6Sigma案例
六西格玛经典案例

六西格玛经典案例在六西格玛质量管理方法中,通过分析和改进业务流程,以减少缺陷和提高效率,从而实现优秀质量和高度效益。
以下是三个经典的六西格玛案例。
1. Motorola的六西格玛实践Motorola是六西格玛的奠基者之一、20世纪80年代,Motorola采用六西格玛方法,以改进生产过程并提高质量。
在一个以缺陷率而不是零缺陷为标准的产业中,Motorola在一年内将缺陷率从超过三十万个降低到每百万个产品中只有5个。
六西格玛的成功引起了其他公司的注意,并成为其他公司实施质量管理的典范。
2. General Electric(GE)的六西格玛实施GE是六西格玛的早期采用者,它将六西格玛引入公司的各个部门和业务领域。
公司的首席执行官杰克·韦尔奇在1995年将六西格玛作为公司的战略重点。
GE在实施过程中的一个成功案例是其航空发动机业务部门,该部门通过六西格玛方法降低了生产过程中的缺陷率,并提高了航空发动机的性能和可靠性。
GE的成功证明了六西格玛可以在各种行业中实现卓越的结果。
3.美国政府的六西格玛应用六西格玛方法不仅在企业界取得成功,而且在政府部门中也有很好的应用。
美国政府决定在1995年引入六西格玛方法,以提高效率并减少浪费。
例如,美国联邦航空管理局(FAA)使用六西格玛方法改进了飞行管制和管理过程,减少了航班延误和事故。
美国海军也采用了六西格玛方法来改善军舰维护和修理过程,提高了战斗力和减少了成本。
以上是六西格玛的三个经典案例,它们都展示了通过六西格玛方法来实现质量改进和效益提高的潜力。
这些案例证明了六西格玛是一个非常有力的质量管理方法,可以在各个领域带来显著的结果。
无论是在制造业、服务业还是政府部门,六西格玛都能够提供一个可靠的框架来解决质量和效率方面的挑战。
精益六西格玛案例分析
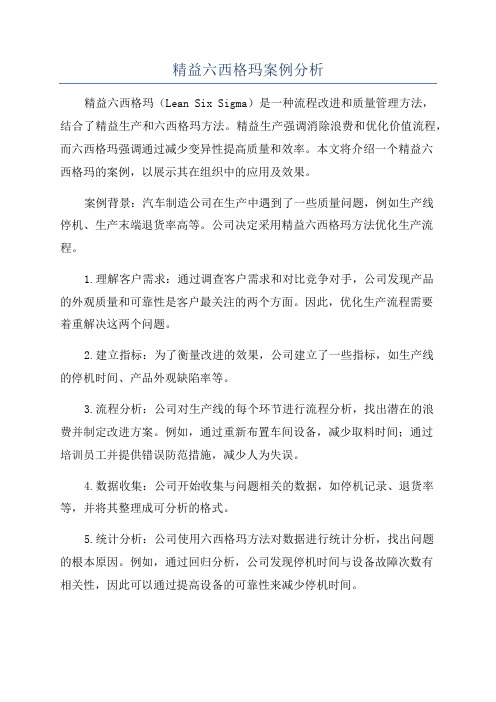
精益六西格玛案例分析精益六西格玛(Lean Six Sigma)是一种流程改进和质量管理方法,结合了精益生产和六西格玛方法。
精益生产强调消除浪费和优化价值流程,而六西格玛强调通过减少变异性提高质量和效率。
本文将介绍一个精益六西格玛的案例,以展示其在组织中的应用及效果。
案例背景:汽车制造公司在生产中遇到了一些质量问题,例如生产线停机、生产末端退货率高等。
公司决定采用精益六西格玛方法优化生产流程。
1.理解客户需求:通过调查客户需求和对比竞争对手,公司发现产品的外观质量和可靠性是客户最关注的两个方面。
因此,优化生产流程需要着重解决这两个问题。
2.建立指标:为了衡量改进的效果,公司建立了一些指标,如生产线的停机时间、产品外观缺陷率等。
3.流程分析:公司对生产线的每个环节进行流程分析,找出潜在的浪费并制定改进方案。
例如,通过重新布置车间设备,减少取料时间;通过培训员工并提供错误防范措施,减少人为失误。
4.数据收集:公司开始收集与问题相关的数据,如停机记录、退货率等,并将其整理成可分析的格式。
5.统计分析:公司使用六西格玛方法对数据进行统计分析,找出问题的根本原因。
