注塑工艺及常见缺陷分析2剖析
注塑常见缺陷和原因分析
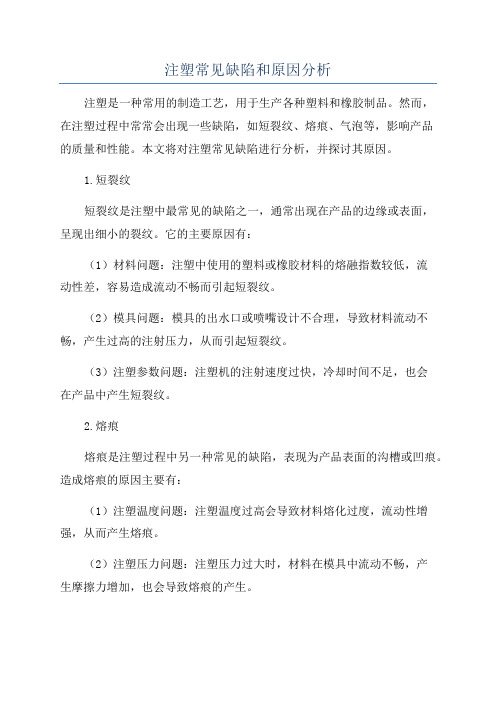
注塑常见缺陷和原因分析注塑是一种常用的制造工艺,用于生产各种塑料和橡胶制品。
然而,在注塑过程中常常会出现一些缺陷,如短裂纹、熔痕、气泡等,影响产品的质量和性能。
本文将对注塑常见缺陷进行分析,并探讨其原因。
1.短裂纹短裂纹是注塑中最常见的缺陷之一,通常出现在产品的边缘或表面,呈现出细小的裂纹。
它的主要原因有:(1)材料问题:注塑中使用的塑料或橡胶材料的熔融指数较低,流动性差,容易造成流动不畅而引起短裂纹。
(2)模具问题:模具的出水口或喷嘴设计不合理,导致材料流动不畅,产生过高的注射压力,从而引起短裂纹。
(3)注塑参数问题:注塑机的注射速度过快,冷却时间不足,也会在产品中产生短裂纹。
2.熔痕熔痕是注塑过程中另一种常见的缺陷,表现为产品表面的沟槽或凹痕。
造成熔痕的原因主要有:(1)注塑温度问题:注塑温度过高会导致材料熔化过度,流动性增强,从而产生熔痕。
(2)注塑压力问题:注塑压力过大时,材料在模具中流动不畅,产生摩擦力增加,也会导致熔痕的产生。
(3)模具设计问题:如果模具中的出水口或喷嘴设计不合理,也会在产品表面形成熔痕。
3.气泡气泡是注塑中常见的缺陷,表现为产品内部或表面的空腔。
气泡的形成原因有:(1)材料问题:注塑材料中含有过多的水分或挥发性物质,注塑过程中被加热蒸发,生成气泡。
(2)注塑温度过高:高温会导致材料熔化过度,容易产生气泡。
(3)注塑压力问题:过高的注塑压力会使材料在注塑过程中产生剧烈的振动,从而引起气泡。
(4)模具问题:模具中存在堵塞或不良的冷却系统,也会导致气泡的产生。
4.缩短问题缩短是指产品在冷却过程中出现尺寸缩小的现象。
产生缩短的主要原因有:(1)注塑温度过低:低温会使注塑材料的熔融程度不足,流动性降低,产生缩短。
(2)冷却时间不足:注塑材料冷却时间不足会导致产品未完全固化,容易产生缩短。
(3)注塑压力问题:过大的注塑压力会使产品产生内部的应力,引起尺寸缩小。
(4)模具问题:模具中存在过多的冷却系统,会导致材料过度冷却而使产品缩短。
注塑贴膜工艺缺陷分析
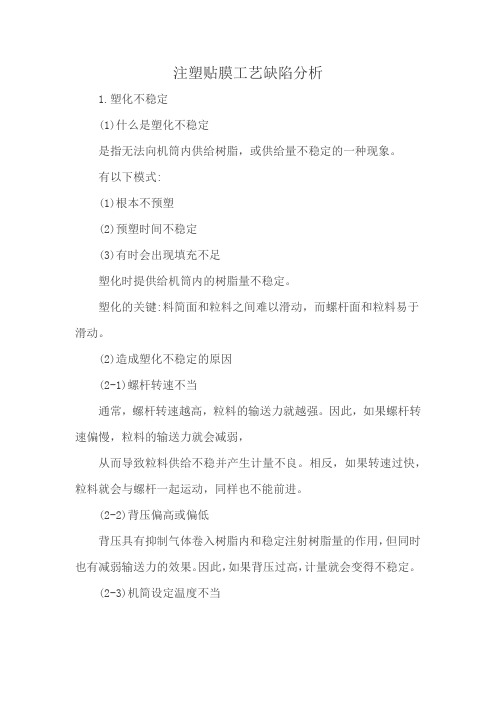
注塑贴膜工艺缺陷分析1.塑化不稳定(1)什么是塑化不稳定是指无法向机筒内供给树脂,或供给量不稳定的一种现象。
有以下模式:(1)根本不预塑(2)预塑时间不稳定(3)有时会出现填充不足塑化时提供给机筒内的树脂量不稳定。
塑化的关键:料简面和粒料之间难以滑动,而螺杆面和粒料易于滑动。
(2)造成塑化不稳定的原因(2-1)螺杆转速不当通常,螺杆转速越高,粒料的输送力就越强。
因此,如果螺杆转速偏慢,粒料的输送力就会减弱,从而导致粒料供给不稳并产生计量不良。
相反,如果转速过快,粒料就会与螺杆一起运动,同样也不能前进。
(2-2)背压偏高或偏低背压具有抑制气体卷入树脂内和稳定注射树脂量的作用,但同时也有减弱输送力的效果。
因此,如果背压过高,计量就会变得不稳定。
(2-3)机简设定温度不当机简设定温度会对机简内的粒料温度产生影响。
也就是说,由于粒料的表面状态及刚性发生变化,因此对计量也有影响。
特别是料斗下方及其相邻的设定温度会对计量带来很大影响。
一般来说,从喷嘴到料斗下方的温度设定由高到低,且料斗下方的设定温度低,计量便会保持稳定。
