无铅焊接产生锡珠原因
无铅焊接缺陷的分类及成因
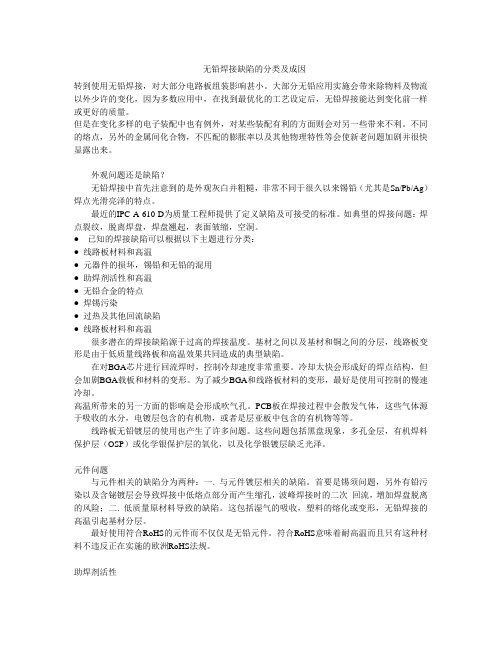
无铅焊接缺陷的分类及成因转到使用无铅焊接,对大部分电路板组装影响甚小。
大部分无铅应用实施会带来除物料及物流以外少许的变化,因为多数应用中,在找到最优化的工艺设定后,无铅焊接能达到变化前一样或更好的质量。
但是在变化多样的电子装配中也有例外,对某些装配有利的方面则会对另一些带来不利。
不同的熔点,另外的金属间化合物,不匹配的膨胀率以及其他物理特性等会使新老问题加剧并很快显露出来。
外观问题还是缺陷?无铅焊接中首先注意到的是外观灰白并粗糙,非常不同于很久以来锡铅(尤其是Sn/Pb/Ag)焊点光滑亮泽的特点。
最近的IPC-A-610-D为质量工程师提供了定义缺陷及可接受的标准。
如典型的焊接问题:焊点裂纹,脱离焊盘,焊盘翘起,表面皱缩,空洞。
● 已知的焊接缺陷可以根据以下主题进行分类:● 线路板材料和高温● 元器件的损坏,锡铅和无铅的混用● 助焊剂活性和高温● 无铅合金的特点● 焊锡污染● 过热及其他回流缺陷● 线路板材料和高温很多潜在的焊接缺陷源于过高的焊接温度。
基材之间以及基材和铜之间的分层,线路板变形是由于低质量线路板和高温效果共同造成的典型缺陷。
在对BGA芯片进行回流焊时,控制冷却速度非常重要。
冷却太快会形成好的焊点结构,但会加剧BGA载板和材料的变形。
为了减少BGA和线路板材料的变形,最好是使用可控制的慢速冷却。
高温所带来的另一方面的影响是会形成吹气孔。
PCB板在焊接过程中会散发气体,这些气体源于吸收的水分,电镀层包含的有机物,或者是层亚板中包含的有机物等等。
线路板无铅镀层的使用也产生了许多问题。
这些问题包括黑盘现象,多孔金层,有机焊料保护层(OSP)或化学银保护层的氧化,以及化学银镀层缺乏光泽。
元件问题与元件相关的缺陷分为两种:一. 与元件镀层相关的缺陷。
首要是锡须问题,另外有铅污染以及含铋镀层会导致焊接中低熔点部分而产生缩孔,波峰焊接时的二次回流,增加焊盘脱离的风险;二. 低质量原材料导致的缺陷。
锡珠的产生原因与预防措施

14 3 E 型
。
12 m m
的 而 不选 择其 他 更 大 的
一
。
高速 贴片机测 量
,
0 0 1mm
。
实
来
,
在冷 却 时 形 成锡 珠
。
如果元件重
一
开 口 比例
般是 1 :
1
,
但 是对 于
,
际 测 量 P CB 焊 盘 的 尺 寸 为 表 1
际 测 量 ( F UJ
0 0 0 1mm )
.
