双螺杆组合排列原则
高材1班-张健-玻纤增强PP螺杆元件组合方法
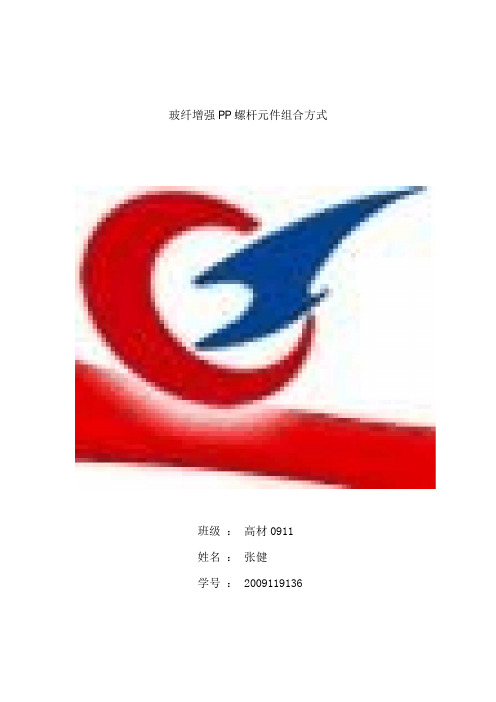
玻纤增强PP螺杆元件组合方式班级:高材0911姓名:张健学号:2009119136前言:在聚合物材料加工中,有一种重要的混炼设备,那就是挤出机,挤出机的发展,大大提高了聚合物材料的加工水平和应用范围。
它分为单螺杆、双螺杆、多螺杆,但实际应用中,还是双螺杆应用最为广泛。
由于双螺杆挤出机要完成许多混合任务,因此目前关于双螺杆挤出机的混合机理研究也比较多。
将双螺杆挤出机用作连续混炼机时,可以对聚合物进行共混改性、填充改性和增强改性;另外,双螺杆挤出机还可以用来进行反应挤出。
双螺杆挤出机的种类很多,根据两根螺杆的位置,可以分为啮合型和非啮合型;根据螺杆旋转的方向不同,又可以分为同向旋转型和异向旋转型。
由此,我们将常见的双螺杆挤出机分为非啮合异向旋转的双螺杆挤出机、啮合同向双螺杆挤出机和啮合异向双螺杆挤出机啮合同向双螺杆挤出机简介啮合同向双螺杆挤出机真正应用于聚合物加工是在20世纪30年代,由意大利LMP公司Roberto Colombo 研制出来。
自从其诞生后,经过半个多世纪的不断改进和完善,它便以其积木式结构带来的多变性和适应性以及优异的混合性能,在成型、共混、改性、反应挤出等聚合物加工过程中得到了广泛应用一、双螺杆挤出机组合的一般原则为:(1)正确分析所要混合物料的形态、性能与配比;(2)必须了解螺杆元件及螺杆各区功能,工作原理及螺杆构型;(3)确定加料方式与位置;(4)选择适当几何参数的螺纹,捏合元件;(5)根据共混体系混合程度要求选择螺杆组合。
(6)加工工艺、设备各部分参数二、啮合同向双螺杆挤出机玻璃纤维增强塑料制备工艺流程玻璃纤维增强作用的好坏,与它在聚合物混合料或制品中的长度、分散状态或分布均匀性、取向以及被聚合物润湿性有关。
玻纤在制品或混合料中长度太短,只起填料作用,不起增强作用;太长,会影响玻纤在混合料或制品中的分散性、成型性能和制品的使用性能。
一般认为,增强热塑性塑料中玻纤的理想长度应为其临界长度的5倍。
双螺杆挤出机的螺杆设计(实用精典)
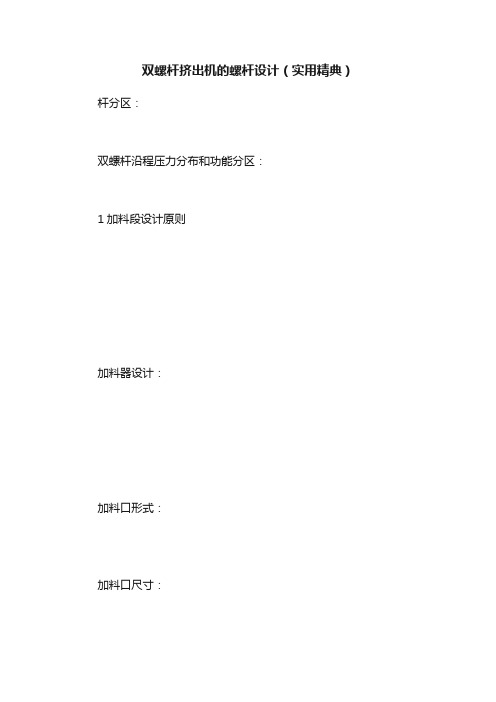
双螺杆挤出机的螺杆设计(实用精典)杆分区:
双螺杆沿程压力分布和功能分区:
1加料段设计原则
加料器设计:
加料口形式:
加料口尺寸:
粉体加料:
挤出机输送能力:
2熔融段设计原则
挤出机越大,外加热所占比越小熔融区螺杆组合设计:
3排气段设计原则:
特种工程塑料需要侧排气口:4计量段设计原则:
计量段中熔体的流动:
熔体的输送与螺纹导程的关系:螺杆头的影响:
混合型螺杆头:
5螺杆组合设计的注意事项:防止损坏或磨损:
同向双螺杆的分离力:
不同元件产生的分离力比较:内向挤压力的产生:
螺杆组合-芯轴变形的补偿:芯轴的变形及磨损:
(来源:韧科技)。
双螺杆挤出机螺杆组合原则
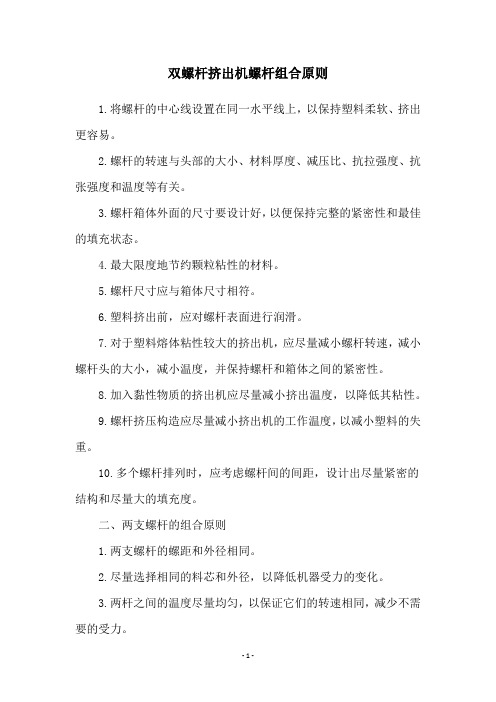
双螺杆挤出机螺杆组合原则
1.将螺杆的中心线设置在同一水平线上,以保持塑料柔软、挤出更容易。
2.螺杆的转速与头部的大小、材料厚度、减压比、抗拉强度、抗张强度和温度等有关。
3.螺杆箱体外面的尺寸要设计好,以便保持完整的紧密性和最佳的填充状态。
4.最大限度地节约颗粒粘性的材料。
5.螺杆尺寸应与箱体尺寸相符。
6.塑料挤出前,应对螺杆表面进行润滑。
7.对于塑料熔体粘性较大的挤出机,应尽量减小螺杆转速,减小螺杆头的大小,减小温度,并保持螺杆和箱体之间的紧密性。
8.加入黏性物质的挤出机应尽量减小挤出温度,以降低其粘性。
9.螺杆挤压构造应尽量减小挤出机的工作温度,以减小塑料的失重。
10.多个螺杆排列时,应考虑螺杆间的间距,设计出尽量紧密的结构和尽量大的填充度。
二、两支螺杆的组合原则
1.两支螺杆的螺距和外径相同。
2.尽量选择相同的料芯和外径,以降低机器受力的变化。
3.两杆之间的温度尽量均匀,以保证它们的转速相同,减少不需要的受力。
4.两支螺杆应以同样的长度设置,以保持塑料的平均性。
5.应保持螺杆的中心距离,以减少填料的压力,使挤出机的挤出更准确,更安全可靠。
6.尽量使两支螺杆的料芯相同,以减少塑料的挤压比例。
锥双螺杆的工作原理

锥双螺杆的工作原理
锥双螺杆是一种常用的机械传动装置,工作原理如下:
1. 锥双螺杆由两根螺杆以一定的角度交叉组合而成。
其中一根螺杆为主螺杆,另一根螺杆为从螺杆,两根螺杆以刀具加工方式形成一对相互交织的渐开线螺旋槽。
2. 当主螺杆转动时,从螺杆也会跟随着转动。
由于螺杆的槽设计是渐开线形状,主螺杆和从螺杆在转动的过程中会产生一个逐渐减小的内外径差。
3. 当物体进入锥双螺杆的螺旋槽时,由于内外径差的存在,物体会受到一定的挤压和螺旋推力。
4. 主螺杆和从螺杆的转动方向相反,因此物体在螺旋槽中的推进方向是沿着锥体的轴线方向。
5. 锥双螺杆的推进力程由主螺杆的螺旋槽高度、转速和进给速度决定。
6. 锥双螺杆可以实现高效的力传递和精确的位移控制,常被应用于液体泵、塑料挤出机、压瓦机等设备中。
高材1班 张健 玻纤增强PP螺杆元件组合方法

玻纤增强PP螺杆元件组合方式班级:高材0911姓名:张健学号: 2009119136前言:在聚合物材料加工中,有一种重要的混炼设备,那就是挤出机,挤出机的发展,大大提高了聚合物材料的加工水平和应用范围。