这是因为温度升高后,粒料表面就会熔化,粒料之间的摩擦增大,从而导致互相交织缠绕,或粘着在螺杆或机筒上。
材料在未成粘流态之前,温度越高,塑料和金属的摩擦越大。
(2-4) 使用了回收材料回收材料通常形状很不规整,因此与普通粒料相比,料粒之间的摩擦容易增大,从而容易引起计量不良。
此外,粉末混入后会粘着在螺杆上,从而使输送力减弱。
(2-5)等级固有的问题在滑动等级中,由于与金属之间的滑动过于良好,因此螺杆旋转力不能很好地转换成向前的输送力,从而容易造成计量不良。
另外,在耐冲击等级中(以及PA, LCP等),粒料之间的摩擦容易增大,这也极易造成计量不良。
(2-6)止回阀磨损或螺杆磨损造成熔体回流,使塑化不稳定(2-7 )材料未烘干。
注塑缺陷原因分析与解决方案

注塑缺陷原因分析与解决方案注塑是一种常见的塑料加工方法,广泛应用于各个行业。
然而,在注塑过程中,可能会出现各种缺陷,如气泡、翘曲、短射等问题,影响产品的质量和性能。
为了解决这些问题,我们需要进行缺陷原因分析,并提出相应的解决方案。
一、缺陷原因分析1. 气泡缺陷气泡是注塑过程中常见的缺陷之一。
其主要原因可能包括以下几个方面:- 塑料材料中含有挥发性物质,如水分、溶剂等,这些物质在高温下蒸发产生气泡。
- 注塑机温度设置不当,过高的温度会使塑料材料中的气体膨胀形成气泡。
- 注塑模具设计不合理,存在气孔或死角,导致塑料充填不均匀,形成气泡。
2. 翘曲缺陷翘曲是注塑产品常见的缺陷之一,其主要原因可能包括以下几个方面:- 注塑机温度不均匀,导致塑料材料在冷却过程中收缩不均匀,引起产品翘曲。
- 注塑模具设计不合理,存在过于薄弱的部位,无法承受注塑过程中的压力,导致产品变形。
- 注塑过程中冷却时间不足,使得产品在脱模后还未完全固化,导致变形。
3. 短射缺陷短射是指注塑产品未能充填满模具而产生的缺陷,其主要原因可能包括以下几个方面:- 注塑机温度设置不当,导致塑料材料粘度过高,无法充填满模具。
- 注塑模具设计不合理,存在过于狭窄的充填道或浇口,导致塑料流动受阻,无法充填满模具。
- 注塑过程中注射速度过快,导致塑料材料无法充填满模具。
二、解决方案1. 气泡缺陷的解决方案- 检查塑料材料的质量,确保其含水量和挥发性物质含量符合要求。
- 调整注塑机的温度,确保塑料材料在注塑过程中不会过热。
- 优化注塑模具的设计,避免气孔和死角的存在,确保塑料充填均匀。
2. 翘曲缺陷的解决方案- 调整注塑机的温度分布,确保塑料材料在冷却过程中收缩均匀。
- 优化注塑模具的设计,增加产品的结构强度,避免过于薄弱的部位。
- 增加注塑过程中的冷却时间,确保产品完全固化后再进行脱模。
3. 短射缺陷的解决方案- 调整注塑机的温度,降低塑料材料的粘度,促进充填。
注塑缺陷原因分析与解决方案
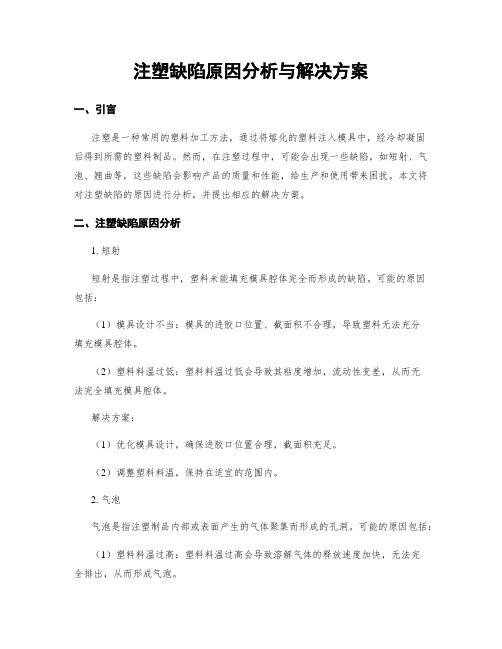
注塑缺陷原因分析与解决方案一、引言注塑是一种常用的塑料加工方法,通过将熔化的塑料注入模具中,经冷却凝固后得到所需的塑料制品。
然而,在注塑过程中,可能会出现一些缺陷,如短射、气泡、翘曲等,这些缺陷会影响产品的质量和性能,给生产和使用带来困扰。
本文将对注塑缺陷的原因进行分析,并提出相应的解决方案。
二、注塑缺陷原因分析1. 短射短射是指注塑过程中,塑料未能填充模具腔体完全而形成的缺陷。
