密闭电石炉操作培训-课件2014
密闭电石炉节能技术交流和培训
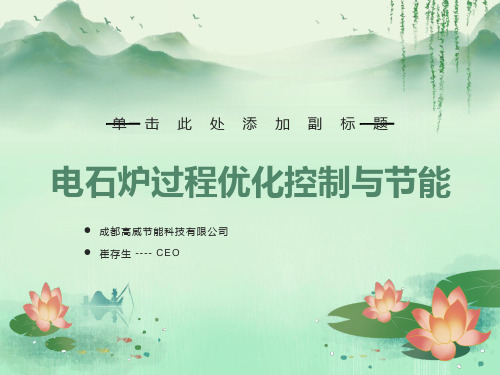
确定最佳:档位(电压)、电流 电极位置由计算机控制
紧密监控:供料系统运行,杜绝 偏加料
产量高、电耗低
时刻监控:电极位置变化规律,并 以此调整电极压放时间
时刻关注:电极做功点位置和发 气量高低 确定最佳:出炉次数, 坚持每班7炉
四、炉前操作要点
偏加料
01
料层分支电流过大
02
补加新料
03
明弧冶炼
04
电流稳定
四、炉前操作要点
超功率区,电流增加、功率降低
01
最高功率点
02
较高功率区,电流增加、功率增加
03
电流大小
04
功率高低
05
电石炉节电的基本机理
电 石 炉 节 电 的 基 本 机 理
三条电极的做功点基本维持在同一个平 面上,电流流向集中,电热转换效率高。
热力场集中,电极放电区域边际效应好
电极极心圆过大或电极功率偏小时的温度分布 低温浪费区 低温浪费区 低温浪费区 电弧高温区 电弧高温区 电极做功点偏远,增加热量浪费 减小热量浪费是节能的根本
电极极心圆过大或电极功率偏小时的温度分布 低温区 电弧高温区 低温区 低温区 电弧高温区 电极做功点偏离大,增加热量浪费 减小热量浪费是节能的根本
电极插入过浅
05
炉底温度低
06
炉底抬高
07
干烧后捣炉、破 坏高温料层
08
偏加石灰料
09
电极插入过深
10
偏加碳
11
电极插入过浅
12
四、炉前操作要点
处理料面观察炉况好坏的方法
料面火苗范围小
电极周围喷火严重
电流波动大、频繁
炉况不好、 指标不好
电石炉岗位操作规程
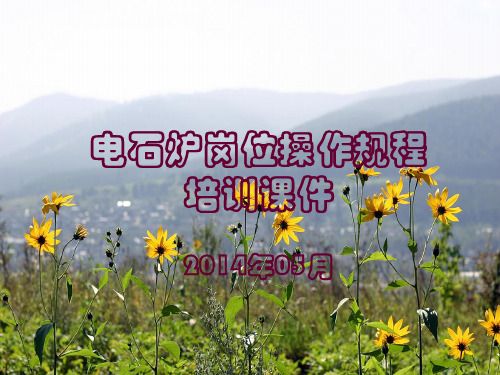
2.3.4正常停电后前四小时每隔半小时活动一次电极,四小时以后
每隔一小时活动一次电极,活动方式为先降后升,反复几次。(
活动电极时确保炉盖上没有其他工作人员)。 3配电操作 3.1正常操作 3.1.1在电炉正常工作时,通常通过提升、下落电极或调整变压器 档位来调整电极电流和电极电压的大小。操作中,提升电极,电 流减小电极电压升高,提升档位电流增大,电压增大,功率增大 ,反之亦然。当电流为零(悬空时),电极电压(对底电压)最 大。 3.1.2电极电压(即有效相电压)对电炉运行的作用。 3.1.2.1三相变压器在同一档位,电极位置基本在同一位置时,那 个电极电压高,说明那个电极相对短一些,反之亦然。 3.1.3正常操作时,为了确保安全生产,炉压应控制在微正压( 0—10Pa)进行操作。(除测电极、打扫炉盖周围卫生等工作外 杜绝负压操作)。
3.2.4.3.2检查各个油泵的指示灯是否正确;此时应通知巡检工到
现场察看是不是和电脑显示一致。 4停炉送电后负荷提升操作 一般停炉送电后,按以下要求增加负载
