转炉炼钢原材料与铁水预处理
炼钢的过程
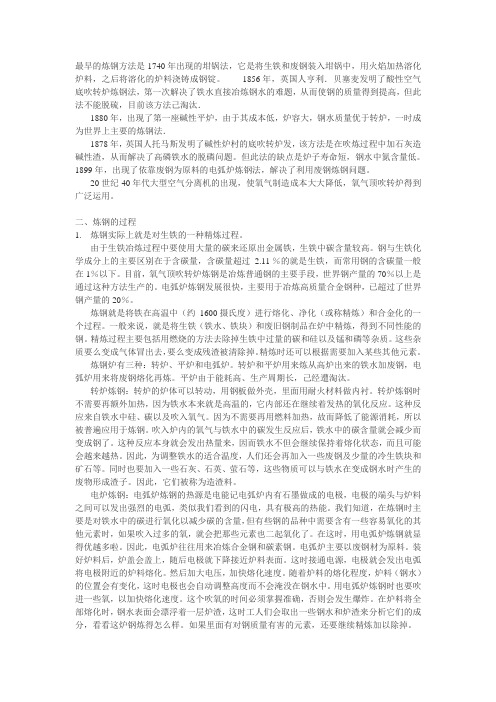
最早的炼钢方法是1740 年出现的坩锅法,它是将生铁和废钢装入坩锅中,用火焰加热溶化炉料,之后将溶化的炉料浇铸成钢锭。
1856 年,英国人亨利.贝塞麦发明了酸性空气底吹转炉炼钢法,第一次解决了铁水直接冶炼钢水的难题,从而使钢的质量得到提高,但此法不能脱硫,目前该方法己淘汰.1880 年,出现了第一座碱性平炉,由于其成本低,炉容大,钢水质量优于转炉,一时成为世界上主要的炼钢法.1878 年,英国人托马斯发明了碱性炉村的底吹转炉发,该方法是在吹炼过程中加石灰造碱性渣,从而解决了高磷铁水的脱磷问题。
但此法的缺点是炉子寿命短,钢水中氮含量低。
1899 年,出现了依靠废钢为原料的电弧炉炼钢法,解决了利用废钢炼钢问题。
20 世纪40 年代大型空气分离机的出现,使氧气制造成本大大降低,氧气顶吹转炉得到广泛运用。
二、炼钢的过程1.炼钢实际上就是对生铁的一种精炼过程。
由于生铁冶炼过程中要使用大量的碳来还原出金属铁,生铁中碳含量较高。
钢与生铁化学成分上的主要区别在于含碳量,含碳量超过 2.11 %的就是生铁,而常用钢的含碳量一般在1%以下。
目前,氧气顶吹转炉炼钢是冶炼普通钢的主要手段,世界钢产量的70%以上是通过这种方法生产的。
电弧炉炼钢发展很快,主要用于冶炼高质量合金钢种,已超过了世界钢产量的20%。
炼钢就是将铁在高温中(约1600 摄氏度)进行熔化、净化(或称精炼)和合金化的一个过程。
一般来说,就是将生铁(铁水、铁块)和废旧钢制品在炉中精炼,得到不同性能的钢。
精炼过程主要包括用燃烧的方法去除掉生铁中过量的碳和硅以及锰和磷等杂质。
这些杂质要么变成气体冒出去,要么变成残渣被清除掉。
精炼时还可以根据需要加入某些其他元素。
炼钢炉有三种:转炉、平炉和电弧炉。
转炉和平炉用来炼从高炉出来的铁水加废钢,电弧炉用来将废钢熔化再炼。
平炉由于能耗高、生产周期长,己经遭淘汰。
转炉炼钢:转炉的炉体可以转动,用钢板做外壳,里面用耐火材料做内衬。
炼钢流程及合金辅料
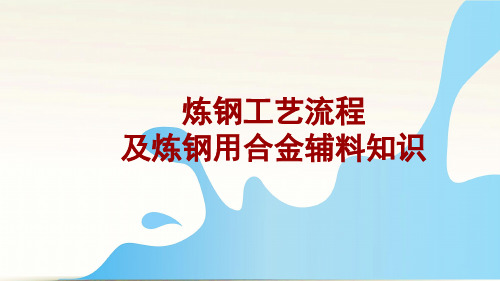
钢与生铁的区别: 元素 C Si Mn p s
(2)转炉吹炼
生铁货铸铁(%) 2.5-4.5 0.3-4.0 0.4-2.0 0.015-0.5 0.01-0.1
2.高炉是炼铁的主要设备,使用的原料有铁矿石(包括 烧结矿、球团矿和块矿)、铁水送炼钢厂炼钢; 高炉煤气主 要用来烧热风炉,同时供炼钢厂和轧钢厂使用;高炉渣经水 淬后送水泥厂生产水泥。
炼钢简述
3.炼钢,目前主要有两条工艺路线,即转炉炼钢工艺流 程和电弧炉炼钢流程。通常将“高炉——铁水预处理——转 炉——精炼——连铸”称为长流程,而将“废钢——电弧 炉——精炼——连铸”称为短流程。
硅钙合金牌号及化学成份
牌号 化学成份% Ca Si C Al P S ≥≤
Ca31Si60 31 55-65 1.0 2.4 0.04 0.05 Ca28Si60 28 55-65 1.0 2.4 0.04 0.05 Ca24Si60 24 55-65 1.0 2.5 0.04 0.04 Ca20Si55 20 50-60 1.0 2.5 0.04 0.04
几种常见铁合金
1.硅钙:
