铜线拉丝工艺理论知识
电线电缆基本知识之五:拉丝工艺技术

一、线材拉伸的基本原理1.线材的拉伸线材的拉伸是指线坯在一定的拉力作用下,通过模孔发生塑性变形,使截面减小、长度增加的一种压力加工方法。
2.拉伸的特点(1)拉伸的线材有较精确的尺寸,表面光洁,断面形状可以多样。
(2)能拉伸大长度和各种直径的线材。
(3)以冷加工为主,拉伸工艺、模具、设备简单,生产效率高。
(4)拉伸能耗较大,变形受一定的限制。
3.拉伸的原理拉伸属于压力加工范围,拉伸过程中除了产生极少的粉屑外,体积变化甚微,因此拉伸前、后金属的体积基本相等。
4.影响拉伸的因素(1)铜、铝杆(线)材料。
在其他条件相同时,拉铜线比拉铝线的拉伸力大,拉铝线容易断,所以拉铝线时应取较大的安全系数。
(2)材料的抗拉强度。
材料的抗拉强度因素很多,如材料的化学成分,压延工艺等,抗拉强度高则拉伸力大。
(3)变形程度。
变形程度越大,在模孔变形段长度越长,因而增加了模孔对线的正压力,摩擦力也随之增加,拉伸力也增加。
(4)线材与模孔间的摩擦系数。
摩擦系数越大,拉伸力越大。
摩擦系数由线材和模具材料光洁度、润滑液的成分和数量决定。
(5)线模模孔工作区和定径区的尺寸和形状。
定径区越大,拉伸力也越大。
(6)线模的位置。
线模安放不正或模座歪斜也会增加拉伸力。
也是线径及表面质量不达标。
(7)外来因素。
线材不直,拉线过程中线的抖动,放线阻力,都会增加拉伸力。
二、拉丝设备1.拉丝机的分类按模具数量分:单模拉丝机和多模拉丝机。
按工作特性分:滑动式拉丝机和非滑动式拉丝机。
按鼓轮形状分:塔形鼓轮拉丝机、锥形鼓轮拉丝机及圆柱形鼓轮拉丝机。
按润滑型式分:喷射式拉丝机和浸入式拉丝机。
按拉制线径分:巨、大、中、小、细、微拉丝机。
2.多模拉丝机的特点多模拉丝机是线材通过几个规格逐渐减小尺寸的模子和其后的拉线鼓轮,而实现拉伸的拉丝机。
(1)滑动式连续拉丝机滑动式连续拉丝机是拉丝鼓轮圆周速度大于线材拉伸速度,并以次而产生摩擦力。
它的优点是总的延伸系数高,加工率大,拉伸速度高,产量大,易于实现自动化、机械化。
电线电缆基本知识之五拉丝工艺技术

一、线材拉伸的基本原理1. 线材的拉伸线材的拉伸是指线坯在一定的拉力作用下,通过模孔发生塑性变形,使截面减小、长度增加的一种压力加工方法。
2. 拉伸的特点(1)拉伸的线材有较精确的尺寸,表面光洁,断面形状可以多样。
(2)能拉伸大长度和各种直径的线材。
(3)以冷加工为主,拉伸工艺、模具、设备简单,生产效率高。
(4)拉伸能耗较大,变形受一定的限制。
3. 拉伸的原理拉伸属于压力加工范围,拉伸过程中除了产生极少的粉屑外,体积变化棋微, 因此拉伸前、后金属的体积基本相等。
4. 影响拉伸的因素(1)铜、铝杆(线)材料。
在其他条件相同时,拉铜线比拉铝线的拉伸力大,拉铝线容易断,所以拉铝线时应取较大的安全系数。
(2)材料的抗拉强度。
材料的抗拉强度因素很多,如材料的化学成分,压延工艺等,抗拉强度高则拉伸力大。
(3)变形程度。
变形程度越大,在模孔变形段长度越长,因而增加了模孔对线的正压力,摩擦力也随之增加,拉伸力也增加。