例如,通过回归分析,公司发现停机时间与设备故障次数有相关性,因此可以通过提高设备的可靠性来减少停机时间。
6.解决问题:公司根据数据和分析结果制定了一些解决方案,如增加设备维护频率、招聘更有经验的操作员等。
7.测试和验证:公司对解决方案进行测试,并跟踪指标的变化。
例如,公司实施了新的设备维护计划,并在一段时间后再次收集停机数据进行对比分析。
8.控制和持续改进:公司建立了一套控制措施,以确保改进效果的持续。
例如,定期对生产线进行巡检,培训新员工并提供继续教育,以保持高质量的生产。
通过采用精益六西格玛方法,该汽车制造公司取得了显著的改进效果。
例如,生产线的停机时间减少了50%;产品外观缺陷率下降了30%;退货率减少了20%。
这些改进不仅提高了产品质量和可靠性,还降低了生产成本。
6西格玛平安案例

6西格玛平安案例案例1一个半导体簿膜设备制造商在"6-Sigma"实施前的状况是:由于设计研发周期太长,该公司老是不能及时将产品推入市场,而且由于故障率太高,致使售后效劳和维修本钱太高。
售后效劳和维修本钱包括:(1)顾客埋怨、投诉和保修本钱;(2)客户维修本钱;(3)延迟发货和停产损失。
该公司一台设备的平均单价是US$7500K。
该公司希望通过"6-Sigma"的改进运作,能使公司赶上其竞争对手,如Toshiba,Actel,Applied,Material等公司。
该公司的"6-Sigma"运作是从建立"6-Sigma"团队开始的。
核心团队由研发工程、应用工程及可靠性工程组成,其它部门(如市场、制造、财务、质量等)负责支持与协助。
公司的总裁直接领导一个"6-Sigma"负责人,该"6-Sigma"负责人是由公司的副总裁担任。
在"6-Sigma"负责人之下,是"6-Sigma"黑带委员会(包括MBB黑带师、研发总监、技术总监)、"6-Sigma"财务委员会、研发系统1#、研发系统2#、研发系统3#和两个黑带项目团队。
该公司"6-Sigma"的推进步骤如下:由管理高层确定"6-Sigma"的开展计划和管理结构,选定KPI,然后进行管理高层的培训和"6-Sigma"BB培训。
在培训过程中,BB黑带项目也要同时选定和实施,最后是项目的审核。
选定的KPI是:(1)研发周期缩短2个月;(2)生产过渡期合格率由65%提高到80%;(3)减少客户报怨和维修率80%;(4)预计财务回报:通过降低研发周期可创造亿美元(US$350KK);通过提高合格率可创造2亿美元(US$200KK);通过降低维修成本可节约4亿美元(US$400KK)。
六西格玛案例分析
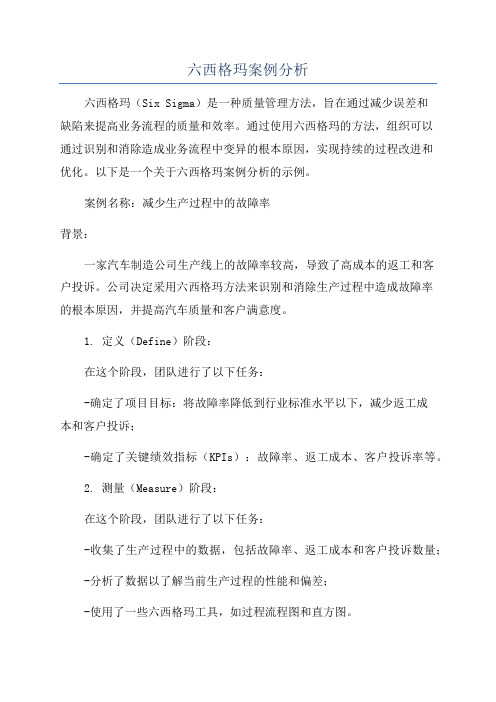
六西格玛案例分析六西格玛(Six Sigma)是一种质量管理方法,旨在通过减少误差和缺陷来提高业务流程的质量和效率。
通过使用六西格玛的方法,组织可以通过识别和消除造成业务流程中变异的根本原因,实现持续的过程改进和优化。
以下是一个关于六西格玛案例分析的示例。
案例名称:减少生产过程中的故障率背景:一家汽车制造公司生产线上的故障率较高,导致了高成本的返工和客户投诉。
公司决定采用六西格玛方法来识别和消除生产过程中造成故障率的根本原因,并提高汽车质量和客户满意度。
