输送带工艺简介
输送带生产工艺及设备

第31卷 第10期第18页输送带生产工艺及设备曾宪奎1山东 青岛 266042本文从宏观的角度全面介绍了输送带的分类和用途文章还介绍了多种典型的输送带生产线覆盖胶挤出生产线并以德国S i e m p e l ka m p公司产品为例关键词输送带设备B文章编号曾宪奎副教授原青岛化工学院发表论文20余篇2004-12-27输送带是用于输送松散物料或成品物件的带式输送机上的关键部件覆盖胶和带芯胶输送带的生产和使用已有近百年的历史码头工厂等都有输送带在应用随着输送带的快速发展除通用设备外所用材料的性质和输送带的结构决定的主要有以下几种方式1主要用于层叠式帆布带芯普通输送带的制造浸渍式冷胶片贴合式橡胶型3用于输送带骨架材料浸渍设备2 橡胶型输送带生产工艺橡胶型输送带基本制造工艺包括混炼胶加工成型也可采用同样的设备和工艺混炼胶在进入压延机之前需经预热处理以达到一定的温度和均匀塑性以往预热以采用开炼机为主压延工序主要完成织物擦胶多采用四辊压延机压延擦胶胶料应渗透到织物结构中去以产生机械结合合成纤维织物和钢丝绳编织物都采用贴胶但经过擦胶的棉织物贴一面即可带坯与覆盖胶贴合则是利用压延机将带坯1次2面贴上覆盖胶温度控制和胶料通过量需平衡造成焦烧轻贴或冷纹2织物的预加张力大约是其断裂强度的2%~3%42侧贴上边胶成型质量最基本的要求是在各布层保持张力一致的情况下一次贴合成型为无张力控制下的自由贴合影响了输送带的强度和承载能力跑偏和跑长等现象它可在张力下一次操作完成5层胶布的贴合成型供生产大宽度钢丝绳芯输送带使用此法是基于输送带的减层化趋势而出现的再在压延机上贴上下覆盖胶生产效率也高第31卷 第10期第20页如图2所示压辊及转鼓组成帆布经擦胶压延机擦胶后并由其送出卸下针铗经压合形成带圈在贴合机传动鼓前剪开带芯卷送至压延机联动装置贴覆盖胶胶布张力均衡贴覆盖胶在压延机联动装置上进行成型好的带芯由导开装置导开导开装置可根据定中心气动传感器的信号进行位置调整同带芯贴合在一起由输送带送到压延机贴好覆盖胶的带坯通过胶片包边装置和牵引辊将带边包上胶片带坯端部由端部胶条贴合装置贴上端部加固胶条挂胶帆布的贴合始终在恒张力同时免去了成型过程中胶布的来回运输但装备投资大3.3 硫化设备硫化除了追求输送带全宽度还应注在成型时应注意一个比较重要的工艺参数缩窄因数现在使用的合成纤维织物否则在平板硫化机上硫化时易产生带坯宽度与成品宽度之比就是缩窄因数是一个经验值前苏联和欧洲国家常用所谓供料开炼机345678~14而后用压延机联动装置贴覆盖胶12356781011121314151617保证均匀一致的张力是充分发挥输送带强伸性能的重要环节1234鼓式硫化机和新近出现的平板连续硫化机宽度为2~3m压力为2.5~3MPa与之配套的有导开目前为提高生产能力一次硫化二三条平带平板硫化机具有热板单位面积压力大平板硫化机的主要功能是提供硫化所需的压力和温度通常为蒸汽按液压系统工作介质则有油压和水压之分但目前则多采用框式结构维修量少上横梁受力合理其主要结构是用立柱及螺母或框板将上横梁和下横梁在每一个这样的部件内每个液压缸内有柱塞并用螺钉及连接板将各个活动平台连接成一体便构成整台柱式平带平板硫化机为此或活动平台此外或平动平台对于活动平台在其纵向的2端也设有纵向导套由此起到导向的作用但是由于框式平带平板硫化机的机架均为由多个框板组合而成图4所示为框式单层平板硫化机 23456789第31卷 第10期第22页在开机时为此利用该缸产生的拉力确保下热板的下降动作与上热板和下热板一起构成一个活动模腔达到对带坯进行加压硫化的目的在平板硫化机的前端设有夹持装置操作时然后用夹持装置分别夹住带坯的2端最后下热板上升加压硫化拉伸缸回复到拉伸前的初始位置硫化后必须在恒张力下进行冷却中夹持装置和后夹待拉伸装置3.3.2 鼓式硫化机鼓式硫化机在20世纪30年代即已出现钢带贴在硫化鼓上可硫化带宽为1 200~2 000 