精益生产(IE)计算器-完整版全中文
精益生产改善方案(精益生产改善方案)IE标准时间管理程序
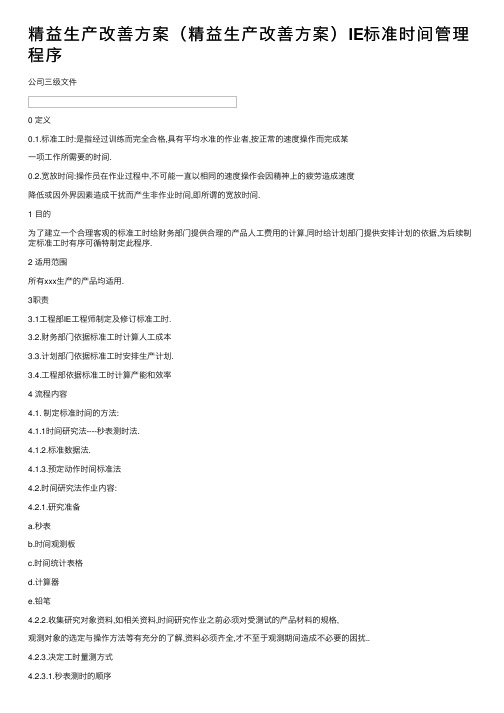
精益⽣产改善⽅案(精益⽣产改善⽅案)IE标准时间管理程序公司三级⽂件0 定义0.1.标准⼯时:是指经过训练⽽完全合格,具有平均⽔准的作业者,按正常的速度操作⽽完成某⼀项⼯作所需要的时间.0.2.宽放时间:操作员在作业过程中,不可能⼀直以相同的速度操作会因精神上的疲劳造成速度降低或因外界因素造成⼲扰⽽产⽣⾮作业时间,即所谓的宽放时间.1 ⽬的为了建⽴⼀个合理客观的标准⼯时给财务部门提供合理的产品⼈⼯费⽤的计算,同时给计划部门提供安排计划的依据,为后续制定标准⼯时有序可循特制定此程序.2 适⽤范围所有xxx⽣产的产品均适⽤.3职责3.1⼯程部IE⼯程师制定及修订标准⼯时.3.2.财务部门依据标准⼯时计算⼈⼯成本3.3.计划部门依据标准⼯时安排⽣产计划.3.4.⼯程部依据标准⼯时计算产能和效率4 流程内容4.1. 制定标准时间的⽅法:4.1.1时间研究法----秒表测时法.4.1.2.标准数据法.4.1.3.预定动作时间标准法4.2.时间研究法作业内容:4.2.1.研究准备a.秒表b.时间观测板c.时间统计表格d.计算器e.铅笔4.2.2.收集研究对象资料,如相关资料,时间研究作业之前必须对受测试的产品材料的规格,观测对象的选定与操作⽅法等有充分的了解,资料必须齐全,才不⾄于观测期间造成不必要的困扰..4.2.3.决定⼯时量测⽅式4.2.3.1.秒表测时的顺序a.分解观测对象的作业即分成若⼲(操作单元)b.依照作业顺序把(操作单元)之要素记⼊时间研究表格中.c.在时间表格上记载必要事项.d.使⽤夹⼦将研究表格夹在观测板上.e.把秒表置于观测板上.f.仔细观察操作员作业.g.启动秒表.h.把最初的操作单元观测时间尽快积在研究表格上.i.依照顺序对所有(操作单元)展开观测.j.重复进⾏h⾄j的动作⼏遍k.整理观测结果,计算各(操作单元)所需的时间.4.2.3.2.时间观测归纳有四⼤要项a.⼀边观察操作者的动作.b.同时利⽤秒表测出各(操作单元)所需时间.c.再记⼊研究表格中.d.外来单元需记⼊时间记录表格中.4.2.3.3归纳数据根据时间研究统计表格统计并记录数据进⾏处理.通常在整个观测过程中,会因测时⼈员的疏失,不熟练或外来因素,如换模具,更换测试线和测试程序,班长询问等造成作业的延迟,这些数值必须作特殊记录并归纳为外来单元.4.2.3.4.抛丢异常值对上述归纳之数据进⾏资料分析,将异常数据予以抛丢,再将抛丢异常值后所剩的有效样本值求其平均值.4.2.3.5.决定评⽐值.a.意义:评⽐是⼀中判断或评价的技术,⽬的在实际的操作时间在正常标准的⼯作环境之下调整⾄正常速度的基准.b.实施时间:观测各操作单元⼯时,必须同时依实际操作情况给以评⽐.c.