4.1 0-3小时停炉:送电五分钟无异常,用1.5小时均匀提高负载 至停炉前的负载,根据当时情况及时出炉,调整好三相电极的位 置,使三相电极都有好的做功。 4.2 3-5小时停炉:送电五分钟无异常,30分钟内将电极电流加 载至30-45kA,再用3.5-5.0小时均匀提高负载至停炉前的负载,根 据当时情况及时出炉,调整好三相电极的位置,使三相电极都有 好的做功。 4.3 6-8小时停炉:前1小时稳定电极电流30-45kA, 逐步缓慢提升 电炉负荷,出炉后电流有好的回落,可继续升档,用5-6小时均 匀提高负载至停炉前的负载,调整好炉压0-10Pa.安全稳定运行 。 4.4 8小时以上的停炉及非计划停炉:前三小时将电极电流控制 在30-45kA,之后每20分钟提升1kA电流,电极电流升至5055kA,稳定运行2小时之后,开始每15分钟升一档,升到10档后 稳定30-60分钟,出炉后电流回落较好可继续升档,之后每15分 钟升一档,升至原负荷。调整好三相电极的位置,使三相电极都 有好的做功。
密闭电石炉操作培训-课件2014

六、碳化钙生产的三个基本要求
碳化钙生产的三个基本要求:
(1)要有良好的原料,也就是反应物氧化钙和还原 剂碳。
(2)反应需要在高温条件下进行,并在反应中吸收 大量的热量。
(3)要有良好的透气性,因在生成物一方除生产碳 化钙,同时要放出CO气体。 总之,电炉的操作重点就是围绕三根电极的管 理展开一系列的工作,同时还要认识到电极操作管 理是一个整体,每个环节都不能出现问题。大概的 说,要真正管理好电石炉工作,重点要抓好“八个 稳定”即原料、配比、电极、料面、负荷、产量、 质量、炉眼才能达到安、稳、长、满、优的运行。
炉气CO含量:
70%-85%
炉气热值
>2600 kJ/Nm3。
炉压
±5Pa
炉气中氢气的含量
≤12%
糊柱高度度
冬季3.5-4.5m 夏季4-5m
电极糊块度
<100mm
加糊量
400-500 kg/次
变压器组一次电压:
110KV
变压器组一次电流:
219.96A
变压器组二次电压:
75.06—280V
满功率电压范围:
油温
<50℃
炉眼高度:
与炉底相平
炉眼深度:
≥600mm
出炉次数:
8炉/班(每炉间隔60分钟)
出炉时间
<20分钟
拔插板时间
>30分钟
电石拔锅时间
>180---240分钟
电石冷却时间
≥48小时
电石额定生产率:
10.1T/h
电石冷样发气量: 290-305L/kg(20℃时)
热样发气量:295-315L/kg;
要想办法提高炉料电阻; 1、使用符合标准的原料。包括化学成分和粒度,炉料粒 度过大电阻小,支路电流大,电极不易入炉。 2、保证正常的料面温度,减少表面红料层,减少之路电 流。 3、要保证炉料有良好的透气性。因为,透气性不良一氧 化碳不易排出,造成塌料和料层表面结壳,炉料电阻减小支路 电流曾大电极上升。
电石生产培训课件

13、炉顶单梁电动葫芦吊
功能描述及用途:炉顶吊车是用于吊装电极糊、电极壳及 检修设备。为单梁电动葫芦吊,吊车防爆。(土建中应设 置有检修平台。)
技术要求:吊钩对中各电极中心 起重能力:3吨 提升高度:5米
14、电石炉变压器系统
母线及冷却水管
⑥铜母线装置---连接二次母线及接触元件 ⑨冷却水供应装置---用于向底环、水冷保护套、接触元件
提供冷却水
4、炉盖系统
功能描述及用途:炉盖用于密封炉膛、减少热损失和改善 冶炼区间的工作条件。