根据 实
,
,
由于 表
它有趋
被挤 压 等各 种 原 因 而 超 出在 印 刷 焊 盘
之外
,
融化 的 锡 膏 聚 成 圆 球
,
,
锡 球 的 主 要 原 因 是在 焊 点 成 形 的 过程 中
,
在进 行 焊 接 时
,
这 些 超 出焊 盘
势抬 高 元 件
,
反 被元
熔 融 的金 属 合 金 因 为 各 种 原
”
的锡 膏 在 焊 接 过 程 中未 能 与 焊 盘 上 的
料 受 到 过 快 的加 热 或 者 冷 却
无 铅 的高温 工 艺
,
,
尤其是 图 1 片式 元 件 的 锡 珠
会 导致锡 球 的形
w H t t p :/ v c /
a
.
s t a
te n e t
.
P QF P / i n 0 5 ra m 间 距 的 可 以 选 择 0 1 2
. .
例
,
图 3 为 电阻 焊 盘 设 计 示 意 图 ( 实
,
只要
线 路 的 短 路 的危 险
锡珠产生的原因分析
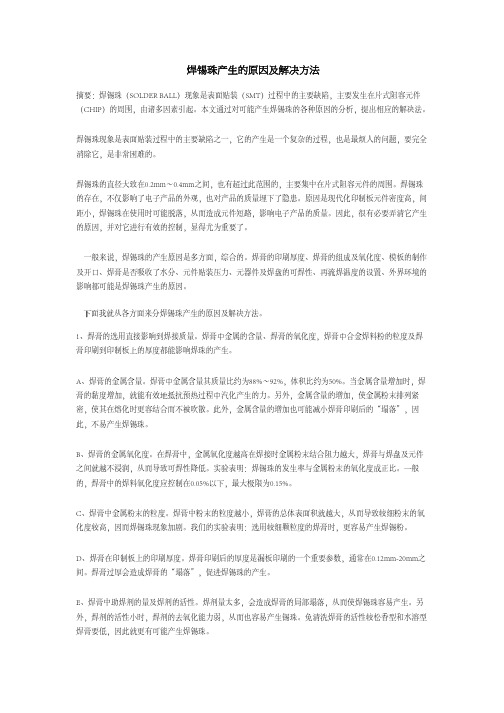
焊锡珠产生的原因及解决方法摘要:焊锡珠(SOLDER BALL)现象是表面贴装(SMT)过程中的主要缺陷,主要发生在片式阻容元件(CHIP)的周围,由诸多因素引起。
本文通过对可能产生焊锡珠的各种原因的分析,提出相应的解决法。
焊锡珠现象是表面贴装过程中的主要缺陷之一,它的产生是一个复杂的过程,也是最烦人的问题,要完全消除它,是非常困难的。
焊锡珠的直径大致在0.2mm~0.4mm之间,也有超过此范围的,主要集中在片式阻容元件的周围。
焊锡珠的存在,不仅影响了电子产品的外观,也对产品的质量埋下了隐患。
原因是现代化印制板元件密度高,间距小,焊锡珠在使用时可能脱落,从而造成元件短路,影响电子产品的质量。
因此,很有必要弄清它产生的原因,并对它进行有效的控制,显得尤为重要了。
一般来说,焊锡珠的产生原因是多方面,综合的。
焊膏的印刷厚度、焊膏的组成及氧化度、模板的制作及开口、焊膏是否吸收了水分、元件贴装压力、元器件及焊盘的可焊性、再流焊温度的设置、外界环境的影响都可能是焊锡珠产生的原因。
㆘面我就从各方面来分焊锡珠产生的原因及解决方法。
1、焊膏的选用直接影响到焊接质量。
焊膏中金属的含量、焊膏的氧化度,焊膏中合金焊料粉的粒度及焊膏印刷到印制板上的厚度都能影响焊珠的产生。
A、焊膏的金属含量。
焊膏中金属含量其质量比约为88%~92%,体积比约为50%。
当金属含量增加时,焊膏的黏度增加,就能有效地抵抗预热过程中汽化产生的力。
另外,金属含量的增加,使金属粉末排列紧密,使其在熔化时更容结合而不被吹散。
此外,金属含量的增加也可能减小焊膏印刷后的“塌落”,因此,不易产生焊锡珠。
B、焊膏的金属氧化度。
在焊膏中,金属氧化度越高在焊接时金属粉末结合阻力越大,焊膏与焊盘及元件之间就越不浸润,从而导致可焊性降低。
实验表明:焊锡珠的发生率与金属粉末的氧化度成正比。
