精益理念(2009)
精益生产管理理念

精益生产管理理念精益生产管理(Lean Production Management)是一种以提高效率、降低浪费和实现持续改进为目标的商业运营理念和管理方法。
它起源于日本的丰田汽车公司,通过简化流程、减少库存、增加产品质量和提高员工参与度来提高企业的竞争力。
精益生产管理不仅仅在制造业中有应用,它也成为了一种在服务行业和其他组织中普遍使用的管理方法。
精益生产管理的核心理念是尽可能减少浪费并实现持续改进。
浪费是指任何不会增加产品或服务的价值,但会增加成本或时间的活动。
精益生产管理方法通过以下几个步骤来减少浪费:第一步是优化价值流。
价值流是指从原材料到最终产品或服务交付的整个过程。
通过剖析整个价值流,可以找到并消除其中的浪费,以提高效率。
例如,通过精确控制库存并与供应商密切合作,可以减少库存的积压和浪费。
第二步是实施精准生产。
这意味着根据产品的需求量进行生产,最大限度地降低库存和成本。
不仅如此,还要通过制定合理的生产计划,确保产品能够按时交付给客户,以提高客户满意度。
第三步是实施标准化工作。
标准化工作是指制定和遵循一套标准化的工作方法和程序,以确保质量和效率。
通过标准化工作,可以降低错误和重新工作的发生率,并提高产品和服务的一致性。
第四步是提高员工参与度和团队合作。
精益生产管理鼓励员工主动参与和贡献,倡导员工团队合作和共同学习。
通过培养员工的创新能力和问题解决能力,可以不断改善工作流程和提高整体效率。
除了以上步骤,精益生产管理还强调持续改进和追求卓越。
持续改进是指以持续性的方式不断寻找并解决问题,从而不断提高业务和流程的效率和质量。
追求卓越是指以超越竞争对手的高标准和目标为导向,不断追求卓越。
通过持续改进和追求卓越,企业可以不断提高其竞争力和市场份额。
精益生产管理的优势是显而易见的。
它可以帮助企业降低成本、提高效率和质量,以及增加客户满意度。
通过减少浪费和提高流程效率,企业可以实现更高的盈利能力和持续改进。
精益工作推进的核心理念
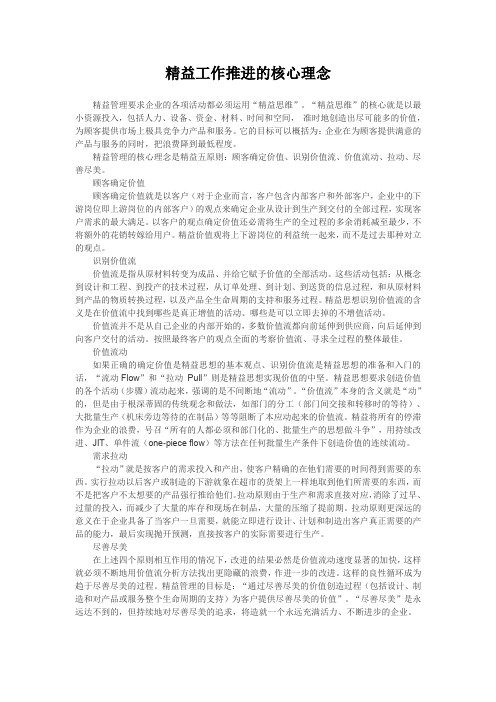
精益工作推进的核心理念精益管理要求企业的各项活动都必须运用“精益思维”。
“精益思维”的核心就是以最小资源投入,包括人力、设备、资金、材料、时间和空间,准时地创造出尽可能多的价值,为顾客提供市场上极具竞争力产品和服务。
它的目标可以概括为:企业在为顾客提供满意的产品与服务的同时,把浪费降到最低程度。
精益管理的核心理念是精益五原则:顾客确定价值、识别价值流、价值流动、拉动、尽善尽美。
顾客确定价值顾客确定价值就是以客户(对于企业而言,客户包含内部客户和外部客户,企业中的下游岗位即上游岗位的内部客户)的观点来确定企业从设计到生产到交付的全部过程,实现客户需求的最大满足。
以客户的观点确定价值还必需将生产的全过程的多余消耗减至最少,不将额外的花销转嫁给用户。
精益价值观将上下游岗位的利益统一起来,而不是过去那种对立的观点。
识别价值流价值流是指从原材料转变为成品、并给它赋予价值的全部活动。
这些活动包括:从概念到设计和工程、到投产的技术过程,从订单处理、到计划、到送货的信息过程,和从原材料到产品的物质转换过程,以及产品全生命周期的支持和服务过程。
精益思想识别价值流的含义是在价值流中找到哪些是真正增值的活动、哪些是可以立即去掉的不增值活动。
价值流并不是从自己企业的内部开始的,多数价值流都向前延伸到供应商,向后延伸到向客户交付的活动。
按照最终客户的观点全面的考察价值流、寻求全过程的整体最佳。
价值流动如果正确的确定价值是精益思想的基本观点、识别价值流是精益思想的准备和入门的话,“流动Flow”和“拉动Pull”则是精益思想实现价值的中坚。
