本文将对转炉干法除尘系统煤气回收进行分析与研究,探讨其技术优势、存在的问题以及未来发展方向。
二、转炉干法除尘系统煤气回收技术优势1. 降低环境污染传统的煤气回收技术存在排放物中煤尘粒子过多的问题,而转炉干法除尘系统可以有效地减少煤尘排放,降低环境污染。
2. 提高能源利用率转炉干法除尘系统可以将煤气回收后的煤气重新利用,从而提高能源利用率。
这对于能源资源的合理利用具有重要意义。
3. 节约能源消耗在煤气回收过程中,传统的工艺一般需要耗费大量的能源,而转炉干法除尘系统采用先进的高效除尘技术,可以节约能源消耗。
三、转炉干法除尘系统煤气回收存在的问题1. 技术成熟度不高目前转炉干法除尘系统煤气回收技术相对较新,技术成熟度不高,存在着很多技术难点有待攻克。
2. 设备成本较高转炉干法除尘系统煤气回收需要大量设备和投入,设备成本较高,对企业来说是一个不小的负担。
3. 运行维护成本较高转炉干法除尘系统煤气回收的长期运行和维护成本也较高,这对企业的经济效益产生一定的影响。
四、未来发展方向1. 技术研究与创新针对转炉干法除尘系统煤气回收存在的问题,需要加大技术研究与创新,解决技术难题,提高技术成熟度。
2. 降低成本可以通过技术改进和设备优化的方式,降低转炉干法除尘系统煤气回收的设备成本和运行维护成本。
3. 政策支持政府可以出台相关政策,给予企业一定的补贴和支持,鼓励企业积极推进转炉干法除尘系统煤气回收的应用。
四、结论转炉干法除尘系统煤气回收具有一定的应用前景和发展潜力,但目前仍存在一些问题和难点需要克服。
通过技术创新、成本降低、政策支持等方面的努力,未来转炉干法除尘系统煤气回收技术将得到进一步发展和推广。
企业也应该关注煤气回收技术的发展趋势,积极应对市场变化,抓住机遇,推动技术升级,提高企业竞争力。
- 1、下载文档前请自行甄别文档内容的完整性,平台不提供额外的编辑、内容补充、找答案等附加服务。
- 2、"仅部分预览"的文档,不可在线预览部分如存在完整性等问题,可反馈申请退款(可完整预览的文档不适用该条件!)。
- 3、如文档侵犯您的权益,请联系客服反馈,我们会尽快为您处理(人工客服工作时间:9:00-18:30)。
转炉煤气干法(LT)净化回收技术的国产化应用我国现有600多座转炉,年产钢超过4亿吨,节能减排潜力巨大。
目前我国绝大多数转炉的转炉煤气净化采用较为落后的湿法(以下简称老OG)除尘,耗水耗电量大,是钢铁工业节能减排的薄弱环节。
除了老OG除尘之外,近年来我国新建转炉采用了第四代湿法(以下简称新OG法),以及引进的千法(以下简称LT法):使转炉煤气净化技术取得了突破性进展。
在转炉煤气净化技术引进的同时,国内多家设计研究单位进行了吸收开发,目前转炉煤气净化的LT法、新OG法除引进少量关键技术和部件,大量的设备设计、系统设计立足于国内,甚至新OG法基本实现全国产化。
对我国转炉炼钢节能减排、实现负能炼钢起到了积极的推动作用。
但是我们仍清醒看到,转炉煤气净化发展到今天,这些技术包括引进技术都不同程度的存在一些问题、或有值得改之处,这是我国钢铁工业节能减排要追求和持续研究的新目标和新课题。
正是由于目前各种除尘方式的利弊所在,使新建转炉除尘设计选择LT法还是新OG法似乎难以确定。
本文就两种除尘方式进行比较,提出自己的建议。
1.国内外转炉烟气除尘技术的发展和现状当前,转炉烟气净化及煤气回收技术主要有两大类型:即日本的湿法系统(OG法)和德国的干法系统(LT法)。
1.1 湿法系统图1 OG法工艺流程OG法是以双级文氏管为主,抑制空气从转炉炉口流入,使转炉煤气保持不燃烧状态,经过冷却而回收的方法,因此也叫未燃法,又称湿法。
在湿法方面,日本从60年代起开发了OG法,这是世界上普遍采用的流程。
1962年,日本新日铁公司的转炉首次成功地应用该法对转炉烟气进行除尘并回收,合理地利用废气中的化学能和显能及含铁粉尘。
目前己成为世界上最广泛采用的转炉烟气处理方法,在保护环境、回收能源方面发挥了积极作用。
OG法装置主要由烟气冷却系统、烟气净化系统及附属设备组成(见图1)。
在冶炼中生成高一氧化碳浓度且含150~200mg/m3粉尘的煤气,温度达1600℃。
在风机吸力作用下,煤气从活动烟罩进入全封闭的回收系统,经汽化冷却烟道后温度降至1000℃。
