金属热处理硬度通用检验标准
热处理标准规范

3、硬度测量方法:3.1各种硬度测量的试验条件,见下表1:为保证零件热处理后达到其图纸技术(或工艺)要求,待检件选取应有代表性,通常从热处理后的零件中选取,能反映零件的工作部位或零件的工作部位硬度的其他部位,对每一个待检件的正时试验点数一般应不少于3个点。
通常连续式加热炉(如网带炉):应在连续生产的网带淬火入回火炉前、回火后入料框前的网带上抽检3-5件/时。
且及时作检验记录。
同时,若发现硬度超差,应及时作检验记录。
同时,若发现硬度越差,应及时进行工艺参数调整,且将前1小时段的零件进行隔离处理(如返工、检)。
通常期式加炉(如井式炉、箱式炉):应在淬火后、回火后均从料框的上、中、下部位抽检6-9件/炉,且及时作检验记录。
同时,若发现硬度超差,应及时进行工艺参数调整,且将该炉次的零件进行隔离处理(如返工、逐检)。
通常感应淬火工艺及感应器与零件间隙精度调整,经首件(或批)感应淬火合格后方可生产,且及时作检验记录。
GB4342 金属显微维氏硬度试验方法 GB5030 金属小负荷维氏试验方法2、待检件选取与检验原则如下:热处理检验规范一、使用范围:二、硬度检验:通常是根据金属零件工作时所承受的载荷,计算出金属零件上的应力分布,考虑安全系数,提出对材料的强度要求,以强度要求,以强度与硬度的对应关系,确定零件热处理后应具有大硬度值。
为此,硬度时金属零件热处理最重要的质量检验指标,不少零件还时唯一的技术要求。
金属零件的内在质量主要取决于材料和热处理。
因热处理为特种工艺所赋予产品的质量特性往往又室补直观的内在质量,属于“内科”范畴,往往需要通过特殊的仪器 (如:各种硬度计、 金相显微镜、各种力学性能机)进行检测。
在GB/T19000-ISO9000系列标准中,要求对机械产品零部件在整个热处理过程中一切影响因素实施全面控制,反映原材料及热处理过程控制,质量检验及热处理作业条件(包括生产与检验设备、技术、管理、操作人员素质及管理水平)等各方面均要求控制,才能确保热处理质量。
JB/T 6050-2006《钢铁热处理零件硬度测试通则》介绍
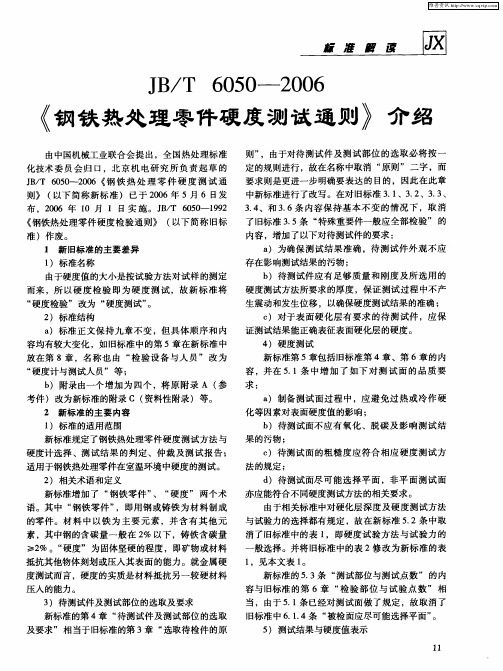
c )待测试面 的粗糙度应符合相应硬度测试方 法 的规定 ;
d 待测试 面 尽 可 能 选 择 平 面 ,非 平 面 测 试 面 )
亦应能符合不同硬度测试方法 的相关要求。
由于相关 标 准 中对 硬化 层深 度 及 硬 度测 试 方 法
语。其中 “ 钢铁零件” ,即用钢或铸铁 为材料制成 的零件。材 料 中以铁 为主要 元素 ,并含有 其他元 素 ,其中钢 的含碳量一般在 2 以下,铸铁含碳量 % ≥2 %。“ 硬度”为固体坚硬的程度 ,即矿物或材料 抵抗其他物体刻划或压入其表面的能力。就金属硬 度测试而言,硬度 的实质是材料抵抗另一较硬材料
布 ,20 年 l 月 1 日实 施 。 J/ 65 ~ l9 06 0 B T 00 92
34 . 、和 3 6 内容保持基本 不变的情况下 ,取消 .条 了旧标准 35条 “ . 特殊重要件一般应全部检验” 的 内容 ,增加了以下对待测试件的要求 : a )为确保测试结果 准确 ,待测试件外 观不应
正火件 与退火件
部分 :试验方 法》 B T 2 11 o 2 《 属 布 氏 D型装置测试 、G / 3 . _2 o 金 硬度试验 第 1部分 :试验方 法》 B T 44 . - 、G / 30 1 第 1部分 :试验 方法》 、
一般 按 G / 2 0 1 ( B T 3 . C标 尺 )测试 ;辊类 件按
2 新 标 准的主 要 内容
新标准第 5 章包括旧标准第 4章 、第 6 的内 章 容 ,并在 5 1条 中增 加 了如下对测 试 面的 品质 要 .
