数控回转工作台的回转运动驱动电机的选择计算
习题册数控机床系统结构答案

第一章第一节数控机床的产生和发展第二节数控机床的特点和应用范围一、填空题1、第一代数控机床产生于1952年美国国麻省理工学院研究出一套试验性的数字数控系统,并把它安装在立式铣床上。
2、我国是1958年开始研究数控技术的。
3、机械加工的目标是高速、高效。
高精度。
4、在数控机床上加工工件,工件的加工精度主要取决于机床精度、插补精度、编程伺服精度。
5、最早的数控机床伺服系统执行机构采用液压转矩放大器。
二、选择题1、第一代数控机床产生于(B )年。
A、1951B、1952C、19542、第三代数控机床产生于( C )年,研制出了小规模集成电路。
A、1951B、1952C、19603、经济型数控机床一般都采用(A)数控系统。
A、开环B、闭环C、半闭环4、(C)数控机床产生于1960年,研制出了小规模集成电路。
A、第一代B、第二代C、第三代D、第四代三、判断题1、第三代数控机床产生于1960年,研制出了小规模集成电路。
(1 )2、点位控制系统控制刀具或机床工作台,从一点准确地移动到另一点,也控制点与点之间运动的轨迹。
(2)3、第四代数控机床的标志是小型计算机。
(1)四、简答题1、简述数控机床发展的六个时代及标志。
1952电子管时代;1956晶体管时代;1960小规模集成电路;1970由计算机作控制单元的数控系统;1974以微处理器为核心的数控系统;1990柔性制造单元2、数控机床的特点是什么?适应性强;能实现复杂的运动;加工精度高;生产效率高;能减轻劳动强度,改善劳动环境,有利于科学的生产管理3、简述数控机床的应用范围。
1)多品种小批量生产的零件。
2)形状结构比较复杂的零件。
3)需要频繁改型的零件。
4)价格昂贵,不允许报废的关键零件。
5)需要最短周期制作的急需零件。
6)批量较大精度要求很高的零件。
第二节数控机床的分类一、填空题1、按控制方式划分,数控机床可分为开环、半闭环和闭环三类。
其中开环中没有检测反馈装置,控制精度较低。
数控回转工作台的回转运动驱动电机的选择计算
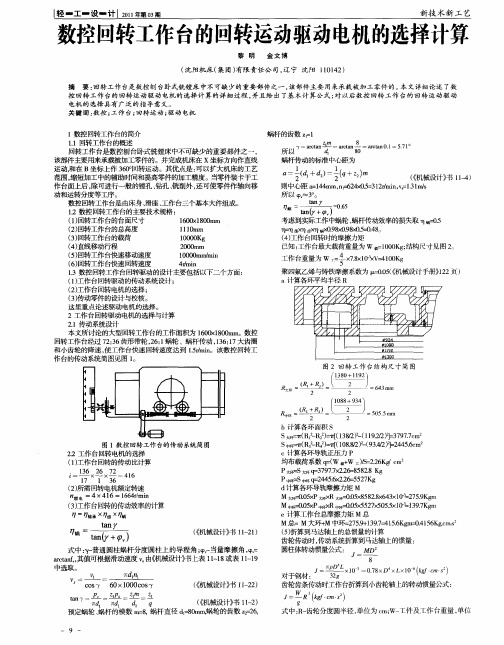
2 . 2工作 台回转 电机 的选择 () 1工作台回转的传动比计算
16 3
一
b计算各环 面积 s S TR2 2= 1 8 ) 19 /) 7 7 c 2 } 1 lR 2 ( 3 / L( 1. 2 3 9 . m =’ _ ) ( 2 2 7 S ( 3R2 (0.2L 9 .2 ̄2 4. m 十 : Rz 4= 18 /) (3 /) 4 5 c _ ) 8 4 = 6 c计算 各环导轨 正压力 P 均 布载荷 系数 (( 载 w ) =. K / m F W 十 I/ 2 6 g c : S 2
关键 词 : 数控 ; 工作 台; 回转 运 动 ; 动 电机 驱
1数控 回转 工作 台的简介 蜗杆 的齿数 z l l = 1 . 1回转 工作 台的棚述 ra 1 . 1 cn rt 7 一 a c ar t c an d tn f c a 旦 :at 0 : 57 。 r 所 以 一 一 8 O ・ ・ 回转 工作 台是数 控刨 台卧 式铣镗 床 中不 可缺 少 的重要 部件 之一 , 蜗 杆传动 的标 准 中心距 为 该部件主要用来承载被加工零件的。并完成机床在 x坐标方向作直线 运动, B坐标上作 3 0回转运动。其优点是: 和在 6 ̄ 可以扩大机床的工艺 范围, 缩短加 工 中的辅 助时间和提 高零件 的加 工精度 。当零 件装卡 于工 作 台面上后 , 除可进行一 般 的镗 孔 、 钻孔 、 削外 , 可使零 件作 轴 向移 铣 还 则 中心距 a14 m, ̄ 2x. 32 mnv 1 l / =4 m n 640 = 1r i,e . ms = 5 / =3 动和运转 分度等工序 。 所 以 ‘ 一3。 p 。 数控回转工作台是 由床身、 、 滑座 工作台三个基本大件组成。 1 . 2数控 回转工作 台的主要技术 规格 : () 1回转工作 台的台面尺寸 10x 80 m 60 10 m 考虑到实 际工 作 中蜗轮 、 杆传动效率 的损失取 =. 蜗 0 5 -_q蒗× 齿 q- - - 1 ×1 ̄x .8 098 0.= .8 09 x . x 5 04 。 () 工作 台的总高度 2回转 11r 0m 1 a () 工作 台的载荷 3回转 100 g 00K () / 台回转时的摩擦 力矩 45 r E ̄ () 4直线移动行程 20 m 00 m 已知 : 台最大 载荷重量 为 W -00 g ̄ 尺寸见 图 2 工作 - 0K ; 1 。 () 5回转工作 台快 速移动速度 100 mm n 0 0 m /i 工作台重量 为 w x. 1 ̄V 40 K 7 x 0x - 10 g 8 () 6回转工作 台快 速 回转速 度 4/i r n m 聚四氟乙烯与铸 铁摩擦 系数 为  ̄ o 5( - . (机械没 汁手册 》2 页 ) o ( l2 1 . 3数控 回转 工作 台回转驱动 的设 计主要包 括以下二 个方 面 : a 计算各环平均半径 R () 1工作台回转驱动的传动系统设计; () 2工作台 回转 电机的选择 ; () 动零件 的设 计与校核 。 3传 这里重 点论述驱 动 电机 的选 择 。 2工作 台回转 驱动 电机 的选择与计算 2 . 1传动系统设计 本文 所讨论 的大型 回转工作 台的工作 面积为 10 x8 0 m 60 l0 m 。数控 回转工作 台经过 7 : 齿 形带轮 ,6 1 23 6 2 : 蜗轮 、蜗 杆传动 ,3 :7 161 大齿 圈 和小齿 轮的降速 , 工作 台快速 回转速度 达到 1 r i。该数 控 回转工 使 5/ n m 作台 的传 动系统简 图见 图 1 。
数控回转工作台的原理和设计

数控回转工作台的原理和设计崔旭芳1周英2(1燕山大学继续教育学院,河北秦皇岛066004;2海湾安全技术股份有限公司,河北秦皇岛066004)摘要:数控回转工作台是五轴联动的基础,它能够实现回转轴与摆动轴的两坐标定位。
在三轴联动的数控铣床上增加数控回转工作台,并通过数控改造使之成为五轴数控铣床,是扩展机床使用功能的简捷方式。
详细分析和说明了双回转工作台的分类、结构、工作原理和设计过程。
设计中采用了先进的电主轴作为主轴系统的核心部件,使机械结构更加简单、控制部分相应简化,并可以方便地与CAD/CAM结合,为数控机床的改造提供依据。
关键词:数控回转工作台;结构;原理;设计中图分类号:TU522.05文献标识码:A文章编号:1001-6945(2008)06-0023-051引言近年来,随着我国国民经济的迅速发展和国防建设的需要,对高档数控机床提出了急迫的大量需求。
机床制造业是一国工业之基石,它为新技术、新产品的开发和现代工业生产提供重要的手段,是不可或缺的战略性产业。
即使是发达工业化国家,也无不高度重视。
机床是一个国家制造业水平的象征,代表机床制造业最高境界的则是五轴联动数控机床系统。
从某种意义上说,五轴联动数控机床系统反映了一个国家的工业发展水平状况。
2五轴联动机床简介及加工特点数控机床加工某些零件时,除需要有沿X、Y、Z三个坐标轴的直线进给运动之外,还需要有绕X、Y、Z三个坐标轴的圆周进给运动,分别称为A、B、C轴。
五轴联动机床也称五坐标机床,它是在三个平动轴(沿X、Y、Z轴的直线运动)的基础上增加了两个转动轴(能实现绕X轴、Z轴旋转运动,即A轴和C轴),不仅可使刀具相对于工件的位置任意可控,而且刀具轴线相对于工件的方向也在一定范围内任意可控,由此使五坐标加工工具有以下特点:a.可避免刀具干涉,加工普通三坐标机床难以加工的复杂零件,加工适应性广,如图1(a)所示。
图1五坐标加工的特点b.对于直纹面类零件,可采用侧铣方式一刀成型,加工质量好、效率高,如图1(b)所示。
伺服电机计算选择应用实例

伺服电机计算选择应用实例1. 选择电机时的计算条件 本节叙述水平运动伺服轴(见下图)的电机选择步骤。
例:工作台和工件的 W :运动部件(工作台及工件)的重量(kgf )=1000 kgf 机械规格 μ :滑动表面的摩擦系数=0.05π :驱动系统(包括滚珠丝杠)的效率=0.9 fg :镶条锁紧力(kgf )=50 kgfFc :由切削力引起的反推力(kgf )=100 kgfFcf :由切削力矩引起的滑动表面上工作台受到的力(kgf )=30kgfZ1/Z2: 变速比=1/1 例:进给丝杠的(滚珠 Db :轴径=32 mm 丝杠)的规格 Lb :轴长=1000 mm P :节距=8 mm例:电机轴的运行规格 Ta :加速力矩(kgf.cm )Vm :快速移动时的电机速度(mm -1)=3000 mm -1 ta :加速时间(s)=0.10 sJm :电机的惯量(kgf.cm.sec 2) Jl :负载惯量(kgf.cm.sec 2)ks :伺服的位置回路增益(sec -1)=30 sec -1 1.1 负载力矩和惯量的计算 计算负载力矩 加到电机轴上的负载力矩通常由下式算出:Tm = + TfTm :加到电机轴上的负载力矩(Nm) F :沿坐标轴移动一个部件(工作台或刀架)所需的力(kgf) L :电机转一转机床的移动距离=P ×(Z1/Z2)=8 mmTf:滚珠丝杠螺母或轴承加到电机轴上的摩擦力矩=2Nm无论是否在切削,是垂直轴还是水平轴,F 值取决于工作台的重量,摩擦系数。