它分为单螺杆、双螺杆、多螺杆,但实际应用中,还是双螺杆应用最为广泛。
由于双螺杆挤出机要完成许多混合任务,因此目前关于双螺杆挤出机的混合机理研究也比较多。
将双螺杆挤出机用作连续混炼机时,可以对聚合物进行共混改性、填充改性和增强改性;另外,双螺杆挤出机还可以用来进行反应挤出。
双螺杆挤出机的种类很多,根据两根螺杆的位置,可以分为啮合型和非啮合型;根据螺杆旋转的方向不同,又可以分为同向旋转型和异向旋转型。
由此,我们将常见的双螺杆挤出机分为非啮合异向旋转的双螺杆挤出机、啮合同向双螺杆挤出机和啮合异向双螺杆挤出机啮合同向双螺杆挤出机简介啮合同向双螺杆挤出机真正应用于聚合物加工是在20世纪30年代,由意大利LMP公司Roberto Colombo研制出来。
自从其诞生后,经过半个多世纪的不断改进和完善,它便以其积木式结构带来的多变性和适应性以及优异的混合性能,在成型、共混、改性、反应挤出等聚合物加工过程中得到了广泛应用一、双螺杆挤出机组合的一般原则为:(1) 正确分析所要混合物料的形态、性能与配比;(2) 必须了解螺杆元件及螺杆各区功能,工作原理及螺杆构型;(3) 确定加料方式与位置;(4) 选择适当几何参数的螺纹,捏合元件;(5) 根据共混体系混合程度要求选择螺杆组合。
(6) 加工工艺、设备各部分参数二、啮合同向双螺杆挤出机玻璃纤维增强塑料制备工艺流程玻璃纤维增强作用的好坏,与它在聚合物混合料或制品中的长度、分散状态或分布均匀性、取向以及被聚合物润湿性有关。
玻纤在制品或混合料中长度太短,只起填料作用,不起增强作用;太长,会影响玻纤在混合料或制品中的分散性、成型性能和制品的使用性能。
一般认为,增强热塑性塑料中玻纤的理想长度应为其临界长度的5倍。
双螺杆挤出机螺杆组合原则

双螺杆挤出机螺杆组合原则
双螺杆挤出机螺杆组合原则作用是将螺杆和螺套的推力均衡地分配到螺杆的两端,保证挤出机的正常工作。
一、基本原则
1、螺杆的芯腔深度应大于螺套深度,以保证螺杆和螺套之间存在有效的推力传递;
2、螺杆的前端应与螺套的尾端构成一个无接触滑动面,以使螺杆在螺套中滑动时不受到外力抵抗;
3、螺杆和螺套的直径差应小于规定值,以保证螺杆和螺套之间的推力传递有效;
二、两端组合原则
双螺杆挤出机的两端螺杆组合原则用于保证螺杆和螺套之间的推力均衡,提高挤出机的工作效率。
1、内螺杆芯腔深度:该值应大于螺套深度,以保证螺杆之间的推力传递;
2、外螺杆填芯长度:该值应大于螺套的深度,以保证螺杆能够有效地填充推力;
3、螺杆直径差:螺杆直径应小于规定值,以保证螺杆和螺套之间的推力传递有效。
- 1 -。
同向双螺杆挤出特点及螺杆组合原则
!!!"
