塑胶模具及成型缺陷分析3.pptx
合集下载
注塑缺陷的分析ppt
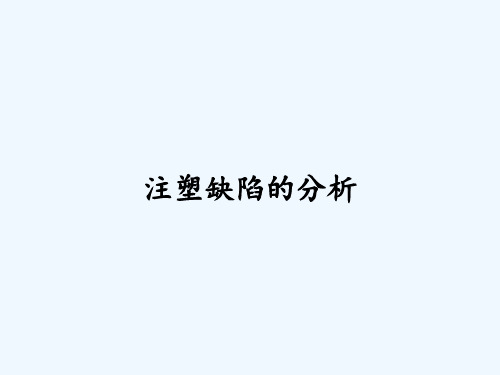
强,因为玻璃微珠不存在方向性。
1、选择合理得浇口位置及 形式,将熔接线引导至不显
眼位置。
1、增加模温;2、加高熔体温度;3、优化注射速度 及注射压力。
六、湿气痕; 湿气痕由模壁上得冷凝水汽造成,就是顺着塑流得方向出现得灰白色喷射
线段,一些个案表现为表面气泡及粗糙。
故障件图片
成形原因:塑料粒子在存储或注塑过程中吸入了空气中得水分,当这种潮湿得 粒子在注塑熔化时,水分便变为水蒸气泡。由于熔料得模壁流动速度慢于中心 部位,这样这些水蒸气泡就被推向了塑件得表层,受压得气泡因为补偿压力而 爆破,随之被熔胶得流动波峰压至变形,并在模壁上固化。
度缺陷
1、选择合理得浇口位置(将熔接线放在不影响 产品处或将料流改为75°以上得汇流);2、模具 水路要合理,让有熔接线得模具对应处温度能调
得更高些;3、要有充分得排气。
1、加大保压;2、优化注射速度;3、增加熔胶温度 ;5、增加模具温度。
三、喷射纹; 喷射纹就是像蛇形般蜿蜒得粗糙得编织纹,出现在注塑件表面上, 极大得影响着零件得外观质量。 喷射纹一般均从浇口处开始,有时也可以从塑件得狭窄处开始。
1、选择合理得浇口大小及形式,需保证能 充分得补压;2、模具水路要合理,通过模 温得控制使其更好补压;3、要有充分得
排气。
1、料筒得储料行程就是否足够;2、保压及保压 时间就是否太小;3、注射速度就是否太小;4、增
加熔胶温度;5、增加模具温度。
二、熔接线; 熔接线一般均以线形方式显现。熔接线得出现会直接影响零件得 外观质量及零件强度。
得出现。
直接对着空腔得细小得浇 口最易形成喷射纹
优化后得浇口,料流通过上侧 壁模腔得阻挡,使前锋料与后 面得料流能很好得融合在一
1、选择合理得浇口位置及 形式,将熔接线引导至不显
眼位置。
1、增加模温;2、加高熔体温度;3、优化注射速度 及注射压力。
六、湿气痕; 湿气痕由模壁上得冷凝水汽造成,就是顺着塑流得方向出现得灰白色喷射
线段,一些个案表现为表面气泡及粗糙。
故障件图片
成形原因:塑料粒子在存储或注塑过程中吸入了空气中得水分,当这种潮湿得 粒子在注塑熔化时,水分便变为水蒸气泡。由于熔料得模壁流动速度慢于中心 部位,这样这些水蒸气泡就被推向了塑件得表层,受压得气泡因为补偿压力而 爆破,随之被熔胶得流动波峰压至变形,并在模壁上固化。
度缺陷
1、选择合理得浇口位置(将熔接线放在不影响 产品处或将料流改为75°以上得汇流);2、模具 水路要合理,让有熔接线得模具对应处温度能调
得更高些;3、要有充分得排气。
1、加大保压;2、优化注射速度;3、增加熔胶温度 ;5、增加模具温度。
三、喷射纹; 喷射纹就是像蛇形般蜿蜒得粗糙得编织纹,出现在注塑件表面上, 极大得影响着零件得外观质量。 喷射纹一般均从浇口处开始,有时也可以从塑件得狭窄处开始。
1、选择合理得浇口大小及形式,需保证能 充分得补压;2、模具水路要合理,通过模 温得控制使其更好补压;3、要有充分得
排气。
1、料筒得储料行程就是否足够;2、保压及保压 时间就是否太小;3、注射速度就是否太小;4、增
加熔胶温度;5、增加模具温度。
二、熔接线; 熔接线一般均以线形方式显现。熔接线得出现会直接影响零件得 外观质量及零件强度。
