精益生产之基本概念
精益生产简介及六西格玛基本概念
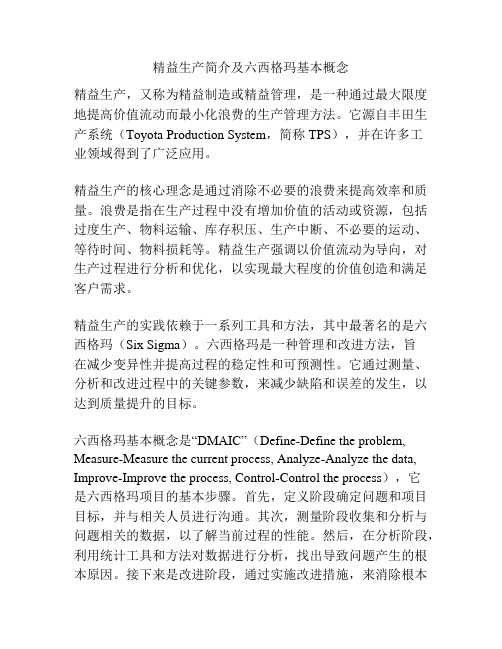
精益生产简介及六西格玛基本概念精益生产,又称为精益制造或精益管理,是一种通过最大限度地提高价值流动而最小化浪费的生产管理方法。
它源自丰田生产系统(Toyota Production System,简称TPS),并在许多工业领域得到了广泛应用。
精益生产的核心理念是通过消除不必要的浪费来提高效率和质量。
浪费是指在生产过程中没有增加价值的活动或资源,包括过度生产、物料运输、库存积压、生产中断、不必要的运动、等待时间、物料损耗等。
精益生产强调以价值流动为导向,对生产过程进行分析和优化,以实现最大程度的价值创造和满足客户需求。
精益生产的实践依赖于一系列工具和方法,其中最著名的是六西格玛(Six Sigma)。
六西格玛是一种管理和改进方法,旨在减少变异性并提高过程的稳定性和可预测性。
它通过测量、分析和改进过程中的关键参数,来减少缺陷和误差的发生,以达到质量提升的目标。
六西格玛基本概念是“DMAIC”(Define-Define the problem, Measure-Measure the current process, Analyze-Analyze the data, Improve-Improve the process, Control-Control the process),它是六西格玛项目的基本步骤。
首先,定义阶段确定问题和项目目标,并与相关人员进行沟通。
其次,测量阶段收集和分析与问题相关的数据,以了解当前过程的性能。
然后,在分析阶段,利用统计工具和方法对数据进行分析,找出导致问题产生的根本原因。
接下来是改进阶段,通过实施改进措施,来消除根本原因并改善过程表现。
最后,在控制阶段,确保改进持久化,并制定适当的监控和控制措施,以防止问题再次出现。
总之,精益生产是一种以消除浪费、提高质量和效率为目标的生产管理方法。
它借鉴了丰田生产系统的经验,并结合了六西格玛等管理工具和方法。
通过精益生产的实践,企业可以提高竞争力、满足客户需求,并实现持续的改进和创新。
精益生产基本概念介绍

精益生产基本概念介绍精益生产是一种以提高效率和降低浪费为核心的生产管理理念,旨在通过优化生产流程,满足客户需求,提高产品质量并降低成本。
精益生产最初由日本的丰田汽车公司引入并得到广泛应用。
它起源于日本的“丰田生产方式”(Toyota Production System,简称TPS),并得到了美国的“精益生产”(Lean Manufacturing)概念的发展和完善。
精益生产的核心理念是通过消除无效的活动和浪费来提高生产效率,以满足客户需求。
这种管理思想可以应用于各种生产领域,包括制造业、服务业、医疗保健等。
精益生产的基本概念包括以下几个方面:1. 价值:精益生产强调以客户价值为导向,将每个生产活动的价值与客户的需求联系起来。
只有在客户眼中具有价值的活动才是有意义的,其余的活动被视为浪费。
2. 浪费:精益生产关注浪费的问题,并试图消除它们。
