注塑中常见30大问题
注塑品质问题总结范文

一、前言注塑工艺在塑料制品的生产中占据着重要的地位,然而,在注塑生产过程中,品质问题时有发生,严重影响了产品的质量和企业的声誉。
为了提高注塑产品的品质,减少品质问题的发生,现将我司近期注塑品质问题进行总结分析,并提出改进措施。
二、品质问题总结1. 产品外观缺陷(1)表面有油污、划痕、气泡等。
(2)产品尺寸不稳定,存在较大公差。
2. 产品内部缺陷(1)产品内部有空洞、缩孔、熔接痕等。
(2)产品内部有冷料、飞边等杂质。
3. 材料问题(1)原材料质量不稳定,导致产品性能波动。
(2)材料配比不当,影响产品性能。
4. 设备问题(1)模具设计不合理,导致产品缺陷。
(2)设备磨损严重,影响产品质量。
5. 操作问题(1)操作人员技能水平不足,导致产品品质下降。
(2)生产过程不规范,存在安全隐患。
三、原因分析1. 原材料问题:原材料质量不稳定,供应商管理不到位。
2. 设备问题:设备维护保养不及时,模具设计不合理。
3. 操作问题:操作人员技能水平不足,生产过程不规范。
4. 管理问题:品质管理制度不完善,缺乏有效的监督机制。
四、改进措施1. 优化原材料采购流程,提高原材料质量。
2. 加强设备维护保养,确保设备正常运行。
3. 提高操作人员技能水平,规范生产过程。
4. 完善品质管理制度,加强监督机制。
5. 加强与供应商的沟通与合作,提高原材料质量。
五、总结通过本次注塑品质问题总结,我司将针对存在的问题,采取有效措施进行改进。
在今后的生产过程中,我们要高度重视注塑品质问题,不断提高产品质量,以满足客户需求,提升企业竞争力。
同时,要加强员工培训,提高整体素质,确保生产过程规范化、标准化。
相信在全体员工的共同努力下,我司的注塑品质一定会得到全面提升。
注塑常见缺陷和原因分析
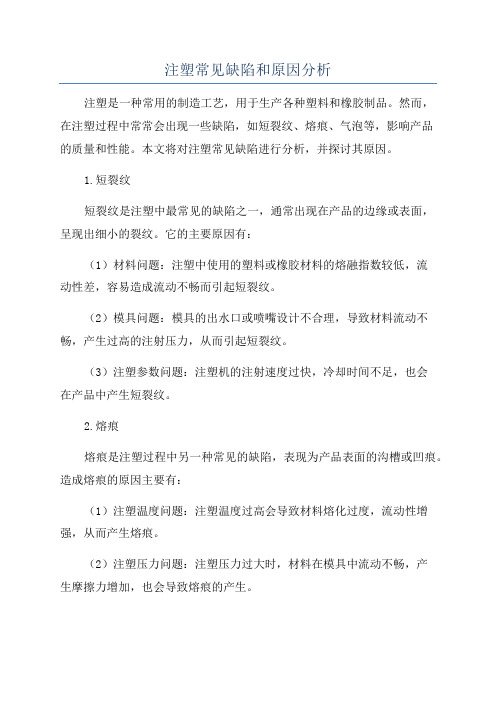
注塑常见缺陷和原因分析注塑是一种常用的制造工艺,用于生产各种塑料和橡胶制品。
然而,在注塑过程中常常会出现一些缺陷,如短裂纹、熔痕、气泡等,影响产品的质量和性能。
本文将对注塑常见缺陷进行分析,并探讨其原因。
1.短裂纹短裂纹是注塑中最常见的缺陷之一,通常出现在产品的边缘或表面,呈现出细小的裂纹。
它的主要原因有:(1)材料问题:注塑中使用的塑料或橡胶材料的熔融指数较低,流动性差,容易造成流动不畅而引起短裂纹。
(2)模具问题:模具的出水口或喷嘴设计不合理,导致材料流动不畅,产生过高的注射压力,从而引起短裂纹。
(3)注塑参数问题:注塑机的注射速度过快,冷却时间不足,也会在产品中产生短裂纹。
2.熔痕熔痕是注塑过程中另一种常见的缺陷,表现为产品表面的沟槽或凹痕。
造成熔痕的原因主要有:(1)注塑温度问题:注塑温度过高会导致材料熔化过度,流动性增强,从而产生熔痕。
(2)注塑压力问题:注塑压力过大时,材料在模具中流动不畅,产生摩擦力增加,也会导致熔痕的产生。
(3)模具设计问题:如果模具中的出水口或喷嘴设计不合理,也会在产品表面形成熔痕。
3.气泡气泡是注塑中常见的缺陷,表现为产品内部或表面的空腔。
气泡的形成原因有:(1)材料问题:注塑材料中含有过多的水分或挥发性物质,注塑过程中被加热蒸发,生成气泡。
(2)注塑温度过高:高温会导致材料熔化过度,容易产生气泡。
(3)注塑压力问题:过高的注塑压力会使材料在注塑过程中产生剧烈的振动,从而引起气泡。
