某机械厂年度生产计划的编制
生产计划与控制 课程设计

目录1 课程设计任务书 (1)1.1 设计题目 (1)1.2 设计任务 (1)1.3 设计要求 (1)1.4 设计具体内容 (1)1.5 原始数据 (1)2 综合生产计划的编制 (4)2.1 综合生产计划概述 (4)2.2某机械厂2015年度策略分析 (4)2.3 综合生产计划的决策 (9)3 设备组生产能力的测定 (10)3.1 生产能力概述 (10)3.2 生产能力测定(计算)分析 (10)4 主生产计划的编制 (12)4.1 主生产计划概述 (12)4.2 主生产计划编制分析 (12)5 十张订单在单台机器作业排序 (14)5.1 作业排序概述 (14)5.2 作业排序规则 (14)5.3 十张订单作业分析 (14)1 课程设计任务书1.1 设计题目某机械厂2015年度生产计划及生产作业计划的编制1.2 设计任务(1)编制主流产品的综合生产计划与主生产计划(全年);(2)编制机加工车间甲、乙、丙三种主要产品(零件)的生产作业计划。
1.3 设计要求根据所提供的材料,按设计任务要求进行分析、计算和设计,并在2周内独立完成1份完整的课程设计报告。
1.4 设计具体内容(1)编制综合生产计划,运用三种策略进行分析比较,选择最优方案。
2、计算设备组的生产能力;3、编制主生产计划。
4、计算1-3月每周的现有库存和待分配库存;5、十张订单在单台机器作业顺序的安排1.5 原始数据1、该公司主要产品主流型机械的有关资料:⑴该产品2015年度各月出产计划预测量(见表1);⑵该产品的投入批量为600,期初库存为400,设备组车床数15台2、机加工车间主要产品甲、乙、丙、丁四种零件的有关资料:⑴四种零件结构、工业和劳动量构成差别较大,月产量分别为200,300,400和100件。
⑵四种零件在主要工序的加工时间见(表2);⑶每月工作天数见表1,每月份后面括号内为实际工作天数。
3、其他相关数据(1)有关于成本的数据见表3(2)关于订货量的预测,见表4。
生产计划编制

生产计划编制生产计划是企业生产经营活动的重要组成部分,它直接关系到企业的生产能力和生产效率。
一个科学合理的生产计划能够有效地调配企业的生产资源,提高生产效率,降低生产成本,提高产品质量,满足市场需求,从而实现企业的可持续发展。
因此,生产计划的编制显得尤为重要。
首先,生产计划的编制需要全面了解企业的生产能力和市场需求。
企业需要对自身的生产设备、技术水平、人力资源等方面进行全面的评估,明确自己的生产能力和生产条件。
同时,还需要对市场需求进行调研,了解市场对产品的需求量和需求趋势,从而为生产计划的编制提供依据。
其次,根据企业的生产能力和市场需求,制定合理的生产计划。
生产计划需要根据市场需求量和生产能力来确定生产任务量和生产周期,合理安排生产计划,确保生产任务的完成。
在制定生产计划时,还需要考虑到季节性因素、市场竞争状况等外部因素,灵活调整生产计划,确保生产计划的有效性和可行性。
然后,生产计划的执行是生产计划编制的重要环节。
企业需要根据生产计划,合理安排生产流程,科学调配生产资源,确保生产过程的顺利进行。
在生产过程中,还需要不断监控生产进度和产品质量,及时调整生产计划,确保生产任务的完成和产品质量的稳定。
最后,生产计划的评估和调整是生产计划编制的必要环节。
企业需要对生产计划的执行情况进行全面评估,分析生产过程中存在的问题和不足,及时调整生产计划,完善生产流程,提高生产效率和产品质量。
同时,还需要根据市场需求和企业发展情况,灵活调整生产计划,确保生产计划与市场需求和企业发展相适应。
综上所述,生产计划的编制是企业生产经营活动中的重要环节,它直接关系到企业的生产能力和生产效率。
一个科学合理的生产计划能够有效地调配企业的生产资源,提高生产效率,降低生产成本,提高产品质量,满足市场需求,从而实现企业的可持续发展。
因此,企业需要重视生产计划的编制,不断完善和改进生产计划,确保企业的生产经营活动顺利进行。
3.1 主生产计划编制

第三章生产管理一、生产管理概述生产是一个过程,将一些输入转换成商品或服务。
