机械伤害事故原因分析及其对策参考文本
工程施工中机械伤害(3篇)
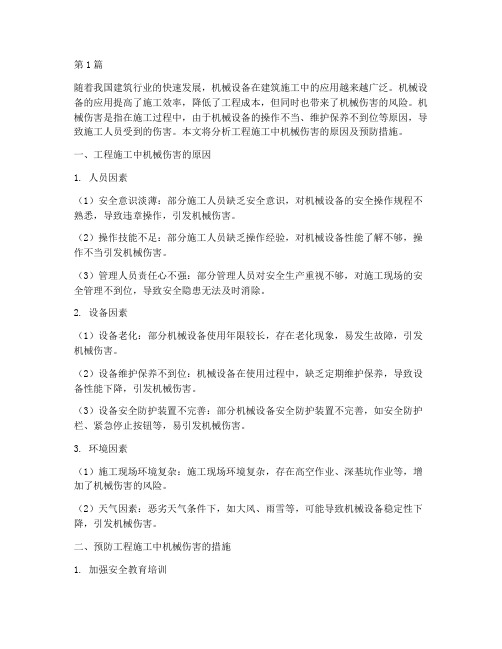
第1篇随着我国建筑行业的快速发展,机械设备在建筑施工中的应用越来越广泛。
机械设备的应用提高了施工效率,降低了工程成本,但同时也带来了机械伤害的风险。
机械伤害是指在施工过程中,由于机械设备的操作不当、维护保养不到位等原因,导致施工人员受到的伤害。
本文将分析工程施工中机械伤害的原因及预防措施。
一、工程施工中机械伤害的原因1. 人员因素(1)安全意识淡薄:部分施工人员缺乏安全意识,对机械设备的安全操作规程不熟悉,导致违章操作,引发机械伤害。
(2)操作技能不足:部分施工人员缺乏操作经验,对机械设备性能了解不够,操作不当引发机械伤害。
(3)管理人员责任心不强:部分管理人员对安全生产重视不够,对施工现场的安全管理不到位,导致安全隐患无法及时消除。
2. 设备因素(1)设备老化:部分机械设备使用年限较长,存在老化现象,易发生故障,引发机械伤害。
(2)设备维护保养不到位:机械设备在使用过程中,缺乏定期维护保养,导致设备性能下降,引发机械伤害。
(3)设备安全防护装置不完善:部分机械设备安全防护装置不完善,如安全防护栏、紧急停止按钮等,易引发机械伤害。
3. 环境因素(1)施工现场环境复杂:施工现场环境复杂,存在高空作业、深基坑作业等,增加了机械伤害的风险。
(2)天气因素:恶劣天气条件下,如大风、雨雪等,可能导致机械设备稳定性下降,引发机械伤害。
二、预防工程施工中机械伤害的措施1. 加强安全教育培训(1)提高施工人员的安全意识:通过开展安全教育培训,使施工人员充分认识到机械伤害的危害,提高安全意识。
(2)提高操作技能:定期对施工人员进行操作技能培训,使其熟练掌握机械设备的使用方法,降低机械伤害风险。
2. 加强设备管理(1)定期检查设备:对机械设备进行定期检查,发现隐患及时维修或更换,确保设备安全运行。
(2)完善安全防护装置:对机械设备的安全防护装置进行完善,如设置安全防护栏、紧急停止按钮等。
3. 优化施工现场环境(1)合理规划施工现场:合理规划施工现场,确保施工区域安全、整洁。
机械制造过程中发生伤害的原因分析和预防对策

机械制造过程中发生伤害的原因分析和预防对策机械制造过程中发生伤害的原因分析和预防对策机械制造是工业的基础,适用于各种生产领域,但是在机械制造过程中,由于各种原因,可能会发生伤害事故,严重影响操作者的安全和健康。
为此,需要对机械制造过程中发生伤害的原因进行分析,并采取一定的预防措施,以确保机械制造过程中的安全和健康。
一、原因分析1. 设备安全性低:机床、机器人和其他设备在使用和检修时,由于制造过程不符合标准或使用不当,容易出现安全性问题。
2. 机械操作者对操作规程和安全标准的不了解:有些工人不了解机械制造设备的操作规程和安全标准,或者不按规程操作,容易出现安全问题。
3. 设备老化和损坏:机械制造设备在生产过程中经常使用,容易出现设备磨损、老化或损坏,这些问题不及时得到维修或更换,会严重影响设备安全性。
4. 人为错误:操作者在操作过程中因疏忽大意或不注意安全,操作过程中出现人为错误,如操作中兴起的纱线、工具刀具上的铁屑、工具上的油脂等可能导致伤害。
5. 自然因素:例如受外界气温和湿度等自然因素影响,会导致设备零部件的膨胀或收缩,由此产生的误差和偏差,影响机械操作的安全性。