一般的,焊膏中的焊料氧化度应控制在0.05%以下,最大极限为0.15%。
C、焊膏中金属粉末的粒度。
锡珠产生的原因及解决方法

锡珠产生的原因及解决方法(总2页)-CAL-FENGHAI.-(YICAI)-Company One1-CAL-本页仅作为文档封面,使用请直接删除焊锡珠产生的原因及解决方法摘要:焊锡珠(SOLDER BALL)现象是表面贴装(SMT)过程中的主要缺陷,主要发生在片式阻容组件(CHIP)的周围,由诸多因素引起。
本文通过对可能产生焊锡珠的各种原因的分析,提出相应的解决方法。
焊锡珠现象是表面贴装过程中的主要缺陷之一,它的产生是一个复杂的过程,也是最烦人的问题,要完全消除它,是非常困难的。
焊锡珠的直径大致在0.2mm~0.4mm 之间,也有超过此范围的,主要集中在片式阻容组件的周围。
焊锡珠的存在,不仅影响了电子产品的外观,也对产品的质量埋下了隐患。
原因是现代化印制板组件密度高,间距小,焊锡珠在使用时可能脱落,从而造成组件短路,影响电子产品的质量。
因此,很有必要弄清它产生的原因,并对它进行有效的控制,显得尤为重要了。
一般来说,焊锡珠的产生原因是多方面,综合的。
焊膏的印刷厚度、焊膏的组成及氧化度、模板的制作及开口、焊膏是否吸收了水分、组件贴装压力、元器件及焊盘的可焊性、再流焊温度的设置、外界环境的影响都可能是焊锡珠产生的原因。
下面我就从各方面来分焊锡珠产生的原因及解决方法。
1、焊膏的选用直接影响到焊接质量。
焊膏中金属的含量、焊膏的氧化度,焊膏中合金焊料粉的粒度及焊膏印刷到印制板上的厚度都能影响焊珠的产生。
A、焊膏的金属含量。
焊膏中金属含量其质量比约为88%~92%,体积比约为50%。
当金属含量增加时,焊膏的黏度增加,就能有效地抵抗预热过程中汽化产生的力。
另外,金属含量的增加,使金属粉末排列紧密,使其在熔化时更容结合而不被吹散。
此外,金属含量的增加也可能减小焊膏印刷后的“塌落”,因此,不易产生焊锡珠。
B、焊膏的金属氧化度。
在焊膏中,金属氧化度越高在焊接时金属粉末结合阻力越大,焊膏与焊盘及组件之间就越不浸润,从而导致可焊性降低。
锡珠的产生原因及解决方法

锡珠的产生原因及解决方法锡珠的产生原因及解决方法锡珠现象是smt过程中的主要缺陷,主要发生在片式阻容元件的周围,由诸多因素引起。
它的产生是一个复杂的过程,也是最烦人的问题,要完全消除它,是非常困难的。
锡珠的直径大致在0.2mm——0.4mm之间,也有超过此范围的。
锡珠的存在,不仅影响了电子产品的美观,对产品的质量也有极大的隐患。
我们都知道现在smt工艺中的元件间距小,密度高,若是锡珠在使用时脱落,就可能造成元件短路,影响电子产品的质量。
因此,弄清锡珠产生的原因,并对它进行有效的控制,显得尤为重要了。
锡珠的产生原因是多方面造成的。
锡膏的印刷厚度、其组成及氧化度、模板的制作及开口都有可能造成锡珠现象,同时锡膏是否吸收了水分、元件贴装压力、元器件及焊盘的可焊性、再流焊温度的设置、外界环境的影响都可能是锡珠产生的原因。
