烘窑投料操作1详解
窑投料时现场应做哪些工作
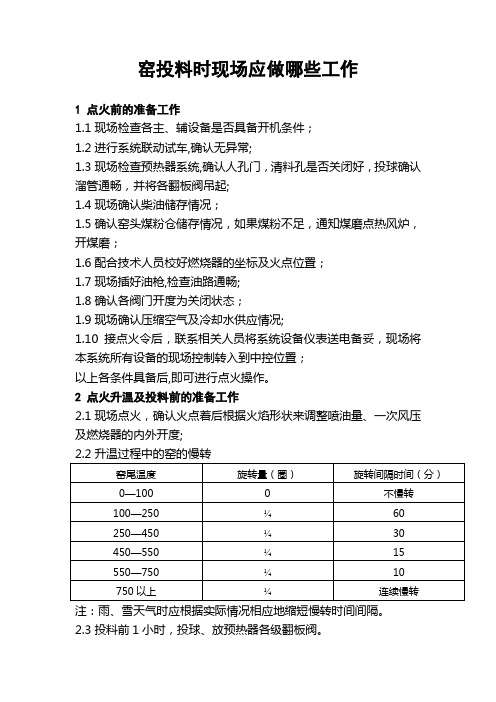
窑投料时现场应做哪些工作
1 点火前的准备工作
1.1现场检查各主、辅设备是否具备开机条件;
1.2进行系统联动试车,确认无异常;
1.3现场检查预热器系统,确认人孔门,清料孔是否关闭好,投球确认溜管通畅,并将各翻板阀吊起;
1.4现场确认柴油储存情况;
1.5确认窑头煤粉仓储存情况,如果煤粉不足,通知煤磨点热风炉,开煤磨;
1.6配合技术人员校好燃烧器的坐标及火点位置;
1.7现场插好油枪,检查油路通畅;
1.8确认各阀门开度为关闭状态;
1.9现场确认压缩空气及冷却水供应情况;
1.10接点火令后,联系相关人员将系统设备仪表送电备妥,现场将本系统所有设备的现场控制转入到中控位置;
以上各条件具备后,即可进行点火操作。
2 点火升温及投料前的准备工作
2.1现场点火,确认火点着后根据火焰形状来调整喷油量、一次风压及燃烧器的内外开度;
2.2升温过程中的窑的慢转
注:雨、雪天气时应根据实际情况相应地缩短慢转时间间隔。
2.3投料前1小时,投球、放预热器各级翻板阀。
2.4当窑尾温度达到750℃以上时,启动窑慢转传动装置,窑连续慢转,通知润滑班给轮带内加石墨锂基脂。
点火、升温、投料操作指南
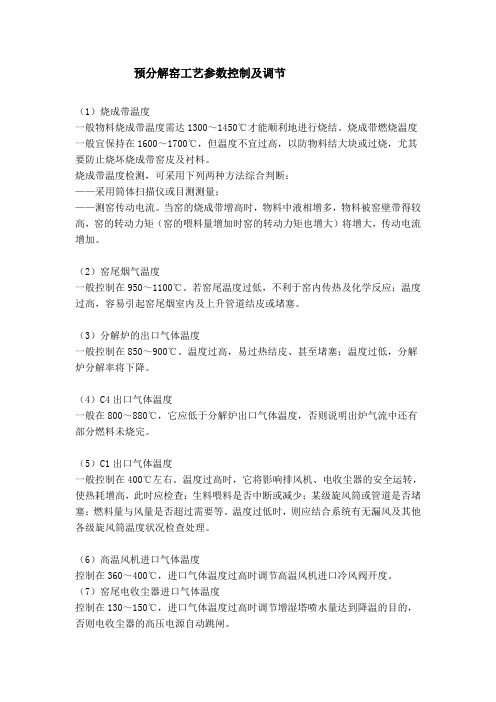
预分解窑工艺参数控制及调节(1)烧成带温度一般物料烧成带温度需达1300~1450℃才能顺利地进行烧结。
烧成带燃烧温度一般宜保持在1600~1700℃,但温度不宜过高,以防物料结大块或过烧,尤其要防止烧坏烧成带窑皮及衬料。
烧成带温度检测,可采用下列两种方法综合判断:——采用筒体扫描仪或目测测量;——测窑传动电流。
当窑的烧成带增高时,物料中液相增多,物料被窑壁带得较高,窑的转动力矩(窑的喂料量增加时窑的转动力矩也增大)将增大,传动电流增加。
(2)窑尾烟气温度一般控制在950~1100℃。
若窑尾温度过低,不利于窑内传热及化学反应;温度过高,容易引起窑尾烟室内及上升管道结皮或堵塞。
(3)分解炉的出口气体温度一般控制在850~900℃。
温度过高,易过热结皮、甚至堵塞;温度过低,分解炉分解率将下降。
(4)C4出口气体温度一般在800~880℃,它应低于分解炉出口气体温度,否则说明出炉气流中还有部分燃料未烧完。
(5)C1出口气体温度一般控制在400℃左右。
温度过高时,它将影响排风机、电收尘器的安全运转,使热耗增高,此时应检查:生料喂料是否中断或减少;某级旋风筒或管道是否堵塞;燃料量与风量是否超过需要等。
温度过低时,则应结合系统有无漏风及其他各级旋风筒温度状况检查处理。
(6)高温风机进口气体温度控制在360~400℃,进口气体温度过高时调节高温风机进口冷风阀开度。