二、预防措施1. 加强设备安全:检查设备是否规范、合格以及是否需要定期维修、更换设备备件等。
2. 操作者要了解机械制造设备的操作规程和安全标准,并且在使用机械制造设备时,要按照标准操作,如正确穿着劳保用具、使用机器防护设备、杜绝非规定用途的操作等。
3. 加强设备维护和检查:定期走访和检查机械设备,发现问题及时维护和更换损坏部分。
4. 增强操作者的安全意识:对操作者进行安全教育,加强操作者的安全意识,让他们更加重视安全问题。
5. 加强管理:建立完善的管理机制,健全事故应急预案,加强事故预防、处置和搜救救援等工作。
存在安全问题及时通报,确保机械制造过程的安全性。
综上所述,在机械制造过程中,要注意对设备的维护以及操作人员对设备的了解,对相关工作外的操作应加强管理,提高操作者的安全意识,预防事故发生,确保机械操作过程的安全和健康。
机械伤害事故的原因与预防措施详细版

文件编号:GD/FS-2991(解决方案范本系列)机械伤害事故的原因与预防措施详细版A Specific Measure To Solve A Certain Problem, The Process Includes Determining The Problem Object And Influence Scope, Analyzing The Problem, Cost Planning, And Finally Implementing.编辑:_________________单位:_________________日期:_________________机械伤害事故的原因与预防措施详细版提示语:本解决方案文件适合使用于对某一问题,或行业提出的一个解决问题的具体措施,过程包含确定问题对象和影响范围,分析问题,提出解决问题的办法和建议,成本规划和可行性分析,最后执行。
,文档所展示内容即为所得,可在下载完成后直接进行编辑。
机械伤害事故的原因:1、机械设备在设计制造上存在缺陷;2、设备设施、工具、附件有缺陷;3、是设备日常维护、保养不到位、机械设备带病作业;4、从业人员个人操作错误、人为造成安全装置失效、机械运转时加油、维修、清扫,或者操作者进入危险区域进行检查、安装、调试;5、生产作业环境缺陷,操作空间不符合安全要求。
机械伤害事故的预防措施:1、在选择机械设备时,一定要选择有资质的正规厂商生产的机械设备,防护罩、保险、限位、信号等装置齐全,设备本身质量达到安全状态;2、专用设备必须配备专用的工具,设备设施上的安全附件有缺陷时,一定应及时处理,处理不了的要及时更换设备;3、加强对设备的使用、维护、保养、检查等工作,建立完善点巡检工作制,及早发现设备隐患并迅速处理,使机械设备不带病作业;4、以制度为切入点,规范员工操作行为,进一步完善规章制度和安全技术操作规程,杜绝违章指挥和违章操作的行为。
狠抓安全生产知识和安全操作技能培训工作,提高员工的自我保护意识;5、积极改善员工的生产作业环境,设备的改造应充分考虑到操作空间与周围环境,必须能够保证员工安全操作的需要。
造成机械伤害事故的原因分析

造成机械伤害事故的原因分析
从安全系统工程学的角度来看,造成机械伤害的原因可以从人、机、环境三个方面进行分析。
人、机、环境三个方面中的任何一个出现缺陷,都有可能引起机械伤害事故的发生。
一、人的不安全行为
1.误触开关或违章开机。
操作者操作时注意力不集中或思想过紧张而发生误操作或误动作或操作者业务技术素质低,操作不熟练,缺乏正规的专业培训以及监督检查不够。