可能的原因包括:(1)模具设计不当:模具的进胶口位置、截面积不合理,导致塑料无法充分填充模具腔体。
(2)塑料料温过低:塑料料温过低会导致其粘度增加,流动性变差,从而无法完全填充模具腔体。
解决方案:(1)优化模具设计,确保进胶口位置合理,截面积充足。
(2)调整塑料料温,保持在适宜的范围内。
2. 气泡气泡是指注塑制品内部或表面产生的气体聚集而形成的孔洞。
可能的原因包括:(1)塑料料温过高:塑料料温过高会导致溶解气体的释放速度加快,无法完全排出,从而形成气泡。
(2)模具排气不畅:模具腔体内的气体无法顺利排出,导致气泡的形成。
解决方案:(1)控制塑料料温,使其保持在适宜的范围内。
(2)优化模具结构,增加排气通道,确保气体能够顺利排出。
3. 翘曲翘曲是指注塑制品在冷却过程中,由于温度不均匀而导致的变形现象。
可能的原因包括:(1)模具温度不均匀:模具温度不均匀会导致注塑制品在冷却过程中收缩不均匀,从而产生翘曲。
(2)注塑压力不均匀:注塑过程中的压力分布不均匀,会导致塑料在模具中的填充不均匀,从而产生翘曲。
解决方案:(1)优化模具冷却系统,确保模具温度均匀。
(2)调整注塑过程中的压力分布,使之均匀。
三、结论注塑缺陷的原因多种多样,需要综合考虑多个因素。
在解决问题时,需要根据具体情况进行分析,并采取相应的解决方案。
通过优化模具设计、控制塑料料温、优化模具结构等手段,可以有效减少注塑缺陷的发生,提高产品质量和生产效率。
四、参考文献[1] 刘明, 张三. 注塑工艺缺陷原因分析及改进措施[J]. 塑料工业, 2018, 46(5): 12-15.[2] 王五, 李四. 注塑缺陷分析与解决方案研究[J]. 机械设计与制造, 2019, 37(2): 45-49.以上是对注塑缺陷原因分析与解决方案的详细描述,请参考。
注塑缺陷原因分析与解决方案
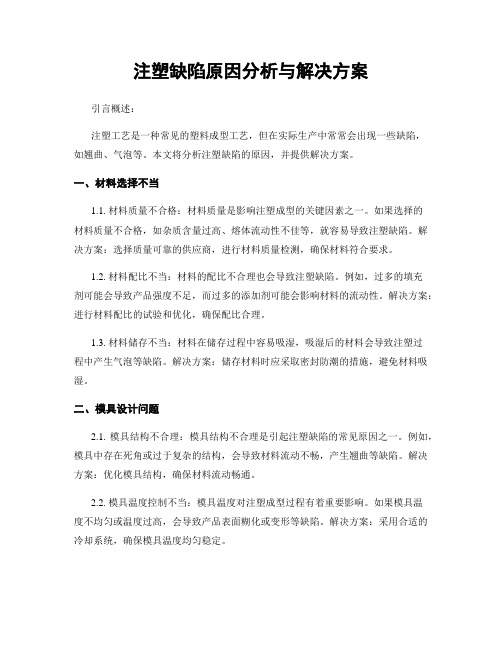
注塑缺陷原因分析与解决方案引言概述:注塑工艺是一种常见的塑料成型工艺,但在实际生产中常常会出现一些缺陷,如翘曲、气泡等。
本文将分析注塑缺陷的原因,并提供解决方案。
一、材料选择不当1.1. 材料质量不合格:材料质量是影响注塑成型的关键因素之一。
如果选择的材料质量不合格,如杂质含量过高、熔体流动性不佳等,就容易导致注塑缺陷。
解决方案:选择质量可靠的供应商,进行材料质量检测,确保材料符合要求。
1.2. 材料配比不当:材料的配比不合理也会导致注塑缺陷。
例如,过多的填充剂可能会导致产品强度不足,而过多的添加剂可能会影响材料的流动性。
解决方案:进行材料配比的试验和优化,确保配比合理。
1.3. 材料储存不当:材料在储存过程中容易吸湿,吸湿后的材料会导致注塑过程中产生气泡等缺陷。
解决方案:储存材料时应采取密封防潮的措施,避免材料吸湿。
二、模具设计问题2.1. 模具结构不合理:模具结构不合理是引起注塑缺陷的常见原因之一。
例如,模具中存在死角或过于复杂的结构,会导致材料流动不畅,产生翘曲等缺陷。
解决方案:优化模具结构,确保材料流动畅通。
2.2. 模具温度控制不当:模具温度对注塑成型过程有着重要影响。
如果模具温度不均匀或温度过高,会导致产品表面糊化或变形等缺陷。
解决方案:采用合适的冷却系统,确保模具温度均匀稳定。
2.3. 模具磨损严重:模具长时间使用后会出现磨损,磨损严重的模具会导致产品尺寸不准确或表面粗糙等缺陷。