(7)窑尾电收尘器进口气体温度控制在130~150℃,进口气体温度过高时调节增湿塔喷水量达到降温的目的,否则电收尘器的高压电源自动跳闸。
(8)预热器系统的负压——当C1出口负压升高时,首先检查旋风筒是否堵塞,如属正常,则检查高温风机转速是否过高或进口阀门开度过大。
——当C1出口负压降低时,首先检查喂料是否正常,如属正常,则检查高温风机转速是否降低或进口阀门开度偏小。
——当发生粘结、堵塞时,其粘结堵塞部位与高温风机间的负压有所增高,而窑与粘堵部位间的气温升高、负压值下降。
窑投料操作程序
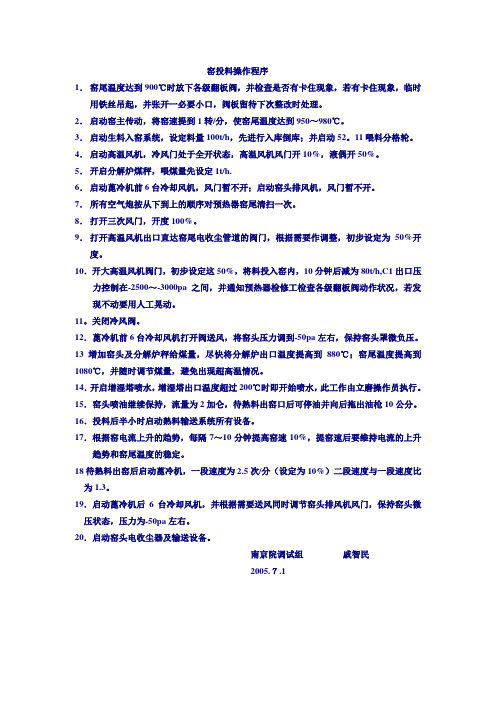
窑投料操作程序1.窑尾温度达到900℃时放下各级翻板阀,并检查是否有卡住现象,若有卡住现象,临时用铁丝吊起,并张开一必要小口,阀板留待下次整改时处理。
2.启动窑主传动,将窑速提到1转/分,使窑尾温度达到950~980℃。
3.启动生料入窑系统,设定料量100t/h,先进行入库倒库;并启动52。
11喂料分格轮。
4.启动高温风机,冷风门处于全开状态,高温风机风门开10%,液偶开50%。
5.开启分解炉煤秤,喂煤量先设定1t/h.6.启动蓖冷机前6台冷却风机,风门暂不开;启动窑头排风机,风门暂不开。
7.所有空气炮按从下到上的顺序对预热器窑尾清扫一次。
8.打开三次风门,开度100%。
9.打开高温风机出口直达窑尾电收尘管道的阀门,根据需要作调整,初步设定为50%开度。
10.开大高温风机阀门,初步设定这50%,将料投入窑内,10分钟后减为80t/h,C1出口压力控制在-2500~-3000pa之间,并通知预热器检修工检查各级翻板阀动作状况,若发现不动要用人工晃动。
11。
关闭冷风阀。
12.蓖冷机前6台冷却风机打开阀送风,将窑头压力调到-50pa左右,保持窑头罩微负压。
13增加窑头及分解炉秤给煤量,尽快将分解炉出口温度提高到880℃;窑尾温度提高到1080℃,并随时调节煤量,避免出现超高温情况。
14.开启增湿塔喷水,增湿塔出口温度超过200℃时即开始喷水,此工作由立磨操作员执行。
15.窑头喷油继续保持,流量为2加仑,待熟料出窑口后可停油并向后拖出油枪10公分。
16.投料后半小时启动熟料输送系统所有设备。
17.根据窑电流上升的趋势,每隔7~10分钟提高窑速10%,提窑速后要维持电流的上升趋势和窑尾温度的稳定。
18待熟料出窑后启动蓖冷机,一段速度为2.5次/分(设定为10%)二段速度与一段速度比为1.3。
19.启动蓖冷机后6台冷却风机,并根据需要送风同时调节窑头排风机风门,保持窑头微压状态,压力为-50pa左右。
20.启动窑头电收尘器及输送设备。
新型干法窑投料操作的注意事项
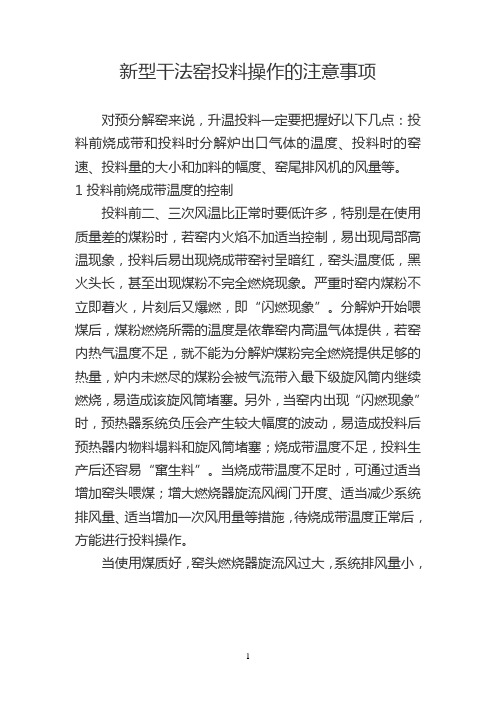