(4)模具问题:模具中存在堵塞或不良的冷却系统,也会导致气泡的产生。
4.缩短问题缩短是指产品在冷却过程中出现尺寸缩小的现象。
产生缩短的主要原因有:(1)注塑温度过低:低温会使注塑材料的熔融程度不足,流动性降低,产生缩短。
(2)冷却时间不足:注塑材料冷却时间不足会导致产品未完全固化,容易产生缩短。
(3)注塑压力问题:过大的注塑压力会使产品产生内部的应力,引起尺寸缩小。
(4)模具问题:模具中存在过多的冷却系统,会导致材料过度冷却而使产品缩短。
注塑过程中常见的问题及解决方案

注塑过程中常见的问题及解决方案一、飞边(披锋)1. 问题描述- 这飞边就像塑料偷偷长出来的小翅膀,在注塑件的边缘或者分型面那里冒出来,看着可闹心了。
就像好好的一块蛋糕,边缘突然多出了一些不规则的奶油坨坨。
2. 解决方案- 首先得检查模具的合模力。
要是合模力不够,那塑料就会像调皮的小孩从门缝里挤出来。
适当增加合模力,把模具紧紧抱住,让塑料乖乖待在该待的地方。
- 模具的磨损也会导致飞边。
就像穿破了的鞋子会漏脚指头一样,磨损的模具缝隙变大了。
这时候就得修模啦,把那些磨损的地方补一补或者磨平。
- 注塑压力也不能太大。
如果压力太大,塑料就像被大力士猛推的水,到处乱流。
降低注塑压力,找到一个合适的值,既能把模具填满,又不会让塑料溢出来。
二、短射(缺料)1. 问题描述- 短射就像给一个杯子倒水,结果没倒满一样。
注塑件看着不完整,有些地方该有塑料的却空着,就像一个没发育好的小怪物。
2. 解决方案- 先看看注塑压力是不是太小。
压力小的话,塑料就像没力气的小蚂蚁,爬不到模具的每个角落。
增加注塑压力,让塑料充满整个模具型腔。
- 塑料的流动性也很关键。
如果塑料太黏,就像浓稠的糨糊,很难流到模具的远端。
这时候可以提高料筒温度,让塑料变得稀一点,流动性更好,就像把糨糊加热变成稀粥一样,能顺利流到各个地方。
- 浇口尺寸也可能有问题。
要是浇口太小,就像一个小得可怜的水龙头,水流不出来多少。
适当扩大浇口尺寸,让塑料能畅快地流进模具。
三、气泡(气穴)1. 问题描述2. 解决方案- 注塑速度可能太快了。
塑料像一阵风呼呼地冲进模具,把空气都裹在里面了。
降低注塑速度,让塑料慢慢流进去,就像散步一样,这样空气就有机会跑出来了。
- 模具的排气也很重要。
如果模具没有排气孔或者排气不良,空气就被困在里面出不来。
在模具上开排气槽或者使用透气钢材料,给空气一条逃跑的路。
- 塑料干燥不彻底也会产生气泡。
如果塑料里有水份,加热的时候就会变成水蒸气,形成气泡。
注塑生产中常见的问题

注塑生产中常见的问题1. 刚开机时产品跑披锋,生产一段时间后产品缺胶的原因及解决方案。
刚开机时注塑机料管内的熔胶由于加热时间长,熔胶粘度低,流动性好,产品易跑披锋,生产一段时间后由于熔胶不断把热量带走,造成熔胶不足,粘度大,流动性差,使产品缺胶。
在生产一段时间后,逐渐提高料管温度来解决。
2. 在生产过程中,产品缺胶,有时增大射胶压力和速度都无效,为什么?解决方法?是因为生产中熔胶不断把热量带走,造成熔胶不足,胶粘度大,流动性差,使产品缺胶。
提高料管温度来解决。
3. 产品椭圆的原因及解决方法。
产品椭圆是由于入胶不均匀,造成产品四周压力不匀,使产品椭圆,采用三点入胶,使产品入胶均匀。
4. 精密产品对模具的要求。
要求模具材料刚性好,弹变形小,热涨性系数小。