得出现。
直接对着空腔得细小得浇 口最易形成喷射纹
优化后得浇口,料流通过上侧 壁模腔得阻挡,使前锋料与后 面得料流能很好得融合在一
塑料件的缺陷及造成的原因ppt课件
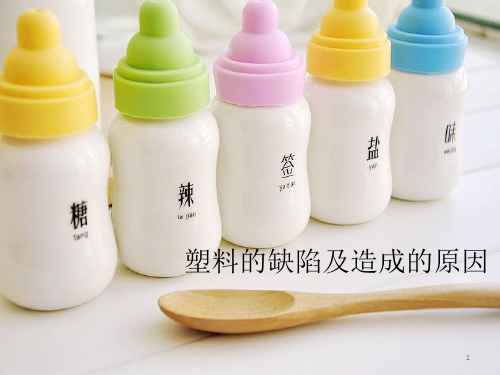
7
2.飞边
飞边又称溢边,是冲模 时,熔体从模具的分型面 及其他配合面处溢出,经 冷却后形成。
8
产生原因及解决措施
产生原因
1.注射过量 2.锁模力不足 3.材料流动性过好 4.分型面闭合不严,有间隙或杂物 5.型腔和型芯部分滑动零件间隙过大 6.模具各承接面平行度差 7.模具安装时未被压紧
解决措施
解决措施
从形成熔接痕的原因而言,要减少熔接痕,就要降低注射或挤出过程 中物料的"分流后汇合"现象发生的可能性。有如下方法:
1)提高模具温度 2)调整注射速度 3)全面排气 4)保持模具表面清洁 5)调整注射压力和补塑压力 6)合理设置浇口位置
19
9.表面收缩
通常由于制品上受力不足,物料 充模不足以及制品设计不合理,凹痕 常出现在与壁厚相近的薄壁部分。
炭化
认真清洗料筒使之干净 使用前烘干塑料,去除水分 清理型腔表面,应无杂物及水分存在 合理配料 采用新材料 控制熔料温度 控制熔料加热时间
17
8.熔接痕
熔接痕是指两股料流相 遇熔接而产生的表面缺陷。
18
形成原因
塑件表面的一种线状痕迹,系由注射或挤出中若干股流料在模具中分 流汇合,熔料在界面处未完全熔合,彼此不能熔接为一体,造成熔合印迹, 影响塑件的外观质量及力学性能。
6
解决措施
(1)变更塑件设计:应设法使射出的熔料容易流动,如增 大壁厚。
(2)变更模具设计:增加浇口尺寸或数目,以缩短流动长 度。增大流道系统尺寸,以减少流动阻力。增加排气孔尺 寸与数目。将排气孔设置在最后充填区域,以利排气,设 置均匀冷却。
(3)调整成型工艺:增大注射压力;增大注射量;增加注 射速度以产生更多的黏滞热,降低熔料粘度。
2.飞边
飞边又称溢边,是冲模 时,熔体从模具的分型面 及其他配合面处溢出,经 冷却后形成。
8
产生原因及解决措施
产生原因
1.注射过量 2.锁模力不足 3.材料流动性过好 4.分型面闭合不严,有间隙或杂物 5.型腔和型芯部分滑动零件间隙过大 6.模具各承接面平行度差 7.模具安装时未被压紧
解决措施
解决措施
从形成熔接痕的原因而言,要减少熔接痕,就要降低注射或挤出过程 中物料的"分流后汇合"现象发生的可能性。有如下方法:
1)提高模具温度 2)调整注射速度 3)全面排气 4)保持模具表面清洁 5)调整注射压力和补塑压力 6)合理设置浇口位置
19
9.表面收缩
通常由于制品上受力不足,物料 充模不足以及制品设计不合理,凹痕 常出现在与壁厚相近的薄壁部分。
炭化
认真清洗料筒使之干净 使用前烘干塑料,去除水分 清理型腔表面,应无杂物及水分存在 合理配料 采用新材料 控制熔料温度 控制熔料加热时间
17
8.熔接痕
熔接痕是指两股料流相 遇熔接而产生的表面缺陷。
18
形成原因
塑件表面的一种线状痕迹,系由注射或挤出中若干股流料在模具中分 流汇合,熔料在界面处未完全熔合,彼此不能熔接为一体,造成熔合印迹, 影响塑件的外观质量及力学性能。
6
解决措施
(1)变更塑件设计:应设法使射出的熔料容易流动,如增 大壁厚。