新型干法窑投料操作的注意事项对预分解窑来说,升温投料一定要把握好以下几点:投料前烧成带和投料时分解炉出口气体的温度、投料时的窑速、投料量的大小和加料的幅度、窑尾排风机的风量等。
1 投料前烧成带温度的控制投料前二、三次风温比正常时要低许多,特别是在使用质量差的煤粉时,若窑内火焰不加适当控制,易出现局部高温现象,投料后易出现烧成带窑衬呈暗红,窑头温度低,黑火头长,甚至出现煤粉不完全燃烧现象。
严重时窑内煤粉不立即着火,片刻后又爆燃,即“闪燃现象”。
分解炉开始喂煤后,煤粉燃烧所需的温度是依靠窑内高温气体提供,若窑内热气温度不足,就不能为分解炉煤粉完全燃烧提供足够的热量,炉内未燃尽的煤粉会被气流带入最下级旋风筒内继续燃烧,易造成该旋风筒堵塞。
另外,当窑内出现“闪燃现象”时,预热器系统负压会产生较大幅度的波动,易造成投料后预热器内物料塌料和旋风筒堵塞;烧成带温度不足,投料生产后还容易“窜生料”。
当烧成带温度不足时,可通过适当增加窑头喂煤;增大燃烧器旋流风阀门开度、适当减少系统排风量、适当增加一次风用量等措施,待烧成带温度正常后,方能进行投料操作。
当使用煤质好,窑头燃烧器旋流风过大,系统排风量小,窑头喂煤量大时,则易形成烧成带温度过高,且窑头温度集中。
透过看火镜,火焰白亮刺眼,窑衬白亮,这时很容易烧坏前窑衬,造成红窑事故。
当出现上述现象时,应立即较大幅度减少窑头喂煤,增加系统排风量,根据情况适当减少一次风量,调整内外风比例,加大外风,减少内风,待烧成带温度、亮度适中,窑尾及预热器温度适当后,再进行投料操作。
2 投料时,分解炉出口气体的温度的控制投料前分解炉喂煤量一般控制在正常水平的20%~30%,炉内煤粉着火燃烧温度由窑内高温气体提供,燃烧所需氧气主要由三次风提供。
煤粉燃烧后分解炉内温度逐渐上升,当分解炉出口气体温度或最低级旋风筒出口气体温度上升到某一温度时,就应投料。
投料时分解炉出口气体的温度我们称为“投料温度”,此温度比正常生产时分解炉出口气体的温度低,这有几方面的原因:(1)开始投料后,生料从均化库下计量仓卸出,经输送设备、预热器、旋风筒,到分解炉,尚需要一段时间(约5~6min)。
烘窑操作办法和要点
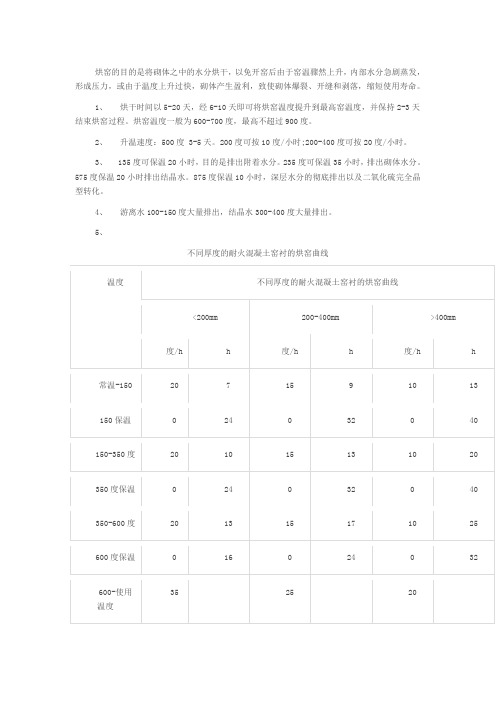
烘窑的目的是将砌体之中的水分烘干,以免开窑后由于窑温骤然上升,内部水分急剧蒸发,
形成压力,或由于温度上升过快,砌体产生盈利,致使砌体爆裂、开缝和剥落,缩短使用寿命。
1、烘干时间以5-20天,经6-10天即可将烘窑温度提升到最高窑温度,并保持2-3天结
束烘窑过程。
烘窑温度一般为600-700度,最高不超过900度。
2、升温速度:500度 3-5天。
200度可按10度/小时;200-400度可按20度/小时。
3、 135度可保温20小时,目的是排出附着水分。
