凹印常见故障及解决方法
凹版印刷中的故障、原因及解决方法
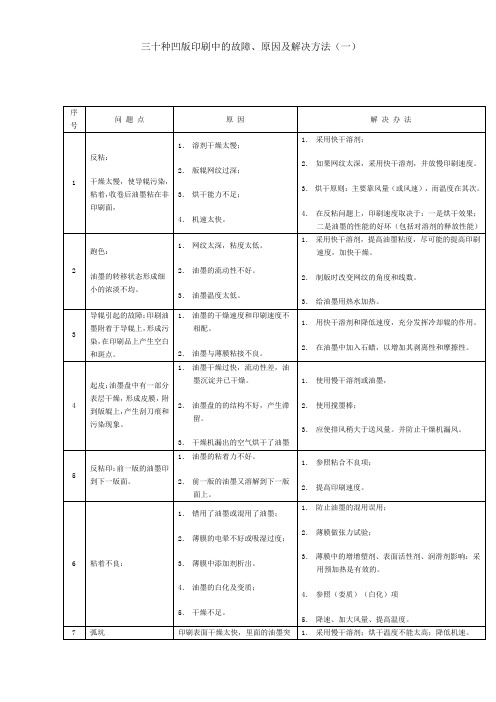
2
跑色:
油墨的转移状态形成细小的浓淡不均。
1.网纹太深,粘度太低。
2.油墨的流动性不好。
3.油墨温度太低。
1.采用快干溶剂,提高油墨粘度,尽可能的提高印刷速度,加快干燥。
2.制版时改变网纹的角度和线数。
3.给油墨用热水加热。
1.使用快干溶剂、提高机速,尽快送入烘干机,印版直径不当造成薄膜滑动;
2.对含增塑剂的薄膜,应避免使用含染料的油墨。从染料的结构知道这种迁移是可能的。
29
粘着、反粘:此时收卷时会有剥离声、重叠部分的油墨会有异常光泽。
1.干燥不良;
2.温度高造成油墨部分软化;
3.收卷太紧;
4.极度的粘着不良;
5.印刷面与接触面的油墨之间亲和力过强。
三十种凹版印刷中的故障、原因及解决方法(一)
序号
问 题 点
原 因
解 决 办 法
1
反粘:
干燥太慢,使导辊污染,粘着,收卷后油墨粘在非印刷面,
1.溶剂干燥太慢;
2.版辊网纹过深;
3.烘干能力不足;
4.机速太快。
1.采用快干溶剂;
2.如果网纹太深,采用快干溶剂,并放慢印刷速度。
3.烘干原则:主要靠风量(或风速),而温度在其次。
1.使用正确的溶剂配方;
2.水白化时:应采用慢干溶剂或提高印刷速度,尽快将薄膜送入烘干机;
3.没有热量的过大风速是有害无益的。
23
起泡:使网点脱落、泡沫飞溅造成印刷品污染
1.水性油墨多发;
2.循环系统缺失。
1.加入消泡剂;
2.避免循环系统中油墨从大的落差流下。
凹版印刷常见故障及解决方法

凹版印刷常见故障及解决方法干燥太慢问题:干燥速度如果太慢,会引发导辊污染、粘附、以及过高的残留溶剂;原因:溶剂的干燥速度过慢、版深过于深、烘干机能力不足、印刷速度过快;解决方案:选择合适干燥速度的溶剂;如果不得不使用较深的版,应配合快干溶剂,并放慢印刷速度;印刷速度应有烘干机能力决定,烘干首要依靠风量,其次才是温度。
跑色问题:阴影部分的油墨转移,形成西小的浓淡不均,绿色的印刷特别常见;原因:凹版的深度太深而油墨粘度太低、由于某种原因影响了油墨的流动性、幽默的温度低;解决方案:采用干燥快的溶剂以高粘度的油墨印刷,制版时改变版网的角度和线数,使用油墨前用热水加温。
卷曲问题:印刷物向内侧卷曲,影响制品美观,也给二次加工带来困难;原因:由于油墨溶剂造成的薄膜膨胀,油墨层和薄膜因温度、湿度变化产生的膨胀率不同;解决方案:选择不溶胀薄膜的油墨及溶剂,尽可能使用较浅的版深来再现色调,在薄膜背面涂布防卷曲剂。
起皮问题:油墨盘中的油墨上有一层干燥的表皮,该表皮可能会附着到滚筒上,形成凹凸不平、刮刀痕或污染;原因:油墨干燥速度过快,干燥机漏出的空气烘干了油墨表层;解决方案:调整油墨干燥速度,应使干燥机的排风量略大于送风量,并防止空气从干燥机中漏出,对油墨盘给予适当覆盖,避免风吹到油墨。