!"#"$%&’( &#) *+,-+.
!!!!!!!!!!!!!!!!!!!!!!!!!!!!!!!!!!!" !!!!"
同向双螺杆挤ห้องสมุดไป่ตู้特点及螺杆组合原则
郭奕崇 李庆春 闫宝瑞 (北京化工大学塑料机械及塑料工程研究所,北京,!"""#$)
提
要
以及对同向双螺杆挤出工艺制定中的关键问题— — —螺杆组合进行了探讨。 关键词 同向双螺杆,螺杆组合
图! 粉料的熔融
生的漏流和反向元件、中性元件的存在使正位移进 一步被削弱;另一方面,在双螺杆的非啮合区,物 料的运动现象及机理确与单螺杆挤出有相似之处。 因此,同向双螺杆挤出过程兼具摩擦拖曳和正位移 两种特征。 !"% 同向双螺杆挤出中的熔融 上面提到,单螺杆挤出的机理是摩擦拖曳,这 时正常挤出只有在螺槽完全充满,物料被压实后才 能进行。在螺杆机筒的摩擦拖曳及机筒内压力的作 用下,熔料逐渐在螺棱推进面的前方堆积,形成熔 池,使螺槽中熔料与固体物料间界线分明。而同向 双螺杆挤出时,摩擦拖曳作用较小,但由于有正位 移作用,螺槽未充满时物料也可以向前运动,没有 条件形成熔池,熔料与固体料间的位置变换频繁, 未熔物料始终散布在熔料中。这种情况可见图 "。 这是同向双螺杆挤出的熔融与单螺杆挤出最明显的 不同。
开发历史,应用也越来越广泛,但是人们对双螺杆 挤出过程的认识仍不够深入,相关的基础研究也滞 后于应用。双螺杆较为复杂的运动关系和几何关系 造成人们对双螺杆挤出过程定性和定量描述的困 难,但对其研究始终没有间断。因此,深入了解双 螺杆挤出过程,不断地针对生产实际遇到的问题进 行理论分析和总结,逐渐建立起在可靠的试验基础 上能够服务于生产的同向双螺杆挤出应用基础理 论,具有重要的理论意义和实用意义。
双螺杆挤出机机筒的双头和三头捏合块的组合方法
双螺杆挤出机机筒的双头和三头捏合块的组合方法简介双螺杆挤出机是一种常见的塑料加工设备,用于将塑料树脂加热熔融后,通过双螺杆的旋转将熔融的塑料从机筒中挤出,并形成所需的塑料制品。
在挤出机的机筒中,有两种常见的填充物:双头捏合块和三头捏合块。
这两种捏合块都是用于加强机筒内的混合效果,并混合更加均匀的塑料熔体。
本文将介绍双头和三头捏合块的组合方法以获得更好的混合效果。
双头和三头捏合块的区别首先,我们来看看双头和三头捏合块的区别。
如其名,双头捏合块有两个头部,而三头捏合块则有三个头部。
这些头部上都有凸起的齿轮,用于将挤出的熔体牵引和搅拌,以促进混合。
虽然它们都有相同的作用,但由于头部数量的不同,它们之间也有一些区别。
双头捏合块通常用于更简单的加工任务,例如将两种熔体混合在一起。
而三头捏合块则适用于更复杂的应用,例如将多个成分混合在一起,并控制混合过程中的温度。
双头和三头捏合块的组合方法在通常情况下,挤出机的机筒内会使用一种捏合块,但使用两种或两种以上的捏合块可以有效增加混合效果。
使用双头捏合块和三头捏合块的组合是一种常见的方法,可以让挤出机生产更高质量的产品。
具体而言,在机筒入口处先安装一个双头捏合块,然后在它的后面再加上一个三头捏合块。
这样可以首先将两种熔体混合在双头捏合块中,然后让三头捏合块将其进一步混合和搅拌。
这种组合方式将有助于产生更均匀的混合质量,并且可以通过优化双头和三头捏合块的位置来达到更好的效果。
结论在双螺杆挤出机的机筒中,使用双头和三头捏合块的组合方法可以有效提高混合效果,并生产更高质量的产品。
在实际应用中,可以通过优化捏合块的位置和数量,来获得最佳的混合效果。