⽅法:评⽐⽅法中最为⼴泛应⽤的为”平准化法”此法系以熟练,努⼒,⼯作环境和⼀致性四项为主要的衡量因素,每个评⽐因素再分成若⼲程序的等级,各等级予以因定⽽适当的系数,评⽐时将各因素的系数相加即得评⽐系数.通常(⼀致性)与(熟练性)近似相关.可并⼊(熟练)因素中考虑.⽽(⼯作环境)在评⽐时⼀般视为(平均),其调整通常并在(宽放)中,严格说来,只需评⽐(熟练)及(努⼒)两项因素.4.2.3.6.决定宽放值A. 意义:操作员在作业过程中,不可能⼀直以相同的速度操作,会有⼲扰或因精神上的疲劳,造成速度降低.这些(⾮作业)时间就是所谓的 (宽放时间)B. 宽放时间的种类:可分为⼀般宽放及特殊宽放.a.⼀般宽放时间可分为:私事,疲劳,作业三种a).私事宽放---例如:喝⽔等⽅⾯的宽放时间.b).疲劳宽放---恢复疲劳所必需的休息时间.c).作业时间---进⾏作业时发⽣的⼩事,例如作业前的准备⼯作台的清理.b.特殊宽放时间分为管理,⼩组,特殊⼲扰等.a).管理宽放:上班时间管理问话等情况所造成的⼲扰.b).⼩组宽放:⼩组⼯作中作业员碰到⼀时没有⼯作的情况.c) 特殊宽放:例如⼀个作业者同时操作多台机器或测试设备,因顾及某台机器或设备⽽造成其它机器空转或停⽌等待,这种时间就是机器或设备⼲扰的宽放.c.宽放时间的求法a).⼀般宽放率的范围在10%~17%观测⼈员可依据被观测⼈员的实际作业情况给予宽放率.b) 宽放时间=实际时间*宽放率C. 宽放取值标准a.私事宽放3%~5%.b.疲劳宽放5%~7%.c.作业宽放2%~3%.4.2.3.7制定标准⼯时标准⼯时:测量时间*(1+评⽐%)*(1+宽放率%)4.2.3.标准⼯时的发⾏:标准⼯时经IE⼯程师制定完成后经相关⼈员审核,核对后发⾏给相关部门..4.2.4. 标准⼯时的修订4.2.4.1.当制程变更,⼯艺更改或新产品试产后,由IE⼯程师给予修订.4.2.4.2.正常⽣产的产品每三个⽉进⾏更新⼀次。
精选精益生产与IE培训课件
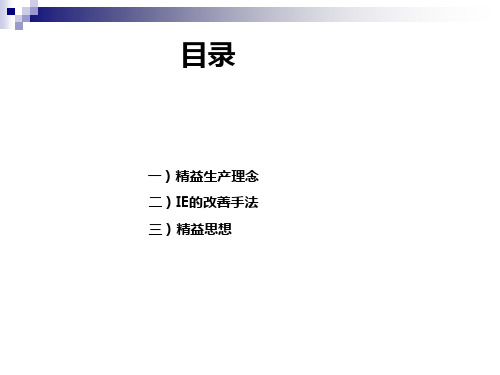
原則9:尽可能采用下滑式运送装置。
动改法---有關工具設備之原則
原則10:尽量以足踏/夾具替代手之工作。 例:缝纫机。
原則11:尽可能將二種工具合並。
例:两用钉锤,双头板手,附橡皮之铅笔。
原則12:工具、物料預放在工作位置(例:目視工具定位板)。 原則13:以手指負荷能力分配工作。
搬运
检验
储存
动改法
运用動作經濟原則::
人体運用方面的原則5項。 工作場地的布置與環境之原則4項。 作用: 減少操作人員的疲勞。 縮短操作人員的操作時間。 提高工作效率。
动改法---有關人体運用的原則
原則1:兩手同時開始及完成動作(例:試想獨臂作業)。 原則2:除休息時間外,兩手不應同時空閑。 原則3:兩臂的動作應反向同時對稱。(左手拾螺丝,右手拾