在现代工业企业中,生产是企业最基本、最重要的一项活动,困此生产管理也就显得尤为重要,它直接关系到企业经营的成败和对社会提供产品的数量和质量。
生产管理一般来说是指企业对生产活动的计划、组织和控制工作。
具体工作包括产品结构设计及产品工艺设计、生产过程组织、生产能力审核,生产计划与生产作业计划编制及执行、生产调度和产品质量管理等。
企业的生产管理工作由生产计划部门、技术部门、生产车间等部门完成。
生产管理在业务上与销售部门、采购部门、仓库部门、质量部门、设备管理部门以及财务部门都有着密切联系。
编制MPS所需要的产量数据由销售合同和销售预测提供,编制MRP所需要的物料供应和库存数据由采购和仓库部门提供,编制能力需求计划所需要的设备状况数据由设备管理部门提供,车间生产用料凭领料单从仓库中领取,生产出的产品和半成品进入仓库暂存;生产过程中的质量检验和产品入库前的检验由质量部门负责,并根据检验结果给出检验单;生产过程中的所有产品用料情况、加工情况、加工工时情况、废品情况及各种费用发生情况都要详细统计并上报给财务部门进行产品成本核算。
二、生产管理工作的具体内容1、生产数据准备新产品在投入生产前由工程技术部门绘制产品装配图纸、编制零件明细表、制定工艺规程、制定工艺方案、设计制造工艺装备、此外还要评定设备的能力及维护设备正常运转、建立完整、统一的工程数据,这是今后编制各种生产计划,保证生产按计划进行的前提。
生产数据主要包括:物料清单(产品结构)、工作中心、工艺路线和物品文件。
2、主生产计划(MPS)编制生产计划部门根据客户合同和预测,把生产规划中确定的产品大纲或产品系列进一步具体化,使之成为展开物料需求计划和能力需求计划的主要依据,主生产计划说明了在什么时间生产出某种产品的数量。
3、物料需求计划编制物料需求计划是对生产MPS项目的所需的全部制造件和采购件的网络支持计划,它是按时间段的进度计划。
机械加工年度工作计划
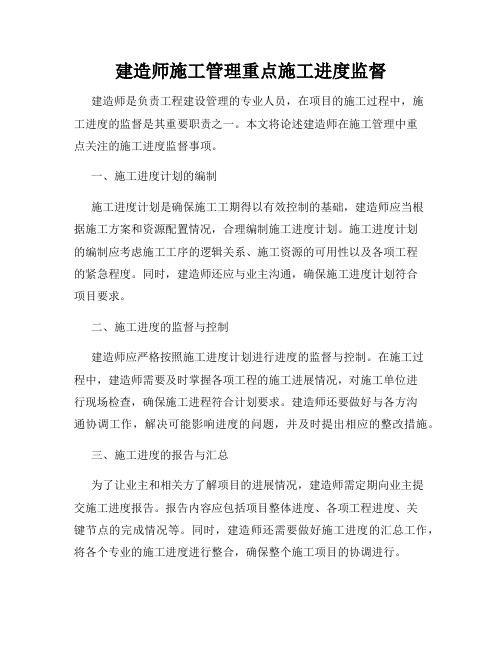
建造师施工管理重点施工进度监督建造师是负责工程建设管理的专业人员,在项目的施工过程中,施工进度的监督是其重要职责之一。
本文将论述建造师在施工管理中重点关注的施工进度监督事项。
一、施工进度计划的编制施工进度计划是确保施工工期得以有效控制的基础,建造师应当根据施工方案和资源配置情况,合理编制施工进度计划。
施工进度计划的编制应考虑施工工序的逻辑关系、施工资源的可用性以及各项工程的紧急程度。
同时,建造师还应与业主沟通,确保施工进度计划符合项目要求。
二、施工进度的监督与控制建造师应严格按照施工进度计划进行进度的监督与控制。
在施工过程中,建造师需要及时掌握各项工程的施工进展情况,对施工单位进行现场检查,确保施工进程符合计划要求。
建造师还要做好与各方沟通协调工作,解决可能影响进度的问题,并及时提出相应的整改措施。
三、施工进度的报告与汇总为了让业主和相关方了解项目的进展情况,建造师需定期向业主提交施工进度报告。
报告内容应包括项目整体进度、各项工程进度、关键节点的完成情况等。
同时,建造师还需要做好施工进度的汇总工作,将各个专业的施工进度进行整合,确保整个施工项目的协调进行。
四、施工进度与质量的协调施工进度与施工质量密切相关,建造师需要在施工过程中协调进度与质量的关系。
一方面,建造师应确保项目按时交付,避免进度拖延导致的额外成本和损失;另一方面,建造师还需确保施工质量符合相关标准,避免施工进度过快而导致质量问题。
五、施工进度的变更管理在实际施工中,可能会出现一些突发情况,导致原有施工进度计划无法继续执行。
这时,建造师需及时进行变更管理,对施工进度计划进行调整。
建造师需要与施工单位协商,制定新的施工进度计划,并及时报备给业主和相关方。
综上所述,建造师在施工管理中的重点之一是施工进度的监督。
通过合理编制施工进度计划,严格监督施工进度,并与各方保持良好的沟通协调,建造师可以有效控制施工进度,确保施工工期的顺利进行。
同时,建造师还需注重施工进度与质量的协调,及时处理进度变更事项。
2024年某机械有限公司安全生产责任制(2篇)

2024年某机械有限公司安全生产责任制一、概述随着社会经济的发展,安全生产已成为企业发展的重要组成部分。
