镗削加工
镗削加工

镗削加工1.什么叫悬伸镗削法?它有哪些特点?使用悬伸的单镗刀杆,对中等孔径和不穿通的同轴孔进行镗削加工,这种加工方法叫悬伸镗削法。
悬伸镗削法的主要特点有:(1)由于悬伸镗削所使用的镗刀杆一般均较短、粗,刚性较好,切削速度的选择可高于支承镗刀杆,故生产效率高。
(2)在悬伸镗刀杆上装夹、调整刀具方便,在加工中又便于观察和测量,能节省辅助时间。
(3)用悬伸镗削法采用主轴送进切削时,由于镗刀杆随主轴送进而不断悬伸,刀杆系统因自重变化产生的挠度也不同,在加工较长内孔时,孔的轴线易产生弯曲。
由于主轴不断伸出,整个刀杆系统刚性不断变差,镗削时在切削力作用下,系统弹性变形逐渐增大,影响孔的镗削精度,使被加工孔产生圆柱度误差。
2、试述采用工作台进给悬伸镗削的特点。
这种镗削方式对被加工孔的精度有何影响?用工作台进给悬伸镗削时;由于主轴悬伸长度在切削前已经调定,故切削过中由刀杆系统自重和受切削力引起的挠曲变形及弹性变形相对较为稳定。
因此被加工孔产生的轴线弯曲和圆柱度误差均比用主轴进给悬伸镗削时小。
这种镗削方式影响孔加工精度的主要原因是床身和工作台导轨的直线度误差,以及它们之间的配合精度。
若床身导轨在水平平面和垂直平面内有直线度误差,会使被加工孔的轴线产生直线度误差和对基准表面产生位置误差;若导轨配合精度差,将会使被加工孔产生圆度误差。
3、什么叫支承镗削法?它有哪些特点?支承镗削法是采用架于镗床尾座套筒内的支承镗杆进行镗削的一种切削加工方式。
支承镗削法的特点是:(1)与悬伸镗削法相比,大大增强了镗杆的刚性。
(2)适合同轴孔系的加工。
可配用多种精度较高的镗刀,加工精度高,能确保加工质量。
(3)装夹和调整镗刀较麻烦、费时,不易观察加工情况,试镗、测量等操作没有悬伸镗削法那样直观、方便。
4、试述采用镗杆进给支承镗削法的特点。
这种镗削方式对被加工孔的精度有何影响?采用镗杆进给支承镗削法镗孔,镗杆伸出长度随主轴进给而不断变化,但镗杆和主轴在两支承点之间的距离不变。
第三章钻削与镗削工艺与装备ppt课件

寒假来临,不少的高中毕业生和大学 在校生 都选择 去打工 。准备 过一个 充实而 有意义 的寒假 。但是 ,目前 社会上 寒假招 工的陷 阱很多
§3-2 钻削方法
1.扩孔的特点
(1)扩孔钻因中心不切削,无横刃,切削刃只做成靠边缘 的一段,避免了横刃切削所引起的不良影响。 (2)因扩孔产生的切屑体积小,不需大容屑槽,扩孔钻可 加粗钻芯,提高刚度,切削平稳。 (3)由于容屑槽较小,扩孔钻可做出较多刀齿,增强了导 向作用,一般整体式扩孔钻有3~4个主切削刃。 (4)扩孔时,切削深度较小,切屑易排出,切削阻力小。 (5)由于扩孔时的切削条件优于钻孔,因此扩孔精度可达 IT9~IT10,表面粗糙度值可达Ra3.2~12.5μm,常作为孔的 半精加工及铰孔前的预加工。
寒假来临,不少的高中毕业生和大学 在校生 都选择 去打工 。准备 过一个 充实而 有意义 的寒假 。但是 ,目前 社会上 寒假招 工的陷 阱很多
§3-1 钻削加工工艺装备
一、钻削加工方法
钻削加工是在钻床上利用钻孔刀具进行切削的一种方法。 钻削加工时,工件固定不动,刀具随主轴旋转完成主运动,同 时沿轴线移动做进给运动。
§3-2 钻削方法
一、钻孔
1.钻削用量的选择 (1)背吃刀量ap:钻实心孔时,背吃刀量 ap是钻头直径d0的一半。
(2)进给量f:进给量是指钻头旋转一周,