怎样做呢? ---消除浪费,追求真正的效率
精益生产追求的目标
零 7个“
”目标
☆ 零切换浪费 ☆ 零库存 ☆ 零浪费 ☆ 零不良 ☆ 零故障 ☆ 零停滞
☆ 零事故
2. 理想的精益生产系统
传统的效率是: 简单化 高速大量生产
生产过剩是 最大的浪费
同步化 均衡化 柔性化
精益生产的效率是: 增加有价值的活动 消除浪费
復制原理: 同一工作,如需做二次以上,最好以方式達成。 例:复写纸/印章
層別原理: 線條粗細,不同的顏色。 例:特別管制線/制服颜色不同。
警告原理: 以聲光等方式发出各种讯号。 例:自動報警燈/Open/Short測試的報警。
緩和原理: 以各种方法来减少错误发生后造成的损害,
虽然不能避免错误的发生,但能减少损害的程度。 例:鸡蛋隔层装运盒/安全带/安全帽。
IE计算公式
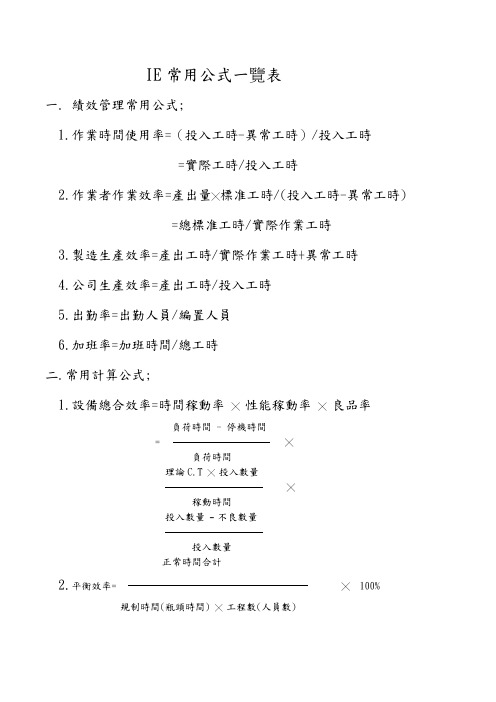
IE常用公式一覽表
一. 績效管理常用公式;
1.作業時間使用率=(投入工時-異常工時)/投入工時
=實際工時/投入工時
2.作業者作業效率=產出量╳標准工時/(投入工時-異常工時)
=總標准工時/實際作業工時
3.製造生產效率=產出工時/實際作業工時+異常工時
4.公司生產效率=產出工時/投入工時
5.出勤率=出勤人員/編置人員
6.加班率=加班時間/總工時
二.常用計算公式;
1.設備總合效率=時間稼動率╳性能稼動率╳良品率
負荷時間- 停機時間
= ╳
負荷時間
理論C.T ╳投入數量
╳
稼動時間
投入數量–不良數量
投入數量
正常時間合計
2.平衡效率= ╳100%
規制時間(瓶頭時間) ╳工程數(人員數)
1.時間利用率
實際作業時間
總投入時間
2.作業效率
總標準工時
總實際工時
單位時間實際產出標準人數
標準產出實際人數
實際作業時間內之效率指針
3.生產效率
生產效率= 作業效率x 時間利用率
單位時間實際產出標準人數
標準產出實際人力總標準時間總投入時間
總投入時間內之效率指針(含除外工時在內)
1.生產線平衡率
T1+T2+T3+…+T n
n.T m a x
T m a x﹕瓶頸工時
2.平衡率提升途徑
1.合併
2.重排
3.取消
4.簡化。
IE标准工时及产能计算表

间接人力(人)
线长/物料员
全能员
维修员
工作时间
0.00 节拍
10 标准时间
0.00 预定效率 直通率
#DIV/0! 标准产能
目标产能
0 注:1.各工站宽放率为10%;
0.00 2.标准工时=观测时间×评定系数×(1+宽放率);
3.瓶颈工时为所有工序中标准工时最大值;
4.标准时间为各站标准工时之和;
5.产线平衡率=各工序标准工时和/(最长工序时间×总人数); 7.不平衡损失=瓶颈工时×总人数-各工序(每人)时间之和;
0.00
10
0.00
#DIV/0!