5. 产品耐酸试验的目的产品耐酸试验是为了检测产品内应力,和内应力着力点位置,以便消除产品内应力。
6. 产品中金属镶件受力易开裂的原因及解决方法。
产品中放镶件,在啤塑时由于热熔胶遇到冷镶件,会形成内应力,使产品强度下降,易开裂。
在生产时,对镶件进行预热处理。
7. 模具排气点的合理性与选择方法。
模具排气点不合理,非但起不到排气效果,反而会造成产品变形或尺寸变化,所以模具排气点要合理。
选择模具排气点,应在产品最后走满胶的地方和产品困气烧的地方开排气。
8. 产品易脆裂的原因及解决方法。
产品易脆裂是产品使用水口料和次料太多造成产品易脆裂,或是料在料管内停留时间过长,造成胶料老化,使产品易脆裂。
增加新料的比例,减少水口料回收使用次数,一般不能超过三次,避免胶料在料管内长时间停留。
9. 加玻纤产品易出现泛纤的原因及解决方法是由于熔胶温度低或模具温度低,射胶压力不足,造成玻纤在胶内不能与塑胶很好的结合,使纤泛出。
加高熔胶温度,模具温度,增大射胶压力。
10. 进料口温度对产品的影响。
进料口温度的过高或过低,都会造成机器回料不稳定,使加料量不稳定,而影响产品的尺寸和外观。
注塑成型常见不良及对策
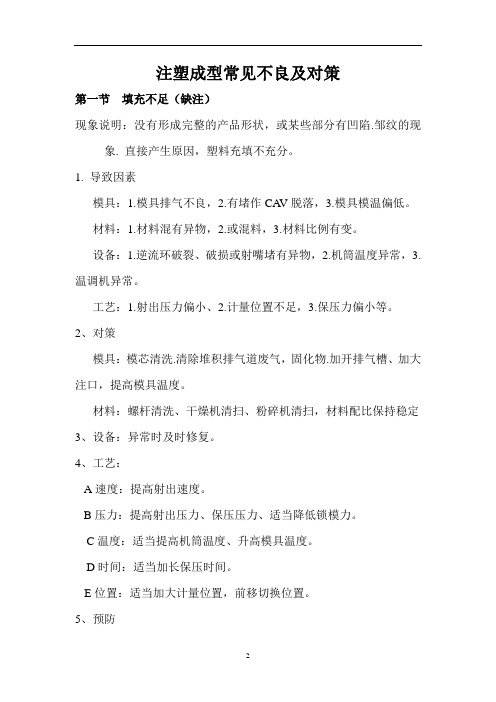
注塑成型常见不良及对策第一节填充不足(缺注)现象说明:没有形成完整的产品形状,或某些部分有凹陷.邹纹的现象. 直接产生原因,塑料充填不充分。
1. 导致因素模具:1.模具排气不良,2.有堵作CA V脱落,3.模具模温偏低。
材料:1.材料混有异物,2.或混料,3.材料比例有变。
设备:1.逆流环破裂、破损或射嘴堵有异物,2.机筒温度异常,3.温调机异常。
工艺:1.射出压力偏小、2.计量位置不足,3.保压力偏小等。
2、对策模具:模芯清洗.清除堆积排气道废气,固化物.加开排气槽、加大注口,提高模具温度。
材料:螺杆清洗、干燥机清扫、粉碎机清扫,材料配比保持稳定3、设备:异常时及时修复。
4、工艺:A速度:提高射出速度。
B压力:提高射出压力、保压压力、适当降低锁模力。
C温度:适当提高机筒温度、升高模具温度。
D时间:适当加长保压时间。
E位置:适当加大计量位置,前移切换位置。
5、预防A、产前模具分解清洗,产后及时防锈保养,生产过程中定时清洗。
B、现场异常处理必须防止金属物掉入螺杆。
C、材料管理操作,不可混料。
D、模具温度、成形条件定时点检。
第二章飞边现象说明:产品外围或内围形成薄膜状、超出完整产品形状。
产生原因:塑料充填过多或模芯缺损、配合间隙大、模芯腐蚀而造成。
1、飞边形成:A、模具本身(设计)缺陷产生飞边。
如:本司“408”B、型修后,配合间隙大,导致飞边。
2、正常量产出现飞边,主要有以下几点:A、材料干燥不充分,导致飞边。
B、产品压模,二次成形造成飞边。
如:本司PDIC BASE,产品压模,合模面受损,导致飞边。
C、模芯腐蚀,清洗后导致飞边。
如:82机种890产品。
D、模芯进胶:如本司“389”柱子合模线飞边(进胶造成)E、粉末、拉丝二次成形导致飞边,主要表现在二分模。
如:818F、混料:因材料流动指数变异导致飞边。
如90混有900P等G、材料比例(原:再):变更导致飞边。
H、设备异常:如计量不稳定,机筒温度异升高,模温升高。
注塑成型常见不良现象及处理措施

