WOODWARD调速器说明书02702b
woodward505调速系统控制参数的选择问题

woodward505调速系统控制参数的选择问题摘要: 介绍了汽轮机负荷高的危害,展示了woodward505基本的控制功能,以及如何限制负荷。
现有水泥线余热电站的汽轮机供货商---青岛捷能汽轮机厂和杭州中能汽轮机厂(本文只列举设计中常用的汽轮机供货商),两家在505汽轮机厂家的调速系统控制参数选择不同,可能存在的隐患进行阐述,并建议在余热发电系统中woodward505组态设计中应有限制功率。
关键词: 汽轮机负荷; 505限制负荷;(一)前言在水泥线余热发电的小型机组中,使用woodward505调速器,是一种较为成熟的设计,在现有的水泥线余热电站的机组中有着较多的应用。
通过系统调试,系统完全满足控制要求。
在现有水泥线余热电站woodward505编程中经常用到的参数有:汽轮机进汽压力,发电机有功功率,汽轮机转速。
我们公司设计项目中主要采用的是青岛捷能汽轮机厂和杭州中能汽轮机厂的汽轮机,这两个厂家供货的woodward505调速器在各自的编程中采用的控制参数不全相同,虽都能保证机组的正常运行,但是从设计优化角度讲,还可以改进。
(二)woodward505简介1)woodward505调速机的原理woodward505调速器是以微处理器为基础的数字式转速调节器,专用于汽轮机控制。
根据汽轮机的特性,参数以及应用场合,在505调速器面板上直接进行组态。
其控制原理是:接收两个转速探头的信号,与内部设定值进行比较,经PID运算模块运算后输出4-20mA的电流信号。
该信号经电液转换器转换为二次油压信号,二次油压通过油动机、错油门调节汽轮机气阀的开度,控制进气量,使汽轮机转速稳定在设定值。
2)505调速机的应用505调速器采用了数字式信号低选(LSS)总线使三个信号中的最小信号去控制汽轮机的调节阀。
这三个控制调节阀位置的信号分别为:转速PID输出,可编程辅助PID输出和阀位限制器输出。
LSS 总线的输出直接设定了执行机构输出电流。
WDT 调速器电气说明书解析
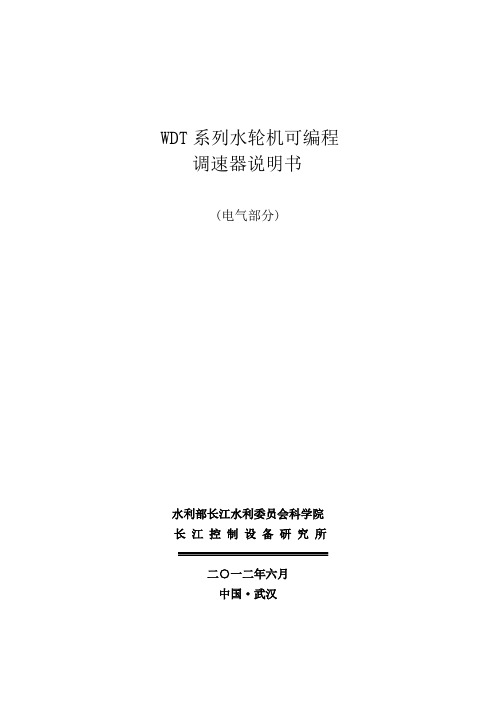
WDT系列水轮机可编程调速器说明书(电气部分)水利部长江水利委员会科学院长江控制设备研究所二○一二年六月中国·武汉目录第一章概述1.1性能和特点1.2主要技术参数1.3结构布置第二章系统工作原理2.1自动调节2.2手动操作第三章可编程调节器3.1组成与特点3.2功能模块简介3.3对外配线第四章操作说明4.1安装4.2调整4.3维护第五章调试大纲第一章概述1.1 性能特点比例阀控制可编程调速器是专为水轮发电机组研制的新型电液调速器,它采用了武汉长江控制设备研究所的专利技术:“水轮机调速器的电液比例随动装置”(专利号:95 2 38033.1)。
其电气部分采用可编程序控制器(PLC),配以比例集成式电液随动装置及相应的油压装置,构成一个完整的电液调速器,完全满足各式机组对调速器的各项技术要求。
其主要特点为:(1) 电气部分以可靠性极高的可编程序控制器为其硬件的主体,软件采用统一的时变参数控制策略,可适时辨识空载、并网和孤立运行等不同工况,可靠性高,稳定性好,带孤立负荷能力较强。
(2)具有残压测频(根据实际需要,可增加调速器齿盘测量频率),频率跟踪等功能,能快速并网。
(3)能够按转速、水位或给定负荷进行自动调节,具有数字协联及波动控制的功能。
(4)触摸显示屏能显示调速系统的运行状态和主要参数,如机组频率,电网频率,导叶开度,桨叶开度,调节器输出,协联输出和调节器的诸参数,具有多种显示界面,包括调速器的各种状态及故障指示,能显示调速系统的动态过程曲线。
(5)能以PLC专用通讯协议方式方便地实现与上位机的通讯。
(6)用电液比例阀直接控制主配压阀,结构简单,调整方便,可靠性高,耗油量小。
1.2 主要技术参数1.2.1 主要技术指标转速死区 ix≤0.02%静态特性线性度误差ε≤5%桨叶协联装置不准确度 ia≤1.5%自动空载三分钟转速摆动相对值不超过±0.15%接力器不动时间 Tq≤0.2秒平均故障间隔时间不少于 10000小时1.2.2 电气部分主要技术参数比例系数KP 0.5~20积分系数KI 0.05~10(1/S)微分系数KD 0~5(S)永态转差系数bp 0~10%频率人工失灵区E 0~1.0%频率给定范围FG 50Hz±5Hz功率给定范围PG 0~120%水位给定范围HG ±20%电源:AC220V ≯200WDC110V或220V ≯50W1.2.3 机械液压部分主要技术参数主配压阀名义直径 80;100;150mm工作油压 2.5MPa;4.0MPa;6.3MPa压力油罐容积 1.6m3;2.5m3;4.0m3;6.0m3第二章系统工作原理水轮发电机组有多种运行工况,不同的工况, 需要采用不同的控制规律、控制结构和调节参数。
调速器中文说明书(触摸屏)
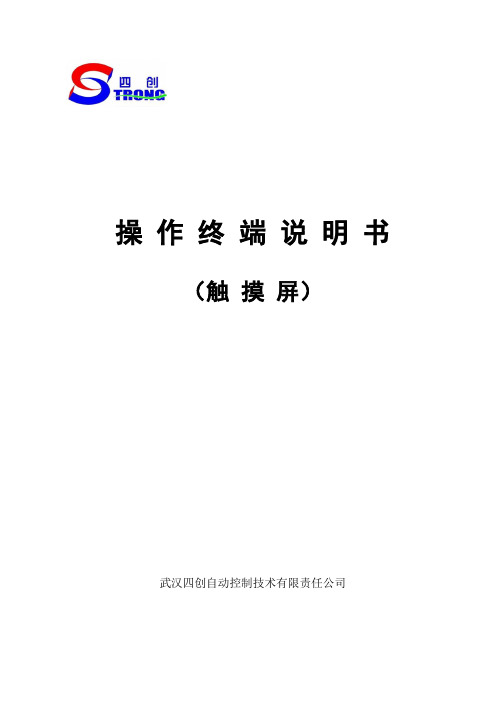
操作终端说明书(触摸屏)武汉四创自动控制技术有限责任公司目录一、系统概述 (2)二、画面简介 (2)1.状态指示画面 (3)2.操作画面 (4)3.主菜单画 (5)4.密码框 (6)5.数值键盘画面 (7)6.参数设置 (8)7.导叶参数设置 (9)8.浆叶参数设置(*双调机组) (11)9.功率参数设置 (13)10.大网参数、小网参数、空载参数、负载频率参数 (14)11.水头参数设置 (15)12.PID优化参数设置 (16)13.过程监视 (17)14.动态过程记录 (18)15.空载频率扰动 (18)16.空载频率摆动 (20)17.甩负荷试验 (20)18.故障查询 (21)19.协联数据(*双调机组) (22)一、系统概述图示操作终端可对调速器的各种状态进行监视,如开机、停机、并网、调相、机械手动/自动、水头手动/自动、跟踪网频/跟踪频给等。
用触摸键代替按钮,当需要增加某些按键时,只须修改程序,避免了采用按钮须修改硬件的敝端。
可对调速器进行静态、动态试验;对不同操作人员设置不同的权限,只有知道密码方可操作;对采样数据和报警记录进行存储,并可打印。
图示操作终端采用24V供电,背景灯使用寿命长,亮度可根据现场进行调整。
当调速器处于运行状态而没有任何操作时,背景灯到一定时间就熄灭。
这时,画面呈黑色,当需要看画面内容时,只须用手点屏幕即可。
也可以不用此功能,而使画面总是处于显示状态。
二、画面简介图示操作终端由各种画面组成,每个画面具有不同的功能。
当进行画面操作时,请勿用尖、硬物体点画面,以免损坏机器。
下面对各种画面进行介绍。
1.状态指示画面状态指示画面双调机组状态指示画面(*双调机组)状态指示画面如图所示。
该画面显示调速器的各种状态:开机、停机、并网、调相、开度调节/功率调节、机械自动/机械手动、浆叶手动/自动(双调机组)、水头手动/水头自动、跟踪频给/跟踪网频、调速器故障/调速器正常、停机备用、故障锁定。
WOODWARDPG_PL调速器的维护和调试[1]
![WOODWARDPG_PL调速器的维护和调试[1]](https://img.taocdn.com/s3/m/01a2cf0576c66137ee06195e.png)
WOODWARD PG 2P L 调速器的维护和调试严慧萍1,蒋湘佺2Maintenance and C ommissioning of W OODW ARD PG 2P L G overnorY an Hui 2ping 1,Jiang X iang 2quan 2(11兰州工业高等专科学校,甘肃省兰州市 730050;21兰化维达建筑安装工程公司,甘肃省兰州市 730060)摘 要:通过分析PG 2P L 机械液压式调速器结构和工作原理,提出日常维持保养方法及在线调试技术,为实践工作提供可行、实用、简单的方法。
关键词:调速器;离心力;在线调试中图分类号:TH13715 文献标识码:B 文章编号:100024858(2002)12200252031 引言调速器是调整与恒定汽轮机转速的部件,它对汽轮机组开停车及正常运行起着至关重要的作用。
其种类很多,常用的有德国某公司的SRI V 全液压调速器、美国某公司的PG 2P L 机械液压式调速器、W OOD 2W ARD505电子调速器等。
2 调速器结构分析211 调速器主要组成(1)汽轮机转速感应机构:用于检测汽轮机实际转速;(2)转速参考设定机构;(3)比较器:用于将汽轮机实际转速与转速参考设定点相比较;(4)执行机构:是与汽轮机的调节气阀相连的机构,用于控制汽轮机进气量。
以上4部分组成的汽轮机转速闭环控制系统如图1所示。
图1 汽轮机转速闭环控制系统 收稿日期:2002207201 作者简介:严慧萍(1964—),女,副教授,硕士研究生,主要从事机械制造及自动化方面的工作。
(4)负载压力 液压缸出口油接比例溢流阀进口腔,负载压力通过AD7520完成D/A 数模转换及电液控制器控制比例溢流阀定压提供。
比例溢流阀输出的压力与输入的电流信号的大小呈线性关系,改变电流的大小,可改变比例溢流阀的输出压力。
电流信号大小改变通过单片机发送给AD7520的数字量大小来实现。
--WOODWARD调速器参数修改及调速阀校验作业指导书

1 适用范围适用于WOODWARD调速器505D、505E。
2 目的熟悉WOODWARD调速器的组态方法,通晓参数所包含的意义并能够修改参数;校验WOODWARD调速阀的阀门特性,使其精确工作。
3 人员资格、人员数量及职责分工3.1人员资格和数量3.1.1熟悉WOODWARD调速器的接线、调速器的组态方法、调速阀供油系统,会正确使用WOODWARD的操作界面,能正确修改参数。
3.1.2作业前应协同分工,一般应有2-3人进行,2人操作,另外人员配合。
3.2 职责分工3.2.1 车间技术组是本作业指导书的主管部门,负责对作业的技术指导、监督、检查。
3.2.2 各班组在作业过程中应严格执行操作技术要求及相应安全生产禁令。
4 工器具准备及要求4.1作业前准备一份空白的505调速器组态菜单。
4.2仪表常用工具一套。
4.3信号发生器一台、万用表一台、对讲机一对。
4.4干净抹布几块。
5作业前检查项目5.1检查对讲机通话是否正常、信号发生器工作是否正常、万用表的电流档是否完好。
5.2检查需要修改的参数是否在所选择的菜单里,参数值是否正确同时对系统的原参数进行记录以备核对。
5.3检查WOODWARD调速器工作正常、无系统报警。
5.4检查WOODWARD调速阀供油压力正常。
5.5检查并确认T&T阀中TRIP阀在全关位置。
6技术要点6.1了解WOODWARD调速器的接线。
6.2了解WOODWARD调速器的组态方法。
6.3了解WOODWARD调速器的操作界面。
6.4了解WOODWARD调速阀的供油系统6.5了解WOODWARD调速器的人机界面7使用具体作业步骤7.1确认T&T阀中的TRIP阀处于全关位置(机组停车)7.2在WOODWARD调速器上按PROGRAM,屏幕上会要求输入PASSWORD,输入密码后就进入组态界面。
7.2.1WOODWARD505调速器的组态菜单共有十三个大菜单,分别为:1、TURBINE START(透平启动)主要包含:启动方式、启动时速度斜率、IDLE设定点、冷启动与热启动的时间设定、冷启动与热启动的斜率设定、IDLE延迟时间、是否使用外部跳闸以及是否使用复位来清除跳闸输出等等。
WoodWardPG-PL型调速器

学习汇报材料
WoodWardPG-PL型调速
一、Woodward PG-PL调速器简介
简介
PG型的调速器是指PNEUMATIC GOVERNOR,它以 总的控制箱为基础发展许多分类的型号调速器,是根据使 用和它操作形式分为:PGD、PGL、PGPL、PGA、 PGATL、PGE、PGAV、PGPH、PGTR、PGG、PGGEG 和PG/2301等型号。头两个字样PG是指以PG型基本的工 作原理,后的几个字样是以何种的操作形式,如D是转盘 式(Dial)、L是连桿式(Level)、A是以气动调速等等 。
WoodWardPG-
二、PG-PL调速器组成部分
PG-PL型调速器底座
WoodWardPG-
二、PG-PL调速器组成部分
PG-PL型调速器底座
蓄能器
WoodWardPG-
二、PG-PL调速器组成部分
PG-PL型调速器底座
进油、回油孔
(与其相接的 是动力活塞侧)
WoodWardPG-
二、PG-PL调速器组成部分
调速弹簧,飞锤,飞锤头装置
滑阀柱塞
飞锤 调速弹簧
WoodWardPG-
二、PG-PL调速器组成部分
已磨损的飞锤(更换)
WoodWardPG-
二、PG-PL调速器组成部分
调速滑阀
内有轴承(本次拆检过程检查时此轴承无磨损)
WoodWardPG-
二、PG-PL调速器组成部分
速度设定活塞
WoodWardPG-
WoodWardPG-
Woodward PG-PL调速器
双合金的 回位连杆
WoodWardPG-
三、PG-PL调速器基本工作原理