2.违章作业,操作者不按规程进行操作。
违章作业一般都是因作业人员缺乏安全知识,心存侥幸造成的认为一次违章不一定会造成事故。
检修、检查机械时,忽视安全措施。
在线检修时,未采取必要的预防措施,如未断电作业、电源处未悬挂警示牌等。
不小心进入机械危险部位或是未与操作人员联系,盲目接触机械危险部位。
3.安全生产意识淡薄,安全管理机制不健全
二、物的不安全因素
1.设计不当致机械不符合安全要求,机械故障,防护及安全装置失灵等。
2.安全防护设施不健全或形同虚设。
主要有以下几种情况:一是无安全防护设施;二是机械设备安全防护设施损坏;三是解除了机械
设备安全防护设施;四是作业人员未按要求使用安全防护设施。
三、环境的不安全因素
噪声干扰、照明光线不良、无通风、温湿度不当、场地狭窄、布局不合理等。
机械伤害事故原因分析及其对策(一)
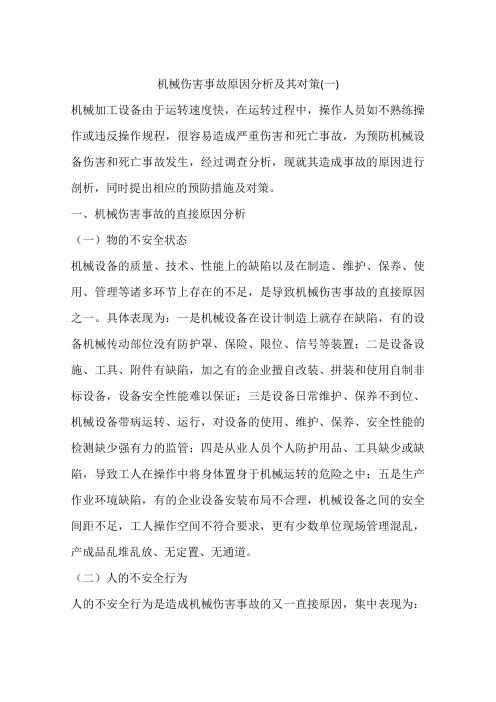
机械伤害事故原因分析及其对策(一)机械加工设备由于运转速度快,在运转过程中,操作人员如不熟练操作或违反操作规程,很容易造成严重伤害和死亡事故,为预防机械设备伤害和死亡事故发生,经过调查分析,现就其造成事故的原因进行剖析,同时提出相应的预防措施及对策。
一、机械伤害事故的直接原因分析(一)物的不安全状态机械设备的质量、技术、性能上的缺陷以及在制造、维护、保养、使用、管理等诸多环节上存在的不足,是导致机械伤害事故的直接原因之一。
具体表现为:一是机械设备在设计制造上就存在缺陷,有的设备机械传动部位没有防护罩、保险、限位、信号等装置;二是设备设施、工具、附件有缺陷,加之有的企业擅自改装、拼装和使用自制非标设备,设备安全性能难以保证;三是设备日常维护、保养不到位、机械设备带病运转、运行,对设备的使用、维护、保养、安全性能的检测缺少强有力的监管;四是从业人员个人防护用品、工具缺少或缺陷,导致工人在操作中将身体置身于机械运转的危险之中;五是生产作业环境缺陷,有的企业设备安装布局不合理,机械设备之间的安全间距不足,工人操作空间不符合要求,更有少数单位现场管理混乱,产成品乱堆乱放、无定置、无通道。
(二)人的不安全行为人的不安全行为是造成机械伤害事故的又一直接原因,集中表现为:一是操作失误,忽视安全,忽视警告。
操作者缺乏应有的安全意识和自我防护意识,思想麻痹,有的违章指挥,违章作业,违反操作规程;二是操作人员野蛮操作,导致机器设备安全装置失效或失灵,造成设备本身处于不安全状态;三是手工代替工具操作或冒险进入危险场所、区域,有的工人为图省事,走捷径,擅自跨越机械传动部位;四是机械运转时加油、维修、清扫,或者操作者进入危险区域进行检查、安装、调试,虽然关停了设备,但未能开启限位或保险装置,又无他人在场监护,将身体置身于他人可以启动设备的危险之中;五是操作者忽视使用或佩戴劳保用品。
二、机械伤害事故的间接原因分析一是安全机构不健全,有的企业没有专职安全员或安全员配备不足,有的安全员一人多职,职责不明,人浮于事;二是安全宣传、安全培训不到位,有的企业新工人未经培训就直接上岗作业,特别是特种作业人员未经相关部门培训,缺乏安全操作技术知识,存在边学边干的现象;三是安全生产制度、操作规程不健全,即使有制度也流于形式,执行不到位,监管不到位;四是对事故隐患整改不力,有的企业虽然定期进行安全检查,但对发现的问题和隐患,往往一查了之,不能跟踪督查整改到位。
机械伤害事故的原因与预防措施正式版