沿进给方向移动的距离,单位为mm/r。
(3)钻削速度:钻削速度为钻头主切削 刃外缘处的线速度。
钻削用量选择的基本原则是:在允许范围内,尽量选择 较大的进给量f,当f受到表面粗糙度和钻头刚度的限制时, 再考虑选择较大的切削速度。
寒假来临,不少的高中毕业生和大学 在校生 都选择 去打工 。准备 过一个 充实而 有意义 的寒假 。但是 ,目前 社会上 寒假招 工的陷 阱很多
机械制造基础:镗削加工

• 双刃镗刀
•
镗刀块
•
定尺寸
•
可调尺寸
•
组合式
双刃镗刀的镗刀片是浮动的,两个对称的 切削刃产生的切削力,自动平衡其位置。
(1) 加工质量较高 刀片浮动可抵偿偏摆引起不良影响 较宽的修光刃可减少孔壁粗糙度值
(2)生产率较高,两刀刃同时工作,故生产率较 高
• 钻孔、扩孔、铰孔
• 4、工件装夹
• 被加工孔与基准面平行时:用压板,螺栓直接
固定在工作台上。 • 被加工孔与基准面垂直时:用角铁或弯板装夹
。 • 对于有孔系的工件批量生产时:常制作镗模。
• 二、镗削方法
孔径小:用主轴
• 1、单孔镗削:
孔小径大,深度小:用平旋盘
孔
• 2、孔系镗削:
•
孔系:两个以上在空间具有一定相对位置的孔。
(3) 刀具成本较单刃镗刀高 浮动镗刀主要用于批量生产,精加工箱体 零件上直径较大的孔。
镗床的主要加工内容
• (a)镗孔(b)镗较深孔(c)镗同轴孔 • (d)镗大孔(e)镗平行孔(f)镗垂直孔
镗床上加工端面及铣平面和成形面
(a)加工端面
(b)加工内环面
(c)铣平面 •(d)铣成形面
• 镗内螺纹 • • •
镗削加工
认识镗床 镗刀种类 镗削方法
镗削
镗削加工:利用各种镗床对孔进行镗削加工的 加工手段 。镗削是对已有孔进行扩大孔径,并提高表面质量。
镗削运动:镗刀旋转为主运动,工件或镗刀移动为进给 运动。 镗床与钻床比较:镗床可以加工大直径孔,精度较高, 且与孔的轴线的同轴度、垂直度、平行度及孔距精度均 较高。因此镗床特别适合加工箱体、机架等结构复杂, 尺寸较大零件。
镗削加工
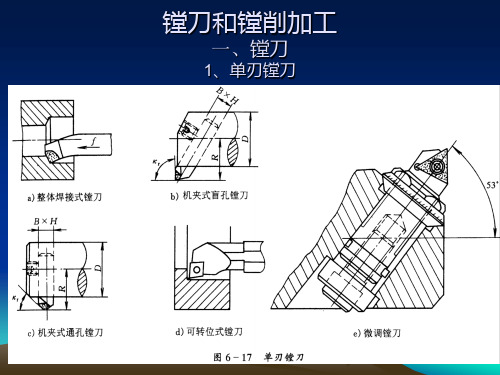
镗刀和镗削加工
一、镗刀
1、单刃镗刀
单刃镗刀 a ) 镗通孔 b)镗盲孔
孔 加 工 刀 具
a
b
单刃镗刀 1 —紧固螺钉 2—精调螺母 3—刀块 4—刀片 5—镗杆 6—导向键
镗 床
单面卧式金刚镗床
镗床夹具
一、镗床夹具的类型 镗床夹具:主要用于加工箱体、支架、支座等 零件上的孔或孔系,保证孔的尺寸精度、几何 形状精度、孔距及位置精度。 组成:夹具体、定位元件、夹紧装置、镗模架 (镗模板)、镗套等组成。
镗套
镗套
导向
导向
支架
镗套的布置方式
1.单支承引导镗夹具
1).特点:
• ②单支承后引导
• 适用于加工D<60的通 孔、盲孔。 • 特点: • 多数情况下,镗杆导向 部分的直径应大于加工 孔直径。
• h=0.5~1D
前后双支承引导镗夹具
• 双支承引导时镗孔的位置精度由镗模保证,不受机床主 轴精度的影响。因此镗杆与机床主轴采用浮动连接。 • 前后双支承镗模一般用于镗削孔径较大、孔的长径比 L/D>1.5的孔或孔系,加工精度较高,但更换刀具不方 便。
前双支承引导镗夹具
镗 床
(2)镗削特点 刀具结构简单,通用性达,可粗加工也可半精加工和精加工,适用批量较 小的加工,镗孔质量取决于机床精度。
