错检率与漏检率精编版
进货检验错验、漏检的统计
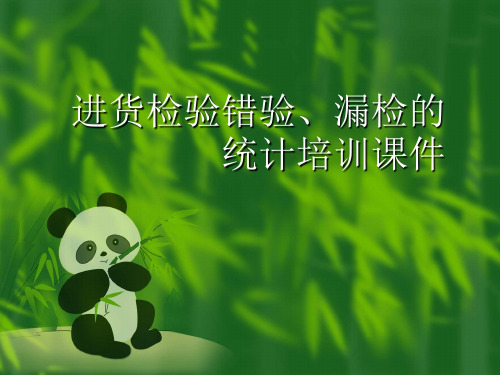
谢谢!
进货检验错验、漏检的 统计培训课件
错验、漏检的由来
• 在质量检验中,由于主客观因素的影响,产生
检验误差是很难避免的,甚至是经常发生的。 据国外资料介绍,检验员对缺陷的漏检率有时 可以高达15%一20%。
• 我国许多企业对检验人员的检验误差,还没有
引起足够的重视,甚至缺乏“检验误差”的概 念,迷信100%检验的可靠性。认为只要通过 检验合格的产品,一定就是百分之百的合格品, 实际上这是不符合事实的,因为这里面还存在 检验误差。检验误差可以分为以下几类:
柜时,车间领料员从仓库领了1000PCS说明书, 此批说明书是供应商盈保1月8号所供的,经质 管部IQC检验合格,车间从上午9点开始生产, 在生产过程中不时发现有说明书型号是JC-48B 的,为不至影响生产进度,在经过领导同意后 进行挑选使用,至生产完毕后,共挑选出 120PCS JC-48B的说明书,下线比率为12%, 这说明了IQC对此批说明书漏检。
错验、漏检如何统计
• 为尽量减少检验误差,减少错验、漏检事故的
发生,有必要对错验、漏检的质量事故进行统 计,用数据和事实为依据,加强对检验人员错 验、漏检的考核,加强对检验人员检验知识的 培训,从根本上杜绝错验、漏检事故的发生。
• 我们生产车间统计员在对进货错验、漏检的比
率统计时,一定要对进货错验、漏检的定义理 解清楚,这样才不会将不属于统计范围内的不 合格物料也纳入错验、漏检比率中。
• 4.建立标准品:用标准品进行比较,以便发现被检查
过的产品所存在的缺陷或误差。
公司质量指标的定义
• 在公司《2010年质量目标》中的管理指标中的
第11个指标“进货检错验、漏检比率≤0.1% ” 是这样被定义的:同一厂家、同一批次同一型 号外购货品下线率≥10% 。这个定义可以这样 直观的理解:
CAN协议的错帧漏检率推导及改进过程简介

CAN协议的错帧漏检率推导及改进过程简介当数据在传送中出错,且错帧被漏检时,就意味着错误的数据被送到应用层,除非应用层有额外的数据识别措施,这个数据就可能引起不可预测的结果。
CAN协议声称有很低的错帧漏检率(4.7×10-11×出错率),有的宣传材料在一定条件下推出要1000年才有1次漏检,这是不正确的。
错帧漏检率是一个十分重要的指标,很多应用就是看到Bosch CAN2.0规范上的说明才选用CAN的。
但是对这个指标的来源仅有极少的公开资料,以及很少的讨论,使用户很难对它确认或验证,这给用户带来风险。
本文采用了重构出错漏检实例的方法,导出了CAN的漏检错帧概率下限,它比CAN声称的要大几个数量级。
在许多应用中,CAN已是可靠性和价格平衡下的不二选择,或者已被长期生产和使用,面对这个新发现的问题,在CAN本身未作改进之前,迫切需要一种“补丁”来加以改善。
由于篇幅有限,所以只能摘要介绍错帧漏检率的推导过程,重点在提供解决方案。
1 关于CAN漏检错帧概率文献的讨论Bosch CAN2.0规范说它的漏检错帧概率小于错帧率(message error rate)×4.7×10-11。
它的来源见参考文献,其中没有提供产生漏检的分析算法,仅提到用大量仿真得到了公式。