下面吉田店铺就从各方面来分锡珠产生的原因及解决方法。
1、锡膏的金属氧化度。
在锡膏中,金属氧化度越高在焊接时金属粉末结合阻力越大,锡膏与焊盘及元件之间就越不浸润,从而导致可焊性降低。
锡珠的发生率与金属粉末的氧化度成正比。
一般的,锡膏中的焊料氧化度应控制在0.05%以下,最大极限为0.15%。
2、锡膏在印制板上的印刷厚度。
锡膏印刷后的厚度是漏板印刷的一个重要参数,通常在0.12mm——0.20mm之间。
锡膏过厚会造成锡膏“塌边”,促进锡珠的产生。
3、锡膏中助焊剂的量及焊剂的活性。
焊剂量太多,会造成锡膏的局部塌落,从而使锡珠容易产生。
另外,焊剂的活性小时,焊剂的去氧化能力弱,从而也容易产生锡珠。
免清洗锡膏的活性较松香型和水溶型锡膏要低,因此就更有可能产生锡珠。
4、此外,锡膏在使用前,一般冷藏在冰箱中,取出来以后应该使其恢复到室温后打开使用,否则,锡膏容易吸收水分,在再流焊锡飞溅而产生锡珠。
58回流焊中锡珠形成的原因及解决方法介绍|南昌回流焊原理2017-03-22 12:44 | #2楼波峰焊第一品牌【精极科技】深圳市精极科技有限公司成立于2002年8月,是一家以设计、生产、销售等工业仓储设备及柔性生产线设备为主的专业生产厂家,同时分销配套的防静电周边产品。
产生“锡珠”的原因分析及措施
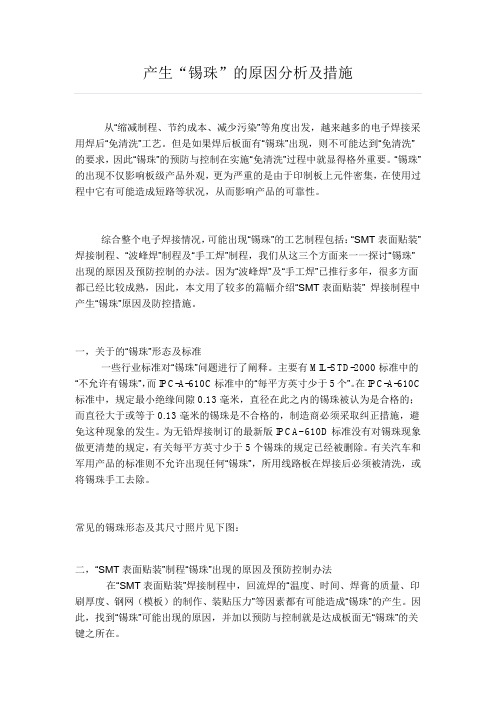
产生“锡珠”的原因分析及措施从“缩减制程、节约成本、减少污染”等角度出发,越来越多的电子焊接采用焊后“免清洗”工艺。
但是如果焊后板面有“锡珠”出现,则不可能达到“免清洗”的要求,因此“锡珠”的预防与控制在实施“免清洗”过程中就显得格外重要。
“锡珠”的出现不仅影响板级产品外观,更为严重的是由于印制板上元件密集,在使用过程中它有可能造成短路等状况,从而影响产品的可靠性。
综合整个电子焊接情况,可能出现“锡珠”的工艺制程包括:“SMT表面贴装”焊接制程、“波峰焊”制程及“手工焊”制程,我们从这三个方面来一一探讨“锡珠”出现的原因及预防控制的办法。
因为“波峰焊”及“手工焊”已推行多年,很多方面都已经比较成熟,因此,本文用了较多的篇幅介绍“SMT表面贴装”焊接制程中产生“锡珠”原因及防控措施。
一,关于的“锡珠”形态及标准一些行业标准对“锡珠”问题进行了阐释。
主要有MIL-STD-2000标准中的“不允许有锡珠”,而IPC-A-610C标准中的“每平方英寸少于5个”。
在IPC-A-610C 标准中,规定最小绝缘间隙0.13毫米,直径在此之内的锡珠被认为是合格的;而直径大于或等于0.13毫米的锡珠是不合格的,制造商必须采取纠正措施,避免这种现象的发生。
为无铅焊接制订的最新版IPCA- 610D标准没有对锡珠现象做更清楚的规定,有关每平方英寸少于5个锡珠的规定已经被删除。
有关汽车和军用产品的标准则不允许出现任何“锡珠”,所用线路板在焊接后必须被清洗,或将锡珠手工去除。