(3)运动分析 主运动为镗刀的旋转运动,进给运动为镗刀或工件的移动 。 (4)分类 ①卧式镗床 卧式镗床既要完成粗加工(如粗镗、粗铣、钻孔等),又要进行精加工 (如精镗孔)。因此对镗床的主轴部件的精度、刚度有较高的要求. 卧式镗床的主参数是镗轴直径 。
镗床及其铣削加工
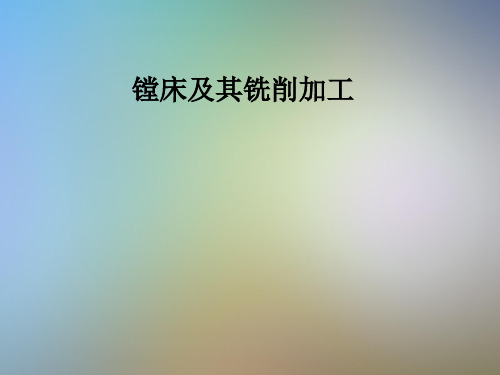
3)镗削刀具结构简单、种类多样,具有较好的通用性 ,但镗削加工(特别是单刃镗刀加工)生产效率较低;
——适用于批量生产的零件加工及位置精度要求较高的 孔的加工。
三、常用镗床
1、卧式铣镗床
工作台
2)砂轮相对于工件的高速旋转运动是主运动,一般砂轮 圆周速度在35米/秒左右;
3)砂轮是非金属刀具,它是由氧化物系(刚玉Al2O3 )、 碳化物系(碳化硅、碳化硼)等磨料,加以结合剂组成, 磨削速度高,工件硬度大,磨削过程产生大量的切削热, 故磨削需要用切削液进行充分的冷却和润滑,以提高加工 表面质量和生产效率;
坐标镗床加工的孔可获 得很高的尺寸和形状精度 ,也可保证精确的孔间或 孔与某基准面间的位置精 度;
坐标镗床可进行精密刻 线和滑线,也可进行孔距 和直线的精密测量;
——主要用于加工精度 要求较高的工件、夹具、 模具和量具等。
3、精镗床(金刚镗床)
主轴箱
主轴
工作台
床身
精镗床的特点:
精镗床以前常采用金刚石 刀具而得其名(现在用硬质 合金);
3、悬臂刨床
立柱
横梁
床身
悬臂刨床的特点:
立刀架
侧刀架
工作台
悬臂刨床的工作特点 与龙门刨床相似;
特别适合加工宽度较 大,且又不需要在整个 宽度上全部加工的工件 ;
横梁的刚度不如龙门 刨床好,故加工精度受 限;
4、插床(立式刨床)
立柱 滑枕 插刀架 工作台 上滑座 下滑座 床身
插床的特点:
插床的主运动是滑枕 与插刀的往复运动,进 给运动是圆工作台带动 工件的回转运动(周向 进给)和上下滑座的纵 向、横向移动;
第8章钻削和镗削加工ppt课件

教学内容
❖ 8.1 钻削加工概述 ❖ 8.2 钻削加工设备 ❖ 8.3 钻孔刀具 ❖ 8.4 扩孔和锪孔 ❖ 8.5 铰孔刀具 ❖ 8.6 复合加工刀具 ❖ 8.7 镗削加工概述 ❖ 8.8 镗削加工刀具
一、钻削加工概述
❖ 1.1 钻削加工特点
径向力相互抵消,切削效率高 排屑困难,加工表面质量差 粗加工,精度为IT13~IT11,Ra为50~12.5μm
进给运动路线表达式
Ⅶ -3 47 8 2 42 1 -Ⅷ -1 38 0//3 2 -Ⅸ 6 4-1 26 /2 /4 31 5-Ⅹ -1 36 //12 45 0-Ⅺ -1 46 0//4 1 -Ⅻ 1 6M 3-M 4(合 )-Ⅹ-Ⅲ 727-M 5(合 )-Ⅹ-Ⅳ z13-齿(条 m3)-轴向进
三、钻削加工刀具
❖ 3.3 麻花钻钻孔方法
按划线位置钻孔 钻较深的孔 在硬材料上钻孔 钻孔径较大的孔 钻高塑性材料上的孔 钻斜面上的孔
三、钻削加工刀具
❖ 3.4 标注麻花钻存在的问题
前角变化且相差较大,使切削变形大 主刃长,宽度大,切屑变形和排屑难 横刃处前角呈负值,轴向力大 外缘转角处和副后刀面摩擦严重 横刃处的前后角是刃磨时自然形成的
灵活性大,适应性强 操作技术要求较高 镗刀结构简单,刃磨方便 可以修正位置误差 尺寸精度和表面质量高
七、镗削加工概述
❖ 7.2 镗床的工艺范围
七、镗削加工设备
❖ 7.1 镗床的加工方法
七、镗削加工设备
❖ 7.2 卧式镗床TP619
镗床的结构组成 镗床的主运动 镗床的进给运动