求:
a )制备测试 面过程 中,应避免过 热或冷作硬 化等因素对表面硬度值的影响; b )待测试面不应有氧化、脱碳及影 响测试 结
硬度标准

金属材料抵抗硬的物体压陷表面的能力,称为硬度。
根据试验方法和适用范围不同,硬度又可分为布氏硬度、洛氏硬度、维氏硬度、肖氏硬度、显微硬度和高温硬度等。
对于管材一般常用的有布氏、洛氏、维氏硬度三种。
一、布氏硬度(HB)用一定直径的钢球或硬质合金球,以规定的试验力(F)压入式样表面,经规定保持时间后卸除试验力,测量试样表面的压痕直径(L)。
布氏硬度值是以试验力除以压痕球形表面积所得的商。
以HBS(钢球)表示,单位为N/mm2MPa。
其计算公式为:式中:F--压入金属试样表面的试验力,N;D--试验用钢球直径,mm;d--压痕平均直径,mm。
测定布氏硬度较准确可靠,但一般HBS只适用于450N/mm2(MPa)以下的金属材料,对于较硬的钢或较薄的板材不适用。
在钢管标准中,布氏硬度用途最广,往往以压痕直径d来表示该材料的硬度,既直观,又方便。
举例:120HBS10/1000130:表示用直径10mm钢球在1000Kgf(9.807KN)试验力作用下,保持30s(秒)测得的布氏硬度值为120N/ mm2(MPa)。
二、洛氏硬度(HK)洛氏硬度试验同布氏硬度试验一样,都是压痕试验方法。
不同的是,它是测量压痕的深度。
即,在初邕试验力(Fo)及总试验力(F)的先后作用下,将压头(金钢厂圆锥体或钢球)压入试样表面,经规定保持时间后,卸除主试验力,用测量的残余压痕深度增量(e)计算硬度值。
其值是个无名数,以符号HR表示,所用标尺有A、B、C、D、E、F、G、H、K等9个标尺。
其中常用于钢材硬度试验的标尺一般为A、B、C,即HRA、HRB、HRC。
硬度值用下式计算:当用A和C标尺试验时,HR=100-e当用B标尺试验时,HR=130-e式中e--残余压痕深度增量,其什系以规定单位0.002mm表示,即当压头轴向位移一个单位(0.002mm)时,即相当于洛氏硬度变化一个数。
e值愈大,金属的硬度愈低,反之则硬度愈高。
上述三个标尺适用范围如下:HRA(金刚石圆锥压头)20-88HRC(金刚石圆锥压头)20-70HRB(直径1.588mm钢球压头)20-100洛氏硬度试验是目前应用很广的方法,其中HRC在钢管标准中使用仅次于布氏硬度HB。
p92材料热影响区最高硬度测试标准
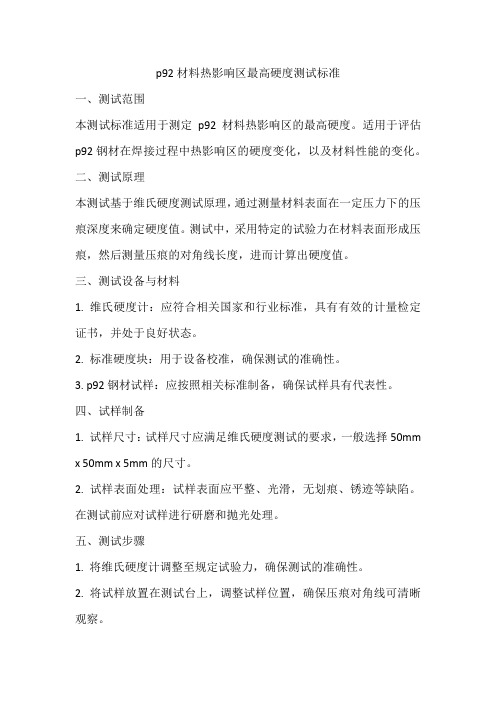
p92材料热影响区最高硬度测试标准一、测试范围本测试标准适用于测定p92材料热影响区的最高硬度。
适用于评估p92钢材在焊接过程中热影响区的硬度变化,以及材料性能的变化。
二、测试原理本测试基于维氏硬度测试原理,通过测量材料表面在一定压力下的压痕深度来确定硬度值。
测试中,采用特定的试验力在材料表面形成压痕,然后测量压痕的对角线长度,进而计算出硬度值。
三、测试设备与材料1. 维氏硬度计:应符合相关国家和行业标准,具有有效的计量检定证书,并处于良好状态。
2. 标准硬度块:用于设备校准,确保测试的准确性。
3. p92钢材试样:应按照相关标准制备,确保试样具有代表性。
四、试样制备1. 试样尺寸:试样尺寸应满足维氏硬度测试的要求,一般选择50mm x 50mm x 5mm的尺寸。
2. 试样表面处理:试样表面应平整、光滑,无划痕、锈迹等缺陷。
在测试前应对试样进行研磨和抛光处理。