WOODWARD调速器说明书02036
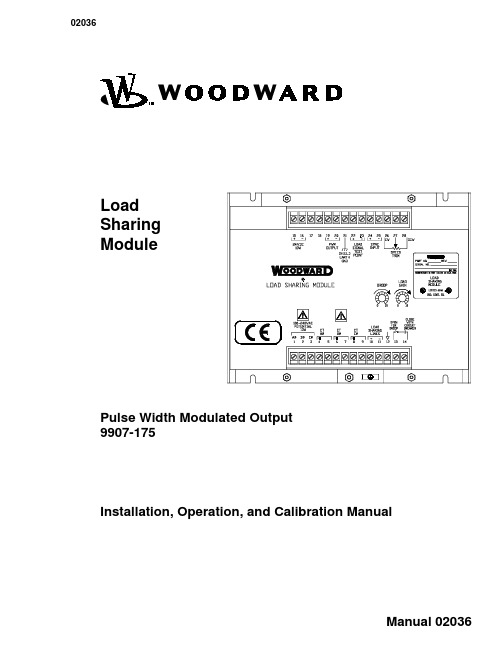
02036LoadSharingModulePulse Width Modulated Output9907-175Installation, Operation, and Calibration ManualManual 02036!WARNINGRead this entire manual and all other publications pertaining to the work to be performed before installing, operating, or servicing this equipment. Practice all plant and safety instructions and precautions. Failure to follow instructions can cause personal injury and/or property damage.The engine, turbine, or other type of prime mover should be equipped with an overspeed (overtemperature, or overpressure, where applicable) shutdown device(s), that operates totally independently of the prime mover control device(s) to protect against runaway or damage to the engine, turbine, or other type of prime mover with possible personal injury or loss of life should the mechanical-hydraulic governor(s) or electric control(s), the actuator(s), fuel control(s), the driving mechanism(s), the linkage(s), or the controlled device(s) fail.!CAUTIONDo not attempt to service the unit beyond that described in the operating instructions. All other servicing should be referred to qualified service personnel.!CAUTIONTo prevent damage to a control system that uses an alternator or battery-charging device, make sure the charging device is turned off before disconnecting the battery from the system.!CAUTIONElectronic controls contain static-sensitive parts. Observe the following precautions to prevent damage to these parts.•Discharge body static before handling the control (with power to the control turned off, contact a grounded surface and maintain contact while handling the control).•Avoid all plastic, vinyl, and styrofoam (except antistatic versions) around printed circuit boards.•Do not touch the components or conductors on a printed circuit board with your hands or with conductive devices.!CAUTIONTo maintain compliance with CE marking requirements, the European Union Low Voltage Directive requires that the Load Sharing Module (LSM) be mounted in an IP43 enclosure as defined in EN60529. Access to the Load Sharing Module must be restricted to qualified personnel.Woodward Governor Company reserves the right to update any portion of this publication at any time. Information provided by Woodward Governor Company is believed to be correct and reliable. However, no responsibility is assumed by Woodward Governor Company unless otherwise expressly undertaken.© 1999 by Woodward Governor CompanyAll Rights ReservedManual 02036 Load Sharing ModuleContentsCHAPTER 1. GENERAL INFORMATION (1)Introduction (1)Description (1)CHAPTER 2. ELECTROSTATIC DISCHARGE AWARENESS (5)CHAPTER 3. INSTALLATION (7)Introduction (7)Unpacking (7)Location Considerations (7)General Wiring Requirements (8)Power Requirements (8)Shielded Wiring (9)Generator Connections (10)Current Transformers (10)Load Sharing Lines, Droop, and Auxiliary Contacts (10)Output to the Caterpillar Digital Electronic Control (11)Synchronization Connections (11)Speed Trim Potentiometer (11)CHAPTER 4. SETUP AND CALIBRATION (13)Introduction (13)Phasing Check (14)Phase Correction Procedure (15)Load Gain Adjustment (19)Droop Adjustment (20)Setting Droop for an Isolated Load (20)Setting Droop for an Infinite Bus (21)CHAPTER 5. THEORY OF OPERATION (23)Introduction (23)Power Supply (23)Power Sensor (23)Load Comparator Circuit (24)Speed Trim Circuit (24)Isochronous Load Sharing (24)Droop Operation (24)Auxiliary Equipment (25)Pulse Width Modulation (25)CHAPTER 6. TROUBLESHOOTING (27)Woodward iLoad Sharing Module Manual 02036ContentsCHAPTER 7. SERVICE OPTIONS (29)Product Service Options (29)Replacement/Exchange (29)Flat Rate Repair (30)Flat Rate Remanufacture (30)Returning Equipment for Repair (30)Packing a Control (31)Additional Instructions (31)Replacement Parts Information (31)How to Contact Woodward (31)Other Service Facilities (32)Additional Aftermarket Product Support Services (32)System Troubleshooting Guide (33)Technical Assistance (36)APPENDIX. LSM CONTROL SPECIFICATIONS (37)Declaration of Conformity (39)Illustrations and Tables1-1.Typical System Using a Load Sharing Module (1)1-2.Outline Drawing of Load Sharing Module (2)1-3.Plant Wiring Diagram of Load Sharing Module (3)1-4.Block Diagram of Load Sharing Module (4)3-1.Preparation of Shielded Cables (9)4-1.Temporary CT Connections (16)4-2.Droop Adjustment (21)ii WoodwardManual 02036 Load Sharing ModuleChapter 1General InformationIntroductionThe Woodward Load Sharing Module is made for use with Caterpillar enginesequipped with a Caterpillar digital speed control with a pulse width modulated(PWM) input. The Load Sharing Module allows use of Woodward powergeneration accessories and allows load sharing between the Caterpillar digitalspeed control equipped engines and engines controlled with Woodward electroniccontrols.DescriptionThe Load Sharing Module provides isochronous and droop load-sharing capability for engines equipped with Caterpillar digital controls in generator set applications.Additional equipment in the control system can include the Woodward SPM-ASynchronizer, Paralleling Phase Switch, Import/Export Control, PrecisionFrequency Control, Automatic Generator Loading Control, and Automatic PowerTransfer and Loading Control.Figure 1-1 shows a typical system using a Load Sharing Module.Figure 1-1. Typical System Using a Load Sharing Module Woodward1Load Sharing Module Manual 02036Figure 1-2. Outline Drawing of Load Sharing Module2WoodwardManual 02036 Load Sharing ModuleFigure 1-3. Plant Wiring Diagram of