汽车用高强钢有新进展
武钢汽车用热轧低合金高强钢的开发进展
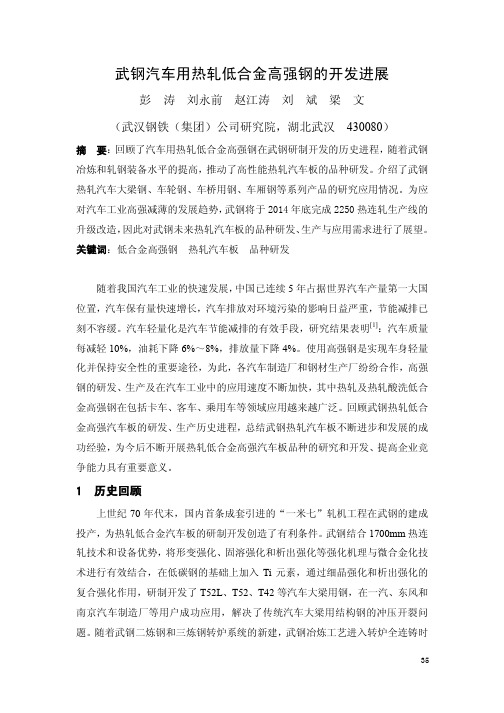
2002 年,武钢与东风汽车联合开发 590MPa 级大梁钢 WL590,成功应用于
重卡纵梁、车厢边板中支柱等零部件的制造,使用效果良好。2009 年武钢开发
出 700MPa 级大梁钢 WL700,批量应用于东风商用车、江淮汽车等厂家制造重
卡纵梁。
为应对未来的高强化发展趋势,武钢成功开发出更高级别大梁钢 WL750 和
作的加大以及高速公路计重收费工作的开展,公共物流领域车辆对降低自重的要
求也越来越强烈。车厢厢体用钢也由最初的 Q235、Q345 级别提高至 Q500 强度
级别,少量车型上对更高强度级别的车厢用钢也有需求。在这种市场需求下,并
随着武钢 CSP 产线的投产,武钢车厢用钢于 2011 年逐步投放市场。从最开始的
武钢汽车用热轧低合金高强钢的开发进展
彭 涛 刘永前 赵江涛 刘 斌 梁 文
(武汉钢铁(集团)公司研究院,湖北武汉 430080)
摘 要:回顾了汽车用热轧低合金高强钢在武钢研制开发的历史进程,随着武钢 冶炼和轧钢装备水平的提高,推动了高性能热轧汽车板的品种研发。介绍了武钢 热轧汽车大梁钢、车轮钢、车桥用钢、车厢钢等系列产品的研究应用情况。为应 对汽车工业高强减薄的发展趋势,武钢将于 2014 年底完成 2250 热连轧生产线的 升级改造,因此对武钢未来热轧汽车板的品种研发、生产与应用需求进行了展望。 关键词:低合金高强钢 热轧汽车板 品种研发
进入 21 世纪,随着汽车行业的蓬勃发展和高强减薄的发展趋势,对高性能 热轧汽车板的需求进一步增加,与此同时高性能产品对生产装备工艺要求提出更 高需求,武钢在对 1700mm 热轧机组进行技术改造的同时,新建了当时世界上技 术水平最高的 2250mm 热连轧机组,该机组先进的板形、尺寸控制系统及除磷系 统为生产高表面质量和高尺寸精度的热轧汽车板提供了基础,高精度层流冷却控 制系统和大功率卷取机为生产高强度热轧汽车板以及先进高强钢提供了有力保 障。在此期间,武钢将微合金化技术、洁净钢生产技术以及相变强化等进行了有 机的结合,在热轧汽车板的开发上实现了新的突破。大梁钢 WL590[4]、W610L、 WL650、WL700 和 WL750 获得大批量生产,450~650MPa 级车轮钢成功研发并 批量应用,510MPa 和 590MPa 级热冲压及冷冲压汽车桥壳用钢开发成功,铁素 体马氏体型热轧双相钢 DP600 和铁素体贝氏体型高扩孔钢 FB45、FB60 作为热 轧先进高强钢研制成功,并在汽车行业获得批量应用[5]。武钢 CSP 连铸连轧机组 的投产还为生产薄规格高强度热轧汽车板提供了有利条件,目前已在 CSP 机组 开发了最薄厚度为 1.2mm 的高强度汽车车厢板等汽车结构钢系列品种。
新型超高强钢突破2000MPa强度极限
