重大生产安全事故隐患判定标准(试行)
重大事故隐患判定标准

国家制定的各行业重大事故隐患判定标准一、化工和危险化学品生产经营单位重大生产安全事故隐患判定标准(试行)依据有关法律法规、部门规章和国家标准,以下情形应当判定为重大事故隐患:(一)危险化学品生产、经营单位主要负责人和安全生产管理人员未依法经考核合格。
(二)特种作业人员未持证上岗。
(三)涉及“两重点一重大”的生产装置、储存设施外部安全防护距离不符合国家标准要求。
(四)涉及重点监管危险化工工艺的装置未实现自动化控制,系统未实现紧急停车功能,装备的自动化控制系统、紧急停车系统未投入使用。
(五)构成一级、二级重大危险源的危险化学品罐区未实现紧急切断功能;涉及毒性气体、液化气体、剧毒液体的一级、二级重大危险源的危险化学品罐区未配备独立的安全仪表系统。
(六)全压力式液化烃储罐未按国家标准设置注水措施。
(七)液化烃、液氨、液氯等易燃易爆、有毒有害液化气体的充装未使用万向管道充装系统。
(八)光气、氯气等剧毒气体及硫化氢气体管道穿越除厂区(包括化工园区、工业园区)外的公共区域。
(九)地区架空电力线路穿越生产区且不符合国家标准要求。
(十)在役化工装置未经正规设计且未进行安全设计诊断。
(十一)使用淘汰落后安全技术工艺、设备目录列出的工艺、设备。
(十二)涉及可燃和有毒有害气体泄漏的场所未按国家标准设置检测报警装置,爆炸危险场所未按国家标准安装使用防爆电气设备。
(十三)控制室或机柜间面向具有火灾、爆炸危险性装置一侧不满足国家标准关于防火防爆的要求。
(十四)化工生产装置未按国家标准要求设置双重电源供电,自动化控制系统未设置不间断电源。
(十五)安全阀、爆破片等安全附件未正常投用。
(十六)未建立与岗位相匹配的全员安全生产责任制或者未制定实施生产安全事故隐患排查治理制度。
(十七)未制定操作规程和工艺控制指标。
(十八)未按照国家标准制定动火、进入受限空间等特殊作业管理制度,或者制度未有效执行。
(十九)新开发的危险化学品生产工艺未经小试、中试、工业化试验直接进行工业化生产;国内首次使用的化工工艺未经过省级人民政府有关部门组织的安全可靠性论证;新建装置未制定试生产方案投料开车;精细化工企业未按规范性文件要求开展反应安全风险评估。
重大事故隐患判定标准
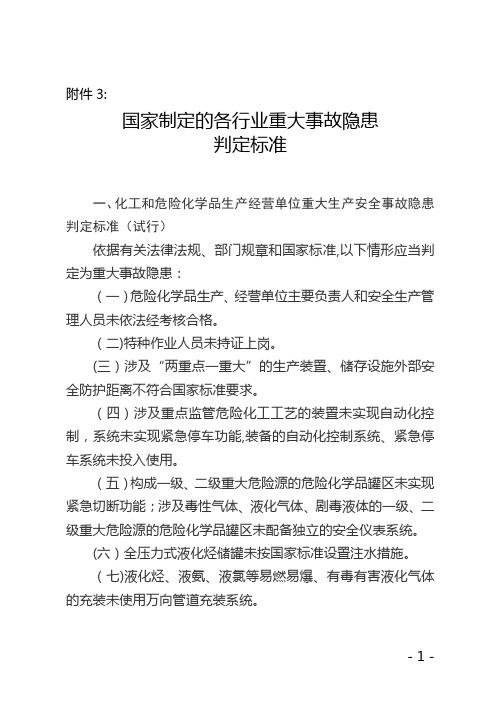
附件3:国家制定的各行业重大事故隐患判定标准一、化工和危险化学品生产经营单位重大生产安全事故隐患判定标准(试行)依据有关法律法规、部门规章和国家标准,以下情形应当判定为重大事故隐患:(一)危险化学品生产、经营单位主要负责人和安全生产管理人员未依法经考核合格。
(二)特种作业人员未持证上岗。
(三)涉及“两重点一重大”的生产装置、储存设施外部安全防护距离不符合国家标准要求。
(四)涉及重点监管危险化工工艺的装置未实现自动化控制,系统未实现紧急停车功能,装备的自动化控制系统、紧急停车系统未投入使用。
(五)构成一级、二级重大危险源的危险化学品罐区未实现紧急切断功能;涉及毒性气体、液化气体、剧毒液体的一级、二级重大危险源的危险化学品罐区未配备独立的安全仪表系统。
(六)全压力式液化烃储罐未按国家标准设置注水措施。