1. 定义(Define)阶段:在这个阶段,团队进行了以下任务:-确定了项目目标:将故障率降低到行业标准水平以下,减少返工成本和客户投诉;-确定了关键绩效指标(KPIs):故障率、返工成本、客户投诉率等。
2. 测量(Measure)阶段:在这个阶段,团队进行了以下任务:-收集了生产过程中的数据,包括故障率、返工成本和客户投诉数量;-分析了数据以了解当前生产过程的性能和偏差;-使用了一些六西格玛工具,如过程流程图和直方图。
3. 分析(Analyze)阶段:在这个阶段,团队进行了以下任务:-确定了导致故障率升高的根本原因;-使用了五力分析和鱼骨图等工具,以识别可能的原因;-根据数据和分析结果,确定了一个或多个关键影响故障率的因素。
4. 改进(Improve)阶段:在这个阶段,团队进行了以下任务:-开发了改进计划,包括减少故障率的具体措施和时间表;-实施了改进措施,并记录了结果。
5. 控制(Control)阶段:在这个阶段,团队进行了以下任务:-实施了独立检查和监控措施,以确保改善措施的可持续性;-追踪关键绩效指标,如故障率、返工成本和客户投诉;-确立了持续改进的机制,以确保过程持续优化。
通过使用六西格玛方法,该汽车制造公司成功降低了生产过程中的故障率。
在实施改进措施后,故障率从10%降低到行业标准的3%以下,成功降低了返工成本和客户投诉率。
此外,公司在生产线上建立了严格的质量控制措施和监控机制,以确保持续改进和优化。
六西格玛管理经典案例一个经典的六西格玛案例

六西格玛管理经典案例一个经典的六西格玛案例导读:就爱阅读网友为您分享以下“一个经典的六西格玛案例”的资讯,希望对您有所帮助,感谢您对的支持!一个经典的六西格玛案例黑带大师的笔录—蓝膜效应蓝膜问题三年前我们接到夏新手机一个新产品的订单,为其生产一种新的,非常薄的手机的按键,我们的工程师设计时用了GE---通用电器最新的高拉力硅橡胶来减少厚度,经过样本确认没有问题就转入量产。
但是制造在量产的时候却出现的严重的问题: 经常性100%的按键板在装配热成型后出现硅胶不成熟的现象,轻轻用手指一掐,按键就陷下去,根本无法使用。
要命的是,有时候又会100%OK。
制造工程师做了很多的分析,调节热成型的温度,时间,压力等关键工艺条件来解决,但是缺陷仍然不时出现。
于是产品和过程设计工程师,以及质量工程师做了很多尝试,却无法解决,最后只好请GE美国的材料专家到工厂来协助解决。
三个月过去了,问题没有任何进展.手机商的项目经理很着急,因为一个新款手机的销售周期才6---9个月,我们花在按键板上却已过去了3个多月。
于是夏新给了工厂一个最后期限,只有两个星期的时间,否则他们将撤单。
在这时已经罩不住了,制造经理才只好来找6SIGMA部门,希望我能派BB去解决。
(一般情况下他们都不相信黑带BB能解决问题的,现在也不相信,但是至少BB可以分担他们的责任,呵呵!制造经理此时对于这种缺陷的发生已经快要疯了,他的观点几乎到了唯心的程度,他说:“奥利弗,虽然我也不迷信,但是好像真的有鬼了”。
我派出了两个刚刚结束培训的BB去联手解决,每天我们会花30分钟一起确认进度,工厂的经理们惊奇的发现: 黑带们并没有快速地去假设一些他们认为可能的原因尽快做试验,也没有任何新的人员加入解决问题的团队。