mm的输送带鼓式硫化机的不足之处是钢带的压力较低平带鼓式硫化机的工作原理如图5所示驱动压力带转动传动各辊筒及硫化鼓被紧压在硫化鼓的鼓面待从硫化鼓上面引出时由油缸的作用力使伸张辊对压力带施加张力便于与成型工序连接起来内部致密且可实现环形无接头硫化由于硫化连续进行其劳动强度也可大大降低其硫化厚输送带的质量和生产能力都比不上平板硫化机国外厚度在15 m m 以下的普通织物芯输送带和浅花纹输送带多采用鼓式硫化机二次加压把压力带对制品的压力从0.5 M Pa 提高到2 MPa 这就为生产厚制品以及提高制品的硫化效率创造了条件3.3.3 平板连续硫化机平板连续硫化机综合了平板硫化机和鼓式硫化机的优点估计通过适当改造还可用于生产钢丝绳芯输送带该机的硫化区域设有2组热板滚子链和钢带各自拥有独立的传动装置钢带传123456硫化时的压力可达3 M Pa该设备既可生产橡胶带也可生产PVC 或PVG带前面一组热板加热平板连续硫化机采用编程管理4 几种典型的输送带生产线4.1 输送带用压延连续生产线现代化输送带用压延生产线的制造和应用始于德国压延生产线采用自动控制S辊筒直径为750mm 最大加工宽度为2 250mm 与之相配套的有导开装置喂料辊直流驱动电机冷却系统其主要技术特征是进入压延机以前自动定中心自动切边和封边全过程微机管理冷却完全填充胶挤出机生产的覆盖胶片无气泡全宽度上的厚度误差小宽幅挤出机头牵引装置卷取和导开装置用于钢丝绳芯输送带挤出胶片宽度为800~2 300mm 最大挤出速率为4 500kg/h高速度和大运输量的散料输送胶带中并排铺放的钢丝绳必须平生产工艺要求很严格分梳夹持和张力装置牵引夹紧装置和卷取装置等带芯胶与覆盖胶是预先贴合后上线的贴合带芯胶和覆盖胶以及切边卷取和切断全过程不能因热板变形而造成局部欠压产生明疤国内生产钢丝绳输送带已有多年历史钢丝绳输送带生产线大致有2种类型带坯内的钢丝绳张力每硫化一段释放一次一次成型相当长度的带坯钢丝绳张力并不释放接着再次成型1234567第31卷 第10期第24页3.2~13 mm的钢丝绳钢丝绳卷由电动葫芦提升以便装载钢丝绳其最大初张力为400N每一层的钢丝绳装有倒卷的钢丝绳驱动装置钢丝绳导出后夹持平板类同于一般的液压机夹持平板的油缸由液压系统供给压力油每组张力辊由2个定滑轮1个动滑轮组成从而使每根钢丝绳在小油缸作用下产生张力其张力范围为834~3 090N成型小车上装有上钢丝绳上利用冷压平板的强大压力把胶片挤压到钢丝绳之间的空隙内每次只能挤压一小段带坯而且能渗透到钢丝绳结构的缝隙内一般认为譬如说60m下面以德国Siempelkamp 公司生产的钢丝绳输送带生产线为例进行介绍它包括钢丝绳导开架冷压平板牵引机及卷取机等生产线全长约116m下4层2345678910 1112131415161718挤压完毕的带坯带坯每成型完一段成型好的带坯由操作人员乘检查小车对其进行逐段检查与修补上述钢丝绳输送带生产线开始生产时张力装置通过牵引带的牵引此时牵引带的另一端穿过平板硫化机牵引机上的夹持装置把牵引带夹住张力装置施加张力当成型小车逐段把带坯成型到足够硫化一次的长度时而夹持平板开启由牵引机通过牵引带把成型好的带坯拉进平板硫化机内检查小车也随带坯一起移动这时牵引机的夹持装置把牵引带夹住带坯硫化时按照上述程序释放夹持平板 硫化好的输送带由牵引机牵引成型小车及检查小车随带坯一起移到靠近平板硫化机位置硫化的一个周期并把成品带头固定到卷取辊筒上进行卷取在硫化的输送带达到规定长度后2台卷取装置交替进行工作生产工艺以及现阶段比较先进的生产设备的原理及结构特点现阶段我国输送带行业已经取得了较大发展在今后随着工业的不断发展其应用将会更加广泛参考文献。
输送带的制作工艺解析

输送带zui重要的两个步骤:成型、硫化,这两个过程直接影响到输送带的使用时间、带体光洁度等,是输送带制造中最重要的环节。
1、输送带成型的生产工艺是看不到输送带的组成,根据设计出的输送带体的形状,成型后的输送带带有胚胎,这一步称为输送带的成型。