七大浪费(Overproduction/超产、Waiting/等待、Transportation/运输、Overprocessing/超加工、Inventory/库存、Motion/移动、Defects/缺陷)被认为是造成资源浪费的主要原因。
3. 价值流:精益生产强调要了解和优化整个价值流程。
价值流程是指将原材料转化为最终产品的所有步骤和流程。
通过深入了解价值流,可以识别出浪费并采取相应的措施。
4. 拉动生产:精益生产提倡拉动生产,即根据客户需求进行生产,而不是根据内部生产能力。
拉动生产要求在生产单元间建立稳定的信号和流程,以确保在需要时引导和控制生产。
5. 持续改善:精益生产鼓励持续改进,通过定期检查生产流程和解决问题,以优化效率和质量。
持续改进是精益生产的核心原则之一,要求全员参与,持续提高生产效率和质量。
总之,精益生产是一种追求高效、高质量的生产管理理念。
它关注客户价值、消除浪费、优化价值流程,通过拉动生产和持续改善来实现最佳效果。
精益生产的理念和方法可以帮助企业提高竞争力,并在不断变化的市场环境中保持持续增长。
精益生产的概念及特点分析

精益生产的概念及特点分析引言精益生产是一种以节约资源、增加价值为中心的生产管理理念,起源于日本汽车业。
它通过最小化浪费和提高效率,实现了生产过程的优化和产品质量的提升。
本文将介绍精益生产的概念,并分析其特点。
一、精益生产的概念精益生产(Lean Production)是一种通过消除浪费、提高效率和灵活性的生产方式。
它最早由日本丰田汽车公司开发和实践,并得到广泛推广和应用。
精益生产的核心理念是尽量减少浪费,提高价值创造,从而实现成本降低和效率提高。
它通过减少库存、减少不必要的活动和流程、优化资源使用等方式,确保生产过程能够快速、高效地运转。
二、精益生产的特点1.去除浪费:精益生产强调去除各种形式的浪费,包括等待时间、过程中的缺陷、运输和库存的浪费等。
通过识别和消除浪费,企业能够大幅度提高生产效率和产品质量。
2.价值流分析:精益生产通过价值流分析,识别出创造价值的步骤和非价值增加的步骤,以便优化生产过程。
通过削减或优化非价值增加的步骤,企业能够实现资源的最大利用。
3.持续改进:精益生产强调持续改进的理念。
企业应该不断地寻求改进的机会,不断优化生产流程和提升产品质量。
通过持续改进,企业可以不断提高效率和竞争力。
4.员工参与:精益生产注重员工的参与和协作。
员工是企业的核心资产,他们的经验和智慧对于改进生产过程非常重要。
通过培养员工的参与意识和团队合作精神,企业可以更好地实现精益生产的目标。
5.质量优先:精益生产强调质量的重要性。
企业应该始终把质量放在第一位,追求卓越的产品质量。
通过不断提高产品质量,企业可以提升品牌形象、增加市场竞争力。
6.灵活性:精益生产注重灵活性和适应性。
企业应该具备快速响应市场需求的能力,同时灵活调整生产流程,以适应市场变化。
通过灵活性,企业可以更好地满足客户需求并获得竞争优势。
三、精益生产的实施步骤1.识别价值流:通过价值流分析,识别出创造价值的步骤和非价值增加的步骤。
2.消除浪费:排除所有不必要的活动和流程,减少浪费,提高效率。