换句话说,人还是这些人,而且BB们先去将整个流程包括他们认为根本无关的工序都问询。
第一天过去后,制造经理忧心忡忡地找我希望我能亲自出马,以期从我身上获得更多信心。
软件研发的6sigma案例解析

软件研发的6sigma案例解析一、6sigma能帮助解决软件技术问题吗?第一个项目是在去年年末,参加一个事业部的6sigma优秀项目公布会看到的。
项目名称是《XX网管系统提高告警吞吐率》,问题是在大量告警上报时,UNIX服务器的告警处理吞吐率仅为8条/秒,同时占用CPU达90%,导致其它模块的操作基本上不能进行。
用户对此非常不满,要求我公司尽快解决此问题,提高吞吐率到至少48条/秒,而系统成本不能有较大幅度增加。
如何解决这个问题?一个解决方案是提高硬件的配置,从而提高处理性能,但是这样做会大大增加采购成本,而性能并不可能有极大的提升,实际上降低了产品的可销性,这样的投入收益比极不合算,此方案被拒绝。
项目组在花了大量时间与精力,仍然寻找不到合适的解决办法之后,想到了6sigma。
大家明白,6sigma项目的选择就是那些“难度大、影响力大”的问题,因此这个项目组的成员将此问题立项,期待6sigma能在黑暗中带来曙光。
除去定义与测量阶段,此项目的分析思路是这样的:首先是头脑风暴鱼骨图,罗列所有大家能想到的可能原因;然后将这些原因按照告警的逻辑处理流程组织成FMEA,进行RPN分析,筛选出RPN值大于100的少数因素,作为潜在的关键因子;之后对这些潜在因子逐一试验,进行确认。
整个项目的突破就出现在第一个因子的试验中,其试验数据如图1所示,横坐标表示输入的告警流量,纵坐标表示告警处理延时。
图中的曲线显示有周期性的拐点,而在拐点之后,告警流量增加,服务器的处理延时反而有较大的降低。
这个现象假如没有针对此原因的试验,没有这些数据是无法看到的。
分析这个现象的原因,难不到我们的软件工程师,很快就得出了结论:TCP协议参数设置不当。
修改此参数后,重新做同样的试验,得到数据如图2所示,可见其告警吞吐率基本上与输入流量呈线性关系增长,瓶颈已经消除。
这不仅仅是确认了此因子是关键因子,同时也验证了改进措施的有效性。
另外几个因子也是类似的,通过针对每一种可疑因子的试验,或者确认此因子为关键因子,或者筛选影响不大的因子;然后针对每个关键因子寻找技术上的解决办法,就更不在话下了。
六西格玛改进案例

六西格玛改进案例以六西格玛改进案例为题,列举如下10个案例:1. 生产流程改进案例:在一个制造业公司,生产流程中存在着许多瑕疵品。
为了提高产品质量,该公司采用了六西格玛方法进行改进。
通过分析生产过程中的关键环节,确定了引起瑕疵品的主要原因,并通过改进工艺和设备,减少了瑕疵品的产生率。
2. 供应链管理改进案例:一家零售公司的供应链管理存在着库存过剩和缺货的问题,导致了销售额下降。
为了解决这个问题,该公司运用了六西格玛方法,对供应链中的各个环节进行了优化。
通过提高库存预测的准确性,优化订货策略,以及改进供应商管理,该公司成功解决了库存过剩和缺货问题。