五、测试步骤1. 将维氏硬度计调整至规定试验力,确保测试的准确性。
2. 将试样放置在测试台上,调整试样位置,确保压痕对角线可清晰观察。
3. 对试样施加规定的试验力,保持一定时间后卸载。
4. 测量压痕对角线长度,记录数据。
5. 根据压痕对角线长度计算硬度值,记录结果。
6. 重复以上步骤,在不同区域测试至少10个点,取平均值作为最终结果。
六、结果解读根据所测得的硬度值,可分析p92材料热影响区的硬度变化趋势,进而评估材料的性能变化和焊接工艺的可靠性。
硬度值越高,表明材料的硬度和强度越高。
通过比较不同温度和时间下的硬度值,可进一步研究焊接工艺参数对热影响区硬度的影响。
七、测试精度与误差本测试标准的精度取决于设备的精度和操作人员的技能水平。
误差可能来源于设备校准误差、压痕测量误差和计算误差等。
为减小误差,应定期对设备进行校准,提高操作人员的技能水平,并遵循标准的测试步骤进行操作。
八、测试报告测试报告应包括以下内容:测试日期、试样编号、试验力、硬度值、平均硬度值、结论等。
热处理后金属表面硬度概念
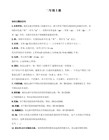
(3)试验条件的选择 布氏硬度试验时,压头球体的直径D、试验载荷F及载荷保持
的时间 t,应根据被试金属材料的种类、硬度值的范围及厚度进行选择。
常用的压头直径 l、2、2.5、5和10毫米五种。
试验载荷可从9.807N ( l kgf) ~29.42 KN (3000 kgf)范围内
HRA
:是采用60kg载荷和钻石锥压入器求得的硬度,用于硬度极高的材料(如硬质合金等)。
HRB:是采用100kg载荷和直径1.58mm淬硬的钢球,求得的硬度,用于硬度较低的材料(如退火钢、铸铁等)。
布氏硬度的符号及表示方法
布氏硬度的符号用 HBS或HBW表示。
HBS表示压头为淬硬钢球,用于测定布氏硬度值在450以下的材料,如软钢、灰铸铁和有色金属等。
HBW表示压头为硬质合金,用于测定布氏硬度值在65ቤተ መጻሕፍቲ ባይዱ以下的树料。
布氏硬度的表示方法: HBS或HBW之前的数字为硬度值,后面按顺序用数字表示试验条件:
金属材料抵抗其他更硬物体压入表面的能力称为硬度,或者说是材料对局部塑性变形的抵抗能力。因此,硬度与强度有着一定的关系。根据硬度的测定方法,主要可以分为:
(1)布氏硬度(代号HB)
用一定直径D的淬硬钢球在规定负荷P的作用下压入试件表面,保持一段时间后卸去载荷,在试件表面将会留下表面积为F的压痕,以试件的单位表面积上能承受负荷的大小表示该试件的硬度:HB=P/F。在实际应用中,通常直接测量压坑的直径,并根据负荷P和钢球直径D从布氏硬度数值表上查出布氏硬度值(显然,压坑直径越大,硬度越低,表示的布氏硬度值越小)。
6.洛式硬度的硬度值是一无名数,没有单位。(因此习惯称洛式硬度为多少度是不正确的。)布式硬度的硬度值有单位,且和抗拉强度有一定的近似关系。
硬度检验方法和规范

硬度检验方法和规范通常是根据金属零件工作时所承受的载荷,计算出金属零件上的应力分布,考虑安全系数,提出对材料的强度要求,以强度要求,以强度与硬度的对应关系,确定零件热处理后应具有大硬度值。
为此,硬度时金属零件热处理最重要的质量检验指标,不少零件还时唯一的技术要求。
