抽检漏检率计算
产品检验基础知识(检验员培训资料含试题及答案)

精心整理产品检验基本知识一、检验基础知识1、什么是检验(QC)?定义:检验是指依照检验标准对产品进行测量、观察或试验,将其检查结果与检验标准进行比较,最终判定产品是否合格的过程。
2、检验三要素1)产品---?检验的对象。
品管人员应当了解产品的用途、关键特性、在你负责的区域内的质量特性对后工序的影响,从这个意义上讲,真正一个称职QC你还应当了解生产流程;2)工具;3)31.2.1)2)3.与确认)二、1.2检验方式:采取全检还是抽检1.3检验手段:使用什么工具和仪器1.4判断准则:经过检查后,如何判定该项目是否合格(分为单件质量和批质量)1.5试验环境:温度、湿度、电磁干扰等,1.6引用的文件信息:如AQL标准、国家标准、企业标准等2.适用的检验标准有哪些?1)产品检验规范(检验标准书)2)产品图纸、技术规格书3)生产指令说明4)客户订单5)产品样板/图片/菲林等,建议尽可能多采用实物标准,作为标准体系的重要补充;6)色板(偏通卡)7)抽样标准(GB2828.1-2003)?三、产品检验的分类1.按产品形成的阶段分类:来料检验包括采购物料和委外加工产品的检验。
过程检验包括首件检查、中间检查和完工检查。
最终检验包括产品检查和出货检查。
2.按岗位分工:IQC即来料检验,可采取抽检或全检。
线上QC一般在特定的关键的工序设置,由线上检查人员对本工序形成的质量进行全检;IPQC即巡检,目的是控制过程的稳定性。
采取抽检,要确定检查频率和抽样量。
FQC即完工检查,在产品包装前执行,一般对特定的关键的项目实施全检,一般在包装之前。
OQC即出货检查,一般采取抽检。
QA即品质保证,一般企业通常情况下指成品检验。
需要说明的是:后三种检验方式不一定要求同时具备的。
一般情况下,采用一种也就足够了。
如果一家公司三种方式全部同时采用,一定不是好事,除非是某个产品客户要求特别严格。
3.生产过程中的检查:首件检查目的:保证下线正式生产的产品符合规定要求,防止批量出错。
进货检验错验、漏检的统计
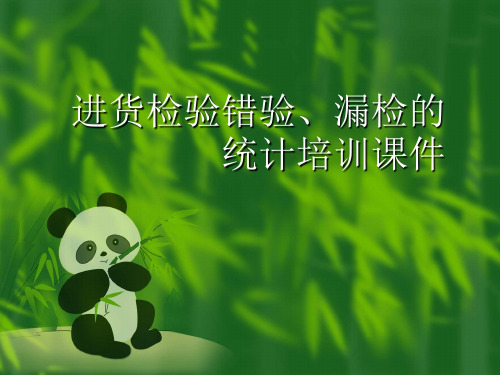
谢谢!
进货检验错验、漏检的 统计培训课件
错验、漏检的由来
• 在质量检验中,由于主客观因素的影响,产生
检验误差是很难避免的,甚至是经常发生的。 据国外资料介绍,检验员对缺陷的漏检率有时 可以高达15%一20%。
• 我国许多企业对检验人员的检验误差,还没有
引起足够的重视,甚至缺乏“检验误差”的概 念,迷信100%检验的可靠性。认为只要通过 检验合格的产品,一定就是百分之百的合格品, 实际上这是不符合事实的,因为这里面还存在 检验误差。检验误差可以分为以下几类:
柜时,车间领料员从仓库领了1000PCS说明书, 此批说明书是供应商盈保1月8号所供的,经质 管部IQC检验合格,车间从上午9点开始生产, 在生产过程中不时发现有说明书型号是JC-48B 的,为不至影响生产进度,在经过领导同意后 进行挑选使用,至生产完毕后,共挑选出 120PCS JC-48B的说明书,下线比率为12%, 这说明了IQC对此批说明书漏检。
错验、漏检如何统计
• 为尽量减少检验误差,减少错验、漏检事故的
发生,有必要对错验、漏检的质量事故进行统 计,用数据和事实为依据,加强对检验人员错 验、漏检的考核,加强对检验人员检验知识的 培训,从根本上杜绝错验、漏检事故的发生。
• 我们生产车间统计员在对进货错验、漏检的比
率统计时,一定要对进货错验、漏检的定义理 解清楚,这样才不会将不属于统计范围内的不 合格物料也纳入错验、漏检比率中。
• 4.建立标准品:用标准品进行比较,以便发现被检查
过的产品所存在的缺陷或误差。
