模具维修常见问题及解决办法
模具常见问题及解决方法

本次培训到此结束,谢谢!
8、产品不容易脱出ห้องสมุดไป่ตู้
通常在对部品进行排料时就应考虑部品的出料问题。一般情况下,我们采用以下几 种出料方式: ⑴:风吹出; 对于一些较小的产品,利用吹气销将其吹出。 ⑵:在重心作用下,产品自然滑落; 在下模铣一出料缺口,利用部品的自身重力滑落。 ⑶:零件推零件; 借助条料的传送力,将冲压完成后的部品推出模具。此时应注意模具的升料高度。 ⑷:零件由条料带出; 此方式一般运用在模具在最后工步对部品的外形进行整体落料的情况下采用,通过大力 弹簧将部品重新压入到条料中,在条料送出的同时将部品一同带出。 ⑸:零件整体落料; 在考虑运用此方式之前必须确认部品的毛刺方向是否允许? 为了避免部品粘附在卸料板或凹模板表面,通常会在最后工位的卸料板或凹模板上使用 小顶杆。
80
t
5° ~10°
°~
85
°
第 一 次 弯 曲
第 二 次 弯 曲
R
回弹抵消
回弹抵消
二次弯曲加工
7、模具容易磨损
影响因素:⑴:模具材料的选用; ⑵:模具润滑不够; ⑶:模具材质热处理不良; ⑷:模具间隙太小; 解决对策:⑴:选用合理优质的模具材料; ⑵:合理的润滑; ⑶:模具材料施以表面处理;(如镀钛) ⑷:选择合理的间隙;
5、冲头容易断裂
影响因素:⑴:由于模具间隙不均匀,冲头受到横向负荷而折断; ⑵:模具间隙小使冲头在脱料时受到横向负荷而折断; ⑶:冲头因导引不良使得冲头在冲切时有偏移现象; ⑷:冲头刃部长度过长; ⑸:冲头阶段部发生应力集中; ⑹:冲头所选用的材料; ⑺:冲屑堵塞造成冲头负荷增大; ⑻:卸料板因受到侧压而倾斜; 解决对策: ⑴:模具间隙要均匀; ⑵:模具间隙取大; ⑶:正确的冲头导引; ⑷:冲头刃部长度减短; ⑸:冲头阶段部施以R角; ⑹:使用高韧性的冲头材料; ⑺:凹模直段部取短及下模有确实的逃孔设计; ⑻:防止卸料板发生倾斜;
模具维修知识点总结

模具维修知识点总结模具是各种工业产品生产所不可或缺的工具,它的质量和维修状况直接关系到产品的质量和生产效率。
因此,了解模具维修知识点对于企业来说是非常重要的。
本文将从模具的损坏原因、维修方法以及预防措施三个方面进行总结。
一、模具的损坏原因模具的损坏原因多种多样,主要包括以下几个方面:1. 使用不当:使用模具时不遵守正确的操作规程,例如超负荷使用、粗暴操作等,会导致模具的磨损和断裂。
2. 材料质量问题:模具的材料质量直接决定了它的使用寿命。
选择质量差的材料或者生产过程中出现问题,都会影响模具的稳定性和耐用性。
3. 加工工艺问题:模具在设计和加工过程中存在瑕疵,导致模具强度不足或者结构设计不合理,容易出现损坏。
4. 环境因素:模具长期暴露在恶劣的环境中,如高温、潮湿等,会引起模具腐蚀、锈蚀等现象,加速模具的损坏。
二、模具的维修方法1. 报废修复:对于严重磨损或损坏的模具,需要进行报废修复。
根据具体情况,可以选择焊接、切割等方式对模具进行修复,使其重新恢复使用功能。
2. 表面处理:模具表面经常会因为摩擦和磨损而受损。
通过表面处理,可以提高模具的硬度和耐磨性,延长模具的使用寿命。
常见的表面处理方法包括镀铬、喷涂等。
3. 维护保养:定期对模具进行维护保养是防止模具损坏的重要方法。
包括定期清洁模具、润滑模具、检查模具状况等,及时发现并解决潜在问题,延长模具的使用寿命。
三、模具的预防措施1. 加强员工培训:提高员工的模具维修技能和操作水平,加强对模具使用规程的培训和宣传,提高员工使用模具的规范性,减少人为因素导致的模具损坏。
2. 合理设计模具结构:在模具设计过程中注重结构的合理性和强度的保证。
避免模具存在隐患,减少模具故障的发生。
3. 定期检查模具:定期对模具进行检查、维护和保养,发现潜在问题及时解决,避免因为模具小故障引起大问题。
4. 控制使用环境:保证模具的使用环境符合要求,避免模具暴露在恶劣的条件下,如温度过高、潮湿等。