各种输送带由于机构类型不同,其成型方法也不同。
输送带和平型传动带均属平带。
平带成型有专用的成型设备,主要由布架、工作台、压辊、包布装置等组成。
在成形过程中,采用机械牵引、自动压合、卷取得连续流水作业,生产效率高。
输送带和平型传动带的成型是由多层一次性叠片组成,包括覆盖输送带的橡胶和平型传动带的对口胶及封口胶条。
贴合时主要要求布层张力均匀,经向布纹正直不偏,各层间压合紧密、无气泡。
2、硫化输送带、平型传动带多用液压蒸汽加热的平板硫化机硫化。
常用的平板固化度一般为3-10米,宽度在3米以下。
因为平板硫化长度有限,因为输送带需要分段硫化。
若采用鼓式硫化机硫化,可连续操作,可避免因接头部位二次硫化而产生硫的现象。
硫化时,输送带要有一定的伸缩性,硫化温度的选择不在此时,输送带容易出现明疤。
耐酸碱输送带耐热输送带设备工艺原理

耐酸碱输送带耐热输送带设备工艺原理前言输送带广泛应用于矿山、电力、化工、钢铁、建材等行业,用于物料的运输。
不同行业对输送带的要求也有所不同,例如在化工行业,需要一种耐酸碱、耐高温的输送带。
本文将介绍耐酸碱输送带和耐热输送带的设备工艺原理。
耐酸碱输送带耐酸碱输送带又称耐化学腐蚀输送带,其主要特点是能够承受酸碱性强、腐蚀性强的化学物料。
这种输送带通常采用三种结构:全芯型、凸缘型和波纹型。
全芯型全芯型耐酸碱输送带是将单层或多层骨架材料和橡胶覆盖料完全粘合,骨架材料通常是聚酯、尼龙、棉布等。
这种结构的优点是抵抗腐蚀性能好,但是耐热性能较弱。
凸缘型凸缘型耐酸碱输送带相对于全芯型,在覆盖料内侧设置凸缘,增加了带体的强度和稳定性,提高了耐张力性能,适用于高张力,化学腐蚀作用较弱的场合。
该结构的缺点是凸缘内侧容易积灰。
波纹型耐酸碱输送带是在全芯型、凸缘型的基础上加入波纹状槽口。
波纹型耐酸碱输送带具有比全芯型和凸缘型更好的横向刚度和强度,适用于各种轻、重型输送机械,但是其缺点也比较明显,容易在波峰处产生断裂。
适用场合耐酸碱输送带广泛适用于如下场合:1.化工厂、化肥厂、制药厂等化学腐蚀性强、易燃原料的输送;2.精细矿山、冶金、焦化、钢铁等领域的输送;3.神经酸、乙酸、浓硝酸、尿素、硫酸等化学品的传输。
耐热输送带耐热输送带主要用于耐高温物料的输送。
一般来说,聚氯乙烯(PVC)、聚丙烯酰胺(PAN)、氟化物、碳纤维等材料都具有较好的耐高温性能,可以用来制作耐热输送带。
结构耐热输送带结构与普通输送带相似,其覆盖层通常为聚氯乙烯、丁腈橡胶、热塑性聚氨酯等。
降低温度是保持耐热输送带寿命的主要方式,因此通常会在输送带内侧加入一层带有特殊成分的橡胶层。
耐热输送带的生产工艺过程主要分为以下几个步骤。
混炼在混炼机上对橡胶进行初始化,加入助剂和填充剂,再逐步加入其他物质。
生产厂家根据需要可以选择加入石墨、氟化物等耐热材料。
成型通过成型机器制作成特定的形状,通常是扁平的和V字型。
输送带工艺流程

输送带工艺流程输送带是指将物料从一个地方运送到另一个地方的装置。
它通常由带式输送机、辊道输送机、螺旋输送机等构成。
输送带的使用可以将物料运送从原料库至制成品库,提高生产效率、降低人工成本等。
下面我们来了解一下输送带的工艺流程。
一、物料装载物料首先需要装载到输送带上。
如果是较重的大块物料,可以使用机械设备进行装载,如挖掘机、装载机等;如果是较小的散装物料,可以使用人工或气动装载的方法进行装载。
在装载物料时,需要保证载荷的均衡分布,防止单边过重导致带子偏移、磨损。
二、输送带运行启动输送带,将物料从源头送至目的地。
在运行过程中,需要定期检查带子的运行情况。
注意检查输送带是否正常运行,是否有异响或异味,是否运行平稳等问题。
同时,也需要关注带子的张力问题,调整输送带的张力,保证物料可以平稳、连续地传输。
三、清理与检查输送带在运行过程中,难免会受到一些杂物的干扰,导致物料传输不畅。
因此,对于有颗粒状物料的输送带,需要定期清扫,防止堆积积存,在运行时引起物料卡料、停滞等问题。