公司质量指标的定义
• 在公司《2010年质量目标》中的管理指标中的
第11个指标“进货检错验、漏检比率≤0.1% ” 是这样被定义的:同一厂家、同一批次同一型 号外购货品下线率≥10% 。这个定义可以这样 直观的理解:
漏检率计算公式

漏检率计算公式
漏检率是目前互联网技术中非常重要的一项指标,它主要是用来衡量一组数据中漏检数据或者被疏忽检查的数据的比率。
计算漏检率的公式如下:漏检率=漏检数据总数/被检查的总数×100%。
这个公式主要是用来衡量某个系统的缺陷率,以了解系统的质量程度。
漏检率的测量是非常重要的,它可以用来衡量一组数据中漏检的比率,也可以用来衡量一个系统的质量程度。
因此,有必要在互联网领域里对数据进行完整的检查,以便降低漏检比率。
此外,网络技术的不断发展,也推动了漏检率的持续降低,这就要求专业人员不断探索新的技术,以实现更加精准的数据检查。
例如,在自动化检查系统中,可以采用深度学习算法和神经网络等辅助技术,提高检查的准确性,减少漏检率,提升检查效率。
通过精确的检查,可以有效降低漏检率,提升数据完整性。
互联网行业中,应该采取务实的措施,将漏检率作为综合衡量系统质量的重要指标,并采取有效措施降低漏检率,以保障数据的安全,提高用户体验品质。
关于产品抽检率的设定

关于产品抽检率的设定关于抽检率的设定V1.0一、抽检率a)定义:在得知一个产品批次全部的单品总数据后,用于计算所需实际测量的单品数量的比率,称之为抽检率b)抽检率下限:通过多次(或一次)验收最终测量过的单品数量与该产品批次全部的单品总量的比。
i.价值:在既定的标准合格率下,只要实际测量的单品数量达到此抽检率下限的要求即可保证此产品批次的整体合格率能够达到或超过标准合格率的要求。
c)计算公式:抽检率=实际抽检的单品数/全部的单品数d)设定方案:i.对目标产品批次的某一代表性样本进行一次全检,获取不合格率为mii.该产品批次的标准合格率为n,标准允许的不合格率为1-niii.目标产品批次满足不合格单品均匀分布iv.欲使不合格率保证在1-n以下v.则该产品批次的抽检率下限为1.例如:对某种手机的出厂合格率要求为98%时,允许的不合格率为2%,2.对此种手机某批样品全检后,发现不合格率为10%,欲使产品出厂合格率至少为98%。
通过以上公式计算得出的抽检率下限为80%。
3.以上,为保证出厂合格率,需对各批次的产品保持80%以上的抽检率,并将发现的次品进行修正或者替换。
vi.设定该产品批次各次验收的抽检率时,只需保证各次的抽检率之和达到或超过此抽检率下限即可vii.注:抽检率上限为100%e)设定方案的限制i.目标产品批次的不合格单品必须接近或完全满足均匀分布ii.必须能够保证所发现的不合格单品能被全部整改并通过合格验收f)对产品质量的控制效果或品质提升率与卫士设定的产品批次抽检率相等。
g)缺陷:i.当目标产品批次的不合格率低于代表性样本不合格率时则所计算的抽检率下限值偏低,即控制力度不够ii.当目标产品批次的不合格率高于代表性样本不合格率时则所计算的抽检率下限值偏高,即控制力度过大iii.规避手段:进行多批次代表性样本不合格率的采集,计算其平均值作为计算时所用的样本标准值。
产品抽检标准产品抽检比例
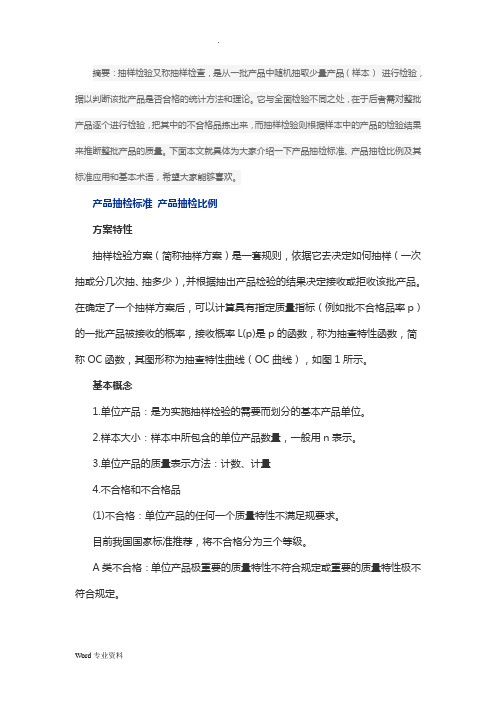
摘要:抽样检验又称抽样检查,是从一批产品中随机抽取少量产品(样本)进行检验,据以判断该批产品是否合格的统计方法和理论。
它与全面检验不同之处,在于后者需对整批产品逐个进行检验,把其中的不合格品拣出来,而抽样检验则根据样本中的产品的检验结果来推断整批产品的质量。
下面本文就具体为大家介绍一下产品抽检标准、产品抽检比例及其标准应用和基本术语,希望大家能够喜欢。