模具常见问题分析及其解决方法

模具常见问题分析及其解决方法概述模具是工业生产中常用的一种工具,它在各个行业中被广泛应用。
然而,随着使用时间的增加,模具也会出现各种问题。
本文将详细分析模具常见问题,并提供相应的解决方法,以帮助读者更好地应对模具问题。
问题一:模具磨损严重模具磨损是使用寿命过程中常见的问题之一。
其主要表现为模具表面磨损或凹陷。
磨损的原因可能是: - 使用材料硬度较高 - 使用时间较长 - 模具润滑不足 - 模具设计不合理解决方法: - 使用耐磨性能更好的模具材料,如优质钢材 - 定期进行模具保养和维护,及时更换磨损严重的部件 - 在使用过程中保持适当的模具润滑,减少磨损 - 对模具进行优化设计,减少出现磨损的可能性问题二:模具尺寸偏差大模具尺寸偏差大是另一个常见问题。
这可能导致生产出的产品尺寸不准确,影响产品质量。
尺寸偏差大的原因包括: - 模具制造过程中的测量误差 - 模具材料膨胀或收缩不均匀 - 模具结构设计不合理解决方法: - 提高模具制造过程中的测量精度,并进行多次验证 - 选择合适的模具材料,控制材料膨胀或收缩的影响 - 对模具结构进行优化设计,避免尺寸偏差的产生问题三:模具易生锈模具易生锈是模具在使用过程中常见的问题之一。
模具生锈不仅影响外观,还可能导致模具损坏。
模具易生锈的原因可能是: - 环境湿度较高 - 模具存放不当 - 模具润滑不足解决方法: - 控制使用环境湿度,尽量保持干燥 - 对模具进行正确的存放,避免受潮或受酸碱腐蚀 - 在使用过程中,保持模具的适度润滑,防止生锈问题四:模具易断裂模具易断裂是一种严重的问题,可能导致模具报废,造成生产线停机。
模具易断裂的原因包括: - 模具结构设计不合理 - 模具材料不合格或强度低 - 模具使用过程中发生过载解决方法: - 对模具结构进行优化设计,提高其受力性能 - 选择合适的模具材料,确保其强度和韧性满足要求 - 在使用过程中,避免过载操作,及时发现并处理异常情况问题五:模具易堵塞模具易堵塞是模具在使用过程中常见的问题,特别是对于塑料注塑模具。
模具失效及解决方法实例

模具失效及解决方法实例一、引言模具是工业生产中必不可少的工具,它能够成型出各种形状和尺寸的产品。
然而,模具在使用过程中会受到各种因素的影响,导致失效。
模具失效不仅会影响生产效率,增加生产成本,还会影响产品的质量。
因此,了解模具失效的原因和解决方法非常重要。
本文将介绍模具失效的类型、原因以及一些常见的解决方法实例。
二、模具失效类型1. 磨损:模具在使用过程中,其工作表面会与材料不断接触,导致工作表面磨损。
2. 腐蚀:模具受到化学或电化学作用,导致腐蚀损坏。
3. 塑性变形:材料在模具内塑性变形,导致模具变形。
4. 热疲劳:模具在工作过程中频繁冷热交替,导致热疲劳损坏。
5. 裂纹扩展:由于制造、使用过程中产生的裂纹在交变应力作用下扩展导致破坏。
三、模具失效原因1. 操作不当:如超负荷生产、材料硬度过高、材料中有杂质等都会导致模具过早磨损或腐蚀。
2. 维护不当:润滑不足、冷却系统不良等都会导致模具过热或腐蚀。
3. 材料问题:模具材料的选择不当,如硬度、耐腐蚀性、耐磨性等都会影响模具的使用寿命。
4. 制造问题:制造过程中的缺陷,如铸造缺陷、热处理不当等都会导致模具产生裂纹或塑性变形。
四、解决方法实例1. 磨损修复:对于磨损的模具,可以采用堆焊、喷涂等方法进行修复。
例如,对于磨损的凸轮表面,可以采用堆焊的方式进行修复,选择耐磨性好、焊前流动性好的合金堆焊焊条。
在修复过程中,需要注意控制热输入,避免热影响扩大。
同时,对于一些磨损严重的模具,还可以采用喷涂的方法进行修复,选择耐磨性好、耐腐蚀的涂层材料,如金属陶瓷、镍基涂层等。
2. 腐蚀防护:对于腐蚀的模具,可以采用镀层、表面处理等方法进行防护。
例如,对于受腐蚀的模具钢表面,可以采用镀铬或镀锌等防腐方法进行防护。
此外,还可以采用表面处理的方法提高模具表面的抗腐蚀性能,如采用氧化处理、磷化处理等。