同时,还需要检查输送带的状态,如果有损坏或磨损,及时更换修理。
四、输送带维护输送带作为重要的输送装置,需要定期进行维护。
首先,要进行润滑保养,防止运行过程中产生过多磨损。
同时,还需要对传动装置、驱动装置、支撑架等进行检查维护,确保它们能够正常运转,不会出现故障。
在进行维护时,需要事先关闭输送带的运行,确保人员安全。
五、停机与开机在一段时间的运行后,输送带也需要进行停机和开机操作。
停机时,需要事先关闭输送带的电源和运行开关,然后进行清理、检查和维护等操作。
待所有的工作都完成后,可以重新启动输送带,恢复正常的运行。
综上所述,输送带的工艺流程主要包括物料装载、输送带运行、清理与检查、输送带维护、停机与开机等环节。
通过合理的操作和维护,可以保证输送带正常、稳定地运行,为生产提供更高效、便捷的输送。
pvc输送带生产工艺

pvc输送带生产工艺PVC输送带是一种广泛应用于各个行业的输送设备,其生产工艺主要包括原料配比、材料制备、混炼挤出、成型冷却和加工工艺等几个关键步骤。
首先是原料配比。
PVC输送带的原料配比一般包括聚氯乙烯树脂、增塑剂、稳定剂、填料和助剂等。
根据不同的需求,适量调整各种原料的比例,确保生产出的PVC输送带具有良好的物理和化学性能。
接下来是材料制备。
将各种原料按照配方比例加入到混合机中,通过机械搅拌和热熔混合的过程,使原料充分融合,形成混合料。
混合料需要经过磨碎、干燥等处理,以保证材料的质量和稳定性。
然后是混炼挤出。
将混合料置于混炼机中,进行高温混炼。
混炼过程中,通过加热和搅拌,使混合料的温度逐渐升高,原料更均匀地混合,同时也可以去除混合料中的气泡。
完成混炼后,将混合料送入挤出机中,通过挤出机的加热、加压和挤出作用,使混合料形成连续的输送带。
接下来是成型冷却。
挤出的PVC输送带经过切割器切割成所需长度,并通过输送带运输到成型机中。
成型机内部设置有多个压辊,通过不同的轨道调节和压紧,使PVC输送带在成型机内形成所需的凹凸形状。
成型后的输送带需要通过冷却设备进行冷却,使其固化并保持所需形状。
最后是加工工艺。
成型的PVC输送带经过冷却后,需要经过修边、砂光、打孔、涂层等工艺,以获得更加平整、光滑和耐磨的表面。
在加工过程中,需要根据产品的要求进行检测和质量控制,确保生产出的PVC输送带能够满足客户的需求。
综上所述,PVC输送带的生产工艺包括原料配比、材料制备、混炼挤出、成型冷却和加工工艺等几个关键步骤。
通过科学合理的工艺设计和技术控制,可以生产出各种规格、性能优异的PVC输送带,满足不同行业的需求。
输送带工艺简介
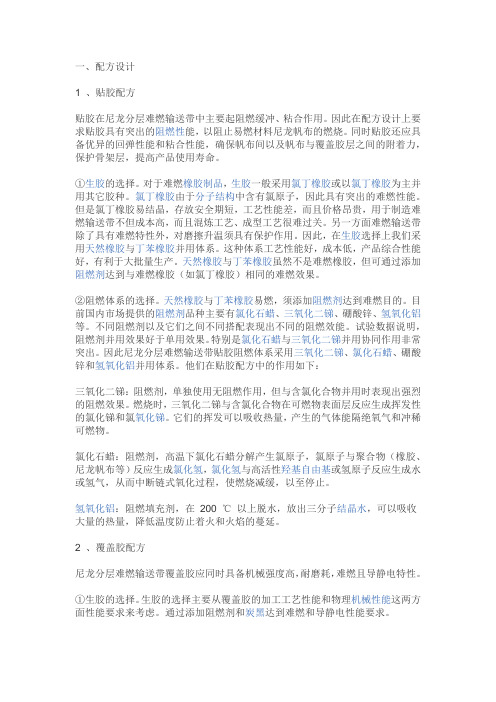
一、配方设计1 、贴胶配方贴胶在尼龙分层难燃输送带中主要起阻燃缓冲、粘合作用。
因此在配方设计上要求贴胶具有突出的阻燃性能,以阻止易燃材料尼龙帆布的燃烧。
同时贴胶还应具备优异的回弹性能和粘合性能,确保帆布间以及帆布与覆盖胶层之间的附着力,保护骨架层,提高产品使用寿命。
①生胶的选择。
对于难燃橡胶制品,生胶一般采用氯丁橡胶或以氯丁橡胶为主并用其它胶种。
氯丁橡胶由于分子结构中含有氯原子,因此具有突出的难燃性能。
但是氯丁橡胶易结晶,存放安全期短,工艺性能差,而且价格昂贵,用于制造难燃输送带不但成本高,而且混炼工艺、成型工艺很难过关。
另一方面难燃输送带除了具有难燃特性外,对磨擦升温须具有保护作用。
因此,在生胶选择上我们采用天然橡胶与丁苯橡胶并用体系。
这种体系工艺性能好,成本低,产品综合性能好,有利于大批量生产。
天然橡胶与丁苯橡胶虽然不是难燃橡胶,但可通过添加阻燃剂达到与难燃橡胶(如氯丁橡胶)相同的难燃效果。
②阻燃体系的选择。
天然橡胶与丁苯橡胶易燃,须添加阻燃剂达到难燃目的。
目前国内市场提供的阻燃剂品种主要有氯化石蜡、三氧化二锑、硼酸锌、氢氧化铝等。
不同阻燃剂以及它们之间不同搭配表现出不同的阻燃效能。