精益生产简介及六西格玛基本概念
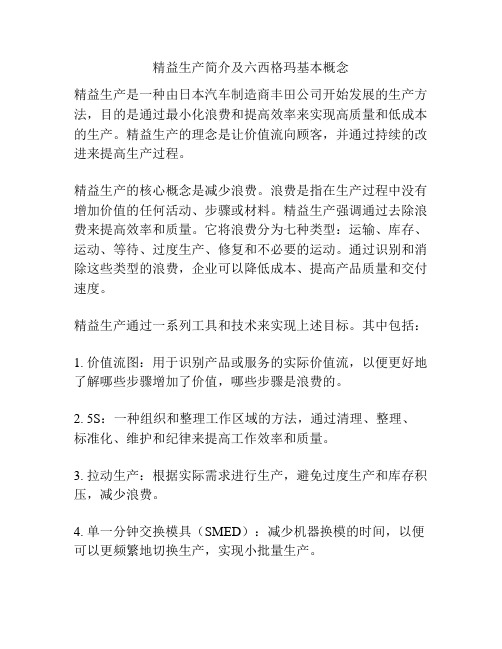
精益生产简介及六西格玛基本概念精益生产是一种由日本汽车制造商丰田公司开始发展的生产方法,目的是通过最小化浪费和提高效率来实现高质量和低成本的生产。
精益生产的理念是让价值流向顾客,并通过持续的改进来提高生产过程。
精益生产的核心概念是减少浪费。
浪费是指在生产过程中没有增加价值的任何活动、步骤或材料。
精益生产强调通过去除浪费来提高效率和质量。
它将浪费分为七种类型:运输、库存、运动、等待、过度生产、修复和不必要的运动。
通过识别和消除这些类型的浪费,企业可以降低成本、提高产品质量和交付速度。
精益生产通过一系列工具和技术来实现上述目标。
其中包括:1. 价值流图:用于识别产品或服务的实际价值流,以便更好地了解哪些步骤增加了价值,哪些步骤是浪费的。
2. 5S:一种组织和整理工作区域的方法,通过清理、整理、标准化、维护和纪律来提高工作效率和质量。
3. 拉动生产:根据实际需求进行生产,避免过度生产和库存积压,减少浪费。
4. 单一分钟交换模具(SMED):减少机器换模的时间,以便可以更频繁地切换生产,实现小批量生产。
六西格玛是另一种与精益生产相结合的管理方法。
六西格玛的目标是通过减少变异、提高质量和效率来满足客户需求。
它主要通过DMAIC(定义、测量、分析、改进和控制)的过程来实现。
1. 定义:明确项目目标和范围,确保所有团队成员对项目的目标有共同的理解。
2. 测量:收集相关数据,了解当前的业绩水平。
3. 分析:分析数据,识别潜在问题和改进机会。
4. 改进:制定和实施改进措施,以提高业绩和增加价值。
5. 控制:确保改进措施的可持续性,通过建立控制措施来监控和维持改进。
精益生产和六西格玛通常被联合应用,以实现连续改进和质量优化。
精益生产关注流程的效率和流畅性,而六西格玛则关注消除变异和提高质量。
通过结合这两种方法,企业可以实现高质量、低成本和高效率的生产。
精益生产和六西格玛是两种在管理领域中广泛应用的方法,它们提供了一个系统性的框架,帮助企业实现高质量、低成本、高效率的生产和服务。
精益生产方式思想基础
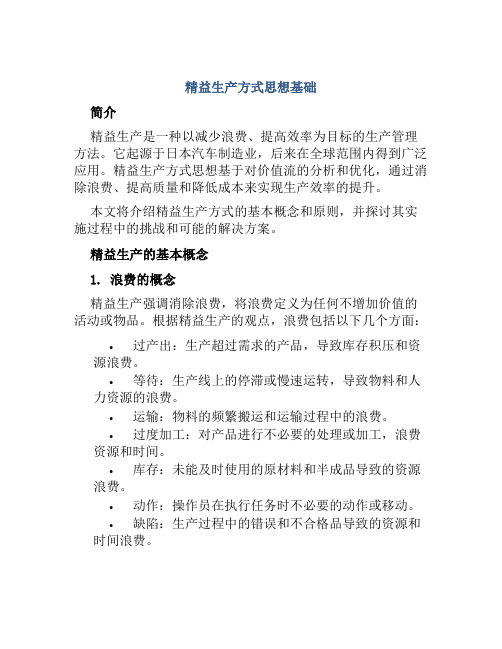
精益生产方式思想基础简介精益生产是一种以减少浪费、提高效率为目标的生产管理方法。
它起源于日本汽车制造业,后来在全球范围内得到广泛应用。
精益生产方式思想基于对价值流的分析和优化,通过消除浪费、提高质量和降低成本来实现生产效率的提升。
本文将介绍精益生产方式的基本概念和原则,并探讨其实施过程中的挑战和可能的解决方案。
精益生产的基本概念1. 浪费的概念精益生产强调消除浪费,将浪费定义为任何不增加价值的活动或物品。
根据精益生产的观点,浪费包括以下几个方面:•过产出:生产超过需求的产品,导致库存积压和资源浪费。
•等待:生产线上的停滞或慢速运转,导致物料和人力资源的浪费。
•运输:物料的频繁搬运和运输过程中的浪费。
•过度加工:对产品进行不必要的处理或加工,浪费资源和时间。