3. 温度控制:对于塑性变形的模具,可以通过调整生产工艺、选择合适的材料等方法来降低模具工作时的温度。
模具常见故障及维修保养-20171103
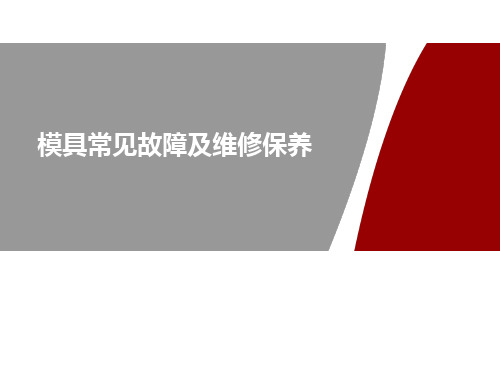
四.常见模具故障及维修方法
10.送料不顺 原因分析: 送料不到位 弹簧力过大 步距分布不合理 挡料块间隙不当 避位不够 刀口毛边过大 压线设计不合理 浮升高度不够 料带变形 维修改善对策: 检查调整送料装置 适量调整弹簧 与设计沟通考虑布局方案 适当研磨挡料块以现场调试为准 研磨或铣削避位不够的地方 检查上下模(冲子)研磨冲子
四.常见模具故障及维修方法
模具常见问题点 1.废料跳屑 2.废料堵塞 3.毛刺 4.切边不齐 5.铁屑压伤 6.抽牙不良 7.折弯尺寸角度不良 8.不脱料 9.成型不良 10.送料不顺
四.常见模具故障及维修方法
1.废料跳屑 原因分析: 冲头过短 凸凹模间隙过大 冲头或模板磁性过大 维修改善对策: 冲头加长 将冲头研磨斜度或弧度 冲头上装顶料销 冲头前端点焊 调整凸凹模间隙, 冲头和或模板退磁
四.常见模具故障及维修方法
4.切边不齐 原因分析: 定位不准,和各工站定位基准不一致,并互相干涉 单边折弯和成型拉料,产生前工站和后工站切边不齐 设计错误造成接口断差和接刀处工艺切口选择不合理 送料不准,步距计算有误 维修改善对策: 调整定位,让各工站定位基准一致 加大弹簧,增加压料力,有条件尽可能考虑双边成型和其它切 折单边折弯成型均匀和平衡 重加工修正接刀处工艺切口 调整送料机,重新计算步距
四.常见模具故障及维修方法
6.抽芽不良 原因分析: 抽芽孔中心与抽芽冲子中心不重合,造成抽芽一边高 一边低甚至破裂 凹模间隙不合理,抽芽一边高一边低甚至破裂 抽芽冲子表面没抛光,造成抽芽单边断裂 抽芽冲子过长,脱料力过大表面拉裂 铝材脱料板间隙过大,形成两边抽芽 维修改善对策: 确定正确中心位置,移动冲子或调整定位 修配抽芽间隙 抛光抽芽冲子 确认抽芽冲子长度,适量减少脱料力 调整脱料板与抽芽冲子的大小间隙,一般采用 C+0.01mm
模具维修常见问题的解决方法
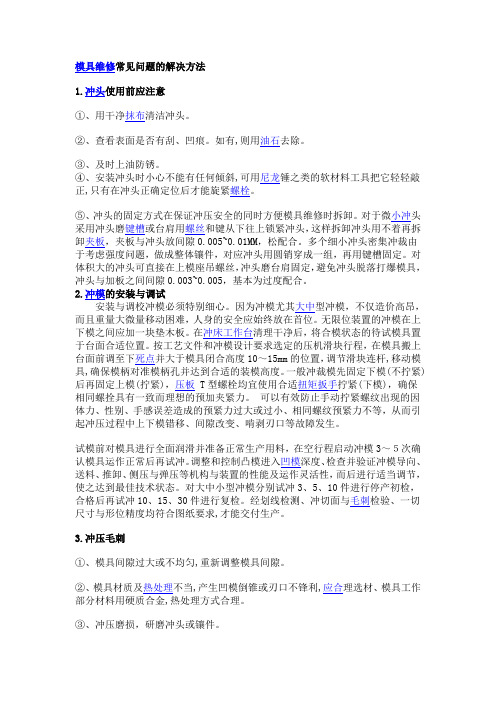
模具维修常见问题的解决方法1.冲头使用前应注意①、用干净抹布清洁冲头。
②、查看表面是否有刮、凹痕。
如有,则用油石去除。
③、及时上油防锈。
④、安装冲头时小心不能有任何倾斜,可用尼龙锤之类的软材料工具把它轻轻敲正,只有在冲头正确定位后才能旋紧螺栓。
⑤、冲头的固定方式在保证冲压安全的同时方便模具维修时拆卸。
对于微小冲头采用冲头磨键槽或台肩用螺丝和键从下往上锁紧冲头,这样拆卸冲头用不着再拆卸夹板,夹板与冲头放间隙0.005~0.01MM,松配合。
多个细小冲头密集冲裁由于考虑强度问题,做成整体镶件,对应冲头用圆销穿成一组,再用键槽固定。
对体积大的冲头可直接在上模座吊螺丝,冲头磨台肩固定,避免冲头脱落打爆模具,冲头与加板之间间隙0.003~0.005,基本为过度配合。
2.冲模的安装与调试安装与调校冲模必须特别细心。
因为冲模尤其大中型冲模,不仅造价高昂,而且重量大微量移动困难,人身的安全应始终放在首位。
无限位装置的冲模在上下模之间应加一块垫木板。
在冲床工作台清理干净后,将合模状态的待试模具置于台面合适位置。
按工艺文件和冲模设计要求选定的压机滑块行程,在模具搬上台面前调至下死点并大于模具闭合高度10~15mm的位置,调节滑块连杆,移动模具,确保模柄对准模柄孔并达到合适的装模高度。
一般冲裁模先固定下模(不拧紧)后再固定上模(拧紧),压板 T型螺栓均宜使用合适扭矩扳手拧紧(下模),确保相同螺拴具有一致而理想的预加夹紧力。
可以有效防止手动拧紧螺纹出现的因体力、性别、手感误差造成的预紧力过大或过小、相同螺纹预紧力不等,从而引起冲压过程中上下模错移、间隙改变、啃剥刃口等故障发生。