七、镗削加工设备
三、钻削加工刀具
❖ 3.5 麻花钻的修磨与改进
修磨横刃
镗削工艺特点
镗削工艺特点
镗削是一种重要的金属加工工艺,它是通过切削刀具将材料从孔内切削成所需形状的一个过程。
镗削工艺主要应用于汽车零件、航空航天等领域,具有以下特点:
一、镗削工艺具有高精度和高质量的特点。
镗削过程是在加工前先进行淬火退火等热处理,然后进行机械加工,保证了镗削加工出来的工件具有高质量和高精度的特点。
此外,镗削加工可以针对不同的材料进行加工,如钢、铜、铝合金等,镗削工艺能够保证材料的物理性质得以保留。
二、镗削技术可实现复杂形状的制造。
不同于传统的加工方法,如铸造、锻造等,镗削工艺能够实现精确的孔内加工,可以制造各种复杂形状的精密零件,能够满足各种机械设备对零件形状的需求。
这为工业生产带来了很大的便利。
三、镗削工艺可减少表面粗糙度,提高加工效率。
镗削加工是一种高速、高效的加工方法,能够使工件表面粗糙度得到减少,大大提高了加工效率。
同时,镗削工艺还可以提高加工质量,使工件外形更加规范。
四、镗削工艺可以通过自动化手段实现生产制造。
镗削机械可以通过数控自动化,实现自动化生产制造,不仅提高了生产效率,也可以避免因人误差带来的生产损失,保证了工件的质量。
其模块化的特点,也方便更换刀具附件等加工零部件,从而加快生产效率。
总之,镗削工艺在加工业中占据着重要的地位,其独特的优势可以适应不同领域的加工需求。
随着机械制造技术的发展,镗削工艺也将进一步发展,不断演化为更加先进和高效的加工方法,为工业自动化生产提供了更多的可能。
第六章-钻削、铰削与镗削加工
应用
下列加工方法中,工件做主运动的是 ( ) (A)铣削加工 (B)车削加工 (C)钻削加工
钻削加工中,刀具作旋转主运动,工件作进给 运动。 ( )
镗削
1、应用:镗床是一种主要用镗刀在工件上加 工孔的机床。通常用于加工尺寸较大,精度 要求较高的孔,特别是分布在不同表面上, 孔距和位置精度要求较高的孔。 2、运动分析:主运动为镗刀的旋转运动,进 给运动为镗刀或工件的移动。 3.镗削加工特点: 刀具结构简单,加工灵活性大、通用性强, 可粗加工也可半精加工和精加工,适用批量较 小的加工,镗孔质量取决于机床精度。
平面磨削
磨削加工的特点
磨削加工是应用较为广泛的切削加工方法之一。 与其他切削加工方式,如车削、铣削、刨削等比 较,具有以下特点: (1)磨削速度高,磨削温度高,将产生大量的 热,需要大量的冷却润滑液。 (2)磨削加工可以获得较高的加工精度和较低 的表面粗糙度。 (3)磨削不但可以加工软材料,而且还可以加 工淬火钢及其他刀具不能加工的硬质材料。 (4)磨削加工的切削深度很小,在一次行程中 所能切除的金属层很薄。 (5)加工范围广。
内、外圆磨削
2、平面磨削 平面磨床用于磨削工件上的各种平面。磨削时 , 砂轮的工作表面可以是圆周表面,也可以是端面。 (1)周边磨削 以砂轮的圆周表面进行磨削时, 砂轮与工件的接触面积小,发热少,磨削力引起的 工艺系统变形也小,加工表面的精度和质量较高, 但生产率较低。以这种方式工作的平面磨床,砂轮 主轴为水平(卧式)布置。 (2)端面磨削 用砂轮(或多块扇形的砂瓦)的 端面进行磨削时,砂轮与工件的接触面积较大,切 削力增加,发热量也大,而冷却,排屑条件较差, 加工表面的精度及质量比前一种方式的稍低,但生 产率较高。以此方式加工的平面磨床,砂轮主轴为 垂直(立式)布置。