精益思想要求创造价值的各个活动(步骤)流动起来,强调的是不间断地“流动”。
“价值流”本身的含义就是“动”的,但是由于根深蒂固的传统观念和做法,如部门的分工(部门间交接和转移时的等待)、大批量生产(机床旁边等待的在制品)等等阻断了本应动起来的价值流。
精益将所有的停滞作为企业的浪费,号召“所有的人都必须和部门化的、批量生产的思想做斗争”,用持续改进、JIT、单件流(one-piece flow)等方法在任何批量生产条件下创造价值的连续流动。
01.精益基本理念介绍
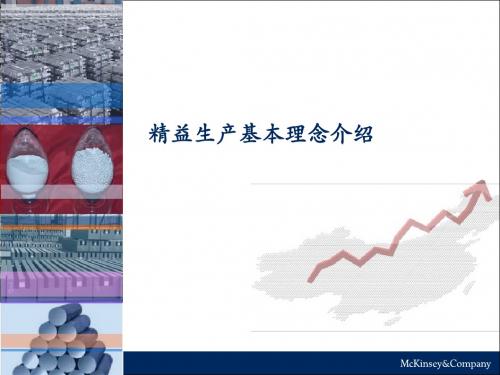
议程
▪ ▪ ▪
精益是一种系统 精益的历史 精益生产的运用
McKinsey & Company
| 1
精益的简单定义
精益是 . . .
精益不是 . . .
▪ 一整套综合原则 ▪ 响应客户需求 ▪ 持续追求完美地为客户
创造价值
▪ 仅仅是生产车间的事情 ▪ 仅限于重复装配 ▪ ▪
方式 一部改进方案 一套工具和技术
McKinsey & Company
GM
Ford
Toyota
| 8
议程
▪ ▪ ▪
精益是一种系统 精益的历史 精益生产的运用
McKinsey & Company
| 9
精益生产源于日本的丰田汽车生产系统 ……
“在丰田,生产一辆凌 志车所需要的人工数, 甚至比 (别的公司)在生 产线终端返工一辆顶级 德国豪华车所需要的人 工数还少” - (摘自 “改变了世界 的机器” The Machine that Changed the World)
McKinsey & Company
| 2
精益生产的主要好处
根本信念是四个主要目标的基础
客户满意度
安全
品质
交付
成本
▪
▪
竞争优势源自 人员 健康和安全是 所有事情中的 重中之重
▪
▪
必须对零缺陷 品质进行设计 和植入 任何缺陷都应 在产生之初即 得到发现并加 以解决
▪
▪
制定流程必须 考虑从端到端 的流程 只在需要的时 间和地点、按 照需要的数量 生产产品
| 5
但是大批量生产有许多不为人注意的陷阱
量产公司所遇到的问题: ▪ 许多公司只注意个别流程的生产率,他们采购大型、 运作迅速的机器,但这些机器不具生产弹性,且必须 批次生产 ▪ 「你可以有任何你想要的颜色,只要是黑色的都行!」 ▪ 但是市场在变 …
精益生产管理的核心理念到底是什么
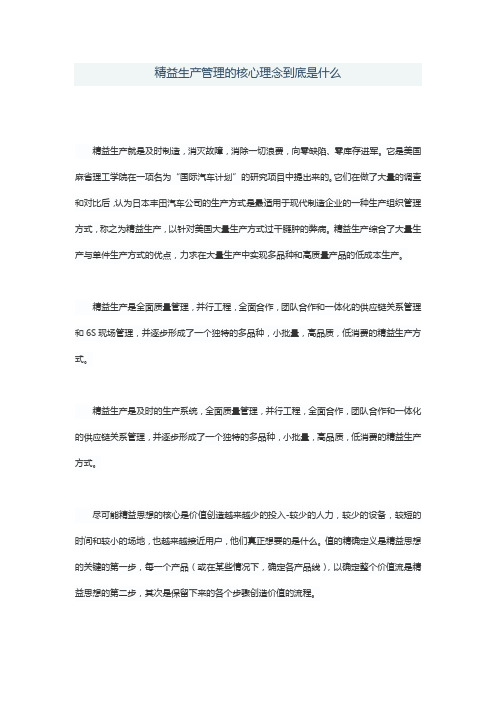
精益生产管理的核心理念到底是什么精益生产就是及时制造,消灭故障,消除一切浪费,向零缺陷、零库存进军。
它是美国麻省理工学院在一项名为“国际汽车计划”的研究项目中提出来的。
它们在做了大量的调查和对比后,认为日本丰田汽车公司的生产方式是最适用于现代制造企业的一种生产组织管理方式,称之为精益生产,以针对美国大量生产方式过干臃肿的弊病。
精益生产综合了大量生产与单件生产方式的优点,力求在大量生产中实现多品种和高质量产品的低成本生产。
精益生产是全面质量管理,并行工程,全面合作,团队合作和一体化的供应链关系管理和6S现场管理,并逐步形成了一个独特的多品种,小批量,高品质,低消费的精益生产方式。
精益生产是及时的生产系统,全面质量管理,并行工程,全面合作,团队合作和一体化的供应链关系管理,并逐步形成了一个独特的多品种,小批量,高品质,低消费的精益生产方式。
尽可能精益思想的核心是价值创造越来越少的投入-较少的人力,较少的设备,较短的时间和较小的场地,也越来越接近用户,他们真正想要的是什么。
值的精确定义是精益思想的关键的第一步,每一个产品(或在某些情况下,确定各产品线),以确定整个价值流是精益思想的第二步,其次是保留下来的各个步骤创造价值的流程。
精益思想,精益生产,精益管理,精益设计和精益供应一系列思想,其核心站点管理“及时和适当的”,“零库存”,“看板”的意思是“按订单生产,以确保产品质量,降低成本。
