管带式汽车散热器试验及数值模拟研究
管带式散热器(二)

第 二对 滚轮 再 进 一 步成 形
图
6
列出
法
。
蘸
: 二二 日 一}
-
二!
目 l口
1 州
,
甘 一
匡
}
l:
三
「1 比 二司 司r- 几 .
团口I 旧 ;
】l 旧习 习
二二 二
; 葬
l 一 业 朴 孔 韭 不 匕| 法 扮 准 派 ù 琳 孤 洲轮 侧 习 滚 ù 反 ù 阵 一 翎 川 “意 步训 习形 成 创 引 贬 区 ì )“ 日 b 到 胜不 卜 1 非 m | ó
,
.
C
二 二二 二 二 二 二
,
J
毛 吕
l
「
l
r 一
一
一
矛 s e
曰令 引 一 日 产 一~ - 州
~
健 旦比 一 一 ,竺口 r- 一 一 卜 _ 二 一 一 r忙 l C 二 二 二二 二 1二 二 二 : 二 二二 二二 :
二 二 二佗 t二
一 井
_
看 群矍哪 一
二` 川 ` 舀二小川
r
卜
珊
j
勤
管 带 式 散 热 器 既 有较 多 优 点 国 却 尚 未大 量 投入 生产
,
,
但 在我
。
其 关键 即 在 于 制
切 出百 叶窗 式 的
一 丫 门
、
\
造 波 纹 带 的 滚 轮 刀 具 的设 计 和制 造 问 题
要 在 滚 制 波纹 带 的 同 时 切 口来
。
,
题 一 度 由美 国 利佛 脑 思 公 司 所 垄 断 方式
的关 系
姗 衅
切 口 角度叹
汽车散热器的优化设计及传热性能分析的研究

厂家 生产 成本 的 目标 。最 后形 成管 带式散 热器 设计 、校 核 、优 化 一体 的设计分 析 。散热 器 的传热与流动阻力计算程序 ,计算结果与实验数据在常规工况范围内基本吻合。运用 图解 的方法分 析 了散热器结 构参数 与材 质对 散热器流 动阻 力与散热性 能的影 响。 关键词 : 汽车散热器 ;传热 ;风阻 ;电偶保护
百 叶窗 的 管带 式 散 热 器 内 的传 热 与 流 动 阻力 特 性
进 行 了研 究 ,编 制 了汽 车 散 热 器 的 传 热 与 流 动 阻
力 计 算 程 序 ,并 由此 分 析 了散 热 器 进 口水 温 为 9 ℃,进 口风 温 为 o
l
匐 化
汽车散热器 的优化设计及传热性 能分析 的研究
A u om obie r t l adi ors i pr v at ' m o em entdesi gn and heatt ans ercap r f abiiy al z lt an y e
关凤艳
由 图 中可 知 ,理 论 值 与 实 测值 基 本 吻 合 ,最
大相对偏差为 8 %,且在高风速区域误差较大。 . 9
中图分 类号 :U 6 43 文献标识码 :B 文章编号 :1 0 —0 3 ( 0 1 7 下) 1 3 3 9 1 4 2 1 ) ( 一04 —0 0
Do: .9 9J Is .0 9 1 4 2 1 . ( ) 4 i1 3 6l . n 1 0-0 .0 1 7 下 .0 0 / s 3
用 S I 0M7A 表 面轮 廓度 、粗 糙度 测试 仪 测量 , U1 C 5 结果 见 表 2 。表 中各 符号 的定 义如 表 1 所示 。
表 1 C 型汽车散热器结构参 数 6
车用热管散热器的数值模拟与设计

车用热管散热器的数值模拟与设计朱晓琼;胡念苏;余万【摘要】随着我国城市轨道交通的快速发展,解决机车电力电子设备的散热问题显得尤为迫切,热管散热器因其结构紧凑、散热能力大、散热效率高等优势受到了越来越多的关注.本文针对某轨道交通车辆牵引控制系统的某单元的散热问题进行了研究,根据设计要求建立了热管散热器的数值模型,得到了其不同工况下的温度场分布和风道阻力特性,分析了翅片间距、热管数、热管长度等对基板最大温升和散热器风阻的影响,设计出了能够保证功率元件安全可靠工作的热管散热器.经测试其热阻及风阻特性与模拟结果的误差均在5%以内,满足工程设计要求.【期刊名称】《三峡大学学报(自然科学版)》【年(卷),期】2016(038)003【总页数】5页(P90-94)【关键词】热管散热器;热阻;风阻;温升【作者】朱晓琼;胡念苏;余万【作者单位】上海威特力热管散热器有限公司,上海201318;武汉大学动力与机械学院,武汉430072;三峡大学机械与动力学院,湖北宜昌 443002【正文语种】中文【中图分类】TK172.4随着我国城市轨道交通的快速发展,解决机车电力电子设备的散热问题显得尤为迫切.