解决方案:定期检查和维护模具,及时更换磨损严重的模具部件。
三、注塑工艺参数设置不当3.1. 注射压力过高或过低:注射压力是影响注塑成型的关键参数之一。
如果注射压力过高,会导致产品变形或开裂,而注射压力过低则会导致产品表面光洁度不高。
解决方案:根据产品要求和材料特性,合理设置注射压力。
3.2. 注射速度不合理:注射速度对产品的充填和冷却过程有着重要影响。
如果注射速度过快,会导致产品内部产生气泡或短射,而注射速度过慢则会导致产品表面瑕疵。
注塑缺陷原因分析与解决方案
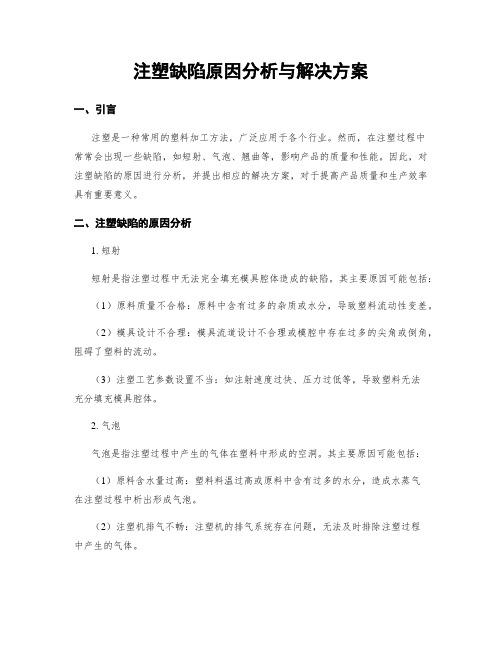
注塑缺陷原因分析与解决方案一、引言注塑是一种常用的塑料加工方法,广泛应用于各个行业。
然而,在注塑过程中常常会出现一些缺陷,如短射、气泡、翘曲等,影响产品的质量和性能。
因此,对注塑缺陷的原因进行分析,并提出相应的解决方案,对于提高产品质量和生产效率具有重要意义。
二、注塑缺陷的原因分析1. 短射短射是指注塑过程中无法完全填充模具腔体造成的缺陷。
其主要原因可能包括:(1)原料质量不合格:原料中含有过多的杂质或水分,导致塑料流动性变差。
(2)模具设计不合理:模具流道设计不合理或模腔中存在过多的尖角或倒角,阻碍了塑料的流动。
(3)注塑工艺参数设置不当:如注射速度过快、压力过低等,导致塑料无法充分填充模具腔体。
2. 气泡气泡是指注塑过程中产生的气体在塑料中形成的空洞。
其主要原因可能包括:(1)原料含水量过高:塑料料温过高或原料中含有过多的水分,造成水蒸气在注塑过程中析出形成气泡。
(2)注塑机排气不畅:注塑机的排气系统存在问题,无法及时排除注塑过程中产生的气体。
(3)注塑工艺参数设置不当:如注射速度过快、压力过高等,造成塑料内部气体无法顺利排出。
3. 翘曲翘曲是指注塑制品在冷却后出现变形的现象。
其主要原因可能包括:(1)模具温度不均匀:模具温度不均匀导致注塑制品冷却不均匀,从而引起翘曲。
(2)注塑过程中的应力积累:注塑过程中,塑料在注射后会受到冷却和收缩的影响,如果释放不及时,会导致应力积累引起翘曲。
(3)注塑工艺参数设置不当:如注射速度过快、冷却时间过短等,造成塑料冷却不充分,引起翘曲。
三、注塑缺陷的解决方案1. 短射的解决方案(1)优化原料质量:选择质量合格的原料,避免杂质和水分的存在。
(2)优化模具设计:合理设计模具流道,避免尖角和倒角的存在,保证塑料的顺畅流动。
(3)优化注塑工艺参数:合理设置注射速度和压力,确保塑料能够充分填充模具腔体。
2. 气泡的解决方案(1)控制原料含水量:确保塑料料温适宜,原料中的水分含量符合要求。
注塑模成型过程中的常见缺陷及解决方法
注塑模成型过程中的常见缺陷及解决方法
1 注塑模成型过程中的缺陷
注塑模是指将塑料以液体状态注入模具内,并承受模具内设计好的形状而成型的加工工艺。
这种加工工艺的缺陷主要体现在:(1)内应力
由于冷凝和冻结等原因,塑料在冷却期内会形成一定的内应力,这些内应力会折断或变形塑料制品,影响其成型的精度和尺寸的准确性;
(2)开裂
由于注塑模具的温度失去平衡,容易引起塑料表面开裂,影响塑料制品的外观质量;
(3)射脂
由于过大的模具压力,塑料在冷却过程中产生弹性变形,导致部分塑料夹在模具内,出现射脂现象,从而影响塑料制品的精度;
(4)易燃体
一些易燃物质在注塑模具成型过程中,受到热源的热量,容易引发火灾。