常见的锡珠形态及其尺寸照片见下图:二,“SMT表面贴装”制程“锡珠”出现的原因及预防控制办法在“SMT表面贴装”焊接制程中,回流焊的“温度、时间、焊膏的质量、印刷厚度、钢网(模板)的制作、装贴压力”等因素都有可能造成“锡珠”的产生。
因此,找到“锡珠”可能出现的原因,并加以预防与控制就是达成板面无“锡珠”的关键之所在。
(一),焊膏本身质量原因可能引起的“锡珠”状况1,焊膏中的金属含量。
产生锡珠的原理
产生锡珠的原理1. 引言锡珠是一种常见的工业原料,广泛应用于电子、建筑、汽车等领域。
本文将探讨产生锡珠的原理,包括锡珠的制备、形成以及其物理性质。
2. 锡珠的制备过程产生锡珠的过程主要包括:原料准备、熔化、冷却、成型四个步骤。
2.1 原料准备制备锡珠的主要原料是锡,以及可能的合金元素。
锡珠通常由纯度高于99.9%的锡制成。
合金元素的添加可根据需要进行调整,以改变锡珠的性能。
2.2 熔化将准备好的锡原料加热到熔点以上,使其完全熔化。
通常使用电炉或气体炉等高温设备进行加热,确保锡珠达到熔化状态。
2.3 冷却在锡珠熔化后,需要将其逐渐冷却。
冷却速度对锡珠的结晶有重要影响,过快或过慢的冷却都可能导致锡珠的结构缺陷。
2.4 成型在冷却过程中,需要通过一定的成型工艺将锡珠塑造成所需的形状。
常见的成型方法包括压制、注射成型等。
3. 锡珠形成的原理锡珠的形成是由于熔化锡在冷却过程中通过相变和凝固产生的。
以下将详细介绍锡珠形成的原理。
3.1 熔化与相变当锡原料加热到熔点时,固体锡开始逐渐熔化成液态锡。
这个过程中,当温度达到锡的熔点时,锡原子开始脱离原子晶格,形成液态结构。
液态锡具有较高的流动性,可以填充在模具中的空隙。
3.2 凝固熔化的锡在冷却过程中,其温度逐渐降低。
当温度低于锡的凝固点时,液态锡开始重新排列,原子逐渐回到晶体晶格中。
这个过程称为凝固,主要包括两个步骤:核化和长大。
3.2.1 核化核化是指在液态锡中形成凝固核的过程。
在锡液中存在一些微小的杂质或基因,它们作为凝固核,引导锡原子重新排列。
核化的发生也依赖于温度和时间等因素。
3.2.2 长大当凝固核形成后,锡液中的锡原子开始围绕凝固核排列,并逐渐增长。
这个过程称为长大。
长大的速度取决于温度梯度以及凝固过程中的固液界面能。
3.3 形成锡珠随着锡液的继续冷却和凝固,凝固核逐渐增大,相邻的凝固核开始连接。
当凝固核连成一片时,锡珠即形成。
锡珠的大小和形状可以通过调整冷却速度、合金成分以及成型工艺等因素进行控制。
锡珠的形成及对策分析
7
而非锡珠(solder beads)
返回
锡珠形成的原因概述
锡珠
是怎样产生的
A 材料的原因
B 工艺的原因
I. 锡膏触变系数大
①
II. 锡膏冷坍塌或轻微热坍塌 ②
III. 焊剂过多或活性温度低
③
IV. 锡粉氧化率高或颗粒不均匀 ④
V. PCB的焊盘间距小
⑤
VI. 刮刀材质硬度小或变形
刮刀
锡膏
焊盘
钢版
9 PCB
返回
PCB 与钢版的间隔
在紧密印刷中不建议有间隔
!!