为了确保员工的生命安全和财产安全,保障企业的可持续发展,某机械有限公司决定制定并实施安全生产责任制。
二、总体目标某机械有限公司的总体目标是实现“安全第一、预防为主、综合治理”的安全生产方针。
通过建立完善的安全生产责任制,提高员工的安全意识和能力,确保生产过程中没有事故发生,降低事故发生的概率和损失。
三、安全生产责任制的主体和内容1. 企业领导层企业领导层是安全生产责任制的核心,在安全方面应负有最终责任。
企业领导层应制定并完善安全生产政策和制度,并确保其执行。
他们应为安全生产提供必要的资源和支持,加强对安全生产工作的监督和检查,及时发现和解决安全风险。
2. 安全生产责任人企业应选派专门的安全生产责任人,负责组织实施安全生产责任制。
责任人应具备相应的安全管理专业知识和技能,并组织开展安全培训和演练。
他们应协调各部门的安全工作,及时处理和报告安全事故,并提出安全改进措施。
3. 部门主管各部门主管是企业安全生产责任制的重要组成部分。
他们应确保本部门的安全生产工作落实到位,切实负起安全责任。
部门主管应为员工提供安全培训和指导,确保员工掌握必要的安全知识和技能。
他们还应协助安全生产责任人,制定安全生产计划和措施。
4. 全体员工每位员工都应严格遵守公司的安全生产规章制度,履行安全生产责任。
员工应积极参与安全培训和演练,提高自身的安全意识和能力。
在工作过程中,员工应发现并及时报告存在的安全隐患,积极参与安全改进活动。
四、安全生产责任制的实施步骤1. 制定安全生产责任制的工作计划企业应制定一份详细的工作计划,明确责任制的实施步骤和时间节点,并明确责任人和相关部门的任务和职责。
2. 完善安全管理制度和流程企业应依据国家相关法律法规和标准,制定并完善安全管理制度和流程。
安全管理制度和流程应涵盖企业内各个环节和层级,确保员工的生产行为符合安全标准。
年度生产计划
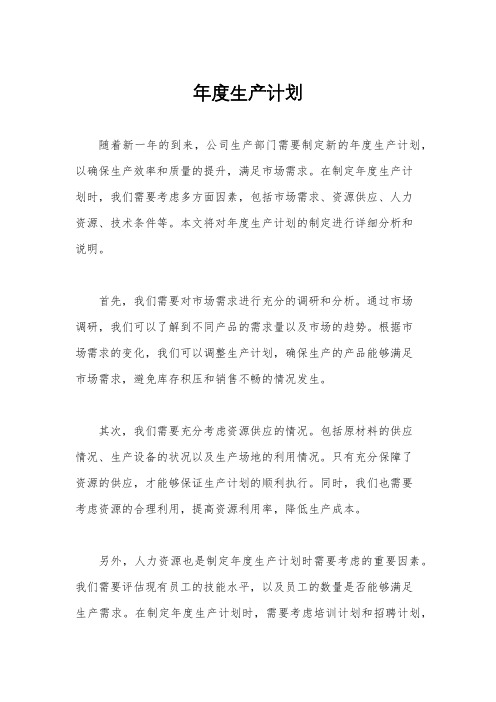
年度生产计划随着新一年的到来,公司生产部门需要制定新的年度生产计划,以确保生产效率和质量的提升,满足市场需求。
在制定年度生产计划时,我们需要考虑多方面因素,包括市场需求、资源供应、人力资源、技术条件等。
本文将对年度生产计划的制定进行详细分析和说明。
首先,我们需要对市场需求进行充分的调研和分析。
通过市场调研,我们可以了解到不同产品的需求量以及市场的趋势。
根据市场需求的变化,我们可以调整生产计划,确保生产的产品能够满足市场需求,避免库存积压和销售不畅的情况发生。
其次,我们需要充分考虑资源供应的情况。
包括原材料的供应情况、生产设备的状况以及生产场地的利用情况。
只有充分保障了资源的供应,才能够保证生产计划的顺利执行。
同时,我们也需要考虑资源的合理利用,提高资源利用率,降低生产成本。
另外,人力资源也是制定年度生产计划时需要考虑的重要因素。
我们需要评估现有员工的技能水平,以及员工的数量是否能够满足生产需求。
在制定年度生产计划时,需要考虑培训计划和招聘计划,确保公司拥有足够的人力资源来支撑生产计划的实施。
除此之外,技术条件也是制定年度生产计划的重要考虑因素。
我们需要评估现有的生产技术水平,是否能够满足新产品的生产需求。
同时,我们也需要考虑技术的更新换代,引进新的生产技术,提高生产效率和产品质量。
综上所述,制定年度生产计划是一个综合考虑多方面因素的过程。
只有充分考虑市场需求、资源供应、人力资源和技术条件,才能够制定出科学合理的年度生产计划,确保公司的生产效率和产品质量得到提升,满足市场需求。
希望全体员工能够共同努力,为公司的年度生产计划的实施贡献自己的力量。
机械厂生产计划

机械厂生产计划
机械厂要生产东西了,那首先得知道要生产多少,什么时候生产完,对吧?这就是需求分析。
然后,得看看咱工厂有多少能力,能不能完成这么多生产任务,这就是产能评估。
接下来,咱们就可以开始制定生产计划了。
比如先确定一下要生产多少,什么时候交货。
然后想想生产流程是怎么样的,需要哪些机器、工人和材料。
在生产过程中,咱们得时刻盯着进度,看看生产是不是按计划来的,如果不对劲,就得赶紧调整。
产品质量也很重要,得确保每个产品都合格。
所以还得做质量控制,检查原材料和成品的质量。