2 注塑模成型过程中的解决方法
(1)改善冷凝条件
合理设计模具内的冷凝段,增加冷却水的循环流量,加快冷却速度,降低内应力,减少变形现象;
(2)模具润滑
模具润滑能有效减少注塑模具生产过程中开裂的几率;
(3)改变模具温度
根据注塑塑料特性,采取合理的模具温度,确保合理的射出压力,有效减少射脂;
(4)加强安全防护
增强环境湿度,禁止一切产生火花的设备进入生产现场,防止火灾。
总之,正确处理注塑模具成型过程中的缺陷和解决方法,能有效
改善塑料制品的成型精度,改善它们的外观、可靠性和使用寿命,能
为有效利用注塑技术提供有效援力。
注塑缺陷原因分析与解决方案
注塑缺陷原因分析与解决方案一、引言注塑是一种常用的塑料加工方法,广泛应用于各个行业。
然而,在注塑过程中,可能会浮现一些缺陷,例如短斑、气泡、翘曲等问题,这些缺陷会影响产品质量和使用寿命。
因此,对注塑缺陷的原因进行分析,并提出相应的解决方案,对于提高产品质量具有重要意义。
二、注塑缺陷原因分析1. 温度控制不当:注塑过程中,温度是一个关键因素。
如果温度过高或者过低,都会导致注塑缺陷。
例如,温度过高会导致熔融物流动性增加,易产生短斑;温度过低会导致熔融物流动性降低,易产生翘曲。
2. 压力控制不当:注塑过程中,压力也是一个重要因素。
如果压力过高或者过低,都会导致注塑缺陷。
例如,压力过高会导致短斑、气泡等缺陷;压力过低会导致产品密度不足,易产生翘曲。
3. 注塑模具设计问题:注塑模具的设计也会影响产品质量。
如果模具设计不合理,例如流道设计不良、冷却系统不完善等,都会导致注塑缺陷的产生。
4. 塑料材料选择不当:不同的塑料材料具有不同的熔点、流动性等特性。
如果选择的塑料材料与产品要求不匹配,也会导致注塑缺陷。
例如,选择的塑料材料熔点过高,容易产生短斑;选择的塑料材料流动性不足,容易产生翘曲。
5. 操作人员技术水平不高:注塑过程需要操作人员具备一定的技术水平。
如果操作人员技术水平不高,不了解注塑工艺的要点,也会导致注塑缺陷的产生。
三、注塑缺陷解决方案1. 温度控制方案:合理控制注塑过程中的温度,根据塑料材料的特性和产品要求,调整熔融温度和模具温度。
可以通过使用温度传感器和温度控制器来实时监测和调整温度,确保温度在合适的范围内。
2. 压力控制方案:合理控制注塑过程中的压力,根据塑料材料的特性和产品要求,调整注射压力和保压压力。
可以通过使用压力传感器和压力控制器来实时监测和调整压力,确保压力在合适的范围内。
3. 注塑模具设计方案:优化注塑模具的设计,确保流道设计合理、冷却系统完善。
可以通过使用CAD软件进行模具设计和摹拟分析,优化模具结构,减少缺陷的产生。
注塑产品常见缺陷
注塑产品常见缺陷注塑产品常见缺陷及其原因分析注塑产品在生产过程中可能会遇到各种缺陷,这些缺陷可能源于产品设计、模具制造、材料选择、注塑工艺等多个因素。
以下是一些常见的注塑产品缺陷及可能的原因分析:1.填充不足(缺料)这可能是由于注塑压力不足、注射时间过短、模具排气不良、浇口设计不合理等原因造成的。
解决这个问题的方法包括增加注塑压力、延长注射时间、优化模具排气设计、改进浇口位置等。
2.溢料(毛边)溢料通常是由于注射压力过高、浇口设计不当、模具磨损等原因造成的。
解决溢料问题的方法包括降低注塑压力、优化浇口设计、修复模具磨损等。