注塑成型常见不良现象及处理措施注塑成型常见的不良现象有以下几种:
1. 短射:指注塑料进模型中未充满模腔,导致产品缺陷。
处理措施:增加注射
压力、延长注射时间、增加料缸温度、增加模具温度、增加模具出料口直径等。
2. 气泡:指产品表面或者内部浮现气泡,影响产品质量。
处理措施:增加注射
压力、延长注射时间、增加模具温度、增加料缸温度、增加模具出料口直径、增加模具排气孔等。
3. 热熔线:指产品表面浮现细小的线状缺陷,通常是由于注射速度过快导致的。
处理措施:减小注射速度、增加模具温度、增加模具出料口直径等。
4. 毛刺:指产品表面浮现细小的凸起,通常是由于模具设计不合理或者模具磨
损导致的。
处理措施:修复模具、修改模具设计、增加模具温度、增加模具出料口直径等。
5. 缩水:指产品尺寸缩小,通常是由于注射压力不足或者冷却时间不足导致的。
处理措施:增加注射压力、延长冷却时间、增加模具温度等。
6. 毛洞:指产品表面或者内部浮现凹陷,通常是由于注射速度过快或者模具设
计不合理导致的。
处理措施:减小注射速度、修改模具设计、增加模具温度等。
处理不良现象的关键是找到问题的根源,然后针对性地采取相应的处理措施。
同时,注塑成型过程中的参数控制和模具维护也是关键的因素,需要进行定期检查和调整。
注塑模具问题点汇总清单
注塑模具问题点汇总清单一、外观问题1. 飞边(披锋)- 这模具做出来的产品边缘毛毛糙糙的,就像人没刮干净胡子似的。
在合模的地方或者一些薄壁处,老是有多余的塑料跑出来,形成飞边,影响产品的外观,也可能会刮伤人呢。
2. 缩水痕- 产品表面有那种凹下去的小坑洼,就像人脸上突然长了麻子一样。
在产品壁厚比较厚的地方,冷却的时候不均匀,就容易出现这种缩水痕,看起来可丑了。
3. 流痕- 那些像波浪一样的纹路在产品表面,就像有人在塑料还没干的时候乱划了几笔。
塑料在模具里流动的时候不顺畅,就产生了这种流痕,让产品看起来很不精致。
4. 气泡- 产品里面有像小珠子一样的空洞,就像面包没发好里面有大气泡一样。
注塑的时候,空气没排干净或者塑料里有水分,就会产生这种气泡,感觉产品就像个空心萝卜。
5. 熔接痕- 产品表面有一条明显的线,就像衣服上缝了一道歪歪扭扭的补丁。
不同的塑料流在模具里汇合的时候没融合好,就出现了熔接痕,把产品的美观都破坏了。
6. 表面光泽度不一致- 有的地方亮晶晶的,有的地方却雾蒙蒙的,就像人穿了件一半是绸缎一半是粗布的衣服。
可能是模具表面的光洁度不一样,或者脱模剂喷得不均匀造成的。
二、尺寸问题1. 尺寸偏差过大- 做出来的产品大小跟设计的不一样,有的地方大得像个胖子,有的地方小得像个瘦子。
可能是模具的型腔尺寸没加工准确,或者注塑的时候温度、压力等工艺参数影响了塑料的收缩率。
2. 形状变形- 本来应该是方方正正的产品,结果变成了歪歪扭扭的四边形,就像被人捏过的橡皮泥。
可能是模具的结构不合理,在脱模的时候对产品施加了不均匀的力,或者冷却不均匀导致产品变形。
三、结构问题1. 脱模困难- 产品在模具里就像被胶水粘住了一样,死活不愿意出来。
可能是拔模斜度不够,或者模具的表面粗糙度太大,摩擦力太大,让产品卡在里面出不来。
2. 模具零件损坏- 像那些顶针啊、滑块啊,有时候会断掉或者磨损得很厉害。
就像人的牙齿掉了或者磨平了一样,顶针断了就没法正常顶出产品,滑块磨损了可能会导致合模不严或者产品表面划伤。
注塑缺陷及其解决方法