•库存:未能及时使用的原材料和半成品导致的资源浪费。
•动作:操作员在执行任务时不必要的动作或移动。
•缺陷:生产过程中的错误和不合格品导致的资源和时间浪费。
2. 价值流图精益生产使用价值流图来分析生产过程中的价值流和浪费。
价值流图是一种图形化工具,用于可视化生产过程中的各个环节和流程,并标识出其中的浪费点。
价值流图的绘制需要考虑以下几个要素:•价值流:从原材料到最终产品的所有流程。
•价值流中的价值增加环节:实际为产品添加价值的环节。
•流程时间:完成每个环节所需的时间。
•库存:每个环节中存储的物料数量。
•流程中的浪费:包括等待时间、运输时间、过度加工等。
3. 在精益生产中消除浪费的方式精益生产通过量化和深入分析浪费的根源,提出了一系列消除浪费的方式,包括:•质量管理:通过强调质量的重要性和培养质量意识,减少产品缺陷,避免浪费。
•5S方法:通过整理、整顿、清扫、清洁和纪律的执行,改善工作环境,提高工作效率。
•供应链优化:与供应商和合作伙伴合作,通过减少物料运输时间和库存,降低整体生产成本。
•作业标准化:定义明确的工作标准和流程,减少错误和重复工作。
•连续改进:通过监测和分析生产过程中的绩效指标,持续改进生产效率和质量。
精益生产的认识
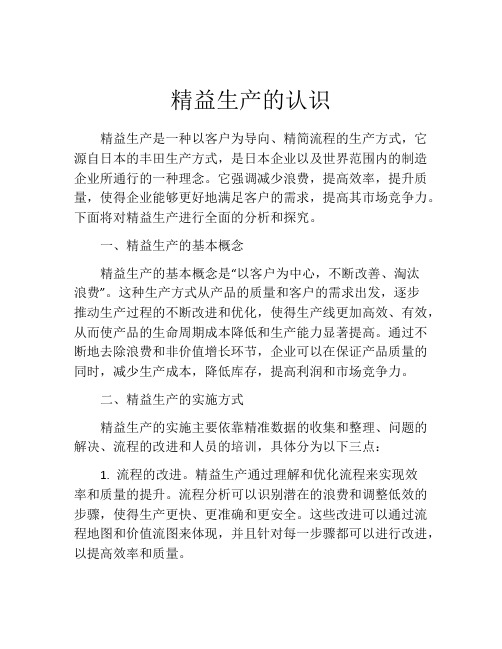
精益生产的认识精益生产是一种以客户为导向、精简流程的生产方式,它源自日本的丰田生产方式,是日本企业以及世界范围内的制造企业所通行的一种理念。
它强调减少浪费,提高效率,提升质量,使得企业能够更好地满足客户的需求,提高其市场竞争力。
下面将对精益生产进行全面的分析和探究。
一、精益生产的基本概念精益生产的基本概念是“以客户为中心,不断改善、淘汰浪费”。
这种生产方式从产品的质量和客户的需求出发,逐步推动生产过程的不断改进和优化,使得生产线更加高效、有效,从而使产品的生命周期成本降低和生产能力显著提高。
通过不断地去除浪费和非价值增长环节,企业可以在保证产品质量的同时,减少生产成本,降低库存,提高利润和市场竞争力。
二、精益生产的实施方式精益生产的实施主要依靠精准数据的收集和整理、问题的解决、流程的改进和人员的培训,具体分为以下三点:1. 流程的改进。
精益生产通过理解和优化流程来实现效率和质量的提升。
流程分析可以识别潜在的浪费和调整低效的步骤,使得生产更快、更准确和更安全。
这些改进可以通过流程地图和价值流图来体现,并且针对每一步骤都可以进行改进,以提高效率和质量。
2. 领导风险管理。
领导风险管理是指公司领导团队的参与和支持。
在实施精益生产的过程中,每个人都需要参与,领导团队可以帮助员工识别问题并为他们提供必需的资源,以便进行改进和创新。
3. 培训和参与。
教育和培训是实施精益生产的关键。
员工需要盲目地支持和协作,以确保各个部门之间的协同工作。
员工还需要具备分析和解决问题的技能,以帮助公司改进过程、降低成本、提高质量和效率。
三、精益生产的优点精益生产可谓是一个非常好的生产方式,具有诸多优点。
接下来,我们将对精益生产的优点进行简要总结。
1. 增加顾客满意度。