产品抽检标准产品抽检比例方案特性抽样检验方案(简称抽样方案)是一套规则,依据它去决定如何抽样(一次抽或分几次抽、抽多少),并根据抽出产品检验的结果决定接收或拒收该批产品。
在确定了一个抽样方案后,可以计算具有指定质量指标(例如批不合格品率p)的一批产品被接收的概率,接收概率L(p)是p的函数,称为抽查特性函数,简称OC函数,其图形称为抽查特性曲线(OC曲线),如图1所示。
基本概念1.单位产品:是为实施抽样检验的需要而划分的基本产品单位。
2.样本大小:样本中所包含的单位产品数量,一般用n表示。
3.单位产品的质量表示方法:计数、计量4.不合格和不合格品(1)不合格:单位产品的任何一个质量特性不满足规要求。
目前我国国家标准推荐,将不合格分为三个等级。
A类不合格:单位产品极重要的质量特性不符合规定或重要的质量特性极不符合规定。
B类不合格:单位产品重要的质量特性不符合规定或质量特性严重不符合规定。
C类不合格:单位产品的一般质量特性不符合规定或质量特性轻微不符合规定。
美国贝尔系统将不合格的严重程度性分为四级。
A级——非常严重(不合格分值100分)B级——严重(不合格分值50分)C级——中等严重(不合格分值10分)D级——不严重(不合格分值1分)(2)不合格品:具有一个或一个以上不合格的单位产品。
按不合格的重轻程度可划分为A类不合格品、B类不合格品、C类不合格品。
5.检查批及批量(1)检查批:是提交进行检验的一批产品,也是作为检验对象而汇集起来的一批产品。
(2)批量:批中所包含的单位产品数,即提交检查的一批产品中所包含单位产品的总数,以N表示。
错检率与漏检率

错检:就是把合格品当成了不合格品(即在检验后的不合格品中还有合格品)。
漏检:就是把不合格品当成了合格品(即在检验后的合格品中还有不合格品)。
错检是由于各种因素造成检验失误、错判,主要是由客观因素造成。
漏检是由于部分或全部项目没有经过检验、判定就流入下一道工序,大部分是由主观因素或管理原因造成的。
当产品的质量主要靠检验把关的情况下,检验人员的检验能力就成了质量控制的关键因素。
本文提供一种考核方法,供本公司的客户参考。
各单位应该根据本单位和被检验产品的具体情况加以采用。
一、考核准备•明确考核的范围——事先告诉被考核者,这次检验要求查出哪些不合格的问题。
这些不合格的判别准则是什么。
必要时应该事先用不合格样品向被考核者展示。
确信被考核者理解后才能进行。
如果从生产线上抽调检验员进行考核时,应该按照生产规定的要求,检查出应该查出的各种不合格问题。
•考核材料——总的检验样件数N(100件)。
它包括两部分:i. 数量A(不少于50件)的不合格品。
每件存在多多少少不等的某种不合格问题。
这个数量A应该包容各种典型的不合格类型。
至少必须包容顾客认为接受不了的各种问题。
ii. 数量B的合格品。
iii. 把A 和B混合起来。
由考核者用粘胶纸对每个产品编上号码。
根据号码事先分别记录A 中有哪些不合格问题,数量多少。
譬如,第1个产品有跳针2处、污油渍1处、定线外露1处。
第3个产品有脱针1处、针洞2处、没有商标1处、缝子吊1处、对位不准1处。
当然。
不能让被考核者知道。
•设计一张记录表格——上面第1行列出要求检查发现的不合格问题。
从第2行起顺序编上产品的号码。
要求被考核者把所检验产品发现的不合格问题和数量分别对应填写在该编号产品内。
•规定检验时间——根据日常生产的检验平均时间规定在一定时间内检验完这些产品数N。
二、考核办法•把N数量产品按照顺序排好,交给被考核者,要求在规定时间内检验完。
•当被考核者发现自己认为是不合格的问题,用贴粘胶纸的办法做标志,并在表格对应的不合格问题中填写数量。
漏检率计算公式范文

漏检率计算公式范文漏检率是指在检测过程中未能发现异常或错误的比例。