235度可保温35小时,排出砌体水分。
575度保温20小时排出结晶水。
875度保温10小时,深层水分的彻底排出以及二氧化硫完全晶
型转化。
4、游离水100-150度大量排出,结晶水300-400度大量排出。
5、
不同厚度的耐火混凝土窑衬的烘窑曲线
温度不同厚度的耐火混凝土窑衬的烘窑曲线
<200mm 200-400mm >400mm
度/h h 度/h h 度/h h 常温-150 20 7 15 9 10 13 150保温0 24 0 32 0 40 150-350度20 10 15 13 10 20 350度保温0 24 0 32 0 40 350-600度20 13 15 17 10 25 600度保温0 16 0 24 0 32
35 25 20
600-使用
温度。
干燥窑操作规程讲解

干燥窑生产岗位操作规程一、湿矿下料岗位1.必须清楚岗位职责,配合指导装载机、挖掘机上料,确保干燥窑正常用料需求。
2.根据中控指令,增减料,根据生产要求指示装载机按时定量混合上料。
3.及时清除矿料中混合的铁器、杂物,定时清理仓壁上粘结物料,保证供料畅通充足,保持料仓及周边无散料、无铁器、无杂物。
4.料仓中存料保持在2/3左右,不可过多或少,过多则粘仓不好处理,过少则砸坏皮带或托辊,发生皮带压死滚筒打滑时,换用另一台定量给料机供应并报告中控或班长,清理完后可恢复使用,严禁无料运行。
5.紧急情况发生时必须急停定量给料机或1#输送带,报告中控和班长,迅速处理完毕后,确认无事方可开机。
6.经常与中控、班长、挖机、装载机联系,报告岗位上出现的问题,提出整改方案,确保生产正常运行。
二、1#皮带岗位工1.努力掌握操作技能,认真干好本职工作;检查分料阀有无粘结,听从中控安排,合理分料。
2.定时观察调整皮带头轮,尾轮,涨紧轮皮带处有无跑偏现象,检查各部位托辊,滚筒有无损坏、异响、刮蹭皮带现象,不能处理的及时上报中控或班长,联系机修工加以调整。
3.及时清理各部位漏料及滚筒处粘料,观察皮带接头是否完好,下料口有无粘结,加强与中控,班长及上下道工序的联系,确保皮带运行正常。
4.在设备运转情况下禁止拆卸配件维修,开停机要与中控密切配合,在检查输送设备时,要等物料走空后再停机,开机前要检查设备,现场无维修人员和闲杂人员时再开机。
5.检查皮带机是否开股撕裂。
跑偏的情况;检查下料槽内有无杂物,皮带罩挡皮是否完好,爬坡处及临时下料口矿料通过是否正常,严禁用钢管、钢筋、钢板、铁锹等调整皮带,阻挡漏料;检查过程中如发现问题及时向班长或中控汇报。
6.遇到紧急情况时先停机后报告,地坑内可急拉拉绳开关或尾轮处断电器,也可呼叫下料岗位急停,决不允许损坏皮带、割破皮带,影响正常运行的情况发生。
7.及时清理涨紧轮配重板下面的积料,不能让料堆起来,托起配重影响皮带运行,需调整皮带跑偏时可拉紧或松动轮下葫芦即可。