精益生产的目标是满足客户需求。
通过优化流程和减少浪费,提高生产效率和质量,客户将获得高质量的产品,既满足顾客需求,又提高了客户满意度。
2. 降低成本和库存。
精益生产敦促厂商最大化地利用现有的资源和员工技能,减少不必要的浪费,从而有效地提高效率,降低生产成本和库存。
精益生产的思想和方法
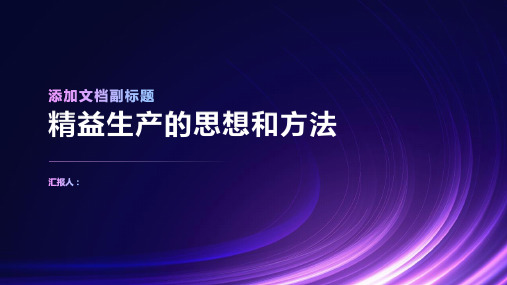
背景介绍:本田公司作为一家知名的汽车制造商,在精益生产方面有着丰富的实践经验。
精益生产理念:本田公司通过消除浪费、提高效率、降低成本等手段,实现了精益生产的目标。
戴尔公司的精益生产实践
戴尔公司背景介绍
制定实施计划:根据项目目标,制定详细的实施计划,包括时间表、资源需求、预算等
实施精益生产:按照实施计划,逐步推进精益生产,包括流程优化、减少浪费、提高效率等
持续改进:在实施过程中,不断收集数据,分析问题,持续改进,提高精益生产的水平
总结经验:项目结束后,总结经验教训,为今后的精益生产项目提供参考和借鉴。
持续改进
实施步骤:识别问题、分析原因、制定解决方案、实施改进、评估效果
定义:持续改进是一种不断优化和改进生产过程的方法,以提高生产效率、降低成本并提高产品质量
重要性:持续改进是精益生产的核心思想之一,它有助于企业不断适应市场变化,提高竞争力
工具和技术:包括六西格玛、5S管理、可视化管理等
04
制定实施计划
法律法规限制:精益生产需要符合法律法规的要求,但一些法律法规可能限制了精益生产的实施
未来发展方向和前景
数字化转型:利用大数据、人工智能等技术提升生产效率和产品质量
智能化制造:实现自动化、柔性化生产,降低成本,提高生产效率
绿色环保:注重环保和可持续发展,减少浪费和排放
个性化定制:满足消费者个性化需求,提高产品附加值和市场竞争力
培训员工
培训对象:全体员工,特别是生产线员工
培训效果:提高员工对精益生产的认识和技能水平,促进生产效率提升
培训内容:精益生产理念、方法、工具等
如何正确理解精益生产

如何正确理解精益生产简介精益生产是一种管理哲学和方法论,最早由日本丰田汽车公司引入并发扬光大。
精益生产通过寻求效率、减少浪费和持续改进,帮助组织提高质量、降低成本,并实现持续增长和发展。
本文将介绍精益生产的概念、原则和实施步骤,以帮助读者正确理解和运用精益生产。
精益生产的概念精益生产是一种以最小化浪费为目标的生产管理方法。
它的核心理念是通过持续的改进和消除无价值的活动来提高生产效率,从而实现更高的质量和更低的成本。
精益生产强调的关键原则包括价值流分析、平衡生产流程、减少浪费、追求零缺陷和质量一致性、建立员工参与和学习的文化等。
精益生产的原则1. 价值流分析价值流分析是精益生产中的重要工具之一。
通过对生产过程中的所有活动进行详细分析,确定哪些活动增加了价值,哪些活动是浪费的,从而找出改进的方向。
在进行价值流分析时,需要将所有生产活动标记为价值增加、非价值增加和浪费。
通过定期的价值流分析,组织可以发现并消除浪费,提高整体效率。
2. 平衡生产流程平衡生产流程是指通过合理安排生产活动,实现零缺陷和流畅生产。