精益最初的想法是体现在对产品质量的控制,产品的成本优势和技术领先地位的追求,但强调,合理匹配的产品和技术,协调的成本。
自那时以来,商业社会将是逐渐延伸的精益思想延伸的业务活动的全过程,也就是最大限度地追求企业的投资和经济产出,以价值最大化为。
企业可以受益于“精”的字面意思是体现在品质,追求“完美”和“卓越”,“福利”体现在成本,只有成本低于行业平均成本,因此,精益思想不单纯追求以最低的成本,企业的眼睛最好的质量,而是追求用户和企业都满意的质量,追求最好的成本和质量,追求产品的价格和性能的最佳比例分配。
精益理念

精益理念顾客确定价值(Customervalue)、识别价值流(Value stream mapping)、价值流动(Value flow)、拉动(Pulling)、尽善尽美(Perfection)。
1.顾客确定价值顾客确定价值就是以客户的观点来确定企业从设计到生产到交付的全部过程,实现客户需求的最大满足。
价值功能服务什么是价值:价值是一种感知,是感觉能够获利,或者觉得某项产品或服务对顾客有用。
顾客只会为能够为他带来价值的功能付费,而不是产品本身。
互动案例:手机营销3~5年前强调技术参数最近:强调顾客价值企业战略-竞争战略:万分仔细地观察或模拟体验顾客价值生成的过程,发现其价值生成模式,制定你的产品战略或服务战略。
案例:1)快消品-个人护理用品营销现有分类方式:根据气味分类2)学校网站所有的消费品都在服务化-工业品也在服务化:打印复印机、化学品按照服务的视角重新审视自己的产品-做出精准定位-建立满足该客户需求的精干组织架构-培养员工-与竞争对手决战。
潍柴的产品:柴油机(重卡、工程机械、发电设备、中小型船舶)重卡、法士特齿轮、汉德车桥、株洲火花塞猛士、勇士、豪华游艇案例:潍柴乘用车-龙江汽车-潍力汽车,如何提升其产品竞争力?1.客户细分:物流公司客户、专业公司、中小创业者2.产品细分:冷链配送、药品配送、快递配送、餐饮配送3.服务细分:货厢定制服务、配套培训服务、售后服务2.识别价值流价值流是指从原材料转变为成品、并给它赋予价值的全部活动。
这些活动包括:从概念到设计和工程、到投产的技术过程,从订单处理、到计划、到送货的信息过程,和从原材料到产品的物质转换过程,以及产品全生命周期的支持和服务过程。
精益思想识别价值流的含义是在价值流中找到那些是真正增值的活动、那些是可以立即去掉的不增值活动。
精益思想将所有业务过程中消耗了资源而不增值活动叫做浪费。
识别价值流就是发现浪费和消灭浪费。
发现浪费:八大浪费1)不良与返修的浪费所谓不良、修理的浪费,指的是由于工厂内出现不良品,需要进行处置的时间、人力、物力上的浪费,以及由此造成的相关损失。
精益理念(2009)

精益管理理念及实践
精益管理理念及实践简介精益管理是一种管理方法论,旨在通过消除浪费和提高价值创造能力来改进企业的绩效。
精益管理是由托氏制造系统(Toyota Production System)发展而来,被认为是现代企业管理的重要工具。
本文将介绍精益管理的核心理念以及如何实施精益管理。
精益管理的核心理念精益管理的核心理念是“以价值为导向,以流程为导向,通过减少浪费来改进效率和质量”。
它强调对顾客价值的关注,通过优化价值流程,减少不必要的浪费,实现效率和质量的提升。
价值流程精益管理将价值流程定义为一系列的活动,这些活动对顾客提供了有意义的价值。
价值流程包括所有与产品或服务有关的活动,包括从原材料采购到生产和交付的整个过程。
价值流程是精益管理的核心,通过优化价值流程,可以提高整个企业的绩效。
浪费的分类精益管理将浪费分为七类,称之为“七种浪费”:过度生产、等待时间、运输、不合理的库存、过度加工、不合理的动作和不合理的设计。