Load Sharing Module Woodward3Load Sharing Module Manual 02036Figure 1-4. Block Diagram of Load Sharing Module4WoodwardManual 02036 Load Sharing ModuleWoodward 5Chapter 2Electrostatic Discharge AwarenessAll electronic equipment is static-sensitive, some components more than others. To protect these components from static damage, you must take special precautions to minimize or eliminate electrostatic discharges.!CAUTIONTo prevent possible serious damage to the Load Sharing Module, do not attempt to service the unit beyond that described in the operating instructions. All other servicing should be referred to qualifiedservice personnel.Follow these precautions when working with or near the Load Sharing Module.1.Before doing maintenance on the Load Sharing Module, discharge the staticelectricity on your body to ground by touching and holding a grounded metalobject (pipes, cabinets, equipment, etc.).2.Avoid the build-up of static electricity on your body by not wearing clothingmade of synthetic materials. Wear cotton or cotton-blend materials as muchas possible because these do not store static electric charges as much assynthetics.3.Keep plastic, vinyl, and styrofoam materials (such as plastic or styrofoamcups, cup holders, cigarette packages, cellophane wrappers, vinyl books orfolders, plastic bottles, and plastic ash trays) away from the Load SharingModule, the modules, and the work area as much as possible.4.Do not remove the printed circuit board (PCB) from the electronic cabinetunless absolutely necessary, and then only after all input power has beenremoved from the unit. If you must remove the PCB from the electroniccabinet, follow these precautions:•Do not touch any part of the PCB except the edges.•Do not touch the electrical conductors, the connectors, or thecomponents with conductive devices or with your hands.•When replacing a PCB, keep the new PCB in the plastic antistaticprotective bag it comes in until you are ready to install it. Immediatelyafter removing the old PCB from the electronic cabinet, place it in theantistatic protective bag.Load Sharing Module Manual 02036 6WoodwardChapter 3InstallationIntroductionThis section contains general installation instructions for the Load Sharing Module. Environmental precautions and location considerations are included to determine the best location for the Load Sharing Module. Additional information includes unpacking instructions, electrical connections, and an installation check-out procedure.UnpackingBefore handling the Load Sharing Module, read Chapter 2, Electrostatic Discharge Awareness. Be careful when unpacking the Load Sharing Module. Check the unit for signs of damage such as bent or dented panels, scratches, and loose or broken parts. Notify the shipper of any damage.Location ConsiderationsConsider these requirements when selecting the mounting location:• Adequate ventilation for cooling• Space for servicing and repair• Protection from direct exposure to water or to a condensation-prone environment• Protection from high-voltage or high-current devices, or devices which produce electromagnetic interference• Protection from excessive vibration• An ambient operating temperature range of –40 to +70 °C (–40 to +158 °F) Do not mount the Load Sharing Module on the engine.Figure 1-2 is an outline drawing of the Load Sharing Module. Install the unit near the electronic engine control. It may be installed in any position.To maintain compliance with CE marking requirements, the European Union Low Voltage Directive requires that the Load Sharing Module (LSM) be mounted in an IP43 enclosure as defined in EN60529. Access to the Load Sharing Module must be restricted to qualified personnel.General Wiring RequirementsThe circled ground symbol identifies the Protective Earth Terminal.This terminal must be connected directly to protective earth using agrounding conductor at least as large as those used on terminals 1through 9. The insulation of the grounding conductor must be of greenand yellow color.This symbol identifies functional or EMC earth. This terminal is to beused for cable shield connections only. It is not to be used as aprotective earth terminal.External wiring connections and shielding requirements for a typical installation are shown in the plant wiring diagram, Figure 1-3. These wiring connections and shielding requirements are explained in more detail in this chapter.To maintain compliance with CE marking requirements, the Low Voltage Directive requires that the Load Sharing Module must only be connected to Class III equipment.Wiring for the Load Sharing Module must be suitable for at least 90 °C (194 °F) and also be suitable for the maximum installed operating temperature.The Load Sharing Module must be permanently connected and employ fuses or circuit breakers in each of the PT lines to limit current to the LSM PT inputs to no more than 5 A. In addition, a 2 A fast-acting fuse or circuit breaker must be provided in the 24 Vdc power supply line.All terminal block screws must be tightened to 0.56 to 0.79 N·m (5.0 to 7.0 lb-in). To maintain compliance with CE marking requirements, the EMC Directive requires that all shields be connected to the terminals provided per the plant wiring diagram, Figure 1-3.Power RequirementsThe Load Sharing Module is powered from a 24 Vdc source. The 24 Vdc source must be a minimum of 18 Vdc and a maximum of 32 Vdc continuous. If a battery is used for operating power, an alternator or other battery charging device is necessary to maintain a stable supply