硅钙合金是由元素硅、钙和铁组成的复合合金,是一种较为理想的复合脱氧剂、脱硫 剂。被广泛应用于优质钢、低碳钢、不锈钢等钢种和镍基合金、钛基合金等特殊合金的生 产当中;并适合作转炉练钢车间用的增温剂;还可以作铸铁的孕育剂和球墨铸铁生产中的 添加剂。
钙和硅与氧都有很强的亲和力。特别是钙,不仅与氧有极强的亲和力,而且与硫、氮 都有很强的亲和力。所以硅钙合金是一种较理想的复合胶氧剂、脱硫剂。硅合金不仅脱氧 能力强,脱氧产物易于上浮,易于排出,而且还能改善钢的性能,提高钢的塑性、冲击韧 性和流动性。目前硅钙合金可以代替铝进行终脱氧。被应用于优质钢。特殊钢和特殊合金 生产中。例如低碳钢、不锈钢等钢种和镍基合金、钛基合金等特殊合金,均可用硅钙合金作 脱氧剂。硅钙合金也适合作转炉练钢车间用的增温剂,硅钙合金还可用作铸铁的孕育剂和 球墨铸铁生产中的添加剂。
常用铁水预处理技术

常用铁水预处理技术常用铁水预处理技术铁水预处理基础知识1、什么是铁水预处理?★铁水预处理指铁水兑人炼钢炉之前,为除去某些有害成份或回收某些有益成分的处理过程。
针对炼钢而言,主要是使铁水中硅、磷、硫含量降低到所要求的范围,以简化炼钢过程,提高钢的质量。
铁水预处理具体分为铁水炉外脱硅、脱磷和脱硫,有时脱磷和脱硫同时进行。
对于铁水含有特殊元素提纯精炼或资源综合利用而进行的提钒、提铌、提钨等预处理技术则称为特殊预处理。
2、什么是铁水“三脱”技术?★指铁水兑人炼钢炉之前,进行脱硫、脱硅、脱磷的预处理工艺过程。
3、铁水脱硫的目的是什么?★提高钢质、扩大品种和改善炼钢操作,提高钢的机械、工艺性能。
4、铁水脱硅的目的是什么?⑴减少转炉炼钢渣量、改善操作和提高炼钢经济指标。
硅是氧气转炉炼钢发热的元素,所以为了提高炼钢熔池温度和早化渣,往往希望铁水含硅高一些,但实践证明铁水含硅高时,为了保证转炉渣有较高的碱度,势必增加石灰消耗量,使渣量增多,冶炼时间延长,耗氧量增加,喷溅加剧,铁损增加,并给操作带来困难,从而降低炼钢生产率和增加生产成本。
铁水含硅量一般应控制在0.4%以下的水平。
(2)铁水预脱磷的需要脱硅是铁水预脱磷的先决条件。
铁水预脱磷要求脱磷反应区的氧位高,当加入氧化剂提高氧位时,硅首先就与氧作用而降低铁水中的氧位。
为此,脱磷首先要脱硅,脱磷前控制硅含量一般要求在0.15%以下。
5.铁水脱磷的目的是什么?(1)生产低磷钢、超低磷钢和不锈钢等工艺需要。
磷在钢中对性能的影响,除少数钢种为提高强度或耐大气腐蚀性,要求有一定含磷外,对大多数钢种是有害的,它降低钢的冲击韧性,尤其是低温冲击韧性;磷的枝晶偏析使板材产生带状组织,造成钢板各向异性。
随着新技术材料的发展,对某些品种钢要求磷含量≤0.01%(低磷钢) 或≤0.005%(超低磷钢) 。
用转炉工艺脱磷,虽然有较好的脱磷效果,但达到这种低磷的水平是难以完成的,如采取多次造渣操作,有可能达到,但都存在渣料消耗大,冶炼时间长,热损失大,金属收得率低等问题。
(铁水预处理)炼钢工艺学

水含硫又高的小钢铁厂,还经常被采用。
机械搅拌法
靠旋转沉入铁水中的搅拌器或转动盛铁水的容器使铁水 与脱硫剂搅拌混合。
采用搅拌器和采用转动容器机械搅拌法,均可控制铁水 与脱硫剂的搅拌时间和搅拌强度,用CaC2作脱硫剂能得到 >90%的脱硫效率(单向摇包法搅拌混合较差,脱硫率比双向 摇包法约低10%),可以把铁水中的硫稳定地降低到<0.010%。
1、铁水预脱磷的基本原理
铁水中的磷首先氧化成P2O5,然后与强碱性氧化物结合成 稳定的磷酸盐而去除。
在铁水预脱磷过程中,首先要有适当的氧化剂将溶解于 铁水中的磷氧化,然后采用强有力的固定剂,使被氧化 的磷牢固地结合在炉渣中。