In the schedule of the activity, the time and the progress of the completion of the project content are described in detail to make the progress consistent with the plan.机械伤害事故的原因与预防措施正式版机械伤害事故的原因与预防措施正式版下载提示:此解决方案资料适用于工作或活动的进度安排中,详细说明各阶段的时间和项目内容完成的进度,而完成上述需要实施方案的人员对整体有全方位的认识和评估能力,尽力让实施的时间进度与方案所计划的时间吻合。
文档可以直接使用,也可根据实际需要修订后使用。
机械伤害事故的原因:1、机械设备在设计制造上存在缺陷;2、设备设施、工具、附件有缺陷;3、是设备日常维护、保养不到位、机械设备带病作业;4、从业人员个人操作错误、人为造成安全装置失效、机械运转时加油、维修、清扫,或者操作者进入危险区域进行检查、安装、调试;5、生产作业环境缺陷,操作空间不符合安全要求。
机械伤害事故的预防措施:1、在选择机械设备时,一定要选择有资质的正规厂商生产的机械设备,防护罩、保险、限位、信号等装置齐全,设备本身质量达到安全状态;2、专用设备必须配备专用的工具,设备设施上的安全附件有缺陷时,一定应及时处理,处理不了的要及时更换设备;3、加强对设备的使用、维护、保养、检查等工作,建立完善点巡检工作制,及早发现设备隐患并迅速处理,使机械设备不带病作业;4、以制度为切入点,规范员工操作行为,进一步完善规章制度和安全技术操作规程,杜绝违章指挥和违章操作的行为。
狠抓安全生产知识和安全操作技能培训工作,提高员工的自我保护意识;5、积极改善员工的生产作业环境,设备的改造应充分考虑到操作空间与周围环境,必须能够保证员工安全操作的需要。
——此位置可填写公司或团队名字——。
机械伤害事故教训及防范措施
案例二:设备维护不当引发的事故
总结词
设备维护缺失、安全隐患未及时 排查
详细描述
某工厂的机械设备在长时间运行 后,由于未及时进行维护保养, 导致设备故障,引发事故。
案例三:安全防护措施缺失导致的事故
总结词
缺乏安全防护措施、员工安全意识薄 弱
详细描述
某工厂在生产过程中,未对危险区域 设置安全防护设施,员工在危险区域 作业时发生事故。
02
机械伤害事故原因剖析
操作人员技能不足
总结词
操作不熟练、缺乏经验
详细描述
操作人员技能水平低,对机械设备的性能、操作规程不熟悉,容易发生误操作或 操作失误,导致机械伤害事故。
设备维护保养不当
总结词
维护保养缺失、设备老化
详细描述
设备长时间未进行维护保养,导致机械部件磨损、老化,设备故障频发,增加了发生机械伤害事故的风险。
缺乏自我保护能力
在事故发生时,部分操作人员缺乏自我保护能力,不能正 确应对和逃生,导致事故后果加重。
加强安全宣传教育和演练
企业应加强安全宣传教育,使操作人员充分认识到安全的 重要性,并定期进行事故应急演练,提高操作人员的自我 保护能力。
THANKS
谢谢您的观看
培训不足导致安全意识薄弱
缺乏培训和教育使操作人员对安全操作规程和注 意事项不了解,导致安全意识薄弱,容易发生事 故。
培训内容需涵盖安全知识和技能
为了提高操作人员的安全意识和技能,培训内容 应包括机械安全操作规程、应急处理和自救互救 等方面的知识和技能。
加强设备维护和安全管理