反粘印问题:前一版印刷的油墨又到下一版的版面上;原因:前一版的油墨膜溶解到下一版面上;解决方案:第二版以后各班的油墨要使用溶解力稍弱的溶剂稀释,此外印刷速度不能过慢。
网线问题:转移到薄膜上的油墨呈网点状态,在应该涂布的阴影部分形成各自的小点;原因:油墨干燥过快或粘度过高,在油墨流平之前就已干燥固化,制版时网幅过宽;解决方案:用干燥较慢的溶剂,刮刀位置尽量前移并注意烘干机的漏封,保证流动性适宜的前提下尽量使用低粘度油墨进行印刷。
粘着不良问题:达不到油墨粘接力的要求;原因:用错油墨,薄膜表面张力不足,薄膜中的添加剂影响,油墨干燥不足;解决方案:加强管理,对用剩的油墨表面品名及日期以备再用,印刷前检测薄膜的表面张力,注意薄膜中的爽滑剂等添加剂影响,首次使用新的薄膜时应了解相关情况,利用烘干机进行充分干燥。
凹版印刷常见故障处理方法

凹版印刷常见故障处理方法凹版印刷是一种常见的印刷技术,但在实际操作过程中,常常会遇到一些故障,影响印刷质量和工作效率。
下面是凹版印刷常见故障及处理方法:1.胶辊过磨损胶辊过磨损会导致墨量不稳定,在印刷过程中出现墨色深浅不一的情况。
处理方法是更换新的胶辊,确保其表面光滑。
2.胶辊不均匀磨损胶辊不均匀磨损会导致墨量分布不均匀,造成印刷图案不够清晰。
处理方法是通过精确调整胶辊的位置和轴向,使其均匀磨损。
3.油墨不连续油墨不连续会导致印刷图案有色差或缺墨现象。
处理方法是检查墨盘的墨量,补充油墨或清洁墨盘,以保持墨量稳定。
4.墨色不准确墨色不准确会导致印刷品颜色偏差。
处理方法是调整墨辊和胶辊的间隙,以控制墨色的传递量。
5.凹版压力不均匀凹版压力不均匀会导致印刷图案不清晰或出现模糊现象。
处理方法是检查印刷机的平衡性,调整压力辊和背压辊,以确保凹版压力均匀。
6.凹版转速过快或过慢凹版转速过快或过慢会导致印刷图案模糊或出现缺失。
处理方法是根据实际情况调整印刷机的速度,使其与凹版的匹配度最佳。
7.凹版磨损凹版磨损会导致印刷品细节不清晰或产生噪点。
处理方法是定期更换凹版,并及时做好保养工作,延长凹版的使用寿命。
8.印刷雾化印刷雾化会导致文字或图案模糊不清。
处理方法是调整印刷机的湿度和温度,以控制墨水的流动性,减少雾化现象的发生。
9.纸张吸湿纸张吸湿会导致纸张变形,影响印刷质量和注册精度。
处理方法是调整印刷机的湿度和温度,选择合适的纸张,并进行事前处理,防止纸张吸湿。
10.印刷品色差印刷品色差会导致不同批次的印刷品颜色不一致。
处理方法是确保油墨的配比准确,并严格控制墨水的传递量和温度。
11.印刷精度不高印刷精度不高会导致图案偏移或错位。
处理方法是检查印刷机的注册设备,调整凹版和印刷机的位置,确保印刷精度达到要求。
总的来说,凹版印刷常见故障的处理方法包括更换磨损部件,调整印刷机的湿度和温度,控制油墨的传递量和墨色,以及定期维护保养设备。
凹印常见问题分析与解决

第二节凹印常见问题分析及解决一、凹印问题的成因二、凹印常见问题(一)、堵版在凹版印刷中,油墨从印版滚筒网穴中的转移率通常在50%-70%,大约还有1/2-1/3左右的油墨总是残留在印版滚筒网穴中。