试验数据说明,阻燃剂并用效果好于单用效果。
特别是氯化石蜡与三氧化二锑并用协同作用非常突出。
因此尼龙分层难燃输送带贴胶阻燃体系采用三氧化二锑、氯化石蜡、硼酸锌和氢氧化铝并用体系。
他们在贴胶配方中的作用如下:三氧化二锑:阻燃剂,单独使用无阻燃作用,但与含氯化合物并用时表现出强烈的阻燃效果。
燃烧时,三氧化二锑与含氯化合物在可燃物表面层反应生成挥发性的氯化锑和氯氧化锑。
它们的挥发可以吸收热量,产生的气体能隔绝氧气和冲稀可燃物。
氯化石蜡:阻燃剂,高温下氯化石蜡分解产生氯原子,氯原子与聚合物(橡胶、尼龙帆布等)反应生成氯化氢,氯化氢与高活性羟基自由基或氢原子反应生成水或氢气,从而中断链式氧化过程,使燃烧减缓,以至停止。
氢氧化铝:阻燃填充剂,在200 ℃以上脱水,放出三分子结晶水,可以吸收大量的热量,降低温度防止着火和火焰的蔓延。
钢丝绳输送带生产工艺
钢丝绳输送带生产工艺钢丝绳输送带是现代工业中使用广泛的一种运输工具,它具有耐高温、耐磨损、拉力大等优点,因此在各种重型工业领域中得到了广泛应用。
钢丝绳输送带的生产工艺涉及多个环节,下面将对其进行详细介绍。
首先,钢丝绳输送带的生产开始于原材料的准备。
常见的原材料包括钢丝、橡胶等。
钢丝是钢丝绳输送带的主要增强材料,它具有高强度和耐磨损的特点。
而橡胶则是用于包裹钢丝,起到保护和增加摩擦力的作用。
在原材料准备完成后,接下来是钢丝绳的制造。
首先,要将钢丝进行拉拔,使其具有所需的强度和精度。
然后,根据设计要求将钢丝编织成绳索的形状。
这一步需要高度的技术和经验,以保证绳索的质量和性能。
接下来,钢丝绳需要进行预处理。
预处理包括清洗、脱脂、干燥等工序,以保证绳索表面干净,并提高橡胶与钢丝的粘合力。
预处理后的钢丝绳将进入橡胶胶化工序。
橡胶胶化是生产钢丝绳输送带的关键工艺之一。
在这一步中,将橡胶料与添加剂混合均匀后,通过橡胶挤出机将橡胶胶缸加工成胶层。
然后,将钢丝绳放置在胶层上,并通过辊筒将其压实,以确保钢丝与橡胶胶层间达到良好的粘合。
接下来,输送带需要进入硫化炉进行硫化处理。
硫化是使橡胶在高温和高压下形成交联结构的过程,以提高其耐磨性和耐高温性能。
硫化时间和温度需根据具体材料来确定,以确保硫化效果的理想。
最后,钢丝绳输送带还需要进行切割、修整、检测等工序,以使其符合设计要求。
切割是指根据需要将输送带切成所需长度;修整是指将输送带两边修整平整,以确保其宽度一致;检测则是通过检测设备对输送带进行质量检测,以确保其性能和质量。
综上所述,钢丝绳输送带的生产工艺包括原材料准备、钢丝绳制造、预处理、橡胶胶化、硫化处理以及后续的切割、修整和检测等环节。
这一系列工艺的成功应用能够确保钢丝绳输送带具有优异的性能和质量,满足不同行业对输送设备的需求。
橡胶输送带生产工艺
橡胶输送带生产工艺
橡胶输送带是一种用于物料输送的装置,广泛应用于矿山、电厂、港口、建材厂等各种工业领域。
下面为大家介绍一下橡胶输送带的生产工艺。
首先,橡胶输送带的生产开始于制胶。
制胶主要包括橡胶的混炼和硫化。
橡胶混炼是将原始橡胶与各种辅助材料进行混合,使其获得一定的硬度和强度,并且能够抵抗外部环境的侵蚀。
然后,混炼好的橡胶料进入硫化罐进行硫化,以提高橡胶的强度和耐磨性。
制胶完成后,需要进行布料的生产。
布料主要由纤维和橡胶进行复合而成,以增加橡胶输送带的强度和耐磨性。
纤维通常采用聚酯和尼龙等材料,经过涂覆、压延和硫化等工艺,将纤维与橡胶粘合在一起。
接下来是输送带的成型。
在成型过程中,先将制胶好的橡胶料通过辊压装置均匀地铺在下面的布料上,然后再覆盖一层布料在上面,形成三明治状的构造。
经过高温和高压的处理,使橡胶与布料紧密结合。
成型完成后,还需要进行辊压和修边等工艺,以确保输送带的尺寸和表面质量达到要求。
然后进行输送带的喷涂和切割,喷涂可以提高输送带的耐腐蚀性和耐磨性,切割则根据需要将输送带切成不同的长度。
最后,还需要进行输送带的检验和包装工作。
检验主要包括对