设备维护保养不当
机械设备的正常运行依赖于日常的维护和保养,如果维护保养不 当,会导致设备故障或异常运行,从而引发事故。
机械伤害事故的常见原因及现场急救
机械伤害事故的常见原因及现场急救机械伤害事故是指在生产、工作和生活中发生的由机械设备、工具、机器、车辆等造成的人身伤害和财产损失的事件。
机械伤害事故的后果往往是不可估量的,所以一定要重视起来。
本文就机械伤害事故的常见原因及现场急救措施进行分析。
一、机械伤害事故的常见原因:1. 设备维护不当设备运转过程中,如果维护不当或维修不及时,容易引起设备故障,导致机械伤害事故。
2. 工人故意操作设备由于工人对机械设备的不了解或粗心大意,操作不当,甚至故意乱动机器,因此也会产生机械伤害事故。
3. 设备设计缺陷设备设计不合理,如部件不牢固、结构不稳定等缺陷,出现故障或失效后,也会引起机械伤害事故。
4. 劳动保护意识淡薄劳动者的劳动保护意识淡薄,不戴安全帽、护眼镜等防护措施,不按照规定操作机器,也容易导致机械伤害事故的发生。
5. 设备过旧设备使用年限过长,失去了正常使用功能,会产生许多隐患,容易导致机械伤害事故。
二、机械伤害事故的现场急救:机械伤害事故的发生给被害人造成了很大的危害,对于此类伤害,我们必须要了解到现场急救的方法:1. 立刻停机在现场发生机械伤害事故时,首先要将机器停止。
以免继续对被伤害人造成更大的伤害。
2. 避免损伤扩大如果被害人在机器中,我们首先要尝试将机器停下来,同时也要警告其他人不得靠近机器。
3. 防止烧伤如果系皮肤脱离,只需用凉水降温,不要用创可贴或其他绷带紧绷,若表面已烧伤,可用消毒纱布覆盖。
4. 预防失血性休克在机械伤害事故发生时,往往会出现大量失血,可能导致失血性休克。
因此,我们要尽快切断出血点,并用布条或医用绷带加压包扎,防止大量失血引起失血性休克。
5. 调动心理安慰机械伤害事故虽然给被伤害者带来了巨大的身体伤害,但我们不能忘记,在受到伤害和害怕的时候,心理上的调整也很重要。
当发生机械伤害事故时,我们应当及时安慰被伤害者,让他们放松心情。
在今天这个机械化程度越来越高的社会,机械伤害事故在生产、工作和生活中不时地发生。
机械制造企业中安全生产事故原因分析与对策措施[五篇范例]
机械制造企业中安全生产事故原因分析与对策措施[五篇范例]第一篇:机械制造企业中安全生产事故原因分析与对策措施机械制造企业中安全生产事故原因分析与对策措施随着我国社会生产力的发展,机械制造企业逐年增多,安全生产事故频频发生。
在机械制造企业中,如何对安全生产事故进行有效预防,保持良好的安全生产秩序,对维护安全生产稳定起着极其重要的作用。
一、问题的提出据统计机械制造企业的安全生产事故在所有安全生产事故中所占比例是相当大的,它不仅影响企业的声誉与效益,而且严重伤害员工的身心健康,甚至生命。
在机械制造企业有秩序的生产活动和过程中发生的不测事件,不仅造成生产的中断或干扰,而且造成生产设施和材料的损坏,直接延误了生产,给员工和企业造成的伤害和损失是不言而喻的。
所以开展安全与事故研究是机械制造企业的重要工作。
本文将对机械制造企业中安全生产事故的原因进行分析与研究,并提出对策措施。
二、事故原因分析一)事故的直接原因分析(一)物的不安全状态机械设备的质量、技术、性能上的缺陷以及在制造、维护、保养、使用、管理等诸多环节上存在的不足,是导致机械伤害事故的直接原因之一。