4.4 铁水预脱磷工艺
2、铁水预脱磷方法 ◆ 在高炉出铁沟或出铁槽内进行脱磷 ◆ 在铁水包或鱼雷罐车中进行预脱磷 ◆ 在专用转炉内进行铁水预脱磷
武钢旋转实心搅拌器的KR机械搅拌法,铁水的含硫量 可从0.06%降低到0.005%。实践证明,此类脱硫设备可以用 价廉的石灰进行有效的脱硫。设备最简单,脱硫效率高。
转动容器的回转炉法和摇包法,由于设备复杂,维修费用高 和难于大型化,发展前途不大。
搅拌器法
旋转实心搅拌器的 搅拌法(KR法)
旋转空心搅拌器的搅 拌法(DORA法)
4.5 铁水“三脱”工艺
铁水三脱工艺特点 o 优点: ▪ 可实现转炉少渣冶炼(渣量< 30 kg/t)。 ▪ 铁水脱硫有利于冶炼高碳钢、高锰钢、低磷钢、特殊钢
(如轴承钢、不锈钢)等。 ▪ 可提高脱碳速度,有利于转炉高速冶炼。 ▪ 转炉吹炼终点时钢水锰含量高,可用锰矿直接完成钢水合
金化。 o 缺点: ▪ 铁水中发热元素减少,转炉的废钢加入量减少。 转炉少渣炼钢工艺——铁水预处理将S、P(脱P需先脱Si )
转炉炼钢操作-铁水预处理

相关知识
四、常见脱硫剂及特点 1.苏打灰
其主要成分为Na2CO3,铁水中加入苏打灰后,与硫作用发生以下3个化学 反应:
用苏打灰脱硫,工艺和设备简单,其缺点是脱硫过程中产生的渣会腐蚀 处理罐的内衬,产生的烟尘污染环境,对人有害。目前很少使用。
相关知识
四、常见脱硫剂及特点 2.石灰粉
其主要成分为CaO,用石灰粉脱方法 2. KR搅拌法
KR法铁水预处理脱硫具体操作要求如下: (1)在处理之前,必须将铁水包内的渣子充分扒除,否则会严重影响 脱硫效果。 (2)处理过程中设置搅拌器的转数一般为90~120r/min,在搅动1~ 1.5min后开始加入脱硫剂,搅动时间约13min左右。 (3)处理完毕后,还需仔细地扒除脱硫渣。 ① KR搅拌法的优点:脱硫效率高、脱硫剂消耗少、金属损耗低。 ② KR搅拌法的缺点:温降大,处理10~15min过程温降约50 ℃,搅拌 过程为了铁水液面波动,液面至包口距离应不小于629mm。
石灰价格便宜、使用安全,但在石灰粉颗粒表面易形成2CaO·SiO2致密层, 限制了脱硫反应进行,因此,石灰耗用量大,致使生成的渣量大和铁损大, 铁水温降也较多。另外,石灰还有易吸潮变质的缺点。
相关知识
四、常见脱硫剂及特点 3.电石粉
用电石粉脱硫,铁水温度高时脱硫效率高,铁水温度低于1300℃时脱硫 效率很低。另外,处理后的渣量大,且渣中含有未反应尽的电石颗粒,遇水 易产生乙炔(C2H2)气体,故对脱硫渣的处理要求严格。在脱硫过程中也容 易析出石墨碳污染环境。电石粉易吸潮生成乙炔(乙炔是可燃气体且易发生 爆炸),故电石粉需要以惰性气体密封保存和运输。
相关知识
三、铁水预脱硫的方法 2. KR搅拌法
这种脱硫方法是以一种外衬耐火材料的搅拌器浸入铁水罐内,利用搅拌 器在铁水中旋转搅动铁水,使铁水产生漩涡,在铁液面中央部分产生一个漩 涡下流坑,同时加入脱硫剂使其在下陷坑中被卷入铁水内部进行脱硫反应 (如图所示),从而得到脱硫的目的。
转炉炼钢的原材料
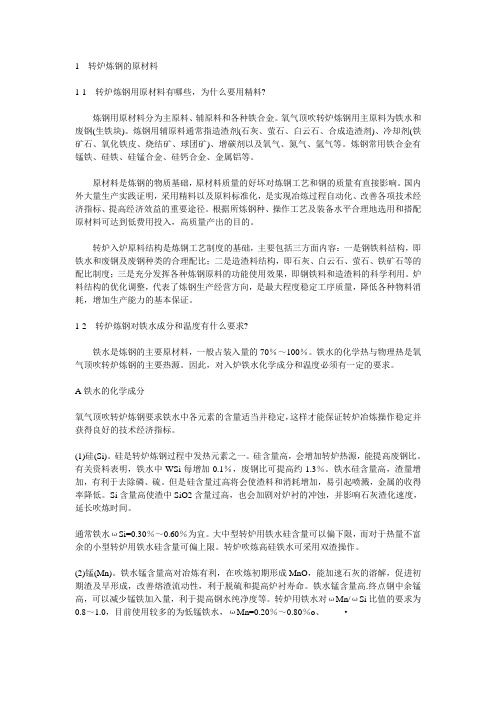
1 转炉炼钢的原材料1-1 转炉炼钢用原材料有哪些,为什么要用精料?炼钢用原材料分为主原料、辅原料和各种铁合金。
氧气顶吹转炉炼钢用主原料为铁水和废钢(生铁块)。