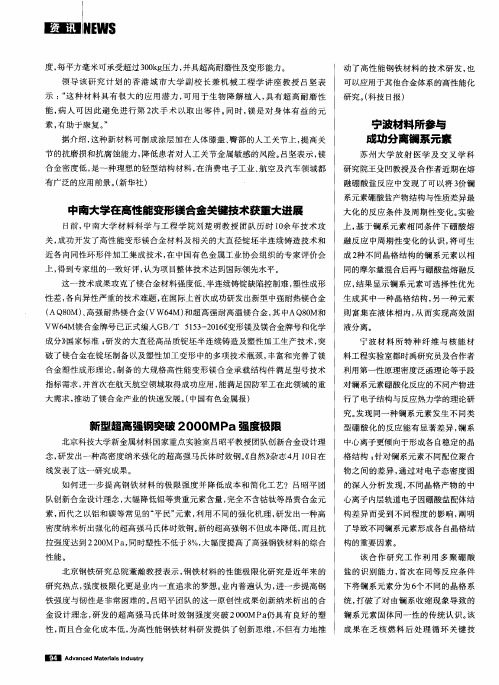
I
匿洄
£ WS
度, 每平方毫 米可承受 超过 3 0 0 k g 压力 , 并具超 高耐磨性 及变形 能力 。 领 导 该 研 究 计 划 的 香 港 城 市 大 学 副 校 长 兼机 械 工程 学 讲 座 教 授 吕坚 表 示 : “ 这 种 材 料 具有 很 大 的 应 用潜 力 ,性 能, 病 人可 因此 避 免 进 行 第 2 次手 术 以取 出零 件 。 同时 , 镁 是 对 身体 有 益 的 元
密度 纳米析 出强化 的超高 强马 氏体 时效钢 。 新 的超高强 钢不但成 本 降低 , 而且 抗 拉 强度达 到 2 2 0 0 MP a , 同时塑性不 低于 8 %, 大幅度提 高 了高强钢铁 材料 的综合
性能。
匕 京 钢铁 研究 总 院董 瀚教 授表 示 , 钢铁 材料 的性 能极 限化研 究是 近年 来 的 研 究 热点 , 强度 极 限化更是 业 内一直 追求 的梦想 。 业 内普 遍认 为 , 进一 步提 高钢 铁 强度 与韧性 是 非常 困难 的。 吕昭平 团 队的这一 原创 性成果 创新 纳米 析 出的合
大化 的反 应条 件 及周 期性 变 化。 实验 上, 基于 镧 系元 素相 同条 件 下硼 酸熔 融反 应 中周 期性 变化 的认 识 , 将 可生
成2 种 不 同晶格结 构 的镧 系元 素 以相
关, 成 功开 发了 高性 能变形 镁合金 材 料及相 关的 大直 径锭坯 半连 续铸 造技术 和
料 工程实 验室都 时禹研究 员及合作 者 利用第一性 原理密 度泛 函理 论等手段
对 镧系元 素硼酸化 反应 的不 同产物 进
行 了电子 结构与反 应热力学 的理论研 究。 发 现 同一种 镧 系元 素发 生不 同 类
中国汽车用钢行业市场现状行业发展趋势及未来前景预测
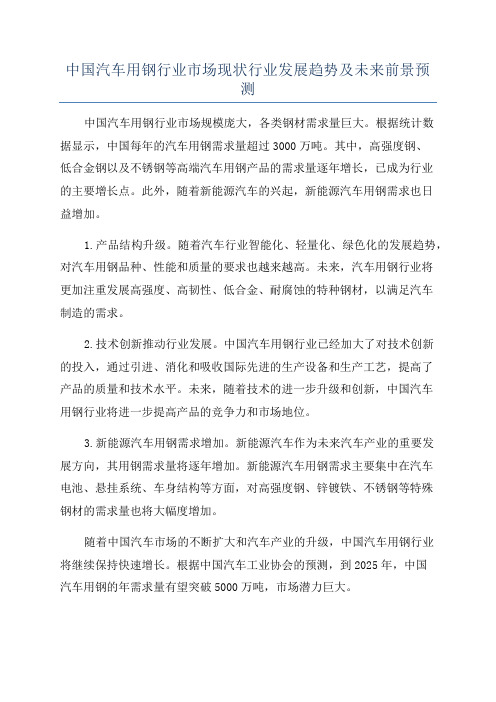
中国汽车用钢行业市场现状行业发展趋势及未来前景预测中国汽车用钢行业市场规模庞大,各类钢材需求量巨大。
根据统计数据显示,中国每年的汽车用钢需求量超过3000万吨。
其中,高强度钢、低合金钢以及不锈钢等高端汽车用钢产品的需求量逐年增长,已成为行业的主要增长点。
此外,随着新能源汽车的兴起,新能源汽车用钢需求也日益增加。
1.产品结构升级。
随着汽车行业智能化、轻量化、绿色化的发展趋势,对汽车用钢品种、性能和质量的要求也越来越高。
未来,汽车用钢行业将更加注重发展高强度、高韧性、低合金、耐腐蚀的特种钢材,以满足汽车制造的需求。
2.技术创新推动行业发展。
中国汽车用钢行业已经加大了对技术创新的投入,通过引进、消化和吸收国际先进的生产设备和生产工艺,提高了产品的质量和技术水平。
未来,随着技术的进一步升级和创新,中国汽车用钢行业将进一步提高产品的竞争力和市场地位。
3.新能源汽车用钢需求增加。