(4)线材及模孔间的摩擦系数。
摩擦系数越大,拉伸力越大。
摩擦系数山线材和模具材料光洁度、润滑液的成分和数量决定。
(5)线模模孔工作区和定径区的尺寸和形状。
定径区越大,拉伸力也越大。
(6)线模的位置。
线模安放不正或模座歪斜也会增加拉伸力。
也是线径及表面质量不达标。
(7)外来因素。
线材不直,拉线过程中线的抖动,放线阻力,都会增加拉伸力。
二、拉丝设备1. 拉丝机的分类按模具数量分:单模拉丝机和多模拉丝机。
按鼓轮形状分:塔形鼓轮拉丝机、锥形鼓轮拉丝机及圆柱形鼓轮拉丝机。
按润滑型式分:喷射式拉丝机和浸入式拉丝机。
按拉制线径分:巨、大、中、小、细、微拉丝机。
2. 多模拉丝机的特点多模拉丝机是线材通过儿个规格逐渐减小尺寸的模子和其后的拉线鼓轮,而实现拉伸的拉丝机。
(1)滑动式连续拉丝机滑动式连续拉丝机是拉丝鼓轮圆周速度大于线材拉伸速度,并以次而产生摩擦力。
它的优点是总的延伸系数高,加工率大,拉伸速度高,产量大,易于实现自动化、机械化。
电线电缆基本知识之五:拉丝工艺技术

一、线材拉伸的基本原理1.线材的拉伸线材的拉伸是指线坯在一定的拉力作用下,通过模孔发生塑性变形,使截面减小、长度增加的一种压力加工方法。
2.拉伸的特点(1)拉伸的线材有较精确的尺寸,表面光洁,断面形状可以多样。
(2)能拉伸大长度和各种直径的线材。
(3)以冷加工为主,拉伸工艺、模具、设备简单,生产效率高。
(4)拉伸能耗较大,变形受一定的限制。
3.拉伸的原理拉伸属于压力加工范围,拉伸过程中除了产生极少的粉屑外,体积变化甚微,因此拉伸前、后金属的体积基本相等。
4.影响拉伸的因素(1)铜、铝杆(线)材料。
在其他条件相同时,拉铜线比拉铝线的拉伸力大,拉铝线容易断,所以拉铝线时应取较大的安全系数。
(2)材料的抗拉强度。
材料的抗拉强度因素很多,如材料的化学成分,压延工艺等,抗拉强度高则拉伸力大。
(3)变形程度。
变形程度越大,在模孔变形段长度越长,因而增加了模孔对线的正压力,摩擦力也随之增加,拉伸力也增加。
(4)线材与模孔间的摩擦系数。
摩擦系数越大,拉伸力越大。
摩擦系数由线材和模具材料光洁度、润滑液的成分和数量决定。
(5)线模模孔工作区和定径区的尺寸和形状。
定径区越大,拉伸力也越大。
(6)线模的位置。
线模安放不正或模座歪斜也会增加拉伸力。
也是线径及表面质量不达标。
(7)外来因素。
线材不直,拉线过程中线的抖动,放线阻力,都会增加拉伸力。
二、拉丝设备1.拉丝机的分类按模具数量分:单模拉丝机和多模拉丝机。
按工作特性分:滑动式拉丝机和非滑动式拉丝机。
按鼓轮形状分:塔形鼓轮拉丝机、锥形鼓轮拉丝机及圆柱形鼓轮拉丝机。
按润滑型式分:喷射式拉丝机和浸入式拉丝机。
按拉制线径分:巨、大、中、小、细、微拉丝机。
2.多模拉丝机的特点多模拉丝机是线材通过几个规格逐渐减小尺寸的模子和其后的拉线鼓轮,而实现拉伸的拉丝机。
(1)滑动式连续拉丝机滑动式连续拉丝机是拉丝鼓轮圆周速度大于线材拉伸速度,并以次而产生摩擦力。
它的优点是总的延伸系数高,加工率大,拉伸速度高,产量大,易于实现自动化、机械化。
铜拉丝生产工艺