一级文氏管进行粗除尘和煤气降温、灭火,温度降至75℃;随之煤气经重力脱水器脱水后再进入二级文氏管进行精除尘和再冷却,温度降至65℃左右,含尘量降至150mg/m3以下,煤气再度脱水后进入除尘风机。
煤气借风机出口正压力、通过三通阀切换,当煤气CO<30%时,送入烟囱,燃烧后排放;当CO>30%时,进入煤气柜回收,再供给用户作能源使用。
1985年,宝钢一期300t转炉成功引进了日本“OG”技术和设备,国内在立足自主开发的基础上对这项技术进行了消化吸收,使“OG”法技术在国内得到了较快的发展而占据主要地位,并取得了成熟的经验。
其核心是二级可调文氏管喉口。
但这种流程也有缺点,如设备单元多、系统阻力损失大、RD喉口易堵塞等。
武钢三炼钢250t转炉OG系统,引进了西班牙TR 公司技术,该系统是将两级文氏管及脱水器串联重组安装在一个塔体内,烟气自上而下运行,总阻力损失仅为18kPa,且流程系统紧凑、简洁、易于维护管理。
1998年,作为环保示范项目,日本政府在马钢三炼钢厂70t转炉扩容改造项目中向马钢无偿提供了一套新型“OG”法除尘技术和设备。
这项技术对传统的“OG”法进行了技术改进,将二文RD可调喉口改为重铊式,即环缝洗涤器(简称RSW),还用饱和器代替了一文喉口。
烟气首先进入饱和器,然后经过二文RSW和下部弯头脱水器到风机系统,被称新型“OG”法。
该技术流程简洁、单元设备少、阻损小。
二文采用RSW技术,除尘效率高,易于控制,且不易堵塞。
除尘效果保证值≤50mg/m3。
目前在柳钢转炉、太钢转炉、济钢转炉上采用,取得初步经验。
OG法具有技术成熟、可靠性好、一次投资少、吨钢煤气回收量高、投资回收期短、设备国产率高及安装工程量少等优势。
OG法除尘系统虽然日趋完善,但是仍存在一些问题,如:供排水系统和净化设备的积灰堵塞问题,部分设备受含尘污水的冲刷磨损问题,污泥的脱水处理问题以及由上述问题引起的维修工作量增加问题。
此外,由于OG法属“高压流程”,系统阻力损失大,除尘供水量大,风机、水泵的耗电量大,因而增加了运行费用。
1.2 干法系统图 2 LT法流程LT称为干式净化回收法,又称干法。
60年代后期,西德鲁奇公司开发了LT法,至80年代技术上已日趋完善。
目前,LT法已有逐渐取代OG法的趋势。
LT法工艺流程如下:转炉烟气出炉口后,通过活动烟罩、固定烟罩进入汽化冷却烟道。
炉气出口温度为1700℃,汽化冷却烟道出口为800~1000℃。
蒸发冷却器有两个作用,一是将烟气温度降至180~200℃;二是对烟气进行增湿调质,以降低烟尘的比电阻,确保电除尘器的除尘效果。
然后进入圆形静电除尘器,烟气轴向进入其中,并通过气流分布板均匀分布在横截面上,烟气得到净化。
静电除尘器一般设有三到四个电场,采用专门的变电系统供电,在电除尘器下部的集灰,用扇形刮灰器刮到位于其下部的链式输送机中,送入中间料仓,然后通过气力输送系统再将干灰送到压块系统的集尘料仓中。
除尘效率高达99%,烟气经过电除尘器后进入除尘风机。
煤气借风机出口正压力、通过三通阀切换,进行回收或放散。
回收柜前设置二次冷却塔使煤气温度降至50℃左右。
流程如图2。
1995年宝山钢铁公司三期工程的转炉煤气净化系统为全套引进的德国LT技术,总投资4060多万美元,处理风量175000m3/h,原始含尘浓度70g/m3,出口含尘浓度<10mg/m3。
LT法目前在德国、法国、奥地利、澳大利亚等国有较为广泛的应用。
相比较而言,LT法具有以下优点:用电场除尘,除尘效率高达99%;省去庞大的循环水系统;回收的粉尘压块可返回转炉代替铁矿石利用;系统阻力损失小。
LT法虽然比OG法有许多优势,但是,经过国内几十年的运行,LT法的问题也逐渐凸显出来。
主要问题有:(1)国内尚不掌握此项技术,需引进国外技术和设备,投资造价高;(2)自动控制连锁多,要求自动化程度高,故障率高,维修时间长;(3)由于蒸发冷却使煤气中含有较高的水分,易形成结露,影响极间距和运行电压,还影响输灰系统设备运行寿命;(4)系统泄爆频繁,影响电除尘器内部件的寿命和除尘效果;出口粉尘浓度不能稳定在设计的10mg/m3;(5)烟气800~1000℃以下余热未回收,除尘后高温煤气热能浪费。