要判断一个帧出错后是否会漏检,至少要计算2次CRC,对每一bit仅就汇编语言也需要几条指令,以该文考虑的80~90 bit的帧,CRC覆盖58~66 bit 就要循环58~66次,以1989年时常用的PDP11或VAX机,一条机器指令要0.1 μs左右,一帧的判断要0.07 ms,即使不停机做一年,能作2.20×1011帧,考虑58 bit可构成258=2.88×1017种不同的帧,再加有58×57种不同的加入2位bit错的位置组合,所以能作的仿真只是可能情况的微乎其微的一部分(百万分之一)。
泄漏率统计及检查标准【范本模板】

设备泄漏率统计标准一、密封点分类和统计范围1、动密封:各种设备的连续运动、旋转和住复、的两个部件之间的密封,属于动密封。
如压缩机轴,泵轴,各种釜类旋转轴等的密封均属动密封。
2、静密封:设备及其附属管线和附件,在运行过程中两个没有相对运动的部件之间的密封属于静密封.如设备管线上的法兰、各种阀门、丝堵、活接头;机泵设备上的油标、附属管线以及其他设备的结合部位均属静密封。
二、密封点统计标准1、动密封点的统计标准:一对连续运动、旋转或往复、两个部件之间的密封算一个动密封点.2、静密封点的统计标准:一个静密封点接合处,算一个静密封点。
如一对法兰,不论其规格大小,均算一个密封点。
一个阀门一般算四个密封点,如阀门后有丝堵或阀后紧接放空,则应各多算一点。
一个丝扣活接头,算三个密封点。
特别部位如连接法兰的螺栓孔与设备内部是连通的,除了接合面算一个密封点外,有几个螺栓孔应加几个密封点。
3、泄漏点的统计标准:有一处泄漏,就算一个泄漏点,不论是密封点或因焊缝裂纹、砂眼、腐蚀以及其他原因造成的泄漏,均作泄漏点统计。
4.泄漏率计算公式静(动)密封点泄漏率(‰)=静(动)密封点泄漏点数/静(动)密封点数×1000‰三、动、静密封检验标准:(一)、静密封检验标准:1、设备及管线的接合部位用,肉眼观察不结焦、不冒烟、无漏痕、无渗迹、无污垢。
2、仪表设备及汽、风源引线,焊接及其他连接部位用肥皂水试漏,无气泡;真空部位,用薄纸条顺的办法.3、电气设备变压器、油开关、油浸纸绝缘电缆头等接合部位,用肉眼观察无渗漏。
4、氧气、氮气、空气系统,用用肥皂水检查无气泡.5、蒸汽系统,用肉眼观察不漏气无水垢。
6、酸、碱等化学系统,用肉眼观察无渗迹、无漏痕、不结垢、不冒烟或用精密试纸试漏不变色。
7、水、油系统,宏观检查或用手摸无渗漏、无水垢。
8、各种机床的各种变速箱、立轴、变速手柄、宏观检查无明显渗漏。
没有密封的部位,如滑枕、导轨等不进行统计和考核。
血片标准

血片判定标准
一、血片制作质量和合格率
好:厚薄血膜均好,或薄血膜好,厚血膜中
中:薄血膜中,厚血膜好或中
差:薄血膜差,或厚血膜均差
二、合格率计算方法:分别以血片制作、染色和清洁度的好、中合并计算合格率。
三、三级中心镜检站抽复检要求及漏检、错检率计算方法:阴性血片县级抽检不少于血片的5%;市级复检率不少于已检血片的2%;省级复检不少于已检血片的1%。
漏检率按每次或全年复检阴性片总数分别计算,所有阳性片均需复查,检查率按每年复查总数计算。
血片四个合格率要求
一、血片制作合格率在85%以上。
二、染色合格率在85%以上。
三、清洁度合格率在80%以上。
四、阳性片错检率以乡(镇)为单位全年不超过10%,阴性血片漏检率以乡(镇)为单位全年不超过0.1%。
盱眙县卫生局