试模前对模具进行全面润滑并准备正常生产用料,在空行程启动冲模3~5次确认模具运作正常后再试冲。
调整和控制凸模进入凹模深度、检查并验证冲模导向、送料、推卸、侧压与弹压等机构与装置的性能及运作灵活性,而后进行适当调节,使之达到最佳技术状态。
对大中小型冲模分别试冲3、5、10件进行停产初检,合格后再试冲10、15、30件进行复检。
模具设计中的故障分析与维修措施推荐
模具设计中的故障分析与维修措施推荐在制造业中,模具设计是一个重要的环节。
模具的质量和性能直接影响着产品的质量和生产效率。
然而,模具在使用过程中难免会出现故障,给生产带来一定的困扰。
因此,对模具设计中的故障进行分析,并提出相应的维修措施是十分必要的。
一、故障分析1. 模具磨损模具在使用过程中,由于长时间的摩擦和冲击,会导致模具表面的磨损。
磨损严重会导致模具尺寸偏差增大,甚至无法继续使用。
常见的磨损形式有磨损、疲劳破坏等。
2. 模具变形模具在使用过程中,由于受到外力的作用或温度变化等因素,会发生一定程度的变形。
模具变形会导致产品尺寸不准确,甚至无法使用。
常见的变形形式有弯曲、扭曲等。
3. 模具裂纹模具在使用过程中,由于受到冲击或应力集中等原因,会出现裂纹。
裂纹的出现会导致模具寿命减少,甚至造成模具损坏。
常见的裂纹形式有疲劳裂纹、应力腐蚀裂纹等。
二、维修措施推荐1. 模具磨损的维修对于磨损严重的模具,可以采取修复或更换零部件的方式进行维修。
修复可以通过表面处理、热处理等方式进行,以恢复模具的原始尺寸和性能。
如果磨损过于严重,无法修复,就需要更换零部件。
2. 模具变形的维修对于模具的变形问题,可以通过热处理或机械加工等方式进行维修。
热处理可以通过加热和冷却等方式,使模具恢复原始形状。
机械加工可以通过切削、磨削等方式,修复模具的尺寸和形状。
3. 模具裂纹的维修对于模具的裂纹问题,可以采取焊接、热处理等方式进行维修。
焊接可以通过填充和熔化等方式,修复模具的裂纹。
热处理可以通过加热和冷却等方式,消除模具的应力,防止裂纹扩展。
维修措施的选择要根据具体情况进行。
在进行维修之前,需要对模具的故障原因进行分析,确定维修的方式和方法。
同时,维修过程中需要注意保护模具的表面,避免二次损坏。
除了维修措施,预防措施也是非常重要的。
在模具设计和使用过程中,应注意以下几点:1. 合理设计模具结构,减少应力集中和磨损。
2. 选择适当的材料,提高模具的耐磨性和耐腐蚀性。
塑料模具维修手册
塑料模具维修手册第一章:引言塑料模具是在工业生产中广泛应用的一种工具,用于制造各种塑料制品。
然而,模具在长期使用过程中难免会出现损坏、磨损等问题,因此需要进行维修。
本手册将为您提供塑料模具维修的详细步骤和技巧,帮助您解决常见的模具问题。
第二章:常见模具问题及解决方法2.1 模具表面损伤修复2.1.1 表面划痕修复表面划痕是模具常见的问题之一,影响产品表面质量。
修复方法:首先清洁受损区域,然后使用细砂纸轻轻擦拭,最后使用抛光剂进行修复,直到划痕消失。
2.1.2 磨损修复模具在使用过程中,由于摩擦和挤压等原因,可能会出现磨损现象。
修复方法:使用磨削工具将磨损部分处理平整,然后进行抛光,最后进行防锈处理,以免再次产生磨损。
2.2 模具变形问题修复2.2.1 热胀冷缩引起的变形在高温环境下使用的模具,由于热胀冷缩,可能会出现变形问题。
修复方法:使用专业的冷却工具对受损部分进行冷却,恢复到原始状态。
2.2.2 加工误差引起的变形模具在加工过程中可能会出现误差,导致变形问题。
修复方法:使用校正工具对模具进行调整,确保模具尺寸和几何形状符合要求。
第三章:模具保养与维护3.1 模具清洁模具在使用过程中会积累塑料残留物和油脂等污垢,需要进行定期清洁。
清洁方法:使用专业的清洁剂喷洒在模具表面,然后用软毛刷进行擦拭,最后用干净的布擦拭干净。
3.2 模具润滑模具的润滑工作对保证模具的正常运行至关重要。
使用适量的润滑油喷洒在模具表面和滑动部位,确保模具零件间的摩擦最小化。
