气体保护焊CO2焊接飞溅大的原因分析
气体保护焊接过程中的飞溅与喷溅控制

气体保护焊接过程中的飞溅与喷溅控制气体保护焊接是一种常见的焊接方法,广泛应用于工业生产中。
然而,在气体保护焊接过程中,飞溅与喷溅是常见的问题,给焊接工作带来了不便和隐患。
本文将探讨气体保护焊接过程中的飞溅与喷溅控制的方法和技巧。
首先,了解飞溅与喷溅的原因是解决问题的第一步。
飞溅与喷溅主要是由于焊接电弧和熔池的不稳定造成的。
焊接电弧的不稳定会导致电弧在焊接过程中频繁地闪烁和跳动,从而引起熔池的剧烈波动,进而产生飞溅与喷溅。
因此,控制焊接电弧和熔池的稳定性是解决飞溅与喷溅问题的关键。
其次,选择合适的焊接参数也是控制飞溅与喷溅的重要因素。
焊接参数包括焊接电流、焊接电压、焊接速度等。
合理选择这些参数可以使焊接电弧和熔池保持稳定,减少飞溅与喷溅的发生。
一般来说,增加焊接电流和焊接速度可以减少飞溅与喷溅的产生,但是过高的焊接电流可能会导致熔池过热,从而影响焊缝的质量。
因此,在选择焊接参数时,需要综合考虑焊接质量和飞溅与喷溅的控制。
另外,合理选择焊接材料和气体保护剂也可以有效地控制飞溅与喷溅。
不同的焊接材料和气体保护剂具有不同的特性,对飞溅与喷溅的控制效果也有所差异。
一般来说,选择低飞溅性的焊接材料和气体保护剂可以减少飞溅与喷溅的发生。
此外,保持气体保护剂的流量稳定也是控制飞溅与喷溅的重要因素之一。
适当增加气体保护剂的流量可以提高焊接区域的气氛稳定性,减少飞溅与喷溅的产生。
在实际操作中,还可以采取一些技巧来控制飞溅与喷溅。
例如,通过调整焊枪的角度和位置,可以改变焊接电弧和熔池的稳定性,减少飞溅与喷溅的发生。
此外,合理选择焊接工艺和焊接设备也可以提高焊接的稳定性,从而降低飞溅与喷溅的风险。
总之,控制飞溅与喷溅是气体保护焊接过程中的重要任务。
通过了解飞溅与喷溅的原因,选择合适的焊接参数和材料,合理使用气体保护剂,以及采取一些操作技巧,可以有效地控制飞溅与喷溅的发生。
这不仅可以提高焊接质量,还可以保障焊接工作的安全。
CO2气体保护焊飞溅产生的原因及减少措施

、\
Y
\
2
孓v斛繇P
4
\
60 40 40 60
——一
80 20
—————~
\\
≤
C02(%) Ar(%)
20 80
、/≯2
幽.4
\
H08Mn2SiA /≯2・5
一
摹
一 褂 越6 _
—/
夕
疹 ≤受 \ \ ——/ /
/—≮
/
图2
c02+Ar混合气体中的飞溅率
焊丝≯1.2ram;电流250A;电弧电压30V l——颗粒直径>0.8ram;2——颗粒直径<0.8mm
■●●■■■■■●●■■■●■■■■■_
o
致使电源的动特性不合适,或造成短路电流增长速度过 快或过慢,导致产生飞溅。此外,焊接电流、电压和极 性等规范参数选择不当,也会对飞溅有直接影响。