组成:炉盖由6个边缘炉盖及1个防磁中心炉盖组成。 每瓣炉盖均为水冷结构,6个边缘炉盖为耐热锅炉钢板焊
技术要求:在制造厂进行预装配,组装后炉壳的 直径极限偏差为±18mm。
12、出炉烟罩
功能描述及用途:在出电石时,用于对出炉口烟 气进行收集、输送。
组成:由烟罩、烟气管道、手动翻板阀、烟道吊 挂等组成。
K、炉底风冷装置 功能描述及用途: 用于降低炉底温度,以提高炉
壳及炉衬的使用寿命。 组成:炉底风冷装置由一台风机供风,以维持电
电石锅由锅本体、锅底及插板组成。电石锅由耐热铸钢铸 造而成。
技术要求:容量:1000kg,材质为耐热铸钢
18、炉前挡屏
功能描述及用途:炉前挡屏用于电石出炉时遮挡辐射热。 组成:炉前挡屏为钢制非标准件,内部通水冷却,中间留
有出炉操作口。材质要求:耐热钢板
19、卷扬机系统
功能描述及用途: 用于来回牵引电石包车 组成: 卷扬机是由带罩子的焊接钢架结构组成,包括:卷
炉盖
①边缘水冷段---由多边形组成,近似圆盖状,防热辐射 ②中心水冷段---连接边缘炉瓣,形成电极孔 ③水冷密封套---在电极相对炉盖运动过程中提供密封
电石生产培训资料 ppt课件
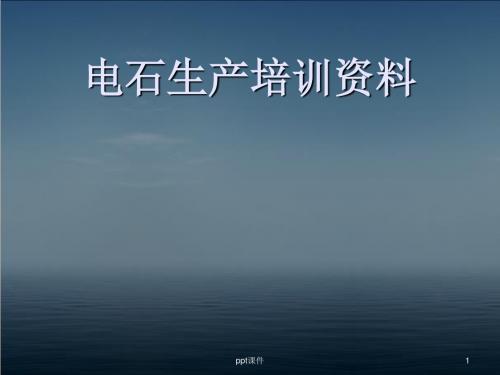
理的抽气系统以及其他技术改进,可使电炉的 维护管理费用降低20%,电能单耗降低20%,焦 炭单耗降低8%,电极糊降低20%该公司在克纳 普沙克还改建了两座有功功率为27000千瓦的半 密闭炉和两座有功功率为22000千瓦的开放炉。 据该公司断定,生产能力的提高以及容量为 47000千伏安(有功功率为42000千瓦)的两座 新型电石炉在生产中积累的经验,可作出如下
ppt课件
18
三、我国电石生产情况
我国在解放前几乎没有电石工业,只是在某些采矿场建有几度小型电 石炉,容量为300千伏安左右,生产的电石主要用于点灯。与国外电 石工业相比,相差约半个世纪。
解放后,1948年在吉林建成了第一座容量为1750千伏安的开放炉,年生 产能力为3000吨。抗美援朝战争爆发后,1951年在吉林建成第二座电石 炉,容量与第一座相同。两年后,为适应国家经济建设的需要,又将 这两座电石炉由1750千伏安改成3000千伏安和6000千安。1956年河北 省下花园建成一座容量为3000千伏安的电石炉,1957年又从苏联引进 一座容40000千伏安的长方形三相半密闭炉,在吉林建成投产。这时 候全国电石总产量接近10万吨。
(4)通过电子计算机监控所有冷却水的变化。
(5)通过电子计算机监视和预测电极糊软化烧结 情况。
(6)通过电子计算机可以测量,控制电极工作长 度,并保持电石炉在恒定功率运行。
密闭电石炉
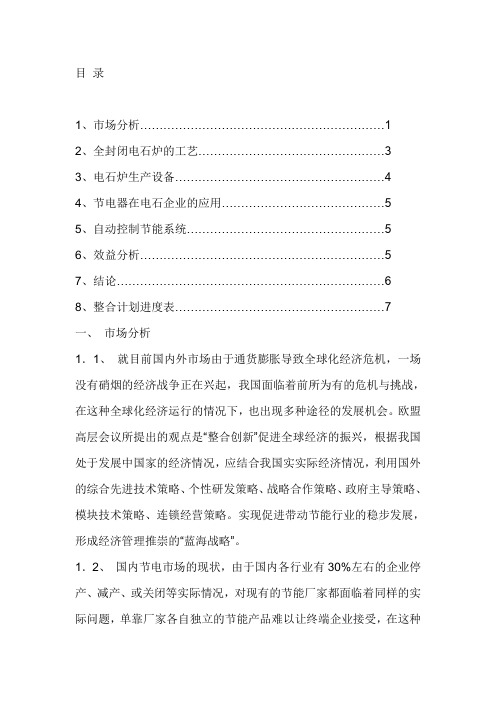
目录1、市场分析 (1)2、全封闭电石炉的工艺 (3)3、电石炉生产设备 (4)4、节电器在电石企业的应用 (5)5、自动控制节能系统 (5)6、效益分析 (5)7、结论 (6)8、整合计划进度表 (7)一、市场分析1.1、就目前国内外市场由于通货膨胀导致全球化经济危机,一场没有硝烟的经济战争正在兴起,我国面临着前所为有的危机与挑战,在这种全球化经济运行的情况下,也出现多种途径的发展机会。