盱眙县疾病预防控制中心。
错检率与漏检率

错检:就是把合格品当成了不合格品(即在检验后的不合格品中还有合格品)。
漏检:就是把不合格品当成了合格品(即在检验后的合格品中还有不合格品)。
错检是由于各种因素造成检验失误、错判,主要是由客观因素造成。
漏检是由于部分或全部项目没有经过检验、判定就流入下一道工序,大部分是由主观因素或管理原因造成的。
当产品的质量主要靠检验把关的情况下,检验人员的检验能力就成了质量控制的关键因素。
本文提供一种考核方法,供本公司的客户参考。
各单位应该根据本单位和被检验产品的具体情况加以采用。
一、考核准备•明确考核的范围——事先告诉被考核者,这次检验要求查出哪些不合格的问题。
这些不合格的判别准则是什么。
必要时应该事先用不合格样品向被考核者展示。
确信被考核者理解后才能进行。
如果从生产线上抽调检验员进行考核时,应该按照生产规定的要求,检查出应该查出的各种不合格问题。
•考核材料——总的检验样件数N(100件)。
它包括两部分:i. 数量A(不少于50件)的不合格品。
每件存在多多少少不等的某种不合格问题。
这个数量A应该包容各种典型的不合格类型。
至少必须包容顾客认为接受不了的各种问题。
ii. 数量B的合格品。
iii. 把A 和B混合起来。
由考核者用粘胶纸对每个产品编上号码。
根据号码事先分别记录A 中有哪些不合格问题,数量多少。
譬如,第1个产品有跳针2处、污油渍1处、定线外露1处。
第3个产品有脱针1处、针洞2处、没有商标1处、缝子吊1处、对位不准1处。
当然。
不能让被考核者知道。
•设计一张记录表格——上面第1行列出要求检查发现的不合格问题。
从第2行起顺序编上产品的号码。
要求被考核者把所检验产品发现的不合格问题和数量分别对应填写在该编号产品内。
•规定检验时间——根据日常生产的检验平均时间规定在一定时间内检验完这些产品数N。
二、考核办法•把N数量产品按照顺序排好,交给被考核者,要求在规定时间内检验完。
•当被考核者发现自己认为是不合格的问题,用贴粘胶纸的办法做标志,并在表格对应的不合格问题中填写数量。
漏检率年总结

漏检率年总结1. 漏检率概述在医疗领域,漏检率是指某一特定时期内未能准确检测到患者疾病的比例。
漏检率是衡量医疗机构或医生工作质量的重要指标之一,对于确保患者的健康和安全具有重要意义。
在过去的一年里,我们医疗机构对漏检率进行了详细的分析和评估,并采取了一系列措施来降低漏检率,在本文档中,将对我们医疗机构在过去一年里的漏检率进行总结和分析。
2. 漏检率变化趋势分析通过对漏检率数据进行统计和分析,我们可以看到在过去一年里,漏检率有明显的变化趋势。
具体来说,漏检率从年初的 X% 下降到年末的 X%。
这表明我们在过去的一年里在降低漏检率方面取得了一定的进展,但仍然有改进的空间。
在接下来的章节中,我们将深入分析影响漏检率变化的因素,并提出相应的改进措施。
3. 影响漏检率的因素分析人为因素人为因素是导致漏检率升高的主要原因之一。
其中包括医生或技术人员的疏忽、疲劳或缺乏准确的诊断能力等。
为了降低人为因素导致的漏检率,我们医疗机构在过去一年里采取了以下措施:•加强医生和技术人员的培训,提高其专业知识和技能水平;•实施轮班制度,确保医生和技术人员的休息和工作时间合理安排;•引进新的检测设备和技术,提高诊断的准确性。