新能源汽车作为未来汽车产业的重要发展方向,其用钢需求量将逐年增加。
新能源汽车用钢需求主要集中在汽车电池、悬挂系统、车身结构等方面,对高强度钢、锌镀铁、不锈钢等特殊钢材的需求量也将大幅度增加。
随着中国汽车市场的不断扩大和汽车产业的升级,中国汽车用钢行业将继续保持快速增长。
根据中国汽车工业协会的预测,到2025年,中国汽车用钢的年需求量有望突破5000万吨,市场潜力巨大。
未来,中国汽车用钢行业将继续朝着创新、绿色、可持续发展的方向迈进。
在产品结构升级方面,中国汽车用钢行业将加大对高端特种钢材的研发和生产,以提高产品质量和竞争力。
在技术创新方面,中国汽车用钢行业将加强与相关科研院所和高校的合作,推动技术进步和产业升级。
同时,随着新能源汽车的发展,中国汽车用钢行业将加大对新能源汽车用钢的研发和生产,以满足市场需求。
总之,中国汽车用钢行业市场现状良好,发展前景广阔。
随着中国汽车市场的继续增长和汽车产业的升级,中国汽车用钢行业有望迎来更加美好的未来。
新型车辆碰撞防护材料研究与应用

新型车辆碰撞防护材料研究与应用在现代社会,交通事故频发,车辆碰撞防护成为了重要的研究领域。
为了提高车辆乘坐者的安全性能,科学家们投入大量精力研究和应用新型车辆碰撞防护材料。
本文将探讨新型车辆碰撞防护材料的研究与应用,包括材料的特点、发展趋势和主要应用领域。
首先,新型车辆碰撞防护材料具备一系列重要特点。
首要的特点是高吸能性能。
在碰撞过程中,车辆乘坐者会受到冲击力的影响,高吸能的材料能够吸收冲击能量,减缓乘坐者所承受的压力。
其次,新型材料具备较低的密度,可以减轻车辆整体重量。
低密度的材料比传统材料更轻巧,有助于提高车辆的燃油经济性和减少污染排放。
此外,新型材料要具备良好的可加工性和成本效益,以便大规模应用于车辆制造业。
随着科技的进步,新型车辆碰撞防护材料的研究和应用得到了极大的发展。
一种重要的新型材料是高强度钢(TWIP和TRIP钢)。
高强度钢具有优异的可塑性和耐用性,能够有效吸收碰撞能量,减少车辆乘坐者的受伤风险。
此外,碳纤维增强复合材料也被广泛应用于车辆制造中。
碳纤维材料具有轻质高强度、刚性好等优点,能够提供卓越的碰撞保护性能。
同时,镁合金和铝合金也被用作车辆碰撞防护材料。
与传统的钢材相比,镁合金和铝合金具有较低的密度和较高的强度,可以减轻车辆整体重量,并提供可靠的碰撞保护。
新型车辆碰撞防护材料的研究和应用还面临着一些挑战。
首先,这些材料的制造过程相对复杂,需要高端技术和设备的支持。
制造过程中的工艺控制和质量保证也是一个关键问题。
其次,新型材料在制造成本方面可能会比传统材料更高,这限制了其大规模应用。
另外,新材料与传统材料相比,相对较新,还需要进一步的研究和验证,以确保其性能的可靠性和稳定性。
尽管面临一些挑战,新型车辆碰撞防护材料仍在不断发展并得到广泛应用。
目前,新型材料已经应用于汽车和公共交通工具的制造中。