它的目标是消除过程中的瓶颈和阻塞,确保生产能够按时、高质量地完成。
平衡生产流程需要考虑到各个环节之间的关系,合理分配资源和工作量。
通过工作平衡、作业规范化和减少变动,可以实现生产流程的优化。
3. 减少浪费减少浪费是精益生产的核心目标之一。
精益生产通过识别和消除各种形式的浪费,包括超产、库存、传输、等待、过度加工、不合格品等,从而提高效率、降低成本。
要减少浪费,需要从根本上改变生产过程和流程。
通过流程改进、优化布局、标准化工作等手段,可以降低资源消耗和时间浪费。
4. 追求零缺陷和质量一致性追求零缺陷和质量一致性是精益生产的另一个关键原则。
精益生产强调通过提高质量和减少变异来降低成本和提高效率。
为了实现零缺陷和质量一致性,组织需要建立良好的质量管理体系,包括从原材料采购到产品交付的全过程控制。
通过监测、检验和反馈机制,可以提高产品质量和生产的稳定性。
- 1、下载文档前请自行甄别文档内容的完整性,平台不提供额外的编辑、内容补充、找答案等附加服务。
- 2、"仅部分预览"的文档,不可在线预览部分如存在完整性等问题,可反馈申请退款(可完整预览的文档不适用该条件!)。
- 3、如文档侵犯您的权益,请联系客服反馈,我们会尽快为您处理(人工客服工作时间:9:00-18:30)。
Define
•
• • • • • • •
Measure
•
• • • • • • •
Analyze
•
• • • • • • • •
Improve
•
• • • • • • •
Control
•
• • • • • • •
项目识别工具 项目定义表 净现值NPV分析 Internal Rate of Return分 析 Discounted Cash Flow分 析 PIP Management Process RACI Quad Charts
7
第三部:五项原则
8
五大特点/五项原则
• 定义价值 • 识别价值流
• 拉动
• 流动 • 尽善尽美
9
第一项原则:定义价值
• 价值的增加由客户判定 • 产品价值的定义
– 特定产品
– 具有特定的性能 – 一定的价格 – 通过与特定客户的对话实现
1 0
第一项原则:定义价值
• 产品价值的定义:
–
产品有价值指作为具有特定的性能的特定产品、顾客愿意为此付出一定的价格。而这点 必须通过与特定客户的对话来实现 任何增加产品特性、功能或改变形状的努力或作业,例如机械加工、喷绘、组装等。 完成加值作业所花的时间称为加值时间,完成非加值作业所花时间为非加值时间。 加值时间又可分为客户加值时间和过程加值时间
– 消除停机时间
– 减少废品产生
• 提高劳动利用率
– 提高直接劳动利用率(一人多机、自动检测)
– 提高间接劳动利用率
2 1
精益工具/术语
• 目标:高品质、低成本、最短的前置时间
•SMED •价值流 •价值定义
•5S
•TPM •Jidoka / 自动化 •Kaikaku / 创新 •Kanban / JIT •Kaizen / CI
• 过程加值时间(BVA)
1 1
第一项原则:定义价值
• 非增值时间(NVA)
