非常好的精益生产案例值得借鉴
非常好的精益生产案例值得借鉴

总结各案例的优点和不足
案例1:优点是 提高了生产效 率,降低了成 本;不足是忽 视了员工培训 和团队建设。
案例2:优点是 实现了精益生产, 提高了产品质量; 不足是忽视了客 户需求和市场变
化。
案例3:优点是 优化了生产流程, 提高了生产效率; 不足是忽视了员 工满意度和员工
流失率。
案例4:优点是 实现了精益生产, 提高了产品质量; 不足是忽视了供 应链管理和供应
商关系。
对其他企业的借鉴意义
精益生产可以提高生产效率,降低 成本
精益生产可以优化生产流程,提高 生产灵活性
添加标题
添加标题
添加标题
添加标题
精益生产可以减少浪费,提高产品 质量
精益生产可以提升员工素质,提高 员工满意度
对未来精益生产的展望
持续改进:不断优化生产流程,提 高生产效率
绿色生产:注重环保和可持续发展, 降低生产对环境的影响
解决方案:加强质量管理,提高员工技能,确保产品质量
问题:库存积压,资金周转困难 解决方案:实施JIT(准时生 产),减少库存,提高资金周转率
解决方案:实施JIT(准时生产),减少库存,提高资金周转 率
问题:员工士气低落,离职率高 解决方案:加强企业文化建设, 提高员工满意度,降低离职率
解决方案:加强企业文化建设,提高员工满意度,降低离职 率
精益生产的核心思想
消除浪费:通过 持续改进,消除 生产过程中的浪 费,提高生产效 率
持续改进:不断 追求更好的生产 方式,持续改进 生产流程
准时生产:根据 市场需求,准时 生产出所需的产 品,减少库存积 压
质量至上:注重 产品质量,追求 零缺陷,提高客 户满意度
精益生产的应用范围
精益生产在中国成功的经典案例
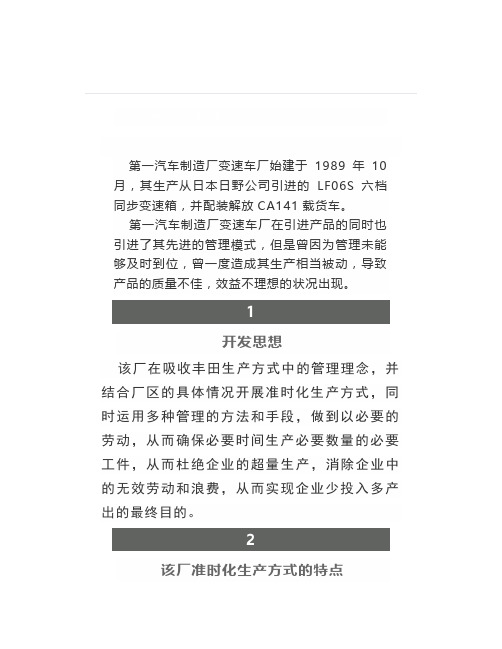
第一汽车制造厂变速车厂始建于1989年10月,其生产从日本日野公司引进的LF06S六档同步变速箱,并配装解放CA141载货车。
第一汽车制造厂变速车厂在引进产品的同时也引进了其先进的管理模式,但是曾因为管理未能够及时到位,曾一度造成其生产相当被动,导致产品的质量不佳,效益不理想的状况出现。
1开发思想该厂在吸收丰田生产方式中的管理理念,并结合厂区的具体情况开展准时化生产方式,同时运用多种管理的方法和手段,做到以必要的劳动,从而确保必要时间生产必要数量的必要工件,从而杜绝企业的超量生产,消除企业中的无效劳动和浪费,从而实现企业少投入多产出的最终目的。
2该厂准时化生产方式的特点01.目标明确,系统性强。
围绕提高产品质量,降低成本,满足市场需求的目标,进行“配套设计,同步实施”的开发与建议方式02.采用“拉动式”生产组织方式。
变“推动式”生产为“拉动式”生产组织方式,以市场需求为目标组织生产03.向工序间在制品为“0”进军。
04.实行“一人多机”操作。
实行U形生产设备布置,“一人多机”操作,大大提高劳动生产率05.工具定置集配,精度刀具强制换刀与跟踪管理。
06.“三为”现场管理。
强调观念更新,以生产现场为中心,生产工人为主体,车间主任为首的“三为”管理体制。
一切后方部门围绕准时化生产服务,使生产不停地创造附加价值07.生产现场实行“5S”活动——整顿、整理、清扫、清洁和素质。
08.实行“三自一控”、“创合格”、“深化工艺”、“五不流”和“产品创优”的“五位一体”的管理体系。
3实施效果经过1年多的实践,准时化生产方式使工厂面貌产生巨大变化。