具体表现为:一是机械设备在设计制造上就存在缺陷,如有的设备机械传动部位没有防护罩;有的设备没有安全保险措施;有的设备运动部件没有限位装置;有的设备没有工作运行提示信号装置;有的设备没有处理好人机工程学问题,使得机器的可操作性太差,容易引起操作者的误操作;二是设备设施、工具、附件有缺陷,加之有的企业擅自拆装、改装、拼装和使用自制非标设备,设备安全性能得不到保障;三是设备日常维护、保养不到位、机械设备带病运转、运行,对设备的使用、维护、保养、安全性能的测试缺乏有效的日常管理机制;四是从业人员个人劳动防护用品、生产工具缺少或缺陷,导致工人在操作中将身体直接置身于机械运转的危险区域之中;五是生产作业环境有缺陷,有的企业设备安装布局不合理,机械设备之间的安全间距不足,工人操作空间不符合要求,更有少数企业现场管理混乱,产成品乱堆乱放、无定置、无通道。
机械伤害成因分析及防范措施
机械伤害成因分析及防范措施机械伤害成因分析及防汇范措施1、机械伤害的特点1).什么是机械伤害机械伤害是指机械做出强大的功能作用于人体的伤害。
2).机械伤害事故有什么特点机械伤害死亡事故的形式惨重,如搅死、挤死、压死、碾死、被弹出物体打死、磨死等。
当发现有人被机械伤害的情况时,虽及时紧急停车,但因设备惯性作用,仍可将受害造成致使性伤害,乃至身亡。
一般性工伤事故表现为:职工手指、胳膊、腿、脚趾骨骨折、挫伤,皮肤裂伤等。
3).常见伤害人体的机械设备有哪些有皮带运输机、球磨机、行车、卷扬机、干燥车、气锤、车床、磨床、铣床、锻床、砂轮机、弯管机、混砂机、螺旋输送机、泵、压模机、破碎机、推焦机、硫化机、卸车机、离心机、搅拌机、轮碾机、滚筒筛等。
2.形成机械伤害的事故主要原因分析形成机械伤害的事故其主要原因有:1)检修、检查机械忽视安全措施。
如人进入设备(球磨机等)检修、检查作业,不切断电源,未挂不准合闸警示牌,未设专人监护等措施而造成严重后果。
也有的因当时受定时电源开关作用或发生临时停电等因素误判而造成事故。
也有的虽然对设备断电,但因未等至设备惯性运转彻底停住就下手工作,同样造成严重后果。
2)缺乏安全装置。
如有的机械传动带、齿轮、接近地面的或人手能够着的联轴节、皮带轮、飞轮等易伤害人体部位没有完好防护装置;还有的人孔、投料口绞笼井等部位缺护栏及盖板,无警示牌,人一疏忽误接触这些部位,就会造成事故。
3)电源开关布局不合理,一种是有了紧急情况不立即停车;另一种是好几台机械开关设在一起,开关位号未标识清楚,极易造成误开机械引发严重后果。
4)机械线路安装不规范,私拉乱接。
临时线路多,线路跨起、拖起、磨起。
5)自制或任意改造机械设备,不符合安全要求。
6)在机械运行中进行清理、卡料、上皮带蜡,加油等作业。
7)任意进入机械运行危险作业区(采样、干活、借道、拣物等)。
8)物件乱堆乱放,物件堆放不安全,堆放过高,车床床头、小刀架、床面、滑道面上随便放置工、量具,物件占压安全通道。
- 1、下载文档前请自行甄别文档内容的完整性,平台不提供额外的编辑、内容补充、找答案等附加服务。
- 2、"仅部分预览"的文档,不可在线预览部分如存在完整性等问题,可反馈申请退款(可完整预览的文档不适用该条件!)。
- 3、如文档侵犯您的权益,请联系客服反馈,我们会尽快为您处理(人工客服工作时间:9:00-18:30)。
机械伤害事故原因分析及其对策参考文本