输送带的物理性能、外观质量和规格尺寸的检测,以确保输送带的质量符合标准。
包装则通常采用织物袋或塑料薄膜包装,以保护输送带在运输和储存过程中不受损坏。
综上所述,橡胶输送带的生产工艺包括制胶、布料生产、成型、辊压和修边、喷涂和切割、检验和包装等环节。
各个环节的工艺操作精细,需要严格控制工艺参数和质量标准,确保最终产品符合要求。
输送带热硫化接头工艺
输送带热硫化接头工艺1. 简介输送带热硫化接头工艺是一种用于连接输送带的方法,通过热硫化技术将输送带的两端连接在一起,以实现输送带的延长或修复。
该工艺具有高强度、耐磨损、耐腐蚀等优点,广泛应用于矿山、港口、电厂等场所。
2. 工艺步骤2.1 准备工作在进行输送带热硫化接头之前,需要进行以下准备工作:•检查输送带的损坏情况,并确定需要修复或延长的部位;•清洗和打磨输送带的连接面,确保表面干净平整;•准备好连接所需的材料和设备,包括硫化胶、胶水、加热板等。
2.2 切割和准备根据需要延长或修复的部位,使用切割机将输送带切割成相应长度,并确保切口平直整齐。
在连接面上涂抹一层胶水,待胶水变干后再涂抹一层硫化胶。
2.3 接头组装将两端切口对齐,将硫化胶涂抹的一端与胶水涂抹的一端紧密贴合。
使用夹具将两端固定在一起,并确保连接面之间没有气泡和杂质。
2.4 硫化加热将连接好的输送带放置在加热板上,调整加热板的温度和压力。
根据硫化胶的要求,加热板温度通常在150°C至180°C之间,并保持一定时间,以确保硫化胶能够充分发挥作用。
2.5 冷却和固化待硫化时间结束后,关闭加热板并等待输送带冷却。
冷却过程中,硫化胶会逐渐固化并与输送带形成牢固的连接。
冷却时间通常根据具体情况而定,但一般不少于30分钟。
2.6 检查和测试冷却结束后,对接头进行检查和测试。
检查接头是否平整、无气泡、无松动现象,并进行拉力测试以确保连接强度符合要求。
3. 工艺优势输送带热硫化接头工艺具有以下优势:•高强度:硫化胶能够牢固地连接输送带,使接头具有较高的拉力强度和抗磨损能力;•耐腐蚀:硫化胶具有较好的耐腐蚀性能,能够在恶劣环境下长期使用;•耐磨损:接头处采用硫化胶连接,能够有效减少磨损和摩擦,延长输送带的使用寿命;•快速修复:输送带热硫化接头工艺操作简单、快速,可以在短时间内完成输送带的修复或延长。
4. 应用领域输送带热硫化接头工艺广泛应用于以下领域:•矿山行业:用于输送煤炭、矿石等物料的输送带修复和延长;•港口行业:用于码头、船舶等场所的输送带连接和维护;•电厂行业:用于火力发电厂、核电厂等场所的输送带维修和更换。
输送带设备工艺原理
输送带设备工艺原理
输送带作为一种常见的物料输送设备,被广泛应用于各种行业中。
本文将介绍输送带设备的工艺原理,包括其组成、工作原理、分类及
应用。
组成
输送带由输送带体、传动部分和支撑部分三部分组成。
输送带体是输送带的核心部件,其由多层耐磨橡胶帆布和塑料层组成,不同的输送带使用不同的组件材料。
传动部分包括电机、减速机、液压耦合器、齿轮箱等。
支撑部分则有输送带架、滑动台、张紧装置、挡板等。
工作原理
输送带的工作原理是将物料从一个点输送到另一个点,其基本工作
方式分为两种:滚筒式和滚轮式。
滚筒输送带的主要零部件是滚筒,滚筒通过驱动机制使输送带沿着
滚筒方向运行,物料则通过输送带带体上升、下降、从而完成输送。
滚轮输送带则采用滚轮替代滚筒,其工作原理基本相同。
分类
根据输送带运输方式的不同,可分为普通输送带、和堆积机输送带、波浪边输送带、花纹面输送带、防滑型输送带等。
不同的输送带根据
其适用场所的不同,具有不同的特点。
应用
输送带设备广泛应用于矿山、冶金、化工、电力、轻工、建筑等各种行业。
其中煤炭、电力、轻工等行业使用的比较多,主要用于从生产过程中输送各种散装、片块状物料,如煤炭、沙子、水泥等。
在现代物流系统中,输送带设备也扮演着非常重要的角色,也广泛应用于物流仓储、大层码放、邮政包裹分拣等领域。
总结