1、生产能力大幅度提高,实现均衡生产原设计能力 6.8万台/年,92年实施准时化生产后实现8000台/月生产水平。
产品品种由原来1个基本型发展为18个改型产品。
2、产品质量稳步提高 91年废品率下降35%,一次装配合格率由80%提高到92%,市场占有率大幅度提高。
3、推行看板管理,在制品大幅度下降在制品流动资金占用从91年初的700万下降到年底的350万,下降了50%,92年月产量增加了25%,而流动资金下降到300万。
精益生产成功案例
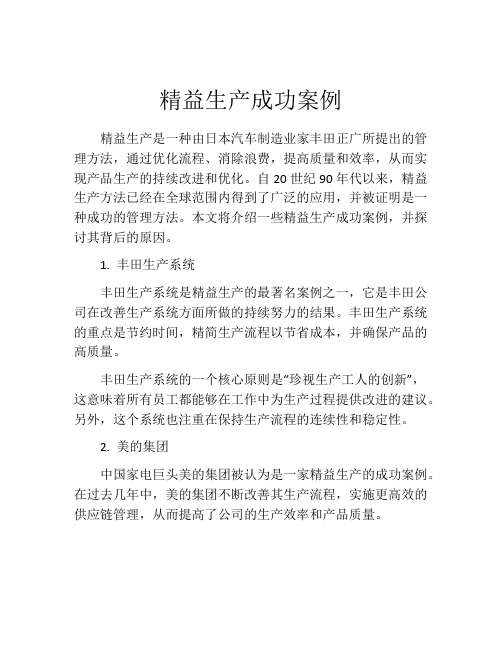
精益生产成功案例精益生产是一种由日本汽车制造业家丰田正广所提出的管理方法,通过优化流程、消除浪费,提高质量和效率,从而实现产品生产的持续改进和优化。
自20世纪90年代以来,精益生产方法已经在全球范围内得到了广泛的应用,并被证明是一种成功的管理方法。
本文将介绍一些精益生产成功案例,并探讨其背后的原因。
1. 丰田生产系统丰田生产系统是精益生产的最著名案例之一,它是丰田公司在改善生产系统方面所做的持续努力的结果。
丰田生产系统的重点是节约时间,精简生产流程以节省成本,并确保产品的高质量。
丰田生产系统的一个核心原则是“珍视生产工人的创新”,这意味着所有员工都能够在工作中为生产过程提供改进的建议。
另外,这个系统也注重在保持生产流程的连续性和稳定性。
2. 美的集团中国家电巨头美的集团被认为是一家精益生产的成功案例。
在过去几年中,美的集团不断改善其生产流程,实施更高效的供应链管理,从而提高了公司的生产效率和产品质量。
美的集团还注重员工的培训和发展,积极实施“知识共享”与“技能传承”等管理模式,使员工能够充分地参与到公司的生产过程中,提高员工的生产效率和质量。
3. GE电气GE电气公司也被视为精益生产管理方法的成功实践者。
GE电气公司致力于优化生产流程,提高生产效率和质量,并减少产品制造过程中的浪费。
GE电气公司采用的精益生产管理方式是“快速反应制造”,即在产品制造过程中遵循快速反应的原则,避免不必要的等待和延迟。
同时,公司还采取了标准化和自动化的生产流程,并专注于对员工进行培训和发展。
以上三个案例展示了在实践精益生产管理方法时所采取的共性策略。
这些成功案例的主要特点包括优化供应链,精简生产流程,采用标准化和自动化的生产技术,培养员工的技能和知识。
另外,这些公司还注重提高产品的质量和关注客户的需求。
总之,精益生产方法已经被广泛证明是一种成功的管理方法。
这些成功案例表明,对于公司而言,采用精益生产方法是提高生产效率和产品质量的一个重要途径,同时,也可以为公司带来更高的效益和利润。
精益生产案例总结借鉴经验

精益生产案例总结借鉴经验精益生产是一项以提高生产效率和质量为目标的管理方法,它在过去的几十年间在许多行业中得到了广泛应用。
以下是几个精益生产案例的总结,从中我们可以借鉴一些经验。
第一个案例是丰田汽车公司。
丰田公司是精益生产的创始者之一,他们的达成了在数量庞大的生产线中实现高效率和高质量的目标。
他们采用了一系列的流程改进措施,以降低生产过程中的浪费,并将线路进行优化。
此外,丰田还通过在员工培训方面投入大量资源,使员工具备了应对问题和改善生产过程的技能。
通过这种方式,丰田成功地提高了生产效率和质量,成为了全球汽车行业的领导者之一第二个案例是麦当劳。