若坐标轴是垂直轴,F 值还与平衡锤有关。
对于水平工作台,F 值可按下列公式计算: 不切削时: F = μ(W+fg ) 例如: F=0.05×(1000+50)=52.5 (kgf) Tm = (52.5×0.8) / (2×μ×0.9)+2=9.4(kgf.cm)= 0.9(Nm)切削时:F = Fc+μ(W+fg+Fcf) 例如: F=100+0.05×(1000+50+30)=154(kgf) Tmc=(154×0.8) / (2×μ×0.9)+2=21.8(kgf.cm)=2.1(Nm)为了满足条件1,应根据数据单选择电机,其负载力矩在不切削时应大于0.9(Nm ),最高转速应高于3000(min -1)。
2024-数控机床回转工作台(全)
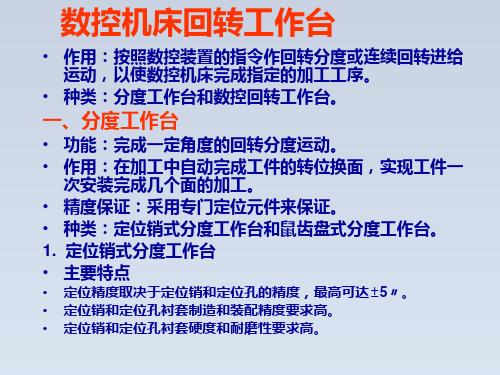
由于多齿啮合,啮合率高,所以定位刚 度好,承载能力强。
最小分度为360º/Z,分度数目多,适用于 多工位分度。
由于离合过程具有磨合作用,其定位精 度不断提高,使用寿命长。
缺点是鼠齿盘制造相较困难。
鼠齿盘及齿形结构如图
工作过程分为三步:
工作台抬起
工作台回转分度
工作台下降并定位锁紧
为了尽量消除反向间隙和传动间隙,通过调整偏 心环3来消除齿轮2和4啮合侧隙。
齿轮4与蜗杆9是靠楔形拉紧圆柱销5〔A一A剖面〕 来连接。
这种连接方式能消除轴与套的配合间隙。
蜗杆9采用螺距渐厚蜗杆,通过移动蜗杆的轴向位 置来调节间隙。
〔图〕测蜗杆的左右两侧具有不同的螺距因此蜗杆 齿厚从头到尾逐渐增厚。 但由于同一侧的螺距是相同的,所以仍能保持正确 的啮合。 调整时松开螺母7的锁紧螺钉8使压块6与调整套松 开。 然后转动调整套11带动蜗杆9作轴向移动。 调整后锁紧调整套11和楔形圆柱销5。 蜗杆的左右两端都有双列滚针轴承支承, 左端为自由端可以伸缩以消除温度变化的影响, 右端装有两个推球轴承能轴向定位。
• TK56系列数控等分转台是数控镗铣床和加工中 心的理想配套附件,可以安装于主机工作台面 上,工作时,在主机相关控制系统控制下,能 够完成以1°为基数的等分分度零件的加工。
• TK14系列数控可倾斜回转工作台,可完 成等分和不等分的角度分度工作。工作台 既可回转,又可倾斜,具有2个自由度。
数控机床回转工作台
电磁铁控制液压阀〔图中未示出〕,使压力油经 孔23进入到工作台7中央的夹紧液压缸下腔10推 动活塞6向上移动,
经推力轴承5和13将工作台7抬起,上下两个鼠齿 盘4和3脱离啮合,
〔图〕当工作台静止时,必须处于锁紧状态。
数控回转工作台
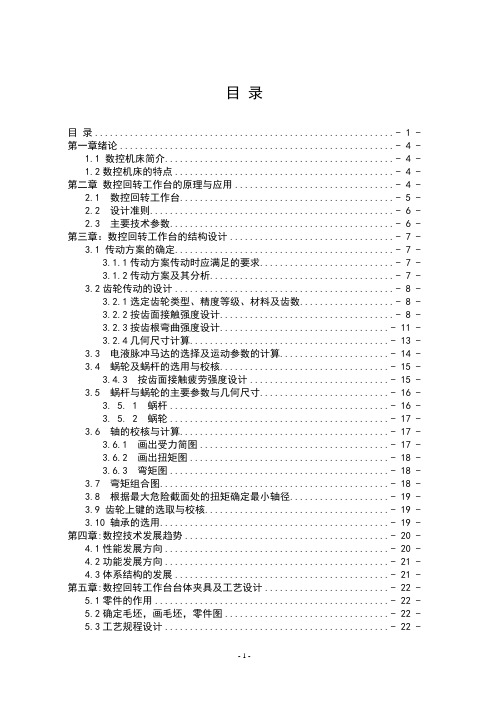
目录目录............................................................ - 1 - 第一章绪论....................................................... - 4 -1.1 数控机床简介.............................................. - 4 -1.2数控机床的特点............................................ - 4 - 第二章数控回转工作台的原理与应用................................ - 4 -2.1 数控回转工作台........................................... - 5 -2.2 设计准则................................................. - 6 -2.3 主要技术参数............................................. - 6 - 第三章:数控回转工作台的结构设计................................. - 7 -3.1 传动方案的确定............................................ - 7 -3.1.1传动方案传动时应满足的要求........................... - 7 -3.1.2传动方案及其分析..................................... - 7 -3.2齿轮传动的设计............................................ - 8 -3.2.1选定齿轮类型、精度等级、材料及齿数................... - 8 -3.2.2按齿面接触强度设计................................... - 8 -3.2.3按齿根弯曲强度设计.................................. - 11 -3.2.4几何尺寸计算........................................ - 13 -3.3 电液脉冲马达的选择及运动参数的计算...................... - 14 -3.4 蜗轮及蜗杆的选用与校核.................................. - 15 -3.4.3 按齿面接触疲劳强度设计............................ - 15 -3.5 蜗杆与蜗轮的主要参数与几何尺寸.......................... - 16 -3. 5. 1 蜗杆............................................ - 16 -3. 5. 2 蜗轮............................................ - 17 -3.6 轴的校核与计算.......................................... - 17 -3.6.1 画出受力简图...................................... - 17 -3.6.2 画出扭矩图........................................ - 18 -3.6.3 弯矩图............................................ - 18 -3.7 弯矩组合图.............................................. - 18 -3.8 根据最大危险截面处的扭矩确定最小轴径.................... - 19 -3.9 齿轮上键的选取与校核..................................... - 19 -3.10 轴承的选用.............................................. - 19 - 第四章:数控技术发展趋势......................................... - 20 -4.1性能发展方向............................................. - 20 -4.2功能发展方向............................................. - 21 -4.3体系结构的发展........................................... - 21 - 第五章:数控回转工作台台体夹具及工艺设计......................... - 22 -5.1零件的作用............................................... - 22 -5.2确定毛坯,画毛坯,零件图................................. - 22 -5.3工艺规程设计............................................. - 22 -5.3.1定位基准的选择...................................... - 22 -5.3.2选择加工设备及刀,夹,量具.......................... - 22 -5.4夹具设计................................................. - 23 - 结论............................................................ - 24 - 致谢......................................................... - 25 - 参考文献........................................................ - 26 -摘要数控车床今后将向中高挡发展,中档采用普及型数控刀架配套,高档采用动力型刀架,兼有液压刀架、伺服刀架、立式刀架等品种,预计近年来对数控刀架需求量将大大增加。