这些浪费会降低企业的效率和质量,精益管理的目标是通过消除这些浪费来提高绩效。
持续改进精益管理强调持续改进的重要性。
通过不断地识别和解决问题,优化流程和提高绩效。
持续改进是一个循环过程,包括问题的识别、解决方案的制定、实施和评估。
通过持续改进,企业可以不断提高效率和质量。
精益管理的实践精益管理的实践包括以下几个方面:价值流程映射价值流程映射是精益管理中的一种工具,用于可视化和分析价值流程。
通过价值流程映射,企业可以清楚地看到价值流程中的每个步骤和环节,识别出浪费和瓶颈,并制定改进计划。
5S5S是精益管理中用于改善工作环境和工作效率的工具。
5S包括整理、整顿、清扫、清洁和素养五个步骤,目的是创造一个整洁、有序、高效的工作环境,提高工作效率和质量。
KaizenKaizen是精益管理中的一种持续改进方法。
它通过小步骤的改进来不断提高效率和质量,避免一次性的大改革。
Kaizen强调团队合作和员工参与,通过改进工作流程、减少浪费和改进质量来实现持续改进。
精益生产方式的基本理念与主要方法
精益生产方式的基本理念与主要方法1. 精益生产方式的基本理念精益生产模式(Lean Production)是一种以提高企业效率、降低成本和优化生产流程为目标的管理方法。
它的基本理念是去除浪费,即所有不为客户创造价值的活动都应该被消除或简化,从而实现最大化的价值创造。
在精益生产方式中,价值是以客户的需求为导向的。
企业应该通过优化生产流程,降低制造成本、提高产品质量、缩短交付周期等方式来满足客户的需求,并在此过程中减少浪费。
2. 精益生产方式的主要方法2.1 价值流分析价值流分析是精益生产方式中的一项重要方法,用于识别整个价值流中的各个环节,找出存在的浪费和瓶颈,并通过精益工具和技术来改进生产流程。
价值流分析有助于企业发现隐藏的浪费,并提供了改进的方向。
2.2 五大S五大S是指整理(Seiri)、整顿(Seiton)、清扫(Seiso)、清洁(Seiketsu)和遵守(Shitsuke)。
这是一种管理手段,旨在通过整理工作场所、标识物品、保持整洁和定期检查等方式来优化工作环境,提高工作效率和品质。
2.3 一次设定一次设定是指在生产过程中尽可能减少设备的停机时间和调整时间,以提高生产效率。
通过优化设备的加工工艺和工装夹具,减少装卸和调整时间,可以减少不必要的等待并降低生产成本。
2.4 小批量生产小批量生产是精益生产方式中的一种生产方式,相比大规模生产更加灵活和高效。
小批量生产可以减少库存和待加工物料的数量,降低仓储和流通成本,并能更快地响应市场需求的变化。
2.5 连续流水线连续流水线是一种高效的生产方式,通过将各个生产环节有机地连接起来,实现连续流动的生产过程。
连续流水线能够减少停机和等待时间,提高工作效率和产品质量。
2.6 精益定额生产和拉动生产精益定额生产是根据市场需求制定生产定额,以确保生产能力与市场需求相匹配。
而拉动生产则是通过根据市场需求拉动生产,避免过度生产和库存积压,以减少浪费和降低成本。
精益理念的内容理解
精益理念的内容理解1. 精益理念是一种管理哲学,旨在通过最小化浪费和提高价值创造的效率来改进组织的绩效。
它起源于丰田汽车公司的生产方式,并在全球范围内得到了广泛应用。
精益理念强调通过优化流程、减少非必要步骤和消除浪费来提高效率和质量。
2. 精益理念中最重要的概念之一是价值流。
价值流是指在产品或服务的创造过程中,为顾客创造实际价值的一系列活动和步骤。
精益管理的目标是通过理解和优化价值流来减少浪费,并确保价值以最快的方式传递给顾客。
3. 浪费是精益理念中的一个关键问题。
浪费是指在生产或服务过程中没有增加价值、没有满足顾客需求的任何活动或资源的使用。
常见的浪费包括过度生产、库存积压、运输等。