轨道交通车辆牵引控制系统的散热系统,主要是针对功率元件来设计,原因在于系统中发热绝大部分来自于功率开关元件(如IGBT、整流桥等)的损耗功率.功率开关元件本身对温度比较敏感,温度的变化会影响元件的开通、关断过程,影响元件的工作性能.当温度过度增高时,甚至会导致元件的永久性损坏,带来极大的安全隐患,直接影响列车运行的安全性和可靠性.随着电子技术的发展,电子元器件不断地向小型化、微小型化和集成化方向发展,同时设备的组装密度也在不断提高,导致单位面积的热流密度迅速增加,如果不能采用合理的散热技术,必将严重影响电子器件及系统的工作[1].热管作为一种新型的高效传热元件,由于其热阻小、重量轻、导热性能好等优点已经成为解决高热流密度发热元件冷却问题的重要途径[2-3].热管散热器的性能与很多参数相关,如冷却条件、结构尺寸等,如何选择或设计合理的热管散热器是解决机车电力电子设备的散热问题的关键.本文针对某轨道交通车辆牵引控制系统的某单元的散热问题进行了研究,采用CFD软件Flotherm建立了热管散热器的CFD模型,得到了其不同工况下的温度场分布和风道阻力特性,分析了翅片间距、热管数、热管长度等对基板最大温升和散热器风阻的影响,并进行了实验验证,最终设计出了能够保证功率元件安全可靠工作的热管散热器.轨道交通车辆牵引控制系统内的散热系统通常由多单元组成,以适应功率元件的灵活排布、组装及各单元不同的散热需求.目前,在轨道交通车辆牵引控制系统的散热系统中,一般有风冷和水冷散热两种方式.有资料表明[4],强制风冷的散热效果是自然冷却的5~10倍,水冷的散热效果是自然冷却的120~150倍.虽然水冷具有极高的散热效率,但通常由于辅助水循环系统的存在,导致整个系统的结构复杂,成本较高,因此风冷的应用更为广泛.轨道交通车辆在运行过程中,功率器件的散热器的外部冷却条件一般按走行风考虑.由于车辆速度较快,站点间距小,启停频繁,其牵引控制系统的散热功率较大,散热器常处于非稳态散热状态,启动之初和停车制动时车速较小,外部气流掠过散热器的风速较小,但此时发热量较大,在平稳运行时散热功率较小,外部气流掠过散热器的风速较大,因此,散热器设计时既要考虑自然冷却工况,又要考虑一定风速条件下的强制风冷工况.本文针对其中某竖直安装使用的单元的散热问题展开研究,该单元采用自然冷却和强制风冷结合的热管散热系统.该单元的元件排布和散热部分受限体积如图1所示,它由9个元器件组成,总功耗为Qh=4 070 W,元器件与散热器分别装在基板的两侧,最大外形尺寸为876 mm×501 mm×353 mm(长×宽×高).为保证元件的安全工作,在环境温度Tair=40℃时,散热器元件安装面的温度及散热器的风阻要求见表1.2.1 热管散热器的设计原理功率元件的工作效率无法达到100%,其工作中的能耗最终以热耗形式体现出来,热量自功率元件内部通过三种方式(传导、对流和辐射)传至外界环境.如同电流流过电路受到电阻的阻碍一样,热流传递时也会受到阻碍,称为热阻.在分析热传递过程时,常采用比拟电路分析中欧姆定律(R=U/I)的方法,以温差Δt比拟欧姆定律中的电压势差Δu,以热流量q比拟欧姆定律中的电流i,则有:热阻Rth=Δt/q,单位为℃/W,Δt为通过所分析的热传递环节的温度差,单位为℃,q 为通过的热流量,单位为W.若将功率元件的热流路径以封装(壳体)外表面为界划分为内、外两部分,对应的热阻分别为内热阻和外热阻.当元件封装完成后,其内热阻就基本固定.散热器热设计的原理就是通过对散热器结构和冷却方式等的合理设计,不断调整热流路径的外热阻,从而控制元件的温升在允许范围内.必要时,还需考虑产品的工艺可行性和经济性.2.2 初始物理模型的建立由设计参数可知,本课题需设计的热管散热器应满足如下要求:Tair=40℃时,热管散热器热阻及风阻要求:自然冷却时热阻Rth≤0.018 9 ℃/W(即最大温升≤77℃);风速v=2 m/s时,热阻Rth≤0.009 1 ℃/W(即最大温升≤37℃),风阻≤15 Pa;风速v=4 m/s时,热阻Rth≤0.006 6 ℃/W(即最大温升≤27℃),风阻≤54 Pa;热管散热器体积限制在876 mm×501 mm×353 mm以内.