2.新型转炉煤气净化回收2.1 双层滤料床过滤除尘器图3 双层颗粒床除尘原理杨国华研究发明了双层滤料床(图3),该过滤床由上粗下细、上轻下重的双层滤料组成(下层滤料选用石英砂,粒径为015~1mm,堆积密度约1300kg/m3;上层滤料选用普通膨胀珍珠岩颗粒,粒径为2~5mm,是下层滤料砂的4~5倍,堆积密度约70kg/m3,为下层滤料砂的近1/20)。
过滤时,含尘气体自上而下穿过滤层,先经过粗颗粒的上层滤料层,进行第一级过滤,称为粗除尘,截留气体中的绝大部分粉尘,膨胀珍珠岩层为深层过滤,双层滤料过滤床容尘量将远远超过单层沙床;再经过细粒径的下层滤料层,进行第二级过滤,称为精除尘,截获漏过上滤层的微细粉尘,细沙层为表面过滤,是双层滤料床高过滤效率的主要贡献者。
其除尘效率高达99199%,容尘量也达到28163kg/m2。
反吹清灰时,反吹气自下而上通过滤层,由于上层滤料颗粒密度小于下层滤料正常流化时所形成的流化床床层密度,且有足够的密度差,因此,流化时,上层滤料颗粒始终悬浮于下层滤料层之上,形成不相混分层流化床。
清灰结束后,上下两层滤料界面清晰,互不相混,双层滤料层结构保持不变。
该项技术是对不等密度双组份颗粒流化床技术的创新性应用,已取得国家专利。
该项技术对粉尘的过滤效率高,容尘量大,而且对细小颗粒的过滤效率也比较好,对粉尘的成分不敏感。
双层滤料除尘器耐高温而且系统阻力损失小。
2.2 转炉煤气的净化回收和余热利用新工艺图4 转炉煤气净化回收及余热利用系统整个新工艺系统可分为过滤除尘系统、余热利用系统和煤气回收系统三部分(如图4)。
除尘器内壳体采用耐1000℃高温的耐热钢材料制成。
从汽化冷却烟道引来的高温烟气,进入颗粒床过滤器,在颗粒床过滤器内,含尘烟气从上往下经过双层颗粒床除尘器得到净化,经由洁净气出口管排出,进入余热回收装置。
清灰时高压空气自下而上穿过双层颗粒床,颗粒床流化而使粉尘脱落,脱落的粉尘被氮气吹扫带出。
在整个系统开始运行、运行间隙及运行结束时,对煤气除尘和余热回收系统进行氮气吹扫。
反吹阀门的开关由专门的PLC控制,反吹阀门与相应的洁净煤气出口阀自动控制连锁,当某一床层的反吹阀门打开的同时,相应的洁净煤气出口阀门关闭,高压氮气反吹气流对床层进行反吹。
气流自下而上穿过双层颗粒床,颗粒床流化而使粉尘脱落。
脱落的粉尘由于重力作用自然沉降到除尘器底部。
反吹次序、反吹时间和反吹间隔时间由PLC自动控制。
转炉烟气中,绝大部分是CO。
CO是有毒、易燃易爆气体。
为人员和设备的安全考虑,系统运行前和结束后要进行N2吹扫,在卸灰机构和浓度测试点设N2封和N2吹扫设施。
3.结语围绕新型双层滤料除尘器,近年来做了不少从理论到现场试验的工作,其中在江阴鑫裕2×13t熔铝炉的除尘器运行良好,江阴海虹6×15t熔铝炉的除尘器也已经投入使用。
实测数据显示,新型除尘器过滤效率高、容尘量大、压降小,而且所需原料耐高温、价格低廉,为双层滤料除尘器能够全干法处理炼钢转炉烟气,提供了理论和实践经验。
新工艺除尘后可以采用余热利用系统回收800~1000℃烟气的余热,实现全干法除尘,节约水资源,提高余热回收率,可解决当前炼钢转炉烟气除尘面临的难题。
国家已将节能减排,改善环境提升到关系全局的战略高度,强调所有民众要有认清其极端的重要性和紧迫感,而冶金节能减排是治理之重点,消化了国外先进技术,自主研发创新,提升我国节能环保的技术装备水平,是冶金科技工作者的历史责任。
一.概述氧气转炉炼钢采用吹氧冶炼,在吹炼过程中,其烟气量烟气成份和烟气温度随冶炼阶段呈周期性变化。
同时在吹炼过程中,会产生大量烟尘和CO气体,特别在吹炼中期CO浓度可达80%以上,一般情况下,转炉煤气成份中CO的含量占55~66%(体积百分比),其烟尘成份中金属铁占13%,FeO占68.4%,Fe2O3占6.8%,当CO含量在60%左右时,其热值可达8000KJ/Nm3,而烟尘量一般为10~20kg/t钢。
从中可以看出,在氧气转炉炼钢中,转炉煤气中CO含量很高,烟尘中铁含量也很高,因此都有很高的回收利用价值。
通过转炉煤气的回收,不仅可以节约大量能源,而且对烟尘加以综合利用,变废为宝,同时又净化了大气环境。
●国内外概况和发展趋势随着氧气转炉炼钢生产的发展,炼钢工艺的日趋完善,相应的除尘技术也在不断地发展完善。