不建议
印刷钢板
PAD
PAD
线路板
10
不建议
脱模
返回
锡珠形成的原因(贴零件环节)锡膏印刷来自贴零件装 IC
回流焊接
检验
零件贴装部分
a) 贴片压力太大 b) 贴片精度太差 c) 其它因素
11
返回
贴片精度
线路板的精确度 ( PAD,校准点等)
共需要45分钟
介绍
锡珠 的形成和解决 SMT各工艺环节锡珠的预防措施和解决方法 根据鱼骨图逐项排除
3
大纲
相关词汇 (名词解释或定义)
SMT焊接中形成锡珠的现象
(正确的认识,错误的识别)
形成锡珠的原因(各工艺环节)
(印刷,贴件,回流焊接)
不停线调整减少锡珠的暂时对策
(暂时对策)
改良网版设计消除产生锡珠的隐患
14
Solder Beads
返回
其它的预防和改良措施
SMT各层工作人员的素质 SMT管理人员品质标准的培训 SMT 操作人员的相关操作的培训 明确各个工作岗位的权责(该做与不该做) 思想觉悟以及品质意识的提高
焊锡珠产生的原因及解决方法
焊錫珠産生的原因及解決方法焊錫珠産生的原因及解決方法摘要: 焊錫珠(SOLDER BALL)現象是表面貼裝(SMT)過程㆗的主要缺陷,主要發生在片式阻容元件(CHIP)的周圍,由諸多因素引起。
本文通過對可能産生焊錫珠的各種原因的分析,提出相應的解決方法。
焊錫珠現象是表面貼裝過程㆗的主要缺陷之㆒,它的産生是㆒個複雜的過程,也是最煩㆟的問題,要完全消除它,是非常困難的。
焊錫珠的直徑大致在0.2mm〜0.4mm 之間,也有超過此範圍的,主要集㆗在片式阻容元件的周圍。
焊錫珠的存在,不僅影響了電子産品的外觀,也對産品的質量埋㆘了隱患。
原因是現代化印製板元件密度高,間距小,焊錫珠在使用時可能脫落,從而造成元件短路,影響電子産品的質量。
因此,很有必要弄清它産生的原因,並對它進行有效的控制,顯得尤爲重要了。
㆒般來說,焊錫珠的産生原因是多方面,綜合的。
焊膏的印刷厚度、焊膏的組成及氧化度、模板的製作及開口、焊膏是否吸收了水分、元件貼裝壓力、元器件及焊盤的可焊性、再流焊溫度的設置、外界環境的影響都可能是焊錫珠産生的原因。
㆘面我就從各方面來分焊錫珠産生的原因及解決方法。
1、焊膏的選用直接影響到焊接質量。
焊膏㆗金屬的含量、焊膏的氧化度,焊膏㆗合金焊料粉的粒度及焊膏印刷到印製板㆖的厚度都能影響焊珠的産生。
A、焊膏的金屬含量。
焊膏㆗金屬含量其質量比約爲88%〜92%,體積比約爲50%。
當金屬含量增加時,焊膏的黏度增加,就能有效㆞抵抗預熱過程㆗汽化産生的力另外,金屬含量的增加,使金屬粉末排列緊密,使其在熔化時更容結合而不被吹散。
手工焊接锡珠产生的原因
手工焊接锡珠产生的原因
嘿,你问手工焊接锡珠产生的原因啊?这可有不少情况呢。
一个原因可能是焊接温度太高啦。
就像你做饭火开太大,锅里的东西就容易溅出来。
焊接的时候温度太高,锡就容易变成小珠子到处乱跑。
温度一高,锡就变得特别活跃,不好控制。
还有可能是焊锡丝的质量不太好。
要是焊锡丝里面有杂质啥的,焊接的时候就容易出问题。
就像你买了个质量不好的水果,吃的时候可能会觉得味道怪怪的。
焊锡丝不好,就容易产生锡珠。
操作手法也很重要哦。
如果焊接的时候手不稳,或者速度太快太慢,都可能导致锡珠产生。
就像你写字,如果手不稳,字就写得歪歪扭扭的。