– 如果客户知道我们做此类工作,他们是否会要求我们消除此类活动以
降低价格? – 任务是否更适合其它两类? – 是否可以消除或减少此类活动? – 如:计数、搬运处理、检测、返修等
1 2
第二项原则:识别价值流
• 价值流是完成以下任务,创造特定产品的价值的一系列相关活
产品制造的时候真正制造时间占总时间的百分比
1 5
第五项原则:尽善尽美
• 找到改善机会
– 工作量减轻
– 时间减少
– 空间利用节约 – 成本降低 – 减少出错
– 增加客户满意度
按照顾客的需求定义价值、按价值流重新设计全部的生产经营活动、让价值流动 起来并浪顾客拉动价值流,这个过程必须要不断完善。不断改进、尽善尽美正是 精益生产的基本原则。消除浪费的过程没有止境,只有不断地把它进行下去。
1 6
第四部:核心思想
1 7
精益生产体系结构图
1 8
精益生产管理思想核心的分析
• 基于内部的团队式工作方式,在外部企业密切合作的环境下,
无限追求物流平衡是精益生产的真正核心所在。
• 我们学习精益生产生产方式的目的在于提高我们如下方面的能
力:
– 识别和确认浪费 – 承认浪费的勇气 – 消除浪费的愿望 – 消除浪费的行动 – 明白浪费将: • 加大成本 • 不会产生任进工具摘要
• • • • • • • • • • • • •
MRP修正— 普通拉系统— 补充拉系统— MRP/拉系统合成— Kaizen— 5S— 视觉控制工具— 分解批量— 减少设置时间— 缺陷预防— 过程流程改进— 生产线平衡— 全员生产维护—
通过更新MRP的输入数据,改进MRP的完整性和功 能性 按一定的产出速度,控制WIP以稳定循环时间的系统 基于客户的实际需求出发产品补充的系统 提供集成MRP和拉系统的方法以求最有效的解决方案 为“闪电式”改进项目提供DMAIC的架构 对于某一区域清洁、组织以及维持组织化的系列方 法,是关于生产率、质量及产出等精益改善的基础 建立高度的目视化工具以量测、改进和控制过程 修订批量以改进过程能力和柔性的分析方法 减少设置时间以改进过程柔性的四步法 预防(而非检验出)缺陷以降低质量成本提高客户 满意度的系列方法 工作单元内减少非增值时间(运输时间、队列等候 时间及材料处理时间)提高生产率的方法 均衡过程的任务以提高铲除和生产率的方法 增加资源的正常运行时间,提高过程能力和柔性的 系列方法
•
• • •
Propose Critical X’s Prioritize Critical X’s Verify Critical X’s Estimate the Impact of Each X on Y Quantify the Opportunity Prioritize Root Causes Conduct Root Cause Analysis on Critical X’s
•Heijunka / 均衡 / 稳定性
•拉动 / Kanban •单元布局 •标准化作业 •制造策略
2 2
考察我们当前的测量
• 关键指标
– 报废
– 消耗
– 返修 – 效率 – 浪费
– 利用率
• Y= F(X)… 以上所有的指标都是Y!!