由传热方程式:式中,q为热流量(W);Δt为传热温差(℃);K为传热系数(W/(m2·℃)).已知q 和Δt,代入经验传热系数K,先初步核算出所需散热面积F,建立如图2所示的物理模型.2.3 热阻网络模型的建立在强制风冷时,辐射换热量可忽略不计,则其热阻网络如图3所示.其中Qh为单元总功耗(W);Tair为环境温度;Tref为参考温度(分析散热器时指模块安装面的温度).Rth1为基板导热热阻,代表基板一侧接收热源热量并传至另一侧的环节的热阻;为基板对流换热热阻,代表基板表面直接与空气接触的部分通过对流将热量传至空气中的环节;Rth2为热管导热热阻,代表热管接收基板传过来的热量并传给翅片的环节的热阻;为热管的对流换热热阻,代表热管外表面直接与空气接触的部分通过对流将热量传至空气中的环节的热阻;Rth3为翅片的综合热阻,代表翅片接收热管传递的热量后通过导热在翅片上传导并通过对流在翅片与空气界面上换热的环节的热阻.2.4 强制风冷散热CFD模型的建立图2所示的模型是典型的热管散热器模型,在强制风冷系统中整个散热系统由风机、风道、热管散热器和热源组成,其中的热管散热器由热管、基板、翅片组成.散热系统的建模过程简述如下:1)热管散热器:依据热管的物理几何特征并结合对现有热管产品的性能测试确定其传热系数,最终建立超导热管的模型;依据物理几何特征建立翅片和基板的模型;2)风机:根据给定的风速条件,风机采用定流量风机模型;3)风道:根据系统实际通流边界建立模型;并设为绝热边界条件,忽略其散热量;4)热源:实际热源为形状复杂的功率元件IGBT或二极管,安装时与基板有固定的接触面积,建模时将其简化为分布在基板上的9个面积与之对应的均匀发热的面热源,记为H1,H2,…,H9;并假定所有热量均由散热器带走.5)求解域的确定:本模型用于强制风冷条件下的热分析,热量主要由主流方向上的冷却风带走,由风道壁面散失的热量极小,以散热器作为求解主体并将求解域扩大到整个风道时,求解域尺寸为:x=1 626 mm,y=363 mm,z=511 mm.6)网格的划分:基于有限体积法的思想,利用网格将求解域内的体积分成若干微小的控制体,对各控制体建立控制方程并联立求解得到温度场和流场等.对整个求解域合理划分网格,在边界处、热流或气流变化剧烈处进行局域化并加密网格.如翅片和基板区域,翅片选用1 mm厚的铝片,厚度尺寸相对整个求解域较小,对翅片区进行网格加密以使所有翅片上均能生成网格节点.基板的模块安装面上的温度分布是设计重点关注的区域,且基板上热量集中,对基板区域加密网格可使温度场求解更为准确;7)温度监控点设置:在基板上各热源中心布置温度监控点,用以监控温度的变化;8)其他设置:①环境温度:设为40℃;②流体种类:设为海拔0 m,1个大气压下的空气;③材料属性及热物性设置:如翅片材料设为Al1060,导热系数λ=201 W/(m·K),密度ρ=2.71×103 kg/m3,比热容c= 913 J/(kg·K)等;④求解器属性:迭代次数设为500,收敛判断精度设为0.5℃.2.5 自然冷却散热CFD模型的建立自然冷却散热模型与强制风冷模型相比,不同点主要体现在求解域设定和对辐射散热的考虑.首先在重力方向上,需扩大求解域求解.其次在自然冷却时,散热主要依靠自然对流和辐射,辐射的影响不可忽略,建模时需启用辐射模式,并对各材料设置合适的辐射系数.采用迭代算法对建立的热管散热器模型进行了求解,得到了不同工况下散热器的温度场,如图4所示为强制风冷迎面风速为2 m/s时的散热器温度场分布云图.同时也对各个工况下各个监测点的温升和流道的风阻进行了计算,得出了基板的最大温升和风阻在不同工况下的变化规律,从而可以找出热管散热器的主要结构参数对传热性能的影响.3.1 翅片间距对传热性能的影响图5给出了翅片间距在7~11 mm时,在不同冷却条件下基板的最高温升.从图中可以看出在自然冷却条件下,随着翅片间距的增大,最高温升先下降后上升.这是因为翅片间距过小时,不利于自然对流,虽然换热面积充裕,但自然对流换热系数较小,因此温升较高;随着翅片间距的增大,自然对流效果得到改善,温升逐渐降低,当降低到一定程度后,翅片间距对自然对流换热系数的影响减弱,此时,由于翅片间距加大导致的面积减少起主导作用,面积减少导致温升升高.