本文主要介绍了输送带设备的工艺原理,从其组成、工作原理、分类及应用等方面进行了详细的介绍,希望可以为读者们更好的了解输送带设备提供帮助。
- 1、下载文档前请自行甄别文档内容的完整性,平台不提供额外的编辑、内容补充、找答案等附加服务。
- 2、"仅部分预览"的文档,不可在线预览部分如存在完整性等问题,可反馈申请退款(可完整预览的文档不适用该条件!)。
- 3、如文档侵犯您的权益,请联系客服反馈,我们会尽快为您处理(人工客服工作时间:9:00-18:30)。
一、配方设计
1 、贴胶配方
贴胶在尼龙分层难燃输送带中主要起阻燃缓冲、粘合作用。
因此在配方设计上要求贴胶具有突出的阻燃性能,以阻止易燃材料尼龙帆布的燃烧。
同时贴胶还应具备优异的回弹性能和粘合性能,确保帆布间以及帆布与覆盖胶层之间的附着力,保护骨架层,提高产品使用寿命。
①生胶的选择。
对于难燃橡胶制品,生胶一般采用氯丁橡胶或以氯丁橡胶为主并用其它胶种。
氯丁橡胶由于分子结构中含有氯原子,因此具有突出的难燃性能。
但是氯丁橡胶易结晶,存放安全期短,工艺性能差,而且价格昂贵,用于制造难燃输送带不但成本高,而且混炼工艺、成型工艺很难过关。
另一方面难燃输送带除了具有难燃特性外,对磨擦升温须具有保护作用。
因此,在生胶选择上我们采用天然橡胶与丁苯橡胶并用体系。
这种体系工艺性能好,成本低,产品综合性能好,有利于大批量生产。
天然橡胶与丁苯橡胶虽然不是难燃橡胶,但可通过添加阻燃剂达到与难燃橡胶(如氯丁橡胶)相同的难燃效果。
②阻燃体系的选择。
天然橡胶与丁苯橡胶易燃,须添加阻燃剂达到难燃目的。
目前国内市场提供的阻燃剂品种主要有氯化石蜡、三氧化二锑、硼酸锌、氢氧化铝等。
不同阻燃剂以及它们之间不同搭配表现出不同的阻燃效能。
试验数据说明,阻燃剂并用效果好于单用效果。
特别是氯化石蜡与三氧化二锑并用协同作用非常突出。
因此尼龙分层难燃输送带贴胶阻燃体系采用三氧化二锑、氯化石蜡、硼酸锌和氢氧化铝并用体系。
他们在贴胶配方中的作用如下:
三氧化二锑:阻燃剂,单独使用无阻燃作用,但与含氯化合物并用时表现出强烈的阻燃效果。
燃烧时,三氧化二锑与含氯化合物在可燃物表面层反应生成挥发性的氯化锑和氯氧化锑。
它们的挥发可以吸收热量,产生的气体能隔绝氧气和冲稀可燃物。
氯化石蜡:阻燃剂,高温下氯化石蜡分解产生氯原子,氯原子与聚合物(橡胶、尼龙帆布等)反应生成氯化氢,氯化氢与高活性羟基自由基或氢原子反应生成水或氢气,从而中断链式氧化过程,使燃烧减缓,以至停止。
氢氧化铝:阻燃填充剂,在200 ℃以上脱水,放出三分子结晶水,可以吸收大量的热量,降低温度防止着火和火焰的蔓延。
2 、覆盖胶配方
尼龙分层难燃输送带覆盖胶应同时具备机械强度高,耐磨耗,难燃且导静电特性。
①生胶的选择。
生胶的选择主要从覆盖胶的加工工艺性能和物理机械性能这两方面性能要求来考虑。
通过添加阻燃剂和炭黑达到难燃和导静电性能要求。
②阻燃体系的选择。
对于难燃且导静电制品,难燃体系的选择非常重要。
炭黑在橡胶制品中即是很好的补强剂又能有效地降低制品表面电阻。
但是炭黑的使用往往使制品产生无焰燃烧(炭黑),对阻止制品无焰燃烧将产生极为不利的影响。
因此,对于使用炭黑作补强剂的难燃且导静电的橡胶制品,如何有效地抑制无焰燃烧是配方设计中着重考虑的问题。
结果表明,氯化石蜡和三氧化二锑并用能有效地阻止有焰燃烧,但同时助长了无焰燃烧。
氯化石蜡、十溴二苯醚、氢氧化铝、硼酸锌体系虽能有效地抑制无焰燃烧,但对阻止有焰燃烧效果不够显著。
因此尼龙分层难燃输送带覆盖胶的难燃体系选择氯化石蜡、十溴二苯醚、三氧化二锑、氢氧化铝和硼酸锌并用体系。
二、生产工艺
尼龙分层难燃输送带生产工艺流程:干燥→塑炼→合炼→混炼→停放→热炼→压延→成型→硫化→包装。
与非尼龙骨架输送带有所不同,尼龙分层难燃输送带生产工艺硫化后要经过二次拉伸定型处理。
二次拉伸定型主要有两种方法,一种是模内压力下冷却定型方法(以下简称模内定型),另一种是模外拉伸冷却定型方法(以下简称模外定型)。