xxxx水泥有限公司点火烘窑操作规程
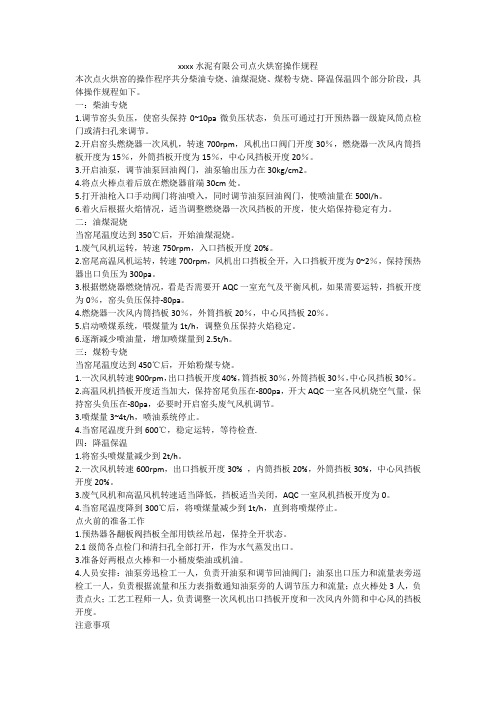
xxxx水泥有限公司点火烘窑操作规程本次点火烘窑的操作程序共分柴油专烧、油煤混烧、煤粉专烧、降温保温四个部分阶段,具体操作规程如下。
一:柴油专烧1.调节窑头负压,使窑头保持0~10pa微负压状态,负压可通过打开预热器一级旋风筒点检门或清扫孔来调节。
2.开启窑头燃烧器一次风机,转速700rpm,风机出口阀门开度30%,燃烧器一次风内筒挡板开度为15%,外筒挡板开度为15%,中心风挡板开度20%。
3.开启油泵,调节油泵回油阀门,油泵输出压力在30kg/cm2。
4.将点火棒点着后放在燃烧器前端30cm处。
5.打开油枪入口手动阀门将油喷入,同时调节油泵回油阀门,使喷油量在500l/h。
6.着火后根据火焰情况,适当调整燃烧器一次风挡板的开度,使火焰保持稳定有力。
二:油煤混烧当窑尾温度达到350℃后,开始油煤混烧。
1.废气风机运转,转速750rpm,入口挡板开度20%。
2.窑尾高温风机运转,转速700rpm,风机出口挡板全开,入口挡板开度为0~2%,保持预热器出口负压为300pa。
3.根据燃烧器燃烧情况,看是否需要开AQC一室充气及平衡风机,如果需要运转,挡板开度为0%,窑头负压保持-80pa。
4.燃烧器一次风内筒挡板30%,外筒挡板20%,中心风挡板20%。
5.启动喷煤系统,喂煤量为1t/h,调整负压保持火焰稳定。
6.逐渐减少喷油量,增加喷煤量到2.5t/h。
三:煤粉专烧当窑尾温度达到450℃后,开始粉煤专烧。
1.一次风机转速900rpm,出口挡板开度40%,筒挡板30%,外筒挡板30%,中心风挡板30%。
2.高温风机挡板开度适当加大,保持窑尾负压在-800pa,开大AQC一室各风机烧空气量,保持窑头负压在-80pa,必要时开启窑头废气风机调节。
3.喷煤量3~4t/h,喷油系统停止。
4.当窑尾温度升到600℃,稳定运转,等待检查.四:降温保温1.将窑头喷煤量减少到2t/h。
2.一次风机转速600rpm,出口挡板开度30% ,内筒挡板20%,外筒挡板30%,中心风挡板开度20%。
烘窑投料操作1
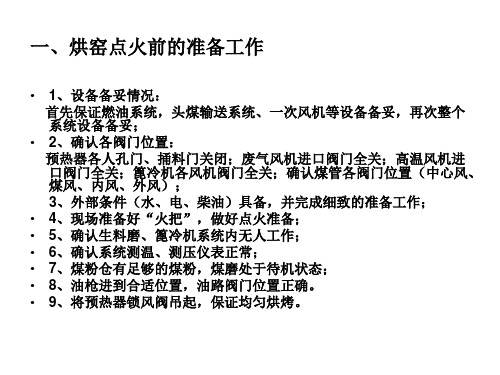
3、 设定喂料量150-200吨/时进行投料。 • 4、投料时,注意控制几个主要参数: C5出口温度~860℃,分解炉出口温度880~900℃,C1出口温度 <400℃,烟室温950~1050℃,窑速1-1.2 rpm。 投料后 • (1)当观察到C1出口温度有下降趋势,增加分解炉喂煤量,使分解炉 出口温度不低于870℃。不超过900℃。长时间低温控制会造成跑黄 料,温度高易造成预热器烧结性堵塞。 • (2)喂料后生料从一级到入窑大约只需30秒左右,投料初期要密切注 意预热器,注意各级翻板闪动情况。由于温度不稳定,各级翻板应专 人看管,人工帮助卸料。在投料后的一小时内要严密注意预热器各翻 板阀闪动情况。设专人看管,及时调整重锤或人工帮助排料。(物料 进入某一级,该级的出口温度会下降,锥体压力和出口压力会升高)