voltage.!CAUTIONTo prevent possible serious damage to the Load Sharing Module, make sure the alternator or other battery charging device is turned off or disconnected before disconnecting the battery from the unit.Shielded WiringAll shielded cable must be twisted conductors with either a foil or braided shield. Do not attempt to tin (put solder on) the braided shield. All signal lines should be shielded to prevent picking up stray signals from adjacent equipment. Connect the shields to the terminals indicated in the plant wiring diagram. Wire exposed beyond the shield must be as short as possible.The other end of the shields must be left open and insulated from any other conductor. Do not run shielded signal wires with other wires carrying large currents. See Application Note 50532, EMI Control for Electronic Governing Systems, for more information.Where shielded cable is required, cut the cable to the desired length and prepare the cable as instructed below and shown in Figure 3-1.Figure 3-1. Preparation of Shielded Cables1. Strip outer insulation from both ends, exposing the braided or spiral wrappedshield. Do not cut the shield on the end nearest to the Load Sharing Module.Cut off the shield on the end away from the unit.2. Use a sharp, pointed tool to carefully spread the strands of the shield.3. Pull the inner conductors out of the shield. Twist braided shields to preventfraying.4. Connect lugs to the shield and to the control wires. Number 6 slotted or roundcrimp-on terminals are used for most installations. Connect the wires to the appropriate terminals on the module.Installations with severe electromagnetic interference (EMI) may require shielded wire run in conduit, double shielded wire, or other precautions.Generator ConnectionsNOTE Use 1 mm² (18 AWG) or larger wire for all PT and CT connections.The spacing between the lugs on terminals 3 and 4 must be 6.5 mm(0.256 inch) or greater to comply with the European Union LowVoltage Directive (see Figure 1-3). The lugs must have insulatedsleeves.IMPORTANTConnections from the potential transformers and currenttransformers must be made correctly in regard to the three phasesfor the Load Sharing Module to operate correctly. Sorting out thethree phases at the module is tedious and requires numerousgenerator starts and stops. If at all possible, make sure that the wiringis correctly done at the time of installation and the phases correctlyand permanently identified at the generator and at the module.Connect the PT output from the A leg to terminal 1. Connect the PT output fromthe B leg to terminal 2. Connect the PT output from the C leg to terminal 3. Sizethe potential transformers to produce 100–240 Vac.Current TransformersPower source current transformers should be sized to produce 5 A secondarycurrent with maximum generator current (3–7 A secondary current at full load isacceptable). CT burden is 0.1 VA. To prevent lethal high voltage from developingon leads to the terminals, the Load Sharing Module contains internal burden whichmust be connected across the power source current transformers whenever the unitis running. Ammeters may be installed on the leads from the current transformers.Connect phase “A” CT to terminals 4 and 5. Connect phase “B” CT to terminals 6and 7. Connect Phase “C” CT to terminals 8 and 9. Observe correct phasing asshown in the plant wiring diagram, Figure 1-3.Load Sharing Lines, Droop, and Auxiliary ContactsThe droop contact for selecting droop or isochronous operation is wired in serieswith the circuit breaker auxiliary contact between terminals 13 and 14. When boththe droop contact and circuit breaker auxiliary contact are closed, the LoadSharing Module is in the isochronous load sharing mode. In this mode the internalload-sharing-line relay is energized, the droop signal is disabled, and the loadmatching circuit is connected to the load-sharing lines, permitting isochronous loadsharing.The Load Sharing Module is in the droop mode when EITHER the droop contactor the circuit breaker auxiliary contact is open. If the droop contact is open, theLoad Sharing Module remains in the droop mode even when the circuit breakerauxiliary contact is closed. If droop is not desired when the auxiliary contact is open, turn the droop potentiometer fully counterclockwise.Use a single pole, single-throw switch with a 0.1 A minimum rating for the “open for droop” switch.Output to the Caterpillar Digital Electronic Control Use twisted 0.5 mm² (20 AWG) or larger shielded wire to connect the pulse-width modulated output signal from terminals 19(+) and 20(–) to the Caterpillar control. Connect the shield to terminal 21 only. Do not connect the shield at the Caterpillar control end of the wiring.Synchronization ConnectionsIf an SPM-A synchronizer is used, connect twisted-pair 0.5 mm² (20 AWG) or larger shielded wire from the synchronizer to terminals 24(+) and 25(–). Tie the shield to terminal 21. Do not connect the shield at the synchronizer end of the wiring.Speed Trim PotentiometerIf a speed-trim potentiometer is used, connect a 10 k 10-turn potentiometer to terminals 26 (CW), 27 (wiper), and 28 (CCW). Use 0.5 mm² (20 AWG) or larger shielded wire, and connect the shield to terminal 21. Do not connect the potentiometer end of the shield. The potentiometer is used to move the speed setting when manually synchronizing the generator or to change load demand in droop mode.Chapter 4Setup and CalibrationIntroductionUse this calibration procedure after a Load Sharing Module is installed on a generator set, to