在强制风冷条件下,随着翅片间距的增大,最高温升先下降后上升.在翅片间距较小时,最高温升的变化不明显.这是因为该结构下,强制对流时的面积相对已有富余,再减小翅片间距增加换热面积对温升的影响较小,此时改变风速影响较大,如图5可见,风速4 m/s时相对2 m/s温升有明显降低.翅片间距增大后,面积减少的影响逐渐体现出来,使得温升随之升高.从图中可以看出,无论是采用自然冷却还是强制冷却,翅片间距为9 mm时基板最高温升均为最小.图6给出了翅片间距在7 mm至11 mm时,在不同冷却条件下风阻的变化.发现风阻随着翅片间距增大时在不断降低.从图5和图6发现,满足不同冷却条件下基板的最高温升设计要求的翅片间距为7 mm、8 mm、9 mm,但翅片间距为7 mm、8 mm时的风阻超出了设计要求,因此可以认为在本热管散热器的设计中,翅片间距采用9 mm比较合适.3.2 热管数对传热性能的影响图7给出了在不同冷却条件下基板的最高温升随着热管数的变化情况.可以看出热管数对最高温升的影响比较大,随着热管数的增加,最高温升呈现出先减小后增大的趋势.这主要是由于热管数的增加会使得换热面积增大,从而使得散热效果更好.随着热管数的进一步增加,空气的流动将会受到影响,使对流换热减弱,导致散热效果变差.从图7可看出,热管数在150左右拥有最小的温升.根据设计要求,3种冷却条件下最高温升应分别低于77℃、37℃、27℃.图8给出了在不同冷却条件下风阻随着热管数的变化情况.可以看出随着热管数的增加,风阻也在不断上升.这主要是由于热管数的增加会使得管间距变小,流动阻力变大.从图8中可以看出,热管数在150左右时强制冷却的风阻满足设计要求,分别低于15 Pa和54 Pa.在热管散热器中热管是嵌入基板内部的,结合图1中元件安装位置的要求,在设计中发现,采用151根热管时可较好地避免热管与模块安装空位的几何干涉.因此,最终选用151根热管.3.3 热管长度对传热性能的影响考虑到车载系统中各结构轻量化的要求,为了减重和降低风阻,结合仿真云图,将未发挥最大传热效果即热管顶端温度相对较低的一部分热管的长度进行缩短,图9和图10分别给出了基板的最高温升和风阻随着热管长度的不同的变化规律.从图中可以看出,最高温升随着热管长度的缩短会略有上升,这是由于热管长度缩短会导致换热面积减小,散热效果削弱,与此同时风阻随着热管长度的缩短会逐渐减小.由图9可见,当热管长度缩短至150 mm和120 mm,各工况下均仍能满足最高温升要求,但当缩短至90 mm时,基板最高温升在强制冷却工况下分别超过37℃和27℃.由图10可见,当热管长度在150 mm时,风阻超出设计要求,当热管长度缩短至120 mm和90 mm时,风阻满足要求.根据最高温升和风阻的设计要求,最终缩短的热管长度选用120 mm.3.4 热管散热器的实验根据CFD模拟结果并结合实际制造工艺,制作了热管散热器样品,如图11所示,并按照设计工况对该样品实施了热阻和风阻的模拟测试.将数值模拟结果与实测结果进行比较,结果如表2所示.可见在自然冷却以及风速为2 m/s和4 m/s强制冷却条件下,基板的最大温升和风阻实测结果与模拟结果相对误差均在5%以内,同时也符合工程设计要求.1)采用CFD软件进行轨道交通车辆牵引控制系统的散热系统的设计,可以较为准确地模拟散热器产品的温度场和阻力特性,有助于确定热管散热器的结构.2)对影响热管散热器传热性能的主要几何因素进行了分析,发现翅片间距为9 mm,热管数为151根,热管长度为120 mm时,散热器拥有最佳的散热性能.3)本文中所开发的适用于轨道交通车辆牵引控制系统的热管散热器产品,其散热性能优越:在自然冷却工况下使用时,散热能力达4 070 W,热阻<0.016 3℃/W;该产品经测试其热阻及风阻特性与模拟结果的误差均在5%以内,满足工程设计要求,不仅为产品最终进入市场奠定了良好的基础,也为今后设计此类大功率强制风冷的热管散热器产品积累了成功的经验.【相关文献】[1] 王博,宣益民,李强.微/纳尺度高功率电子器件产热与传热特性[J].科学通报,2012,57(33):3195-3204.[2] 牛志愿,张伟.脉动热管应用技术研究进展[J].节能技术,2014,32(1):22-27.[3] Rahman M L, Nawrin S, Sultan R A, et al. Effect of Fin and Insert on the Performance Characteristics of Close Loop Pulsating Heat Pipe(CLPHP)Procedia Engineering, 2015, 105:129-136.[4] 胡建辉,李锦庚,邹继斌,等.变频器中的IGBT模块损耗计算及散热系统设计[J].电工技术学报,2009,24(3):159-163.。