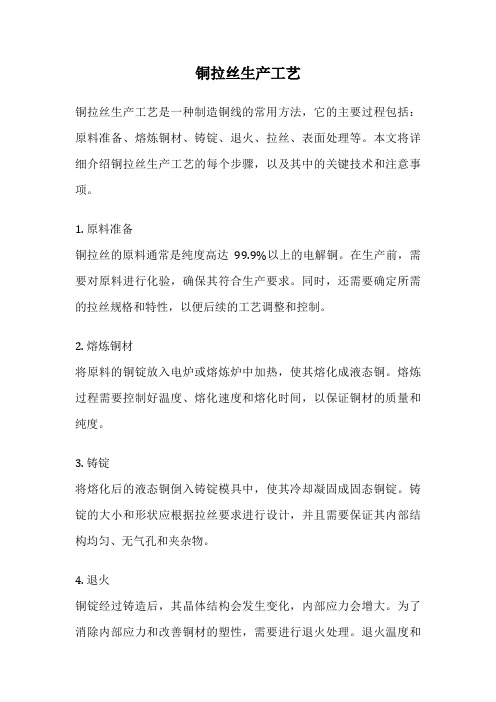
铜拉丝生产工艺铜拉丝生产工艺是一种制造铜线的常用方法,它的主要过程包括:原料准备、熔炼铜材、铸锭、退火、拉丝、表面处理等。
本文将详细介绍铜拉丝生产工艺的每个步骤,以及其中的关键技术和注意事项。
1. 原料准备铜拉丝的原料通常是纯度高达99.9%以上的电解铜。
在生产前,需要对原料进行化验,确保其符合生产要求。
同时,还需要确定所需的拉丝规格和特性,以便后续的工艺调整和控制。
2. 熔炼铜材将原料的铜锭放入电炉或熔炼炉中加热,使其熔化成液态铜。
熔炼过程需要控制好温度、熔化速度和熔化时间,以保证铜材的质量和纯度。
3. 铸锭将熔化后的液态铜倒入铸锭模具中,使其冷却凝固成固态铜锭。
铸锭的大小和形状应根据拉丝要求进行设计,并且需要保证其内部结构均匀、无气孔和夹杂物。
4. 退火铜锭经过铸造后,其晶体结构会发生变化,内部应力会增大。
为了消除内部应力和改善铜材的塑性,需要进行退火处理。
退火温度和时间的选择要根据铜材的厚度和拉丝要求进行合理调整。
5. 拉丝将退火后的铜锭放入拉丝机中进行拉丝操作。
拉丝机通过不断减小铜材的截面积,逐渐将其拉长成所需的线材。
拉丝过程需要控制好速度、温度和张力等参数,以保证铜线的尺寸和表面质量。
6. 表面处理拉丝后的铜线通常会有一定的表面粗糙度和氧化层。
为了提高铜线的表面质量,需要对其进行表面处理。
常用的方法包括酸洗、电镀、喷砂等。
表面处理的目的是去除表面污染物和氧化层,使铜线具有良好的导电性和外观。
在整个铜拉丝生产工艺中,关键的技术和注意事项有以下几点:1. 温度控制:熔炼、退火和拉丝过程中的温度控制是非常重要的,过高或过低的温度都会影响铜材的质量和性能。
2. 拉丝速度:拉丝速度的选择要根据铜线的规格和要求进行合理调整,过快的拉丝速度会导致拉伸应力过大,影响铜线的强度和延展性。
3. 张力控制:拉丝过程中的张力要适中,过大的张力会导致铜线断裂,过小的张力会导致铜线断面不均匀。
4. 机械设备:拉丝机的质量和性能也对铜拉丝工艺有着重要的影响,优质的机械设备能够提高生产效率和产品质量。
铜线拉丝工艺理论知识

抽气嘴
井式炉
真空罐
电缆盘
加热丝
地面
图1 真空退火炉结构示意图
热电偶
1 真空退火炉
1.1优点:技术简单,设备简陋,设备投资 低,对操作 人员要求低。 1.2缺点:耗电量大,退火一吨铜丝耗电在230度电以上;生产工艺不稳定,一旦漏气全炉均会氧化变色;真空炉内的上下、左右温度不均匀,会出现内外电线软硬不均,更有甚者,还会出现电线粘连现象;不能在线连续退火,且退一罐线的周期太长。 1.3 建议:由于真空退火炉工艺落后,能耗大,产品质量不稳定,生产成本高,市场竞争能力低,建议尽快淘汰真空退火炉。
二、模具
1、模具的作用 拉线的主要工模具是线模,线模的工作部分是模孔,拉线时线材通过模孔受力而变形. 2、模具分类: 2.1按材质分: 1.硬质合金模;2.钻石模;3. 聚晶模(人造金刚石);4.钢模 2.2按孔型分: 圆模和型模 2.3按在拉线过程的作用分:成品模和过渡模 从成本考虑,一般使用的钻石模和聚晶模两种线模.