1、常用硬度检验方法的标准如下:GB230 金属洛氏硬度试验方法GB231 金属布氏硬度试验方法GB1818 金属表面洛氏硬度试验方法GB4340 金属维氏硬度试验方法GB4342 金属显微维氏硬度试验方法GB5030 金属小负荷维氏试验方法2、待检件选取与检验原则如下:为保证零件热处理后达到其图纸技术(或工艺)要求,待检件选取应有代表性,通常从热处理后的零件中选取,能反映零件的工作部位或零件的工作部位硬度的其他部位,对每一个待检件的正时试验点数一般应不少于3个点。
通常连续式加热炉(如网带炉):应在连续生产的网带淬火入回火炉前、回火后入料框前的网带上抽检3-5件/时。
且及时作检验记录。
同时,若发现硬度超差,应及时作检验记录。
同时,若发现硬度越差,应及时进行工艺参数调整,且将前1小时段的零件进行隔离处理(如返工、检)。
通常期式加炉(如井式炉、箱式炉):应在淬火后、回火后均从料框的上、中、下部位抽检6-9件/炉,且及时作检验记录。
同时,若发现硬度超差,应及时进行工艺参数调整,且将该炉次的零件进行隔离处理(如返工、逐检)。
通常感应淬火工艺及感应器与零件间隙精度调整,经首件(或批)感应淬火合格后方可生产,且及时作检验记录。
3、硬度测量方法:各种硬度测量的试验条件,见下表1:测量硬化层深度不同的零件表面硬度时,硬度试验方法与试验力的一般选择,见表经不同热处理工艺处理后的表面硬度测量方法及其选择,见小表3:备注:(1)零件心部或基体硬度,一般按或GB4340的试验方法测量。
(2)若确定的硬度试验方法有几种试验力可供选择时,应选用试验条件允许的最大试验力。
铝合金硬度测试标准

铝合金硬度测试标准铝合金是一种由铝和其他元素合金化而成的材料,在现代工业领域中得到广泛应用。
铝合金具有较低的密度、良好的导热性和可加工性,同时具有较高的强度和硬度。
因此,对于铝合金的硬度测试非常重要,它可以帮助判断材料的性能和适用范围。
下面将介绍一些常见的铝合金硬度测试方法和标准。
一、洛氏硬度测试洛氏硬度测试是最常用的金属硬度测试方法之一,也适用于铝合金材料。
它通过将一个金属圆锥压入被测试材料的表面,然后测量圆锥在材料表面形成的印痕直径来确定硬度值。
对于铝合金,常用的洛氏硬度标准有洛氏A硬度、洛氏B硬度和洛氏F硬度,其测试规程和要求由ISO 6506和ASTM E10等标准规定。
二、布氏硬度测试布氏硬度测试是另一种常见的金属硬度测试方法,也可以用于铝合金材料的硬度测试。
它通过将一个钢球或钻石锥压入被测试材料的表面,然后测量形成的印痕的大小来确定硬度值。
布氏硬度测试方法有很高的准确度和重复性,对于铝合金的硬度评估非常有用。
常用的布氏硬度标准包括ISO 6507和ASTM E18等。
三、维氏硬度测试维氏硬度测试是一种间接硬度测试方法,适用于较软的金属材料。
它通过从一个特定高度自由落下的小圆锥的弹性回弹来判断材料的硬度。
对于铝合金材料的硬度测试,常使用的是维氏硬度测试的维氏硬度(VHN)。
维氏硬度测试方法由ISO 6507和ASTM E92等标准规定。
四、洛氏硬度和布氏硬度的关系洛氏硬度测试和布氏硬度测试都可以用于铝合金的硬度测试,它们之间有一定的相关性。
通常情况下,从布氏硬度值可以估算出相对应的洛氏硬度值,这种关系可以由硬度转换表提供。
硬度转换表中列出了不同硬度测试之间的近似转换关系,可以帮助用户在不同测试方法之间进行比较和转换。
在进行铝合金硬度测试之前,需要保证测试的准确性和可重复性。
这包括选用适当的测试方法、正确选择合适的硬度测试仪器和标准试样,并对硬度仪进行定期校准。
此外,还应根据需要选择合适的测试力和停留时间,以及合适的测试环境温度。
金属硬度检测的试验方法