车用散热器传热性能的数值模拟研究

车用散热器传热性能的数值模拟研究密腾阁;王舫;龙云【摘要】车用散热器作为汽车冷却系统的重要构成部分,其工作性能的优劣将直接影响到汽车发动机的运行状态,进而影响汽车行驶安全.文章采用数值模拟的方法,通过建立散热器百叶窗翅片的三维数值模型,研究不同进口空气流速及翅片重要几何结构参数—翅片间距、百叶窗宽度、开窗角度,对散热器传热性能的影响.结果表明:随着散热器进口空气流速增大,散热器的换热系数与压降损失也逐渐增大;结构模拟优化后发现,散热器结构参数在翅片间距为2.50mm,百叶窗宽度6.00mm,开窗角度为23°时,换热性能及阻力性能皆最佳;可为车用散热器优化设计提供参考依据.【期刊名称】《汽车实用技术》【年(卷),期】2017(000)015【总页数】5页(P140-144)【关键词】车用散热器;传热性能;数值模拟【作者】密腾阁;王舫;龙云【作者单位】南华大学,湖南衡阳 421001;南华大学,湖南衡阳 421001;南华大学,湖南衡阳 421001【正文语种】中文【中图分类】U462.1CLC NO.:U462.1 Document Code: A Article ID: 1671-7988 (2017)15-140-05 散热器作为汽车冷却系统的重要组成部分,其工作性能的优劣直接影响发动机的寿命、功率、排放行为以及经济性[1]。
百叶窗式翅片散热器因其结构紧凑、换热性能良好且成本较低的优点被车用冷却系统频繁采用。
随着汽车工业的迅猛发展,对汽车发动机冷却系统的要求日渐提高[2]。
为适应发动机不断增加的热负荷,并局限于发动机舱有限的空间,迫切需要对散热器进行散热性能的优化设计。
目前对百叶窗翅片散热器常用的优化设计方法有实验研究和数值模拟研究两种方法。
实验研究主要是通过风洞实验方法测试百叶窗翅片散热器在不同材质、不同布置形式、不同结构形式下的传热性能和流动阻力性能。
例如A.Vaisi[3]通过风洞实验方法对百叶窗翅片式散热器百叶窗区域的布置方式进行研究,获得了散热器空气侧的传热和压降特性,结果表明百叶窗区域的布置方式对散热器的传热和压降特性有比较大的影响。
管带式汽车散热器传热与阻力预测模型的建立
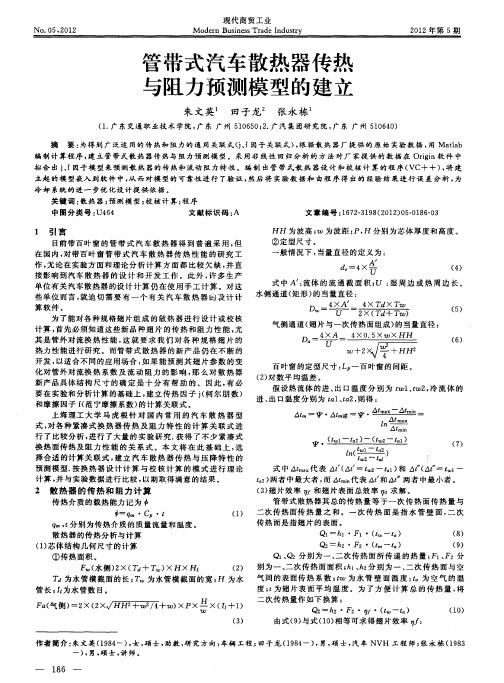
0 0 7 . 9 6
0 0 2 . 90 0 0 0 . 8 2 0 0 2 . 8 1
Q一 — ——T—— ———
1 - 1
・(~ 一 £ ) £ ( 6 1)h ・F ・ d
。 ・F h
由于在 热交 换器 中, 体 的温度 通 常是沿 流程 变化 的 , 流 所 以将 (6 式 中 的两 流 体 温 差取 为对 数 平 均 温 差 △ , 得 : 1) 则
一
), , 士 , 师 。 男 硕 讲
一
16 — 8
N o. 05, 12 20
现 代 商 贸 工 业 M o enB s es rd n uty d r ui s T a eId s n r
2 1 第 5期 0 2年
' I f一
( 1 1)
表2 2 #散 热 器 的 J因 子 值 和 , 因 子值 f
N o. 05, 012 2
现代 商贸工业 Mo enB s es rd n ut d r ui s T aeId s y n r
21 第 5 0 2年 期
管带式汽车散热 器传热 与阻 力预测 模 型 的 建 立
朱 文 英 田子 龙 张 永 栋
( . 东 交 通 职 业 技 术 学 院 , 东 广 州 5 0 5 ;. 汽 集 团研 究 院 , 东 广 州 5 0 4 ) 1广 广 16 0 2 广 广 1 6 0
m a
—
—
—
ax
_
.