(2)变更模具设计:增加浇口尺寸或数目,以缩短流动长 度。增大流道系统尺寸,以减少流动阻力。增加排气孔尺 寸与数目。将排气孔设置在最后充填区域,以利排气,设 置均匀冷却。
(3)调整成型工艺:增大注射压力;增大注射量;增加注 射速度以产生更多的黏滞热,降低熔料粘度。
塑料模具制品常见缺陷及解决办法ppt课件

排气不良
改善排气系统
浇口位置不对称,熔体进入各 型腔的速度不同,各型腔中的 浇口尽量设置在对称处 制品冷却不均衡
冷却系统设计不合理,冷却不 均衡或冷却不足
改善冷却系统
可编辑ppt
23
凹陷成因及改善措施 -- 注塑工艺
熔体温度太高
降低熔体温度
模具温度太高
适当加大冷却水量或降低冷却 水温度
注射时间和保压时间太短 适当延长注射时间和保压时间
完整,如图所示 ❖ 短射的主要产生原因是注射压力或注射速度太低,熔体在
流向最末端的过程中冷却,通常在低熔料温度和模温的条 件下注射高粘度原料时会碰到这种情况,它也会发生在保 压设置过低的时候
可编辑ppt
7
短射成因及改善措施 -- 注塑模具
模具排气结构欠佳
修正或改善排气结构
浇口或流道的截面积较小且 长,熔体பைடு நூலகம்力在流动过程中 损失太大
换用较大直径喷嘴
可编辑ppt
17
熔合纹成因及改善措施 -- 原料
润滑剂太少,熔体的流动性差 适当增加润滑剂的添加量
含湿量大或易挥发物含量高
干燥原材料或清除易挥发物 质
可编辑ppt
18
喷射流(Jetting)
❖ 喷射流是指当熔体以高速流过喷嘴、流道、或浇口等狭窄 的区域后,进入开放或较宽厚的区域,并且没有与模壁接 触,发生喷射。蛇状的喷射流使熔体折叠而互相接触,造 成小规模的缝合线,如图所示
修正或改善浇注系统
薄壁处的厚度不够
增加截面厚度
没有冷料井或冷料井设计不 合理,熔体进入型腔并快速 冷凝,使得熔体流动不畅
合理设计冷料井
可编辑ppt
8
短射成因及改善措施 -- 注塑工艺
超详细注塑缺陷分析ppt课件
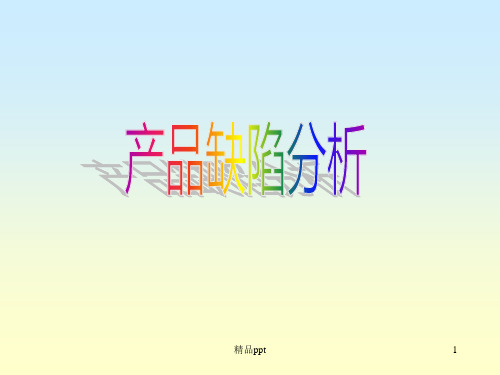
图1. 试样上出现的凹痕
精品ppt
15
(2)凹痕的生成原因
(2-1) 有效保压偏低:树脂填补偏少
在保压过程中,通过保压压力压入来填补因冷却固化→收缩的树脂量。如果因某种原因变成 有效保压偏低=树脂难以填补的状态,则在模具温度偏高时就容易形成凹痕,而在模具温 度偏低时容易形成空洞。
图2. 保压偏低时产生凹痕
图3. 模温引发空洞或凹精痕品ppt
13
(3) 真空空洞的对策
(3-1) 补充树脂
工艺上: · 确认转压点 · 提高保压压力;延长保压时间
模具上: · 增大浇口尺寸 · 增大主流道和分流道的口径 · 浇口应尽可能设在空洞产生部位(较厚部分)的附近
设备上: · 检查螺杆及止回阀三件套是否磨损
(3-2) 减慢表面固化
(2-3) 材料未烘干
图3. 卷入空气
精品ppt
10
(3)气泡的对策
(3-1) 减少空气卷入
1.减少料筒内空气卷入: - 降低螺杆转速 - 提高背压 - 回吸量设定不要过多
2. 减少填充时模腔内空气卷入: - 降低注射速度 - 调整浇口位置, 大小和形状。 - 调整主流道脱模斜度
关键要通过填充试验, 把握住流动样式,然后在此基础上确立相应的对策。
精品ppt
11
4. 空洞
(1)什么是空洞(外观)
是指成型品内部产生空洞的一种现象。 空洞一般发生在产品壁厚最厚处!