obtain the needed operating characteristics during load sharing.1.Check that the proper voltage is connected to terminals 15(+) and 16(–).Proper polarity must be maintained. See the plant wiring diagram, Figure 1-3.2.Remove wires from load sharing line terminals 10 and 11, and from theSPM-A Synchronizer (if used) at terminals 24 and 25.3.Select isochronous operation by shorting terminals 13 and 14.4.If a speed setting potentiometer is used, set it to mid position (50%).!WARNINGTO PROTECT AGAINST POSSIBLE PERSONAL INJURY, LOSS OF LIFE, and/or PROPERTY DAMAGE EACH TIME you START the engine, turbine, or other type of prime mover, BE PREPARED TO MAKE AN EMERGENCY SHUTDOWN to protect against runaway or overspeed should the mechanical-hydraulic governor(s), or electric control(s), the actuator(s), fuel control(s), the driving mechanism(s), thelinkage(s), or the control devices fail.5.Start the engine according to the engine manufacturer’s instructions. Adjustthe engine for rated speed. Apply full load to the generator set.NOTE The most accurate calibration is made at full load. However, if it is notpossible to run the generator set at full load, run it at less than fullload, and reduce the voltage readings given in this calibrationprocedure proportionally. For example: run a 200 kW generator set at100 kW and divide all voltages given in this calibration procedure by2. If you reduce the load in this manner, be sure to reduce it by thesame amount throughout the calibration procedure.6.Set the LOAD GAIN potentiometer fully clockwise.7.Check the load signal voltage between terminals 22 and 23. Adjust the LOADGAIN potentiometer for 6.0 Vdc signal. If this voltage is not obtainable, setthe load signal as close as possible to 6 Vdc.8.Remove the load from the generator set.9.Check the voltage between terminals 22 and 23. This voltage should be 0.0 ±0.25 Vdc. If this voltage is not correct, the Load Sharing Module unit isfaulty or there may still be load on the generator.Phasing Check!WARNINGA high voltage across open CTs (current transformers) can cause death or serious injury. Do not disconnect a CT from the Load Sharing Module while the engine is running. The CTs can develop dangerously high voltages and may explode if open circuited while the engine is running.For this check, the generator set must be running isochronously, not paralleled, and with a power factor greater than 0.8.10.Check that the potential connections are made as follows and correct them ifthey are not.• Phase A to terminal 1• Phase B to Terminal 2• Phase C to Terminal 3NOTE The most accurate calibration is made at full load. However, if it is notpossible to run the generator set at full load, run it at less than fullload, and reduce the voltage readings given in this calibrationprocedure proportionally. For example: run a 200 kW generator set at100 kW and divide all voltages given in this calibration procedure by2. If you reduce the load in this manner, be sure to reduce it the sameamount throughout this calibration procedure.11.Start the engine and apply full load to the generator set.ing a dc voltmeter, measure the load signal at terminals 22 and 23. Adjustthe load gain potentiometer to give a 6 Vdc load signal. If 6 Vdc is notobtainable, set the load signal as close as possible to 6 Vdc. Record thisvoltage.13.Shut down the generator set.!WARNINGA high voltage across open CTs (current transformers) can cause death or serious injury. Do not disconnect a CT from the Load Sharing Module while the engine is running. The CTs can develop dangerously high voltages and may explode if open circuited while the engine is running.14.Disconnect the wire from terminal 5 that comes from the phase “A” CT andconnect both wires from this CT to terminal 4.15.Start the generator set and apply full load.16.Measure the load signal at terminals 22 and 23. If the phase “B” and “C”current transformers are connected correctly, this voltage will be 1/3 lower than the voltage recorded in step 13. For example: if the reading was 6 volts in step 13, the reading in this step should be approximately 4 volts.17.Shut down the generator set.18.Reconnect the phase “A” CT wire to terminal 5.19.If the reading in step 16 was correct, proceed to Load Gain Adjustment laterin this chapter. Otherwise, perform the following Phase CorrectionProcedure.Phase Correction ProcedureIf this procedure is followed, the correct connection of the current transformers is assured; the correct CT will be connected to the correct input on the Load Sharing Module with the correct polarity. Use this procedure only if the Phasing Check indicates that the phasing is incorrect.A CT for any phase (A, B, or C), will produce the most positive load signal voltage when it is connected, in the proper polarity, to the terminals on the Load Sharing Module which correspond to the same phase. Any other connections of this CT will produce a less positive load signal voltage. This procedure makes trial connections of the first CT to all three CT inputs on the Load Sharing Module, polarized both ways on each CT input. The load signal voltage is recorded for each connection, and the CT is then connected to the CT input terminals that produced the most positive load signal voltage and with the polarity that produced the most positive load signal voltage.In a like manner, the second CT is tried on each of the two remaining CT input terminals in each polarity, then connected, in the correct polarity, to the terminals which produced the most positive load signal