(七)液化烃、液氨、液氯等易燃易爆、有毒有害液化气体的充装未使用万向管道充装系统。
(八)光气、氯气等剧毒气体及硫化氢气体管道穿越除厂区(包括化工园区、工业园区)外的公共区域。
(九)地区架空电力线路穿越生产区且不符合国家标准要求。
(十)在役化工装置未经正规设计且未进行安全设计诊断。
(十一)使用淘汰落后安全技术工艺、设备目录列出的工艺、设备。
(十二)涉及可燃和有毒有害气体泄漏的场所未按国家标准设置检测报警装置,爆炸危险场所未按国家标准安装使用防爆电气设备.(十三)控制室或机柜间面向具有火灾、爆炸危险性装置一侧不满足国家标准关于防火防爆的要求。
(十四)化工生产装置未按国家标准要求设置双重电源供电,自动化控制系统未设置不间断电源。
(十五)安全阀、爆破片等安全附件未正常投用.(十六)未建立与岗位相匹配的全员安全生产责任制或者未制定实施生产安全事故隐患排查治理制度。
(十七)未制定操作规程和工艺控制指标。
(十八)未按照国家标准制定动火、进入受限空间等特殊作业管理制度,或者制度未有效执行。
(十九)新开发的危险化学品生产工艺未经小试、中试、工业化试验直接进行工业化生产;国内首次使用的化工工艺未经过省级人民政府有关部门组织的安全可靠性论证;新建装置未制定试生产方案投料开车;精细化工企业未按规范性文件要求开展反应安全风险评估.(二十)未按国家标准分区分类储存危险化学品,超量、超品种储存危险化学品,相互禁配物质混放混存。
化工和危险化学品生产经营单位重大生产安全事故隐患判定标准

化工和危险化学品生产经营单位重大生产安全事故隐患判定标准化工和危险化学品生产经营单位是指从事化学工艺过程、原料、副产品、产品仓储以及配送等与化工和危险化学品生产经营活动有关的单位。
为了保障生产安全,防止重大生产安全事故的发生,国家制定了《化工和危险化学品生产经营单位重大生产安全事故隐患判定标准(试行)》。
一、重大生产安全事故隐患判定的基本原则1.生产过程:生产过程中存在的隐患包括工艺缺陷、操作不当、设备老化、维护不及时等问题。
2.现场管理:现场管理方面的隐患主要涉及消防管理、安全设施配备、应急预案和演练等方面。
3.安全环境:安全环境方面的隐患包括场址选址不当、环境治理不到位、周边安全隐患等问题。
4.其他因素:除了生产过程、现场管理和安全环境外,还应考虑其他因素对重大生产安全事故的影响,如管理体系、技术水平、人员素质等。
二、重大生产安全事故隐患判定的主要内容1.从事化学工艺过程、原料、副产品、产品仓储以及配送等与化工和危险化学品生产经营活动有关的单位,应严格按照标准规范进行隐患判定。
2.隐患判定应包括生产过程、现场管理和安全环境等方面的隐患。
3.生产过程方面的隐患判定应包括以下内容:a.工艺缺陷:包括工艺路线、工艺设施等方面的缺陷,如存在工艺不合理、设备不安全、操作不当等问题。
b.原料缺陷:包括原料品质、储存和使用等方面的缺陷,如存在原料不规范、储存条件差、使用方法错误等问题。
c.副产品缺陷:包括副产品的处理和处置等方面的缺陷,如存在对副产品尸体不当、处置方法不正确等问题。
d.产品仓储缺陷:包括产品储存和保管等方面的缺陷,如存在储存条件不合理、包装质量差等问题。