• 5、随着燃料增大,尾温沿设定趋势上升,当燃烧空气不足或窑头负 压较高时,(窑前火焰燃烧有刚度但烟囱帽冒黑烟)启动篦冷机G13 平衡风机,逐步加大G13平衡风机进口阀门开度。随着燃料量的增加, 当平衡风机进口阀门开至60%,仍感风量不足时,逐步启动G11、 G16两台固定篦床充气风机,增加入窑风量。 • 6、窑头、窑尾护口铁冷却风机应在烘窑四小时后开起(350℃)前 25米筒体超过350℃及时开筒体冷却风机。 • 7、分解炉出口200℃时 ,开启窑尾一次风机或尾煤罗茨风机,保护 火嘴和软连接。 • 8、当一级出口温度上升到70℃时,开启入窑分格轮及入窑斜槽风 机. 。 • 注意事项: • 1、由于窑内温度较低,煤粉燃烧不稳定,操作不良会造成爆燃回火 危险,窑头看火操作防止烧伤烫伤。 • 2、升温过程中保证火焰形状,遵循“慢升温不回头”的原则。 • 3、根据火焰燃烧状况,逐步加大喂煤量,防止尾温剧升。 • 4、防止筒体温度局部过热。 • 5、窑内温度较高再行点火时,应先翻窑后给煤,且窑门罩前不得留 人,以防回火伤人。
- 1、下载文档前请自行甄别文档内容的完整性,平台不提供额外的编辑、内容补充、找答案等附加服务。
- 2、"仅部分预览"的文档,不可在线预览部分如存在完整性等问题,可反馈申请退款(可完整预览的文档不适用该条件!)。
- 3、如文档侵犯您的权益,请联系客服反馈,我们会尽快为您处理(人工客服工作时间:9:00-18:30)。
三、升温(按回转窑升温制度升温)
当尾温>350℃时: • 1、根据窑前火焰燃烧情况,适时开启窑头喂煤,给定0.5t/h,根据 窑前火焰燃烧状况慢慢加大喷煤量。小技巧:在开启头煤罗茨风机前, 先点燃火把放在火嘴头部下端助燃,以防止煤风将火焰吹灭;在开头 煤称前先将头煤罗茨风机外放一部分风,但不能太多,防止风量太小 煤粉沉积在管道中,随着头煤量的加大(2吨后)逐渐将外放风关闭, 要间隔缓慢的关闭,如果关的太急易造成头煤跑煤严重。 • 2、不断调整一次风量及点火烟囱帽开度,保持火焰稳定燃烧,不灭 火,不返火。如果火焰很难稳定,可控制窑头罩微正压,局部烧热后 再控制为负压。 • 3、启动回转窑主减速机稀油站,按转窑制度,现场用慢驱动转窑。 升温期间要定期检查回转窑托轮,减速机、大齿圈润滑状况。 • 4、随烟室温度升高,要逐渐减油加煤,调整一次风量、点火烟囱帽 开度,保持火焰形状,避免局部高温以及窑尾温度不能大起大落。 (烟囱帽高度,以点火孔微负压即可)