最后,产品得按时送到客户那里。
这就是物流和交货的部分。
不过,机械厂的生产计划还可能受到一些其他因素的影响,比如供应链稳不稳定、原材料价格变没变、政策法规变没变等等。
所以,在制定生产计划的时候,得把这些因素都考虑进去,才能做得更好。
总之,机械厂的生产计划就是这么回事,得综合考虑各种因素,才能确保生产顺利进行。
工厂车间年度计划

工厂车间年度计划
一、总体目标
本年度工厂车间总产值完成万元,同比增长5%。
所有产品质量合格率达到99%以上。
二、主要产品计划
1. 产品:本年度产量台,其中新产品1产量台。
2. 产品:本年度产量台。
3. 产品:本年度产量件。
三、生产任务分配
1. 一车间:主导产品的生产,产量完成率不低于95%。
2. 二车间:主导产品的生产,产量完成率不低于97%。
3. 三车间:主导产品的生产,产量完成率不低于98%。
四、质量目标
1. 各单项产品质量目标都是99%以上。
2. 严格把控质量问题,每月不超过3项质量问题。
3. 加强技能培训和技术交流,提高工作效率。
五、安全生产
1. 全年无重大安全生产事故。
2. 开展安全生产月活动3期。
3. 每季度检查所有设备和操作,杜绝隐患。
本计划旨在划定明年车间的生产任务和质量安全目标,希望全体同仁携手共同完成。
- 1、下载文档前请自行甄别文档内容的完整性,平台不提供额外的编辑、内容补充、找答案等附加服务。
- 2、"仅部分预览"的文档,不可在线预览部分如存在完整性等问题,可反馈申请退款(可完整预览的文档不适用该条件!)。
- 3、如文档侵犯您的权益,请联系客服反馈,我们会尽快为您处理(人工客服工作时间:9:00-18:30)。
目录1 课程设计任务书 (1)1.1 设计题目 (1)1.2 设计任务 (1)1.3 设计要求 (1)1.4 设计具体内容 (1)1.5 原始数据 (1)2 综合生产计划的编制 (4)2.1 综合生产计划概述 (4)2.2某机械厂2018年度策略分析 (4)2.3 综合生产计划的决策 (8)2.4 综合生产计划的编制 (8)3 设备组生产能力的测定 (12)3.1 生产能力概述 (12)3.2 生产能力测定(计算)分析 (12)4 主生产计划的编制 (14)4.1 主生产计划概述 (14)4.2 主生产计划编制分析 (14)5 十张订单在单台机器作业排序 (18)5.1 作业排序概述 (18)5.2 作业排序规则 (18)5.3 十张订单作业分析 (18)1 课程设计任务书1.1 设计题目某机械厂2018年度生产计划及生产作业计划的编制1.2 设计任务1、编制主流产品的综合生产计划与主生产计划(全年);2、编制机加工车间甲、乙、丙三种主要产品(零件)的生产作业排序。
1.3 设计要求根据所提供的材料,按设计任务要求进行分析、计算和设计,并在2周内独立完成1份完整的课程设计报告。
1.4 设计具体内容1、编制综合生产计划,运用三种策略进行分析比较,选择最优方案;2、计算设备组的生产能力;3、编制主生产计划;4、计算1-12月每周的现有库存;5、十张订单在单台机器作业顺序的安排。
1.5 原始数据1、该公司主要产品主流型机械的有关资料:⑴该产品2018年度各月出产计划见表1。
⑵该产品的投入批量为600,期初库存为400,设备组车床数15台。
2、机加工车间主要产品甲、乙、丙、丁四种零件的有关资料:⑴四种零件结构、工业和劳动量构成差别较大,月产量分别为200,300,400和100件。
⑵四种零件在主要工序的加工时间见表2。
⑶每月工作天数见表1,每月份后面括号内为实际工作天数。
3、其他相关数据⑴有关于成本的数据见表3。
⑵关于订货量的预测,见表4。
⑶十张订单情况见表5。
表1 主流型产品2018年度各月出产计划表2 主要零件在车削工序上的加工时间表3 相关数据表5 十张订单加工情况2 综合生产计划的编制2.1 综合生产计划概述1、综合生产计划的概念综合生产计划也称生产大纲、年度生产计划或年度生产大纲。
综合生产计划是企业根据市场预测和企业所拥有的生产资源,对企业计划期内生产的产品、产量以及为保证生产所需的劳动力水平、库存等措施的决策性描述。