e.配送缺陷:包括产品配送和运输等方面的缺陷,如存在运输工具不合格、运输方式不安全等问题。
4.现场管理方面的隐患判定应包括以下内容:a.消防管理:包括消防设施、灭火器材、消防通道等方面的管理,如存在消防设施损坏、灭火器材不足、消防通道堵塞等问题。
重大生产安全事故隐患判定标准(试行)

化工和危险化学品生产经营单位重大生产安全事故隐患判定标准(试行)安监总管三〔2017〕121号依据有关法律法规、部门规章和国家标准,以下情形应当判定为重大事故隐患:一、危险化学品生产、经营单位主要负责人和安全生产管理人员未依法经考核合格。
二、特种作业人员未持证上岗。
三、涉及“两重点一重大”de生产装置、储存设施外部安全防护距离不符合国家标准要求。
四、涉及重点监管危险化工工艺de装置未实现自动化控制,系统未实现紧急停车功能,装备de自动化控制系统、紧急停车系统未投入使用。
五、构成一级、二级重大危险源de危险化学品罐区未实现紧急切断功能;涉及毒性气体、液化气体、剧毒液体de一级、二级重大危险源de危险化学品罐区未配备独立de安全仪表系统。
六、全压力式液化烃储罐未按国家标准设置注水措施。
七、液化烃、液氨、液氯等易燃易爆、有毒有害液化气体de充装未使用万向管道充装系统。
八、光气、氯气等剧毒气体及硫化氢气体管道穿越除厂区(包括化工园区、工业园区)外de公共区域。
九、地区架空电力线路穿越生产区且不符合国家标准要求。
十、在役化工装置未经正规设计且未进行安全设计诊断。
十一、使用淘汰落后安全技术工艺、设备目录列出de工艺、设备。
十二、涉及可燃和有毒有害气体泄漏de场所未按国家标准设置检测报警装置,爆炸危险场所未按国家标准安装使用防爆电气设备。
十三、控制室或机柜间面向具有火灾、爆炸危险性装置一侧不满足国家标准关于防火防爆de要求。
十四、化工生产装置未按国家标准要求设置双重电源供电,自动化控制系统未设置不间断电源。
十五、安全阀、爆破片等安全附件未正常投用。
十六、未建立与岗位相匹配de全员安全生产责任制或者未制定实施生产安全事故隐患排查治理制度。
十七、未制定操作规程和工艺控制指标。
十八、未按照国家标准制定动火、进入受限空间等特殊作业管理制度,或者制度未有效执行。
十九、新开发de危险化学品生产工艺未经小试、中试、工业化试验直接进行工业化生产;国内首次使用de化工工艺未经过省级人民政府有关部门组织de安全可靠性论证;新建装置未制定试生产方案投料开车;精细化工企业未按规范性文件要求开展反应安全风险评估。
化工和危险化学品生产经营单位二十条重大生产安全事故隐患判定标准
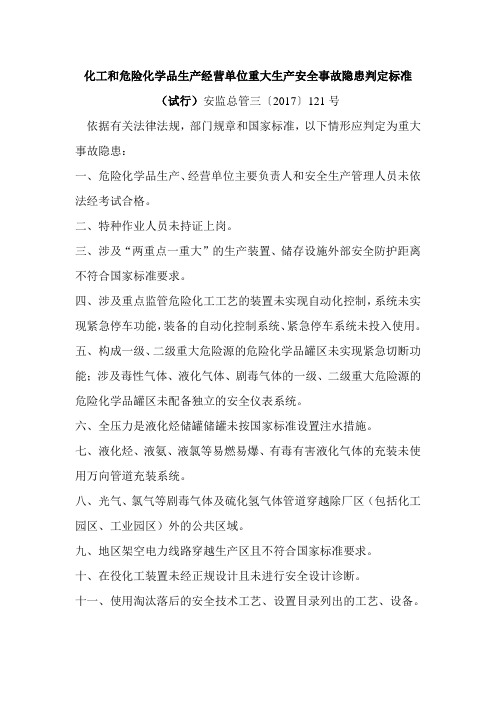
化工和危险化学品生产经营单位重大生产安全事故隐患判定标准(试行)安监总管三〔2017〕121号依据有关法律法规,部门规章和国家标准,以下情形应判定为重大事故隐患:一、危险化学品生产、经营单位主要负责人和安全生产管理人员未依法经考试合格。
二、特种作业人员未持证上岗。
三、涉及“两重点一重大”的生产装置、储存设施外部安全防护距离不符合国家标准要求。
四、涉及重点监管危险化工工艺的装置未实现自动化控制,系统未实现紧急停车功能,装备的自动化控制系统、紧急停车系统未投入使用。