数控回转工作台资料

在目前的机械行业当中只有数控铣床、加工中心和数控镗床都应用回转工作台,并且这三种机床的使用最普遍。与其他的普通回转台相比起来,在外形上看来他们并没有什么区别,只是他们有不同的驱动,一种是手动回转,而数控回转工作台是与其他的数字控制驱动结合。
图1-1闭环内部结构
1-进电机;2-主动齿轮;3-偏心环;4-从动齿轮;5-柱销;6-压块;7-螺母;8-锁紧螺钉、11-轴承盖、套筒;9-蜗杆;10-蜗轮;12、13-加紧瓦;14-压紧液压缸;15-活塞;16-弹簧;17-钢球;18-光栅;
蜗杆传动的特点:
1.结构紧凑蜗杆每旋转一周,蜗轮转过一个齿距,所以可以实现大的传动比。传动比比其他传动方式的大,所需零件数目少,不占用空间,所以结构相对紧凑。
2.冲击载荷小、传动平稳、噪声低因为蜗轮蜗杆在传动过程中是很缓慢的进入啮合然后慢慢地退出啮合的,而且齿对相对来说较多。
3.自锁由于蜗杆的螺旋线升角与当量摩擦角相比较小,所以当蜗杆传动时具有自锁功能。
转工作台主要是与立式铣床配套使用,其精度直接影响到机床的性能。本次设计选择由步进电动机作为动力源,一级圆柱直齿轮减速器进行减速及传递转矩和转速,将其传递给蜗轮蜗杆机构来带动工作台进行回转加工工作。数控回转工作台与数控立式铣床结合使用可进行工件的分度和切削旋转,配合机床X、Y、Z三轴的直线运动可以扩大机床的加工范围,来提高机床的工作效率。配合数控系统的控制,数控回转工作台可以有效提高生产效率,消除人为误差,提高加工精度。本次主要设计方向是数控铣床中的数控回转工作台,我们对主要的零件进行了结构功能设计。装配图、零件图用CAXA软件绘制。
关键词:立式铣床数控回转工作台齿轮蜗轮蜗杆
Abstract
Thedesignof the NC rotary table is mainly with vertical milling machine , Its precision directly affects the performance of the machine. The design choices the stepping motor as a power source. Level of cylindrical spur gear reduce of reduction and transmission torque and rotational speed, pass it to worm and worm wheel mechanism to drive the workbench rotary processing work. NC rotary table with NC vertical milling machine combined with the use of artifacts can be dividing and cutting rotation, cooperate with X,Y,Z three axis machine tool can expand the linear motion of the machine toolprocessing range, to improve the working efficiency of the machine tool. With NC system, the control of NC rotary table can effectively improve the production efficiency, eliminating human error, and improve the machining accuracy. The main design direction is the NC rotary table in CNC milling machine, structure and function of main parts of our design. Assembly drawing and part drawing drawn using CAXA software.