空洞的原因大致分为两种:一种是大量气体的混入, 另一种则是厚壁处的的树脂收缩。前者称为“气体空 洞”,后者称为“真空空洞”,以示区别。
图1. 厚壁处出现的空洞
精品ppt
图2. 气体空洞与真空空洞的区别
精品ppt
塑胶件的种常见不良缺陷图片(ppt)
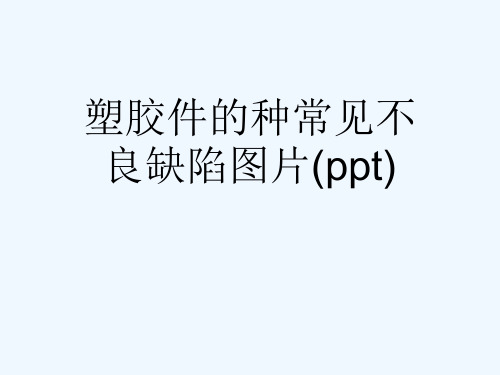
混色
混色(杂色料)
十、划伤(刮伤):
划伤
刮花
十一、烧焦:
烧焦
十二、拖花(拉伤):
拖花(拉伤)
十三、顶高(顶白):
顶高(顶针印)
十四、料花:
料花
十五、油污:
油污NG!
十六、碰伤:
碰伤
十七、削伤:
削缺(削伤)
十八、气泡:
气泡(透明件中央白泡状)
十九、色差(上下盖阴阳色):
上盖色偏哑
下盖色偏亮
二十、披锋丝(拉丝):
披锋丝(拉丝)NG
二十一、应力痕:
应力痕:因注射时内应力过大而在产品表面形成的光影;
二十二、进胶位发蓝:
进胶点发蓝
二十三、多胶:
多胶 NG
塑胶件的种常见不 良缺陷图片(ppt)
一、缩水:
缩水(凹痕)
缩水(凹痕)
二、气纹:
气纹
三、缺料(走胶不足):
走胶不足
缺料
四锋
毛边
六、夹线(结合线):
夹线 夹线(结合线)
七、黑点:
黑点NG!
八、变形:
平面中间拱起变形
柱子弯曲变形
九、混色(异色):
混色(杂色料)
十、划伤(刮伤):
划伤
刮花
十一、烧焦:
烧焦
十二、拖花(拉伤):
拖花(拉伤)
十三、顶高(顶白):
顶高(顶针印)
十四、料花:
料花
十五、油污:
油污NG!
十六、碰伤:
碰伤
十七、削伤:
削缺(削伤)
十八、气泡:
气泡(透明件中央白泡状)
十九、色差(上下盖阴阳色):
上盖色偏哑
下盖色偏亮
二十、披锋丝(拉丝):
披锋丝(拉丝)NG
二十一、应力痕:
应力痕:因注射时内应力过大而在产品表面形成的光影;
二十二、进胶位发蓝:
进胶点发蓝
二十三、多胶:
多胶 NG
塑胶件的种常见不 良缺陷图片(ppt)
一、缩水:
缩水(凹痕)
缩水(凹痕)
二、气纹:
气纹
三、缺料(走胶不足):
走胶不足
缺料
四锋
毛边
六、夹线(结合线):
夹线 夹线(结合线)
七、黑点:
黑点NG!