.
.
.
2 散热 器 的传热 和 阻力计 算
传 热 介 质 的 载 热 能力 记 为
' I 一 ・Cp・t () 1
q £ 别为传热 介质 的质量流量 和温度 。 m,分 散 热 器 的 传 热 分 析 与 计 算
非均匀进风管带式汽车散热器数值模拟研究

图1风速分布
本文研究的散热器,其所有壁面都是静止的且没 有表面化学反应,忽略热辐射,所以主要设置壁面热 力学边界条件。因在传热风洞试验中对测量段和试 验段都进行了严格的隔热保温,因此空气通道外壁和 水室外壁都假定壁面为绝热的,即热通量设置为0。 因为水管壁简化成相应壁厚的双侧壁面,所以只需在 计算中选择把正反侧面耦合起来,求解器就能直接用 邻近网格的流场变量计算壁面上的热交换。 本文的边界条件设置情况为进风口和进水口采
35.00 35.00
出风温度/℃
105.86 108.82
散热i'/kW
133.72 139.18
吸热量/kw
133.86 139.60
风I垂【/Pa
124.29 124.29
不均匀4.00 不均匀
6.00
温度,℃
温度/。C
温度,℃
黑}萎
91
溅
空气
9l
83
黔
空气 空气
匕=二:>
鍪隧震
%
昭;2酊
59
ks/s;P为水的密度,P=
m/s,Ⅳ=3.948 m/s。
kg/m3;S为管道横截面积,m2;d为水管直径,
mm。算出Ⅳ=2.632
2数值模拟
2.1换热量的计算 换热量是设计散热器时要达到的主要技术要求 之一。 水侧放热量Q。:
Q。=qwc。。(t。1一tw2)
图3空气流入域划分形式
其中:q。为水的质量流量,kg/s;C。为水的定压比 热,J/kg・K,利用水进、出口温度的平均值采用线性 插值的方法求解;£。。为水的进口温度,oC;t吡为水的
Non-unifornl into Duct Tape Car Radiator Numerical Simulation Research
汽车管带式散热器仿真设计方法的研究

第32卷第2期2011年4月内 燃 机 工 程Chinese Internal Combustion Eng ine Eng ineeringVo l.32No.2Apr il.2011收稿日期:2009-08-24基金项目:国家 八六三 高技术研究发展计划现代交通技术领域 汽车开发先进技术 重点项目(2006AA110104)作者简介:袁兆成(1954-),男,教授,博士,主要研究方向为内燃机现代设计理论与方法,E -mail:yuanzc@ 。
文章编号:1000-0925(2011)02-0085-04320034汽车管带式散热器仿真设计方法的研究袁兆成1,朱 晴1,王 吉2,王宏志2,常 贺3(1.吉林大学汽车动态模拟国家重点实验室,长春130000;2.一汽集团技术中心,长春130000;3.一汽轿车股份有限公司,长春130000)S tudy on Simulation Design Method of Corrugated Tube Radiator for AutomobileYUAN Zhao -cheng 1,ZHU Qing 1,WANG Ji 2,WANG Hong -zhi 2,CHANG He3(1.State Key Laboratory of Automo bile Dynam ic Simulatio n,Jilin U niversity,Changchun 130000,China;2.FAW T echno logy Center,Changchun 130000,China;3.FAW CAR Co.,Ltd.,Chang chun 130000,China)Abstract:Using CFD technique,the simulation design method of autom otive radiator with complexstructure w as studied.T he radiator w as partially simulated to calculate the heat ex change coefficient betw een cor rug ated band and cooling air,and the effects of the radiator louver opening angle on r adiator heat ex change perform ance w er e analy