voltage.The remaining CT is then connected to the remaining CT input and the load signal checked for each polarity. This CT is then connected to the CT input, polarized so that it produces the most positive load signal voltage.When the procedure is completed, all three CTs are connected to the proper CT inputs on the Load Sharing Module, with the correct polarity, and are now labeled with their correct designations.The procedure for correcting phase wiring requires that the generator set be shut down and the current transformers disconnected many times. For convenience during the phasing check, the temporary method of connecting the current transformers shown in Figure 4-1 is recommended. By connecting a burden resistor (a 0.5 , 20 W resistor), across each current transformer, that current transformer can be disconnected from the Load Sharing Module after removing all load. The connections between the terminal strip and the Load Sharing Modulecan be changed with the generator set running; however, remove all load before any changes in connections are made. Do not disconnect a wire from a current transformer with load on the system. After completion of the procedure remove the terminal strip and the resistors.Figure 4-1. Temporary CT Connections!WARNINGA high voltage across open CTs (current transformers) can cause death or serious injury. Do not disconnect a CT from the Load Sharing Module while the engine is running. The CTs can develop dangerously high voltages and may explode if open circuited while the engine is running.For this procedure, the generator set must be running isochronously, not paralleled, and with a power factor greater than 0.8.1.Start with the generator shut down.bel each CT wire with the phase and polarity that you think it should be.Even though this identification may prove to be wrong during this procedure, this step is necessary so that the individual wires may be identified during the description of the procedure.3.Disconnect the phase “B” CT wires from terminals 6 and 7 and connect thesetwo wires together. Use a small screw and nut and tape the connection.4.Disconnect the phase “C” CT wires from terminals 8 and 9 and connect thesetwo wires together. Use a small screw and nut and tape the connection.5.Connect the two wires from the phase “A” CT to phase “A” input terminals 4and 5.!WARNINGTO PROTECT AGAINST POSSIBLE PERSONAL INJURY, LOSS OF LIFE, and/or PROPERTY DAMAGE EACH TIME you START the engine, turbine, or other type of prime mover, BE PREPARED TO MAKE AN EMERGENCY SHUTDOWN to protect against runaway or overspeed should the mechanical-hydraulic governor(s), or electric control(s), the actuator(s), fuel control(s), the driving mechanism(s), thelinkage(s), or the control devices fail.6.Start the engine and apply full load.7.Measure the load signal voltage between terminals 22 and 23 and record thisvoltage.8.Shut the generator set down and reverse the phase “A” wires on terminals 4and 5.9.Start the engine and apply full load.10.Measure the load signal voltage between terminals 22 and 23 and record thisvoltage.11.Shut the generator set down.12.Remove the phase “A” CT wires from terminal 4 and 5 and connect the phase“A” CT wires to the phase “B” input terminals 6 and 7.13.Start the engine and apply full load.14.Measure the load signal voltage between terminals 22 and 23 and record thisvoltage.15.Shut the generator set down and reverse the phase “A” CT wires on terminals6 and 7.16.Start the engine and apply full load.17.Measure the load signal voltage between terminals 22 and 23 and record thisvoltage.18.Shut down the generator set.19.Remove the phase “A” CT wires from terminal 6 and 7 and connect the phase“A” CT wires to the phase “C” input terminals 8 and 9.20.Start the engine and apply full load.21.Measure the load signal voltage between terminals 22 and 23 and record thisvoltage.22.Shut the generator set down and reverse the phase “A” wires on terminals 8and 9.23.Start the engine and apply full load.24.Measure the load signal voltage between terminals 22 and 23 and record thisvoltage.25.Shut down the generator set.26.Remove the phase “A” CT wires from terminal 8 and 9 and connect the wiresto the pair of terminals, in the same polarity, that produced the most positive load signal voltage.27.Untape and disconnect the Phase “B” CT wires. Connect the phase “B” CTwires to one pair of the two remaining CT input terminals on the LoadSharing Module.28.Start the generator set and apply full load.29.Measure the load signal voltage at terminals 22 and 23 and record thisvoltage.30.Shut the generator set down and reverse the phase “B” wires on the CT inputterminals.31.Start the engine and apply full load.32.Measure the load signal voltage between terminals 22 and 23 and record thisvoltage.33.Shut down the generator set.34.Remove the phase “B” CT wires from the terminals they are connected to andconnect them to the remaining pair of CT input terminals on the LoadSharing Module.35.Start the generator set and apply full load.36.Measure the load signal at terminals 22 and 23 and record this voltage.37.Shut the generator set down and reverse the phase “B” wires on the CT inputterminals.38.Start the engine and apply full load.。
WOODWARD调速器说明书02021d
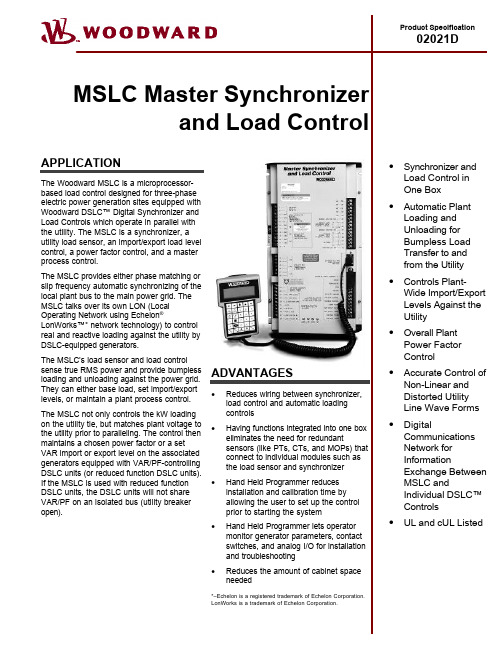