流程因素不合理的流程可能导致漏检率升高。
而在过去一年里,我们医疗机构对存在问题的流程进行了改进:•对流程进行了全面的评估和优化,消除了繁琐和冗余的环节;•引入了新的信息系统,提高了流程的数字化管理和监控。
设备因素医疗设备的性能和质量也会直接影响漏检率。
在过去一年里,我们医疗机构注重设备的维护和更新:•建立了设备维护团队,定期对设备进行维护和保养;•更新了部分老化和性能不佳的设备,提高了诊断的准确性和可靠性。
4. 改进措施和效果评估为了降低漏检率,我们医疗机构采取了一系列的改进措施,并对其效果进行评估。
定期培训和评估通过定期的培训和评估,我们提高了医生和技术人员的专业能力和诊断水平。
同时,我们也通过不同的评估工具,例如模拟病例和随机抽查等手段,评估了医生和技术人员的表现,并针对性地提供了改进意见和建议。
健康体检采血项目弃检、漏检原因分析与对策
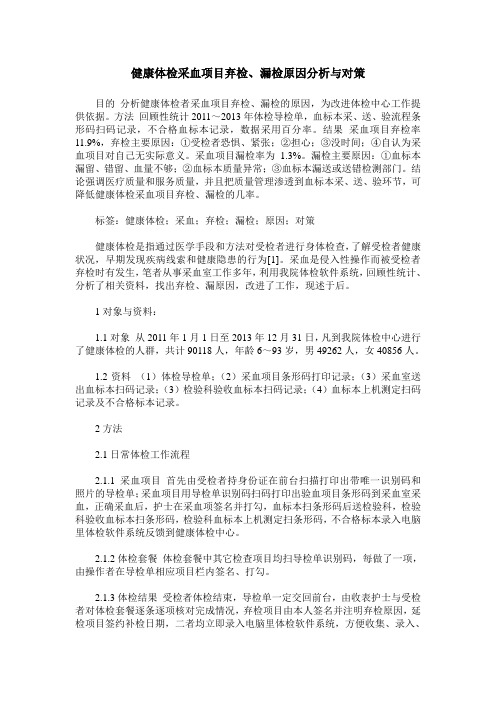
健康体检采血项目弃检、漏检原因分析与对策目的分析健康体检者采血项目弃检、漏检的原因,为改进体检中心工作提供依据。
方法回顾性统计2011~2013年体检导检单,血标本采、送、验流程条形码扫码记录,不合格血标本记录,数据采用百分率。
结果采血项目弃检率11.9%,弃检主要原因:①受检者恐惧、紧张;②担心;③没时间;④自认为采血项目对自己无实际意义。
采血项目漏检率为 1.3%。
漏检主要原因:①血标本漏留、错留、血量不够;②血标本质量异常;③血标本漏送或送错检测部门。
结论强调医疗质量和服务质量,并且把质量管理渗透到血标本采、送、验环节,可降低健康体检采血项目弃检、漏检的几率。
标签:健康体检;采血;弃检;漏检;原因;对策健康体检是指通过医学手段和方法对受检者进行身体检查,了解受检者健康状况,早期发现疾病线索和健康隐患的行为[1]。
采血是侵入性操作而被受检者弃检时有发生,笔者从事采血室工作多年,利用我院体检软件系统,回顾性统计、分析了相关资料,找出弃检、漏原因,改进了工作,现述于后。
1对象与资料:1.1对象从2011年1月1日至2013年12月31日,凡到我院体检中心进行了健康体检的人群,共计90118人,年龄6~93岁,男49262人,女40856人。
1.2资料(1)体检导检单;(2)采血项目条形码打印记录;(3)采血室送出血标本扫码记录;(3)检验科验收血标本扫码记录;(4)血标本上机测定扫码记录及不合格标本记录。
2方法2.1日常体检工作流程2.1.1采血项目首先由受检者持身份证在前台扫描打印出带唯一识别码和照片的导检单;采血项目用导检单识别码扫码打印出验血项目条形码到采血室采血,正确采血后,护士在采血项签名并打勾,血标本扫条形码后送检验科,检验科验收血标本扫条形码,检验科血标本上机测定扫条形码,不合格标本录入电脑里体检软件系统反馈到健康体检中心。
2.1.2体检套餐体检套餐中其它检查项目均扫导检单识别码,每做了一项,由操作者在导检单相应项目栏内签名、打勾。
进货检验错验、漏检的统计
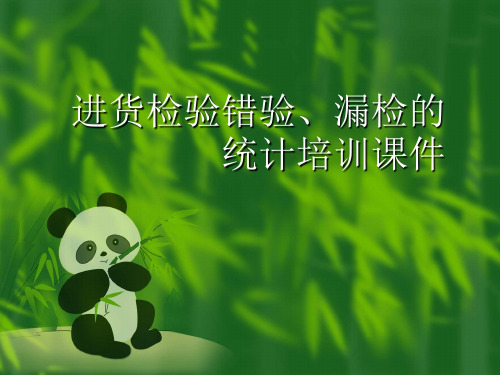
错验、漏检如何统计
• 为尽量减少检验误差,减少错验、漏检事故的
发生,有必要对错验、漏检的质量事故进行统 计,用数据和事实为依据,加强对检验人员错 验、漏检的考核,加强对检验人员检验知识的 培训,从根本上杜绝错验、漏检事故的发生。