注塑缺陷及其解决方法注塑是一种常用的塑料加工方法,通过将加热熔融的塑料材料注入到模具中,冷却后形成所需的产品。
然而,在注塑过程中,往往会出现一些缺陷,影响产品的质量。
以下是一些常见的注塑缺陷及其解决方法。
1.气泡:气泡是注塑中最常见的缺陷之一、它们可能是由于塑料材料中的挥发性成分排放不完全,或者是熔融塑料中的气体在注射过程中迅速扩散而形成的。
解决气泡问题的方法包括:合理选择塑料材料、充分预干燥材料、提高注射速度和压力、优化模具结构等。
2.沉痕:沉痕是表面上的凹陷,通常是由于塑料材料的收缩不均匀或冷却不充分造成的。
解决沉痕问题的方法包括:调整注射温度和压力、改善模具冷却系统、增加冷却时间等。
3.翘曲:翘曲是注塑过程中产品变形的一种形式。
它可能是由于模具设计不合理、注射温度过高或产品冷却不充分引起的。
解决翘曲问题的方法包括:优化模具结构、调整注射温度和压力、增加冷却时间等。
4.热断裂:热断裂指的是在注塑加工过程中,产品的一些部位出现开裂或裂纹。
它可能是由于注射过程中产生的应力超过了材料的承受能力引起的。
解决热断裂问题的方法包括:调整注射速度和压力、改变注射顺序、增加降温时间等。
5.色差:注塑产品在颜色上出现不均匀或异色现象。
这可能是由于原料配比不准确或注射过程中的温度变化等原因造成的。
解决色差问题的方法包括:准确控制原料比例、稳定注射温度、使用色差控制剂等。
6.熔接线:熔接线是由于注塑模具的设计和操作问题导致两个或多个熔融塑料部分相互连接而形成的。
解决熔接线问题的方法包括:调整模具结构,避免部件交汇点过多,调整注射速度和压力等。
总之,注塑缺陷的解决方法主要包括调整材料配比、优化模具结构、控制注射温度和压力、增加冷却时间等。
同时,及时调整机器参数、进行模具维护和清洁,以保证注塑过程的稳定性和可靠性。
通过以上的措施,可以有效减少注塑缺陷,提高产品质量。
常见注塑产品缺陷及处理措施
现象
产生原因
处理措施
产品不足
填充不满
1、 注塑速度不足。2、塑料短缺。3、螺杆在行程结束处没留下螺杆垫料。4、运行时间变化。5、射料缸温度太低。6、注塑压力不足。7、射嘴部分被封。8、射嘴或射料缸外的加热器不能运作。9、注塑时间太短。10、塑料贴在料斗喉壁上。11、注塑机容量太小(即注射重量或塑化能力)。12、模温太低。13、没有清理干净模具的防锈油。14、止退环损坏,熔料有倒流现象。
注塑件尺寸差异
1、 输入射料缸内的塑料不均。2、射料缸温度或波动的范围太大。3、注塑机容量太小。4、注塑压力不稳定。5、螺杆复位不稳定。6、运作时间的变化、溶液黏度不一致。7、注射速度(流量控制)不稳定。8、使用了不适合模具的塑料品种。9、考虑模温、注射压力、速度、时间、和保压等对产品的影响。
1、 检查有无充足的冷却水流经料斗喉以保持正确的温度。2、检查是否劣质或松脱的热电偶。3、检查与温度控制器一起使用的热电偶是否属于正确类型。4、检查注塑机的注塑量和塑化能力,然后与实际注塑量和每小时的注塑料用量进行比较。5、检查是否每次运作都有稳定的熔融热料。6、检查回流防止阀有否泄露,若有需要就进行更换。7、检查是否错误的进料设定。8、保证螺杆在每次运作复回位置都是稳定的,即不多于0.4mm的变化。9、检查运作时间的不一致性。10、使用背压。11、检查液压系统运作是否正常,油温是否过高或过低(25-60℃)。12、选择适合模具的塑料品种(主要从缩率及机械强度考虑)。13、重新调整整个生产工艺。