7
0.00
10
0.00
#DIV/0!
8
0.00
10
0.00
#DIV/0!
9
0.00
10
0.00
#DIV/0!
10
0.00
10
0.00
#DIV/0!
11
0.00
10
0.00
#DIV/0!
12
0.00
10
0.00
#DIV/0!
13
0.00
10
0.00
#DIV/0!
14
0.00
10
0.00
#DIV/0!
23
0.00
10
0.00
#DIV/0!
24
0.00
10
0.00
#DIV/0!
25
0.00
10
0.00
#DIV/0!
26
0.00
10
0.00
#DIV/0!
27
0.00
精益生产培训资料 - 工具篇(ie)

(2)原理 模特法的基本原理基于人机工程学的实验,归纳如下: 1)所有人力操作时的动作,均包括一些基本动作。 2)不同的人做同一动作(在条件相同时)所需的时间值基本相等。 3)使用身体不同部位动作时,其动作所用的时间值互成比例。
(3)特点 1 模特法把生产实际中操作的动作归纳为21种。 2 模特法把动作符号与时间值融为一体。 如移动小臂取有定位的螺钉,在模特法中用M3G3表示,其中M3表示小臂的移动,G3 表示复杂的抓取,M3G3时间值是6MOD,时间为6*0.129秒=0.774秒
作业测定的主要方法及其对应的应用阶次可列表如下:
① 第一阶次:动作 — 基本动作测定的最小工作阶次。 ② 第二阶次:单元 — 由几个连续动作集合而成。 ③ 第三阶次:作业 — 通常由两到三个操作集合而成。若将其分解为两个以
上的操作,则不能分配给两个以上的人以分担的方式进行作业。 ④ 第四阶次:制程 — 指为进行某种活动所必须的作业的串连。
(2)人因工程的目的: A. 使人工作地更有效 B. 使人工作地更安全 C. 使人工作地更舒适
2、作业测定
是指运用各种技术来确定合格工人按规定的作业标准,完成某项工作所需的时
间。它是在方法研究的基础上,对工作细节进行分析并制定标准时间的一种方法。
1)标准时间的构成
观察时间
评比因素
私事 宽放
疲劳 宽放
a)辅助性(6个):寻找、选择、检查、持住、定位、预定位 b) 消耗性(4个):休息、故延、迟延、计划 2)目视动作分析:分析者直接 观测实际的作业过程,并将观察到的情况进行记录 的一种分析方法。 3)影片分 析:通过录像和摄影记录作业的实施过程,再通过放影、放像的方法观 察和分析 作业动作的方法。
延迟 宽放
精益术语-IE
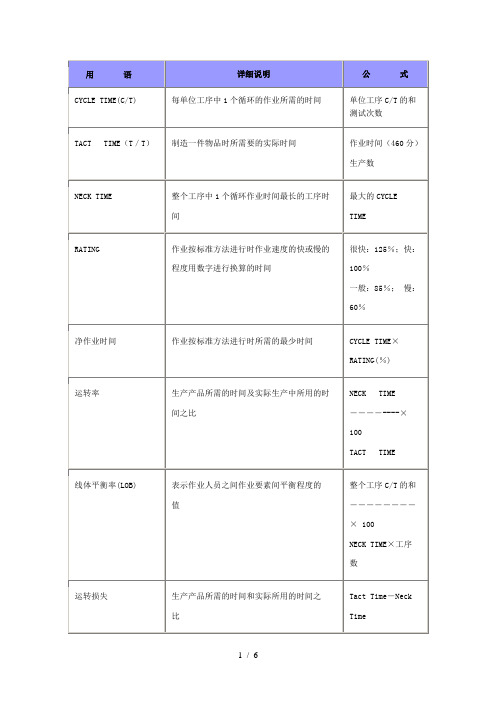
* 作业效率
标准工时
可用工时-损失工时
MTM (Motion-Time Measurement Or Methods-Time Measurement)
所有作业用基本动作来分析,根据指定的基本动作的性格和条件提前给予时间的方法
TMU (time-measurement unit)
给予基本动作的时间值的单位
1分=1.667TMU
1秒=27.8TMU
R.W.F (Ready-Work Facfor)
所有动作分八个基本要素,每执行一个要素动作时根据动作的困难决定W/F数,根据时间表计算净作业时间的方法
1RU=0.001分
基本动作分析法
利用科学家研究出来的17个动作符号测试作业动作时尽量以最小单位来分割的方法
-----------×100
TACT TIME
效率损失