3.气泡(气孔)气泡可能是由于塑料在模具中未完全填满、气体未完全排出、注射速度过快等原因造成的。
解决气泡问题的方法包括降低注射速度、增加冷却时间、优化模具设计等。
4.变形变形可能是由于产品结构不合理、冷却不均匀、模具温度波动等原因造成的。
解决变形问题的方法包括优化产品结构设计、改善冷却条件、稳定模具温度等。
5.银纹(流纹)银纹可能是由于塑料流动不均匀、模具温度过低、注射速度过快等原因造成的。
解决银纹问题的方法包括优化注射条件、提高模具温度、降低注射速度等。
6.裂纹(龟裂)裂纹可能是由于产品结构设计不合理、材料韧性不足、注射压力过高等原因造成的。
解决裂纹问题的方法包括优化产品结构设计、更换韧性更好的材料、降低注射压力等。
7.翘曲(扭曲)翘曲可能是由于产品结构设计不合理、模具温度不均匀、注射压力过低等原因造成的。
解决翘曲问题的方法包括优化产品结构设计、改善冷却条件、提高注射压力等。
8.冷块(冷凝物)冷块可能是由于塑料在冷却过程中速度过快、模具温度过低等原因造成的。
解决冷块问题的方法包括降低冷却速度、提高模具温度等。
9.喷射痕迹(蛇形纹)喷射痕迹可能是由于注射速度过快、浇口设计不当等原因造成的。
解决喷射痕迹问题的方法包括降低注射速度、优化浇口设计等。
10.颜色分布不均(色差)颜色分布不均可能是由于材料混合不均匀、注塑条件不稳定等原因造成的。
注塑缺陷原因分析与解决方案
注塑缺陷原因分析与解决方案一、背景介绍注塑是一种常见的塑料加工工艺,广泛应用于各个行业。
然而,在注塑过程中,可能会出现一些缺陷,如短射、气泡、翘曲等问题,这些缺陷会直接影响产品的质量和性能。
因此,对注塑缺陷的原因进行分析,并提出相应的解决方案,对于提高产品质量和生产效率具有重要意义。
二、注塑缺陷的常见原因1. 原料质量问题:注塑过程中使用的塑料原料可能存在质量问题,如杂质、颗粒不均匀等,这些问题会导致注塑缺陷的产生。
2. 注塑机参数设置不当:注塑机的温度、压力、速度等参数的设置不当会导致注塑缺陷的产生。
例如,温度过高或过低都会对塑料的熔融和流动性产生影响。
3. 模具设计问题:模具的设计不合理,如出口处设计不良、冷却系统不完善等,会导致注塑缺陷的产生。
4. 注塑工艺操作问题:操作人员对注塑工艺的不熟悉或不规范操作,如注塑时间过长、注射速度过快等,都会引发注塑缺陷。
5. 环境因素:环境温度、湿度等因素也会对注塑缺陷产生影响,例如,湿度过高会导致塑料吸湿,从而产生气泡。
三、注塑缺陷的解决方案1. 优化原料选择:选择质量可靠的原料供应商,确保原料的纯度和均匀性。
进行原料检测,排除存在问题的原料。
2. 调整注塑机参数:根据不同的塑料材料和产品要求,合理设置注塑机的温度、压力、速度等参数,确保塑料材料的熔融和流动性。
3. 优化模具设计:对模具进行优化设计,确保出口处的设计合理,冷却系统完善,避免注塑缺陷的产生。
使用高质量的模具材料,提高模具的耐磨性和使用寿命。
4. 规范操作流程:对操作人员进行培训,提高其对注塑工艺的理解和操作技能。
建立规范的操作流程和记录,及时发现和解决问题。
5. 控制环境因素:保持注塑车间的适宜温湿度,避免环境因素对注塑缺陷的影响。
使用除湿设备,控制湿度在合理范围内。
四、注塑缺陷分析方法1. 观察法:通过对注塑产品外观的观察,发现缺陷的类型和位置,进而分析可能的原因。
2. 断面分析法:通过截取注塑产品的断面,观察其内部结构,分析缺陷产生的原因。