1、 增加注塑速度。2、检查料斗内的塑料量。3、检查是否正确设定了注射行程,需要的话进行更改。4、检查止逆阀是否磨损或出现裂缝。5、检查运作是否稳定。6、增加熔胶温度。7、增加背压。8、增加注塑速度。9、检查射嘴孔有没有异物或未塑化塑料。1、增加螺杆向前时间。12、增加料斗喉区或降低射料缸后区温度。13、用较大的注塑机。14、适当升高模温。15、清理干净模具内的防锈剂。16、检查或更换止退环。
注塑产品常见缺陷
注塑产品常见缺陷注塑产品常见缺陷及其原因分析注塑产品在生产过程中可能会遇到各种缺陷,这些缺陷可能源于产品设计、模具制造、材料选择、注塑工艺等多个因素。
以下是一些常见的注塑产品缺陷及可能的原因分析:1.填充不足(缺料)这可能是由于注塑压力不足、注射时间过短、模具排气不良、浇口设计不合理等原因造成的。
解决这个问题的方法包括增加注塑压力、延长注射时间、优化模具排气设计、改进浇口位置等。
2.溢料(毛边)溢料通常是由于注射压力过高、浇口设计不当、模具磨损等原因造成的。
解决溢料问题的方法包括降低注塑压力、优化浇口设计、修复模具磨损等。
3.气泡(气孔)气泡可能是由于塑料在模具中未完全填满、气体未完全排出、注射速度过快等原因造成的。
解决气泡问题的方法包括降低注射速度、增加冷却时间、优化模具设计等。
4.变形变形可能是由于产品结构不合理、冷却不均匀、模具温度波动等原因造成的。
解决变形问题的方法包括优化产品结构设计、改善冷却条件、稳定模具温度等。
5.银纹(流纹)银纹可能是由于塑料流动不均匀、模具温度过低、注射速度过快等原因造成的。
解决银纹问题的方法包括优化注射条件、提高模具温度、降低注射速度等。
6.裂纹(龟裂)裂纹可能是由于产品结构设计不合理、材料韧性不足、注射压力过高等原因造成的。
解决裂纹问题的方法包括优化产品结构设计、更换韧性更好的材料、降低注射压力等。
7.翘曲(扭曲)翘曲可能是由于产品结构设计不合理、模具温度不均匀、注射压力过低等原因造成的。
解决翘曲问题的方法包括优化产品结构设计、改善冷却条件、提高注射压力等。
8.冷块(冷凝物)冷块可能是由于塑料在冷却过程中速度过快、模具温度过低等原因造成的。
解决冷块问题的方法包括降低冷却速度、提高模具温度等。
9.喷射痕迹(蛇形纹)喷射痕迹可能是由于注射速度过快、浇口设计不当等原因造成的。
解决喷射痕迹问题的方法包括降低注射速度、优化浇口设计等。
10.颜色分布不均(色差)颜色分布不均可能是由于材料混合不均匀、注塑条件不稳定等原因造成的。
- 1、下载文档前请自行甄别文档内容的完整性,平台不提供额外的编辑、内容补充、找答案等附加服务。
- 2、"仅部分预览"的文档,不可在线预览部分如存在完整性等问题,可反馈申请退款(可完整预览的文档不适用该条件!)。
- 3、如文档侵犯您的权益,请联系客服反馈,我们会尽快为您处理(人工客服工作时间:9:00-18:30)。
注塑中常见30大问题
刚开机时产品跑披锋,生产一段时间后产品缺胶的原因及解决方案。
1. 刚开机时注塑机料管内的熔胶由于加热时间长,熔胶粘度低,流动性好,产品易跑披锋,生产一段时间后由于熔胶不断把热量带走,造成熔胶不足,粘度大,流动性差,使产品缺胶。
在生产一段时间后,逐渐提高料管温度来解决。
2.在生产过程中,产品缺胶,有时增大射胶压力和速度都无效,为什么?解决方法?