这些材料可以保护乘坐者在碰撞中的安全,并减少受伤风险。
此外,新材料还可以提高车辆的燃油经济性和减少污染排放,符合可持续发展的要求。
先进材料在汽车结构设计中的应用
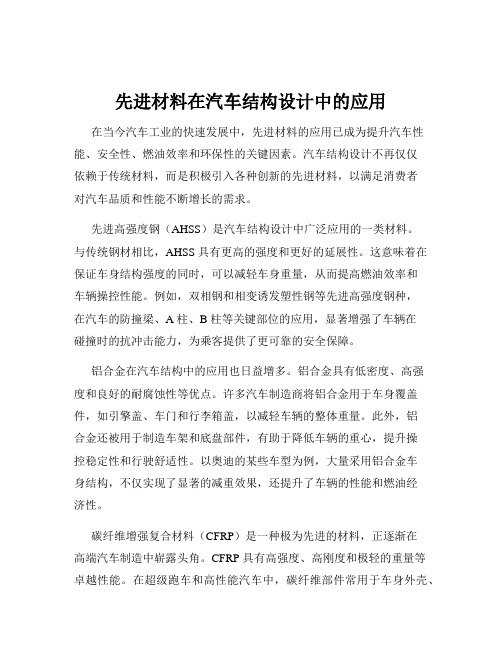
先进材料在汽车结构设计中的应用在当今汽车工业的快速发展中,先进材料的应用已成为提升汽车性能、安全性、燃油效率和环保性的关键因素。
汽车结构设计不再仅仅依赖于传统材料,而是积极引入各种创新的先进材料,以满足消费者对汽车品质和性能不断增长的需求。
先进高强度钢(AHSS)是汽车结构设计中广泛应用的一类材料。
与传统钢材相比,AHSS 具有更高的强度和更好的延展性。
这意味着在保证车身结构强度的同时,可以减轻车身重量,从而提高燃油效率和车辆操控性能。
例如,双相钢和相变诱发塑性钢等先进高强度钢种,在汽车的防撞梁、A 柱、B 柱等关键部位的应用,显著增强了车辆在碰撞时的抗冲击能力,为乘客提供了更可靠的安全保障。
铝合金在汽车结构中的应用也日益增多。
铝合金具有低密度、高强度和良好的耐腐蚀性等优点。
许多汽车制造商将铝合金用于车身覆盖件,如引擎盖、车门和行李箱盖,以减轻车辆的整体重量。
此外,铝合金还被用于制造车架和底盘部件,有助于降低车辆的重心,提升操控稳定性和行驶舒适性。
以奥迪的某些车型为例,大量采用铝合金车身结构,不仅实现了显著的减重效果,还提升了车辆的性能和燃油经济性。
碳纤维增强复合材料(CFRP)是一种极为先进的材料,正逐渐在高端汽车制造中崭露头角。
CFRP 具有高强度、高刚度和极轻的重量等卓越性能。
在超级跑车和高性能汽车中,碳纤维部件常用于车身外壳、传动轴和悬架系统等部位。
其高强度和轻质量的特性使得车辆能够在高速行驶时保持出色的稳定性和加速性能。
然而,由于碳纤维材料成本较高,目前在大规模量产汽车中的应用还相对有限,但随着技术的不断进步和成本的降低,其应用前景十分广阔。
镁合金也是汽车结构设计中的新兴材料之一。
镁合金的密度比铝合金更低,具有良好的减震性能和可加工性。
在汽车内饰件、座椅框架和仪表盘支架等部件中使用镁合金,可以进一步减轻车辆重量,提高燃油效率。
同时,镁合金的减震性能有助于降低车内噪音和振动,提升乘坐舒适性。
汽车用高强度IF钢的研究进展

维普资讯
第5 期
李 守华 等 : 车用 高强 度 I 的研 究 进展 汽 F钢
6 7
以I F钢 为基础 发 展起来 的深冲热 镀锌 I F钢
度 为 1 0 1 2mm, 身 板 可 减 薄 至 0 7 0 8 . ~ . 车 . ~ .
mm, 车身重 量减 轻 1 ~2 , 油 8 ~1 %。 5 O 节 5 因此大 力发 展 高强 I F钢 对 汽 车 的 减 重 节 能降 低 汽 车 的生产 成本 有利 。
维普资讯
6 第 2 卷 第 5期 6 9
2 00 7年 9月
上 海 金
属
Vo _ 9 l2 No 5 .