深孔的镗削加工
深孔的镗削加工1.加工方案分析在深孔的镗削加工中按照进给方式的不同分为推镗法和拉镗法两种。
推镗法按其不同的排屑方式又分外排屑推镗法和内排屑推镗法。
1.1.1.外排屑推镗法外排屑推镗法的冷却液由油泵输入输油器,通过镗杆外圆与已加工内孔之间的环形空隙流入切削区,可以充分起到镗刀导向块(条)的强制润滑冷却和消振作用,并将切屑通过坯孔冲向镗床床头方向进入集屑箱。
1.1.2.內排屑推镗法内排屑推镗法的冷却液输入方式和外排屑推镗法相同,而冷却液的回流方式则是强制切屑从镗刀体上的排屑孔通过镗杆内孔向后排到集屑箱。
这种排屑方式不仅能起到强制冷却和消振作用,而且迫使全部切屑从镗杆内孔排出,又称BTA 镗削法【1】。
推镗法在镗削加工过程中,镗杆始终处于轴向受压的工作状态,易引起镗杆的弯曲及振动,产生孔加工的直线性误差。
但由于加工较大孔径时,镗杆外径可达孔径的80~85%,故镗杆刚性一般都能满足要求。
此外,推镗法镗刀导向套的装夹也十分方便。
外排屑推镗法由于排屑空间相对大些,对镗刀切削时的断屑要求也较宽,短时间出现一些长切屑不会影响镗削效果,并可以通过改变工艺参数达到断屑效果;内排屑推镗法由于排屑空间极为有限,要求切屑成“C”字形,一旦出现带状长屑将会堵塞排屑孔,损坏镗刀,划伤孔壁。
从对密封装置的要求看,外排屑推镗法对切削液压力要求较低,通常由内孔倒角与金属环接触密封即能达到要求;内排屑推镗法是一个(机床-工件内孔-镗杆间)封闭切削液通道,切削液压力高,故工件内孔与机床的密封要求较为严格,一般选用工件内孔与橡胶密封环接触密封。
1.1.3.组合镗刀推镗法组合镗刀即推镗、精镗、浮镗、滚压组成一体,一次走刀完成镗削。
这种方法的优点是工序集中,辅助工时短,但存在刀具结构复杂、笨重,刀具成本高,镗削时切削余量、切削速度和进给量等参数相互制约的缺陷。
同时组合镗刀切削力比较大,镗杆刚性差时易振动,这些均直接影响内孔的加工质量,故国内加工深孔时采用此工艺的较少。
镗削
镗削的工艺特点
2)可校正原有孔的轴线偏斜 可校正原有孔的轴线偏斜 与其他孔加工的方法相比,镗孔的突出 优点为,可利用镗刀在一定范围内加工出任 意直径的孔,可修正已有孔的位置偏差。 3)加工质量受镗刀杆尺寸影响 加工质量受镗刀杆尺寸影响 由于镗刀和镗杆直径受孔径与孔深限制, 刚度差,易产生变形和振动,孔的加工精度 和表面粗糙度受到较大影响。
镗削的工艺特点
4)生产效率低 生产效率低 为减少镗杆的弯曲变形,需采用较 小的背吃刀量和进给量进行切削,不能 高速切削和强力切削。 从镗刀结构看,其切削刃少,并且 切削液的注入和排屑困难,切削效率低。
镗削的工艺特点
5)工件装夹次数少 工件装夹次数少 能在工件的一次安装中完成粗加工、 半精加工和精加工等多工序的加工,减 小了因多次装夹而带来的误差,保证加 工精度。
(三Байду номын сангаас坐标镗床
坐标镗床主要用于镗削高精度的孔, 特别适用于加工相互位置精度很高的 孔系,还可钻孔、扩孔、铰孔。也可 以用于高精度测量工作。是一种万能 性很强的精密机床。
二、镗削的工艺特点
1)适应范围广 适应范围广 镗削既可加工通孔也可加工盲孔。可在钻 孔、铸孔和锻孔基础上进行,主要用于箱体、 机架等结构复杂的大中型零件上的孔与孔系加 工。设有坐标测量装置,容易保证孔与孔之间、 孔与基准平面之间的尺寸精度和位置精度。
§6.6 镗削加工