麦当劳是精益生产方法在快餐业中的成功应用者。
麦当劳通过统一的流程和标准化操作来简化操作,减少浪费,并提高工作效率。
他们还利用精益生产的思想来进行菜单设计和供应链管理,以确保食品的质量和服务的一致性。
通过这些措施,麦当劳能够快速地为客户提供高质量的食品和满意的服务。
第三个案例是斯图亚特·麦迪逊酒店。
这家酒店以提供尽可能高效和舒适的服务而闻名。
他们利用精益思维来优化客户服务流程,通过减少等待时间和提高响应速度来提高客户满意度。
酒店还通过减少不必要的库存和降低员工失误率来降低成本。
通过这些改进,斯图亚特·麦迪逊酒店实现了更高的客户满意度和更好的经济效益。
从这些案例中,我们可以总结出一些精益生产的经验。
首先,流程和操作的标准化是关键,这样可以简化操作,减少浪费并提高效率。
其次,员工培训和参与是至关重要的,员工需要具备改进生产过程的技能和意识。
第三,持续改进是一项重要的工作,公司需要不断地寻找和解决问题,以进一步提高生产效率和质量。
最后,客户需求应始终放在首位,公司需要根据客户需求进行产品和服务的设计和提供。
在实践中,每个组织都可以根据自己的需求和情况进行精益生产的应用。
通过借鉴成功案例的经验并灵活运用其核心原则,可以帮助组织实现更高的效益和更好的竞争力。
精益求精的案例
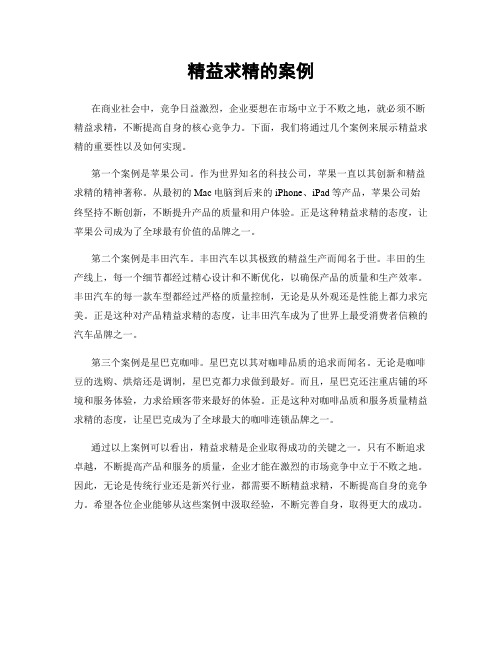
精益求精的案例
在商业社会中,竞争日益激烈,企业要想在市场中立于不败之地,就必须不断精益求精,不断提高自身的核心竞争力。
下面,我们将通过几个案例来展示精益求精的重要性以及如何实现。
第一个案例是苹果公司。
作为世界知名的科技公司,苹果一直以其创新和精益求精的精神著称。
从最初的Mac电脑到后来的iPhone、iPad等产品,苹果公司始终坚持不断创新,不断提升产品的质量和用户体验。
正是这种精益求精的态度,让苹果公司成为了全球最有价值的品牌之一。
第二个案例是丰田汽车。
丰田汽车以其极致的精益生产而闻名于世。
丰田的生产线上,每一个细节都经过精心设计和不断优化,以确保产品的质量和生产效率。
丰田汽车的每一款车型都经过严格的质量控制,无论是从外观还是性能上都力求完美。
正是这种对产品精益求精的态度,让丰田汽车成为了世界上最受消费者信赖的汽车品牌之一。
第三个案例是星巴克咖啡。
星巴克以其对咖啡品质的追求而闻名。
无论是咖啡豆的选购、烘焙还是调制,星巴克都力求做到最好。
而且,星巴克还注重店铺的环境和服务体验,力求给顾客带来最好的体验。
正是这种对咖啡品质和服务质量精益求精的态度,让星巴克成为了全球最大的咖啡连锁品牌之一。
通过以上案例可以看出,精益求精是企业取得成功的关键之一。
只有不断追求卓越,不断提高产品和服务的质量,企业才能在激烈的市场竞争中立于不败之地。
因此,无论是传统行业还是新兴行业,都需要不断精益求精,不断提高自身的竞争力。
希望各位企业能够从这些案例中汲取经验,不断完善自身,取得更大的成功。
非常好的精益生产案例-值得借鉴

32246.70
27409.69
26514.19
31757.05
26993.49
需做辅助工作:每完成20个需翻转,100个需打包
27000 26500 26000 25500 25000 24500 24000 23500 23000
65#平均每天产量(pcs)
24122 WK32
提高 MORE 产品产量
是否可以把脚踏板的动作变为自动呢?