伺服电机选型计算实例
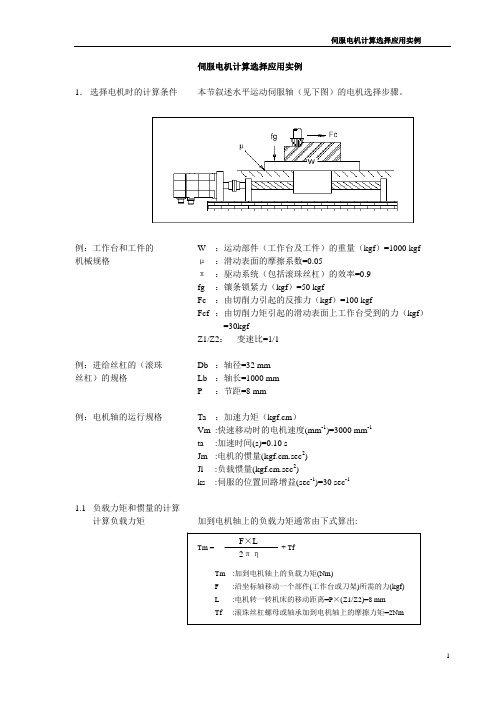
4
1.2 加速力矩的计算 计算加速力矩:步骤 1
·直线加/减速
伺服电机计算选择应用实例
如果负载惯量比 3 倍的电机惯量大的多,则控制特性将大大下降。 此时,电机的特性需要特殊调整。使用中应避免这样大的惯量。若 机械设计出现这种情况,请与 FANUC 联系。
按下步骤计算加速力矩: 假定电机由 NC 控制加/减速,计算其加速度。将加速度乘 以总的转动惯量(电机的惯量 + 负载惯量),乘积就是加速力矩。 计算式如下。
切削时: F = Fc+μ(W+fg+Fcf) 例如: F=100+0.05×(1000+50+30)=154(kgf) Tmc=(154×0.8) / (2×μ×0.9)+2=21.8(kgf.cm) =2.1(Nm)
为了满足条件 1,应根据数据单选择电机,其负载力矩在不切削时 应大于 0.9(Nm),最高转速应高于 3000(min-1)。考虑到加/减速, 可选择α2/3000(其静止制加/减速时
速度
指令
转矩
Vm
Ta
ta
时间
Vm 速度
计算加速力矩:步骤 2
公式为:
Ta =
Vm ×2π× 1 ×(Jm+JL)
60
ta
1
Ta = 为了得到电机k轴s 上的力矩 T,应在加速力矩 Ta 上增加 Tm
(摩擦力矩)。
T = Ta+Tm T = 12.1(Nm)+0.9(Nm) = 13.0 (Nm)
J L= 0.0082+0.0165 = 0.0247(kgf.cm.s2) 负载惯量对电机的控制特性和快速移动的加/减速时间都有 很大影响。负载惯量增加时,可能出现以下问题:指令变化后,需 要较长的时间达到新指令指定的速度。若机床沿着两个轴高速运动 加工圆弧等曲线,会造成较大的加工误差。 负载惯量小于或等于电机的惯量时,不会出现这些问题。若负载惯 量为电机的 3 倍以上,控制特性就会降低。实际上这对普通金属加 工机床的工作的影响不大,但是如果加工木制品或是高速加工曲线 轨迹,建议负载惯量要小于或等于电机的惯量。
- 1、下载文档前请自行甄别文档内容的完整性,平台不提供额外的编辑、内容补充、找答案等附加服务。
- 2、"仅部分预览"的文档,不可在线预览部分如存在完整性等问题,可反馈申请退款(可完整预览的文档不适用该条件!)。
- 3、如文档侵犯您的权益,请联系客服反馈,我们会尽快为您处理(人工客服工作时间:9:00-18:30)。
数控回转工作台的回转运动驱动电机的选择计算1.数控回转工作台的简介
1.1回转工作台的概述
回转工作台是数控刨台卧式铣镗床中不可缺少的重要部件之一,该部件主要用来承载被加工零件的。
并完成机床在X坐标方向作直线运动,和在B坐标上作360°回转运动。
其优点是:可以扩大机床的工艺范围,缩短加工中的辅助时间和提高零件的加工精度。
当零件装卡于工作台面上后,除可进行一般的镗孔、钻孔、铣削外,还可使零件作轴向移动和运转分度等工序。
数控回转工作台是由床身、滑座、工作台三个基本大件组成。
1.2数控回转工作台的主要技术规格:
(1)回转工作台的台面尺寸1600×1800mm
(2)回转工作台的总高度1110mm
(3)回转工作台的载荷10000Kg
(4)直线移动行程2000mm
(5)回转工作台快速移动速度10000mm/min
(6)回转工作台快速回转速度4r/min