退火的解释
退火是一种金属热处理工艺,指的是将金属缓慢加热到一定温度,保持足够时间,然后晶粒,调整组织,消除组织缺陷。退火工艺随目的之不同而有多种,如等温退火、均匀化退火、球化退火、去除应力退火、再结晶退火,以及稳定化退火、磁场退火等等。准确的说,退火是以适宜速度冷却。目的是降低硬度,改善切削加工性;消除残余应力,稳定尺寸,减少变形与裂纹倾向;细化一种对材料的热处理工艺,包括金属材料、非金属材料。而且新材料的退火目的也与传统金属退火存在异同。
E、 铜刺或裂片(主要是铜才原因所致) 铜刺的发生与夹杂物相似,在延扎或铸造时产生,因此可以分为铸成(CAST-IN SLIVER)及扎成(ROLLED-IN SLIVER)两种,铸成铜刺发生于铸造时冷却不当或铜水中含氧量过高;扎成铜刺来自延扎过程中,修边机未调整好,或扎轮间隙调整不当,导致刮伤等。 一般来讲,铜刺或长条裂片与铸造或延扎时所发生的氧化亚铜粒子有关,因为氧化亚铜的存在阻止铜杆在加工时裂痕闭合,因此在拉伸后铜线表面产生刺或长条裂片,严重时造成断线。 F、 张力断线 张力断线是拉伸过程中常见的一种断线,其断线特征是断头呈杯锥状或尖锥状,由于拉力大于铜线本身的抗拉强度,造成断线。 产生原因:铜线拉伸过程中润滑不良,眼模角度不当,眼模前堆积铜粉,减面率过大及速度匹配不当均可能造成张力断线。 G、 铜粉断线 拉丝润滑液中有相当量的铜粉,拉丝时铜粉会在眼模进角处堆积,使铜线卡紧在眼模内造成断线;另外铜刺剥落堆积在眼模前也会造成断线。
铜_电缆_拉丝_工艺__概述说明以及解释

铜电缆拉丝工艺概述说明以及解释1. 引言1.1 概述铜电缆拉丝工艺是一种在电缆制造过程中广泛应用的重要工艺。
它通过将铜材料加热熔化后经过一系列步骤进行拉伸,最终制得所需直径和长度的铜丝。
这种工艺不仅可以满足传输电力和信号的要求,还能在某些特殊场合提供导电性能和可靠性。
1.2 文章结构本文将分为六个主要部分来介绍和解释铜电缆拉丝工艺。
首先,在引言部分我们将概述这篇文章的目的和结构。
其次,我们会详细介绍铜电缆拉丝工艺的概述以及与之相关的步骤。
然后,我们将探讨拉丝工艺中涉及到的参数与控制方法。
接着,我们会分析铜电缆拉丝工艺优化和发展趋势,并介绍一些创新技术应用和环保要求实践。
最后,我们会总结全文并得出结论。
1.3 目的本文旨在全面了解铜电缆拉丝工艺,并深入探讨其关键步骤、参数控制以及优化和发展趋势。
通过阅读本文,读者将能够掌握铜电缆拉丝工艺的基本原理和操作技巧,为相关行业的从业人员提供有益的参考和指导。
同时,本文还将对当前的环保要求进行分析,并展望未来该领域可能出现的创新技术和应用方向,以推动铜电缆拉丝工艺的可持续发展。
2. 铜电缆拉丝工艺概述铜电缆拉丝工艺是一种将铜材料通过拉伸和挤压的过程制造成细丝或绳索的加工方法。
这种技术被广泛应用于电力传输和通信行业,以生产各种类型的电缆和导线。
在铜电缆拉丝工艺中,首先需要选择高质量的铜材料作为原料。
常见的铜材料包括无氧铜、低氧铜和含锡铜等。
这些材料具有较高的导电性和良好的强度,能够满足电缆使用的要求。
拉丝工艺主要分为四个步骤:原料准备、熔化铜材料、进行拉丝过程和冷却处理。
首先,在原料准备阶段,需要对选定的铜材料进行清洗和烘干处理,以去除表面污染物和水分。
然后将经过处理的材料切割成合适大小的坯料。
接下来,在熔化铜材料过程中,坯料被加入到特殊设计的感应加热设备中进行加热,使其达到熔点。
