现场改善工具与案例
现场改善工具及案例分析
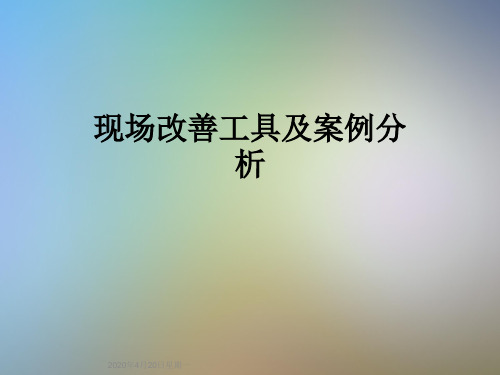
•浪费的种类:
•1、生产过剩
•4、搬运 •7、不良 品
•2、等待
•3、工序设计不当
•5、库存过高 •6、动作不当
•8、时间的浪费
•1、生产过剩
•资金积压 •质量劣化 •占用场地 •管理费用增加 •经营风险
•2、等待
•观察机器 •等待材料 •机器故障 •质量检验 •生产不均衡
•3、搬运
•厂区布置差 •材料放置地点不合理 •中间库存 •物流不畅 •管理混乱
•什么是改善
一种企业经营理念,用以持续不断地改进工作方法和人员的效率等
低成 本
全员 性
阶梯式
•改善意识
把现场作为实验室,日夜努力奋斗 不只是自己一个人,要让所有的下属参与到改善中 让下属参与到改善中,每天接受新的挑战,激发创造性 自身需要不断地从现场学习,并改善现场
•现场之屋
团队
•人
1) 取得高层领导的支持 2) 全体员工理解5S的内涵和重要性 3) 确立挑战性目标 4) 选取活动主题、重点项目 5) 设立5S推行组织 6) 熟悉5S推行技巧、手法 7) 建立评价体制 8) 建立激励机制 9) 活动持续不断 10)引用外力支援
• 5S从我做起 !
• 从现在做起 !
•5S活动铸造 •整洁的工厂、 •有规律的企业、 •高效的工厂。
•4S清洁
清洁:标准化
整理做好了 吗
整顿做好了 吗
清扫做好了 吗
不乱放 干净的工作场所
•5S素养
素养:持续改进
好的,我马上做
•三 现
•立
•彻
即
底
•三 态
•现场 •物品 •员工
•三爱
•公司推进事项
NO
推进事项
操作工现场改善计划方案

操作工现场改善计划方案一、改善目标。
让咱的工作现场变得更顺溜儿,就像给一辆老破车换上新零件,又快又稳,效率嗷嗷提高,错误啥的都躲得远远的,工作环境也变得舒服得像在自己家客厅一样自在。
二、现状分析。
# (一)工具摆放。
现在工具就像一群调皮的小鬼,到处乱窜,想用的时候找半天,急得人直跺脚。
有的工具放在老远的地方,每次拿都得跑个马拉松似的。
# (二)操作流程。
操作流程就像一团乱麻,有些步骤绕来绕去,让人晕头转向。
有时候不知道先干啥后干啥,就像在黑暗里摸瞎一样。
# (三)工作环境。
那环境啊,有时候乱得像被龙卷风席卷过。
物料堆得乱七八糟,地上也不干净,感觉就像在垃圾场里干活儿似的。
三、改善措施。
# (一)工具摆放改善。
1. 专属地盘。
给每个工具都划一块“小地盘”,就像给每个小伙伴分个小房间一样。
拿个木板或者小盒子,在上面写上工具的名字,然后把工具规规矩矩地放在里面。
这样一眼看过去,就知道谁在哪儿,再也不用翻箱倒柜地找了。
2. 近水楼台先得月。
按照使用频率来摆放工具。
那些经常要用的工具,就放在手边,伸手就能够着。
不常用的,就稍微放远一点,但也要保证能很快找到。
这就好比把常用的碗筷放在餐桌边,不常用的放在橱柜里。
# (二)操作流程改善。
1. 流程图绘制。
咱把操作流程像画画一样画出来。
从第一步开始,到最后一步结束,每一步都画得清清楚楚,就像给操作工们画了一张寻宝图。
把这个流程图贴在工作台上,谁要是迷糊了,看一眼就明白接下来该干啥了。
2. 简化与优化。
大家一起坐下来,像挑刺儿一样看看操作流程里有没有多余的步骤。
要是有,就像剪掉枯枝一样把它去掉。
然后再看看能不能把几个步骤合并起来,让整个流程像滑滑梯一样顺畅。
# (三)工作环境改善。
1. 物料整理。
给物料来个大集合,分类整理。
把相似的物料放在一起,就像把水果放在一个篮子里,蔬菜放在另一个篮子里。
再给每个物料堆做个小标签,写上是什么东西、有多少数量。
这样不仅看着整齐,而且拿取也方便。
现场改善工具及案例