五、构成一级、二级重大危险源的危险化学品罐区未实现紧急切断功能;涉及毒性气体、液化气体、剧毒气体的一级、二级重大危险源的危险化学品罐区未配备独立的安全仪表系统。
六、全压力是液化烃储罐储罐未按国家标准设置注水措施。
七、液化烃、液氨、液氯等易燃易爆、有毒有害液化气体的充装未使用万向管道充装系统。
八、光气、氯气等剧毒气体及硫化氢气体管道穿越除厂区(包括化工园区、工业园区)外的公共区域。
九、地区架空电力线路穿越生产区且不符合国家标准要求。
十、在役化工装置未经正规设计且未进行安全设计诊断。
十一、使用淘汰落后的安全技术工艺、设置目录列出的工艺、设备。
十二、涉及可燃和有毒有害气体泄漏的场所未按国家标准设置检测报警装置,爆炸危险场所未按国家标准安装使用防爆电气设备。
十三、控制室或机柜间面向具有火灾、爆炸危险性装置一侧不满足国家标准关于防火防爆的要求。
十四、化工生产装置未按国家标准要求设置双重电源供电,自动化控制系统未设置不间断电源。
十五、安全阀、爆破片等安全附件未正常投用。
十六、未建立与岗位相匹配的全员安全生产责任制或者未制定实施生产安全事故隐患排查治理制度。
十七、未指定操作规程和工艺控制指标。
十八、未按照国家标准制定动火、进入受限空间等特殊作业管理制度,或者制度未有效执行。
十九、新开发的危险化学品生产工艺未经小试、中试、工业化试验直接进行工业化生产;国内首次使用的化工工艺未经省级人民政府有关部门组织的安全可靠性认证;新建装置未制定试生产方案投料开车;精细化工企业未按规范性文件要求开展反应安全风险评估。
化工和危险化学品生产经营单位重大生产安全事故隐患判定标准

化工和危险化学品生产经营单位重大生产安全事故隐患判定标准(试行)依据有关法律法规、部门规章和国家标准,以下情形应当判定为重大事故隐患:一、危险化学品生产、经营单位主要负责人和安全生产管理人员未依法经考核合格。
二、特种作业人员未持证上岗。
三、涉及“两重点一重大”的生产装置、储存设施外部安全防护距离不符合国家标准要求。
四、涉及重点监管危险化工工艺的装置未实现自动化控制,系统未实现紧急停车功能,装备的自动化控制系统、紧急停车系统未投入使用。
五、构成一级、二级重大危险源的危险化学品罐区未实现紧急切断功能;涉及毒性气体、液化气体、剧毒液体的一级、二级重大危险源的危险化学品罐区未配备独立的安全仪表系统。
六、全压力式液化烃储罐未按国家标准设置注水措施。
七、液化烃、液氨、液氯等易燃易爆、有毒有害液化气体的充装未使用万向管道充装系统。
八、光气、氯气等剧毒气体及硫化氢气体管道穿越除厂区(包括化工园区、工业园区)外的公共区域。
九、地区架空电力线路穿越生产区且不符合国家标准要求。
十、在役化工装置未经正规设计且未进行安全设计诊断。
十一、使用淘汰落后安全技术工艺、设备目录列出的工艺、设备。
十二、涉及可燃和有毒有害气体泄漏的场所未按国家标准设置检测报警装置,爆炸危险场所未按国家标准安装使用防爆电气设备。
十三、控制室或机柜间面向具有火灾、爆炸危险性装置一侧不满足国家标准关于防火防爆的要求。
十四、化工生产装置未按国家标准要求设置双重电源供电,自动化控制系统未设置不间断电源。
十五、安全阀、爆破片等安全附件未正常投用。
十六、未建立与岗位相匹配的全员安全生产责任制或者未制定实施生产安全事故隐患排查治理制度。