摘要硬度是评定金属材料力学性能最常用的指标之一。
硬度的实质是材料抵抗另一较硬材料压入的能力。
硬度检测是评价金属力学性能最迅速、最经济、最简单的一种试验方法。
硬度检测的主要目的就是测定材料的适用性,或材料为使用目的所进行的特殊硬化或软化处理的效果。
对于被检测材料而言,硬度是代表着在一定压头和试验力作用下所反映出的弹性、塑性、强度、韧性及磨损抗力等多种物理量的综合性能。
由于通过硬度试验可以反映金属材料在不同的化学成分、组织结构和热处理工艺条件下性能的差异,因此硬度试验广泛应用于金属性能的检验、监督热处理工艺质量和新材料的研制。
金属硬度检测主要有两类试验方法。
一类是静态试验方法,这类方法试验力的施加是缓慢而无冲击的。
硬度的测定主要决定于压痕的深度、压痕投影面积或压痕凹印面积的大小。
静态试验方法包括布氏、洛氏、维氏、努氏、韦氏、巴氏等。
其中布、洛、维三种试验方法是应用最广的,它们是金属硬度检测的主要试验方法。
另一类试验方法是动态试验法,这类方法试验力的施加是动态的和冲击性的。
这里包括肖氏和里氏硬度试验法。
动态试验法主要用于大型的,不可移动工件的硬度检测。
关键词:硬度;物理量;试验方法;力学性能Abstract第1章引言 (5)1.1金属材料硬度的定义 (5)1.2硬度试验的作用和特点 (5)1.3常用硬度试验方法的分类 (6)第二章金属材料硬度的检测方法 (8)2.1 洛氏硬度检测方法 (8)2.1.1原理 (8)2.1.2符号和计算公式 (8)2.1.3检测过程及其示意图 (9)2.1.4洛氏硬度标尺及技术参数 (12)2.1.5标尺的应用原则 (12)2.1.6应用范围及其特点 (13)2.1.7检测及注意事项 (13)2.2布氏硬度检测方法 (18)2.2.1原理 (18)2.2.2计算公式 (18)2.2.3相似原理及其应用 (19)2.2.4 K值于K常数的选用 (20)2.2.5应用范围及其优缺点 (21)2.2.6检测方法和技术条件 (21)2.3维氏硬度检测方法 (24)2.3.1原理 (24)2.3.2范围、符号和说明 (24)2.3.3 计算公式 (25)2.3.4相似原理 (26)2.3.5应用及其特点 (27)2.3.6检测方法和注意事项 (28)2.3.7试样最小厚度于检测力间关系 (29)第三章方法选用和硬度要求 (30)3.1硬度检测方法的选用 (30)第四章金属硬度检测技术现状及其展望 (34)4.1硬度计发展现状 (34)4.2现代硬度计量测试的发展趋势 (35)4.3现代硬度计的展望 (35)附录A 部分发达国家有关硬度试验方法标准号(不是全部) (37)第1章引言1.1金属材料硬度的定义硬度是金属材料力学性能中最常见的一个性能指标。
- 1、下载文档前请自行甄别文档内容的完整性,平台不提供额外的编辑、内容补充、找答案等附加服务。
- 2、"仅部分预览"的文档,不可在线预览部分如存在完整性等问题,可反馈申请退款(可完整预览的文档不适用该条件!)。
- 3、如文档侵犯您的权益,请联系客服反馈,我们会尽快为您处理(人工客服工作时间:9:00-18:30)。
金属热处理硬度通用检验标准
编制:
审核:
批准:
生效日期:
受控标识处:
分发号:
1.0 目的
明确并统一本公司自制及委外生产产品热处理硬度检验与测试的方法和依据,使产品质量得到有效控制,从而确保本公司向客户提供满意的产品。
2.0 范围
自制或委外生产的各类产品及金属热处理零件硬度的检验与测试。