正常的制定总和生产计划指标,既可以满足社会和用户需求,又能充分发挥企业的人力、物力和财力,还可以在提高劳动生产率和降低成本的基础上增加利润。
2、综合生产计划编制步骤⑴确定计划期生产产品的市场需求;⑵分析外部约束条件和企业内部的生产条件;⑶拟定生产指标方案,方案优化;⑷综合平衡,编制计划草案;⑸审核批准综合生产计划。
2.2某机械厂2018年度策略分析1、综合生产计划编制策略3种策略的特点:追逐策略:通过调整员工的数量来达到满足生产要求,以适应变化的生产需求。
平准策略:保持工人数量不变,将超出能力之外的工作外包出去,以满足最小需求预测。
外包策略:通过改变库存量、订单积压和减少销售来消化缺货与剩余产品,保持稳定的劳动力数量和产品的生产量。
2、三种编制方案的分析(2-1)式中:——每月实际需求量;——每月需求预测量;——每月初期需求量;——每月安全库存量;每月的期末库存公式为:(2-2)式中:——每月月末库存量;——每月实际需求量;——每月初期需求量;——每月需求预测量;通过上述公式得出表6:表6每月的实际需求量与库存量表期初库存量400 235 240 210 220 225 230 210 215 240 200 205 需求预测量940 960 840 880 900 920 840 860 960 800 820 1000 安全库存量235 240 210 220 225 230 210 215 240 200 205 250 实际需求量755 965 810 890 905 925 820 865 985 760 825 1045 期末库存量235 240 210 220 225 230 210 215 240 200 205 250 策略一:追逐策略,即满足需求量变化,以改变工人数调节生产能力,假设每班次工作8h。
安全库存量=需求预测量×25%每人月工时=月工作天数×8h满足需求所需时间=实际需求量×5小时/件所需人数=满足需求所需生产时间/每人月工时招聘成本=新招收的人员×200元/人解聘成本=解聘人员×300元/人自制材料成本=实际需求量×100元/每件库存总成本=期末库存量×2元/件正常人工总成本=满足需求所需时间×4元/小时通过上述公式得出表7:表7 追逐策略成本分析表月份 1 2 3 4 5 6 7 8 9 10 11 12 实际需求量755 965 810 890 905 925 820 865 985 760 825 1045 满足需求所需时间3875 4825 4050 4450 4525 4625 4100 4325 4925 3800 4125 5225 每月工作天数22 18 23 23 20 22 22 21 21 20 23 23 每人每月工时176 144 184 184 160 176 176 168 168 160 184 184 所需人数23 35 23 25 29 27 24 26 30 24 23 29 招聘人数0 12 0 2 0 2 0 2 4 0 0 6 招聘成本0 2400 0 400 0 400 0 400 800 0 0 1200续表月份 1 2 3 4 5 6 7 8 9 10 11 12 解聘人数0 0 12 0 0 0 3 0 0 6 1 0 解聘成本0 0 3600 0 0 0 900 0 0 1800 300 0 材料成本755009650081000 89000 90500 92500 82000 86500 98500 76000 82500 104500 库存成本470 480 420 440 450 460 420 430 480 400 410 500 正常人工成本15500 19300 16200 17800 18100 18500 16400 17300 19700 15200 16500 20900 总成本1283960由表7得出,招聘成本为5600元,解聘成本为6600元,自制材料成本为1055000元,正常人工成本为211400元,总成本为1283960元。
策略二:平准策略,保持工人人数不变,变动库存,既不加班也不外包。
固定工人人数。