• 我们生产车间统计员在对进货错验、漏检的比
率统计时,一定要对进货错验、漏检的定义理 解清楚,这样才不会将不属于统计范围内的不 合格物料也纳入错验、漏检比率中。
Hale Waihona Puke 谢谢!产品再检查一到二次。查明合格品中有多少不合格品, 及不合格品中有多少合格品。
• 2.复核检查:由技术水平较高的检验人员或技术人员,
复核检验已检查过的一批合格品和不合格品。
• 3.改变检验条件:为了解检验是否正确,当检验员检
查一批产品后,可以用精度更高的检测手段进行重检, 以发现检测工具造成检验误差的大小。
• (4)明知故犯误差
由于检验人员动机不良造成的检验误差。如有 意报复,迫于生产部门的压力,工检关系不和, 或为了多拿奖金等原因所造成;少数情况下可能 有意破坏。
检验误差的两个指标
不论哪类原因造成的误差,均可概括为以 下两类,包括产品形成中的任一环节:
• 1.漏检:漏检就是有的不合格品没有被检查出
• 4.建立标准品:用标准品进行比较,以便发现被检查
过的产品所存在的缺陷或误差。
公司质量指标的定义
• 在公司《2010年质量目标》中的管理指标中的
第11个指标“进货检错验、漏检比率≤0.1% ” 是这样被定义的:同一厂家、同一批次同一型 号外购货品下线率≥10% 。这个定义可以这样 直观的理解:
比如:2010年2月24日供应商瑞德所供的120V 电源板(物料编号0800000,批量:10000PCS) 经质管部IQC检验后由总一车间领到车间使用, 在使用过程中发现有1100PCS电源板不工作而 被挑选下线,不良率为11%。
- 1、下载文档前请自行甄别文档内容的完整性,平台不提供额外的编辑、内容补充、找答案等附加服务。
- 2、"仅部分预览"的文档,不可在线预览部分如存在完整性等问题,可反馈申请退款(可完整预览的文档不适用该条件!)。
- 3、如文档侵犯您的权益,请联系客服反馈,我们会尽快为您处理(人工客服工作时间:9:00-18:30)。
错检:就是把合格品当成了不合格品(即在检验后的不合格品中还有合格品)。
漏检:就是把不合格品当成了合格品(即在检验后的合格品中还有不合格品)。
错检是由于各种因素造成检验失误、错判,主要是由客观因素造成。
漏检是由于部分或全部项目没有经过检验、判定就流入下一道工序,大部分是由主观因素或管理原因造成的。
当产品的质量主要靠检验把关的情况下,检验人员的检验能力就成了质量控制的关键因素。
本文提供一种考核方法,供本公司的客户参考。
各单位应该根据本单位和被检验产品的具体情况加以采用。
一、考核准备
•明确考核的范围——事先告诉被考核者,这次检验要求查出哪些不合格的问题。
这些不合格的判别准则是什么。
必要时应该事先用不合格样品向被考核者展示。
确信被考核者理解后才能进行。
如果从生产线上抽调检验员进行考核时,应该按照生产规定的要求,检查出应该查出的各种不合格问题。
•考核材料——总的检验样件数N(100件)。
它包括两部分:
i. 数量A(不少于50件)的不合格品。
每件存在多多少少不等的某种不合格问题。
这个数量A应该包容各种典型的不合格类型。
至少必须包容顾客认为接受不了的各种问题。
ii. 数量B的合格品。
iii. 把A 和B混合起来。
由考核者用粘胶纸对每个产品编上号码。