以上是本文对双头和三头捏合块组合方法的介绍,希望对挤出机的使用者有所帮助。
螺杆组合专题
第23卷 第1期中 国 塑 料Vol.23,No.1 2009年1月CHINA PLASTICS J an.,2009论坛・交流螺杆组合专题编者按:螺杆挤出是最常用的聚合物加工方法之一,螺杆挤出机出现于20世纪30年代,主要有单螺杆与双螺杆两种形式,螺杆组合是针对双螺杆挤出机的。
双螺杆挤出机根据两根螺杆相对旋转方向的不同,分为同向旋转和异向旋转两大类。
异向旋转双螺杆挤出机挤出稳定,主要用于管材、型材等对截面尺寸要求高的制品的挤出成型,同向旋转双螺杆挤出机主要用于混料。
目前使用的同向双螺杆挤出机的挤压系统绝大多数采用模块结构,各机筒组件、各螺杆元件可以通过变换组合来满足特定混料过程对输送、熔融、混炼、脱挥、均化等方面的特殊要求,使用者为了特定的目的将各元件按照一定的顺序排列安装就称为螺杆组合。
“中塑互联”论坛里面已经有很多坛友对螺杆组合进行了深入讨论,本期推出螺杆组合专题,对聚合物加工应用中的螺杆组合问题提供一些解决方案,供读者参考。
我刊今后将不定期将“中塑互联”()上优秀的帖子整理刊发,敬请读者关注。
1 改性PBT的螺杆组合问:以下为72双螺杆组合:56/56、96/96、72/72/ 56/5623、60/4/56、45/5/5622、56/56、90/5/56、45/5/ 362反、56/282反、96/96、92/92、72/72、52/52、45/4522、72/36、45/5/96、45/5/56、56/56、60/4/56、45/5/56、45/5/362反、56/282反、96/9623、72/72、56/5622、52/522 2,其中“45/5/362反”是反向捏合块,“56/282反”是反向螺纹。
长径比32/1,电机110kW,额定转速400r/min,电流270A,生产PBT阻燃增强材料,性能很不稳定,生产20%玻纤改性PBT的冲击强度为50~70MP a,拉伸强度为96~110MP a,弯曲强度为140~180MP a,工艺相同,拉条不稳定,断线多。
双螺杆挤出机螺杆组合原则
双螺杆挤出机螺杆组合原则
双螺杆挤出机是一种常见的挤出设备,常用于制造塑料制品、橡胶制品等。
其螺杆组合原则如下:
1. 同向双螺杆组合原则:两个螺杆的旋转方向相同,同步旋转,适用于挤出高粘度、高分子量的物料。
2. 反向双螺杆组合原则:两个螺杆的旋转方向相反,互相推挤,适用于挤出低粘度、低分子量的物料。
3. 等向异转双螺杆组合原则:两个螺杆的旋转方向相同,但旋转速度不同,适用于挤出中等粘度、中等分子量的物料。
4. 异向异转双螺杆组合原则:两个螺杆的旋转方向相反,旋转速度不同,适用于挤出高粘度、高分子量的物料。
在螺杆组合原则的基础上,还需要考虑螺杆的结构和参数。
例如,螺杆的螺距、螺杆直径、螺杆间隙等参数都会影响挤出效果。
因此,在选择双螺杆挤出机时,需要根据具体的生产需求和物料特性,选择合适的螺杆组合原则和螺杆参数。
- 1、下载文档前请自行甄别文档内容的完整性,平台不提供额外的编辑、内容补充、找答案等附加服务。
- 2、"仅部分预览"的文档,不可在线预览部分如存在完整性等问题,可反馈申请退款(可完整预览的文档不适用该条件!)。
- 3、如文档侵犯您的权益,请联系客服反馈,我们会尽快为您处理(人工客服工作时间:9:00-18:30)。
双螺杆组合排列原则塑料混合是一种有效的将多种组分的原料加工成更均匀、更实用的产品过程。