短,同时熔滴和熔池都在不停的运动,熔滴与熔池极易 发生短路过程,所以CO,气体保护焊除大滴状排斥过渡 外,还有一部分熔滴是短路过渡,在焊接回路中串联大 一些的电感,使短路电流上升速度慢一些,这样可以适 当的减少飞溅。焊接回路中电感值对飞溅率的影响如图 3所示,当电感系数由100肛H增至600pH时,焊接飞溅 显著减小。
敷效率,降低焊接生产率;飞溅物易粘附在焊件上,影 丝,电流为300—350A)、电弧电压较高时,由于CO, 响焊接质量,使焊接劳动条件变差;焊接熔池不稳定, 气体的性质活泼,这时熔滴在斑点压力的作用下而上 使焊缝外形较为粗糙等。 挠,易形成大滴状飞溅。如果再增加电流,熔滴过渡形
二、C02气体保护焊飞溅产生的机理
删灰稍c删昭坦型面
C02气体保护焊飞溅产生的 原因及减少措施
焊接飞溅产生的原因及克服途径
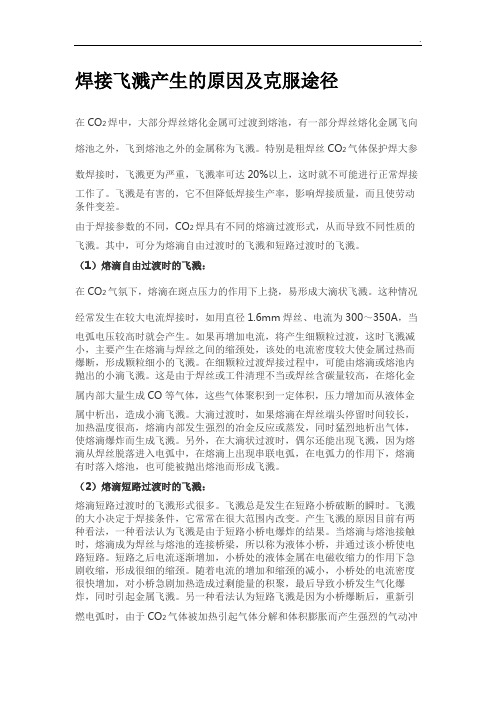
焊接飞溅产生的原因及克服途径在CO2焊中,大部分焊丝熔化金属可过渡到熔池,有一部分焊丝熔化金属飞向熔池之外,飞到熔池之外的金属称为飞溅。
特别是粗焊丝CO2气体保护焊大参数焊接时,飞溅更为严重,飞溅率可达20%以上,这时就不可能进行正常焊接工作了。
飞溅是有害的,它不但降低焊接生产率,影响焊接质量,而且使劳动条件变差。
由于焊接参数的不同,CO2焊具有不同的熔滴过渡形式,从而导致不同性质的飞溅。
其中,可分为熔滴自由过渡时的飞溅和短路过渡时的飞溅。
(1)熔滴自由过渡时的飞溅:在CO2气氛下,熔滴在斑点压力的作用下上挠,易形成大滴状飞溅。
这种情况经常发生在较大电流焊接时,如用直径1.6mm焊丝、电流为300~350A,当电弧电压较高时就会产生。
如果再增加电流,将产生细颗粒过渡,这时飞溅减小,主要产生在熔滴与焊丝之间的缩颈处,该处的电流密度较大使金属过热而爆断,形成颗粒细小的飞溅。
在细颗粒过渡焊接过程中,可能由熔滴或熔池内抛出的小滴飞溅。
这是由于焊丝或工件清理不当或焊丝含碳量较高,在熔化金属内部大量生成CO等气体,这些气体聚积到一定体积,压力增加而从液体金属中析出,造成小滴飞溅。
大滴过渡时,如果熔滴在焊丝端头停留时间较长,加热温度很高,熔滴内部发生强烈的冶金反应或蒸发,同时猛烈地析出气体,使熔滴爆炸而生成飞溅。
另外,在大滴状过渡时,偶尔还能出现飞溅,因为熔滴从焊丝脱落进入电弧中,在熔滴上出现串联电弧,在电弧力的作用下,熔滴有时落入熔池,也可能被抛出熔池而形成飞溅。
(2)熔滴短路过渡时的飞溅:熔滴短路过渡时的飞溅形式很多。
飞溅总是发生在短路小桥破断的瞬时。
飞溅的大小决定于焊接条件,它常常在很大范围内改变。
产生飞溅的原因目前有两种看法,一种看法认为飞溅是由于短路小桥电爆炸的结果。
当熔滴与熔池接触时,熔滴成为焊丝与熔池的连接桥梁,所以称为液体小桥,并通过该小桥使电路短路。
短路之后电流逐渐增加,小桥处的液体金属在电磁收缩力的作用下急剧收缩,形成很细的缩颈。