• Digital signal processing makes the MSLC resistant to power line distortions and harmonics• Digital communications across the LON reduce susceptibility to noise on the load sharing lines• Three-phase true RMS power sensing makes the MSLC accurate even with unbalanced phase loading and voltage fluctuations• Local Area Network carries plant parameters for use in a distributed control systemOPERATING MODESSynchronizing—The MSLC controls all DSLC-equipped generators to match both frequency and voltage between the local bus and the main, and then closes the utility tie breaker when they are synchronized.Base Load—The MSLC talks over its LON to set all DSLC-equipped generators in isochronous load sharing to a chosen percentage of their individual rated loads and power factor.Import/Export Control—TheMSLC controls real load andreactive power across theutility tie. Real load (kW) iscontrolled by changing theload levels; reactive load(kVAR) is controlled bychanging the power factorreference on all DSLC-equipped system generatorswhich are in isochronous loadsharing.Process Control—TheMSLC control adjusts thereal load on the plantgenerators to maintain aprocess at a chosen level.ADJUSTMENTSThe Woodward Hand Held Programmer makes all adjustments quickly and easily through the control’s ten convenient menus. The control saves all set points in permanent memory, which does not require batteries or other power sources to retain data. The Hand Held Programmer prevents tampering with set points, yet allows entries to be changed at any time. The Hand Held Programmer displays in plain English, so there are no codes to look up or memorize.•Menu 1–Synchronizer•Menu 2–Load Control•Menu 3–Load Limits and Switches•Menu 4–Process Control•Menu 5–Configuration•Menu 6–Calibration•Menu 7–Electric Parameters•Menu 8–Control Status Monitor•Menu 9–Discrete Inputs/Outputs•Menu 0–DiagnosticsTypical Wiring ConnectionsSPECIFICATIONSEnvironmental SpecificationsOperating Temperature.....................................................–40 to +70 °C (–40 to +158 °F)Storage Temperature........................................................–55 to +105 °C (–67 to +221 °F) Humidity...............................................................................95% at 38 °CElectromagnetic Susceptibility.........................................ANSI/IEEE C37.90.2; ANSI C37.90.1-1989Mechanical MIL-STD 810C, Method 516.2, Procedures I, II, V MIL-STD 167, Type IElectrical SpecificationsControl Power Supply Input Operating.............................................................................8–32 Vdc continuous (as low as 10 Vdc, 1.8 A max, or as high as 77 Vdc for upto 5 min) Reverse................................................................................–56 Vdc continuous Burden..................................................................................18 W, 1 A maximumVoltage Sensing Inputs120 Vac Input (L-N) Wye PT Configuration....................65–150 Vac, terminals 4–5, 7–12, 9–12, and 11–12240 Vac Input (L-N) Wye PT Configuration....................150–300 Vac, terminals 3–5, 6–12, 8–12, and 10–12120 Vac Open Delta PT Configuration...........................65–150 Vac, terminals 3–5, 6–8, 8–10, and 10–6240 Vac Open Delta PT Configuration...........................150–300 Vac, terminals 3–5, 6–8, 8–10, and 10–6 Phases.................................................................................Three phase utility bus, single phase generator bus Frequency............................................................................45–66 Hz Burden..................................................................................Less than 0.1 VA per phase Accuracy...............................................................................0.1% of full scaleCurrent Transformer Inputs (CTs) Current..................................................................................0–5 Arms, 7 Arms max. Frequency............................................................................56 to 66 Hz Burden..................................................................................Less than 0.1 VA per phase Accuracy...............................................................................0.1% of full scale Phases.................................................................................Three phase utility busDiscrete Inputs ...................................................................18–40 Vdc @ 10 mAAnalog Inputs......................................................................4–20 mA @ 243 A or 1-5 Vdc @ 10 k AAnalog Outputs...................................................................Speed Bias: ±2.5 Vdc, 0.5–4.5 Vdc, 1–5 Vdc across 243 A, or 500 Hz PWMVoltage Bias: high in ±9 Vdc, low in ±3 Vdc, current 50 mARelay Driver Outputs..........................................................18–40 Vdc @ 200 mA sinkLocal Area Network ...........................................................Echelon® LonWorks™ Technology, Standard Protocol, 1.25 MBPS Calibration and Diagnostics Port ...................................RS-422ComplianceUL/cUL..................................................................................ListedMSLC PartVersion N umberWye, 120 or 240 Vac9907-004Open delta, 120 Vac9907-005Open delta, 240 Vac9907-006MSLC/DSLC Hand Held Programmer9907-205PO Box 15191000 East Drake Road Fort Collins CO, USA 80522-1519Ph: (1)(970) 482-5811 Fax: (1)(970) 498-3058 Plants & Subsidiaries Australia (New South Wales) Brazil (Campinas)China (Tianjin)Germany (Aken/Elbe)India (Haryana)Japan (Tomisato & Kobe) Netherlands (Hoofddorp & Rotterdam)SingaporeUK (Reading, England, & Prestwick, Scotland)US (Colorado, Illinois, Michigan, New York, South Carolina, Tennessee) Branch/Regional Offices China (Beijing)Czech Republic (Plzen) Germany (Tettnang)Korea (Pusan)Mexico (Mexico City)New Zealand (Christchurch) Poland (Warsaw)UAE (Abu Dhabi)UK (Dundee, Scotland)US (Alabama, California, Illinois, Pennsylvania, Texas, Washington) Distributors & Service Woodward has an international network of distributors and service facilities. For your nearest representative call(1)(800) 835-5182 or see the Worldwide Directory on our web site (). CORPORATE HEADQUARTERS Rockford IL, USAPh: (1)(815) 877-7441T his document is distributed for informational purposes only. It is not to be construed as creating or becoming part of any Woodward Governor Company contractual or warranty obligation unless expressly stated in a written sales contract.