该残留率如果保持一定尚可,但在印刷过程中由于种种原因,网穴中的油墨残留率逐步提高,油墨的转移率也就随之下降,造成堵版故障。
发生堵版以后,会引起印刷图案和文字的模糊不清、印刷颜色的变化,严重时基至无法继续进行印刷。
特别是浅网层次部位容易发生堵版。
1、赌版产生原因:(1)、油墨干固于版面印版滚筒网穴中油墨的转移率通常是由油墨的类型、粘度、印刷速度等因素决定的,总有1/2-1/3的油墨残留在网穴中。
当这些残余油墨在某些因素影响下发生干固(粘度增高)后,印版滚筒再次进入油墨槽时其也难以完全溶解,油墨转移率随之降低。
久而久之,网穴越来越浅,转移率越来越低,最后形成堵版。
此类堵版故障当然与油墨类型、溶剂配比、干燥速度等因素有关,而且印刷机的构造也有很大影响。
(2)、油墨中混入杂质在印刷时,印刷薄膜由于高速运行往往会产生静电,吸附周围的尘埃及基材碎屑等杂质并带人油墨中。
(3)、制版质量低下在腐蚀或雕刻过程中网穴内壁生成小毛刺,镀铬后表面不平滑;研磨时产生的毛刺以及Ω型网穴等,对油墨的转移率也有一定的影响,情况严重时也往往造成转移率低下而成为堵版的原因。
(4)、油墨溶解不良(劣化)油墨变质或溶剂平衡发生变化时引起溶解力下降,或者混入不同类型的油墨、误用溶剂等导致油墨溶解劣化,造成转移率低下,同时也会直接造成堵版。
(5)、化学变化两液型油墨或反应型油墨随着印刷的进行会逐步发生交联等化学反应,流动性变差,粘度增高,转移率随之降低,也可能成为堵版的原因之一。
2、解决方法:(1)、塑料凹印生产过程中发生堵版故障时,应使用溶剂或专用的清洗剂进行清洗,并针对发生堵版的原因加以解决。
(2)、调整适当的环境温湿度、选择与印刷速度、印刷环境相适应的溶剂配比。
凹印常见问题分析与解决

精心整理第二节凹印常见问题分析及解决一、凹印问题的成因二、凹印常见问题(一)、堵版在凹版印刷中,油墨从印版滚筒网穴中的转移率通常在50%-70%,大约还有1/2-1/3左右的油墨总是残留在印版滚筒网穴中。
该残留率如果保持一定尚可,但在印刷过程中由于种种原因,网穴中的油墨残留率逐步提高,油墨的转移率也就随之下降,造成堵版故障。
发生堵版以后,会引起印刷图案和文字的模糊不清、印刷颜色的变化,严重时基至无法继续进行印1(1)(2)中。
(3)(4)(5)转2(1)、(2)(3)、刮刀与压印辊之间的距离尽可能缩短,防止干燥箱漏出的热风直吹版面。
(4)、混合使用慢干溶剂,适当提高印刷速度,降低工作墨粘度。
(5)、如果是由油果性能缺陷引起的堵版,应及时更换油墨(或与油墨供应商联系解决),尽量避免比重有显着差异的油墨组合。
(6)、油墨槽中的油墨要经常搅拌,使油墨保持良好的流动状态,及时加入新的油墨或更换新油墨,减少皮膜化现象的发生。
(7)、由网穴内壁质量引起的堵版,应重新镀版或制版。
(8)、开车前或刚开车时用溶剂镇拭印版滚筒。
印刷过程中尽量避免中途停车,长时间停车时一定要先把印版滚筒洗干净,或者把印版滚筒浸人油墨中连续空转。