精益理念要求组织识别和消除浪费,以提高效率和降低成本。
4. 另一个重要的概念是持续改进。
精益理念认为改进应该是一个持续的过程,而不是一次性的行动。
持续改进涉及到组织内部的所有层面和员工,鼓励团队合作和共同学习,以不断提高工作流程和产品质量。
5. 精益理念还强调员工的参与和价值。
它认为员工是组织中最重要的资产,他们具有独特的专业知识和经验。
精益管理鼓励员工参与决策和问题解决过程,以发挥他们的潜力和创造力。
6. 另外,精益理念也强调对供应链的管理。
它认为供应链的优化是提高整体效率和质量的关键。
精益管理通过减少库存、优化物流和提高供应商关系等方式来改善供应链的运作。
总结起来,精益理念是一种管理哲学,旨在通过优化流程、减少浪费、持续改进和员工参与来提高组织的效率和质量。
它强调了价值流、浪费的消除、持续改进和供应链管理的重要性。
通过贯彻精益理念,组织可以实现更高效的生产和服务,提高客户满意度并降低成本。
精益思想介绍
3)为了进一步揭开日本汽车工业成功之谜,1985年,美国麻省理工学院筹资 美国麻省理工学院筹资500万美元,确定了一个名叫“国际汽车计划”的研 究项目,在丹尼尔鲁斯教授的领导下,组织了53名专家学者,从 从1984到1989,用了5年时间对14个国家的近90个汽车装配厂进行 实地考察,并对西方的大量生产方式和日本的丰田生产方式进行对比分析 并对西方的大量生产方式和日本的丰田生产方式进行对比分析。最后于1990年出版《改变世界的机器》一书。
精益思想介绍
Greek Li
2009/6/12
什么是精益思想
精益中的“ 精益中的“精”就是精干,不浪费,“益”就是效益。精益就是要少投入,多产出,把成果最终落实到经济效益上来。这是 就是精干,不浪费, 就是效益。精益就是要少投入,多产出,把成果最终落实到经济效益上来。 精益思想的核心所在。
精益以消除浪费为手段,最大限度的为企业谋取经济效益。 。 精益以消除浪费为手段 目标依据: 价格基本上由市场决定,要想取得预期的利润,必须降低成本。而降 目标依据:根据公式:价格-利润=成本。买方市场下,价格基本上由市场决定 低成本的空间在于企业生产活动中存在大量的浪费,消除浪费 消除浪费,就能降低成本。 当然,买方市场下的客户,对于产品的要求不仅仅在于成本 对于产品的要求不仅仅在于成本(C)低廉,还要质量(Q)好,交货期(T)也短,即对TQC的综合要 求。通过主要消除浪费的活动及相关的一些举措,反而能够促进产品质量的提升和快速满足客户交期 反而能够促进产品质量的提升和快速满足客户交期,从而能够真正实现以 客户为中心,为企业谋取最大的经济效益。
精益思想——生产制造目视管理 7种浪费 单元生产 全面生产保全(TPM) 生产均衡化 看板拉式生产 快速换模技术 培养多能工,实现少人化 生产自动化(人、机自动防错) 全面质量管理(TQM)
- 1、下载文档前请自行甄别文档内容的完整性,平台不提供额外的编辑、内容补充、找答案等附加服务。
- 2、"仅部分预览"的文档,不可在线预览部分如存在完整性等问题,可反馈申请退款(可完整预览的文档不适用该条件!)。
- 3、如文档侵犯您的权益,请联系客服反馈,我们会尽快为您处理(人工客服工作时间:9:00-18:30)。
Minor Improvement 小改进
Lead Time 最初的生产提前期
Major
Improvement大改进
Time时间
Value-Adding Activities 增加价值的活动 Non-Value-Adding Activities 不增加价值的活动
箭牌精益培训
利润产生的源泉就是产生效率化
箭牌精益培训
什么是精益生产-Lean发展历史?