欧盟高层会议所提出的观点是“整合创新”促进全球经济的振兴,根据我国处于发展中国家的经济情况,应结合我国实实际经济情况,利用国外的综合先进技术策略、个性研发策略、战略合作策略、政府主导策略、模块技术策略、连锁经营策略。
实现促进带动节能行业的稳步发展,形成经济管理推崇的“蓝海战略”。
1.2、国内节电市场的现状,由于国内各行业有30%左右的企业停产、减产、或关闭等实际情况,对现有的节能厂家都面临着同样的实际问题,单靠厂家各自独立的节能产品难以让终端企业接受,在这种全球化经济萎缩的情况,EMC节能形成了巨大的市场潜力,也是政府投资拉动内需最有效的切入点,做为我公司是节电行业的促进者,要抓住这次机会整合新技术达到主动开创新行业市场,确保公司在节电行业的地位,同时我公司可以获得短期、中期、长期的经济效益。
1.3、经过半年多对电石企业行业的了解,我国的电石企业有85%左右的是70年代的内燃式12500KVA以下的小炉型,每出一吨电石单耗电能为36000-38000度的用电,产品合格率在85-93%左右,操作需要有丰富实践经验的人员来控制,人为的因素较多。
而全封闭的电石炉每出一吨电石单耗电能为≤32000度的用电,与原有的内燃式炉子相比较节能率在11.1-15%左右,(不含余热回收,安装节电设备)就目前电石行业的全封闭的电石炉节电设备的应用,主要是采用高压功率补偿、低压风机变频、余热回收、自动化控制等手段,高压功率补偿、自动化控制系统电石炉厂家已采用。
电石炉讲课资料(090720修改)
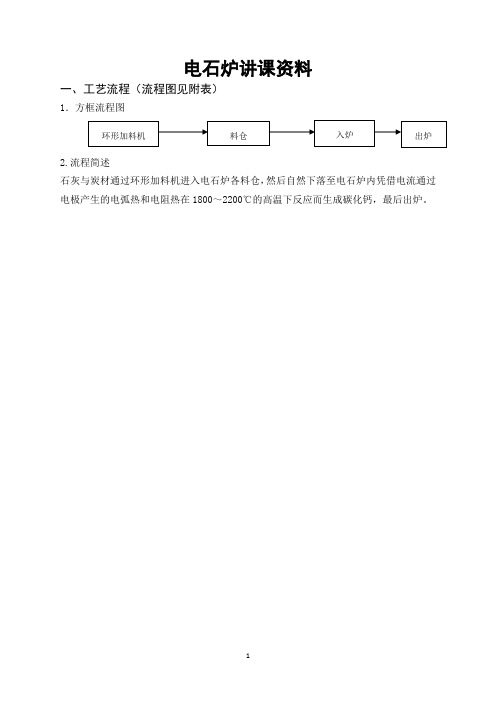
电石炉讲课资料一、工艺流程(流程图见附表)1.方框流程图2.流程简述石灰与炭材通过环形加料机进入电石炉各料仓,然后自然下落至电石炉内凭借电流通过电极产生的电弧热和电阻热在1800~2200℃的高温下反应而生成碳化钙,最后出炉。
二、操作阀门(操作点)1、荒气烟道水冷蝶阀:此阀门为电动阀门(或气动),阀芯通水安装在荒气烟道第17节上即主厂房25.5米层,是碳钢制造而成,管径为DN600,主要用于电石炉排空泄压之用,正常运行时为关闭状态。
2、净气烟道水冷蝶阀:此阀门为电动阀门(或气动),阀芯通水安装在净气烟道第21节上即主厂房25.5米层,是碳钢制造而成,管径为DN500,主要用于电石炉给净化系统输送尾气之用,正常运行时为开启;如若电石炉炉温不高净化系统不能投运时此阀门为关闭状态。
三、仪表点1、温度测点:(1)炉底温度:3个,每相电极对应1个,此点能准确判断炉温的高低,工况的好坏。
(一般在500-700度之间,高于450度时炉底风机投运。
)(2)炉盖温度:1个,此点能准确判断电石炉料层结构的好坏。
(400-600度)(3)炉气温度:1个,此点能准确判断电石炉料层结构的好坏,与净化系统正常投运有着密切关联。
(小于750度)(4)各水路回水温度:85个,此点一般在45度以内,特别是重要部位(密封套、底环、炉盖)回水温度超过45度,说明电石炉内翻电石、喷料或设备内有漏水现象。