措施一:
脚踏板改为自动(短路)状态。
机器异常时及换胶试胶时无法实行!
措施二:
脚踏板改为自动与手动两种状态。
正常时自动状态,异常时手动状态。
针对H/A工位我们采取措施二:
时间:WK33 地点:W-3 ASM 负责人:谢xx
前改善后
脚踏板用脚踩
脚踩踏板改为自动后:
0.26秒 脚踩踏板
2440
产能(pcs)
25042
25033
8.22 2240 23032 2050 2440 25082
8.23 2190 22473 2600 2440 25073
30000
实际产量(pcs) 耽搁产量(pcs)
25000 7050 4850 2050 2600
50
3320
20000
15000
10000
H/A
65#各工位单件工时(秒)
4.54
4.61
4.04
A2SK
SBB
下工装
时间:WK32 地点:W-3 ASM 负责人:黄xx
由65#各工位的单件工 时可以看出:H/A工位单 件工时为最高,平均在 4.95秒完成一个HGA。 因此H/A工位是我们提
高产量的最大障碍!
精益生产案例总结:借鉴经验,成功复制
精益生产案例总结:借鉴经验,成功复制精益生产案例总结:借鉴经验,成功复制精益生产是一种优化生产流程和提高生产效率的方法,最初由日本的丰田汽车公司推广。
其主要思想是通过消除浪费,增加价值创造活动,提高效率和质量。
在丰田公司的带领下,许多公司纷纷效仿,通过精益生产方法提高自身的竞争力。
本文将介绍几个成功利用精益生产方法提高效率和质量的案例。
这些案例的共同点是他们来自不同领域,但是都成功地应用了精益生产方法,并在他们的业务范畴中获得了显著的成功。
CASE1: 丰田汽车公司丰田是精益生产方法的创始者和领跑者。
丰田公司将精益生产方法运用到生产流程的每个阶段中,消除任何不必要的浪费并增加价值创造活动,以此实现最高效的生产方式。
丰田的精益生产方式的成功之处在于它更加注重员工的参与和追求完美,这也是取得成功的最大关键。
CASE2: 康泰纳仕康泰纳仕公司是一家颇具规模的人力资源公司,他们在促进员工满意度的过程中成功地应用了精益生产方法。
康泰纳仕通过为员工提供培训和支持以及清晰的沟通和指导,使员工将自己的知识和技能应用于最需要的工作中。
同时,通过利用一些自动化清晰的流程,康泰纳仕成功地提高了生产效率和质量。
经过这些努力,康泰纳仕公司的员工忠诚度大大提高,生产效率和质量明显提高。
CASE3: 通用电气公司通用电气公司是一家全球化的企业,在生产面板、电气和照明等领域占据一席之地。
为了提高生产效率和质量,通用电气公司采用了精益生产方法,实现了自动化流程并加强了员工参与和培训。
使用这种方法,通用电气公司在其产品的生产质量上获得了显着的改善。
同时,通过消除浪费和减少存货,通用电气公司极大地降低了成本并提高了赢利。
CASE4: 伯克希尔·哈撒韦公司伯克希尔·哈撒韦公司是由亿万富翁沃伦·巴菲特创建的,该公司在多个行业领域拥有多个品牌。
伯克希尔·哈撒韦公司通过采用精益生产方法,消除了生产流程中的何浪费,并努力实现生产流程的自动化。
非常好的精益生产案例值得借鉴
非常好的精益生产案例值得借鉴前言精益生产是一种专注于提高效率和降低浪费的经营管理方法。
通过消除不必要的步骤和资源浪费,精益生产可以帮助企业实现更高的产出和更好的质量,从而获得竞争优势。
本文将介绍一些非常好的精益生产案例,展示出这种方法的实际应用和可行性,以供其他企业借鉴。
案例一:丰田汽车丰田汽车是精益生产的经典案例之一。
丰田公司以“丰田生产方式”(Toyota Production System,TSP)闻名于世。
TSP 的核心思想是通过限制生产速度来提高质量,消除浪费和降低成本。
丰田将员工视为最重要的资源,鼓励员工参与改进流程,并不断学习和提高。
通过实施流程改进和标准化操作,丰田成功地降低了库存水平、缩短了交付周期,并提高了产品的质量。
流程改进丰田汽车通过实施精细的生产计划和精确的生产控制来改进流程。
他们使用所谓的“拉动式生产”(Pull Systems),这意味着生产进程只会在下一阶段需要材料和部件时才会启动,以此保持生产流程的稳定性。
这种方式可以防止过度生产和库存积压,并减少浪费。
标准化操作丰田汽车非常注重标准化操作。