(9)、在新鲜油墨中,由于温度差等原因,油墨中的添加剂、蜡类物质发生结晶析出时,可试着在使用前对油墨加温(温度控制在40-50度),使之溶解。
(10)、误用溶剂或油墨变质,混入异种油墨时,会显着影响油墨的再溶解性。
所以应使用正规的专用稀释溶剂,更换油墨要在充分洗净墨槽和循环泵后进行。
(二)、反面粘连粘连指印刷收卷后,印品互相粘在一起,印迹粘背。
1、产生原因导致粘作的原因比较复杂,涉及到油墨、溶剂、承印物、工艺条件等多方面,在印刷、复合、分切,过程中都有可能发生。
主要是由油墨发粘、温度太高、残留溶剂太多以及压力过大等因素引起的。
(1)、油墨中的树脂①树脂软化点。
连结料树脂的软化点离低直接影响着印刷墨层的性能。
凹印常见故障及解决方法
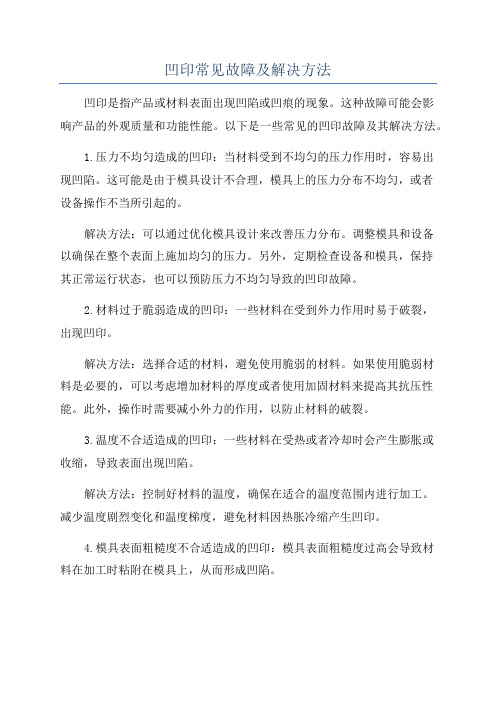
凹印常见故障及解决方法凹印是指产品或材料表面出现凹陷或凹痕的现象。
这种故障可能会影响产品的外观质量和功能性能。
以下是一些常见的凹印故障及其解决方法。
1.压力不均匀造成的凹印:当材料受到不均匀的压力作用时,容易出现凹陷。
这可能是由于模具设计不合理,模具上的压力分布不均匀,或者设备操作不当所引起的。
解决方法:可以通过优化模具设计来改善压力分布。
调整模具和设备以确保在整个表面上施加均匀的压力。
另外,定期检查设备和模具,保持其正常运行状态,也可以预防压力不均匀导致的凹印故障。
2.材料过于脆弱造成的凹印:一些材料在受到外力作用时易于破裂,出现凹印。
解决方法:选择合适的材料,避免使用脆弱的材料。
如果使用脆弱材料是必要的,可以考虑增加材料的厚度或者使用加固材料来提高其抗压性能。
此外,操作时需要减小外力的作用,以防止材料的破裂。
3.温度不合适造成的凹印:一些材料在受热或者冷却时会产生膨胀或收缩,导致表面出现凹陷。
解决方法:控制好材料的温度,确保在适合的温度范围内进行加工。
减少温度剧烈变化和温度梯度,避免材料因热胀冷缩产生凹印。
4.模具表面粗糙度不合适造成的凹印:模具表面粗糙度过高会导致材料在加工时粘附在模具上,从而形成凹陷。
解决方法:选择适合的模具材料,确保其表面粗糙度符合加工要求。
精细加工模具表面,提高其平滑度和抗粘性能。
在加工过程中,可以使用适当的润滑剂来减少材料与模具的摩擦,降低凹印发生的风险。
5.设备振动造成的凹印:在加工过程中,设备的振动会影响材料的加工质量。
解决方法:调整设备和模具的安装,确保其稳定运行。
减少设备的振动,可以增加设备的重量或者采取减振措施。
使用振动传感器和监控设备来及时检测和纠正振动问题。
综上所述,凹印故障可能由多种因素引起,包括压力不均匀、材料脆弱、温度不合适、模具表面粗糙度不合适以及设备振动等。
通过优化模具设计、调整设备和模具、选择合适的材料、控制温度、提高模具表面质量以及降低设备振动等方法,可以有效地预防和解决凹印故障,提高产品的加工质量。
凹印12种常见故障分析及解决方法