八、变形:
平面中间拱起变形
柱子弯曲变形
九、混色(异色):
注塑缺陷总结(含产品缺陷_模具缺陷)(PPT43页).pptx

原因: • 1、NC过切,EDM时积碳等等。 • 2、蚀纹保护不良。 • 3、模具胶位面碰伤。
飞边(披锋)(flash-plastic;burr-metal)
• 飞边:制品边缘、分型面位置、顶针司筒斜顶位置、碰穿
插穿位、镶拼边缘,因钢料配合有一定间隙而产生飞边。
原因: • 1、原料流动性佳。(PA,ABS+PMMA) • 2、模具配合不良,排气及装配间隙过大。 • 3、分型面有异物。 • 4、生产合模速度太快压力太大导致分型面压变形。 • 5、注塑压力过大,锁模力不够。 • 6、碰穿面撞塌,插穿面刮出毛刺。 • 7、合模机配模,推方不能锁死在B板,配模时推方被压回
铲胶
• 铲胶:出模过程中,顶出机构对塑件产生刮擦。
原因: • 1、斜顶高出胶位面,出模时铲胶(低0~0.10mm合适)。 • 2、斜面顶针无防滑,出模时产品偏移被铲伤。 • 3、斜顶或滑块粘模、抛光不良、行程不够等问题,导致
出模时产品向某一方向偏移,被顶出机构铲伤。
熔接线weld line
• 熔接线:来自不同方向的流体热熔接时不够紧密形成线状 的痕迹,常称“夹水纹”;熔体交汇都会出现熔接线,只是 明显与不明显的区别。
缺胶Short Shot
• 缺胶:未完全填充。 原因: • 1、原料流动性差。(HIPS阻燃料、加玻纤等) • 2、模具浇口少、小,胶位离浇口远。 • 3、排气不良,困气导致缺胶。 • 4、薄胶位,难填充。 • 5、注塑压力不够。 • 6、胶料加热温度不够。
多胶
• 多胶:胶位与图纸不符,有多余胶位。
产生(如牛角浇口镶件常出现凹痕)。 • 3、模具变形或组配问题,如注塑过程中顶针板变形、顶
针、顶块微量后退等(与原因2类似)。 • 4、保压压力太高、模温太低、料温太低。 • 5、模具局部过热(无冷却的大顶针、大顶块、大斜顶),
飞边(披锋)(flash-plastic;burr-metal)
• 飞边:制品边缘、分型面位置、顶针司筒斜顶位置、碰穿
插穿位、镶拼边缘,因钢料配合有一定间隙而产生飞边。
原因: • 1、原料流动性佳。(PA,ABS+PMMA) • 2、模具配合不良,排气及装配间隙过大。 • 3、分型面有异物。 • 4、生产合模速度太快压力太大导致分型面压变形。 • 5、注塑压力过大,锁模力不够。 • 6、碰穿面撞塌,插穿面刮出毛刺。 • 7、合模机配模,推方不能锁死在B板,配模时推方被压回
铲胶
• 铲胶:出模过程中,顶出机构对塑件产生刮擦。
原因: • 1、斜顶高出胶位面,出模时铲胶(低0~0.10mm合适)。 • 2、斜面顶针无防滑,出模时产品偏移被铲伤。 • 3、斜顶或滑块粘模、抛光不良、行程不够等问题,导致
出模时产品向某一方向偏移,被顶出机构铲伤。
熔接线weld line
• 熔接线:来自不同方向的流体热熔接时不够紧密形成线状 的痕迹,常称“夹水纹”;熔体交汇都会出现熔接线,只是 明显与不明显的区别。
缺胶Short Shot
• 缺胶:未完全填充。 原因: • 1、原料流动性差。(HIPS阻燃料、加玻纤等) • 2、模具浇口少、小,胶位离浇口远。 • 3、排气不良,困气导致缺胶。 • 4、薄胶位,难填充。 • 5、注塑压力不够。 • 6、胶料加热温度不够。
多胶
• 多胶:胶位与图纸不符,有多余胶位。
产生(如牛角浇口镶件常出现凹痕)。 • 3、模具变形或组配问题,如注塑过程中顶针板变形、顶