定义: 利用镗刀进行的一种应用较广的 孔及孔系的加工方法,可进行孔 的粗加工、半精加工和精加工。
孔的镗削
主运动:镗刀的旋转 运动 进给运动:工件或镗 刀的直线运动 设备:镗床、车床、 铣床、数控机床等。
镗单孔
一、镗 床
镗床通常用于加工尺寸较大、精度要求较 高的孔,特别是分布在不同表面上、孔距 和位置精度要求较高的孔,如各种箱体、 汽车发动机缸体等零件上的孔。 类型:卧式镗床、立式镗床、落地镗床、 坐标镗床和金刚镗床等多种类型。
- 1、下载文档前请自行甄别文档内容的完整性,平台不提供额外的编辑、内容补充、找答案等附加服务。
- 2、"仅部分预览"的文档,不可在线预览部分如存在完整性等问题,可反馈申请退款(可完整预览的文档不适用该条件!)。
- 3、如文档侵犯您的权益,请联系客服反馈,我们会尽快为您处理(人工客服工作时间:9:00-18:30)。
图10-4 立 式双柱坐 标镗床 1—工作台 2—横梁 3、 6—立柱 4—顶梁 5—主轴箱
7—主轴 8—床身
(二)立式双柱坐标镗床 立式双柱坐标镗床如图10-4所示,它具有由两侧立柱、顶梁和床身构 成的龙门框架式结构。主轴箱5装在可沿立柱导轨上下调整位置的横 梁2上,工作台1则直接支承在床身8的导轨上。镗孔的坐标位置由主 轴箱沿横梁导轨横向移动和工作台沿床身导轨纵向移动来确定。立式 双柱坐标镗床的主轴箱(装在龙门框架上)其悬伸距离较小,并且工 作台和床身之间层次少,所以,这种坐标镗床刚度较高,承载能力较 强。因此,大、中型坐标镗床常采用这种布局形式。
图10-7 采用镗削加工的箱体
图10-8 机夹式单刃镗刀
a)盲孔镗孔刀 b)通孔镗刀 c)、d)阶梯孔镗刀 二、镗刀的类型及应用 (一) 单刃镗刀 单刃镗刀 它适用于孔的粗、精加工。单刃镗刀的切削效率低,对工人操作技术要 求高。加工小直径孔的镗刀通常作成整体式,加工大直径孔的镗刀可作 成机夹式。图10-8为机夹式单刃镗刀,它的镗杆可长期使用,镗刀头通 常作成正方形或圆形。 镗杆、镗刀头尺寸与镗孔直径的关系见表10-1。
(1)镗杆的旋转主运动; (2)平旋盘的旋转主运动; (3)镗杆的轴向进给运动; (4)主轴箱垂直进给运动; (5)工作台纵向进给运动; (6)工作台横向进给运动; (7)平旋盘径向刀架进给运动; (8)辅助运动:主轴箱、工作台在进给方向上的快速调位 运动、后立柱纵向调位运动、后支架垂直调位运动、工作台 的转位运动。这些辅助运动由快速电机传动。
三 金刚镗床
图10-6是单面卧式金刚镗床 的外形图。机床的主轴箱固 定在床身上,主轴高速旋转 带动镗刀作主运动。工件通 过夹具安装在工作台上,工 作台沿床身导轨作平稳的低 速纵向移动以实现进给运动。 工作台一般为液压驱动,可 实现半自动循环。
图10-6 单面卧式金刚镗床外形图
主轴组件是金刚镗床的关键部件,它 的性能好坏,在很大程度上决定着机 床的加工质量。这类机床的主轴短而 粗,在镗杆的端部设有消振器;主轴 采用精密的角接触球轴承或静压轴承 支承,并由电动机经皮带直接传动主 轴旋转,可保证主轴组件准确平稳地 运转。 金刚镗床的种类很多,按其布局形式 可分为单面、双面和多面;按其主轴 的位置可分为立式、卧式和倾斜式; 按其主轴的数量可分为单轴、双轴及 多轴。
图10-13 后支座镗孔
图10-21 前单支 承孔
1.前单支承镗模