Many of the key principles were pioneered by Henry Ford, who was the first person to integrate an entire production system, under what he termed “flow production.” Following World War II, the Toyota Motor Company adapted Ford’s principles as a means of compensating for its challenge of limited human, financial, and material resources. The Toyota Production System (or TPS), which evolved from this need, was one of the first managerial systems using lean principles throughout the enterprise to produce a wide variety of products at lower volumes and many fewer defects than competitors.
箭牌精益培训
管理层期望属下转变工作风格
旧方式
操作工 机修工 工程师 主管 经理 公司环境 我用机器,你修机器 坏机了我才修机 我设计的机器能用就行 问题发生“了”我才解决 我下达工作 混乱,危险,命令式的
新方式
我用机器, 我关心机器
我要防止机器坏机
我设计的机器不出故障 我要支持属下并防止问 题发生 我要与员工一起优化系统 我要整洁,安全 ,健康 授权式的
箭牌精益培训
精益生产的由来
◆JIT和自动化 ◆现地,现物,现实 ◆持续改善 ◆一切浪费的可视化 ◆消灭浪费的小组活动 ◆全员参与/技能发展 ◆组织能力发展
*由詹姆斯.沃麦克和丹尼尔.琼斯在研究丰田生产方
式后提出-Initial by James Womack & Daniel Jones (From the study of TPS) --1990<改变世界的机器>(The Machine That Changed The World) --1996<精益思想>(Lean Thinking) --2005<Lean Solution>
箭牌精益培训
什么是精益生产-Lean发展历史?
1985年美国麻省理工学院国际汽车项目组织了世界上14个国家 的专家、学者,花费了5年时间,耗资500万美元,对日本等国汽车 工业的生产管理方式进行调查研究后总结出来的生产方式,在日本称 为丰田生产方式。
The thought process of lean was thoroughly described in the book The Machine That Changed the World (1990) by James P. Womack, Daniel Roos, and Daniel T. Jones. In a subsequent volume, Lean Thinking (1996), James P. Womack and Daniel T. Jones distilled these lean principles even further to five: Specify the value desired by the customer 以客户为导向
箭牌精益培训
市场竞争带来价格竞争
Pr i
利 润 利 润 不 良 成 本 理 论 成 本
ce Er o 降价 si
利 润 不 良 成 本 理 论 成 本
on
利 润
1. 2. 3. 4. 5. 6. 7.
消除或降低 生产过程中 的7大浪费!