Se e be ,20 pt m r 07
SH A N G H A I M ET A LS
汽 车用 高 强度 I F钢 的研 究进 展
L h u u Li u 。 i oha S n J
( S h o f Mae il n tlu g 1. c o l tra sa d Mea l r y,No te senUn v riy,S e a g1 0 4,Ch n o rh a tr ie st h n n 0 0 1 ia;
d e r wi r p ris Th te t e i c a s a d t e c n r lo eo d r r i mb i lme t o ih e p d a n p o et . g e e sr n h nn me h n m n h o to f sc n a y wo kn e rt e n f hg g g i g t
sr n t F t e r nto c d brel Ths p p re te h I se la e i r du e ify. i a e mph t al e ci s t e pr g e s i e e rh o ih sr n t F g a i l d srbe h o r s n r sa c f hg te h I c y g se lf ra t t e o uomo iea p iains tv p lc t o ,whc ee st r meofr fr n e i e e rh o e hg sr n t F te. ih prs nt hefa e ee c n r s a c fn w ih te g h I se 1
钢铁产品在新能源汽车领域的应用有哪些

钢铁产品在新能源汽车领域的应用有哪些在当今全球追求可持续发展和绿色能源的大背景下,新能源汽车产业蓬勃发展。
新能源汽车不仅代表着未来出行方式的变革,也对材料的性能和应用提出了新的要求。
钢铁作为一种传统的基础材料,在新能源汽车领域中依然发挥着重要作用。
首先,车身结构是钢铁产品在新能源汽车中的一个重要应用领域。
高强度钢在新能源汽车车身制造中占据着重要地位。
相较于传统汽车,新能源汽车由于搭载了沉重的电池组,车身重量有所增加。
为了弥补这一增重,同时保障车辆的安全性和操控性能,高强度钢的使用成为了关键。
高强度钢具有出色的强度和韧性,可以在减轻车身重量的同时,提高车身的抗碰撞能力,为乘客提供可靠的安全保障。
汽车的底盘部件同样离不开钢铁产品。
底盘作为支撑整个车辆的关键结构,需要具备高强度和高耐久性。
例如,悬架系统中的控制臂、转向节等部件通常由钢铁制造。
这些部件承受着车辆行驶过程中的各种力和冲击,优质的钢铁材料能够确保底盘的稳定性和可靠性,为车辆的操控性能奠定基础。
在新能源汽车的动力系统中,钢铁也有其用武之地。
电动机的外壳和内部结构件往往采用钢铁材料。
电动机在工作时会产生热量和振动,需要坚固的外壳来保护内部组件并进行有效的散热。
钢铁的良好导热性能和机械强度使其成为理想的选择。
此外,电池包的外壳和支架也常使用钢铁,以保护电池组免受外界冲击和环境影响。
新能源汽车的制造过程中,冲压工艺是常用的成型方法之一。
钢铁板材通过冲压可以制成各种形状复杂的零部件,如车门、引擎盖等。
先进的高强度钢冲压技术能够在保证零部件强度的前提下,实现更轻量化的设计,降低车辆能耗。
值得一提的是,不锈钢在新能源汽车中的应用也逐渐增多。
不锈钢具有良好的耐腐蚀性,能够在恶劣的环境条件下保持性能稳定。
例如,在车辆的排气系统中,不锈钢可以抵御高温和腐蚀气体的侵蚀,延长排气系统的使用寿命。
除了上述直接应用于车辆结构和组件的方面,钢铁产品在新能源汽车的生产设备和工装夹具中也发挥着重要作用。
2024年高强度钢板市场发展现状

2024年高强度钢板市场发展现状引言高强度钢板是一种具有较高强度和较低重量的钢材,广泛应用于汽车、机械制造、造船等领域。
本文将对高强度钢板市场的发展现状进行深入分析。
市场规模与增长趋势高强度钢板市场在过去几年持续增长,预计在未来几年仍将保持稳定增长。
据统计,2019年全球高强度钢板市场规模约为XX亿美元,预计到2025年将达到XX亿美元。