按标准方法进行作业时需要的最少时间和与实际作业中所用的时间之差的比
Cycle Time-净作业时间
-----------×100
TACT TIME
综合损耗
损耗的总合计
运转损失+平衡损失+效率损失
综合能力
按标准方法进行作业时需要的最少时间和与实际生产所用的时间之差的比
很快:125%;快:100%
一般:85%; 慢:60%
净作业时间
作业按标准方法进行时所需的最少时间
CYCLE TIME×RATING(%)
运转率
生产产品所需的时间及实际生产中所用的时间之比
NECK TIME
--------× 100
TACT TIME
线体平衡率(LOB)
表示作业人员之间作业要素间平衡程度的值
IE生产效率管理和人员计算
11
总实际工作时间
总实际工作时间是生产现场每名员工工作时间的合计
在工作时间当中,设备故障、品质不合格、发生异常等现 象所浪费的时间全部包含在内。
为了提高生产效率,就要改善这些异常,使实际工作时间 降低。
为了掌握准确的总实际工作时间,我们现在要导入《时间 记录表》
2019年11月16日10时0分
12
时间管理 时间记录目的是掌握直接、准直接人员的工作时间
班长负 责每日
记录
2019年11月16日10时0分
工作人员(包括班长)A 550 120 130
缺勤人员
B 53 10 12
出勤人员 C=A-B 497 110 118
出勤率 D=(A-B)/A*100% 90.36 91.67 90.76
13
时间管理 车间实施全员的生产性提高
车间 基点 实施 倍率
A
根据班 组的记 录进行 统计
当月 总工 作时 间B
当月 总加 工时 间C
当月实施 基点总工
倍率
作时间
D=B/C E=A*C
生产性提 高率
F=(E-B) /E
C不变
车间对 数据统 计确认
2019年11月16日10时0分
14
总加工时间
总加工时间可以说是制造产品所必须花费的时间的合计
06年目标
日产柴BM
4
零部件
直接人员
生产效率提高的目标
修正 10%
辅助 8.6%
1.6 倍
等待 27.3%
步行 搬运
9.1%
100人
主
体 作
45%
业
34.3%
3.1
精益生产管理培训课件IE(工业工程)及改善技巧
设施规划与物流分析
内
现代制造工程
生产及其制造
容
系统工程
生产计划与控制
质量管理与可靠性
体
工程经济
现代经营工程
系
工业设计 企业战略管理
工业系统分析
量化分析方法
3
方法与技术
计算机系统技术
IE产生的历史背景
189 190
管 古0典管0理
理 理 论
理论阶段
科一 组 学般 织 管管 理
理理 论
理
192
194
0
195 196 197 198 199
0
0
0
0
0
CPC PDM
CE TQM CAE PRM CAE MRPII CIMS MRP CAD/CAM CAPP
CAD FMC N C
IE的历史
年代 第一期 (19世纪中后期)
第二期 (19世纪末期)
第三期 第二次世界大战期间
第四期 第二次世界大战后
人员
E. WHITNEY
14
IE工业工程师的工作职责
1) 提高生产效率 2) 降低不良率 3) 减少物料的转运 4) 控制WIP的数量 5) 消除等待时间 6) 降低库存数量 7) 缩短换模(线)时间(其核心思想是把内部时间尽量转化外部准备时间,其
二尽量取消调整时间,如缺口螺丝,卡口垫片的设计.)