炼钢用辅原料通常指造渣剂(石灰、萤石、白云石、合成造渣剂)、冷却剂(铁矿石、氧化铁皮、烧结矿、球团矿)、增碳剂以及氧气、氮气、氩气等。
炼钢常用铁合金有锰铁、硅铁、硅锰合金、硅钙合金、金属铝等。
原材料是炼钢的物质基础,原材料质量的好坏对炼钢工艺和钢的质量有直接影响。
国内外大量生产实践证明,采用精料以及原料标准化,是实现冶炼过程自动化、改善各项技术经济指标、提高经济效益的重要途径。
根据所炼钢种、操作工艺及装备水平合理地选用和搭配原材料可达到低费用投入,高质量产出的目的。
转炉入炉原料结构是炼钢工艺制度的基础,主要包括三方面内容:一是钢铁料结构,即铁水和废钢及废钢种类的合理配比;二是造渣料结构,即石灰、白云石、萤石、铁矿石等的配比制度;三是充分发挥各种炼钢原料的功能使用效果,即钢铁料和造渣料的科学利用。
炉料结构的优化调整,代表了炼钢生产经营方向,是最大程度稳定工序质量,降低各种物料消耗,增加生产能力的基本保证。
1-2 转炉炼钢对铁水成分和温度有什么要求?铁水是炼钢的主要原材料,一般占装入量的70%~100%。
铁水的化学热与物理热是氧气顶吹转炉炼钢的主要热源。
因此,对入炉铁水化学成分和温度必须有一定的要求。
A铁水的化学成分氧气顶吹转炉炼钢要求铁水中各元素的含量适当并稳定,这样才能保证转炉冶炼操作稳定并获得良好的技术经济指标。
(1)硅(Si)。
硅是转炉炼钢过程中发热元素之一。
硅含量高,会增加转炉热源,能提高废钢比。
有关资料表明,铁水中WSi每增加0.1%,废钢比可提高约1.3%。
铁水硅含量高,渣量增加,有利于去除磷、硫。
但是硅含量过高将会使渣料和消耗增加,易引起喷溅,金属的收得率降低。
Si含量高使渣中SiO2含量过高,也会加剧对炉衬的冲蚀,并影响石灰渣化速度,延长吹炼时间。
转炉炼钢流程
转炉炼钢流程
转炉炼钢是一种常用的钢铁冶炼方法,通过将生铁和废钢放入转炉中,加入适
量的废钢和铁合金,然后进行氧气吹炼,最终得到所需的钢铁产品。
下面将详细介绍转炉炼钢的流程。
首先,将生铁和废钢装入转炉。
生铁是从高炉中得到的铁水,含有较高的碳含量,而废钢是回收利用的废旧钢铁制品。
将这些原料装入转炉后,需要按照一定的比例加入适量的废钢和铁合金,以调整炉料的成分和温度。
接下来是转炉的氧气吹炼过程。
在炉料准备好后,通过转炉底部的氧气鼓风装
置向炉内吹入高压氧气。
氧气与炉内的炉料发生化学反应,使得炉内温度迅速升高,同时氧气氧化了炉料中的杂质和碳,使其逐渐融化。
这个过程需要严格控制氧气的流量和时间,以确保炉内的温度和化学反应达到理想状态。
随着氧气吹炼的进行,炉内的炉料逐渐熔化,形成熔体。
在这个过程中,需要
不断搅拌炉料,以保证炉内温度和成分的均匀性。
同时,根据所需的钢铁品种,可以在这个阶段适量加入合金元素,以调整钢铁的成分和性能。
最后,是炉渣处理和出钢过程。
在炉料完全熔化后,炉内会生成一层炉渣,这
是氧气吹炼过程中产生的氧化物和其他杂质的混合物。
通过合理的炉渣处理方法,可以将炉渣与熔体分离,最终得到所需的钢铁产品。
同时,需要注意控制出钢的速度和温度,以保证钢水的质量和成分符合要求。
总的来说,转炉炼钢流程是一个复杂而精密的过程,需要严格控制各个环节,
以确保最终产品的质量和性能。
通过合理的操作和管理,可以实现高效、低成本的钢铁生产,满足不同领域的需求。
炼钢工艺流程介绍
W
太好 •认知率不高
•以邮局为服务终端,服务 网络覆盖面广
•可靠性与速度不及私营公 司
•私营速递公司多以大公司 为主要客户
•香港近年经济不太景气, 外部环境不利