这一过程中主要发生的是物理反应,当然也存在少量的化学反应。
特殊的,例如反应挤出,我们所期望的更多是化学反应而非物理反应。
而无论是物理还是化学反应,都要求材料的充分混合辊炼,因此就有了共混设备这一有力的加工手段执行者。
先确认几个概念:1.预处理:我们通常说的预处理很多时候是指材料的水分预处理。
由于聚合物和添加剂都具有吸水性,而温度波动和仓库的潮湿都有可能是原材料吸湿,而这正是我们所不希望看到的。
熔融聚合物,如尼龙,聚酯等对水分极其敏感的材料,水分的存在将导致他们的降解,从而导致了各项性能指标的恶化甚至是导致加工失败。
目前比较实用的干燥方式多为热风循环干燥形式。
2.预混合:对于单螺杆而言,吃料能力很大程度上影响了混合效果,很多时候即使是单纯的颜色处理都会因为混合的不均匀而导致材料同批次的前后色差以及后期加工的颜色不均一性;而对于双螺杆,虽然吃料能力基本上不影响混合效果,而且为了计量精确,理论上是应该所有组分在喂料口单独计量、单独喂入。
但是这就意味着需要多个精确喂料器,而这对共混厂家而言是非常的不经济的,因此我们在加工双组分及多组分的材料前,大多都进行预混合。
目前的混合设备多为立式高速搅拌机。
3.分散混合:分散混合是将组分的粒度尺寸减小,将固体块或者聚集体破碎成微粒,或者是不相容的聚合物的分散相尺寸达到所要求的范围。
这一过程通常是依靠大厚度大角度的捏合盘来实现。
4.分配混合:分配混合是使个组分的空间分布达到均匀。
形象点说也就是“平均主义”,保证混合设备内通过分配元件的熔体中各组分的分布均匀。
这个通常是靠窄片小角度捏合盘来实现。
极端的情况先会采取齿轮分配元件来实现。
5.停留时间分布:同批次物料在通过喂料口后通过分散,分布混合最终挤出离开混合设备的时候长短的分布。
这一指标最主要的意义在于评估设备的自洁能力。
其实还有更多的各种公式,我个人觉得这对于我们在实际设计中有一定的指导意义,可惜我这里没有扫描仪,而我这个人又比较懒,公式我就不大打上来了。
下面就按照单螺杆挤出机,双螺杆挤出机(同向,异向啮合),往复式以及挤出的后续加工做一下小结。
(先说明一下,为了方便,我每次都定义一下。
下面出现的挤出机都代表单螺杆挤出机,只到重新进行定义为止。
)单螺杆挤出机的最原型设备应该是阿基米德螺杆。
早在数千年前他就已经提出了在管内装上带螺纹的螺杆向斜面上运送水。
后期的人对其进行了改进,其中最接近于塑料混合的当属使用这种设备将黏土/麦秆(水作为增塑剂加入)进行混合压实,制造砖块。
随后,人们开发了橡胶加工机械,用两辊或三辊混合机对生胶进行塑炼后,再加入挤出机进一步进行加工。
挤出机的5大关键部件包括了:驱动电机和减速箱、止推轴承、料斗、机筒(包括了内部心脏:阿基米德螺杆)。
早期的挤出机的长径比都比较小。
由于橡胶黏度大,在如此小的长径比之下想完成混合加工,意味着必须升高温度。
但是这又将产生一个更大的问题,橡胶在升高温度的情况下将产生交联。
而此时人们发现增加长径比不但能够获得加工热塑性聚合物熔体所需要的高温,同时还能够改善混合性能和熔体的均匀性能。
随着长径比的进一步提高和挤出设备的进一步完善,挤出机逐渐转到了最终用户。
研磨回收和破碎以及废旧塑料回收的出现成为挤出机运用的最大市场。
挤出机的心脏,标准螺杆通常分为三段:喂料段、转化段和计量段。
当然混合螺杆还通常具有其他的组成部分以完成加工中更为复杂的过程。
在整个加工过程中挤出机必须完成:喂料、固体输送、压实、熔融、泵送、均化、排气(可选)到最终的挤出成型。