2、压力测点:(1)炉压:此点安装在炉盖上用22mm的套管引出,正常时在20~-30Pa 之间。
(2)循环水压力:3个水分配器各装1个,循环水总管1个,压力控制在0.28-0.34MPa之间;低于0.25MPa连锁电石炉停车。
(2)油压:控制在8.5-11MPa之间,油压过低,电磁阀不动作电极压放不到位或电极提升时速度较慢。
3、重点操作点:(1)电极电流:小于100KA,高于100 KA容易击穿电极壳、烧毁变压器;(2)对地电压:大于90V,低于90V时说明此相电极积聚生料较多或炉温低;(3)电极升降:电极提升靠升降泵输出的油压至有杆腔完成,电极下降靠有杆腔内的油回至无杆腔后电极自重下落完成;(4)电极压放:电极压放靠压放泵输出的油压完成,通油后夹紧缸按1、2、3、4、5、6依次松开向上挪动20mm,失油后6个压放缸一起向下压,最大行程每次为20mm;(5)档位调节:此点为炉变接点,用于提升或降低负载之用。
密闭电石炉生产教材
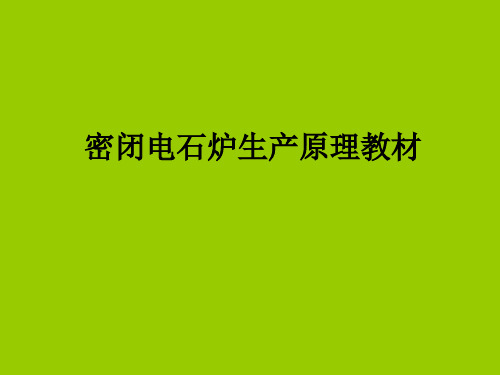
• 交流电弧在每一个周期内改变两次,在每1/2周期 内,电弧都经历起弧、长大、衰减、熄弧的过程, 因此交流电弧是不稳定的。
• 在交流电炉中电弧并不是经常停留在电极端部的 某一固定位置,电弧在电极端部经常跳跃。在磁 场作用下,三相交流电弧与电极成一定角度,即 电弧总向炉墙一侧偏转。
• 冶炼条件下,电弧特性与电气制度、炉料参数、 炉况有关。大量实验数据表明,电弧长度L与电弧
• (2)电弧的形状,长电弧稳定性差,直径大的电弧稳定性好。
• (3)电路电抗和功率因数,交流电路中存在电抗使得电 流相位落后于电压相位,功率因数低有助于稳定电弧。
• (4)电极形状,改变电极的形状可以改变电弧附近的磁 场、电场、热平衡和气体流动状态。尖头的电极和空心电 极的电弧最稳定。电极孔处温度最高易形成电弧,同时, 电弧的路径与空心电极孔流出的气体路径是一致的。
直流电弧与交流电弧的比较
密闭电石炉生产原理教材
第一讲 设备篇
• 矿热炉的分类与特点
• 1.1铁合金电炉概论 • 占铁合金生产总产量90%以上的硅铁、铬铁、锰铁等铁合金主导产品
及钨铁、钒铁等特殊铁合金产品都是用电炉冶炼的。电炉冶炼具有以 下特点:
• (1)电炉使用电这种最清洁的能源。其他能源如煤、焦炭、石油、 天然气等都不可避免的将伴生的杂质带入冶金过程中。只有采用电炉 才能生产最清洁的合金。
- 1、下载文档前请自行甄别文档内容的完整性,平台不提供额外的编辑、内容补充、找答案等附加服务。
- 2、"仅部分预览"的文档,不可在线预览部分如存在完整性等问题,可反馈申请退款(可完整预览的文档不适用该条件!)。
- 3、如文档侵犯您的权益,请联系客服反馈,我们会尽快为您处理(人工客服工作时间:9:00-18:30)。
液压系统最大工作压力 11MPa
油温
<55℃
炉眼高度:
与炉底相平
炉眼深度:
≥500mm
出炉次数:
8炉/班(每炉间隔60分钟)
出炉时间
<20分钟