市场规模的增长主要源于以下几个因素。
首先,汽车行业的发展推动了高强度钢板市场的增长。
随着汽车行业对轻量化材料的需求增加,高强度钢板作为一种重要的轻量化材料得到广泛应用。
高强度钢板的使用可以降低汽车的整体重量,提高燃油效率和安全性能。
其次,机械制造行业对高强度钢板的需求也在不断增加。
高强度钢板具有优异的强度和韧性,适用于各种机械设备的制造。
随着机械制造业的发展和机械设备的更新换代,高强度钢板市场的需求持续增长。
再次,建筑和船舶行业对高强度钢板的需求也在快速增长。
高强度钢板在建筑和船舶领域具有重要的应用价值,可以提供强度和耐久性,满足特定的工程需求。
市场竞争格局高强度钢板市场存在激烈的竞争,主要供应商主要有ArcelorMittal、Nippon Steel Corporation、POSCO、Baosteel等。
这些供应商通过不断提高产品质量、拓展市场份额和加大研发投入来保持竞争优势。
此外,新兴的高强度钢板供应商也在积极进入市场。
这些新兴供应商通过技术创新和定制化服务来满足特定需求,与传统供应商形成一定的竞争。
市场驱动因素高强度钢板市场发展的驱动因素主要包括以下几点。
首先,环保意识的提升推动了高强度钢板的需求。
高强度钢板可以减少材料的使用量,降低能源消耗和碳排放,符合可持续发展的要求。
其次,行业对轻量化材料的需求增加也是推动市场发展的重要因素。
高强度钢板作为一种轻量化材料,可以提高产品的性能并降低成本,符合行业的需求。
再次,技术的进步也推动了高强度钢板市场的发展。
- 1、下载文档前请自行甄别文档内容的完整性,平台不提供额外的编辑、内容补充、找答案等附加服务。
- 2、"仅部分预览"的文档,不可在线预览部分如存在完整性等问题,可反馈申请退款(可完整预览的文档不适用该条件!)。
- 3、如文档侵犯您的权益,请联系客服反馈,我们会尽快为您处理(人工客服工作时间:9:00-18:30)。
∙∙分类:国际新闻创建于2013年7月11日星期四10:14最后更新于2013年7月11日星期四10:14作者:Super User点击数:9浦项制铁技术研究实验室 Young Sool Jin 郭金宇译在现在和未来的汽车上,汽车的减重成为减少CO2排放和降低燃油消耗的关键手段。
同时,复合动力车和电动车更加要求车身减重。
包括有色金属在内的轻量化材料中,从技术和经济性的观点来看,先进高强钢是最有应用前景的汽车用材料。
根据调查,先进高强钢在汽车用钢的比例将从2009年的7%增加到2020年的28%~36%,特别是在亚洲国家,比例将更高。
此外,在未来的白车身和覆盖件上,铝合金的用量也将大幅度增加。
考虑到未来的应用前景,钢铁行业应加快先进高强钢和相关应用技术的研究与发展。
多种高强钢物尽其用为了满足汽车工业在提高安全性、燃油经济性、耐用性和舒适性等方面的要求,钢铁企业开发了多种钢材并应用在车身结构上,更加先进的新型汽车用钢也正在加紧研发中。
强塑积小于25000MPa%的汽车用钢已经广泛应用在汽车行业,如IF钢、HSLA(高强低合金)钢、传统的先进高强钢(AHSS)如DP(双相)钢、TRIP(相变诱导塑性)钢、CP(复相)钢、马氏体钢和HF(热冲压成形)钢。
另外两组钢,分别称为超高强度先进高强钢(X-AHSS)和超高强度先进高强钢(U–AHSS),具有优越的强度和塑性平衡,强塑积大于25000MPa%,被称为下一代汽车用钢。
而这些先进高强钢的微观组织包括铁素体、贝氏体、马氏体和残余奥氏体等组织。
那么,传统先进高强钢有何最新发展,下一代先进高强钢的研发进展如何?附表总结了浦项制铁先进高强钢的研发情况。
热轧先进高强钢。
为了得到性能优异的热轧双相钢、铁素体-贝氏体钢和TRIP钢,在工艺过程中需要优化钢种的成分、轧制工艺和冷却速率。
总的说来,热轧终轧温度大于Ar3点,冷却过程采用2步法进行控制。
中间的冷却温度和空冷时间会对铁素体转变行为产生影响,如铁素体的体积、形态,以及未转变奥氏体的富碳情况。
热轧卷最终的卷曲温度会对产品的微观组织产生影响。
采用低C-Mn-Si的成分体系,590MPa级和780MPa级DP钢的卷曲温度设定在马氏体转变温度以下,冷却后直接得到铁素体和马氏体组织。