焊接复习资料

焊接复习资料1.co2气体保护焊产生飞溅的原因是什么?产生飞溅的措施有哪些及后果?答:①由冶金反应引起飞溅co2=co+【o];②由极点电压产生飞溅,尤其是直流正接的时候,机械冲刷力大,产生飞溅。
③融滴短路时引起飞溅。
④非轴向颗粒过渡飞溅。
⑤焊接工艺参素选择不当引起的飞溅。
措施:①采用硅锰元素脱氧,降低焊丝的含碳量。
②采用直流反接法。
③调节短路电流的增长速度。
④保证喷嘴气流速度均匀。
⑤正确选择工艺参素。
⑥采用co2潜伏焊(I↑U↓)。
后果:①增加了焊丝及电能的消耗。
②飞溅金属溅到喷嘴内壁上产生气流不均保护效果差。
③飞溅金属伤害到非焊接工作表面影响质量。
④飞溅引起烫伤或火灾。
2.试述交流TIG直流分量产生的原因、后果及措施。
答:原因由于在交流焊接Pb、Mg及合金时,正半周电流大,作用时间大,用于焊接过程而在负半周电流小、作用时间短主要用于清除Al2O3杂质。
(阳极破碎作用)。
可以把电流看成2部分,一部分是真正的交流电,另一部分是产生的直流分量。
危害:①负半周作用时间t2太小,所以削弱了阴极破碎作用。
②使变压器铁芯发热损坏设备。
消除装置:①在焊接回路中串接直流电源(大小相等,方向相反)。
②在焊接回路中串接二极管和电阻。
③焊接回路中串联电容,起通交流阻直流作用。
3.氧——乙炔按混合比不同可分为几种火焰?它的性质及应用范围如何?答:中性焰碳化焰氧化焰中性焰氧气与乙炔的比例为1.1至1.2 火焰温度3050至3050 氧与乙炔充分燃烧,既无过剩氧,也无过剩的乙炔。
焰心明亮,轮廓清楚,内焰具有一定的还原性,适用于焊接、切割、低碳钢和中低合金钢碳化焰气与乙炔的比例小于1.1 火焰温度2700至3000 乙炔过剩,火焰中有游离的碳和氢,具有较强的还原作用,也有一定的渗碳作用碳化焰整过火焰比中性焰长,适用于焊高碳钢、铸铁、中高合金钢氧化焰气与乙炔的比例大于1.2 火焰温度3100至3300 火焰中有过量的氧,具有强烈的氧化性,整过火焰较短,内焰和外焰层次不错,适用于黄铜4.双弧产生的原因是什么?防止措施及后果?产生原因:由于喷嘴在冷却水的作用下,在电弧周围形成了冷气膜冷气膜的两大作用;①绝热作用保护喷嘴②绝缘作用保证产生一根弧柱,当冷却效果变差使喷嘴某处的冷气膜消失,则在该点会产生另一根电弧,这就是双弧现象措施:①正确使用喷嘴的结构参数②增大喷嘴的冷却效果③控制离子流量不能过大④调整喷嘴端面与工件表面的距离不能过大⑤控制电弧电流不能过大⑥保证乌极轴心线与孔道轴心线同轴后果:①使热量不集中能量分散②使焊接或切割的成型性变差③容易烧穿喷嘴④易发生触电事故⑤工件热影响区大1.钎焊是采用比(母材)熔点低的的金属材料作(钎料),将(焊件)和(钎料)加热至高于(钎料)熔点的温度利用(液态钎料)润湿母材,填充接头间隙并与母材相互扩散实现连接焊件的方法。
CO2气体保护焊产生飞溅的原因有哪些?