在液态状态下,铜材料能够更好地进行拉伸和挤压。
然后,在进行拉丝过程时,将熔化的铜材料通过预拉、主拉和后拉等多个阶段逐渐加工成所需的细丝或绳索。
拉丝工艺

绪论铜材料在外界温度下总是有一个残留的氧化膜,而这一氧化膜是当铜线进入热杆轧制阶段时,在高温的、连续铸造的铜杆上形成的。
氧化膜具有一定的危害,因为它们会在拉丝过程中导致很多缺陷,如:使拉丝膜过度磨损、可焊性变差、搪瓷膜和裸导体之间的附着力变弱等。
拉线模是生产线材的重要工具,是实现正常的连续拉伸,保证拉伸制品质量的关键。
要使拉线获得高质量的拉伸制品,不仅取决于原材料以及拉线模本身的材质,还取决于模子的孔型设计和使用时的其它配合条件。
目前,随着高速拉丝机的广泛应用,拉线模的使用在拉丝过程中具有相当重要的作用。
在实际的铜拉丝生产过程中,使用的拉丝润滑剂有多种,它们的性能相差很大,严重影响线材的质量,因此为了提高线材质量,节约成本,合理选择和正确使用拉丝润滑剂显得格外重要。
为达到以上目的,就要求润滑剂油基稳定,乳化性好,具有优良的润滑性、冷却性和清洗性,易于把铜粉末过滤与沉淀,在整个生产过程中始终保持最佳的润滑状态,以便形成一层能承受高压力而不被破坏的薄膜,降低工作区的摩擦力,提高拉丝质量。
各种不同的润滑剂具有不同的优缺点,其使用时间要根据不同的特点来决定。
铜单线的退火是电线电缆生产过程中的重要工序之一,导线电性能、机械性能及表面质量的好坏很大程度上取决于退火的工艺及生产方式。
金属塑性变形的重要特点之一是加工硬化。
随着变形程度的增加,变形浪里的所有指标,如屈服极限,强度极限和硬度都增大,而塑性指标如延伸率,断面缩减率都减少,同时还会增大电阻,导热性下降。
这会对拉丝产生不良的影响。
拉线是利用材料的塑性来实现的一种机械操作。
用于这种目的的机械可能是直接的或积累的,这种机械叫做拉丝机或者拉丝台,它包括一系列的固定的拉线模,在每个拉线模之间安置导轮以使导线保持一定的张力,拉丝机把导线拉过拉线模,最终的拉丝操作是由一个拉线模后面所施加的力来完成的,之后把拉过的线材收到线盘上。
第 1 章拉丝工艺及材料的选用在外界温度下,铜线总是有一个残留的氧化膜,而这一氧化膜是当铜线进入热杆轧制阶段时,在高温的、连续铸造的铜杆上形成的。
拉丝工艺理论知识培训

• 2.1 按 材 质 分 : 1. 硬 质 合 金 模 ; 2. 钻 石 模 ; 3. 聚晶模〔人造金刚石〕;4.钢模
• 2.2按孔型分: 圆模和型模
• 2.3按在拉线过程的作用分:成品模和过渡模
• 我们模模孔
模孔分四个区域:入口润滑区、 工作区〔压缩区〕、 定径区、出口区。
三、拉丝油
1、 拉丝液:
拉丝液在拉丝过程中起着润滑、冷却、清洗作用。拉丝液要控 制的主要性能参数有浓度,温度,PH值。
1.1、浓度:浓度太高,拉丝液清洗性能减弱,油脂消耗大,浓度太 低,润滑性能减弱,影响模具使用寿命和铜线外表质量,甚至造 成断线。现我司拉丝液浓度控制范围为大拉15-18%,中拉7-8%, 中小拉4-6%,小拉3-5%,微拉2-3%。
β
β
β 3
出口区 定径区
工作区 入口润滑区
各局部功能.
1). 入口区和润滑区
入口区一般带有圆弧,便于拉伸金 属进入工作区,而不致被模孔边 缘擦伤.润滑区是导入润滑剂, 使拉伸材料得到润滑.在拉线模 扩孔时,靠这局部来加大工作区 2). 工作区
工作区是金属拉伸塑性变形区,即 金属材料通过这个区,直径由大 变小.这个区的选择主要是高度 和锥角.