电石冷却时间:
>48小时
拔插板时间
>30分钟
电石拔锅时间
>150分钟
电石额定生产率:
6.75T/h
电石冷样发气量: 290-305L/kg(20℃时)
热样发气量:295-315L/kg;
三、日常生产异常处置
日常生产异常处置
序 异常现 号象
原因
处理方法
1.炉眼变形,不规则, 1.及时修正炉眼2.人工及时用钢
1
炉眼难 堵
外小里大2.电石粘稠, 堆积在炉外口3.原料杂 质含量异常
钎捅炉眼,保证电石流出畅通, 并清理炉嘴处堆积电石3.检查原 料杂质含量,提起该炉眼电极或
停电
电极入炉深度不够炉膛 1.复测电极检查电极入炉深度2.
作,或掺用部分比电阻较大的碳素材料等。
一、电石生产工艺原理
因此,电石炉的操作关键是控制炉料电阻。因为,炉料 电阻的大小对于稳定电极起着十分重要的作用,在正常情况 下炉料电阻适当,电极就能够深入到理想的位置,使炉底温 度提高保证电炉的正常运行。但是当炉料电阻过小或其它原 因造成电极入炉不够时,电炉就难以正常运行。
物
盖好
备注
三、日常生产异常处置
1.原料粒度大,反应速度 1.及时调整原料进场粒度2.停电打
4
电极压 慢2.电极过烧、卷铁皮3. 放困难 电极过长,顶住炉底4.电
炉气CO含量:
70%-85%
炉气热值
>2600 kJ/Nm3。
炉压
±5Pa
炉气中氢气的含量
≤12%
糊柱高度度
冬季3.5-4.5m 夏季4-5m
电极糊块度
<100mm
加糊量
400-500 kg/次
变压器组一次电压:
110KV
变压器组一次电流:
219.96A
变压器组二次电压:
75.06—280V
满功率电压范围:
218.2---280V
分接头级数:
35档ห้องสมุดไป่ตู้
分接头间电压差:
4.4V
变压器组二次电流: 86.6---111.1KA
电炉总容量:
42MVA
电炉总功率:
34.56MW
循环冷却水分配器压力: 0.35MPa
循环冷却水出口温度: ≤45℃
循环冷却水入口温度: ≤35℃
压缩空气压力
≥0.5MPa
液压系统最大工作压力 12MPa
2
烟道温 料层溶洞多出炉时,吹 及时处理料层溶洞3.维护好炉眼
度高 氧过大兰炭水份大
,减少吹氧4.及时通知调度调整
兰炭入炉水份
1.停炉期间未开加热元 1.停炉检修期间及时开启加热元
件2.加糊量超过规定值 件2.按照工艺规定加糊3.及时抽
3
电极糊 3.进场电极糊、粒度过 查此批电极糊进场质量4.及时用 搭桥 大4.电极筒顶部进去异 重锤砸落,并将电极筒顶部上盖
油温
<50℃
炉眼高度:
与炉底相平
炉眼深度:
≥600mm
出炉次数:
8炉/班(每炉间隔60分钟)
出炉时间
<20分钟
拔插板时间
>30分钟
电石拔锅时间
>180---240分钟
电石冷却时间
≥48小时
电石额定生产率:
10.1T/h
电石冷样发气量: 290-305L/kg(20℃时)
热样发气量:295-315L/kg;
CaO+3C = CaC2+ CO -465.9(KJ)
2、实际上电石的生成反应过程是相当复杂 的,在电石炉内不单是一个化学反应的场 所,也是电磁感应和能量交换的场所。