凹印12种常见故障分析及解决方法在凹版印刷过程中往往会发生一些由机械、工艺原辅材料、工作环境等因素引起的印刷故障,从而影响产品质量和生产进度。
现将在从事凹印工作中积累的实用经验介绍给大家,供同行们参考。
故障一规则性和无规则性线痕(刀线)1、规则性线痕原因:(1)油墨内混有残渣把刮墨刀划伤;(2)印版或能被硬物划伤;(3)印版滚筒磨损掉铬,铜层裸露。
解决方法:(1)用80目的铜网重新过滤油墨,并用600号水砂纸细磨刀刃或更换墨刀;(2)用800号水砂纸蘸溶剂细磨划伤处;(3)用溶剂洗净印版,用502胶水和铜粉填补划伤,并拿细砂纸轻轻打磨光滑(注:此方法适于短版产品)。
2、无规则性线痕原因:(1)刮墨刀刀锋利度不够;(2)刮墨的倾斜度不够,刮墨刀压力过小;(3)刮墨刀安装时平整度差;(4)油墨与溶剂的溶解性、流动性不好;(5)印版滚筒铬层表面处理不平滑,过于粗糙;(6)印刷滚筒印刷时周向跳动大;(7)油墨内有墨渣,粘在刀刃背后‘(8)墨管和位置不理想,油墨流入墨槽过急,造成油墨不匀。
解决方法:(1)用600号水砂纸打磨刀刃;(2)加大刮墨刀的压力,使其倾斜角度向下,并根据实际情况移动刀架,理想接触角度为50―70度;(3)上刀片时,尽量做到用碎布夹紧压条与刀片,使力向外侧拉,同时从中间旋紧螺丝,逐个向外,但紧螺丝不可一步到位,不需重复二三遍完成,使刀片受力均匀;(4)控制好油墨粘度(在不影响印刷效果的前提下),尽可能使用溶解性强,挥发快的深剂,如醋酸乙酯,乙醇,加入少量异丙醇,可增加光泽度;(5)用800号或600号水砂纸蘸溶剂来回打磨印版滚筒,注意磨至图文部分时用力不要过大,如不理想可与制版厂联系重制印版滚筒;(6)检查印版滚筒、滚筒轴、轴承及传动齿轮是否形变、磨损,还可能是由机座水平不正、不稳造成;(7)墨槽、墨箱洗净,油墨多层过滤;(8)移动墨管位置或合理改进墨槽结构。
故障二拖影原因:(1)油墨稀释过滤,粘度下降;(2)刮墨刀与印版接触角度不佳,过于上仰或顶刀力量过大造成刀刃翘曲;(3)调金油与金属粉调配比例不正确;(4)刮墨刀片过软,安装时压条与刀口的距离过大,刀片伸出过长;(5)压印滚筒压力过大,油墨挤出;解决方法:(1)增大油墨粘度,如情况无明显好转,可重新换墨;(2)将刮墨刀的接触角度调节下倾,顶刀力减小;(3)适度减小调金油的用量;(4)改用弹性高的硬刀片,最好用**产的,缩小刀片与压条的伸长距离;(5)减轻压印滚筒的压力;(6)如拖影现象不严重,可适当提高机速来消除。
凹版印刷常见故障及处理办法
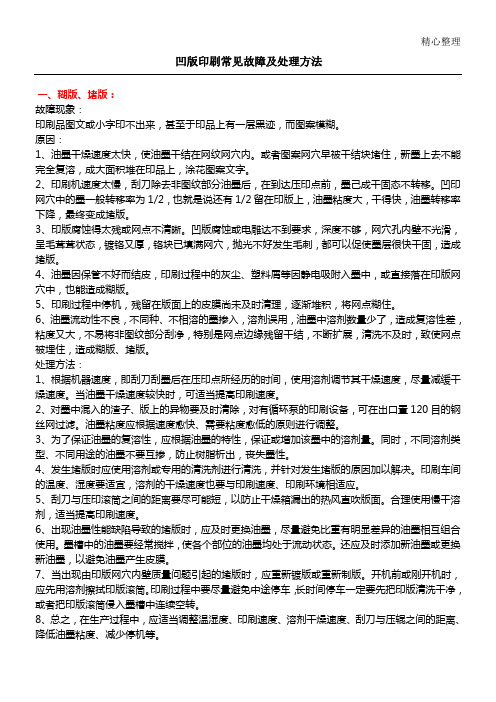
精心整理凹版印刷常见故障及处理方法 一、糊版、堵版:故障现象:印刷品图文或小字印不出来,甚至于印品上有一层黑迹,而图案模糊。
原因:1、油墨干燥速度太快,使油墨干结在网纹网穴内。
或者图案网穴早被干结块堵住,新墨上去不能完全复溶,成大面积堆在印品上,涂花图案文字。