O •中小机构、个人的需求得 T •速递业竞争对手林立,正
不到满足,是个被忽视的
面冲突可能招致报复
市场
制订行动计划
制定计划的基本思路是:发挥优势因素,克服弱点因素,利用机会因素,化
替代者
供货商的品牌或价格特色;
供地货位商 ;的 供战货略商中之本间企的业关的系;供应商
从供货商之间转移的成本来自竞争者新进 入者客户
本企业的部件或原材 料产品占买方成本的 比例;各买方之间是 否有联合的危险;本 企业与买方是否具有 战略合作关系
进入本行业有哪些壁垒?它们阻 碍新进入者的作用有多大?本企 业怎样确定自己的地位(自己进 入或者阻止对手进入)?
This template is the internal standard courseware template of the enterprise
SWOT分析模板
什么是SWOT分析
➢SWOT分析是市场营销管理中经常使用的功能强大的分析工具,最早是由 美国旧金山大学的管理学教授在80年代初提出来的:S代表strength(优势), W代表weakness(弱势),O代表opportunity (机会),T代表threat(威胁)。
SW SW OT OT
当选择行业领域 中只有少数竞争 对手时,可以考 虑做SWOT组图
进行比较
SWOT分析步骤
分析环境因素 构造SWOT矩阵 制定行动计划
运用各种调查 研究方法,分 析出公司所处 的各种环境因 素,即外部环 境因素和内部 能力因素。
转炉炼钢原材料与铁水预处理
处理。
(3)铁水的含硅量:铁水中的硅是转炉炼钢的主要发热元素 之一,含硅量每增加0.1%,废钢比可增加1.3%~1.5%。对于 大、中型转炉,铁水含硅量以0.3%~0.6%为宜。小型转炉的 热损较大,铁水的含硅量可以高些。
铁水质量鉴别
废钢的来源主要有两个方面,一是社会废钢,二是钢厂自己
的返回料。
2、废钢的验收
(1)炼钢用废钢的技术要求见下表
类 别 重型废钢 中型废钢 代 号 GF1 GF2
各种废钢 典型举例
钢锭、铸坯及其 切头、切尾……
供应状态 块状
单重 /kg
500~ <1800 30~ <500 <30
外形尺寸/mm ≤1200*500*40 0 ≤500*400*300
废钢中严禁混入密封容器,因为它受热膨胀容易造成爆炸
等恶性事故。
废钢还要求少锈蚀。因为锈的化学成分是Fe(OH)2或
Fe2O3.H2O,在高温下会分解而使[H]增加,在钢中产生白点, 降低钢的机械性能。
C、废钢块度的影响
入炉废钢的块度要适宜。对转炉来讲,一般以小于炉口直
径的1/2为好,单重也不能太大。
(3) 炼钢采用低硫铁水冶炼,提高转炉生产率、降低成本、 节约能耗。
(4)提高低碳钢的清洁度,钢中T[O]、[N]、[H]含量降低。
(5)有利于复吹转炉冶炼高碳钢时的“保碳出钢技术”。
1. 铁水预脱硫
铁水预脱硫是20世纪70年代发展起来的铁水处理工艺 技术,采用铁水预脱硫,不仅可以减轻高炉负担,降低 焦比,减少渣量和提高生产率,使转炉也不必为脱硫而 采取大渣量高碱度操作,因为在转炉高氧化性炉渣条件 下脱硫是相当困难的。因此铁水预脱硫已成为现代钢铁 工业优化工艺流程的重要手段,是提高钢质量、扩大品 种的主要措施。
铁水预处理技术01-02
¾ 历史背景: 60年代,氧枪转炉炼钢的崛起工业的发展给钢铁材料质量和焊接性能
好;抗腐蚀和高温性能好 用户需求:降低钢中杂质:硫、磷含量越低越好! 发展现状:30年代开始,60年代蓬勃发展!