3. 客户投诉处理改进案例:一家电信运营商的客户投诉率较高,影响了公司的声誉。
为了改善客户满意度,该公司运用了六西格玛方法,对客户投诉处理流程进行了改进。
通过提高投诉处理的效率和质量,该公司成功降低了客户投诉率,并提升了客户满意度。
4. 销售流程改进案例:一家保险公司的销售流程存在着繁琐和低效的问题,导致了销售人员的工作效率低下。
为了提高销售业绩,该公司采用了六西格玛方法,对销售流程进行了改进。
通过简化流程、优化销售工具和培训销售人员,该公司成功提升了销售人员的工作效率和销售业绩。
5. 质量管理改进案例:一家制药公司的质量管理体系存在着缺陷,导致了产品质量不稳定。
为了提高产品质量,该公司采用了六西格玛方法,对质量管理体系进行了改进。
通过加强质量控制、改进检验方法和加强员工培训,该公司成功提升了产品质量的稳定性。
6. 项目管理改进案例:一个IT项目存在着进度延误和成本超支的问题,导致了项目无法按时交付。
为了解决这个问题,该公司采用了六西格玛方法,对项目管理进行了改进。
通过优化项目计划、加强资源管理和改进沟通机制,该公司成功提高了项目的进度控制和成本控制能力。
7. 售后服务改进案例:一家家电企业的售后服务存在着响应速度慢和问题解决率低的问题,导致了客户的不满意。
六西格玛案例6SIGMA确定改进机会课件

范例:小组授权书
产品交付
业务专案
我们目前的X产品平均递送时间是72小时.客户要求48小时.我 们的竞争者可以满足48小时的要求.结果是,我们最近10个月中 每个月损失了1.5%的客户($75,000/月),在同样的10个月内新的 销售额下降了10%($60,000/月).降低我们的递送时间,我们预计 现有客户基础下降可低于0.3%, 新的销售额将在原有的基础上
Page 11
项目范围
目的
➢ 项目范围确定了业务改进机会的边界。
项目范围
➢ 流程及行动的边界,起始和终止步骤是什么? ➢ 业务的什么部分被包括在内? ➢ 业务的什么部分没有被包括在内? ➢ 如果有的话,什么是在小组边界外的?
Page 12
小组挑选
目的
➢ 挑选你的小组成员并分派责任。
小组挑选
➢ 谁对谁负责,负责什么? ➢ 谁是项目担保人?他/她对小组的责任是什么? ➢ 项目小组怎样协调他们的工作? ➢ 谁是小组领导人?小组领导人的责任是什么? ➢ 谁在小组之上? ➢ 小组多久汇报一次?怎样汇报? ➢ 需要什么类型的小组成员?在什么阶段需要他们?
Page 27
职能分布流程图
• 与流程分解图一样,职能分布流程图按顺序显示了流程的步骤, 它也阐明了每个流程在那里和被谁执行.
特征 • 用如以下所列的符号来表示流程流向,决定要点和执行活动. • 职能分布流程图通常要用相当多的时间来准备,但是它们对在
执行改进前了解流程特别有帮助.它们 需要熟悉流程每个领 域人的输入.
Page 8
业务专案
业务专案阐明 • 业务专案描述了项目执行的收益,业务专案解
决以下问题:
➢ 项目和其他业务工作有结合起来吗? ➢ 项目小组的重点是什么? ➢ 小组工作应该在哪里开始和结束? ➢ 项目对其他业务单元和雇员有什么影响? ➢ 项目会收到什么收益? ➢ 收益的价已经被量化了吗?