价 格
总 成 本
分解
竞争
Lean
不 良 成 本
理 论 成 本
不良、返工的浪费(人 +设备); 加工的浪费(设备+人) • 过分加工(精度) • 过时加工(7时间) 动作的浪费(人力); 搬运的浪费(人力); 库存的浪费(原料); 制造过多、过早的浪费 (计划和成品); 等待的浪费(管理)。
箭牌精益培训
什么是精益生产Lean愿景和使命?
Vision愿景: 以客户为宗旨,激励持续改善追求完美的核心价值理念。 提升和创造客户价值,打造一流产品,一流制造,一流供 应,一流人才,成为世界级工厂。 Mission使命:开源节流 人尽其才,地尽其利,物尽其用,货畅其流。 Objective目标:需求拉动,JIT快速反应;多品种,小批量;均 衡生产,单件流;低成本,高质量;低投入,高产出。
外部需求 内部需求
日渐剧烈的市场竞争 日益严格的环境安全法规 顾客&消费者更高的要求
趋高的安全事故 持续增长的成本 员工满意的需求 人员发展的需求 文化改变的需求
箭牌精益培训
精益生产外部需求?
箭牌精益培训
我们的市场正在悄然发生变化
适者生存,不适者淘汰!
以前
以后 环境的变化要求我们比 竞争对手前进得更快! 精益加速我们的改善!
浪费的定义Definition of waste ——不为产品增加价值的任何事情Anything which couldn’t add the value of product ——不利于生产或不为客户增加价值的任何事情Anything which did not benefit to the production or couldn’t add value to cost ——顾客不愿付钱由你去做的任何事情 Anything that customers did not like to pay ——尽管是增加价值的活动,但所用的资源超过了“绝对最少”的界 限,也是浪费.For the value-adding activities, if the resource used beyond the “absolute less" is also waste
决定售价的程序发生了变化
市场变化
箭牌精益培训
精益生产内部需求?
箭牌精益培训
企业为什么要实施精益生产?
复杂的问题简单化,简单的问题 标准化,标准的问题持续化,持 续的问题自働化; 以Lean为核心,以小组为改善 动力,以支柱(纵向)为主要管 理形式,以部门(横向)为支撑 架构,用LEAN的路径方法及工 具进行改善,达成结果; 个人发展与企业的发展相结合, 智慧资源浪费才是最大浪费; 建立持续改善的文化!
箭牌精益培训
提供有效工具来帮助企业搭建 持续改善系统
LEAN提供了寻找问题、解决问题、根除损失和持续改善的全面工具:
制造过程中损失统计分析;工厂OEE系统; 质量和统计工具:QA矩阵、QX矩阵、QM矩阵;QCP监控;SPC过 程能力监控与评估等等; 设备维护方面;MP设备信息系统;DR设计系统;RCM管理系统; BD故障分析工具;WCA设备弱点分析/RCA根本原因分析/PM物理现 象分析/FEMA/FEMCA 失效模式分析等等; 设备管理日常执行方面:AM活动;Tag标签体系;CIL/OPL执行与检 查;T卡活动等等; 安全方面:Near Miss未遂事件收集及纠正措施;POKA JOKE防呆措 施; 指导员工日常工作改善方面:4M及5Why工具运用;OPL制作;CIL 制作;KaiZen工具的运用等等; 员工发展方面;我们有Skill Mapping系统;I have a suggestion系统。
Wrigley GZ Factory Lean Concept 精益理念
Delivered by Roger Zhao
箭牌精益培训
目标
为什么要做Lean? 什么是Lean 怎么做Lean
箭牌精益培训
为什么要精益生产?
精益生产实施的背景 致力于成为箭牌公司大家庭优秀成员的箭牌广州工 厂,为更好地满足股东和员工的各方面要求,我们需要 利用精益生产这一有效体系进行突破式的改进。
交互式作用,共同性面对!
箭牌精益培训
通过精益生产改变人的工作态度
实 现 人 的 技 能 提 升 实 现 设 备 效 率 最 大 化
箭牌精益培训
搞精益生产要有成本意识
箭牌精益培训
识别16种损失?
制造过程中常见的16种损失:
•
阻碍设备效率8大损失:停机损失;故障损失;调整损失;换线、换模损失;暖机损失;速
箭牌精益培训
认识浪费understand waste
“减少—成浪费就等于增加—倍销售额” ——大野耐一—— Reduce 10% of waste equal to double the amount of sales By Taiichi Ohno