第一章 铁水预处理概述
序,有的厂铁水实现了100%的预处理。平均约80%的铁 水经过脱硫;日本50%左右的铁水经过脱硅,40%以上的 铁水经过脱磷处理。
第一章 铁水预处理概述
• 2. 国外三脱技术的发展
¾ 六类十六种脱硫方法: 摇动法:瑞典的单向偏心摇动铁水罐法,日本神户尼崎铁
厂可逆旋转式DM摇包法。 机 械 搅 拌 法 : 原 西 德 DO(Damage Ostberg) 法 、
受研究者关注。
第一章 铁水预处理概述
• 4. 铁水预处理发展趋势 预脱硫→预脱硅→预脱磷(同时脱磷脱硫);
未来以喷吹法为主; 脱硫剂受原料经济和钢材产品要求而波动; 发展方向:高效、廉价、易得的复合脱硫剂;CaO系、
外预处理技术已在世界各国广泛应用。
第一章 铁水预处理概述
¾ 铁水预处理的必要性和迫切性:
是脱硫反应化学冶金学合理性的必要;
☺高炉: 动力学条件差,脱硫要付出代价;
☺
高炉脱硫:高炉温、焦比高、产量低。
☺转炉: 热力学条件不好,几乎无脱硫能力。
☺炉外: 可创造良好的热力学和动力学条件。
是钢材市场竞争力紧迫性的必要;
RS(Rheinstahl) 法 和 赫 歇 法 、 日 本 新 日 铁 KR(Kambara Reactor)法、千叶NP法。 吹气搅拌法: 新日铁PDS(底喷)法和CLDS(顶喷)法。 钟罩压入法:美国Janes Laughlin公司的镁焦法。 喷 吹 法 : 西 德 Thyssen 的 ATH(斜 插喷 枪 )法; 新日铁的 TDS(顶喷)法。 炉前铁水沟连续脱硫法。
- 1、下载文档前请自行甄别文档内容的完整性,平台不提供额外的编辑、内容补充、找答案等附加服务。
- 2、"仅部分预览"的文档,不可在线预览部分如存在完整性等问题,可反馈申请退款(可完整预览的文档不适用该条件!)。
- 3、如文档侵犯您的权益,请联系客服反馈,我们会尽快为您处理(人工客服工作时间:9:00-18:30)。
特别提醒:严禁放射性物质进入炉内,以免造成污染,危 害人的健康和生命。有时废钢中可能会混入密封的放射源, 对此,一定要及时报告有关部门,不可轻易触摸、打开,更 不可入炉熔炼导致放射污染扩散。
(4) 废钢铁中密封容器和有害元素的识别
2、有害元素的危害
CaC2 + [FeS] = CaS + 2[C] 电石(CaC2)基脱硫剂的脱硫特点是: (的1脱)硫Ca能C力2 分,解而出且的脱钙硫离反子应与是硫放有热极反强应的,亲有和利力于,减因少此铁有水很的强 温降。
铁水质量鉴别
(3)根据所炼钢种的要求选用不同的铁块或铁水
所炼钢种对硫、磷有较高要求的,宜选用含硫、磷低等级的 铁块或铁水。
对钢种硫磷含量要求特别严格的,应对所选用的铁水进行预 处理。
铁水质量鉴别
3.对铁水的要求
1、作用:转炉炼钢的主原料,一般占装入量的70%以上。 2、要求 铁水应符合一定要求,以简化和稳定操作并获得良好技术经济 指标。 1)温度≥1250℃而且稳定 铁水温度的高低,标志着其物理热的多少。较高的铁水温度, 不仅能保证转炉吹炼顺利进行,同时还能增加废钢的配加量, 降低生产成本。因此,希望铁水的温度尽量高些,一般应保证 入炉时仍在1250℃~1300℃以上。 另外,还希望铁水温度相对稳定,以利于冶炼操作和生产调度。
(3)根据所炼钢种的要求选用废钢
所炼钢种对夹杂物有严格要求的,应选用纯净的废钢。 对钢种硫磷含量要求特别严格的,应对所选用的铁水进行预 处理。
(4) 废钢铁中密封容器和有害元素的识别
废钢铁中的密封容器和铜、铅、锡等有害元素都会对冶炼及钢 的质量造成不良后果,因此一定要进行认真、仔细、严格的 检查,严禁密封容器和铜、铅、锡等有害元素进入炉内。 1、密封容器的危害
(2)锡 常见的白锡,银白色金属,富有延展性。镀锡钢皮常称为马 口铁,是废钢中最常见的。锡存在于钢中,会使钢产生热脆 现象,并降低成品钢材的机械性能。所以要防止将锡带入炉 料中。
(3)铅