- 1、下载文档前请自行甄别文档内容的完整性,平台不提供额外的编辑、内容补充、找答案等附加服务。
- 2、"仅部分预览"的文档,不可在线预览部分如存在完整性等问题,可反馈申请退款(可完整预览的文档不适用该条件!)。
- 3、如文档侵犯您的权益,请联系客服反馈,我们会尽快为您处理(人工客服工作时间:9:00-18:30)。
制造三部高内阻改善项目
选题 理由 VOC CTQ MSA Y现状 能力 Y分布 规律 目标 设定 财务 分析
Six sigma
08年高内阻Y的公布:对比07年无明显下降趋势
1-4月汇总高内阻趋势图
3.50% 3.00% 2.50% 2.00% 1.50% 1.00% 0.50% 0.00%
4V M7 4 V K 23 M7 4 V K 28 M7 4 V L 01 M7 4 V L 05 M7 4 V L 11 M7 4 V L 17 M7 4 V L 20 M7 4 V L 25 M7 4 V L 28 M8 4 V A 01 M8 4 V A 04 M8 4 V A 08 M8 4 V A 11 M8 4 V A 18 M8 4 V A 22 M8 4 V A 24 M8 4 V A 28 M8 4 V A 31 M8 4 V B 05 M8 4 V B 12 M8 4 V B 15 M8 4 V B 19 M8 6 V B 29 M8 4 V B 22 M8 4 V B 28 M8 4 V C 04 M8 4 V C 07 M8 4 V C 10 M8 4 V C 13 M8 4 V C 19 M8 4 V C 22 M8 4 V C 25 M8 4 V C 28 M8 D0 To 1 ta l
10200ppm
12000 10000 8000 6000 4000 2000 0
3100ppm
综合Y的分布规律和 历史数据, 得出:主要改善方向 是对滚槽机负极耳 点焊工序进行改善, 从而降低高内阻电芯 的产出。 目标如左图
制造三部高内阻改善项目
选题 理由 VOP CTQ MSA Y现状 能力 Y分布 规律 目标 设定 财务 分析
Six sigma
领取高内阻电池
NG
判定高内阻原因:极组内阻NG
OK
测量极组内阻值
OK 解剖查看负极点焊情况
放电 解剖钢 壳
OK
判定高内阻原因:负极耳虚焊
测量电池内阻值
2.电芯内部不明断路NG NG 1. 判定高内阻原因 : 正极耳抽出 NG
52
48
1
2
3
4
5 6 编号
7
8
9
10
由无人员误差,测量系统非常好。
MSA测量系统: %研究变异 ≤30%,测量系 统合格
制造三部高内阻改善项目
选题 理由 VOP CTQ MSA Y现状 能力 Y分布 规律 目标 设定 财务 分析
Six sigma
高内阻不良项目 y 的分布柏拉图
500 100
按08年1 月至4月 份止产出 的高内阻 不良品数, 不良率合 计是 10200PP M计算得 出
类别 负极耳虚焊 负极耳弯折 正极耳抽出
94.3%
制造三部高内阻改善项目
选题 理由 VOC CTQ MSA Y现状 能力 Y分布 规律 目标 设定
Six sigma
目前Y的CTQ
I
Y:负极耳虚焊
f (X)
滚槽负极点焊
O 高内阻
制造三部高内阻改善项目
选题 理由 VOC CTQ MSA Y现状 能力 Y分布 规律 目标 设定
制造三部高内阻改善项目
选题 理由 VOC CTQ MSA Y现状 能力 Y分布 规律 目标 设定 财务 分析
Six sigma
负极耳虚焊机器分布柏拉图
500 100
负极耳虚焊分布机台 左图是从解剖电芯的数据, 分析负极耳虚焊所 产出的设备分布规律 柏拉图,从图中可得出: 2#滚槽机负极耳虚焊数量 占三台机器所产出的 70.6%,为三台机器中最 高。 故:后续改善可着重分析 2#滚槽机点焊工序。
3
3 2
K22 K23 K24 K26 K27 K28 K29 K30 L01 L03 L04 L05 L06 L07 L10 L11 L12 L14 L15 L25 L26 L28 L31 A01 A02 A03 A04 A26 A28
Batch
制造三部高内阻改善项目
选题 理由 VOC CTQ MSA Y现状 能力 Y分布 规律 目标 设定 财务 分析
400
80
200
40
100
20
0 机器号 数量 百分比 累积 %
2# 358 70.6 70.6
3# 96 18.9 89.5
1# 53 10.5 100.0
0
百分比
数量
300
60
制造三部高内阻改善项目
选题 理由 VOC CTQ MSA Y现状 能力 Y分布 规律 目标 设定
Six sigma