© Woodward Governor Company, 1993All Rights ReservedMSLC Outline DrawingDSLC™ Control in a Parallel Bus/Utility Parallel Application with an MSLC (Master Synchronizer and Load Control)For more information contact:99/7/F。
- 1、下载文档前请自行甄别文档内容的完整性,平台不提供额外的编辑、内容补充、找答案等附加服务。
- 2、"仅部分预览"的文档,不可在线预览部分如存在完整性等问题,可反馈申请退款(可完整预览的文档不适用该条件!)。
- 3、如文档侵犯您的权益,请联系客服反馈,我们会尽快为您处理(人工客服工作时间:9:00-18:30)。
702L o c o A P P L I C A T I O N S702 LOCOMOTIVE CONTROL702 BLOCK DIAGRAMR a c k L i m i t e r I n p u t ..........................................................4 to 20 mA or 1 to 5 Vdc from turbo boost pressure sensor R e m o t e S p e e d S e t t i n g I n p u t ........................................4 to 20 mA or 1 to 5 Vdc for remotely setting engine speed O U T P U T SA c t u a t o r ........................................................................0 to 200 mAS e r i a l P o r t ......................................................................20 mA current loop with a 9-pin D connector. The serial portoperates in full duplex at a baud rate of 1200. The control includes 20 mA current sources and terminal power for the Woodward hand-held control/display terminal. The serial port is compatible with other terminals and computers with 20 mA current-loop serial port. Used for initial setup and diagnostics only.T a c h o m e t e r O u t p u t ......................................................4 to 20 mA for an analog meter or as input to a computer, ormay optionally be configured for 4 to 20 mA proportional to actuator current for input to a load control A D J U S T M E N T SAll adjustments are performed with either the Woodward Set Point Programmer or optionally with a standard ASCII character computer terminal with a 20 mA current-loop serial port.T h e c o n t r o l h a s f i v e c o n v e n i e n t "m e n u s " f o r o p e r a t i o n a n d a d j u s t m e n t :After all set points are adjusted to the desired value, they are saved permanently by the control in nonvolatile memory integrated circuits, which do not require batteries or other power sources to retain data. Entries can be changed at any time using the Set Point Programmer.M e n u A D y n a m i c s M e n u Gain ResetCompensation Gain Ratio Window Width Gain Slope Gain BreakpointM e n u B S p e e d S e t t i n g M e n u 16 Speed Codes (Code 0 through Code 15)Accel Time Decel Time Raise Rate Lower Rate20 mA Remote Reference 4 mA Remote Reference 20 mA Tachometer RPM 4 mA Tachometer RPM Droop idle Droop Idle BreakpointM e n u C R a c k L i m i t e r s a n d C o n t r o l O u t p u t M e n uRack Limit Breakpoint 4 mA Rack Limit Breakpoint Rack Limit 20 mA Rack Limit Torque Limit Breakpoint Minimum Torque Limit Breakpoint Torque Limit Maximum Torque Limit Start Fuel Limit 20 mA Aux Output 4 mA Aux OutputM e n u D D i s p l a y M e n u Engine Speed Speed Reference Actuator Output Aux Output Rack Limit Input Remote Input Notch Code Selected Run/Stop Switch StatusFailsafe On/Off Switch Status Watchdog Status Self Test Result ROM Check SumM e n u 1 C a l i b r a t i o n /C o n f i g u r a t i o n M e n uCalibration Key Number of Gear Teeth Rack Limit Calibration Remote Input Calibration Aux Output Configuration Aux Output CalibrationForward/Reverse Acting Actuator Dynamics Map3800 N. Wilson Ave. P.O. Box 3800 Loveland, CO, U.S.A. 80539-3800Ph: 1 970-663-3900 Ph: 1 800-835-5182 Fax: 1 970-962-7050 w w w.w o o d w a r d.c o mI n t e r n a t i o n a l P l a n t sA u s t r a l i a,New South WalesB r a z i l,CampinasC h i n a,TianjinG e r m a n y,Aken/Elbe & KelbraI n d i a,HaryanaJ a p a n,Tomisato & KobeN e t h e r l a n d s,Hoofddorp & RotterdamS i n g a p o r eU n i t e d K i n g d o m,Reading, England, & Prestwick, ScotlandU n i t e d S t a t e s,Colorado[2], Illinois[3], Michigan[2], New York, South Carolina, TennesseeR e g i o n a l S a l e s O f f i c e sC a n a d a,QuébecC h i n a,BeijingC z e c h R e p u b l i c,PlzenG e r m a n y,TettnangK o r e a,PusanM e x i c o,Mexico CityN e w Z e a l a n d,ChristchurchP o l a n d,WarsawU n i t e d A r a b E m i r a t e s,Abu Dhabi U n i t e d S t a t e s,Alabama, California, Illinois, Pennsylvania, Texas, WashingtonD i s t r i b u t o r s&S e r v i c e Woodward has a network of distributors and service facilities. For your nearest representative call 1 800-835-5182 or see the Worldwide Directory on our web site. CORPORATE HEADQUARTERS/ AIRCRAFT CONTROLS Rockford, IL, U.S.A.1 815-877-7441This document is distributed for informational purposes only. It is not to be construed as creating or becoming part of any Woodward Governor Company contractual or warranty obligation unless expressly stated in a written sales contract.©W o o d w a r d G o v e r n o rC o m p a n y,1990A l l R i g h t s R e s e r v e dFor more information contact:SET POINT PROGRAMMER98/9/L。