3、 设定喂料量150-200吨/时进行投料。 • 4、投料时,注意控制几个主要参数: C5出口温度~860℃,分解炉出口温度880~900℃,C1出口温度 <400℃,烟室温950~1050℃,窑速1-1.2 rpm。 投料后 • (1)当观察到C1出口温度有下降趋势,增加分解炉喂煤量,使分解炉 出口温度不低于870℃。不超过900℃。长时间低温控制会造成跑黄 料,温度高易造成预热器烧结性堵塞。 • (2)喂料后生料从一级到入窑大约只需30秒左右,投料初期要密切注 意预热器,注意各级翻板闪动情况。由于温度不稳定,各级翻板应专 人看管,人工帮助卸料。在投料后的一小时内要严密注意预热器各翻 板阀闪动情况。设专人看管,及时调整重锤或人工帮助排料。(物料 进入某一级,该级的出口温度会下降,锥体压力和出口压力会升高)
• 5、随着燃料增大,尾温沿设定趋势上升,当燃烧空气不足或窑头负 压较高时,(窑前火焰燃烧有刚度但烟囱帽冒黑烟)启动篦冷机G13 平衡风机,逐步加大G13平衡风机进口阀门开度。随着燃料量的增加, 当平衡风机进口阀门开至60%,仍感风量不足时,逐步启动G11、 G16两台固定篦床充气风机,增加入窑风量。 • 6、窑头、窑尾护口铁冷却风机应在烘窑四小时后开起(350℃)前 25米筒体超过350℃及时开筒体冷却风机。 • 7、分解炉出口200℃时 ,开启窑尾一次风机或尾煤罗茨风机,保护 火嘴和软连接。 • 8、当一级出口温度上升到70℃时,开启入窑分格轮及入窑斜槽风 机. 。 • 注意事项: • 1、由于窑内温度较低,煤粉燃烧不稳定,操作不良会造成爆燃回火 危险,窑头看火操作防止烧伤烫伤。 • 2、升温过程中保证火焰形状,遵循“慢升温不回头”的原则。 • 3、根据火焰燃烧状况,逐步加大喂煤量,防止尾温剧升。 • 4、防止筒体温度局部过热。 • 5、窑内温度较高再行点火时,应先翻窑后给煤,且窑门罩前不得留 人,以防回火伤人。
回转窑升温转窑制度
窑尾温度(℃) 旋转量(度) 旋转间隔 时间(分 ) 不转
0—100
0
100—250
250—450 450—550 550—750 750以上
90
90 90 90
60
30 15 10 连续转
当尾温(烟室)>600℃时: • 1、当窑尾预热器点火烟囱不能满足窑头负压的调整,可启动窑尾袋 收尘排风机,打开入口阀门及高温风机入口阀门全开,关闭去生料磨 的热风阀门及其排风机出口阀门。确认去往发电的主阀门关闭,旁路 阀门打开。 • 2、预热器各级翻板阀要人工活动,间隔1小时,以防受热变形卡死。 • 3、检查系统的各点温度是否正常。 • 4、根据筒体温度,应适时开启筒体冷却风机。 • 5、废气风机开启后,根据负压情况及时通知预热器岗位检查。C5锥 体易卡结皮,应勤检查处理. • 当尾温>750℃时: • 1、窑的辅助传动连续转窑。液压挡轮启动. • 2、依次启动各组设备 – 熟料输送组(G5、G9、G10、G40、G6拉链机等) – 生料入窑组(入窑分格轮、斜槽风机、提升机. ) – 生料库供料组(提升机、斜槽、收尘等) – 窑尾各回灰组(绞刀、分格轮、拉链机等)