980MPa级DP钢采用低C-Mn-Si-Cr的成分体系,卷曲温度在马氏体转变温度以上。
通过添加Cr提高钢卷的淬透性,残余奥氏体在卷曲后转变为马氏体。
双相钢主要用在要求良好强度和塑性平衡以及低屈服强度的车轮和汽车悬挂件等零部件上。
为了得到扩孔性能优良的FB钢(铁素体-贝氏体双相钢),减小基体和第二相之间的碳含量和硬度的差别是至关重要的。
低C-Mn系590MPa级、低C-Mn-Si系的780MPa级和980MPa级FB钢的卷曲温度在贝氏体转变温度以下,用来抑制出现马氏体和粗大的渗碳体。
FB 钢具有优异的扩孔性能、高屈强比和在焊接区域硬度变化小的特点。
TRIP钢采用C-Mn-Si-Nb的成分体系,热轧后的780MPa级TRIP钢卷曲温度在贝氏体转变温度以下。
在终轧后和水冷前,钢卷会在铁素体区停留几秒钟,这时碳会从铁素体中扩散出来进入到未转变的奥氏体区。
如果富碳不足,在TRIP钢冷却过程中会出现马氏体。
由于TRIP 效应,TRIP钢具有良好的成形性能,但由于焊接性能不如DP钢,TRIP 钢并没有广泛应用。
冷轧和退火的先进高强钢。
DP钢具有良好的强度和塑性平衡和低屈强比的特点,广泛应用于汽车车身。
相比于TRIP钢,DP钢由于碳含量低,因此具有良好的焊接性能。
在热镀锌过程中,相比于TRIP 钢,DP钢具有更好的表面质量。
DP钢应用在汽车外板正成为一种趋势。
然而,低r值和表面质量因素却限制了DP钢在汽车外板和内部深冲件的应用。
由于DP590具有高抗凹性,近期浦项进行了DP590用于汽车外板的试验,将汽车板厚度由0.7mm减小到0.55mm。
TRIP钢具有良好的成形性能,其延伸率要明显大于相同强度级别的DP钢。
然而,硅元素的添加会降低钢板的表面质量和焊接性。
研究人员采用了很多方法去解决上述问题,如:采用铝代硅的合金成分体系、退火过程中采用预氧化、添加推迟氧化的元素和降低碳含量等。
抗拉强度为1180MPa的CP钢具有高屈复强度和高冷弯性能,主要应用在汽车车身的加强件上。
由于在退火过程中抑制了铁素体转变,CP钢主要含有贝氏体、少量的铁素体和马氏体。
由于钢中碳和硅含量低,CP钢具有良好的点焊性能和镀锌性能。
冷轧和热镀锌马氏体钢也已经研发出来并主要应用在汽车前端的安全件和防撞件上。
热冲压成形钢。
浦项开发了新的具有高锰氮成分体系的热冲压成形钢。
这种钢的优点是可以在较低的加热温度(850℃)下完全奥氏体化,并且在冷却过程中能够完全转变为马氏体,相比于传统的22MnB5钢,其完全奥氏体化温度为880℃。
该钢种的冲压温度要大于850℃,如果加热温度低于850℃或者说加热温度低于完全奥氏体化温度,三点弯曲的断裂角度就会明显下降,这是因为应力会在残余铁素体中集中。
热冲压成形钢的应用范围很广,并且需要表面镀锌。
然而,锌基涂层在热冲压过程中容易氧化和蒸发,并且容易发生断裂。
浦项开发了一种新的含Zn涂层来解决上述问题。
新涂层的特征是在加热过程中能够形成稳定的Fe-Zn,合金层中富Zn的区域很小。
形成的涂层在热冲压过程中也不会出现液态金属脆性敏感的问题。
新研发的合金涂层在热冲压过程中在基板上不会出现裂纹。
表1 浦项先进高强钢的研发状态○实验室开发, ●商业供货超高强度钢更追求轻量化超高强度钢(X–AHSS)和轻量化钢。
被称为超高强度钢的第二代汽车用钢,其强塑积大于25000MPa%,近年来吸引了广泛的关注。
所有的研究都是利用残余奥氏体向马氏体相变的方法来得到高的延伸率。
人们通过添加锰和碳元素来得到足够的奥氏体,在连退过程中的部分逆转变也被采用。
在逆转变过程中,锰和碳在奥氏体中的偏聚增加了奥氏体的稳定性。
通过将退火温度精确控制在Ac1和Ac3之间,我们可以得到晶粒尺寸在200nm~500nm的铁素体和奥氏体。
残余奥氏体的数量约为20%~30%,抗拉强度在1033MPa~1389MPa,延伸率在27.5%~28.8%,强塑积在28408MPa%~40003MPa%之间。
轻重量钢主要是指含有Mn和Al的成分体系为Fe-18~28Mn-9~12Al-0.7~1.2C的合金系。
Fe-26Mn-11Al-1.15C钢的微观结构为“三相复合结构”,即在奥氏体基体中含有6%~8%的铁素体和纳米尺寸的碳化物。