银白色(灰白色)金属,延性弱,展性强,经常混入 社会废钢中。铅的密度大,熔点低,不溶于钢水,在 冶炼时会沉到炉底砖入缝隙中,造成炉底漏钢事故。 同时,在冶炼的高温下,铅还会蒸发,对大气造成污 染,有害于人体健康。
1、废钢的识别
➢ 炼钢生产中所炼钢种碳含量大多在1.00%以下。钢的特点是强 度高,塑性好,可以锻、轧成各种所需要的形状,并且能随 成分、压力加工和热处理方法的不同获得不同性能的材料。
➢ 废钢是指已不能正常应用的钢铁余料;锈蚀或报废的机器零 件;零件加工时的碎屑、刨屑或磨屑等。钢厂的废品及返回 料等,一般以锭、坯、棒、管、板、带、丝、压块、铸件、 轧辊等形态出现。
1. 铁水预脱硫
1) 脱硫剂
脱硫剂是决定脱硫率和脱硫成本的主要因素之一,选择 脱硫剂主要从脱硫能力、成本、资源、环境保护、对容器耐火 材料的侵蚀、对操作的影响及安全等因素综合考虑。常用的脱 硫剂有电石粉、石灰粉、石灰石粉、Na2CO3、金属镁等。
(1)电石(CaC2)基脱硫剂 50%炼~钢8脱0%硫的用工的业电电石石(,Ca1C62%)基~脱40硫%剂的,C是aO由以含及C碳aC组2 成的, 其脱硫反应为:
如果废钢太重太大,可能会导致入炉困难,入炉后由于对 炉衬的冲击力太大而影响炉衬的寿命,个别大块废钢入炉 后甚至到冶炼终点时还不能全部熔化,出钢后会造成钢水 温度或成分出格。
如果废钢太轻太小也不好,其体积必然增大,入炉后会在 炉内堆积,可能会造成送氧点火困难。
一般炼钢厂根据炉子容量大小对废钢块度和单重都有具体 的规定。
铁水质量鉴别
(5)铁水的含碳量:碳也是转炉炼钢的主要发热元素, ≥3.5%的含碳量即可满足冶炼要求,而通常铁水含碳 4%左右,故一般不做要求。 3)带渣量≤0.5% 高炉渣中含有大量的S、SiO2,因此希望兑入转炉的铁 水尽量少带渣,以减轻脱硫任务和减少渣量,通常要 求带渣量不得超过0.5%。
二、废钢
➢ 废钢的来源主要有两个方面,一是社会废钢,二是钢厂自己 的返回料。
2、废钢的验收
(1)炼钢用废钢的技术要求见下表
类别 重型废钢 中型废钢 小型废钢 轻型废钢
代号 GF1 GF2 GF3 GF4
各种废钢 典型举例
单重
供应状态
外形尺寸/mm
/kg
钢锭、铸坯及其 切头、切尾……
块状
500~ ≤1200*500*40
b、铁水成分的影响:铁水中的C、Si、Mn、P、 Fe的氧化放热是 转炉炼钢的重要热源(即化学热),因此铁水的成分对炼钢冶 炼过程的温度控制有重要影响。P、S等是钢中的有害元素,必 须去除到钢种要求的范围,否则会对钢的质量造成危害。在冶 炼的过程中,铁水各成分含量的不同,对冶炼的工艺、时间、 成本等都会产生不同的影响。
2、废钢的预热 目的:提高废钢比,降低生产成本。 方法及效果:利用铁水罐余热和燃料燃烧加热。
废钢的切割
三、铁水预处理
铁水预处理,炼钢生产中主要是指铁水在进入转炉之前的脱硫 处理。广义的铁水预处理是指包括对铁水脱硫、脱硅、脱磷的 三脱处理,另外还有特殊铁水的预处理,如含V铁水的提V、含 Nb铁水的提Nb 等。 (1)满足用户对超低硫、磷钢的需求,发展高附加值钢种: 如: 船板钢、油井管钢:[S]、[P]0.005 % 管线钢:[S] 0.002~0.004 %. (2) 减轻高炉脱硫负担,放宽对硫的限制,提高产量,降低 焦比;
(3) 炼钢采用低硫铁水冶炼,提高转炉生产率、降低成本、 节约能耗。
(4)提高低碳钢的清洁度,钢中T[O]、[N]、[H]含量降低。 (5)有利于复吹转炉冶炼高碳钢时的“保碳出钢技术”。
1. 铁水预脱硫
铁水预脱硫是20世纪70年代发展起来的铁水处理工艺 技术,采用铁水预脱硫,不仅可以减轻高炉负担,降低 焦比,减少渣量和提高生产率,使转炉也不必为脱硫而 采取大渣量高碱度操作,因为在转炉高氧化性炉渣条件 下脱硫是相当困难的。因此铁水预脱硫已成为现代钢铁 工业优化工艺流程的重要手段,是提高钢质量、扩大品 种的主要措施。