提高生产效率:减少换模时间,提高生产速度 降低成本:减少换模次数,降低生产成本 提高产品质量:减少换模过程中的误差,提高产品质量 适应性强:适用于各种生产环境和产品类型
汇报人:
培训员工使用工具:定期对员工进行工具使用培训,提高员工使用工 具的能力
收集反馈意见:收集员工对工具使用的反馈意见,不断改进工具以 满足实际需求
明确目标:确定改善的目标和预期效果 选择合适的工具:根据实际情况选择合适的改善工具 培训员工:对员工进行培训,使他们了解改善工具的使用方法和注意事项 持续改进:不断收集反馈,对改善工具进行优化和调整,以实现持续改进
个领域
目视化管理可 以提高员工的 工作积极性和 参与度,增强 企业的凝聚力
和竞争力
目视化管理可 以提高企业的 透明度和公开 度,增强企业 的形象和信誉
作业标准化是现场改善的重要工具之一 作业标准化可以提高生产效率,降低成本 作业标准化可以提高产品质量,减少不良品 作业标准化可以提高员工技能,降低培训成本 作业标准化可以提高企业竞争力,增强企业实力 作业标准化在制造业、服务业等领域都有广泛的应用前景
快速换模的案例 :某汽车制造厂 通过快速换模, 提高了生产效率 ,降低了生产成 本
企业背景:某制 造企业,生ห้องสมุดไป่ตู้汽 车零部件
问题发现:生产 效率低下,质量 问题频发
改善措施:引入 现场改善工具, 如5S、TPM等
改善效果:生产 效率提高,质量 问题减少,员工 满意度提升
物流公司背景: 大型物流公司, 业务覆盖全国
5S管理将成为企业提高生产效率、 降低成本的重要手段
5S管理将更加注重员工参与和团 队合作
添加标题
添加标题
添加标题
添加标题
现场改善工具与案例!

JMfr.
*«**Nr#n
'Mas
o
4 M.
TPM|p]^ (3)
fugc^iasn^'Hi
-& P 11314^ .
) nuTTlx.
A*H)&
TPMI' p I® (4) 1 -------------------------------------- .
TPM ft
1 TPMft3BB3fe*
• P.... 5-2.0 ft* ^£^ift#$:l/1<M/250>
• Q.......
W$1/4 • C.... «MTTP£30%. • D....... 7* ft, ««&##«¥
• s.......
• M.... &#H3l#£fc5~1<tfg
• g±tsS«W«iz;, sp “g • wit a mmmm«»” »g« • 6'JitMS, 5Sft, *933(8 • £91 irW#®#MR»Wik «*, W&Jfcffiiaffi-HSzS
36
$£$=»
.
fit I*]
IB.
-O
.
®^75%~85%Wtt.
38
.
.
40
400/460=87%
0.5X400/400=50% (400-8) /400=98 %
.
87% X 50% X 98% =42.6%
3.x
+ , Stffi£5^4t^iiW jtutfiUMfc.
- Z-$riZ% .&&*## tetfl&te,
feniiWEt* ’naiumm
现场改善工具与案例

5、库存掩盖了问题
通过库存维持生产
降低库存暴露问题
缺勤 率高
计划 性差
质量 低劣
机器 故障
销售 问题
生产不均衡
换模 时间长
沟通 不佳
缺勤
质量
率高
低劣
计划
性差
机器 故障
销售 问题
生产不均衡
库存之海
换模 时间长
沟通 不佳
12
6、操作动作不合理
场地布置欠佳 料箱设计不合理 工艺设计不合理 人员安排不当 工具取用不方便
现场改善工具及案例
一 、现场改善基础
1
做好现场改善的四个要素
Comprehension
理解
Competence
能力
承诺
Commitment
持续
Continuance
2
什么是现场
当问题发生时,先去现场 检查现物 找到真正的原因并排除 标准化以防止再发生
现场就是产生 附加值或提供 服务的地方。
24
2S整顿
整顿:定物、定位、定量
• 更快地拿到和返还物品 • 物品放得很整齐,易清点 • 物品的库存更低,但不会短缺 • 空间布局是合理的 • 工作环境是安全的 • 不良品和良品是严格区分的
25
3S清扫
清扫:清扫就是点检
• 工作环境是明亮的 • 设备上无积灰和油污 • 地面、墙上没有灰尘、积水、油污 • 空气中没有浮尘、异味 • 工作台、办公桌、货架是干净的 • 物品是干净和很好保护的
29
克服消极因素的方法
易学、易懂、 易操作
进行团队活动
领导以 身作则
采取预防措 施,解决根 本问题
重视现场检 查,有错必 纠
现场改善工具与案例