人数=[5h×总预测量]/[258天×8h]=[5h×10500(总预测量)]/[258天×8h]=26人可用生产时间=总人数×工作天数×工作时间安全库存量=需求预测值×25%月末库存量=实际生产量-需求预测量多余库存成本=多余库存量×2元/件自制材料成本=实际需求量×100元/件正常人工总成本=可用生产时间×4元/小时通过上述公式得到表8:表8 平准策略成本分析表月份 1 2 3 4 5 6 7 8 9 10 11 12 月初库存量400 375 164 281 358 290 285 360 374 287 319 456 月工作天数22 18 23 23 20 22 22 21 21 20 23 23 可用生产时间4576 3744 4784 4784 4160 4576 4576 4368 4368 4160 4784 4784 实际生产量915 749 957 957 832 915 915 874 874 832 957 957 需求预测量940 960 840 880 900 920 840 860 960 800 820 1000月末库存量375 164 281 358 290 285 360 374 287 319 456 413 缺货成本0 0 0 0 0 0 0 0 0 0 0 0 安全库存量235 240 210 220 225 230 210 215 240 200 205 250 多余库存量140 0 71 138 65 55 150 159 47 119 251 163 自制材料成本91500 74900 95700 95700 83200 91500 91500 87400 87400 83200 95700 95700 多余库存成本280 0 142 276 130 110 300 318 94 238 502 326 正常人工成本18304 14976 19136 19136 16640 18304 18304 17472 17472 16640 19136 19136 总成本1194797由表8得出,多余库存成本为2716元,自制材料成本为1073400元,正常人工成本为214656元,总成本为1194797元。
策略三:外包策略。
保持工人人数不变,将超出能力之外的工作外包出去,以满足最小需求预测。
人数=[5h×最小预测量×12个月]/[258天×8h]=[5h×800件(最小预测量) ×12个月]/[258天×8h]=23人可用生产时间=总人数×工作时间×工作天数实际生产量=可用生产时间/单位产品加工时间外包件数=需求预测值-实际生产量外包总成本=外包件数×20元/件自制材料成本=实际需求量×100元/件正常人工总成本=可用生产时间×4元/小时通过上市公式得出表9:表9 外包策略分析表月份 1 2 3 4 5 6 7 8 9 10 11 12 需求预测量940 960 840 880 900 920 840 860 960 800 820 1000 月工作天数22 18 23 23 20 22 22 21 21 20 23 23 可用生产时间4048 3312 4232 4232 3680 4048 4048 3864 3864 3680 4232 4232 实际生产量810 662 846 846 736 810 810 773 773 736 846 846 外包件数0 0 0 0 120 110 30 87 187 64 0 128 外包成本0 0 0 0 2400 2200 600 1740 3740 1280 0 2560 库存量2700 6 0 0 0 0 0 0 0 26 0 库存成本5400 12 0 0 0 0 0 0 0 52 0 自制材料成本81000 66200 84600 84600 73600 81000 81000 77300 77300 73600 84600 84600 正常人工成本1619213248 16928 16928 14720 16192 16192 15456 15456 14720 16928 16928 总成本1154988由表9得出,外包成本为14520元,库存成本为1180元,自制材料成本为864800元,正常人工成本为189888元,总成本为1154988元。