图10-21所示采用前单支承镗孔,镗模支承设置在刀具前方。主要用于加工孔 径D>60mm、加工长度L<D的通孔。一般镗杆的导向部分直径d<D。因导向 部分直径不受加工孔径大小的影响,故在多工步加工时,可不更换镗套。这 种布置也便于在加工中观察和测量。但在立镗时,切屑会落入镗套,应设置 防屑罩。
T68卧式镗床系统图(含子系统图)
旋转(并带动刀架) 径向进给 轴向进给及旋转 后支架 镗主轴 平旋盘 径向刀架 带轮
主轴箱
用平旋盘时鏜杆可缩回去
立柱 后立柱 横向进给 纵向进给
主电机
Hale Waihona Puke 工作台上滑座 下滑座
垂 直 进 给
进给电机
T68卧式镗床床身
图10-2 卧式铣镗床的典型加工方法
图10-2所示为卧式铣镗床的几种典型加工方法:图10-2a) 所示为用装在镗轴上的悬伸刀杆镗孔,图10-2b)所示为利 用长刀杆镗削同一轴线上的两孔,图10-2c)所示为装在平 旋盘上的悬伸刀杆镗削大直径的孔,图10-2d)所示为用装 在镗轴上的端铣刀铣平面,图10-2e)和f)所示为用装在平 旋盘刀具溜板上的车刀车内沟槽和端面。
(二)双刃镗刀
常用的有固定式镗刀块和浮动镗刀。 1.固定式镗刀块 高速钢固定式镗刀块如图10-10所示,也可制成焊接式或 可转位式硬质合金镗刀块。固定式镗刀块用于粗镗或半精 镗直径大于40mm的孔。工作时,镗刀块可通过楔块或者 在两个方向倾斜的螺钉等夹紧在镗杆上。安装后,镗刀块 相对于轴线的不垂直、不平行与不对称,都会造成孔径扩 大,所以,镗刀块与镗杆上方孔的配合要求较高,方孔对 轴线的垂直度与对称度误差不大于0.01mm。 固定式镗刀块镗削通孔时kr取45°,镗削盲孔时kr取90°, 而取5°~10°, 取8°~12°,修光刃起导向和修光 作用,一般取L=(0.1~0.2)dw。
三、无支承镗床夹具
工件在刚性好、精度高的金刚镗床、坐标镗床或数控机床、 加工中心上镗孔时,夹具上不设置镗模支承,加工孔的尺 寸和位置精度均由镗床保证。这类夹具只需设计定位装置、 夹紧装置和夹具体即可。 图10-23为镗削曲轴轴承孔的金刚镗床夹具。在卧式双头 金刚镗床上,同时加工两个工件。工件以两主轴颈及其一 端面在两个V形块1、3上定位。安装工件时,将前一个曲轴 颈放在转动叉形块7上,在弹簧4的作用下,转动叉形块7使工 件的定位端面紧靠在V形块1的侧面上.当液压缸活塞5向下 运动时,带动活塞杆6和浮动压板8、9向下运动,使四个浮 动压块2分别从两个工件的主轴颈上方压紧工件。当活塞 上升松开工件时,活塞杆带动浮动压板8转动90°,以便 装卸工件。
第二节 镗刀
一、镗削特点 二、镗刀的类型及应用 。 一、镗削特点 除了在车床、钻床上加工孔以外,用镗孔刀具在镗床上也可以加工孔。对于 直径较大的孔、内成形面以及有一系列位置精度要求的孔,镗孔是主要的切 削加工方法。 (1) 镗削可以加工机座、箱体、支架等外形复杂的大型零件上的直径较 大的孔、以及有位置精度要求的孔和孔系,特别是有位置精度要求的孔和孔 系,在一般机床上加工很困难,在镗床上利用坐标装置和镗模则很容易做到。 如图10-7所示的箱体。 (2)镗削加工灵活性大,适应性强。加工尺寸可以大亦可小,对于不同的 生产类型和精度要求的孔都可以采用这种加工方法 (3)镗削加工能获得较高的精度和较小的表面粗糙度。一般尺寸公差等级 为IT8~IT7,Ra值为1.6~0.8。 若用金刚镗床和坐标镗床则加工质量可更 好。 (4)镗削加工操作技术要求高,生产率低。要保证工件的尺寸精度和表面 粗糙度,除取决于所用的设备外,更主要的是与工人的技术水平有关,同时 花在机床、刀具上的调整时间亦较多。镗削加工时参加工作的切削刃少,所 以一般情况下,镗削加工生产效率低。若使用镗模可以提高生产率,但一般 用于大批量生产。