是因为生产中熔胶不断把热量带走,造成熔胶不足,胶粘度大,流动性差,使产品缺胶。
提高料管温度来解决。
3.产品椭圆的原因及解决方法。
产品椭圆是由于入胶不均匀,造成产品四周压力不匀,使产品椭圆,采用三点入胶,使产品入胶均匀。
4.精密产品对模具的要求。
模具材料刚性好,弹变形小,热涨性系数小。
5.产品耐酸试验的目的
产品耐酸试验是为了检测产品内应力,和内应力着力点位置,以便消除产品内应力。
6.产品中金属镶件受力易开裂的原因及解决方法。
产品中放镶件,在啤塑时由于热熔胶遇到冷镶件,会形成内应力,使产品强度下降,易开裂。
在生产时,对镶件进行预热处理。
7.模具排气点的合理性与选择方法。
模具排气点不合理,非但起不到排气效果,反而会造成产品变形或尺寸变化,所以模具排气点要合理。
选择模具排气点,应在产品最后走满胶的地方和产品困气烧的地方开排气。
8.产品易脆裂的原因及解决方法。
产品易脆裂是产品使用水口料和次料太多造成产品易脆裂,或是料在料管内停留时间过长,造成胶料老化,使产品易脆裂。
增加新料的比例,减少水口料回收使用次数,一般不能超过三次,避免胶料在料管内长时间停留。
9.加玻纤产品易出现泛纤的原因及解决方法
是由于熔胶温度低或模具温度低,射胶压力不足,造成玻纤在胶内不能与塑胶很好的结合,使纤泛出。
加高熔胶温度,模具温度,增大射胶压力。
10.进料口温度对产品的影响。
进料口温度的过高或过低,都会造成机器回料不稳定,使加料量不稳定,而影响产品的尺寸和外观。
11.透明产品有白点的原因及解决方法。
透明产品有白点是因为产品内进入冷胶造成,或料内有灰尘造成的。
提高射嘴温度,加冷料井,原料注意保存,防止灰尘进入。
12.什么是注塑机的射出能力?
射出能力※※=射出压力(kg/cm2)×射出容积(cm3)/1000
13.什么是注塑机的射出马力?
射出马力pw(kw)=射出压力(kg/cm2)×射出率(cm3/sec)×9.8×100%
刚开机时产品跑披锋,生产一段时间后产品缺胶的原因及解决方案。
刚开机时注塑机料管内的熔胶由于加热时间长,熔胶粘度低,流动性好,产品易跑披锋,生产一段时间后由于熔胶不断把热量带走,造成熔胶不足,粘度大,流动性差,使产品缺胶。
在生产一段时间后,逐渐提高料管温度来解决。
14.球面丝印后开裂问题.
由于产品表面存在应力,造成丝印后开裂.增加模具温度,减小应力;可用退火的方法消除应力.
15.眼镜架,水口边易断问题.
射胶压力和保压压力大,水口边残存内应力,造成产品易断.尽量减小射胶压力和保压压力,适当提高模具温度来解决.
16.电器外壳,四个装配柱子,打螺丝时爆裂问题.
由于柱子存在夹水线,造成产品装配柱子易暴裂.模具增加排气,适当提高模温,加快射胶速度来减小夹水线.
17.产品变形问题.
产品变形主要是热收缩时不平衡造成产品变形,或由于产品本身内应力作用下使产品变形.
18.透明pc外壳气泡问题。
原料干燥不够;产品存在胶厚薄不均现象,模具排气不良,原料易分解都可能造成产品气泡.