他们制定了详细的作业指导书,确保每位员工都能按照标准程序工作。
通过标准化操作,丰田能够减少错误和变量,并提高整体生产效率。
标准化操作还使得员工之间可以互相替代,以应对人员变动和流程变化。
持续改进丰田汽车秉持着“持续改进”的信念。
他们鼓励员工积极参与改进流程,并通过小改进和创新来不断提高生产效率和质量。
丰田实行所谓的“就地解决问题”(Genchi Genbutsu),即员工应该亲自去现场了解问题并找到解决方案。
这种方法帮助丰田构建了一个持续改进的文化,使得所有员工都在努力寻找问题并付诸行动。
案例二:美国空军美国空军也是一个非常成功的精益生产案例。
空军一直致力于在各个领域实施精益生产,以提高效率、降低成本,并最大限度地满足任务需求。
下面将以飞机维修作业为例,介绍空军如何运用精益生产方法改进维修流程:改进维修流程空军通过改进维修流程来提高效率。
四个小故事讲透了精益生产质量管理
四个小故事讲透了精益生产质量管理1、割草的男孩一个替人割草打工的男孩打电话给一位陈太太说:“您需不需要割草?”陈太太回答说:“不需要了,我已有了割草工。
”男孩又说:“我会帮您拔掉花丛中的杂草。
”陈太太回答:“我的割草工也做了。
”男孩又说:“我会帮您把草与走道的四周割齐。
”陈太太说:“我请的那人也已做了,谢谢你,我不需要新的割草工人。
” ,男孩便挂了电话,此时男孩的室友问他说:“你不是就在陈太太那割草打工吗?为什么还要打这电话?”男孩说:“我只是想知道我做得有多好!”【启示】这个故事反映了ISO的第一个思想,即以顾客为关注焦点,不断地探询顾客的评价,我们才有可能知道自己的长处与不足,然后扬长避短,改进自己的工作质量,牢牢的抓住顾客。
这也是质量管理八项原则第6条:“持续改进”思想的实际运用的一个例子。
我们每个员工是否也可结合自己的岗位工作,做一些持续改进呢? 所有的员工都可以做到让顾客满意。
对于营销人员来说,这样是可以得到忠诚度极高的顾客。
对于我们每个员工来说,只有时刻关注我们的“顾客(服务对象)”我们的工作质量才可以不断改进。
这也是沟通的问题,一个人想得到公正、客观的评价真的好难。
这个故事是否为我们提供了一个好的方法呢?做质量的大多数时候都是被动的,只是延续出现问题然后再去解决问题的模式,如果能主动查找问题并解决问题那才是完美的质量管理模式。
这也就显示出了一个质量管理者的精髓所在。
一切都属于那些天天做好准备的人。
不要光想着天上能下钞票雨,那是不可能的,凡事靠脑子去想,用双手去做,把不应该发生的事情,提前预防,把不良的缺憾扼杀在萌芽状态。
我们要始终坚信“风险是可以防范的,缺陷是可以预防的”!2 、降落伞的真实故事这是一个发生在第二次世界大战中期,美国空军和降落伞制造商之间的真实故事。
在当时,降落伞的安全度不够完美,即使经过厂商努力的改善,使得降落伞制造商生产的降落伞的良品率已经达到了99.9%,应该说这个良品率即使现在许多企业也很难达到。
精益生产案例
精益生产案例引言精益生产是一种通过最大限度地减少浪费,提高生产效率和产品质量的方法。
它始于丰田生产系统,如今已经被广泛应用于各种行业和组织中。
本文将介绍三个精益生产的案例,以展示其在不同领域的应用。
案例一:汽车制造在汽车制造业中,精益生产被广泛用于提高生产效率和降低成本。
丰田汽车公司是精益生产的典型代表之一。
他们采用了精益生产的原则和技术,通过提高生产线的流程效率,使得汽车制造过程更加高效和可持续。
丰田的生产线采用了“单件流水线”模式,每个工人都负责完成整个工作过程,从而减少了不必要的等待和处理时间。
此外,丰田还推崇“质量至上”的原则,通过在每个生产环节中设置严格的质量控制标准,确保产品质量。
另一个值得注意的案例是日本的一个零件制造公司。
该公司通过消除浪费和优化工作流程,成功地提高了生产效率。
他们分析了原本复杂的生产流程,将其简化为一系列简单的步骤,让每个工人都能清楚地知道自己的工作内容和目标。
案例二:医疗服务精益生产同样适用于医疗服务行业。
一个典型的案例是德国某医院的急诊科。
该医院采用了精益生产的原则和工具,通过优化流程和增加资源的使用效率,将就医时间缩短了70%。
在过去,患者在急诊科等待就医时间往往较长。