3.3 模具存放与保管当模具不使用时,需要妥善存放和保管,以防止损坏和变形。
模具应存放在干燥、通风的地方,避免附近有腐蚀性气体。
同时,模具应进行防锈处理,以延长使用寿命。
第四章:安全注意事项4.1 模具维修安全模具维修时需要严格遵守操作规程,佩戴个人防护设备,避免发生意外事故。
在使用磨削工具时,要保持专注,防止伤及手部。
4.2 模具保养安全模具保养时要注意工作区域的整洁,防止跌倒和滑倒。
模具加工异常改善措施
模具加工过程中出现异常可能会导致产品质量问题和生产效率低下。
下面是一些常见的模具加工异常和相应的改善措施:
1. 模具磨损:模具磨损可能导致尺寸偏差和表面粗糙度增加。
- 改善措施:定期对模具进行维护和修复,涂抹合适的模具保养剂以延长模具寿命。
2. 模具变形:高温和高压会导致模具变形,影响产品精度和质量。
- 改善措施:优化模具材料和结构设计,确保模具具有足够的刚性和抗变形能力。
控制加工过程中的温度和压力,避免过度负荷。
3. 模具冷却不均匀:不均匀的冷却可能导致产品尺寸不稳定和内部应力集中。
- 改善措施:设计合理的冷却系统,确保冷却介质均匀覆盖整个模具,避免冷却死角。
根据模具加工过程中的温度分布情况,调整冷却介质的流量和温度。
4. 模具表面粗糙度不符合要求:模具表面粗糙度不符合要求可能影响产品的外观和性能。
- 改善措施:选择合适的加工方法和刀具,确保切削速度和进给速度适当。
精细调整切削参数,如切削深度和刀具进给量,以达到所需的表面粗糙度。
5. 模具出现断裂或裂纹:模具的疲劳和过载可能导致模具断裂或产生裂纹。
- 改善措施:合理设计和优化模具结构,确保模具具有足够的强度和刚性,减少应力集中。
控制加工过程中的负荷和温度,避免过载。
除了以上措施外,还应建立质量控制体系,包括定期检查和保养模具,记录模具使用情况和维护历史,及时处理和纠正异常情况。
定期培训和提升加工人员的技能和意识,以提高模具加工质量和效率。
请注意,具体的改善措施应根据具体情况和问题进行评估和实施。
17个模具典型问题及解决方案,每一个都很经典
17个模具典型问题及解决方案,每一个都很经典1.废料跳穴a.冲头长度不够按冲头刃口切入凹模一个料厚加1mm更换冲头b.凹模间隙过大割入子减少间隙或用披覆机减小间隙c.冲头或模板未去磁将冲头或模板用去磁器去磁2.废料堵穴a.落料孔小或落料孔偏位加大落料孔,使落料顺畅b.落料孔有倒角加大落料孔去除倒角c.刀口未放锥度线割锥度或反面扩充孔减小直壁位长度d.刀口直壁位过长反面钻孔,使刀口直壁位缩短e.刃口崩,造成披锋大,堵料重新研磨刃口3.披锋不良a.刃口崩,造成披锋过大重新研磨刃口b.冲头与凹模间隙过大线割入块,重新配间隙c.凹模刀口光洁度差抛光刀口直壁位d.冲头与凹模间隙过小重新省模,配间隙e.顶料力过大,反向拉出披锋换弹簧,减小顶料力4.切边不齐a.定位偏移调整定位b.有单边成型,拉料加大压料力,调整定位c.设计错误,造成接刀不平重新线割切边刀口镶块d.送料不准调整送料器e.送料步距计算有误重新计算步距,重定接刀位5.冲头易断a.闭合高度过低,冲头切入刀口部位过长调整闭合高度b.材料定位不当,造成冲孔冲头切单边,调整定位或送料装置因受力不均断裂c.下模废料堵死刀口,造成冲头断重新钻大落料孔,使落料顺畅d.冲头的固定部位(夹板)与导向部位修配或重新线割入块使冲头上下顺畅(打板)偏移e.打板导向不良,造成冲头单边受力重新修配打板间隙f.冲头刀口太短,与打板干涉重换冲头,增长刀口部分长度g.冲头固定不好,上下窜动重新固定冲头使之不能上下窜动h.冲头刃口不锋利重新研磨刃口I.冲头表面拉伤,脱料时受力不均重新换冲头j.冲头过细,过长,强度不够重新换冲头类型k.冲头硬度过高,冲头材质不对更换冲头材质,调整热处理硬度6.铁屑a.压筋错位重新计算压筋位置或折弯位置b.折弯间隙过小,挤出铁屑重新调整间隙,或研磨成型块,或研磨成型冲头c.