一般的单螺杆挤出机的长径比为:24、28、30和32;而双螺杆挤出机的长径比为:36、40、42和52;喂料段:在挤出机中,喂料段的主要功能是吃进物料和进行固体输送;同时喂料段对压实固体床(物料在进入螺杆后在螺槽内形成的物料段称之为固体床)以及开始塑化有很大的影响。
在进行喂料段设计时必须注意:螺杆有效扭矩、螺杆材料、螺槽深度与宽度比(纵横比)、摩擦系数等。
同时还应当考虑原材料的尺寸、外观、本体密度和物料的性状。
另外对于添加到混合体系中的添加剂,还需要考虑喂料段是否能够有效吃进这些添加剂。
一般来说,加工结晶性混合物时,喂料段的深度和长度比加工非结晶性材料的喂料段要大。
由于挤出机的输送大部分是靠摩擦拖拽输送,因此喂料区的温度设置一般控制在120-160度之间。
如果该区温度过低,树脂就无法黏附在机筒内壁上,而仅仅是随着螺杆旋转而空转,从而导致了熔融区的缺料;如果该区温度过高,物料会提前熔融塑化,在机筒内壁形成一个环行的熔融膜,起到润滑作用,同样也也引起缺料现象喂料段的另一功能--压实是是固体床的压缩比足够大,保证物料充分密实,达到熔融所需要的状态。
通常情况下粒子或者是破碎的片状材料在压缩后容易在表面发生变形而与机筒内壁贴合在一起,因此也比较容易压缩;而粉体材料由于滑动性较大,因此压缩熔融在时间上和位置上会比粒子或者片状材料滞后。
同时由于粉体材料的空隙面积大,物料密度比较小,在物料中会残留大量的空气,隔离了固体床。
这将进一步减缓熔融过程以及在增大后期的排气工作。
由于挤出机目前比较常见的是屏障形转化熔融段螺杆,比较常见的是在熔融区附加上另外一条螺纹,其螺纹宽度要比原来的窄,而且还进行了根切。
采用这种方式最直观的目的是使熔融的熔体与未熔融的固体床分离,通过避免熔融部分对未熔融的固体床的润滑作用来改善输送能力,同时也降低了熔体的热耗散、熔体过分受热分解以及保证热传递/剪切传递对固体床的热/摩擦能,提高了塑化速度。
计量段:螺杆的计量段长短,螺槽的深浅都属于可变。
不是所有的挤出机的螺杆都是一致的。
如果仅仅是单纯的熔融挤出(例如回收破碎材料),一般采用增大计量段的螺槽深度,这种情况下产量会比较可观,但是混合效果不太理想;如果需要好的混合效果,多采用浅槽螺杆。
这种情况下熔体温度会相应提高,混合质量也相对于深槽要好。
总的思路,计量段的长度应该保证固体床完全塑化,并能够奖励起足够的压力。
因此很多人在设计螺杆是,往往在计量段后面紧接一个混合器。
这里也许有朋友会问:我是采用了浅槽,但是我的产品混合质量还不是非常的理想。
这里存在一个设计产量与实际产量的问题。
一个设计产量远小于你要求的实际产量的设备,即使你进行了必要的改动,但是如果你不放低你的产量要求,这很难保证你的产品质量。
通俗点,就是所谓的一分钱一分货了。
混合段:由于共混加工中仍然有很大一部分涉及到添加剂的混合分散,因此混合段的必要性是不言而喻的。
混合段的主要工作就是在计量段之后帮助提高物料温度、颜色、黏度和添加剂的均匀程度,也有助于确定气体在熔体内发泡的位置。
这对于接下来的排气设置是非常重要的。
除此之外,混合段还将第一计量段隔离开来,建立了一个稳定的排气环境。
所有的塑料颗粒都有其固有的弹性模量,在一定的作用里范围内,粒子会在喂料段和转化段发生形变,而且即使在计量段也部分保持该形变(部分形变粒子会由于固体床破碎后形成的随便在熔体池中呈现游离状态而重新聚集成更大的粒子)。
计量段之后,物料熔融所需要的能量很大一部分是来源于热传递。
由于计量段本身的几何形状限制,在这个区域内很难提供足够的剪切应力。