In The Actual Work Production Management, In Order To Ensure The Smooth Progress Of The Process, And Consider The Relationship Between Each Link, The Specific Requirements Of Each
Link To Achieve Risk Control And Planning
某某管理中心
XX年XX月
机械伤害事故原因分析及其对策参考文
本
使用指引:此安全管理资料应用在实际工作生产管理中为了保障过程顺利推进,同时考虑各个环节之间的关系,每个环节实现的具体要求而进行的风险控制与规划,并将危害降低到最小,文档经过下载可进行自定义修改,请根据实际需求进行调整与使用。
机械加工设备由于运转速度快,在运转过程中,操作
人员如不熟练操作或违反操作规程,很容易造成严重伤害
和死亡事故,为预防机械设备伤害和死亡事故发生,经过
调查分析,现就其造成事故的原因进行剖析,同时提出相
应的预防措施及对策。
一、机械伤害事故的直接原因分析
(一)物的不安全状态
机械设备的质量、技术、性能上的缺陷以及在制造、
维护、保养、使用、管理等诸多环节上存在的不足,是导
致机械伤害事故的直接原因之一。
具体表现为:一是机械
设备在设计制造上就存在缺陷,有的设备机械传动部位没
有防护罩、保险、限位、信号等装置;二是设备设施、工具、附件有缺陷,加之有的企业擅自改装、拼装和使用自制非标设备,设备安全性能难以保证;三是设备日常维护、保养不到位、机械设备带病运转、运行,对设备的使用、维护、保养、安全性能的检测缺少强有力的监管;四是从业人员个人防护用品、工具缺少或缺陷,导致工人在操作中将身体置身于机械运转的危险之中;五是生产作业环境缺陷,有的企业设备安装布局不合理,机械设备之间的安全间距不足,工人操作空间不符合要求,更有少数单位现场管理混乱,产成品乱堆乱放、无定置、无通道。
(二)人的不安全行为
人的不安全行为是造成机械伤害事故的又一直接原因,集中表现为:一是操作失误,忽视安全,忽视警告。
操作者缺乏应有的安全意识和自我防护意识,思想麻痹,有的违章指挥,违章作业,违反操作规程;二是操作人员
野蛮操作,导致机器设备安全装置失效或失灵,造成设备本身处于不安全状态;三是手工代替工具操作或冒险进入危险场所、区域,有的工人为图省事,走捷径,擅自跨越机械传动部位;四是机械运转时加油、维修、清扫,或者操作者进入危险区域进行检查、安装、调试,虽然关停了设备,但未能开启限位或保险装置,又无他人在场监护,将身体置身于他人可以启动设备的危险之中;五是操作者忽视使用或佩戴劳保用品。
二、机械伤害事故的间接原因分析
一是安全机构不健全,有的企业没有专职安全员或安全员配备不足,有的安全员一人多职,职责不明,人浮于事;二是安全宣传、安全培训不到位,有的企业新工人未经培训就直接上岗作业,特别是特种作业人员未经相关部门培训,缺乏安全操作技术知识,存在边学边干的现象;三是安全生产制度、操作规程不健全,即使有制度也流于
形式,执行不到位,监管不到位;四是对事故隐患整改不力,有的企业虽然定期进行安全检查,但对发现的问题和隐患,往往一查了之,不能跟踪督查整改到位。
三、预防机械伤害事故的对策
通过事故原因分析,笔者认为控制和避免机械设备安全生产事故应采取以下应对措施:
第一,以制度为抓手,规范职工操作行为。