针、顶块微量后退等(与原因2类似)。 • 4、保压压力太高、模温太低、料温太低。 • 5、模具局部过热(无冷却的大顶针、大顶块、大斜顶),
塑胶模具成型常见不良原因分析及对策精选优秀ppt

成型常见不良缘由分析及对策
十 变形 A、 缘由: 残留应力的影响
对策: 1 运用多段速度切换;2 料管温度升高; 3 充填速度调慢; 4 模温升高;5 保压降低; 6 背压调高; 7 顶出速度降低; 8 充填速度调快〔压力缺乏情形〕9 延伸
冷却时间; B、 缘由:收缩率不同的影响
对策:1 冷却水量的调整;2 冷却水温度的调整; 3 冷却水路的检修
对策:1松退量减少;2松退 速度减小;
E 、缘由:锁模力缺乏,模具密合不够
对策:锁模力增大;
成型常见不良缘由分析及对策
D、 缘由:体积收缩
对 对策:锁模力增大; 策 : 1 添 加 背 压 ; 对策: 1 运用2多延段速伸度保切换压; 时间;
7 2
顶检出 查速螺3度杆降套增低筒高;的损模伤,具摩温耗,度腐蚀;等;
A3 、模缘温由降4:低计;降量低值缺料乏。管温度;
BC对、策缘缘:由由1:5:降二金低降次属形加压异低热切〕常筒换充磨温不耗度填良2 降速低度充填〔温度厚;肉制 品情
B2 、多缘段由射:出6金;添属异加常磨充耗填速度〔压力缺乏情形〕
成对型策常 :见1E降不、低良背缘缘压由;分由析及:对模策 具内空气排出不良
对策:降低充填速度;
成型常见不良缘由分析及对策
九 银线 A 缘由:熔塑时空气进入
对策:1添加背压;2 添加螺杆转数;3 添加充填压力;4 添加料 管后段温度; B 缘由:松退量过多 对策:1 松退量减少;2 松退速度降低; C 缘由:瓦斯空气卷入 对策:1 充填速度降低;2 模具温度升高; D 缘由:料管内部发热异常 对策:1 降低背压;2 降低螺杆转数;
成型常见不良缘由分析
十一 烧焦 A、缘由:树脂、添加剂分解之影响 对策: 1 降低加热筒温度2 降低充填温度;3 降低充填压力; 4 降低背压; 5 升高模温; 6 充分做好树脂换色; B、缘由:金属异常磨耗 对策:1 检查螺杆,加热筒的损伤,摩耗,腐蚀等; 2 检查螺杆套筒的损伤,摩耗,腐蚀等; C、 缘由:空气断热紧缩 对策:气缸内: 1 添加背压; 2 降低螺杆转数; 3 添加计量后树脂滞留时间; 模具内: 1降低充填速度;2 采用多段射出;
常见塑胶产品缺陷讲义(PPT 28页)_2028

图2. 喷射时的填充状况(采用充填不足法)
2021/3/1
14
波纹 (皱纹)
(1)何谓 波纹(外观)?
波纹是指成型品表面出现皱纹状痕迹。 通常发生在注射速度慢、表层固化Байду номын сангаас于树脂填充的场合。
2021/3/1
图1. 手柄试 验型表面上 出现的波纹
图2. 手柄试验 型表面上出现 的波纹(2)
15
充填不足 (缺胶)
玻纤析出
❖ 玻纤析出的起因与“光泽不好”相同。 详情请参阅光泽不好页。
图1. □120平板表面上出现的玻纤析出(例1)
2021/3/1
11
图2. □120平板表面上出现的玻纤析出(例2)
光泽不好
❖ (1)何谓光泽不好?(外观)
光泽不好是指成型品未粘着在模具上,即复制不良。
图1. 外观评价用的试样表面上出现的光泽不好(凹痕) (*试样大小约为20cm/材料为Duracon M90)
图1. 在外观评价 用的试样上出现 的滑痕 (* 图片中的针 孔大小约为2mm)
2021/3/1
图2. □120 平板浇口附 近的滑痕
19
飞边 (披锋)
❖ (1)何谓飞边(外观)?