第三节 镗床夹具
一、双支承镗模 二、单支承镗模 三、无支承镗床夹具 一、双支承镗模
(一)前后双支承镗模 (二)后双支承镗模 (三)镗套 (四)镗杆 (五)浮动接头 (六)镗模支架和底座
图10-12 镗削车床尾座孔镗模 1-镗模支架 2-回转镗套 3、4-定位板 5、8-压板 6-夹紧螺钉 7-支承钉 9-镗刀杆 10-浮动接头
图10-9 微调镗刀 1—镗刀头 2—微调螺母 5—调节螺母 3—螺钉 6—固定座套 4—波形垫圈
镗刀的刚性差,切削时易引起振动,所以镗刀的主 偏角选得较大,以减小径向力Fp。镗铸件孔或精镗 时,一般取kr=90°;粗镗钢件孔时,取kr=60°~ 75°,以提高刀具的耐用度。镗杆上装刀孔通常对 称于镗杆轴线,因而,镗刀头装入刀孔后,刀尖一 定高于工作中心,而使切削时工作前角减小,工作 后角增大,所以在选择镗刀的前、后角时要相应的 增大前角,减小后角。 镗盲孔时,镗刀头在镗杆上倾斜53°8ˊ。微调螺 母的螺距为0.5mm,微调螺母上刻线80格,调节时, 微调螺母每转过一格,镗刀头沿径向移动量为 mm=0.005mm R 0.5 / 80sin 538
二、坐标镗床
坐标镗床是一种高精度级机床,它具有测量坐标位 置的精密测量装置,而且这种机床的主要零部件的 制造和装配精度都很高,并有良好的刚性和抗振性。 所以它主要用来镗削精密的孔(IT5级或更高)和 位置精度要求很高的孔系(定位精度达 0.002~0.01mm),如,钻模、镗模等的精密孔。 坐标镗床按其布局和型式不同,可分为立式单柱、 立式双柱和卧式等主要类型。
镗削加工
§1 镗床§2 镗刀§3 镗床夹具
开封大学机电工程学院
教师:孙敏
第一节 镗床
一、卧式铣镗床
图10-1 卧式铣镗床 1-后支架 2 —后立柱 8—主轴箱 3 —工作台 9—后尾筒 4—镗轴 10—床身 5—平旋盘 6—径向刀具溜板 7—前立柱 12—上滑座
11—下滑座
卧式镗床具有下列工作运动:
图 10-3 立式单 柱坐标镗床 1—床身 2— 床鞍 3—工作 台 4—立柱
5—主轴箱
立式单柱坐标镗床如图10-3所示。 这种类型机床工作台的三个侧面都是敞开的,操作比较方便。但由于这 种坐标镗床的工作台须实现两个坐标方向的移动,使工作台和床身之间 层次增多,削弱了刚度。此外,由于主轴箱悬臂安装,当机床尺寸较大 时,给保证加工精度增加了困难。因此,此种布局形式多为中、小型坐 标镗床采用。
a)
图10-22 后单支承孔
b)
2. 后单支承镗模 图10-22所示为采用后单支承镗孔,镗套设置在刀具的后方。用于立镗时, 切屑不会影响镗套。 当镗削D<60mm、L<D的通孔或盲孔时,如图10-22a)所示,可使镗杆导向 部分的尺寸d>D。这种形式的镗杆刚度好,加工精度高,装卸工件和更换刀 具方便,多工步加工时可不更换镗杆。 当加工孔长度L=(1~1.25)D时,如图10-22b)所示,应使镗杆导向部分直 径d<D,以便镗杆导向部分可进入加工孔,从而缩短镗套与工件之间的距离 h及镗杆的悬伸长度L1。 为便于刀具及工件的装配和测量,单支承镗模的镗套与工件之间的距离h一 般在20~80mm之间,常取h=(0.5~1.0)D。
图10-5 卧式坐标镗床