- 1、下载文档前请自行甄别文档内容的完整性,平台不提供额外的编辑、内容补充、找答案等附加服务。
- 2、"仅部分预览"的文档,不可在线预览部分如存在完整性等问题,可反馈申请退款(可完整预览的文档不适用该条件!)。
- 3、如文档侵犯您的权益,请联系客服反馈,我们会尽快为您处理(人工客服工作时间:9:00-18:30)。
容易出现在白色产品
现在两股料流汇合处、孔位处
原因:注塑料筒温度偏高,背压偏高,螺杆转速偏快; 原因:注塑射速小,炮筒温度过低,保压太小,模温
原料不洁;没有清干净炮筒;
料温偏低;模具排气不良,浇口位置不合理;
改善对策:注塑降低背压、料温、螺杆转速;原料检 查,重新清炮筒。
改善对策:注塑提高射速、保压,提高料筒温度,提 高模温,和炮筒温度;模具改善排气,加冷料井
改善对策:注塑降低射速,提高背压、炮筒温度;原 料再烘烤干;使用全自动作业,稳定周期。
现象:表面呈波纹状;一般出现浇口处
原因:注塑射速、射压、保压偏小,炮筒温度过低, 模具浇口太小;
批锋、凹凸印、多胶、油污
注塑常见缺陷分析
注塑件缺陷种类
注塑件常见缺陷种类
• • • • • • • • • • • • •
★★★★★★★★★★★★★
缩变批短黑结烧气料皱蛇顶气
水形峰射点合伤纹花纹纹白泡
(((((线((((((
缩翘毛缺异(烧气气波冷顶
孔曲边胶色熔焦痕花纹料凸
)))))接))))凹)
熔接線冷料井
Weld Slug Well
熔接線冷料井 [Weld slug well] 對頭熔接線 [Butt weld]
烧伤(烧焦) +气纹(气痕)
烧焦
气纹
现象:表面烧焦装(成灰黑色),易出现在结合线旁 边,产品末端等位置
原因:注塑射速射压偏高,料筒温度偏高;模具排气 不良;
改善对策:注塑降低射速射压、降低料筒温度;模具 增加排气。
原因:注塑射压小,射胶量不足,锁模力不足;模具 排气不良,浇口小;
改善对策:注塑提高射压射速,加大射胶量,提高保 压及保压时间;提高料筒温度;模具加大浇口,改善 排气。
黑点(异色) +结合线(熔接痕、夹线)
黑点
结合线
现象:表面出现与产品颜色不同的点,常见的有黑点; 现象:熔胶流动汇合处产生的细线叫结合线;一般出
注塑三主体
注射机台
塑胶原料
注塑模具
注塑工艺简介
注塑机台
6大步骤
合模
射胶
保压
冷却
开模
顶出
注塑工艺简介
注塑参数
时间
压力
温度
影响注塑的5大因素
位置
速度
塑料简介
塑料 别名树脂;一种以高分子量有机物质为主要 成分的材料,即一种合成的高分子化合物。
塑料简介
塑胶产品 塑胶产品运用很广,生活用品、交通工具等都离不开塑胶。
现象:表面形成一层薄薄的雾状就是气纹;一般出现 在浇口处
原因:注塑射速偏高,炮筒温度偏低;模具浇口太小, 流道不光滑;
改善对策:注塑降低射速,提高炮筒温度,以及模腔 表面温度;模具加大浇口,改善排气,增加冷料井
料花(气花) + 皱纹(波纹)
料花
皱纹
现象:表面呈银条状或雪花状
原因:注塑射速偏高,炮筒温度偏低,背压偏低,原 料未充分干燥,周期不稳定;
保壓不夠
塑膠的乾燥不夠
模具排氣不好
模具排氣不好
射膠壓力不夠
膠料流動性不夠
射膠速度太快
塑膠的流動性不好
產品壁厚不均勻
模溫或膠料溫度 過低
前後模溫差 射膠壓力太高 冷卻時間太短
模具配合不緊
膠料有異物,結 合不良
頂出太快
塑膠流動性太好
模具頂出結構不 良