模内定型方法简单,定型效果好。
但是采用这种方法定型能耗大,生产效率低。
相比之下模外定型方法虽然须多一套拉伸装置,但是采用这种方法后产品质量可靠,生产效率高,适于大批量规模生产。
三、结果测试
物理机械性能及安全性能测试结果见表 1 和表 2 。
表1 物理机械性能
项目名称标准MT147-87 测试中心本厂
覆盖胶扯断强度/MPa --20.1
覆盖胶伸长率/% --464.0
覆盖胶邵尔硬度/度--68
覆盖胶磨耗量/cm3(1.61km)--0.2
覆盖胶与芯体附着力/(N ·㎜-1)≥4.5 5.12 7.2
帆布层间附着力/(N ·㎜-1)≥4.5 10.16 6.7
带体经向扯断强力/(N ·㎜-1)≥300 556 435
带体经向伸长率/% ≥10 18.6 20
带体纬向扯断强力/(N ·㎜-1)≥120 127 140
带体纬向伸长率/% ≥18 21.0 27
表2 安全性能测试结果
项目名称标准MT147-87 测试中心本厂
酒精喷灯燃烧试验
芯体/s 均值:≤5 3.18 1.14
最大值≤15 5.88 1.42
整体/s 均值:≤3 2.50 1.61
最大值≤10 7.85 2.04
滚筒磨擦试验
吹风工作面/ ℃不高于325 ,无火星272 ,246 无火星297 ,无火星
吹风非工作面/ ℃不高于325 ,无火星260 无火星284 ,无火星
吹风工作面/ ℃不高于325 ,无火星260 无火星279 ,无火星
吹风非工作面/ ℃不高于325 ,无火星261 ,265 无火星284 ,无火星导电性能试验
工作面/ Ω ≤ 3.0×108 3.5×106 5.3×106
非工作面/ Ω ≤ 3.0×108 3.4×107 4.0×106
阻燃输送带
一、阻燃输送带品种结构
阻燃输送带由覆盖胶、带芯及边胶组成。
其中,带芯由结构有全棉、难棉交织、尼龙、聚酯及尼龙和聚酯交织帆布,其胶层具有自熄、阻燃导静电性能。
二、阻燃输送带用途
阻燃输送带适用于化工、轻工、煤炭、洗煤厂、冶金、粮食加工、电力等行业使用难燃或难燃且导静电的场所。
阻燃输送带特点:阻燃输送带是我公司根据冶金、煤矿、电厂等行业在实际使用中经常有炽热物料这一特点研制开发的新型具有抗燃烧、抗静电、等特性的难燃带。
该产品具有使用寿命长,并增加使用安全性等特点。
覆盖胶配方
阻燃输送带覆盖胶应同时具备机械强度高,耐磨耗,难燃且导静电特性。
①生胶的选择。
生胶的选择主要从覆盖胶的加工工艺性能和物理机械性能这两方面性能要求来考虑。
通过添加阻燃剂和炭黑达到难燃和导静电性能要求。
②阻燃体系的选择。
对于难燃且导静电制品,难燃体系的选择非常重要。
炭黑在橡胶制品中即是很好的补强剂又能有效地降低制品表面电阻。
但是炭黑的使用往往使制品产生无焰燃烧(炭黑),对阻止制品无焰燃烧将产生极为不利的影响。
因此,对于使用炭黑作补强剂的难燃且导静电的橡胶制品,如何有效地抑制无焰燃烧是配方设计中着重考虑的问题。
结果表明,氯化石蜡和三氧化二锑并用能有效地阻止有焰燃烧,但同时助长了无焰燃烧。
氯化石蜡、十溴二苯醚、氢氧化铝、硼酸锌体系虽能有效地抑制无焰燃烧,但对阻止有焰燃烧效果不够显著。
因此尼龙分层难燃输送带覆盖胶的难燃体系选择氯化石蜡、十溴二苯醚、三氧化二锑、氢氧化铝和硼酸锌并用体系。
二、阻燃输送带生产工艺
阻燃输送带生产工艺流程:干燥→塑炼→合炼→混炼→停放→热炼→压延→成型→硫化→包装。
与非尼龙骨架输送带有所不同,尼龙分层难燃输送带生产工艺硫化后要经过二次拉伸定型处理。
二次拉伸定型主要有两种方法,一种是模内压力下冷却定型方法(以下简称模内定型),另一种是模外拉伸冷却定型方法(以下简称模外定型)。
模内定型方法简单,定型效果好。
但是采用这种方法定型能耗大,生产效率低。
相比之下模外定型方法虽然须多一套拉伸装置,但是采用这种方法后产品质量可靠,生产效率高,适于大批量规模生产。