对于机械加工企业来说,必须进一步完善规章制度和安全操作规程,落实相关职能部门的工作责任,提高制度的执行能力和可操作性,对一些特殊的专用设备的操作规程必须针对加工产品的特点及使用规定作深入细致的研究,制定更为细致和规范的操作规程,督促操作者掌握该设备的危险源(点)及防范措施。
通过建立健全安全生产规章制度,实行严格检查督促,落实各级各类人员的安全生产责任制,杜绝违章指挥和违章操作的行为。
第二,严格科学设置机械加工设备的安全。
机械加工设备包括所有的金属切削设备,各种类型的锻压压力设备、木工机械、热加工设备、砂轮机以及机械传动装置等。
那么企业对所有机械加工设备的布局、设备与设备之间的间距、设备本身的安全操作空间必须符合《工厂安全卫生规程》,做到统一布局、科学安装。
同时对所有机械加工设备的危险部位都必须安装防护装置,保护机床区域内的操作者和其他人不受机械设备工作点、卷入挤压点、回转零件、飞出的碎屑和火花造成伤害,对防护网、防护罩、栏杆、防护档板等,必要时应增加安全连锁装置,这些装置必须与机械加工设备同时设计、同时施工、同时投入使用。
另外根据机械加工设备的维护保养的要求和规定进行日常的维护保养、定期维护保养及定期的检修,以便及时发现和排除设备安全隐患,将事故隐患遏制在萌芽状态。
第三,狠抓培训教育,全力提高从业人员的自我保护意识。
强化生产经营单位和从业人员安全培训教育工作是贯彻安全生产方针,实现安全生产,提高管理者和从业人员安全意识和安全素质的重要途径,提高产品质量,加快推进现代工业化进程,对从业人员提出越来越高的要求,每个劳动者不但需要熟练掌握生产技术,而且还要求具备安全生产知识和安全操作技能,因此,对新员工上岗前必须进行三级教育、四新教育和变换岗位教育,企业对特种作业人员必须按照国家有关规定经专门的安全教育培训,取得特种作业安全操作资格证书,方可上岗作业。
同时要强行执行劳动防护用品的使用与佩戴,为保护劳动者在劳动过程中的安全和健康,企业必须为劳动者配备必要的预防性装备,同时相关职能部门还必须加大检查和执法力度,通过正确配备和使用劳动防护用品来改善劳动条件,防止伤亡事故,预防职业危害的发生。
一方面用人单位应
正确采购和选用劳动防护用品;另一方面,督促从业人员正确佩戴和使用劳动防护用品,同时建立健全劳动防护用品的购买、验收、保管、发放、使用、更换和报废等管理制度,保障劳动者的安全与健康。
第四,建立健全安全生产检查制度,落实隐患整改。
安全生产检查是一项综合性的安全生产管理措施,是建立良好的安全生产环境,做好安全生产工作的重要手段,也是预防事故、消除隐患、减少职业危害的有效办法。
各机械加工企业必须建立健全安全检查制度,从查培训、查制度、查管理、查违章指挥和违章操作、查隐患、查安全设施等六个方面进行定期不定期的安全检查,对一时难以整改到位的问题和隐患,限期整改,并明确专人负责跟踪督查、督办,确保隐患得到控制和消除。
第五,规范管理,加大行政执法力度。
负有安全生产监督管理部门,应加大安全生产法律法规的宣传力度,通
过媒体、发放法律法规文件、举办安全生产知识培训班等形式,提高用人单位和从业人员的安全生产知识和法律意识,对违法生产、违章指挥和违章操作造成严重后果的,依照《安全生产法》加大处罚力度,通过多种途径进一步提高机械加工企业的安全生产法律意识,减少和控制各类机械伤害事故的发生。
请在此位置输入品牌名/标语/slogan
Please Enter The Brand Name / Slogan / Slogan In This Position, Such As Foonsion。