zed from three aspects of tem perature,pressure and flow v elo city.It is con -cluded that the best effect is achieved at 23 o pening ang le.T he heat transfer perform ance of w ho le radiator w as calculated by using po rous medium to imitate the heat transfer coefficient and flow resistance of the fin -louver heat dissipation band.T he calculated results coincide w ith the m easured data.T his sim ulation desig n method prov ides the possibility for radiator optimization design.摘要:利用CFD 手段对结构复杂的管带式散热器仿真设计方法进行了研究,采用散热器局部完全仿真计算分析得到管带与空气的热交换系数,并从温度、压力和速度三方面分析了散热片开窗角度对其换热性能的影响,得出开窗23 时换热效果最好,又利用多孔介质模拟开窗散热带,进行整体散热器的传热性能仿真模拟计算。
管带式汽车散热器的优化设计及计算软件开发

江苏大学硕士学位论文管带式汽车散热器的优化设计及计算软件开发姓名:杨志坚申请学位级别:硕士专业:热能与动力工程指导教师:魏琪20060401铜质散热器和钎焊式铝散热器为行业的主导产品。
1.2汽车散热器的基本结构散热器是由冷却用的散热器芯子、贮存冷却液的上水室和下水室3部分组成的。
由于散热器工作时会产生水蒸气,所以上水室还承担着气水分离的作用。
图(i-i)直流式散热器1.散热器2.上水室3.下水室4.散热器芯子散热器芯子是散热器的核心部分,起主要的散热作用。
散热器芯子由散热管、散热片(或散热带)、上下主片等组成。
由于它具有足够的散热面积,因此能保证将必须的热量从发动机散发到周围的大气中去。
而且散热器芯子是用极薄的导热性能好的金属及其合金制造的,能使散热器芯子以最小的质量和尺寸达到最高的散热效果。
图(卜2)管带式图(卜3)管片式圜散热器芯子根据翅片的排列方式,主要分为管片式图(卜3)和管带式图(卜2)。
对于管片式芯子,它是由许多散热管和散热片组成。
散热管的外面串装了许多薄的金属平片(散热片)。
空气在平行的散热片及散热管的外表面所形成的风道中通过,从而使散热管内流动的冷却液得到冷却。
管片式散热器的主要特点是结2江苏大学硕士学位论文4.4管带式散热器的设计、校核与优化计算软件介绍为缩短厂家的设计周期、规范设计过程,本文采用Visualc++编制管带式散热器的设计、校核与优化计算软件。
Visualc++(简称vc抖)是美国微软公司推出的目前使用极为广泛的可视化编程平台,是一种强大的程序开发工具,它提供了一个集成环境,用于建立、调试Wmdows应用程序,从而大大简化了复杂的程序开发过程,提高了编程效率。
一、软件的主要功能简介软件打开后,由开始界面自动跳到主界面(图4—4),主界面采用下拉菜单的形式,菜单栏中有四项主要的功能,包括:设计、校核、优化、设计结果。
为了方便设计和校核计算结果的保存和比较,本文用vc++创建数据工程的方法创建数据库和数据表来保存设计和校核计算结果,数据源的类型选择MircrosoftAccess数据库,分别建立设计计算结果和校核计算结果两张数据表。
- 1、下载文档前请自行甄别文档内容的完整性,平台不提供额外的编辑、内容补充、找答案等附加服务。
- 2、"仅部分预览"的文档,不可在线预览部分如存在完整性等问题,可反馈申请退款(可完整预览的文档不适用该条件!)。
- 3、如文档侵犯您的权益,请联系客服反馈,我们会尽快为您处理(人工客服工作时间:9:00-18:30)。
管带式汽车散热器试验及数值模拟研究
为了提高汽车发动机的工作效率,自动化驾驶系统不断完善,汽车制造商不断推出更加节能高效的汽车,汽车散热器也必须跟进发展。
管带式散热器自面世以来,以其自身特点和结构上较传统散热器有所区别,受到人们的广泛关注和研究。
本文将重点介绍管带式汽车散热器的试验及数值模拟研究。
1、管带式汽车散热器试验研究