对于一个检测系统而言,不同的检测方法和策略会导致不同的漏检率。
下面将介绍两种常见的漏检率计算公式。
1.漏检率的基本计算公式:漏检率=漏检样本数量/总样本数量其中,漏检样本数量是指在检测中未检测到的异常样本数量,总样本数量是指检测过程中的样本总数。
例如,批产品有100个,经过检测发现有5个样本存在异常但未被检测到,那么漏检率=5/100=0.05=5%。
这种计算公式直观简单,适用于大多数情况。
但是,如果总样本数量很大,而漏检样本数量相对较小,则漏检率会很低,不足以准确评估检测系统的性能。
因此,有时候需要使用更复杂的漏检率计算方法。
2.统计学中的漏检率计算公式:统计学中提出了一种漏检率计算方法,使用二项分布来考虑样本发生异常但未检测到的情况。
该计算方法将检测系统的灵敏度和样本分布考虑进来,给出了更准确的漏检率计算结果。
漏检率=1-(1-灵敏度)^n其中,灵敏度是指检测系统能够检测到异常样本的概率,n是总样本数量。
例如,检测系统的灵敏度为0.95,检测的样本数量为100,那么漏检率=1-(1-0.95)^100≈0.999=>0.1%。
这种计算方法更加准确,反映了检测系统的真实性能。
但是,需要确切知道检测系统的灵敏度,并且假设样本之间是相互独立的。
如果灵敏度无法准确估计或样本之间不是相互独立的,计算结果可能存在一定误差。
总结起来,漏检率是评估检测系统性能的重要指标之一、根据实际情况可以选择不同的计算公式,简单计算公式适用于大多数情况,统计学中的计算公式更精确但需要更多的参数信息。
漏检率
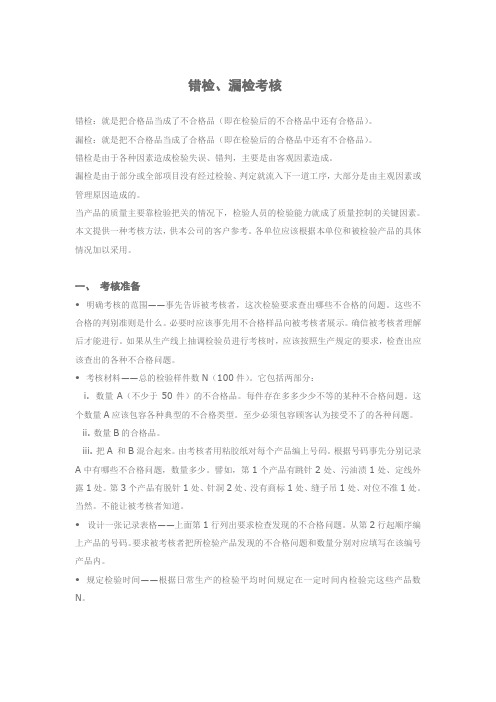
错检、漏检考核错检:就是把合格品当成了不合格品(即在检验后的不合格品中还有合格品)。
漏检:就是把不合格品当成了合格品(即在检验后的合格品中还有不合格品)。
错检是由于各种因素造成检验失误、错判,主要是由客观因素造成。
漏检是由于部分或全部项目没有经过检验、判定就流入下一道工序,大部分是由主观因素或管理原因造成的。
当产品的质量主要靠检验把关的情况下,检验人员的检验能力就成了质量控制的关键因素。
本文提供一种考核方法,供本公司的客户参考。
各单位应该根据本单位和被检验产品的具体情况加以采用。
一、考核准备•明确考核的范围——事先告诉被考核者,这次检验要求查出哪些不合格的问题。
这些不合格的判别准则是什么。
必要时应该事先用不合格样品向被考核者展示。
确信被考核者理解后才能进行。
如果从生产线上抽调检验员进行考核时,应该按照生产规定的要求,检查出应该查出的各种不合格问题。
•考核材料——总的检验样件数N(100件)。
它包括两部分:i. 数量A(不少于50件)的不合格品。
每件存在多多少少不等的某种不合格问题。
这个数量A应该包容各种典型的不合格类型。
至少必须包容顾客认为接受不了的各种问题。
ii. 数量B的合格品。
iii. 把A 和B混合起来。
由考核者用粘胶纸对每个产品编上号码。
根据号码事先分别记录A中有哪些不合格问题,数量多少。
譬如,第1个产品有跳针2处、污油渍1处、定线外露1处。
第3个产品有脱针1处、针洞2处、没有商标1处、缝子吊1处、对位不准1处。
当然。
不能让被考核者知道。
•设计一张记录表格——上面第1行列出要求检查发现的不合格问题。
从第2行起顺序编上产品的号码。
要求被考核者把所检验产品发现的不合格问题和数量分别对应填写在该编号产品内。
•规定检验时间——根据日常生产的检验平均时间规定在一定时间内检验完这些产品数N。
二、考核办法•把N数量产品按照顺序排好,交给被考核者,要求在规定时间内检验完。
•当被考核者发现自己认为是不合格的问题,用贴粘胶纸的办法做标志,并在表格对应的不合格问题中填写数量。