CO2气体保护焊产生飞溅的原因有哪些?在CO2气体保护焊中,大部分焊丝熔化金属可过渡到熔池,有一部分焊丝熔化金属飞向熔池之外,飞到熔池之外的金属称为飞溅。
特别是粗焊丝CO2气体保护焊大参数焊接时,飞溅更为严重,飞溅率可达百/分之20以上,这时就不可能进行正常焊接工作了。
飞溅是有害的,它不但降低焊接生产率,影响焊接质量,而且使劳动条件变差。
由于焊接参数的不同,CO2焊具有不同的熔滴过渡形式,从而导致不同性质的飞溅。
其中,可分为熔滴自由过渡时的飞溅和短路过渡时的飞溅。
(1)熔滴自由过渡时的飞溅熔滴自由过渡时的飞溅主要形式,在CO2气氛下,熔滴在斑/点压力的作用下上挠,易形成大滴状飞溅。
这种情况经常发生在较大电流焊接时,如用直径1.6mm焊丝、电流为300~350A,当电弧电压较高时就会产生。
如果再增加电流,将产生细颗粒过渡,这时飞溅减小,主要产生在熔滴与焊丝之间的缩颈处,该处的电流密度较大使金属过热而爆断,形成颗粒细小的飞溅。
在细颗粒过渡焊接过程中,可能由熔滴或熔池内抛出的小滴飞溅。
这是由于焊丝或工件清理不当或焊丝含碳量较高,在熔化金属内部大量生成CO等气体,这些气体聚积到一定体积,压力增加而从液体金属中析出,造成小滴飞溅。
大滴过渡时,如果熔滴在焊丝端头停留时间较长,加热温度很高,熔滴内部发生强烈的冶金反应或蒸发,同时猛烈地析出气体,使熔滴爆炸而生成飞溅。
另外,在大滴状过渡时,偶尔还能出现飞溅,因为熔滴从焊丝脱落进入电弧中,在熔滴上出现串联电弧,在电弧力的作用下,熔滴有时落入熔池,也可能被抛出熔池而形成飞溅。
(2)熔滴短路过渡时的飞溅短路过渡时的飞溅形式很多。
飞溅总是发生在短路小桥破断的瞬时。
飞溅的大小决定于焊接条件,它常常在很大范围内改变。
产生飞溅的原因目前有两种看法,一种看法认为飞溅是由于短路小桥电爆炸的结果。
当熔滴与熔池接触时,熔滴成为焊丝与熔池的连接桥梁,所以称为液体小桥,并通过该小桥使电路短路。
浅谈碳钢产品焊接飞溅的防治措施

工程技术·157·一、前言目前,我司碳钢产品的焊接主要采用Panasonic KRⅡ350焊机80%Ar+20%CO2的气体保护焊,我们知道,这种焊接工艺所产生的焊接飞溅非常多(如图1所示)。
随着人工成本的不断增高,焊接产生的焊接飞溅成为了我们降低焊接成本的关键阻碍因素,焊接飞溅它难于清理,费时费力,影响生产效率,对产品质量也造成了不利影响。
针对碳钢焊接的焊接飞溅问题,我司成立了项目组进行专项攻关,从焊接工艺和焊接设备两方面着手分析,通过理论分析和相关的焊接工艺试验验证,确保获得焊接低飞溅效果和满意的焊缝质量。
图1 焊接飞溅照片二、焊接飞溅产生的原因分析(一)焊接工艺原因通过理论分析和多年的现场实践经验可知,碳钢焊接时,在同样的焊机和保护气体条件下,焊接工艺参数、焊枪角度等选择不当,容易产生大量的焊接飞溅。
1.焊接电流选择较大时,焊丝熔化时缩颈出现在熔池与熔滴之间,小桥爆炸力排斥熔滴过渡,形成大量飞溅,最高可使熔滴金属的25%以上形成焊接飞溅被抛出焊接熔池;2.焊枪倾角控制不好也会加大焊接飞溅,在计件工时情况下,焊工为了多出活,有意加快焊接速度,把焊枪倾角推得很大,这样会影响电弧的稳定性,造成焊接飞溅增大。