然而,浦项正在研制新型的复相钢,其特征为:钢中含有较低含量的Mn元素和Al元素,微观组织为具有30%~40%奥氏体的复相钢。
由于残余奥氏体的TRIP效应,这种钢的抗拉强度约为780MPa~830MPa,延伸率约为40%,强塑积约为30000MPa%~35000MPa%,属于超高强度钢。
相比于传统钢铁材料,钢板密度减小约10%。
由于在600℃~1200℃钢板的热塑性只有67%,通过连铸可以得到表面质量良好的铸坯。
TWIP钢。
TWIP钢由于具有不同的加工硬化行为而具有优异的力学性能。
最近浦项开发了抗拉强度在980MPa、延伸率在60%以上的冷轧TWIP钢。
并且抗拉强度为900MPa、1000MPa和1200MPa级TWIP钢也已经开发成功并用来满足汽车工业的要求。
通过优化合金成分,具有相同性能的热镀锌TWIP钢已经开发成功,不久后将实现商业供货。
通过将锰含量控制在13%~18%、碳含量控制在0.4%~0.7%,我们可以得到稳定的奥氏体。
通过添加1.5%~2.0% 的Al元素来调整钢的层错能。
Al元素对防止碳化物析出和降低氢致裂纹有益。
TWIP钢不仅具有良好的强塑性,并且在钢卷的横向和纵向上强度和延伸率的变化很小,这是由于在连退过程中没有发生相变。
TWIP980钢板首先应用在防撞梁上。
通过使用TWIP钢来替换原来的DP600,汽车厂家在提高碰撞性能的前提下,减重28%,降低成本22%。
未来将会有更多的TWIP钢应用在车身零件上。
热镀锌技术改善钢材性能为了得到优异的性能,先进高强钢大多含有较多的Si、Mn、B 元素,这些元素会在镀锌过程中降低钢板的润湿性。
为了解决上述问题,人们开发了使用预氧化、预镀和露点控制等方法来改善润湿性。
在露点为-40℃的退火条件下,在气氛为N2+10%H2时可以观察到非晶的Si-Mn氧化物,在气氛为100%N2条件下,观察到Mn的氧化物。
100%N2气氛退火条件下可以得到良好的润湿性,这是由于镀锌过程中氧化锰比Si-Mn氧化物更容易被还原。
在退火条件下我们可以得到不同的氧化物,如Mn2SiO4、SiO2 和MnO,在N2或空气条件下我们可以得到厚的Mn2SiO4和内氧化物,这些会表现出更好的润湿性。
预氧化控制。
成分为0.08C-1.6Mn-1.5Si的590MPa级TRIP钢在连退线上实现热镀锌,其中加热段是在具有氧化气氛的直接火焰加热炉进行,还原段是在辐射管加热炉进行。
可以在还原的铁层和Si-Mn氧化物层之间发现一层均匀的Al分隔层,尽管热镀锌TRIP590具有良好的表面质量,在表面没有发现漏镀点,但是在t=0的弯曲和胶带试验时,镀层有脱落的现象。
切面的XPS试验结果表明,脱落发生在Si-Mn氧化物和还原Fe之间。
预氧化并不能完全保证含Si热镀锌TRIP钢的镀层质量,这意味着我们需要精确的测量和控制氧化物的厚度。
根据反射光谱分析技术,浦项开发了在线测量系统。
这个系统安装在DFF段和RTF段出口位置,测量的精度通过在DFF段出口处取样和实验室制备的样品进行测量比较。
在线测量的精度与通过GDS测量的对比结果表明,在线测量系统具有很高的精度。
合金元素的作用。
最近,一些学者研究了P、B、Sn、Sb等微量元素对氧化物结构的影响。
这些元素通过析出在晶界和金属表面,限制了短程扩散,这样可以有效地控制表面的氧化物。
P在晶界上的偏聚可以限制Si在晶界上的扩散,P元素有利于形成Mn-P复合氧化物并且限制SiO2在表面的形成。
相比于钢中的其他元素,B氧化物非常容易形成。
因此在退火过程中,在距离表面50um~100um处B元素是贫化的,大多数处于钢板表面的B元素会形成氧化物消耗掉。
B2O3的熔点很低,大约在450℃左右,随着含量的增加,Mn-Si-B复合氧化物的熔点下降。
添加小于10ppm的B对AHSS钢的性能是有利的,但是当B 含量超过10ppm时,会降低镀锌板表面质量和产生漏镀。
在生产热镀锌DP590钢板时,含有7ppm的B含量的钢板具有良好的表面质量。
Sb元素容易在钢板的晶界和表面处析出,这一点对AHSS钢板的氧化控制是有利的。
添加Sb元素有利于使钢板表面的氧化物减少、细小和均匀。