折弯凸模太锋利修R角d.接刀口材料太少重新接刀口e.压筋太窄重新研磨压筋7.抽芽不良a.抽芽底孔中心与抽芽冲子中心不重合造确定正确中心位置,或移动抽芽冲子位置,或移成抽芽-边高-边低甚至破裂动预冲孔位置,或调整定位b.凹模间隙不均匀,造成抽芽-边高-边修配抽芽间隙低甚至破裂c.抽芽底孔不符合要求,造成抽芽高度及重新计算底孔孔径,预冲孔增大或减少直径偏差,甚至破裂8.成型不良a.成型模凸模太锋利,造成材料拉裂成型凸模修R角,刀口处适当修R角b.成型冲头长度不够,造成未能成型计算冲头正确长度调整冲头实际长度以达成型要求c.成型冲头过长,成型处材料压变形,甚确定冲头正确长度,调整冲头实际长度以达到要求至冲头断裂d.成型处材料不够造成拉裂计算展开材料,或修R角,或降低成型高度e.定位不良,造成成型不良调整定位或送料装置f.成型间隙太小造成拉裂或变形调配间隙9.折弯尺寸a.模具没调到位造成角度误差导致尺寸偏调整闭合高度不良或角度差不良b.弹力不够造成角度不良导致尺寸偏差换弹簧c.材质不符合要求造成角度不良导致尺寸换材料或重新调整间隙偏差d.材料厚度偏差引起角度不良导致尺寸偏确定料厚,换材料或重新调整间隙差e.定位不当导致尺寸偏差调整定位使尺寸OKf.设计或加工错误造成折弯公拼块间有间補焊研磨,消除拼块间的间隙,导致折弯尺寸小值得关注的“模具人杂志微信~g.成型公无R角,在角度及其他正常情况成型公修R角下折弯高度偏小h.两边折弯尺寸偏大加压筋I.单边折弯拉料造成尺寸不稳定加大弹簧力,调整定位j.间隙不合理,引起角度不良和尺寸偏差修配间隙k.折刀高度不够,折弯冲头合入折刀太短增加折刀高度,使折弯冲头尽可能合入折刀部队位造成角度不良多一些l.折弯时速度太快,造成折弯根部变形调整速比控,选择合理转速m.结构不合理,折刀未镶入固定模板,重新铣槽,将折刀镶入模板冲压时,造成间隙变大n.成型公热处理硬度不够,造成压线崩或重制成型公压线打平10.不卸料a.定位不当或送料不当调整定位或送料装置b.避位不够修磨避位c.内导柱拉伤,造成打板活动不畅更换内导柱d.冲头拉伤或表面不光滑更换冲头e.顶料销摆布不合理重新摆布顶料销位置f.顶料力不够,或脱料力不够更换顶料弹簧或脱料弹簧g.冲头与夹板打板配合不顺畅修配打板和夹板使冲头配合顺畅h.成型滑块配合不畅修整滑块与导向槽使之配合顺畅I.打板热处理不适,冲压一段时间后变形重新研磨打板,矫正变形j.冲头过长或顶料销长度不够增加顶料销长度或换用长度合适之冲头k.冲头断更换冲头l.模板未云磁,工件往上带给模板去磁11.送料不顺a.模具没架正,导致料带与送料器及模具重架模具或调整送料器不在同一条直线上b.料带不平调整校平机或更换材料c.不卸料造成送料不顺参照不卸料解决对策。
- 1、下载文档前请自行甄别文档内容的完整性,平台不提供额外的编辑、内容补充、找答案等附加服务。
- 2、"仅部分预览"的文档,不可在线预览部分如存在完整性等问题,可反馈申请退款(可完整预览的文档不适用该条件!)。
- 3、如文档侵犯您的权益,请联系客服反馈,我们会尽快为您处理(人工客服工作时间:9:00-18:30)。
冲压模具维修常见问题的解决方法
内容介绍>>
1.冲头使用前应注意
①、用干净抹布清洁冲头。
②、查看表面是否有刮、凹痕。
如有,则用油石去除。
③、及时上油防锈。
④、安装冲头时小心不能有任何倾斜,可用尼龙锤之类的软材料工具把它轻轻敲正,只有在冲头正确定位后才能旋紧螺栓。
2.冲模的安装与调试
安装与调校冲模必须特别细心。
因为冲模尤其大中型冲模,不仅造价高昂,而且重量大微量移动困难,人身的安全应始终放在首位。
无限位装置的冲模在上下模之间应加一块垫木板。
在冲床工作台清理干净后,将合模状态的待试模具置于台面合适位置。
按工艺文件和冲模设计要求选定的压机滑块行程,在模具搬上台面前调至下死点并大于模具闭合高度10~15mm的位置,调节滑块连杆,移动模具,确保模柄对准模柄孔并达到合适的装模高度。