頂出結構不良
鎖模力不足
射膠及頂出速度 太快
模具扣位斜度不 夠
射胶速度 保压速度 背压
响
流动性
螺杆
烘料时间 冷却时间
压力
因
压缩比 长径比
射嘴
射压 保压
素
成型缺陷
鱼
骨
加强筋
纹面
型腔系统
图
脱模斜度
排气系统
形式 大小
R角
温差 分布
顶出系统
流程
冷却系统
平衡性 位置
壁厚
流量
介质
位置 大小
流道系统 形式 平衡性
产品结构
模具
浇口
注塑件缺陷原因及对策
缺陷处理步骤
定义 Define
注塑件常见缺陷分析
讲师:Jacky Lee
主要内容
❖ 注塑工艺 ❖ - 注塑工艺简介 ❖ - 塑料简介 ❖ - 注塑模简介 ❖ 注塑件常见缺陷分析 ❖ - 注塑件缺陷种类 ❖ - 注塑件缺陷影响因素 ❖ - 注塑件缺陷原因及对策
注塑工艺
注塑工艺简介
注塑工艺 也叫注塑成型;是通过注塑机台将受热融化的塑胶由高压射入到模腔内,经 过冷却、固化后,得到成形品的一种方法。
现象:产品翘曲
原因:产品结构问题;注塑前后模温差导致,保压太 大,保压时间长,冷却时间短;顶出不均匀造成;
改善对策:注塑参数调整,调整前后模温,降低保压 及时间,延长冷却时间;
氣泡或/和凹陷的形成
Void or/and Sink Mark Forming
氣泡 ( Void )
凹陷 ( Sink Mark )
注塑模简介
注塑模具
是一种生产塑胶制品的工具,也是赋予塑胶制品完整结构和精准尺寸的工具 。日本人称之为“金型”,美国称之为“Tooling” 。
浇注系统
塑
胶
冷却系统
模
具
排气系统
五
大 系
顶出系统
统
成形系统
注塑模简介
注塑模具
水口 产品 滑块 斜顶
顶针
进浇点 外观、结构、尺寸、功能
批锋、段差 批锋、凹凸印、缺胶、油污
痕痕、源自)夹线)
注塑件缺陷影响因素
产品
结构
原料
注
塑
件
缺
陷
成型缺陷影响因素
影
响
因
素
成型 工艺
注塑机及周 边设备
模具
注塑件缺陷影响因素
原料
成型工艺
成型工艺
结晶性
稳定性 稳定性
锁模力 温度
烘料
射胶 切换 松退 位置
计量 残量
缺
收缩率
最大注 射量
熔料温度 模温
转速
速度
陷 影
吸水性
直径
最大 压力
时间
烘料
烘料
发生了何种缺陷?何时发生?频次如何?不良 数/不良率是多少?
分析 Analysis
改善 Improve
相关因素有哪些?主要因素是什么?根本 原因是什么?必要时通过测量得出数据。
制定改进计划并实施.并将此种改善方法应用到 类似的产品上进行改善。
注塑件缺陷原因及对策
a.缺膠
b.縮水
c.流痕
d.燒膠
射膠的壓力不夠
射膠壓力過高 注 塑 成 型 不 良
e.彎曲,翹曲
f.批峰
g.破裂
h.頂白
缩水(缩孔)+ 变形(翘曲)
缩水
变形
翘曲方向
现象:表面出现收缩凹印,容易出现在骨位柱子背面, 胶厚处,侧壁
原因:注塑射速射压低,保压小,料温低;产品肉厚 不均;模具排气不良,浇口太小;
改善对策:注塑参数调整,提高射速射压、保压,升 高料温;模具改善。
批峰(毛边) +短射(缺胶)
批峰
短射
现象:批峰,毛边,毛刺,易出现在分型面,镶件位 置,结合线位置,行位夹线位置;
原因:注塑射速射压偏高,保压、背压偏高,料温偏 高;锁模力不足;模具有间隙;
改善对策:注塑降低射速射压、保压、背压、料温, 增加锁模力;模具修正,重新合模。
现象:产品缺胶,易出现在偏薄胶位,角落处