3.冷态引弧时或送丝速度过快而电弧电压过低,焊丝干伸长过大或焊接回路电感过大等常常发生固体短路,这时固体焊丝可以直接被抛出,同时熔池金属也被抛出,形成大颗粒飞溅。
(二)焊接设备原因碳钢焊接,焊机是产生焊接飞溅的主要因素,焊接设备的好坏,将直接影响焊接飞溅的多与少,一般来说,晶闸管交流焊机焊接飞溅大,逆变式数字脉冲焊机焊接飞溅少。
同时,焊机及其附件的保养,也将直接影响焊接飞溅的多与少,焊机及其附件保养得好,焊机始终处于最佳状态,焊接飞溅少,否则,焊接飞溅大。
1.焊接设备选型目前,市面上焊接碳钢的焊机品牌很多,如果焊机选用不当,焊接过程中,熔滴过渡形式为短路过渡,当熔滴与熔池接触时,熔滴成为焊丝与熔池的连接桥梁,称为液体小桥,并通过该小桥使电路短路,短路之后电流逐渐增加,小桥处的液体金属在电磁收缩力的作用下急剧收缩,形成很细的缩颈,随着电流的增加和缩颈的减小,小桥处的电流密度很快增加,对小桥急剧加热,造成过剩能量的积聚,最后导致小桥发生气化爆炸,引起金属飞溅[1-2](如图2所示)。
焊接飞溅

焊接飞溅产生的原因及克服途径在CO2焊中,大部分焊丝熔化金属可过渡到熔池,有一部分焊丝熔化金属飞向熔池之外,飞到熔池之外的金属称为飞溅。
特别是粗焊丝CO2气体保护焊大参数焊接时,飞溅更为严重,飞溅率可达20%以上,这时就不可能进行正常焊接工作了。
飞溅是有害的,它不但降低焊接生产率,影响焊接质量,而且使劳动条件变差。
由于焊接参数的不同,CO2焊具有不同的熔滴过渡形式,从而导致不同性质的飞溅。
其中,可分为熔滴自由过渡时的飞溅和短路过渡时的飞溅。
(1)熔滴自由过渡时的飞溅熔滴自由过渡时的飞溅主要形式,在CO2气氛下,熔滴在斑点压力的作用下上挠,易形成大滴状飞溅。
这种情况经常发生在较大电流焊接时,如用直径1.6mm焊丝、电流为300~350A,当电弧电压较高时就会产生。
如果再增加电流,将产生细颗粒过渡,这时飞溅减小,主要产生在熔滴与焊丝之间的缩颈处,该处的电流密度较大使金属过热而爆断,形成颗粒细小的飞溅。
在细颗粒过渡焊接过程中,可能由熔滴或熔池内抛出的小滴飞溅。
这是由于焊丝或工件清理不当或焊丝含碳量较高,在熔化金属内部大量生成CO等气体,这些气体聚积到一定体积,压力增加而从液体金属中析出,造成小滴飞溅。
大滴过渡时,如果熔滴在焊丝端头停留时间较长,加热温度很高,熔滴内部发生强烈的冶金反应或蒸发,同时猛烈地析出气体,使熔滴爆炸而生成飞溅。
另外,在大滴状过渡时,偶尔还能出现飞溅,因为熔滴从焊丝脱落进入电弧中,在熔滴上出现串联电弧,在电弧力的作用下,熔滴有时落入熔池,也可能被抛出熔池而形成飞溅。
(2)熔滴短路过渡时的飞溅短路过渡时的飞溅形式很多。
飞溅总是发生在短路小桥破断的瞬时。
飞溅的大小决定于焊接条件,它常常在很大范围内改变。
产生飞溅的原因目前有两种看法,一种看法认为飞溅是由于短路小桥电爆炸的结果。
当熔滴与熔池接触时,熔滴成为焊丝与熔池的连接桥梁,所以称为液体小桥,并通过该小桥使电路短路。
短路之后电流逐渐增加,小桥处的液体金属在电磁收缩力的作用下急剧收缩,形成很细的缩颈。
二氧化碳气体保护焊怎么让飞溅减少!