1.3数控回转工作台回转驱动的设计主要包括以下二个方面:
(1)工作台回转驱动的传动系统设计;
(2)工作台回转电机的选择;
(3)传动零件的设计与校核。
这里重点论述驱动电机的选择。
2.工作台回转驱动电机的选择与计算
2.1传动系统设计
本文所讨论的大型回转工作台的工作面积为1600×1800mm。
数控回转工作台经过72:36齿形带轮,26:1蜗轮、蜗杆传动,136:17大齿圈和小齿轮的降速,使工作台快速回转速度达到1.5r/min。
2.2工作台回转电机的选择
2.2.1工作台回转的传动比计算
i=××=416
2.2.2所需回转电机额定转速
n=4×416=1664r/min
2.2.3工作台回转的传动效率的计算
η=η×η×η
式中:η----轴承的传动效率,取0.98;
η----齿轮的传动效率,取0.98;
η----蜗轮、蜗杆的传动效率,需进一步计算。
η= (《机械设计》书11-21)
式中:γ----普通圆柱蜗杆分度圆柱上的导程角;
φ----当量摩擦角,φ=arctanf,其值可根据滑动速度v由《机械设计》书上表11-18或表11-19中选取。
v== (《机械设计》书11-22)
式中:v----蜗杆分度圆的圆周速度,单位为m/s;
d----蜗杆分度圆直径,单位为mm;
n----蜗杆的转速,单位为r/min。
tanγ==== (《机械设计》书11-2)
预定蜗轮、蜗杆的模数m=8, 蜗杆直径d=80mm,蜗轮的齿数z=26,蜗杆的齿数z=1
所以γ=arctan=arctan=arctan0.1=5.71°
蜗杆传动的标准中心距为
a=(d+d)=(q+z)m (《机械设计》书11-4)
则中心距a=144mm,n=624×0.5=312r/min,v=1.31m/s
所以φ≈3°。
η===0.65
考虑到实际工作中蜗轮、蜗杆传动效率的损失取η=0.5
η=η×η×η=0.98×0.98×0.5=0.48。
2.2.4工作台回转时的摩擦力矩
已知:工作台最大载荷重量为W=10000Kg;结构尺寸见图2。
工作台重量为W=×7.8×10×V=×7.3×10×26×160×180=4100Kg
聚四氟乙烯与铸铁摩擦系数为μ=0.05(《机械设计手册》122页)
a 计算各环平均半径R
R===643mm
R中环===505.5mm
b计算各环面积S
S=π(R-R)=π[(138/2)-(119.2/2)]=3797.7cm2
S=π(R-R)=π[(108.8/2)-(93.4/2)]=2445.6cm2
c计算各环导轨正压力P
均布载荷系数q=(W+W)/S=(10000+4100)/(3797.7+2445.6)=2.26Kg/ cm2
P=Sq=3797.7×2.26=8582.8 Kg
P=Sq=2445.6×2.26=5527Kg
d计算各环导轨摩擦力矩M
M=0.05×P×R=0.05×8582.8×643×10=275.9Kgm
M=0.05×P×R=0.05×5527×505.5×10=139.7Kgm
e 计算工作台总摩擦力矩M总
M= M+M=275.9+139.7=415.6Kgm=0.4156Kg.cm.s2
2.4.5折算到马达轴上的总惯量的计算
齿轮传动时,传动系统折算到马达轴上的惯量:
圆柱体转动惯量公式:J=
对于钢材:J=×10=0.78×D×L×10(kgf·cm·s)