改善目标图
测量正极耳与钢壳内阻值 检查正极耳状态 OK
解剖顶 盖
测量帽盖内阻值
NG
判定高内阻原因:帽盖内阻NG
高内阻电池原因分析解剖流程图
制造三部高内阻改善项目
选题 理由 VOP CTQ MSA Y现状 能力 Y分布 规律 目标 设定 财务 分析
Six sigma
解剖寻找Y的CTQ
图三:测卷芯内阻
图一:用管钳解剖
Six sigma
07年高内阻Y的不良率分布
07年10月份至12月份高内阻推移图
9.00% 8.00% 7.00% 6.00% 5.00% 4.00% 3.00% 2.00% 1.00% 0.00%
4V M7 H 4V 23 M7 H 4V 24 M7 H 4V 25 M7 K 4V 02 N7 J 4V 12 N7 J 4V 13 N7 J 4V 18 N7 J 4V 19 N7 J 4V 20 N7 J 4V 25 N7 J 4V 26 N7 J 4V 27 N7 K 4V 05 N7 K 4V 08 N7 K 4V 10 M7 K 4V 21 M7 K 4V 22 M7 K 4V 23 M7 K 4V 24 M7 K 4V 26 M7 K 4V 27 M7 K 4V 28 M7 K 4V 29 M7 K 4V 30 M7 L 4V 01 M7 L 4V 03 M7 K 4V 23 M7 K2 7 To ta l
批次
10月 4VM7 H25 4VM7J13 4VM7K08 4VM8K27
高内阻最高 不良批次 不良率
8.18% 2.32% 2.49% 2.05% 2.01%
11月
12月
4VM8K29
系列2
汇总07年10-12月份高内阻电芯占生产电芯不良率为:13800PPM;而占工序检测 次品数不良率为: 24610PPM;右表为各月份高内阻电芯占批次不良最高比率的两 个批次。
VOC/VOB调查
高内阻不良品的解剖 + 小组讨论 =
关键CTQ确定
确定关键CTQ的计算公式 图表展示Y现状
对Y的现状进行统计 确定Y和各小y的目标
预算财务收益
按目标进行收益评估
制造三部高内阻改善项目
选题 理由 VOP CTQ MSA Y现 状 能力 Y分 布 规律 目标 设定 财务 分析
Six sigma
2月
3月
4月
内阻不良所占检验数比率
内阻不良所占次品数比率
汇总1--4月份高内阻电芯占生产电芯不良率为:10200PPM;而占工序检测次品 数不良率为: 15830PPM;右表为各月份高内阻电芯占批次不良最高比率的两个 批次。
制造三部高内阻改善项目
选题 理由 VOC CTQ MSA Y现状 能力 Y分布 规律 目标 设定
样本极差
值 H
60
测量人员
Xbar 控制图(按 测量人员)
姜彩虹 56 张娜娜 赵时枚
张娜娜 测量人员
赵时枚
测量人员 乘 编号 交互作用
测量人员
样本均值
平均
_ _ UCL=54.29 X =54.01 LCL=53.74
56 52 48
姜彩虹 张娜娜 赵时枚
研究变异 %研究变 来源 标准差(SD) (6 * SD) 异 (%SV) 合计量具 R&R 0.14335 0.8601 5.72 重复性 0.14335 0.8601 5.72 再现性 0.00000 0.0000 0.00 测量人员 0.00000 0.0000 0.00 部件间 2.50289 15.0173 99.84 合计变异 2.50699 15.0419 100.00
Member
负责方案培 训、指导, 客户和专业 信息收集、 分析指导
负责设备的 管理和维护, 原因分析和 改进项目
负责项目改 善方案、措 施的跟进, 实验验证
负责滚槽A 班人员改善 项目措施执 行和控制
负责滚槽B 班人员改善 项目措施执 行和控制
制造三部高内阻改善项目
Six sigma
项目进度表
data Define
量具名称: 研究日期: 内阻测试仪 2008-5-9
变异分量
100
百分比
% 贡献
报表人: 公差: 其他:
周承亮
值 H
60 55 50
编号
50
0
量具 R&R
重复
再现性
部件间
1
2
3
4
5 编号
6
7ห้องสมุดไป่ตู้
8
9
10
R 控制图(按 测量人员)
姜彩虹 0.50 0.25 0.00 _ R=0.2667 LCL=0 55 50 姜彩虹 张娜娜 赵时枚 UCL=0.6865
完成现状分 析和目标定 义,完成项 目财务收益 估算 完成主要X的 MSA,并找 到主要的X项 目 确认主要X
Measure
Analyze
Improve
Control
3.18-4.30
4.30-5.30
5.30-6.30
6.30-7.30