该医院通过对患者流程进行重新设计,将患者按照病情严重程度进行分类,并在每个分类中设置不同的诊疗团队。
这样,医护人员可以更有效地处理患者,避免了等待时间过长的问题。
此外,该医院还引入了标准化的医疗流程,并充分利用ICT技术,提供了在线预约、电子病历等便捷服务。
这些措施不仅提高了医疗服务的质量,也提高了患者的满意度。
案例三:酒店管理精益生产的原则也可以应用于酒店管理领域。
一个例子是一家高端度假村酒店。
这家酒店通过精益生产的方法,优化了业务流程,提高了客户满意度,并在市场上取得了成功。
首先,酒店管理团队对酒店的工作流程进行了深入分析,并找出了其中的浪费和问题。
然后,他们采取了一系列措施,如优化客房清洁流程、提高服务质量等。
- 1、下载文档前请自行甄别文档内容的完整性,平台不提供额外的编辑、内容补充、找答案等附加服务。
- 2、"仅部分预览"的文档,不可在线预览部分如存在完整性等问题,可反馈申请退款(可完整预览的文档不适用该条件!)。
- 3、如文档侵犯您的权益,请联系客服反馈,我们会尽快为您处理(人工客服工作时间:9:00-18:30)。
平均每天产量(pcs)
23955.2
23935.7
23714.3
52#
79#
65#
提高 MORE 产品产量
二班倒产量目标(pcs)
23150.5
常生产 返修物 料,换 料频繁
20311.7
80#
74#
由WK32 MORE 五条 二班倒的线 每天平均产 量中可看出 :65#机器、 设备相对较 稳定,在五 条线中处于 中间状态, 于是选择提 高65#产量为 我们此次的
ONE ASM
------提高 MORE 产品产量 提高 MORE 产品产量
小组介绍
小组名称:更多
小组课题:提高 MORE产品产量
成立时间:2007.08.01
所属工序:One ASM
小组成员:10人 会议次数:12次 出 席 率:98% 指导员:黎x
提高产 量创 造价值
我们的口号:
146400
4.61
31757.05
26993.49
下工装
146400
4.04
需做辅助工作:每完成20个需翻转,100个需打包
27000 26500 26000 25500 25000 24500 24000 23500 23000
65#平均每天产量(pcs)
24122 WK32
提高 MORE 产品产量
产能(pcs)
24113
24145
24132
25000
2300
0
0
20000
8.08 2440 24146
0 2440 24146
0
8.09 2440 24102
0 2440 24102
0
8.10 2420 23948 150 2440 24098
平均 2397.5 23714.3 408.3 2440.0
20 19 20 19 20 20 20 20 20 20 19 19
吴xx
提高 MORE 产品产量
9
要因分析(二)
65#各工位单件工时:
工位 ILS/K 点胶 A2SK 焊接
1
4.76 4.58 4.45
2
4.97 4.35 4.69
减少车间违规 控制辅料浪费
紧解参影期 急决与响待 程能范力效 度力围度果
4
45
4
5
34544 34433 23323
WK32生产计划表:
PLAN
2 shift
Day
10
Night
9
TTL(team) 19
Day
7
3 shift
Mid
6
Night
7.5
ቤተ መጻሕፍቲ ባይዱ
TTL(team) 20.5
TTL TEAM
39.5
组长 郑xx
发表员 制表员 指导员 跟踪员 实施员 实施员 工程师 培训员 IE人员
许x 谢xx 黎x
高xx 吴xx 廖x
华x
雷xx 黄xx
提高 MORE 产品产量
2
工序介绍
ASM流程介绍
下工装
焊接
金属支架 上工装
点胶
装配第一工位
磁头上工装
提高 MORE 产品产量
3
主题选定(一)
项目
评分
提高产品产量 提高合格率
6 23955.17
79# 143614
6 23935.67
65# 142286
6 23714.33
80# 138903
6 23150.50
74# 121870
6 20311.67
25000 24500 24000 23500 23000 22500 22000 21500 21000 20500 20000
主题!