上游输送过来的未熔融的部分中,一部分由于热传递的作用发生熔融,其余的大部分都被直接输送到下游的混合段。
而分散混合区域则通过剪切应力的作用,将所有进入第二喂料段(排气段之前的一小段区域)的为熔融部分完全塑化,为接下来的排气做好准备工作。
很多在生产过程中出现排气段冒料的个案,绝大部分都是因为混合塑化段未能够充分的塑化熔融而导致在排气区域排气不畅或者冒料等情况。
(也有部分是因为排气段设计不合理导致)。
如前所说,混合塑化段的熔融塑化能力绝大部分是来自于剪切。
而剪切力的产生及其大小主要依赖螺杆的转速和螺杆与机筒之间的间隔。
高的转速和小的间隔意味着更大的剪切应力。
这也就说明了为什么我们在进行增强的时候(这里假设加工的是增强材料),通常我们是在熔融完成后才加入纤维。
纤维在固体床存在的情况下,不可避免的存在着纤维与固体床、纤维与机筒之间的摩擦。
在这种情况下,纤维长度的完成性和设备的磨损就不可避免的产生了。
而在混合塑化段以后加入纤维,这时存在的是螺杆/熔体/纤维/熔体/机筒。
即使存在剪切。
纤维的长度还是能够很大程度的得以保持。
这也同时能够说明为什么我们在做增强材料的时候建议预热纤维(经过预热的纤维不容易在表面形成相对坚固的包复层)。
为了下游有效的排气,就必须是进入第二喂料段(假如存在)或者排气段的物料完全熔融。
本身从熔体中排除挥发分就比较困难,特别是当熔体中还含有未熔融的物质,这种情况下排去挥发分就更困难一般为了改善排气,在排气段一般采用大螺距浅槽的螺纹组合。
同时为了保证螺槽充满度不至于过大而导致冒料或者排气不畅,在排气段的上游一般都采用滞留元件。
例如之前提到的混合器等。
如果物料的分子量比较高,对应着熔体黏度较高,挥发份不容易排脱,这种情况下适当增大真空压力和适当提高排气段的熔体温度。
排气口的方向一般采取垂直式,也有少量是采取水平式或者倾斜式。
考虑的普适性,大多数排气多采用垂直式。
通过排气段后,熔体进入第二计量段。
随着挥发份的排出,此段的熔体压力会随之增高,因此需要的泵送压力也随之增大。
只有在第一/第二计量段的螺槽深度比(泵送比)达到一定程度,第二计量段才能够顺利的克服排料压力顺利的把熔体向下游输送。
调节泵送比可以通过调整螺槽深浅比例或者调节设备的转速来拉开比值。
而在实际生产中通常很难在线改变螺槽深浅,这个时候通常采用局部的螺杆冷却、调整转速或者使用节流阀。
如果对输送压力有更高的要求,例如比较精细的挤出成型,则多数会用到齿轮泵来代替螺杆设计。
几种常用塑料及添加剂加工的一些问题及建议:ABS:ABS的喂料比较容易,而且输送方面由于它与金属具有较好的亲和力,一般比较少出现喂料及输送的问题。
但是由于ABS组成中易产生挥发份的苯乙烯组分,而且由于ABS加工中呈现的黏度都相对来说比较高,因此排气方面需要做些改进POM:POM存在剪切敏感性及分解物具催化分解的能力,因此加工设备的螺槽应当进可能加深,使熔融温度控制在较低范围之内,比降解的可能性降到最低可能。
由于热塑性弹性体颗粒之间存在在很大的内摩擦力及比较搞的黏度,所以很容易在加工过程中产生缺料。
这将造成生产产量的波动和材料的降解。
一般通过提高喂料段的纵横比,强制冷却和震动喂料的方式来解决。
也有一些造粒的原材料是已经经过一次或者多次加工的弹性体。
这些原材料中或多或少存在着填充油、填料,树脂等成分。
虽然内摩擦力和黏度不至于象原料那么夸张,但是由于油的存在导致了材料喂料的输送困难,一般不建议把这类材料粉碎得太过于小。