充分干燥原料,增大模具排气,尽量减少胶厚薄不均现象.
19.复印机,磁性材料的啤塑问题。
应采用高模温,快速射胶方法.
20.产品包胶,水口边缩水问题。
模具排气不良,射胶速度慢,保压压力和时间不够,都能造成水口缩水。
增大模具排气,适当提高射胶速度,增加保压压力和时间.
21.产品内应力,造成产品放置一段时间后爆裂问题。
由于产品内残存应力,产品放置一段时间后由于应力的作用,使产品爆裂.
提高啤塑时的模具温度,降低射胶压力,来消除产品应力,产品可用退火的方法消除应力.
22.abs料在用黑色色母时,造成产品易断裂脱皮问题。
是色母的颜料中用了碳粉过多原因,造成产品脱皮.更换色母颜料.
23.一台180吨14安士机,产品一出四cd盒共120克,外观良好,无批峰,但其中一只重2克,为什么?
模具产品一出四,由于模具进胶不平衡造成其中一只产品啤塑饱满,密度大,出现重2克现象.
24.一台100吨液压曲肘机使用了三年,模具锁紧后,经常打不开。
是由于机器曲肘磨损,造成开模不平衡,所以模具锁紧后,会经常打不开.
25.一台7安士机使用了二年,出现射胶不稳定,一啤批峰一啤缺胶,换过油封和分胶头,系统压力也稳定,就不行。
由于螺杆磨损或损坏,造成回料不匀,所以会出现射胶不稳定.
26.一台150吨新机啤pp水口料半年,原来熔胶最快3秒,而现在要6秒。
由于螺杆磨损,造成回料慢.
27.一啤塑师父在调试一产品,出现缺胶,速度或压力升一点,产品没反应,再升一点就出批峰?
机器锁模机构磨损,造成锁模有间隙,所以会出现披锋.
28.一台机用了二年,啤货时炮筒中间温度偏高,关了电源也没用。
由于螺杆磨损变得粗糙,啤塑回料时磨擦产生热,使炮筒中间温度偏高.
某厂有新旧机十几台,油封经常漏油,换了一段时间又漏?
油温过高使油封易老化损坏,漏油;油缸芯子磨损,造成刮坏油封漏油.
问题18-23请见教材二《注塑机维护保养》相关图解。
29.油泵电机起动电路的讲解。
油泵电机起动是采用星三角起动
30.省电泵原理讲解。
省电泵即为变流量泵,当机器有动作时,压力油通过油阀油缸推动机械动作,再回到油箱,当机器没有动作时,压力油直接回到油箱。
31.电子线路板输入与输出的讲解。
由各个动作感应开关和电子尺等信号输入电子版,电脑通过运算后再输出给油阀,执行动作。
32.略
33.油封顽固性漏油的原因及预防。
油缸芯子磨损刮坏油封,造成顽固性漏油,保持油缸芯子干净,避免磨损预防刮坏油封造成漏油。
34.压力与流量线性对注塑工艺的影响。
压力与流量线性成比例,对注塑工艺的参数准确和稳定有着重要意义。
35.生产周期变慢的原因及改善措施。
生产周期变慢的原因主要是冷却时间延长,和螺杆因磨损使回料时间加长。
改善模具冷却效果,缩短冷却时间,更换磨损的螺杆,使回料时间缩短,加快生产周期。
36.熔胶时发出尖叫声的原因与处理方案。
熔胶时发出尖叫声是由于螺杆与料磨擦发出的或螺杆与炮筒磨擦发出的。
对螺杆抛光处理或电镀,使表面光滑减小磨擦;调整螺杆的中心度使它不与炮筒发生磨擦。
37.锁模平行度的检测与调整方法。
用四个百分表测定机器锁模时哥林柱的拉伸长度,看是否在允许公差内,来检测哥林柱锁模平等度。
然后调整哥林柱大螺母来调整锁模平行度。
(看另一本书《注塑机原理》)
38.哥林柱折断的原因与预防措施。
哥林柱折断的原因是由于锁模不平等造成的。
调整锁模平行度来预防哥林柱折断。
39.曲肘磨损的原因分析。
曲肘磨损的原因是,曲肘润滑不良造成的。