焊接也一样,得稳稳当当的。
另外,电路板不干净也会有影响。
如果电路板上有灰尘、油污啥的,锡就不容易粘在上面,容易形成锡珠。
就像你在脏桌子上画画,颜料就不容易涂均匀。
我给你讲个事儿吧。
我有个朋友自己在家做手工焊接,一开始总是有锡珠。
他不知道咋回事,后来仔细研究了一下。
发现是自己焊接温度调得太高了,而且焊锡丝质量也不太好。
他换了好一点的焊锡丝,调整了温度,焊接的时候也更小心了。
嘿,锡珠就少了很多。
你看,知道锡珠产生的原因很重要呢。
所以啊,手工焊接产生锡珠可能是因为温度太高、焊锡丝质量不好、操作手法不对或者电路板不干净。
在焊接的时候要注意这些问题,才能焊得漂亮。
加油!。
- 1、下载文档前请自行甄别文档内容的完整性,平台不提供额外的编辑、内容补充、找答案等附加服务。
- 2、"仅部分预览"的文档,不可在线预览部分如存在完整性等问题,可反馈申请退款(可完整预览的文档不适用该条件!)。
- 3、如文档侵犯您的权益,请联系客服反馈,我们会尽快为您处理(人工客服工作时间:9:00-18:30)。
原因:1.烙铁温度过高,焊料升温过快,造成助焊剂的溶剂“沸腾”而炸锡;
2.焊锡丝本身的质量原因。
其实焊锡丝都存在锡珠飞溅的现象,尤其是现在的无铅锡丝。
只是不同牌子或型号的锡丝的飞溅现象程度不一样。
目前飞溅现象最小的锡丝应该是日本的ALMIT ,但是价格很贵,都是客户指定要用的,如CASIO ,MATSUSHITA ,IBM ,SHARP。
不过现在很多日系的企业用一种机器在焊锡丝上开一个V型槽,这样助焊剂就可以和空气接触,而不会膨胀而不会产生爆锡的现象,但开槽后的锡丝要在很短的时间里用掉,否则助焊剂会失效。
目前用SONY ,MATSUSHITA ,RICOH 都在用这种机器。
是日本的叫BONKOTE
維修無鉛SMD元件
1)修理普通元件如0603,0805,3216的元件,電烙鉄溫度的範圍:350℃±50℃。
2)修理IC,電烙鉄溫度的範圍:350℃±50℃
3)修理含有金屬材料的元件或元件接觸面積較大散熱較快的物料,電烙鉄溫度範圍:
380℃±50℃。
4.4維修無鉛THD元件
1)修理普通元件如1/4W.1/2W的電阻,小三極管,小容量內壓低的電容,IC,二極管等小元件電烙鉄溫度的範圍:340℃±50℃。
2)修理含有金屬材料的元件如散熱器,內壓高容量大的電解電容,高壓二極管,火牛等較大的物料,電烙鉄溫度的範圍:380℃±50℃。
3)修理含有塑膠皮的連接線,烙鉄溫度的範圍:350℃±50℃。
使用手工焊接时,烙铁的温度及焊接时间是多少?怎么控制?有无相关的标准? ?D#D蔲?n 睠3市
Z1c;??? 貼
這要看所焊的零件種類及面積, 同時要考慮焊接方法 !H g炒媖葏
如果是一般小電阻電容類, 就我過去的經驗如果用的 ?0腳f籗?
是30w左右的烙鐵, 溫度可設在約370度c應該足夠, 焊接時間約2-3秒且用較細的錫絲(0.8mm以下), 但是如果 @雵E?輛a
焊接面積大就應該用較大瓦特數(功率)如40w或更高, z%磕申 U?
有些超大焊接面積甚致用到60w, 而錫絲尺寸也隨著 ?檊靎?x?
焊接面積加大而加粗溫度可設在約400度c, 烙鐵焊接 9鑹?xUm?