十七、未制定操作规程和工艺控制指标。
十八、未按照国家标准制定动火、进入受限空间等特殊作业管理制度,或者制度未有效执行。
十九、新开发的危险化学品生产工艺未经小试、中试、工业化试验直接进行工业化生产;国内首次使用的化工工艺未经过省级人民政府有关部门组织的安全可靠性论证;新建装置未制定试生产方案投料开车;精细化工企业未按规范性文件要求开展反应安全风险评估。
重大生产安全事故隐患判定标准

化工和危险化学品生产经营单位重大生产安全事故隐患判定标准(试行)?依据有关法律法规、部门规章和国家标准,以下情形应当判定为重大事故隐患:一、危险化学品生产、经营单位主要负责人和安全生产管理人员未依法经考核合格。
二、特种作业人员未持证上岗。
三、涉及“两重点一重大”的生产装置、储存设施外部安全防护距离不符合国家标准要求。
四、涉及重点监管危险化工工艺的装置未实现自动化控制,系统未实现紧急停车功能,装备的自动化控制系统、紧急停车系统未投入使用。
五、构成一级、二级重大危险源的危险化学品罐区未实现紧急切断功能;涉及毒性气体、液化气体、剧毒液体的一级、二级重大危险源的危险化学品罐区未配备独立的安全仪表系统。
六、全压力式液化烃储罐未按国家标准设置注水措施。
七、液化烃、液氨、液氯等易燃易爆、有毒有害液化气体的充装未使用万向管道充装系统。
八、光气、氯气等剧毒气体及硫化氢气体管道穿越除厂区(包括化工园区、工业园区)外的公共区域。
九、地区架空电力线路穿越生产区且不符合国家标准要求。
十、在役化工装置未经正规设计且未进行安全设计诊断。
十一、使用淘汰落后安全技术工艺、设备目录列出的工艺、设备。
十二、涉及可燃和有毒有害气体泄漏的场所未按国家标准设置检测报警装置,爆炸危险场所未按国家标准安装使用防爆电气设备。
十三、控制室或机柜间面向具有火灾、爆炸危险性装置一侧不满足国家标准关于防火防爆的要求。
十四、化工生产装置未按国家标准要求设置双重电源供电,自动化控制系统未设置不间断电源。
十五、安全阀、爆破片等安全附件未正常投用。
十六、未建立与岗位相匹配的全员安全生产责任制或者未制定实施生产安全事故隐患排查治理制度。
十七、未制定操作规程和工艺控制指标。
十八、未按照国家标准制定动火、进入受限空间等特殊作业管理制度,或者制度未有效执行。
十九、新开发的危险化学品生产工艺未经小试、中试、工业化试验直接进行工业化生产;国内首次使用的化工工艺未经过省级人民政府有关部门组织的安全可靠性论证;新建装置未制定试生产方案投料开车;精细化工企业未按规范性文件要求开展反应安全风险评估。
重大生产安全事故隐患判定标准(试行)解读

化工和危险化学品生产经营单位重大生产安全事故隐患判定标准(试行)解读一、危险化学品生产、经营单位主要负责人和安全生产管理人员未依法经考核合格。
近年来,在化工(危险化学品)事故调查过程中发现,事故企业不同程度地存在主要负责人和安全管理人员法律意识与安全风险意识淡薄、安全生产管理知识欠缺、安全生产管理能力不能满足安全生产需要等共性问题,人的因素是制约化工(危险化学品)安全生产的最重要因素。