二氧化碳气体保护焊怎么让飞溅减少!
二氧化碳气体保护焊最大的缺点就是飞溅多,想要用调解参数来减少飞溅也是可以的,比如平面焊接薄板,焊丝直径在1.0-1.2时,电流控制在150A左右飞溅较少,因为电流小,只适合焊接薄板,同时在焊接过程中焊丝要跟焊缝离的进一些,让飞溅留在焊枪护嘴上,焊丝离的越远飞溅就会越多。
而且飞溅粘在铁板上难以清除。
同时呢要注意焊枪的角度,二氧化碳气体保护焊焊接时应于焊缝垂直,不要过于倾斜,倾斜角度越大,飞溅也会越多。
要想永久的制止飞溅也是有办法的,把实心的焊丝换成药心焊丝,不仅没有飞溅物,焊接出来的焊道还美观漂亮,一举两得,只是成本要贵一点。
- 1、下载文档前请自行甄别文档内容的完整性,平台不提供额外的编辑、内容补充、找答案等附加服务。
- 2、"仅部分预览"的文档,不可在线预览部分如存在完整性等问题,可反馈申请退款(可完整预览的文档不适用该条件!)。
- 3、如文档侵犯您的权益,请联系客服反馈,我们会尽快为您处理(人工客服工作时间:9:00-18:30)。
气体保护焊CO2焊接飞溅大的原因分析
在CO2焊中,大部分焊丝熔化金属可过渡到熔池,有一部分焊丝熔化金属飞向熔池之外,飞到熔池之外的金属称为飞溅。
特别是粗焊丝CO2气体保护焊大参数焊接时,飞溅更为严重,飞溅率可达20%以上,这时就不可能进行正常焊接工作了。
飞溅是有害的,它不但降低焊接生产率,影响焊接质量,而且使劳动条件变差。
由于焊接参数的不同,CO2焊具有不同的熔滴过渡形式,从而导致不同性质的飞溅。
其中,可分为熔滴自由过渡时的飞溅和短路过渡时的飞溅。
(1)熔滴自由过渡时的飞溅熔滴自由过渡时的飞溅主要形式,在CO2气氛下,熔滴在斑点压力的作用下上挠,易形成大滴状飞溅。
这种情况经常发生在较大电流焊接时,如用直径1.6mm焊丝、电流为300~350A,当电弧电压较高时就会产生。
如果再增加电流,将产生细颗粒过渡,这时飞溅减小,主要产生在熔滴与焊丝之间的缩颈处,该处的电流密度较大使金属过热而爆断,形成颗粒细小的飞溅。
在细颗粒过渡焊接过程中,可能由熔滴或熔池内抛出的小滴飞溅。
这是由于焊丝或工件清理不当或焊丝含碳量较高,在熔化金属内部大量生成CO等气体,这些气体聚积到一定体积,压力增加而从液体金属中析出,造成小滴飞溅。
大滴过渡时,如果熔滴在焊丝端头停留时间较长,加热温度很高,熔滴内部发生强烈的冶金反应或蒸发,同时猛烈地析出气体,使熔滴爆炸而生成飞溅。
另外,在大滴状过渡时,偶尔还能出现飞溅,因为熔滴从焊丝脱落进入电弧中,在熔滴上出现串联电弧,在电弧力的作用下,熔滴有时落入熔池,也可能被抛出熔池而形成飞溅。
(2)熔滴短路过渡时的飞溅短路过渡时的飞溅形式很多。
飞溅总是发生在短路小桥破断的瞬时。
飞溅的大小决定于焊接条件,它常常在很大范围内改变。
产生飞溅的原因目前有两种看法,一种看法认为飞溅是由于短路小桥电爆炸的结果。