(1)铜 金黄色金属,富有延展性,有良好的导热、导电性,常用来 制作电器开关、触头、电线、马达线圈等。铜主要以这些形 态混入废钢铁中。 钢中铜含量超过0.3%以后,在晶界上会有低熔点共晶体出现, 在热加工时造成沿晶界开裂,严重损害使用质量。同时使钢 的切削性能变坏。所以对钢中[Cu]含量要严加限制(特殊钢 种除外)。
>0.70~1.25
> 0.15~0.25
> 0.25~0.40
≤0.02
> 0.02~0.030
> 0.03~0.04
> 0.04~0.07
铁水质量鉴别
(2)铁水质量对冶炼的影响 主要是铁水温度和成分的影响。 a、铁水温度的影响:转炉炼钢所需要的热量主要来自两个方面: 一是铁水本身的温度即物理热,二是铁水中元素在冶炼过程中 发生化学反应产生的热量即化学热,基本上二者各占50%左右。
铁水质量鉴别
(4)铁水的含锰量:铁水中的锰是一种有益元素,主要 体现在锰氧化后生成的氧化锰能促使石灰溶解,有利于提 高炉龄和减轻氧枪粘钢,同时铁水含Mn高,终点钢中余 锰高,从而可以减少合金化时所需的锰铁合金,有利于提 高钢水纯净度。 转炉用铁水对锰与硅比值要求为0.8-1.0,我国大多数钢铁 厂所用铁水的含锰量都不高,多为0.2%~0.4%。提高铁 水含锰量的方法主要是向高炉的原料中配加锰矿石,但这 将会使炼铁生产的焦比升高和高炉的生产率下降。对于铁 水增锰的合理性还需要做详细的技术经济对比,因此,目 前对铁水含锰量不提硬性要求。
二、废钢的作用与要求
1、作用 冷却熔池。
2、要求 ⑴ 清洁、少锈,无混杂,不含有色金属; ⑵ 最大长度不得超过炉口直径的二分之一,最大截面积
要小于炉口面积的五分之一。
三、废钢的加工和预热
1、废钢的加工 应针对所购废钢的特点进行相应的加工处理如切割、打 包、火烧、挑拣、水洗等,以满足转炉炼钢对入炉废钢 的基本要求。
铁水质量鉴别
(2)铁水的含硫量≤0.05%:硫会使钢产生“热脆”现象,也 是钢中的有害元素。转炉的脱硫效果不理想,单渣法冶炼时的 脱硫率仅为30%~35%,而通常要求钢液的含硫量在0.05%以 下,因此国标规定铁水含硫量≤0.05%。 如果铁水含硫量超过0.05%或吹炼低硫钢,则需采用双渣法冶 炼或对铁水进行预脱硫处理。 如果冶炼优质钢,要求水含硫量≤0.005%,对铁水进行预脱硫 处理。 (3)铁水的含硅量:铁水中的硅是转炉炼钢的主要发热元素 之一,含硅量每增加0.1%,废钢比可增加1.3%~1.5%。对于 大、中型转炉,铁水含硅量以0.3%~0.6%为宜。小型转炉的 热损较大,铁水的含硅量可以高些。
废钢中严禁混入密封容器,因为它受热膨胀容易造成爆炸 等恶性事故。
废钢还要求少锈蚀。因为锈的化学成分是Fe(OH)2或 Fe2O3.H2O,在高温下会分解而使[H]增加,在钢中产生白点, 降低钢的机械性能。
C、废钢块度的影响
入炉废钢的块度要适宜。对转炉来讲,一般以小于炉口直 径的1/2为好,单重也重型废钢
钢屑 渣钢
钢屑压块 轻型废钢
(2)废钢质量对冶炼的影响
a、废钢成分的影响:同铁水成分的影响
b、废钢外观质量的影响
废钢外观要求清洁,即要求少泥沙、耐材和无油污、不得 混入橡胶等杂物,否则会使熔池内SiO2、Al2O3、[H]、[P]、 [S]等杂质增加,其结果将增加冶炼的难度,增加熔剂等消 耗,降低钢的质量。
铁水质量鉴别
若含硅量低于0.3%,铁水的化学热不足,会导致废钢比下降, 小容量转炉甚至不能正常吹炼;反之,如果铁水含硅量高 于0.6%,不仅会增加造渣材料的消耗,而且使炉内的渣量偏 大,过多的渣量容易引起喷溅,增加金属损失。 铁水含硅量高时,初期渣子的碱度低,对炉衬的侵蚀作用 加剧; 初期渣中的二氧化硅含量高,这会使渣中的FeO、MnO含 量相对降低,容易在石灰块表面生成一层熔点为2130℃的 2CaO·SiO2外壳,阻碍石灰熔化,降低成渣速度,不利于 早期的去磷。 应该指出的是,一些钢厂铁水的含硅量超过了1.2%,个别 的甚至达到了1.5%,对此应进行预脱硅处理,以减轻转炉 的负担。