危险化学品安全生产是一项科学性、专业性很强的工作,企业的主要负责人和安全生产管理人员只有牢固树立安全红线意识、风险意识,掌握危险化学品安全生产的基础知识、具备安全生产管理的基本技能,才能真正落实企业的安全生产主体责任。
《安全生产法》、《危险化学品安全管理条例》、《生产经营单位安全培训规定》(国家安全监管总局令第3号)均对危险化学品生产、经营单位从业人员培训和考核作出了明确要求,其中《安全生产法》第二十四条要求“生产经营单位的主要负责人和安全生产管理人员必须具备与本单位所从事的生产经营活动相应的安全生产知识和管理能力。
危险物品的生产、经营、储存单位以及矿山、金属冶炼、建筑施工、道路运输单位的主要负责人和安全生产管理人员,应当由主管的负有安全生产监督管理职责的部门对其安全生产知识和管理能力考核合格。
考核不得收费”。
《生产经营单位安全培训规定》明确要求“危险化学品等生产经营单位主要负责人和安全生产管理人员,自任职之日起6个月内,必须经安全生产监管监察部门对其安全生产知识和管理能力考核合格”。
2017年1月25日,国家安全监管总局印发了《化工(危险化学品)企业主要负责人安全生产管理知识重点考核内容(第一版)》和《化工(危险化学品)企业安全生产管理人员安全生产管理知识重点考核内容(第一版)》(安监总厅宣教〔2017〕15号),对有关企业主要负责人和安全管理人员重点考核重点内容提出了明确要求,负有安全生产监督管理的部门应当按照相关法律法规要求对有关企业人员进行考核。
- 1、下载文档前请自行甄别文档内容的完整性,平台不提供额外的编辑、内容补充、找答案等附加服务。
- 2、"仅部分预览"的文档,不可在线预览部分如存在完整性等问题,可反馈申请退款(可完整预览的文档不适用该条件!)。
- 3、如文档侵犯您的权益,请联系客服反馈,我们会尽快为您处理(人工客服工作时间:9:00-18:30)。
化工和危险化学品生产经营单位
重大生产安全事故隐患判定标准(试行)
依据有关法律法规、部门规章和国家标准,以下情形应当判定为重大事故隐患:
一、危险化学品生产、经营单位主要负责人和安全生产管理人员未依法经考核合格。
二、特种作业人员未持证上岗。
三、涉及“两重点一重大”的生产装置、储存设施外部安全防护距离不符合国家标准要求。
四、涉及重点监管危险化工工艺的装置未实现自动化控制,系统未实现紧急停车功能,装备的自动化控制系统、紧急停车系统未投入使用。
五、构成一级、二级重大危险源的危险化学品罐区未实现紧急切断功能;涉及毒性气体、液化气体、剧毒液体的一级、二级重大危险源的危险化学品罐区未配备独立的安全仪表系统。
六、全压力式液化烃储罐未按国家标准设置注水措施。
七、液化烃、液氨、液氯等易燃易爆、有毒有害液化气体的充装未使用万向管道充装系统。
八、光气、氯气等剧毒气体及硫化氢气体管道穿越除厂区(包括化工园区、工业园区)外的公共区域。
九、地区架空电力线路穿越生产区且不符合国家标准要求。
十、在役化工装置未经正规设计且未进行安全设计诊断。
十一、使用淘汰落后安全技术工艺、设备目录列出的工艺、设备。
十二、涉及可燃和有毒有害气体泄漏的场所未按国家标准设置检测报警装置,爆炸危险场所未按国家标准安装使用防爆电气设备。
十三、控制室或机柜间面向具有火灾、爆炸危险性装置一侧不满足国家标准关于防火防爆的要求。