机器、设备不 稳定常修机
5
现状把握
WK32 65#每天产量、工作时间及产能:
日期 实际生产时间(分)
实际产量(pcs) 修机耽搁产量(pcs)
总生产时间(分)
8.05 2205 21813 2300 2440
8.06 2440 24145
0 2440
8.07 2440 24132
0 2440
26500 WK43
目标:65#平均 每天产量从
WK32的24.1K提 高到WK43的 26.5K
7
活动计划
:计划
★ :实际
活动步骤
负责 人
WK WK WK WK WK WK WK WK WK WK WK WK WK WK WK WK WK WK WK 31 32 33 34 35 36 37 38 39 40 41 42 43 44 45 46 47 48 49
工位 生产时间(秒) 单件工时(秒) 产量(PCS) 除充裕率1.15后产量 平均产量
ILS/K
146400
4.05
需做辅助工作:每完成一盒36个需开盒子
点胶 A2SK
146400 146400
4.95 4.54
29575.76 32246.70
25139.39 27409.69
26514.19
焊接
小组介绍 全体 ★
主题选定 谢\高 ★
现状把握 谢\吴
★
目标设定 全体
★
活动计划 高
★
原因分析 全体
★
★
★
制定对策 全体
★
★
★
实施对策 全体
★★ ★ ★★★★★★★
效果确认 高\谢
★
★ ★★★★★
★
巩固标准 全体
★★★★★
活动总结 全体
★★
今后计划 全体
★
提高 MORE 产品产量
8
要因分析(一)
影响产量的因素
ACT 10 9 19 7 6 7.5 20.5 39.5
LESS 1.5 1 2.5 4 4 3.5 11.5 14
LOW 3 2 5 1 0 2 3 8
上合 司计 方分 针数
4 26
3 23 3 20 3 16
0
MORE 5.5 6 11.5 1 1 1 3 14.5
提高 MORE 产品产量
反对
人
精神不好 情绪不佳
新操作员
机
机器不稳定 单件工时过长
料
换料频繁 返修料 Slider少数多
来料不良多
未合理利用时间
未合理合并 同时操作
法
工装少 辅助工作多
other
WK32各CELL的工装数量
TEAM 公司计划 CELL工装(pcs) 工装数
52#
CELLA
24
20
CELLB
24
19
65# 79# 78# 74# 85# 76# 负责人
1
不表态
2
通过
3
赞成
4
特别赞成 5
10
20
30
通过二员表可看出 提高产量的分数最 高,由计划部的生产 需求中得出,MORE产 品的计划产量最大, 因此我们选它做本
次的主题!
4
主题选定(二)
WK32 MORE各线每天平均产量:
生产线 WK32总产量(pcs)
生产天数(天) 平均每天产量(pcs)
52# 143731
24122.7
150
408.3
15000 10000
21813
24145
24132
24146
24102
23948 23714.3
5000
0
8.05
8.06
8.07
8.08 日期
8.09
8.10
平均
提高 MORE 产品产量
6
(pcs)
目标设定
我们以各工位单件工时及充裕率1.15设定目标(ILS/K与下工装工位因辅助工作较多不能以单件工时算)