8) 降低物料的消耗 9) 减少动作的浪费
➢提高作业附加价值; ➢改善作业不平衡状况 。
➢掌握人员和设备的运作能力; ➢为制定标准工时提供依据。;
➢发现并消除损耗时间; ➢评价设计及制造方式的改善程度; ➢作为生产各项计划和制定成本、单价的基础。
➢提高设备利用稼动率
(2020)精益生产改善方案(精益生产改善方案)IE应用(精益生产改善方案)IE技术如何提高生产效率国标GB
精益生产改善方案(精益生产改善方案)IE應用(精益生产改善方案)IE技術如何提高生產效率国标GB讲师:()一、工业工程(I E-Industrial Engineering)的内涵与应用(一)工业工程之定义与内涵Industrial Engineering is concerned with the design, improvement, and installation of integrated systems of people, materials, information,equipment, and energy. It draws upon specialized knowledge and skill in the mathematical, physical, and social sciences together with the principles and methods of engineering analysis and design to specify, predict, and evaluate the results to be obtained from such systems.~ IIE-Institute of Industrial Engineering ~美国工业工程协会之定义:工业工程系有关设计、改进及建立包括人员、物料、信息、设备、能源的整合系统;其系利用数学、物理学、社会科学中的专门知识与技术以及工程分析、工程设计的原理与方法,去确立、预测及评估系统之结果。
(二)I P O系统管理模式Feedforward 前馈Feedback 返馈因(三)IE 机制建立(a) 基本业务(Primary Activities)(b) 工程业务(Engineering Activities)(c) 咨询业务(Consultation Activities)工业工程(IE-Industrial Engineering)业务总览二、标准工时系统(一)作业标准时间(OST- Operation Standard Time)之结构(二)正常时间(Normal Time)1. 正常时间就是以正常速度(Normal Speed) 工作时,完成一个单位之作业所需的时间。
精益生产(IE&TIE)
2011-4-8
25
二、IE程序分析、操作分析、动作分析 二、IE程序分析、操作分析、动作分析 动作的四项原则: 一、缩短(动作)的距离 二、减少(动作)的数量 三、保持(动作)的轻松 四、降低(动作)的等级 企业最怕所遇到变更、插单,多与销售人员沟通 按原计划按部就班,临时插单会影响产品质量成本
2011-4-8 15
二、IE程序分析、操作分析、动作分析 二、IE程序分析、操作分析、动作分析
动作经济十六原则: 1、双手并用原则 2、对称反向原则 3、排除合并原则 4、降低动作等级原则 5、减少动作浪费原则 6、避免动作突变原则 7、保持轻松节奏原则 8、利用惯性原则
2011-4-8
9、手脚并用原则 10、利用工具原则 11、工具万能化原则 12、易于操作原则 13、适当位置原则 14、安全可靠原则 15、透明通风则 16、高度适当原则
IE实战与TIE生产 IE实战与TIE生产
一Hale Waihona Puke IE的起源、定义——方法研 究与时间研究 二、IE程序分析、操作分析、动 作分析与实战技术 三、TIE效率分析与改善 四、生产线平衡 五、快速换型SMED改进机会 六、公司改进计划
2011-4-8 1
一、IE的起源、定义、工作范畴— 一、IE的起源、定义、工作范畴—方法研究与时间研究
3、看板式生产(准时化) Just in time A-标准作业方法 B-生产计划-物流-生产-入库全部采用看 板式信息传递 C-异常问题报警(安灯) D-原因分析、改善对策
2011-4-8
32
三、 TIE效率分析与改善(精益、TPS丰田、流动制造……) TIE效率分析与改善(精益、TPS丰田、流动制造……)
2011-4-8 2