当熔滴与熔池接触时,熔滴成为焊丝与熔池的连接桥梁,所以称为液体小桥,并通过该小桥使电路短路。
短路之后电流逐渐增加,小桥处的液体金属在电磁收缩力的作用下急剧收缩,形成很细的缩颈。
随着电流的增加和缩颈的减小,小桥处的电流密度很快增加,对小桥急剧加热,造成过剩能量的积聚,最后导致小桥发生气化爆炸,同时引起金属飞溅。
另一种看法认为短路飞溅是因为小桥爆断后,重新引燃电弧时,由于CO2气体被加热引起气体分解和体积膨胀,而产生强烈的气动冲击作用,该力作用在熔池和焊丝端头的熔滴上,它们在气动冲击作用下被抛出而产生飞溅。
试验表明,前一种看法比较正确。
飞溅多少与电爆炸能量有关,此能量主要是在小桥完全破坏之前的100~150μs时间内积聚起来的,主要是由这时的短路电流(即短路峰值电流)和小桥直径所决定。
小电流时,飞溅率通常在5%以下。
限制短路峰值电流为最佳值时,飞溅率可降低到1%左右。
在电流较大时,缩颈的位置对飞溅影响极大。
所谓缩颈的位置是指缩颈出现在焊丝与熔滴之间,还是出现在熔池与熔滴之间。
如果是前者,小桥的爆炸力推动熔滴向熔池过渡,而后者正相反,小桥爆炸力排斥熔滴过渡,并形成大量飞溅,最高可达25%以上。
冷态引弧时或在焊接参数不合适的情况下(如送丝速度过快而电弧电压过低,焊丝伸出长度过大或焊接回路电感过大等)常常发生固体短路。
这时固体焊丝可以直接被抛出,同时熔池金属也被抛出。
在大电流射滴过渡时,偶尔发生短路,由于短路电流很大。
所以将引起十分强烈的飞溅。
根据不同熔滴过渡形式下飞溅的不同成因,应采用不同的降低飞溅的不同成因,应采用不同的降低飞溅的方法:
1)在熔滴自由过渡时,应选择合理的焊接电流与焊接电压参数,避免使用大滴排斥过渡形式;同时,应选用优质焊接材料,如选用含C量低、具有脱氧元素Mn和Si的焊丝H08Mn2SiA等,避免由于焊接材料的冶金反应导致气体析出或膨胀引起的飞溅。
2)在短路过渡时,可以采用(Ar+CO2)混合气体代替CO2以减少飞溅。
如加入φ(Ar)=20%~30%的Ar。
这是由于随着含氩量的增加,电弧形态和熔滴过渡特点发生了改变。
燃弧时电弧的弧根扩展,熔滴的轴向性增强。
这一方面使得熔滴容易与熔池会合,短路小桥出现在焊丝和熔池之间。
另一方面熔滴在轴向力的作用下,得到较均匀的短路过渡过程,短路峰值电流也不太高,有利于减少飞溅率。
在纯CO2气氛下,通常通过焊接电流波形控制法,降低短路初期电流以及短路小桥破断瞬间的电流,减少小桥电爆炸能量,达到降低飞溅的目的。
通过改进送丝系统,采用脉冲送丝代替常规的等速送丝,使熔滴在脉动送进的情况下与熔池发生短路,使短路过渡频率与脉动送丝的频率基本一致,每个短路周期的电参数的重复性好,短路峰值电流也均匀一致,其数值也不高,从而降低了飞溅。
如果在脉动送丝的基础上,再配合电流波形控制,其效果更佳。
采用不同控制方法时,焊接飞溅率与焊接电流之间的关系。