一般冲裁模先固定下模(不拧紧)后再固定上模(拧紧),压板 T型螺栓均宜使用合适扭矩扳手拧紧(下模),确保相同螺拴具有一致而理想的预加夹紧力。
可以有效防止手动拧紧螺纹出现的因体力、性别、手感误差造成的预紧力过大或过小、相同螺纹预紧力不等,从而引起冲压过程中上下模错移、间隙改变、啃剥刃口等故障发生。
试模前对模具进行全面润滑并准备正常生产用料,在空行程启动冲模3~5
次确认模具运作正常后再试冲。
调整和控制凸模进入凹模深度、检查并验证冲模导向、送料、推卸、侧压与弹压等机构与装置的性能及运作灵活性,而后进行适当调节,使之达到最佳技术状态。
对大中小型冲模分别试冲3、5、10件进行停产初检,合格后再试冲10、15、30件进行复检。
经划线检测、冲切面与毛刺检验、一切尺寸与形位精度均符合图纸要求,才能交付生产。
3.冲压毛刺
①、模具间隙过大或不均匀,重新调整模具间隙。
②、模具材质及热处理不当,产生凹模倒锥或刃口不锋利,应合理选材、模具工作部分材料用硬质合金,热处理方式合理。
③、冲压磨损,研磨冲头或镶件。
④、凸模进入凹模太深,调整凸模进入凹模深度。
⑤、导向结构不精密或操作不当,检修模具内导柱导套及冲床导向精度,规范冲床操作。
4.跳废料
模具间隙较大、凸模较短、材质的影响(硬性、脆性),冲压速度太高、冲压油过粘或油滴太快造成的附着作用,冲压振动产生料屑发散,真空吸附及模芯未充分消磁等均可造成废屑带到模面上。
①、刃口的锋利程度。
刃口的圆角越大,越容易造成废料反弹,对于材料比较薄的不锈钢等可以采用斜刃口。
②、对于比较规则的废料,可增大废料的复杂程度或在冲头上加聚胺酯顶杆来防止跳废料,在凹模刃口侧增加划痕。
③、模具的间隙是否合理。
不合理的模具间隙,易造成废料反弹,对于小直
径孔间隙减少10%,直径大于50.00毫米,间隙放大。
④、增加入模深度。
每个工位模具冲压时,入模量的要求是一定的,入模量小,易造成废料反弹。
⑤、被加工材料的表面是否有油污。
⑥、调整冲压速度、冲压油浓度。
⑦、采用真空吸附。
⑧、对冲头、镶件、材料进行退磁处理。
5.压伤、刮伤
①、料带或模具有油污、废屑,导致压伤,需擦拭油污并安装自动风枪清除废屑。
②、模具表面不光滑,应提高模具表面光洁度。
③、零件表面硬度不够,表面需镀铬、渗碳、渗硼等处理。
④、材料应变而失稳,减少润滑,增加压应力,调节弹簧力。
⑤、对跳废料的模具进行维修。
⑥、作业时产品刮到模具定位或其它地方造成刮伤,需修改或降低模具定位,教育作业人员作业时轻拿轻放。
6.工件折弯后外表面擦伤
①、原材料表面不光滑,清洁、校平原材料。
②、成型入块有废料,清除入块间的废屑。
③、成型块不光滑,将成型块电镀、抛光,提高凸凹模的光洁度。
④、凸模弯曲半径R太小,增大凸模弯曲半径
⑤、模具弯曲间隙太小,调整上下模弯曲配合间隙。
⑥、凹模成型块加装滚轴成形。
7.漏冲孔
出现漏冲孔的情况,一般有冲头断未发现、修模后漏装冲头、冲头下陷等因素引起,修模后要进行首件确认,与样品对比,检查是否有遗漏现象,对冲头下沉的,应改善上模垫板的硬度。
8.脱料不正常
①、脱料板与凸模配合过紧、脱料板倾斜、等高螺丝高度不统一或其它脱料件装置不当,应修整脱料件,脱料螺钉采用套管及内六角螺钉相结合的形式。
②、模具间隙偏小,冲头在脱离材料时需要很大的脱模力,造成冲头被材料咬住,需增加下模间隙。
③、凹模有倒锥,修整凹模。
④、凹模落料孔与下模座漏料孔没有对正,修整漏料孔。
⑤、检查加工材料的状态。
材料脏污附着到模具上,使得冲头被材料咬住而无法加工。
翘曲变形的材料在冲孔后,会夹紧冲头,发现翘曲变形的材料,需弄平整后再加工。
⑥、冲头、下模的刃口钝化要及时刃磨。
刃口锋利的模具能加工出漂亮的切断面,刃口钝了,则需要额外的冲压力,而且工件断面粗糙,产生很大的抵抗力,造成冲头被材料咬住。
⑦、适当采用斜刃口冲头。
⑧、尽量减少磨损,改善润滑条件,润滑板材和冲头。
⑨、弹簧或橡胶弹力不够或疲劳损耗,及时更换弹簧。