2、印刷机速度太慢,刮刀除去非图纹部分油墨后,在到达压印点前,墨己成干固态不转移。
凹印3堵版。
45612目的钢345剂,适当提高印刷速度。
6、出现油墨性能缺陷导致的堵版时,应及时更换油墨,尽量避免比重有明显差异的油墨相互组合使用。
墨槽中的油墨要经常搅拌,使各个部位的油墨均处于流动状态。
还应及时添加新油墨或更换新油墨,以避免油墨产生皮膜。
7、当出现由印版网穴内壁质量问题引起的堵版时,应重新镀版或重新制版。
开机前或刚开机时,应先用溶剂擦拭印版滚筒。
印刷过程中要尽量避免中途停车,长时间停车一定要先把印版清洗干净,或者把印版滚筒侵入墨槽中连续空转。
8、总之,在生产过程中,应适当调整温湿度、印刷速度、溶剂干燥速度、刮刀与压辊之间的距离、降低油墨粘度、减少停机等。
二、咬色、过版:故障现象:在印刷过程中,第二色油墨将前一色印刷的墨迹粘拉掉了,前一版印刷的油墨又到了下一版的版面上。
原因:1、由于前一色的油墨干燥速度慢,或对被印材料粘附性不强,而后一色附着性太强,印刷压力太大或油墨中树脂量太少,都可将前一色咬掉。
2、印刷速度太快,前一色未干,经受不了第二色的分裂力。
在第一色中,慢干溶剂太多,使前一色不能按要求粘附、干燥而受第二色的粘拉破坏。
312345使原因:1、23染。
45上气温高,就很容易引起聚酰胺分子量降解从而使吸湿性增大,造成与印材的粘接力下降。
6、油墨干燥过慢、收卷张力大、印刷后的收卷温度过高,部分油墨软化、膜卷含水量过大、收卷太紧、印刷油墨与接触面的亲和力过强、静电过大等都会造成粘脏。
处理方法:1、提高油墨的初干性和彻干性,加强吹风和热量,使油墨干燥彻底,在收卷都分增加冷却装置,收卷时张力不要过大。
- 1、下载文档前请自行甄别文档内容的完整性,平台不提供额外的编辑、内容补充、找答案等附加服务。
- 2、"仅部分预览"的文档,不可在线预览部分如存在完整性等问题,可反馈申请退款(可完整预览的文档不适用该条件!)。
- 3、如文档侵犯您的权益,请联系客服反馈,我们会尽快为您处理(人工客服工作时间:9:00-18:30)。
凹印常见故障及解决方法
在凹版印刷过程中往往会发生一些由机械、工艺原辅材料、工作环境等闲素引起的印刷故障,从而影响产品质量和生产进度。
现将在从事凹印工作中积累的实用经验介绍给大家,供同行们参考。
故障一规则性和无规则性线痕(刀线)
1、规则性线痕的原因:
(1)油墨内混有残渣把刮墨刀划伤;
(2) 印版或能被硬物划伤;
(3) 印版滚筒磨损掉铬,铜层裸露。
解决方法:
(1) 用80目的铜网重新过滤油墨,并用600号水砂纸细磨刀刃或更换墨刀。
(2) 用800号水砂纸蘸溶剂细磨划伤处。
(3) 用溶剂洗净印版,用502胶水和铜粉填补划伤,并拿细砂纸轻轻打磨光滑(注:此方法适于短版产品)。
(2)、(3)只针对非图文部分。
2、无规则性线痕原因:
(1) 刮墨刀刀锋利度不够;
(2) 刮墨的倾斜度不够,刮墨刀压力过小;
(3) 刮墨刀安装时平整度差;
(4) 油墨与溶剂的溶解性、流动性不好;