根据号码事先分别记录A 中有哪些不合格问题,数量多少。
譬如,第1个产品有跳针2处、污油渍1处、定线外露1处。
第3个产品有脱针1处、针洞2处、没有商标1处、缝子吊1处、对位不准1处。
当然。
不能让被考核者知道。
•设计一张记录表格——上面第1行列出要求检查发现的不合格问题。
从第2行起顺序编上产品的号码。
要求被考核者把所检验产品发现的不合格问题和数量分别对应填写在该编号产品内。
•规定检验时间——根据日常生产的检验平均时间规定在一定时间内检验完这些产品数N。
二、考核办法
•把N数量产品按照顺序排好,交给被考核者,要求在规定时间内检验完。
•当被考核者发现自己认为是不合格的问题,用贴粘胶纸的办法做标志,并在表格对应的不合格问题中填写数量。
三、考核计算方法
•由考核者按照每件产品统计以下数据:
d -被考核者报告的不合格数,。
譬如45。
k -错检数,在d中实际上是合格的数量。
譬如5。
b -漏检数,从被考核者认为合格品中n-d中实际存在的不合格数,譬如10。
•计算准确率
它是抽检总数中检验人员发现的实际不合格数(d – k )和该抽检总数中实际存在不合格数(d – k + b)之比:
准确率=(d – k )/ (d – k + b)
准确率可以按照件为基础计算。
就是一件衣服只要有一项不合格,就作为不合格。
也可以按照不合格项总数为基础计算。
上例准确率为(45-5)/ (45-5 +10)= 80%。
也可以针对某一个不合格问题为基础计算。
•计算错检率
错检是指本来合格的把它作为不合格。
那么错检率应该用合格总数中错了多少来表示。
因此,它是错检数k与该抽检总数中实际存在合格数(n-d+k-b) 之比:
错检率=k / ( n-d+k-b)
这个例子为10%;它表示有“宁错勿漏”的指导思想。
如果需要还可以考核漏检率。
•计算漏检率
漏检是指本来是不合格的把它当作合格的。
本例子应该是漏检数b与实际存在不合格总数(d – k + b) 之比。
这个例子是20%。
它表示检验人员的粗心情况。
漏检率=b / (d – k + b)
当产品的质量主要靠检验把关的情况下,检验人员的检验能力就成了质量控制的关键因素。
本文提供一种考核方法,供本公司的客户参考。
各单位应该根据本单位和被检验产品的具体情况加以采用。
一、考核准备
∙明确考核的范围——事先告诉被考核者,这次检验要求查出哪些不合格的问题。
这些不合格的判别准则是什么。
必要时应该事先用不合格样品向被考核者展示。
确信被考核者理解后才能进行。
如果从生产线上抽调检验员进行考核时,应该按照生产规定的要求,检查出应该查出的各种不合格问题。
∙考核材料——总的检验样件数N(100件)。
它包括两部分:
i.数量A(不少于50件)的不合格品。
每件存在多多少少不等的某种
不合格问题。
这个数量A应该包容各种典型的不合格类型。
至少必须包容顾客
认为接受不了的各种问题。
ii.数量B的合格品。
iii.把A 和B混合起来。
由考核者用粘胶纸对每个产品编上号码。
根据号码事先分别记录A中有哪些不合格问题,数量多少。
譬如,第1个产品有跳
针2处、污油渍1处、定线外露1处。
第3个产品有脱针1处、针洞2处、没
有商标1处、缝子吊1处、对位不准1处。
当然。
不能让被考核者知道。
∙设计一张记录表格——上面第1行列出要求检查发现的不合格问题。
从第2行起顺序编上产品的号码。