当尾温>900 ℃时: • 1、开启窑尾废气风机、窑头排风机。从篦冷机风机G13逐一向G25 开启。窑头负压保持-20—-100Pa。 • 2、脱开窑盘车,以0.5转/分启动窑主机。 • 3、以200转/分开启高温风机,调节高温风机转速,入口阀门全开。 高温风机和废气风机两者要同步,缓慢调节保证增湿塔出口负压300—-500Pa • 4、开启窑尾喂煤转子秤,开始喂煤时喂煤量1~1.5t/h ,注意分解 炉出口温升情况,如长时间温度不升时,要停止喂煤,进行检查。 • 5、开启窑尾空气炮组。 • 6、再次确认系统各设备正常,各温度压力测点是否正常。 四、投料 • 1、高温风机转速设定600 rpm ,烟囱 帽全关,入窑斜槽收尘管蝶 阀全开。 • 2 、一级筒出口负压在-2000--2500Pa,窑头喂煤量给定平时的5080%,并控制一次风压力,保持火焰稳定。
一、烘窑点火前的准备工作
• 1、设备备妥情况: 首先保证燃油系统,头煤输送系统、一次风机等设备备妥,再次整个 系统设备备妥; • 2、确认各阀门位置: 预热器各人孔门、捅料门关闭;废气风机进口阀门全关;高温风机进 口阀门全关;篦冷机各风机阀门全关;确认煤管各阀门位置(中心风、 煤风、内风、外风); 3、外部条件(水、电、柴油)具备,并完成细致的准备工作; • 4、现场准备好“火把”,做好点火准备; • 5、确认生料磨、篦冷机系统内无人工作; • 6、确认系统测温、测压仪表正常; • 7、煤粉仓有足够的煤粉,煤磨处于待机状态; • 8、油枪进起,保证均匀烘烤。
二、烘窑点火
• 1、首先将点火烟囱帽开至一定的开度,保证窑前微负压(0~20Pa)。 • 2、开启一次风机调节风量 。 • 3、用一根5—6m长的钢管,端部缠上油棉纱,点燃后自窑门罩伸到喷油 管端部。 • 4、立即开启燃油系统,调节油压,引燃雾化油。 注意:使油火焰柔和不发飘即可。 • 注意事项: (1)先点燃后喷油,否则很容易造成返火伤人。 (2)防止柴油溅至耐火砖表面。大修点火前,应先在前10米耐火砖表面铺 上一层窑灰等物品。 (3)合理用风,保证火焰稳定。 一次风量的调节原则:风量小则火焰非 常软,燃烧不完全;风量大则火焰非常急并伴有“刷刷”的声音,易灭。 (4)篦冷机前5排固定蓖板上也应铺上一层熟料,防止煤灰等熔融性物品堵 塞篦缝及减少热辐射对篦板的损害。操作员在点火前应到现场了解窑内 和篦冷机内存有多少物料,以估计多长时间后需要推一推一段。