除了溫度高低外還要考慮熱傳導量, 另外焊接方式方面癆n嚌?敿
傳統上很多人習慣先對錫絲加溫再加熱焊點的方法, "KM?叭繤
最好改為先對焊點加熱1-2秒後再加錫絲以避免錫絲內 ? ?FM诎
助焊劑加溫過久而焦化
焊锡中铅的含量绝不可能过关的,而采用替代品,那产品的寿命又没有保证了,因而只能保证生产工艺过程中不出现锡珠,下面是解决参考:
焊锡珠现象是表面贴装生产中主要缺陷之一,它的直径约为0.2-0.4mm,主要集中出现在片状阻容元件的某一侧面,不仅影响板级产品的外观,更为严重的是由于印刷板上元件密集,在使用过程中它会造成短路现象,从而影响电子产品的质量。
因此弄清它产生的原因,并力求对其进行最有效的控制就显得犹为重要了。
..焊锡珠产生的原因是多种因素造成的,再流焊中的温度时间,焊膏的印刷厚度,焊膏的组成成分,模板的制作,装贴压力,外界环境都会在生产过程中各个环节对焊锡珠形成产生影响。
..焊锡珠是在负责制板通过再流焊炉时产生的。
再流焊曲线可以分为四个阶段,分别为:预热、保温、再流和冷却。
预热阶段的主要目的是为了使印制板和上面的表贴元件升温到120-150度之间,这样可以除去焊膏中易挥发的溶剂,减少对元件的热振动。
因此,在这一过程中焊膏内部会发生气化现象,这时如果焊膏中金属粉末之间的粘结力小于气化产生的力,就会有少量焊膏从焊盘上流离开,有的则躲到片状阻容元件下面,再流焊阶段,温度接近曲线的峰值时,这部分焊膏也会熔化,而后从片状阻容元件下面挤出,形成焊锡珠,由它的形成过程可见,预热温度越高,预热速度越快,就会加大气化现象中飞溅,也就越容易形成锡珠。
因此,我们可以采取较适中的预热温度和预热速度来控制焊锡珠的形成。
..焊膏的选用也影响着焊接质量,焊膏中金属的含量,焊膏的氧化物含量,焊膏中金属粉末的粒度,及焊膏在印制板上的印刷厚度都不同程度影响着焊锡珠的形成。
....1:焊膏中的金属含量:焊膏中金属含量的质量比约为90-91%,体积比约为50%左右。
当金属含量增加时,焊膏的粘度增加,就能更有效地抵抗预热过程中气化产生的力。
另外,金属含量的增加,使金属粉末排列紧密,使其有更多机会结合而不易在气化时被吹散。
金属含量的增加也可以减小焊膏印刷后的塌落趋势,因此不易形成焊锡珠。
....2:焊膏中氧化物的含量:焊膏中氧化物含量也影响着焊接效果,氧化物含量越高,金属粉末熔化后结合过程中所受阻力就越大,再流焊阶段,金属粉末表面氧化物的含量还会增高,这就不利?quot;润湿"而导致锡珠产生。
....3:焊膏中金属粉末的粒度,焊膏中的金属粉末是极细小的球状,直径约为20-75um,在贴装细间距和超细间距的元件时,宜用金属粉末粒度较小的焊膏,约在20-45um之间,焊粒的总体表面积由于金属粉末的缩小而大大增加。
较细的粉末中氧化物含量较高,因而会使锡珠现象得到缓解。
....4:焊膏在印制板上的印刷厚度:焊膏的印刷厚度是生产中一个主要参数,焊膏印刷厚度通常在0.15-0.20mm之间,过厚会导致"塌落"促进锡珠的形成。
在制作模板时,焊盘的大小决定着模板上印刷孔的大小,通常,我们为了避免焊膏印刷过量,将印刷孔的尺寸制造成小于相应焊盘接触面积的10%。
我们做过这样的实践,结果表明这会使锡珠现象有相当程度的减轻。
..如果贴片过程中贴装压力过大,这样当元件压在焊膏上时,就可能有一部分焊膏被挤在元件下面,再流焊阶段,这部分焊膏熔化形成锡珠,因此,在贴装时应选择适当的贴装压力。
..焊膏通常需要冷藏,但在使用前一定要使其恢复至室温方可打开包装使用,有时焊膏温度过低就被打开包装,这样会使其表面产生水分,焊膏中的水分也会导致锡金珠形成。
..另外,外界的环境也影响锡珠的形成,我们就曾经遇到过此类情况,当印制板在潮湿的库房存放过久,在装印制板的真空袋中发现细小的水珠,这些水分都会影响焊接效果。
因此,如果有条件,在贴装前将印制板和元器件进行高温烘干,这样就会有效地抑制锡珠的形成。
..焊膏与空气接触的时间越短越好。
这是使用焊膏的基本原则。
取出一部分焊膏后,立即盖好盖子,特别是里面的盖子一定要向下压紧,将盖子与焊膏之间空气全部挤净,否则几天就可能报废。
..夏天空气温度大,当把焊膏从冷藏处取出时,一定要在室温下呆4-5小时再开后盖子。
如焊膏在1-2个月短期内即可用完,建议不必冷藏,这样可即用即开。
..夏天是最容易产生锡球的季节。
..由此可见,影响锡珠的形成有诸多因素,只顾调整某一项参数是远远不够的。
我们需要在生产过程中研究如何能控制各项因素,从而使焊接达到最好的效果。