虽然制作模具时精度很高(μm级),而且成型时采用高压合模,但由于树 脂的填充压力也很高,所以实际上留有很小的缝隙。飞边就是因树脂进入这 种缝隙而形成的。在PL面、套管、滑芯界面和排气口等处都会出现飞边。
F2021/3/1 图2. □120平板表面上出现的光泽不好(玻纤析出)(材料为Fortron 1140A1)
12
喷射纹
❖ (1)何谓喷射纹?(外观) 通常,溶融的树脂是以喷流的形式来流动的。不过,当 从狭窄处流到宽阔处时,如果流速偏快,有时就会呈带状 飞出,并且在不接触模具的情况下流动。这被称为喷射 纹。根据喷射纹在成品表面的表现方式,有的呈带状, 有的则呈雾状,但它们的原因都是一样的。
- 1、下载文档前请自行甄别文档内容的完整性,平台不提供额外的编辑、内容补充、找答案等附加服务。
- 2、"仅部分预览"的文档,不可在线预览部分如存在完整性等问题,可反馈申请退款(可完整预览的文档不适用该条件!)。
- 3、如文档侵犯您的权益,请联系客服反馈,我们会尽快为您处理(人工客服工作时间:9:00-18:30)。
张力
高配向
低配向
高配向
Shear rate - min
max
分子配向是由塑胶的剪切流动引起,凝固层存在最高的剪切率,故此区域的分
子配向也是最高的。中心区域的剪切率较低,中间区域的分子配向也较低。
创世界品牌 建百年金发
流动截面/热交换
Hot Plastic Melt
Plastic Flow Heat
创世界品牌 建百年金发
14
流痕的原因分析
• 流痕:是指在浇口附近呈波浪状的表面缺陷。
若波浪特别明显,就成了震纹,这种波浪就不仅仅 是视觉所见的痕迹,而是可以触摸到的台阶状的凹 槽。震纹产生原因是熔体粘度过大而以滞流形式充 模时,前端的料一接触到型腔表面便很快冷凝收缩 起来,而后来的熔料又胀开已收缩的冷料继续前进 过程的不断交替使料流在前进中形成了表面震纹。
解决滞流欠注问题的措施: 1.增加滞流部位厚度,制件厚度差异 不要太大,缺点是容易引起缩痕; 2.改变浇口位置为充填的末端,使该 位置形成压力; 3.注塑时首先降低速度和压力,使充 填初期就在料流前锋形成较厚的固化 层,认为增加熔体压力,这一方法是 我们常用的措施; 4.采用流动性好的材料。
创世界品牌 建百年金发
Input
High Shear
Rate
Cold Mold
Heat Loss into the Tool
Frozen Layer
较慢的注射速率
对比
较快的注射速率
由剪切流动产生的热输入和进入模具的热损失之间应当是平衡的。
创世界品牌 建百年金发
欠注的原因分析(1)
• 欠注:是指模具型腔不能被完全填充 满的一种现象。是我们成型时首先要 避免的问题。
12
应用中的欠注现象
创世界品牌 建百年金发
13
溢料(飞边) 的原因分析
• 溢料:又称飞边、溢边、披锋等,大多发生在 模具的分合位置上,有时在顶杆和镶块等位置 也有。
模具 设计
注 塑 机
成型 工艺
材料
▪合理设计模具,利于模具合模紧闭,不产生缝隙 ▪保障模具能够紧固在模板上,确保成型时不损伤模具 ▪检查排气口的尺寸,不超过材料的溢边值 ▪清洁模具表面 ▪打磨使模具产生合模不严的表面,使模具封闭较好
制件设计
▪制件壁厚设计太薄 ▪制件存在导致滞流现象的加强筋
▪制件的厚度存在较大差异,引起滞流在局部出现,无法 通过模具设计来避免
创世界品牌 建百年金发
10
欠注的原因分析(3)