一、拉丝工艺工序流程图
8.000mm铜杆 2.600mm加工铜
检验①
合格
大拉机
退火线 过程线
检验②
不合格〔评审〕 规格线〔不退火〕
退货
让步接收
检验③
A+B类
C类
返拉
检验①
合格
不合格
评审 让步接收
退货
中拉机
规格线〔不退火〕
退火线 过程线
检验③
小拉机
- 1、下载文档前请自行甄别文档内容的完整性,平台不提供额外的编辑、内容补充、找答案等附加服务。
- 2、"仅部分预览"的文档,不可在线预览部分如存在完整性等问题,可反馈申请退款(可完整预览的文档不适用该条件!)。
- 3、如文档侵犯您的权益,请联系客服反馈,我们会尽快为您处理(人工客服工作时间:9:00-18:30)。
• 2.3 建议:由于能耗大,生产成本高,产品竞争能 力低,建议尽快淘汰,采用新技术。
3 接触式电刷传输大电流退火机
接触式电刷传输大电流退火机,是我国上世纪五十年代从前 苏联引进的技术。退火机的工作原理如图3所示。图4为接触 式电刷传输大电流原理。
1
电极轮
退火管 电极轮
冷却水
变压器 可 调 压 电 源
电 极 轮
电轴 刷承
退 火 管
2 放线盘
收线盘
图3 接触式电刷传输大电流退火机
电 极 轮
图4 接触式电刷传输大电流原理
3 接触式电刷传输大电流退火机
• 3.1 优点:比较节能;实现了高速连续退火;导体的柔软 度比较均匀;退火电压可以跟踪退火速度。
此种断线的断面呈孔洞状,其放大图片其孔洞表面非常平滑,无凸起 或开裂的现象。
气泡断线的形成原因是铸成时氢气控制不当,冷却不良产生缩孔
所致,若孔洞较小则在后续的热加工过程中也许会闭合,若孔洞较 大则无法闭合,于是造成气泡断线。
• B、 夹杂物断线(主要是铜才原因所致)
夹杂物断线是断线中较为常见的一种,从外形看可以分为两类,一类 是夹杂物存在的断线,另一类是夹杂物丢失的断线。
扭断:线材因受扭力而断线,最常发生在生产通信电缆的绞合机 上。
• 熔断:这种现象主要出现在连续退火机,由于张力调整不当或 铜材内部缺陷,线与导轮之间有火花产生,铜线表面在火花发生 处有熔毁现象,严重时造成断线。
• K、眼模刮伤
• 拉丝眼模的管理直接影响到断线率及加工成本,如眼模内孔不 光滑,将使拉的线材表面造成严重的连续性刮伤,并造成张力断 线。
• D、“V”形断线
这种断线的主要特征是铜线表面有连续性的“V”字形裂纹,“V” 字的尖端为拉伸方向。
•
形成的主要原因是拉伸眼模角度不当导致,或者是拉线时铜
线没有水平进入眼模而呈某角度进入时,因线材与眼模单面过度摩
擦也可能造成“V”形裂痕,由金相图可以观察到氧化亚铜粒子受外
力的作用以“V”形裂口处为基点呈扭曲波浪状排列。另外,若铜材
铜导体为什么需要退火软化处理?
• 电线电缆导体经冷拔加工后,均存在硬化现象, 抗拉强度和屈服强度明显增加,塑性和韧性普遍 降低,伸长率的变化尤为显著。欲消除冷拔硬化 现象,提高延伸率,就必须进行退火处理,以消 除内部应力及缺陷,使之恢复到冷加工前的物理 及机械性能。如铜导体经550℃退火处理后,导线 柔软,不易被拉断。同时,导体的电阻率降低约 2.1%,减小了线路损耗。因此,退火软化是电线 电缆及漆包线生产过程的主要环节之一。
抽气嘴
气压表
统的退火工艺,其设 真空罐
热电偶
地面
备的结构示意图如图
1所示。它主要有:
真空罐、井式加热系
井式炉
统组成。真空罐的顶 加热丝
部为一个可以打开的
电缆盘
盖,在盖上有抽真空
的接口、气压表、测
温热电偶、密封橡胶
垫、固定螺栓等组成。
图1 真空退火炉结构示 意图
1 真空退火炉
1.1优点:技术简单,设备简陋,设备投资 低,对操作 人员要求低。
接头断线的最大原因在于氧化亚铜粒子在连接部分过分集中,或 者接线时温度太高造成晶粒的成长,另外焊接后花边清除不干净 亦会造成断线。