一、电石生产工艺原理
3、电石的实际反应速度,不仅要由化学反应的速度来 决定,而且还决定于石灰的渗透速度、焦炭的崩裂分散和 扩散速度、焦炭的化学活性等。而影响氧化钙碳化反应速 度的根本因素则是炉温的变化。
要想办法提高炉料电阻; 1、使用符合标准的原料。包括化学成分和粒度,炉料粒 度过大电阻小,支路电流大,电极不易入炉。 2、保证正常的料面温度,减少表面红料层,减少之路电 流。 3、要保证炉料有良好的透气性。因为,透气性不良一氧 化碳不易排出,造成塌料和料层表面结壳,炉料电阻减小支路 电流曾大电极上升。
199.6---240.2V
分接头级数:
35档
分接头间电压差:
3.1V
变压器组二次电流: 41632---50100×√3
电炉总容量:
30MVA
电炉总功率:
22.5MW-24MW
循环冷却水分配器压力: 0.35MPa
循环冷却水出口温度: ≤45℃
循环冷却水入口温度: ≤35℃
压缩空气压力
≥0.5MPa
密闭电石炉工艺规程及操作培训
目录
一、电石生产工艺原理 二、生产控制指标一览表 三、日常生产异常处置 四、主要工艺指标控制的要求 五、炉底上涨的原因及措施 六、碳化钙生产的三个基本要素
一、电石生产工艺原理
一、碳化钙生成反应
1、工业碳化钙的生成是以生石灰和炭素材 料(冶金焦、石油焦、无烟煤)为原料,在 电炉内均匀混合,炉料凭借电弧热和电阻 热在1800℃-2200℃的高温下成熔融状态 而制得的。CaC2的生成反应如下:
炉气CO含量:
70%-85%
炉气热值
>2600 kJ/Nm3。
炉压
±5Pa
炉气中氢气的含量
≤12%
糊柱高度度
冬季3.5-4.5m 夏季4-5m
电极糊块度
<100mm
加糊量
400-500 kg/次
变压器组一次电压:
35KV
变压器组一次电流:
285.7A
变压器组二次电压:
80.9—240.2V
满功率电压范围:
二、工艺控制指标一览表
电石一期控制指标:
炉料配比:石灰:焦炭 100:56~65(干基)
兰炭粒度
5~25mm
>85%
兰炭入炉水份
≤1%
石灰粒度
10~40mm >85%
电极工作端长度
≤1700~1900mm
电极入炉深度:
≧800mm
炉气温度:
<750℃
空冷器出后温度:
<260℃
炉气粉尘含量:
<50mg/Nm3
所以,炉温对反应速度的影响是十分巨大的。要想提 高炉温,主要是靠生产高质量的电石,相应地也要提高电 石炉的负荷。在这种情况下,炉膛内的电阻将会下降,电 极不容易深入到适当的位置,甚至出现明弧操作,这就会 降低各项技术经济指标。通常采用的办法为:适当提高电 流电压比,使其能在电阻较低的情况下,仍然进行闭弧操
电石二期控制指标
炉料配比:石灰:焦炭 100:56~65(干基)
兰炭粒度
5~25mm
>85%
兰炭入炉水份
≤1%
石灰粒度
10~40mm >85%
电极工作端长度
≤2000~2200mm
电极入炉深度:
1100mm-1300mm
炉气温度:
400℃~700℃
空冷器出后温度:
<260℃
炉气粉尘含量:
<50mg/Nm3