⑩、导柱与导套间隙过大,返修或更换导柱导套。
◎、平行度误差积累,重新修磨装配。
◎、推件块上的孔不垂直,使小凸模偏位,返修或更换推件块。
◎、凸模或导柱安装不垂直,重新装配,保证垂直度。
9.折弯边不平直,尺寸不稳定
①.增加压线或预折弯工艺
②.材料压料力不够,增加压料力
③.凸凹模圆角磨损不对称或折弯受力不均匀,调整凸凹模间隙使之均匀、抛光凸凹模圆角
④高度尺寸不能小于最小极限尺寸
10.弯曲表面挤压料变薄
①.凹模圆角太小,增大凹模圆角半径
②.凸凹模间隙过小,修正凸凹模间隙
11.凹形件底部不平
①.材料本身不平整,需校平材料
②.顶板和材料接触面积小或顶料力不够,需调整顶料装置,增加顶料力
③.凹模内无顶料装置,应增加顶料装置或校正
④.加整形工序
12.不锈钢翻边变形
在制造翻边之前向材料施用优质成形润滑剂,这能令材料更好地从模具中分离出来,在成形时顺畅地在下模表面移动。
如此给予材料一个更好的机会去分布被弯曲和被拉伸时产生的应力,防止在成形翻边孔边上出现的变形和翻边孔底部的磨损。
13.材料扭曲
在材料上冲切大量孔,导致材料平面度不良,成因可能是冲压应力累积。
冲切一个孔时,孔周边材料被向下拉伸,令板材上表面拉应力增大,下冲运动也导致板材下表面压应力增大。
对于冲少量的孔,结果不明显,但随着冲孔数目的增加,拉应力和压应力也成倍增加直到令材料变形。
消除这种变形的方法之一是:每隔一个孔冲切,然后返回冲切剩余的孔。
这虽然在板材上产生相同的应力,但瓦解了因同向连续一个紧接一个地冲切而产生拉应力/压应力积聚。
如此也令第一批孔分担了第二批孔的部变形效应。
14.模具严重磨损
①、及时更换已经磨损的模具导向组件和冲头。
②、检查模具间隙是否不合理(偏小),增加下模间隙。
③、尽量减少磨损,改善润滑条件,润滑板材和冲头。
油量和注油次数视加工材料的条件而定。
冷轧钢板、耐蚀钢板等无锈垢的材料,要给模具注油,注油点为导套、注油口、下模等。
油用轻机油。
有锈垢的材料,加工时铁锈微粉会吸入冲头和导套之间,产生污垢,使得冲头不能在导套内自由滑动,这种情况下,如果上油,会使得锈垢更容易沾上,因此冲这种材料时,相反要把油擦干净,每月分解一回,用汽(柴)油把冲头、下模的污垢去掉,重新组装前再擦干净。
这样就能保证模具有良好的润滑性能。
④、刃磨方法不当,造成模具的退火,加剧磨损,应当使用软磨料砂轮,采用小的吃刀量,足量的冷却液并经常清理砂轮。
15.防止冲压噪音
冲床是板料加工工业的最关键的必备设备。
冲床在工作时会产生机械传动噪
声、冲压噪声和空气动力性噪声,该噪声最高值可达125dB(A)大大超过国家标准规定的85dB(A)及其以下的噪声指标要求,因而对操作工人及周围环境(如办公室、居民住宅区、会议室等)造成极其严重的伤害和污染。
有效地治理该噪声己成为急待解决的问题。
特别是我国的第一部《噪声法》的实施,环保产业化的规模日益增大,更加速了对这一噪声治理的迫切性。
从冲床噪声源和模具结构入手,要降低噪音得注意以下几点:
①、注重模具保养、清洁,保持刃口锋利。
②、模具刃口的形状、数量、材料和冲切线长,模具刃口与零件接触面不要太大,冲头做斜刃阶梯冲裁,使模具在不同的位置切入深度不同,整个过程实现真正的切断,而不是同步挤断。
③、模具刃口必须垂直于安装面,且凸凹模刃口配合间隙要合理,卸料困难时可增加下模间隙、增加卸料力,采用软表面的卸料板等方法。
④、各工作模板间的配合精度,加工一些排气槽。
⑤、止挡板改做小块拼件,脱料板、下模板改为镶件式,减小抨击面积。
⑥、脱料板弹顶来源改为T型顶杆,弹簧装在上模座,等高套与顶杆配用,开模状态下保证脱料板仍有一定的自由活动量。
⑦、保持润滑良好,模具无干涉,顺畅。
⑧、上下模座表面垫铝板做冲力缓冲。
⑨、模具调试好后,在冲床上加装隔声罩或海绵板隔音处理。
⑩、提高冲床精度,降低结构噪声。
在工作台上安装缓冲减振降噪油缸,齿轮采用斜齿加强润滑和加装齿轮罩,气动系统中加装消声器。