要求被考核者把所检验产品发现的不合格问题和数量分别对应填写在该编号产品内。
∙规定检验时间——根据日常生产的检验平均时间规定在一定时间内检验完这些产品数N。
二、考核办法
∙把N数量产品按照顺序排好,交给被考核者,要求在规定时间内检验完。
∙当被考核者发现自己认为是不合格的问题,用贴粘胶纸的办法做标志,并在表格对应的不合格问题中填写数量。
三、考核计算方法
∙由考核者按照每件产品统计以下数据:
d -被考核者报告的不合格数,。
譬如45。
k -错检数,在d中实际上是合格的数量。
譬如5。
b -漏检数,从被考核者认为合格品中n-d中实际存在的不合格数,譬如10。
∙计算准确率
它是抽检总数中检验人员发现的实际不合格数(d –k )和该抽检总数中实际存在不合格数(d –k + b)之比:
准确率=(d –k )/ (d –k + b)
准确率可以按照件为基础计算。
就是一件衣服只要有一项不合格,就作为不合格。
也可以按照不合格项总数为基础计算。
上例准确率为(45-5)/ (45-5 +10)= 80%。
也可以针对某一个不合格问题为基础计算。
∙计算错检率
错检是指本来合格的把它作为不合格。
那么错检率应该用合格总数中错了多少来表示。
因此,它是错检数k与该抽检总数中实际存在合格数(n-d+k-b) 之比:
错检率=k / ( n-d+k-b)
这个例子为10%;它表示有“宁错勿漏”的指导思想。
如果需要还可以考核漏检率。
∙计算漏检率
漏检是指本来是不合格的把它当作合格的。
本例子应该是漏检数b与实际存在不合格总数(d –k + b) 之比。
这个例子是20%。
它表示检验人员的粗心情况。
漏检率= b / (d –k + b)
四、数据的运用
∙合格上岗的依据——一般在人员资格鉴定时可以用这能方法。
明确规定在一定的比例下可以上岗。
生产过程中发现漏检问题多,可以再考核。
低于某个数据,要对他(她)培训,再不行,另行分配其他工作。
∙确定预防的重点问题——针对某项不合格分析数据。
譬如,某不合格问题的漏检率普遍很高。
就必须研究各种预防措施,从预防问题发生的角度,避免问题发生后又漏检。
给顾客带来不满。
譬如,某不合格问题发生错检率高,应该加强培训,提高检验人员的正确判断力。
五、结合生产过程的考核方法
以上方法必须取得专门的样品。
我们也可以结合日常的检验工作进行考核。
做法是;
∙被考核人员检验产品,挑出不合格品,用粘胶纸做好标志。
做好记录;
∙请第2位(一般是有权威的人)对被考核人员检验过的产品,用同样的工具、方法、按照同样的判别准则做第二次检验。
分别统计b、k、d等数据。
可以计算出准确率、漏检率和错检率。
针对被考核人员存在的薄弱地方,进行培训。
再用同样方法进行第2次考核。
一直到满意为止。
∙为了避免人情和做到公正,第2位不应该知道被考核人是谁。
反之,被考核人也不知道谁是复验者。
∙有时,对一些重要的产品,要求做两次检验。
可以把第2位也作为被考核者。
做法是,第一位不用粘胶纸做好标志,改用在示意图的相应部位用数码做不合格标志。
譬如,FT表示缝纫脱针不合格,FD表示缝纫的针洞等。
然后,要求第二位对同一批产品重复做检验,做记录。
经过检验人数愈多,漏检的问题愈少。
然后,分别计算准确率、漏检率和错检率。
看看谁的检验能力最高。
最好的总结经验,推广。