3.0 抽样标准
抽样方法及判定标准,按照国标GB/T2828.1-2003规定的抽样程序及计数抽样表中之规定执行。
4.0 检验项目及方法
4.1 热处理件进厂时要查验供应商附送的相应的热处理检验记录,并确认记录内容是否符合相关技术要求。
4.2 硬度测试仪器的选用原则:
1)铸铁类产品(灰铁、球墨铸铁等),应选用布氏硬度计或维氏、里氏硬度计测试,但不可用洛氏或表面洛氏硬度计测试。
2)各类钢件可依产品特性选用适当的测试仪器:布氏、洛氏、维氏或里氏硬度计等。
3)薄壁件(厚度在2mm以下),及有色金属类应选用维氏、里氏或表面洛氏硬度计等,但不可用布氏硬度计测试。
4.3 表面打磨
为得到较为准确的测试结果,零件的测试部位均应进行表面打磨、抛光,表面光洁度应达到Ra1.6以上。
(成品件或不允许表面打磨的零件测试时,先不进行表面打磨直接在零件不影响外观表面检测。
若测试结果不合格时,则须进行破坏性打磨检测,若打磨后检测合格,则判定合格)
4.4 每一零件原则上应至少检测四点,取其平均值作为评价结果。
(零件较小或无法取多点除外)
4.5 当热处理零件表面产生脱碳现象时,须将零件表面磨深0.5~2mm后再进行检测。
4.6 表面热处理硬度检测:
4.6.1化学热处理
化学热处理是使工件表面渗入一种或几种化学元素的原子,从而改变工件表面的化学成分、组织和
性能。
化学热处理工件的主要技术参数是硬化层深度和表面硬度。
化学热处理工件的表面硬度检测与表面淬火热处理工件的硬度检测相近,都可以用维氏硬度计、表面洛氏硬度计或洛氏硬度计来检测,但是渗氮厚的厚度较薄,一般0.7mm以下时,就不能用洛氏硬度计检测。
4.6.2 表面淬火回火热处理
表面淬火回火热处理通常用感应加热或火焰加热的方式进行。
主要技术参数是表面硬度、局部硬度和有效硬化层深度。
维氏硬度计可以检测有效硬化深度超过0.05mm的各种表面硬化工件。
表面洛氏硬度计可以检测有效硬化深度超过0.1mm的各种表面硬化工件。
洛氏硬度计硬度检测有效硬化深度超过0.4mm的各种表面硬化工件。
当硬化层厚度在0.4~
0.8mm时,可采用HRA标尺,当硬化层厚度超过0.8mm时,可采用HRC标尺。
4.6.3 局部热处理
零件如果局部硬度要求较高,可用感应加热等方式进行局部淬火热处理,
局部热处理零件的硬度检测要在指定区域内进行(依工程图纸或技术要求)。
硬度检测仪器可采用洛氏硬度计,测试HRC硬度值,如热处理硬化层较浅,可采用表面洛氏硬度计(可参照表面淬火回火热处理检测方式)。
4.6.4 渗氮层等表面硬化层厚度检查方法
4.6.4.1 渗氮层等表面硬化层厚度检查采用硬度检测评定法,硬化层厚度用维氏硬度计或表面洛氏硬度计来检测。
检测时以逐层打磨检测的方法进行,当表面硬度降到550HV0.1那一层时,量测出打磨深度值即是表面硬化层厚度。
4.6.4.1.1 打磨方式:可以采用角向砂轮机手工打磨或采用工具磨床等机械研磨。
硬化层厚度在0.5mm以内的,以深度0.1mm/次逐次打磨检测。
硬化层厚度在1mm左右的,以深度0.3mm/次到0.6mm深后,再以0.1mm/次逐次打磨检测。
硬化层厚度在1.5mm左右的,以深度0.3mm/次到1.2mm深后,再以0.1mm/次逐次打磨检测。
硬化层厚度在1.5mm以上的,参考上述规则逐次打磨检测。
4.6.4.2 如对依硬度检测评定法的评定结果有异议或有特别要求时,可以委外进行金相检测评法评定。