式中:M----圆柱体质量,单位为kg;
D----圆柱体体积,单位为cm;
L----圆柱体长度或厚度,单位为cm;
ρ----材料比重,单位为gf/cm3。
齿轮齿条传动时工作台折算到小齿轮轴上的转动惯量公式:
J=R(kgf·cm·s)
式中:R----齿轮分度圆半径,单位为cm;
W----工件及工作台重量,单位为kgf。
齿轮齿条传动时传动系统折算到马达轴上的总转动惯量公式:
J=J+J+R(kgf·cm·s)
式中:J,J----分别为Ⅰ轴、Ⅱ轴上齿轮的转动惯量,单位为(kgf·cm·s); R----齿轮z分度圆半径,单位为cm;
W----工件及工作台重量,单位为kgf。
所以J=0.78×9.03×11.7×10=0.06(kgf·cm·s)
J=0.78×18×8×10=0.66(kgf·cm·s)
J=0.78×8×9×10=0.029(kgf·cm·s)
J=0.78×22.4×8.5×10=1.67(kgf·cm·s)
J=0.78×8.5×7.7×10=0.03(kgf·cm·s)
J=J+J+2J+2(J+J)+=0.06+0.66+2×0.029+2×(1.67+0.03)+×=0.242kgf·cm·s
根据J=0.242kgf·cm·s,选SIEMENS-IFT6105-IAC71交流伺服系统
此电机额定转速n=2000r/min
电机输出功率为P=8.7KW
电机额定转矩为M=3.8kg·m
转子转动惯量为J=168×10kg·m2=0.171kgf·cm·s
通常交流电机转动惯量比J/J≤3倍,此电机J/J=0.242/0.171=1.415(倍),所以选用此电机惯量匹配合理。
2.2.6工作台回转电机的校核
根据机床设计手册第三册的513页,对于数控机床而言,因为动态性能要求较高,所以马达力矩主要是用于产生加速度的。
所以通常可先按式(6.6-63)选择马达,要使快速空载启动力矩小于马达的最大转矩,即M≤M
空载启动力矩M:M=M+ M
马达输出转矩的最大值,即峰值转矩M:M=λM
式中:M----折算到马达轴上的摩擦力矩,单位为kgf·m;
M----马达额定转矩;
λ----马达转矩的瞬时过载系数:交流伺服电机λ=1.5~2。
所以取λ=2
J为折算到马达轴上的总惯量:
J=J+J=0.242+0.171=0.413 kgf·cm·s
加速度力矩M:
M=×10kg·m
式中:J----折算到马达轴上总惯量,单位为kgf·cm·s;
T----系统时间常数,单位为s;
n----马达转速,单位为r/min;
n=n,计算M。
所以M=J×n×10/9.6T(T=0.2秒)=0.413×2000×10/9.6×0.2=4.3kgf·m
折算到马达轴上的摩擦力矩:
M= M/iη==2.1 Kg·m即21Nm
所以空载启动力矩M=M+ M=4.3+2.1=6.4 kgf·m
马达的最大转矩M=λM=2×3.8=7.6 kgf·m
由于空载启动力矩M<马达的最大转矩Mmax,所以该伺服电机符合要求。
3.回转台回转系统驱动电机的设计结论
通过上述的设计与计算,可见工作台回转电机的选择是合适的。
【参考文献】
[1]机械设计.高等学校出版社.2001.
[2]机械设计手册.第三卷.机械工业出版社.1991.
[3]机械设计手册.第三册.机械工业出版社.1986.。