管带式散热器试验工作是验证构建的散热器在真实工况下的与性能,其中包括诸如压降、热负荷、温度分布、热流密度、传热性等多个性能指标。
有了试验数据就可以为数值模拟提供基础数据支撑,从而更加精细的研究管带式散热器的性能。
试验中一般会选取三种不同的风速和温度下进行实验,测试管带式散热器在不同工况下的性能表现。
试验结果显示,管带式散热器的传热面积更大、对冷却效果更为明显,对于车辆工作的高温环境和高速行驶都有很好的适应性。
2、数值模拟分析管带式散热器的散热性能
数值模拟是研究管带式汽车散热器最为有效的方法之一。
基于CFD软件(计算流体力学软件)完成的数值模拟可以定量分析散热器的冷却效果,为优化管带式散热器的结构设计提供依据。
在数值模拟中,需要构建三维实体模型,考虑结构和运动部件的影响因素进行相关的计算和分析。
根据实际的工况条件输入
相关参数,运用热力学和传热学原理进行计算,得到管带式散热器内部的温度和压力分布图,以及相关指标的数值计算结果,如温升、冷却效率、压降等。
这样得到的计算结果,能够指导管带式散热器的优化设计,进一步提高汽车的效率。
总结
管带式汽车散热器试验及数值模拟研究是提高汽车制造技术的重要途径之一,能够为技术改进提供科学依据。
本文重点介绍了试验和数值模拟两个方面的内容,分别从试验的流程、结果分析,和数值模拟的原理、应用和分析结果等方面进行具体的讲述。
管带式汽车散热器的研究还有很长的路要走,需要各方的全力支持和不断的研究探究。
除了试验和数值模拟研究,管带式汽车散热器的研究还有其他方面的支持。
例如,材料的选择、制造工艺、焊接技术等也都会影响到管带式汽车散热器的性能。
下面,我们来探讨一下这些方面的研究内容。
1、材料的选择与管带式散热器的性能
管带式散热器主要由散热鳍片、管带和集箱等几个部分组成,因此每个部分的材料在制造和使用中都有不同的要求。
通常情况下,散热鳍片和管带会使用铝合金材料,这种材料具有良好的导热性和机械强度,不易发生变形并且比较轻量。
而集箱则需要选择耐腐蚀性强的材料,例如钢铁材料或者不锈钢材料。
此外,管带式散热器的材料还要具有一定的可焊性和可加工性,这样才能有效提高其制造过程的效率和成本。
2、制造工艺与管带式散热器的性能
管带式散热器的制造工艺主要分为两种,一种是铸造法,另一种是冲压法。
铸造法能够制造出形状复杂的热交换器组件,但是生产周期比较长,并且成本较高。
而冲压法则效率更高,能够生产出大批量的组件。
但是由于该制造工艺的局限性,冲压法能够生产的热交换器组件形状相对来说更加简单。
因此,不同的制造工艺也有不同的优缺点,制造工艺的选择要根据具体情况来确定。
3、焊接技术与管带式散热器的性能
焊接技术是管带式散热器制造过程中最为重要的一环节。
焊接的质量直接影响到散热器的性能和耐久性。
目前,热力焊接和激光焊接是比较新颖和应用广泛的焊接技术。
热力焊接利用高温加热后的材料进行连接,而激光焊接则需要激光束对工件进行加热和焊接。
这两种焊接技术都能够保证连接的质量,并具有高效、环保等优点。
总结
管带式汽车散热器是现代汽车行业中不可或缺的一个组件。
通过试验、数值模拟、材料的选择、制造工艺和焊接技术等多个方面的研究,可以有效地提高管带式散热器的性能和效率。
在未来的发展过程中,不仅需要探讨管带式散热器的性能研究,还需要结合现代汽车行业的特点和需求,为管带式散热器的创新探索和推广提供更为深入和全面的指导和支持。
除此之外,
管带式汽车散热器的研究还有一些其他方面,如气动特性、结构优化等。
接下来,我们来探讨这些方面的研究内容和重要性。
1、气动特性与管带式散热器的性能
气动特性指的是在管带式散热器使用时,在高速行驶的情况下,空气流经散热器鳍片时的流动情况和阻力等问题,这对散热器的散热性能和车辆的加速性能等都有着重要的影响。
通过进行数值模拟和实验研究,可以有效地分析气动特性,并对散热器的设计和排列进行优化,提高其整体性能。
2、结构优化与管带式散热器的性能
结构优化主要是针对散热鳍片的形状、密度等方面进行优化,在不影响散热效果的前提下,最大限度地减少散热器的重量和体积。
同时也可以通过优化集箱和管带的结构等部分,更好地满足不同车型和使用场景下的气动特性和散热需求。
通过对管带式汽车散热器的多个方面进行研究,可以为其未来的发展提供更为深入和全面的指导和支持。
同时,在散热器性能的研究过程中,也能够带动材料、制造工艺、焊接技术等多个相关领域的发展,加快整个产业链的升级和转型。
因此,管带式汽车散热器的研究意义重大,具有广泛的应用前景。