(5) 印版滚筒铬层表面处理不平滑,过于粗糙;
(6) 印刷滚筒印刷时周向跳动大;
(7) 油墨内有墨渣,粘在刀刃背后;
(8) 墨管和位置不理想,油墨流入墨槽过急,造成油墨不匀。
解决方法:
(1) 用600号水砂纸打磨刀刃;
(2) 加大刮墨刀的压力,使其倾斜角度向下,并根据实际情况移动刀架,理想接触角度为50--70度;
(3)上刀片时,尽量做到用碎布夹紧压条与刀片,使力向外侧拉,同时从:㈠间旋紧螺丝,逐个向外,但紧螺丝不可一步到位,不需重复二三遍完成,使刀片受力均匀;
(4)控制好油墨粘度(在不影响印刷效果的前提下),尽可能使用溶解性强,挥发快的深剂,如醋酸乙酯,乙醇,加入少量异丙醇,可增加光泽度;
(5)用800号或600号水砂纸蘸溶剂来回打磨印版滚筒,注意磨至图:艾部分时用力不要过大,如不理想可与制版厂联系重制印版滚筒;
(6) 检查印版滚筒、滚筒轴、轴承及传动齿轮是否形变、磨损,还可能是由机座水平不正、不稳造成;
(7) 墨槽、墨箱洗净,油墨多层过滤;
(8) 移动墨管位置或合理改进墨槽结构。
故障二拖影
原因:
(1) 油墨稀释过滤,粘度下降;
(2) 刮墨刀与印版接触角度不佳,过于上仰或项刀力量过大造成刀刃翘曲;
(3) 调金油与金属粉调配比例不正确;
(4) 刮墨刀片过软,安装时压条与刀口的距离过大,刀片伸出过长;
(5) 压印滚筒压力过大,油墨挤出;
解决方法:
(1) 增大油墨粘度,如情况无明显好转,町重新换墨;
(2) 将刮墨刀的接触角度调节下倾,顶刀力减小;
(3) 适度减小调金油的用量;
(4) 改用弹性高的硬刀片,最好用日本产的,缩小刀片与压条的伸长距离;
(5) 减轻压印滚筒的压力;
(6) 如拖影现象不严重,可适当提高机速来消除。
故障三粘脏
原因:
(1) 烘干箱温度过高或过低;
(2) 冷却循环系统出现故障,水流量过小;
(3) 车间温湿度控制不当;
(4) 油墨粘度太大,干燥速度过慢;
(5) 压印滚筒压力调整不当(过重或过轻)。
解决方法:
(1) 烘干箱温度应根据机速快慢、版面图文情况来决定,大面积印刷,温度为60--80摄氏度,网目调印刷,温度为40-60摄氏度。
(2) 增大冷却辊水流量。
特别要注意输纸导辊发烫,易与承印物粘花,需及时降低烘箱温度;
(3) 印刷车间温湿度控制在18--22摄氏度;
(4) 可在油墨中适时加入挥发性快的溶剂,如醋酸乙酯,降低油墨粘度,加速油墨干燥;
(5) 增加印刷压力,使印迹固实。
故障四印迹发虚,露底
原因:
(1) 压印力不足;
(2) 油墨稀释过度,破坏了油墨的流动性和粘着力;
(3) 油墨中白墨含量过多;
(4) 堵版或印版上网点磨损,掉版;
(5) 原墨调制不适当。
解决方法:
(1) 增大印刷压力;
(2) 提高油墨粘度;
(3) 油墨中尽量少加白墨(颗粒多易伤版),可用冲淡墨代替;
(4) 用毛刷蘸上溶剂洗净版孔内残留的油墨,提高转移率;
(5) 根据原墨的组特点,合理调配油墨。
故障五网点,文字印不全