2 3
LEAN测量浪费
• 过量生产 • 修正
• 库存
• 冗杂处理 • 运输
Cp & Cpk SupplyChainAccelerator Analysis Multi-Vari Box Plots Interaction Plots Regression ANOVA C&E Matrices FMEA
•
• • •
Brainstorming Pull Systems Setup Reduction TPM Process Flow Benchmarking Affinity DOE Hypothesis Testing Force Field Tree Diagrams Gantt Charts
5
第二部:发展史
6
制造技术变更
生产 方式 技术背景 完全手 工生 产方式 蒸汽动力的使 用、加工机械 的发明 作坊式生产 方式 流水线创建、 标准化实施 制造技术变革的背景 分析 市场背景 生产力低,产品 机器代替人力生 生产效率大大提高 相对短缺,完全 产,单件、技艺 是量的需求 性生产 对劳动者的技艺要求 很高、产品价格高、 生产周期长 主要特点 主要优点 主要缺点
• 多余动作
• 等待 • 重复… 以上所有的指标都是Y!!
2 4
精益生产与传统生产的区别
以往
批量 推动
1人/机 运行到发生故障
探测 %缺陷
非增值、 复杂
独立 记件
指导思想 同步化, 单件流, 拉动
机器 交叉培训 TPM
质量 无缺陷 5次为什 么
过程 无浪费、 标准作业
人员 团队工作; 单元、目视 化
动:
– 问题解决
– 信息管理 – 物质转变
1 3
第三项原则:拉动
• 通过客户的真正需求来拉动生产:
– 库存即浪费
– 未售出的在制品也是浪费
• 去除过剩的能力或提高客户的拉动速度
库存的问题:如果没有让用户的需求来拉动价值流,那么这种价值流也是不可实 现的价值流。
1 4
第四项原则:流动
• 产品必须经过的路程距离及所需的时间:
精益生产 基础概念导入
1
课程概述
• 定义 • 发展史
• 五项原则
• 核心思想(七大浪费) • 快速改善(Kaizen)
• 与6 Sigma的比较
2
第一部:定义
3
定义
• 由麻省理工学院在一项名为“国际汽车计划”的项目中提出 • 起源与日本丰田汽车公司
• 其它替代名称
– 丰田生产系统(TPS) – 准时化生产(JIT) – 精益生产 – 流动生产
1 9
七种浪费
• 过量生产的浪费 • 闲置时间的浪费
• 运输的浪费
• 流程冗杂的浪费 • 存货的浪费
• 移动的浪费
• 不良产品的浪费
2 0
面对浪费,我们该如何做?
• 改进生产流程
– 消除质量检测环节和返工现象(Poka-Yoke)
– 消除零件不必要的移动
– 消灭库存
• 改进生产活动
– 减少生产准备时间
流水线大批 大量生产方 柔性制造技术 生产力已大大提 广泛采用柔性制 式 的实施 高,多样化需求 造技术,产品多 成为主要需求 样化 精益生产方 式
生产力较低,以 大量采用自动化 生 产 效 率 极 大 提 库存多、占用资金多 满足量的需求为 机 械 , 产 品 单 高, 减少 了生 产过 、设备多、空间大, 主 一,批量很大 程中对人的依赖 产品单一化 库存 小、 占用 资金 管理的复杂性增强, 、 设 备 少 、 空 间 对职员要求提高 小, 生产 柔性 强, 市场反应灵活
4
定义
• 及时制造 • 消灭故障
• 消除一切浪费
• 零缺陷、零库存
在流水生产方式的基础上发展起来,通过系统结构、人员组织、运行方式和市场 供求等方面的变革,使生产系统能很快适应用户需求不断变化、实施以用户为导 向、以人为中心、以精简为手段、采用Team Work工作方式和并行设计,实施准 时化生产技术(JIT)、提倡否定传统的逆向思维方式,充分利用信息技术等为 内容的生产方式,最终达到包括产品开发、生产、日常管理、协作配套、供销等 各方面最好的结果。
• 加值作业:
– – –
• 客户加值时间(CVA)
– – – – – – – – –
过程是否改变产品 / 服务的性质、特征或功能? 是否能带来竞争利益,如降价、快速交货、减少缺陷? 顾客是否愿意为此支付额外费用或在竞争中选择我们? 如:切削、组装、喷漆等 过程是否能减少风险? 是否支持财务报告的要求 如果不做,则产品无法完成 法律或制度的要求 如:定单接受、采购拥护需求检验、材料或工具的再利用等