强化品质管理,提高客户满意度
详细描述
某机械制造企业重视品质管理,通过建立完善的品质管理体系和检测流程,确保产品品质符合客户需 求。同时,加强与客户的沟通与反馈,及时解决客户问题和改进产品性能,提高客户满意度。通过持 续的品质提升,该企业在市场上获得了良好的口碑和竞争优势。
04
现场改善的未来发展
通过持续的现场改善,推动企 业不断创新和改进,提升企业
的竞争力和市场地位。
现场改善的步骤和原则
现场调查和分析
确定改善目标和方案
对生产现场进行全面调查,了解生产流程 、设备、工艺、材料、环境等方面的情况 ,发现问题和浪费现象。
根据调查和分析结果,确定改善的目标和 方案,包括优化流程、改进设备、调整工 艺参数等。
某电子制造企业的生产线优化
总结词
引入自动化和智能化设备,提高品质和效率
详细描述
某电子制造企业针对生产线存在的问题,引入了自动化和智能化设备。通过设备升级和工艺改进,减少了人工操 作和错误率,提高了产品品质和生产效率。同时,优化了生产线布局和管理模式,进一步提高了整体的生产效益。
某机械制造企业的品质提升案例
现场改善工具与案例
目录
• 现场改善概述 • 现场改善工具 • 现场改善案例 • 现场改善的未来发展 • 结论
01
现场改善概述
现场改善的定义
01
现场改善是指通过一系列的方法 和工具,对生产现场进行优化和 改进,以提高生产效率、降低成 本、提升产品质量的过程。
02
它涉及到对生产流程、设备、工 艺、材料、环境等方面的优化, 以及员工技能和意识的提升。
03
目视化管理能够及时发现异常情况,迅速采取措施解决问题。
现场改善及案例分析

改进效果:生 产效率提高, 产品质量得到 显著提升,降 低了生产成本。
总结:通过现 场改善,某公 司实现了生产 流程的优化, 提高了竞争力。
事故背景:简述事故发生的原因和经过 改善措施:针对事故原因采取的改善措施 实施效果:改善措施实施后的效果评估 案例总结:从案例中获得的经验和教训
Part Four
XX,a click to unlimited possibilities
汇报人:XX
01 02 03 04
05
Part One
减少浪费,降低成本 提升产品质量 增强企业竞争力 满足客户需求
减少浪费:通过 消除生产过程中 的浪费,降低生 产成本
提高效率:优化 生产流程,提高 生产效率,降低 生产成本
添加标题
评估改善成果的可持 续性需要从多个方面 进行考量,包括员工 技能、设备维护、管 理体系等方面,以确 保改善成果能够在长
期内得到维持。
添加标题
为了确保改善成果的 可持续性,需要建立 完善的跟踪机制,定 期对改善成果进行评 估和调整,及时发现 和解决可能出现的问
题。
添加标题
改善成果的可持续性 评估不仅有助于提高 生产效率和质量,还 有助于提升企业的竞 争力和盈利能力。因 此,应该充分重视这 一环节,确保改善成
目的:提高工作效率,降低安全风险,提升员工操作规范性。
实施方法:利用看板、标识、颜色等视觉手段进行管理,使信息传递更加准确、快捷。 案例分析:某企业通过实施目视化管理,提高了生产效率,降低了事故发生率,提升 了员工满意度。
定义:将作业流程、操作步骤、作业要求等标准化,形成统一规范 目的:提高作业效率、减少不良品、降低成本 步骤:分析现有作业流程,制定标准作业指导书,培训员工,监督执行 优势:便于管理、减少人为因素、快速复制成功经验
现场改善工具与案例..103页PPT
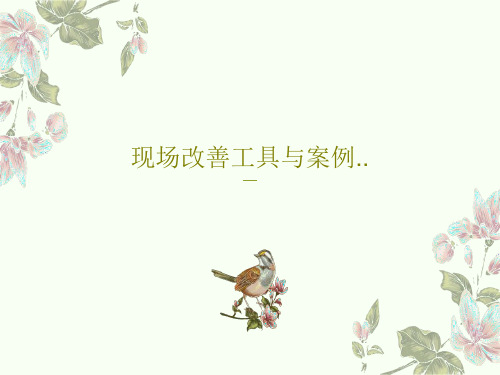
16、自己选择的路、跪着也要把它走 完。 17、一般情况下)不想三年以后的事, 只想现 在的事 。现在 有成就 ,以后 才能更 辉煌。
18、敢于向黑暗宣战的人,心里必须 充满光 明。 19、学习的关键--重复。
20、懦弱的人只会裹足不前,莽撞的 人只能 引为烧 身,只 有真正 勇敢的 人才能 所向披 靡。
xiexie! 38、我这个人走得很慢,但是我从不后退。——亚伯拉罕·林肯
39、勿问成功的秘诀为何,且尽全力做你应该做的事吧。——美华纳
40、学而不思则罔,思而不学则殆。道紧在哪里。——西班牙
37、我们唯一不会改正的缺点是软弱。——拉罗什福科