原因:
(1) 油墨粘度过高,印版上墨层厚实,正负离子难以透过约张,静电吸墨作用减小,不易将印版上的油墨转移到承印物表面;
(2) 静电胶辊两边有油墨,使其未形成绝缘而产生电流导通偏漏,影响吸附力;
(3) 刮墨刀压力过大;
(4) 油墨挥发过快,转移率降低;
(5) 印版在墨槽内吸墨量过少。
解决方法:
(1) 适当降低油墨粘度;
(2) 静电胶辊两边切削2mm深,宽可根据长期印刷面积来定,防止粘墨;
(3) 刮墨刀接触角度上倾;
(4) 加入慢干溶剂,提高油墨转移性能;
(5) 升高刮墨刀架,缩短转移时间,提高网穴存墨量;
(6) 抬高墨槽,使印版吸墨充分。
故障六斑点
原因:
(1) 压印滚筒胶面有伤或粘有污物:
(2) 油墨未完溶解;
(3) 溶剂使用不当或溶剂稀释过量;
(4) 未有效消除纸张静电。
解决方法:
(1) 更换蔌研磨胶辊,使其平滑;
(2) 更确认是否使用了过期或劣质的油墨,并及时更换;
(3) 提高油墨的粘度;
(4) 消除静电,调节印刷车间的湿度。
故障七墨色浓谈不匀
原因:
(1) 墨槽结构有问题油墨易发生沉淀或产生大量泡沫;
(2) 烘干箱漏风,使油墨内溶剂迅速挥发:
(3) 溶剂与油墨未完全溶解。
解决方法:
(1) 改善油墨循环系统,放墨不能过急,适量加入消泡剂;
(2) 找出烘干箱漏风处,并加以补救;
(3) 选用溶解性强的溶剂。
故障八折皱
解决方法:
(1) 校正压印滚筒两侧,使其压力匀衡;
(2) 更换轴承,加固锁紧导辊;
(3) 查找传动齿轮有无磨损,齿全虽否平稳,版轴是否变形,轴承是否“烧死”,并加以校正
故障九印张上图文前后套印不准
原因:
(1) 印刷车间温湿度不当,烘干箱温度过高,纸张收缩严重;
(2) 印刷色组安排不当,前后压印滚筒胶皮硬度不一;
(3) 传动齿轮与版轴未锁紧,致使印版滚筒发生移位:
(4) 自动张力装置发生故障。
解决方法:
(1) 保持印刷车间恒温恒湿,降低烘干箱温度;
(2) 正确安排工艺流程,统一压印滚筒橡胶硬度:
(3) 画线检查传动齿与印版是否产生滑移,并加以锁固;
(4) 若是自动张力装置发生故障,要找电气人员维修。
故障十印迹晶化(粉化)
原因:
(1) 油墨稀释过度;
(2) 印刷压力不足,墨层不实,造成印迹易脱落。
解决方法:
(1) 观察油墨是否混浊,相互分离,若调整粘度后仍不能进行正常印刷,应与油墨供货方联系;
(2) 加大印刷压力,使油墨充分固实。
故障十一在专色上金墨叠印不实(露金)
原因:
(1) 因金粉颗粒粗,加之油墨流量偏大,造成墨层过厚,存墨量大,不易干燥:
(2) 印刷压力过大,形成挤墨;
(3) 印版滚筒上网穴深度不够;
(4) 油墨干燥不够充分。
解决方法:
(1) 在金色中适量加入快干性溶剂,专色则用慢干性溶剂,如不影响印刷效果,油墨粘度尽可能保持适度;
(2) 印刷压力保持适中,均衡;
(3) 制版时网穴深度应根据情况而定:
(4) 大面积印金,应降低机速增加色组间油墨干燥时间。