十四、化工生产装置未按国家标准要求设置双重电源供电,自动化控制系统未设置不间断电源。
十五、安全阀、爆破片等安全附件未正常投用。
十六、未建立与岗位相匹配的全员安全生产责任制或者未制定实施生产安全事故隐患排查治理制度。
十七、未制定操作规程和工艺控制指标。
十八、未按照国家标准制定动火、进入受限空间等特殊作业管理制度,或者制度未有效执行。
十九、新开发的危险化学品生产工艺未经小试、中试、工业化试验直接进行工业化生产;国内首次使用的化工工艺未经过省级人民政府有关部门组织的安全可靠性论证;新建装置未制定试生产方案投料开车;精细化工企业未按规范性文件要求开展反应安全风险评估。
二十、未按国家标准分区分类储存危险化学品,超量、超品种储存危险化学品,相互禁配物质混放混存。
烟花爆竹生产经营单位
重大生产安全事故隐患判定标准(试行)
依据有关法律法规、部门规章和国家标准,以下情形应当判定为重大事故隐患:
一、主要负责人、安全生产管理人员未依法经考核合格。
二、特种作业人员未持证上岗,作业人员带药检维修设备设施。
三、职工自行携带工器具、机器设备进厂进行涉药作业。
四、工(库)房实际作业人员数量超过核定人数。
五、工(库)房实际滞留、存储药量超过核定药量。
六、工(库)房内、外部安全距离不足,防护屏障缺失或者不符合要求。
七、防静电、防火、防雷设备设施缺失或者失效。
八、擅自改变工(库)房用途或者违规私搭乱建。
九、工厂围墙缺失或者分区设置不符合国家标准。
十、将氧化剂、还原剂同库储存、违规预混或者在同一工房内粉碎、称量。
十一、在用涉药机械设备未经安全性论证或者擅自更改、改变用途。
十二、中转库、药物总库和成品总库的存储能力与设计产能不匹配。
十三、未建立与岗位相匹配的全员安全生产责任制或者未制定实施生产安全事故隐患排查治理制度。
十四、出租、出借、转让、买卖、冒用或者伪造许可证。
十五、生产经营的产品种类、危险等级超许可范围或者生产使用违禁药物。
十六、分包转包生产线、工房、库房组织生产经营。
十七、一证多厂或者多股东各自独立组织生产经营。
十八、许可证过期、整顿改造、恶劣天气等停产停业期间组织生产经营。
十九、烟花爆竹仓库存放其它爆炸物等危险物品或者生产经营违禁超标产品。
二十、零售点与居民居住场所设置在同一建筑物内或者在零售场所使用明火。
各省、自治区、直辖市及新疆生产建设兵团安全生产监督管理局,有关中央企业:
为准确判定、及时整改化工和危险化学品生产经营单位及烟花爆竹生产经营单位重大生产安全事故隐患,有效防范遏制重特大生产安全事故,根据《安全生产法》和《中共中央国务院关于推进安全生产领域改革发展的意见》,国家安全监管总局制定了《化工和危险化学品生产经营单位重大生产安全事故隐患判定标准(试行)》和《烟花爆竹生产经营单位重大生产安全事故隐患判定标准(试行)》(以下简称《判定标准》),现印发给你们,请遵照执行。
请各省级安全监管局、有关中央企业及时将本通知要求传达至辖区内各级安全监管部门和有关生产经营单位。
各级安全监管部门要按照有关法律法规规定,将《判定标准》作为执法检查的重要依据,强化执法检查,建立健全重大生产安全事故隐患治理督办制度,督促生产经营单位及时消除重大生产安全事故隐患。
国家安全监管总局
2017年11月13日。