• 迟滞效应:也叫滞流,如果在距离浇口比较近的位置,或者在垂直于流动方 向的位置有一个比较薄的结构,通常为加强筋等,那么在注塑过程中,熔体 经过该位置时将会遇到比较大的前进阻力,而在其主体的流动方向上由于流 动畅通,无法形成流动压力,只有当熔体在主体方向充填完成,或进入保压 时才会形成足够的压力对滞流部位进行充填,而此时,由于该位置很薄,且 熔体不流动没有热量补充,已经固化VC合金非常容易出现这种现象。
Filling Phase Pressurization Phase Compensation Phase
• Filling,计量的充填模穴 • Pressurization,建立模穴压力 • Compensation,挤入额外的塑料以减少收缩 (冷
却过程中发生的收缩)
创世界品牌 建百年金发
4
塑料的喷泉流动
• 描述塑胶分子在模具中的流动形态 ;与塑胶的流变性能及其长分 子链有关;
• 出现的结果为,最先进入模具型腔的塑胶会因凝固而停留在浇口 附近的区域
• 会直接影响到表面的分子形态和纤维配向。
创世界品牌 建百年金发
5
塑料的剪切流动
(1) 剪切流动(Shear Flow)
固定
移动
固定
固定
(2) 剪切率(Shear Rate)
内容提要
塑料的成型加工方法 注塑机以及成型参数简介 制品设计 注塑模具结构及其设计 注塑成型及其缺陷原因分析 Moldflow简介及分析流程 技术支持与客户服务
创世界品牌 建百年金发
1
注塑成型的过程
创世界品牌 建百年金发
2
成型的周期时间
创世界品牌 建百年金发
3
塑料的充填
创世界品牌 建百年金发
9
欠注的原因分析(2)
注塑机 工艺条件
▪检查止逆阀和料筒内壁是否磨损严重,上述磨损会导致 注塑压力和注塑量损失严重 ▪检查加料口是否有料或是否架桥 ▪检查注塑机的能力是否能达到成型要求的能力
▪增大注塑压力 ▪增大注塑速度,增强剪切热 ▪增大注塑量 ▪增大料筒温度和模具温度 ▪增大注塑机的熔胶长度 ▪减小注塑机的缓冲量 ▪延长注射时间 ▪合理调整注射各段的位置和对于的速度、压力
材料
模具 设计
▪增加熔体的流动性 ▪减少再生料的添加 ▪减少原材料中的气体分解
▪浇口的位置设计保证其先填充厚壁,避 免出现滞留现象,导致聚合物熔体过早硬 化。 ▪增加浇口数量,减少流程比。 ▪增加流道尺寸,减少流动阻力 ▪排气口的位置设置适当,避免出现排气 不良的现象(看欠注部位是否烧焦) ▪增加排气口的数量和尺寸 ▪增加冷料井设计,排出冷料 ▪冷却水道的分布要合理,避免造成模具 局部温度偏低
▪设置适当锁模力 ▪保证注塑机的两块安装模板相互平行 ▪注塑机的锁模力不足所至,选择大锁模力的注塑机 ▪模具本身平行度不佳,或装得不平行
▪降低注塑速度 ▪降低料筒温度和喷嘴温度 ▪降低注塑压力和保压压力 ▪减少缓冲长度,使熔体不要在料筒中过填充 ▪降低模具温度
▪提高材料的冷却速度 ▪塑料黏度太高或太低都可能出现飞边 ▪原材料颗粒不均时,导致加料量不稳定,产生飞边 ▪吸水强的材料,或对水分敏感的材料,会因干燥不充分 大幅降低材料流动性,增加材料黏度,导致飞边产生
慢速移动
快速移动
低剪切速率
高剪切速率
固定
固定
(3) 剪切应力(Shear Stress)
慢速移动
快速移动
低剪切应力 固定
高剪切应力 固定
剪切流动是熔融流体在外力下的 相对滑动。
剪切率是熔融流体剪切流动的速率。
剪切应力是熔融流体剪切流动的抵 抗力,高粘度造成高剪切应力。
创世界品牌 建百年金发
6
流动截面/分子配向
创世界品牌 建百年金发
11
滞流现象导致的欠注
上面的制件采用PVC/ABS, 下面的采用了PC/ABS,红色 箭头为浇口位置,黄色箭头和 圆圈为滞流导致欠注部位,绿 色箭头为推荐的浇口位置。材 料流动性越差,滞流越明显。 流动性好的尼龙等材料几乎不 存在滞流问题,即使加玻纤的 尼龙也很少有滞流现象。