• F、 机械损伤断线
• 这种断线的主要原因在于铜杆或铜线的排线不良而造成乱线,在 未进入拉丝机前因乱线形成线与线之间的纠缠打结,无法进入眼 模而断线。
• J、扭短与熔断
软化机 (退火)
眼模在 这里面
挂线
放大图
2.9mmφ銅線(2tコイル )
1
→ 1.28mm φ
→ 0.16~0.45mm φ
2
3
PVC Compound 0.3m㎡~8m㎡
4
第1次伸线
・C 型伸线机 (3 )
屏蔽线
第2次伸线 ・M型伸线机 (5 )
PVC Compound
6
导体捻线
・捻线机 (34 ) 金属箔屏蔽
规格线
检验③
C类
返拉
检验③
C类
返拉
C类
检验③
A+B类
上漆车间
A+B类
报废
A+B类
二、拉丝工艺理论知识培训
• 一、铜材 • 1、现在公司主要以生产漆包圆铜线为主,拉丝主要原材是
Φ8.0mm铜杆(有时也采用Φ2.6mm的加工铜);作为漆包线的 导体材料,铜应具有良好的导电性,导热性和延展性,而且机 械性能要好,容易焊接;铜导体材料主要性能如下:a.标称体 积电阻系数(20℃时)0.017241Ω*mm2/m;b.纯度≥99.97%;
• 3、 中央爆裂的预防 由于连铸连扎铜杆具有较稳定的品质,其它原因断线很少,因此对中央爆
裂的预防尤其重要。
预防方法:
1)、定期检查眼模的变形角,磨损过大应及时更换 2)、定期检查拉丝液的浓度、温度、PH值和电导度,及时添加或更换 拉丝油。
3)、检查拉丝机的塔轮,磨损严重时及时更换。
• A、 气泡断线(主要是铜才原因所致)
二、模具
• 1、模具的作用 拉线的主要工模具是线模,线模的工作部分是模孔,
拉线时线材通过模孔受力而变形. • 2、模具分类:
2.1 按 材 质 分 : 1. 硬 质 合 金 模 ; 2. 钻 石 模 ; 3. 聚晶模(人造金刚石);4.钢模 • 2.2按孔型分: 圆模和型模 • 2.3按在拉线过程的作用分:成品模和过渡模 从成本考虑,一般使用的钻石模和聚晶模两种线模.
•
退火的解释
• 退火是一种金属热处理工艺,指的是将金属缓慢 加热到一定温度,保持足够时间,然后晶粒,调 整组织,消除组织缺陷。退火工艺随目的之不同 而有多种,如等温退火、均匀化退火、球化退火、 去除应力退火、再结晶退火,以及稳定化退火、 磁场退火等等。准确的说,退火是以适宜速度冷 却。目的是降低硬度,改善切削加工性;消除残 余应力,稳定尺寸,减少变形与裂纹倾向;细化 一种对材料的热处理工艺,包括金属材料、非金 属材料。而且新材料的退火目的也与传统金属退 火存在异同。
常用的退火方法和工艺有:(1)真空退火 炉;(2)热管式退火炉;(3)接触式大电 流退火炉;(4)感应式退火炉。其中,接 触式大电流退火炉又分为电刷传输电流式退 火炉和水银传输电流式退火炉。下面逐一分 析这几种退火方法和工艺的优缺点,以便于 用户在选择退火设备时作参考。
1 真空退火炉
真空退火炉是比较传
1.2缺点:耗电量大,退火一吨铜丝耗电在230度电以 上;生产工艺不稳定,一旦漏气全炉均会氧化变色; 真空炉内的上下、左右温度不均匀,会出现内外电 线软硬不均,更有甚者,还会出现电线粘连现象; 不能在线连续退火,且退一罐线的周期太长。
1.3 建议:由于真空退火炉工艺落后,能耗大,产品质 量不稳定,生产成本高,市场竞争能力低,建议尽 快淘汰真空退火炉。
表层的含氧量过分集中,亦较易产生“V”形裂痕,最终导致断线。
• E、 铜刺或裂片(主要是铜才原因所致)
• 铜刺的发生与夹杂物相似,在延扎或铸造时产生,因此可以分为 铸成(CAST-IN SLIVER)及扎成(ROLLED-IN SLIVER)两种, 铸成铜刺发生于铸造时冷却不当或铜水中含氧量过高;扎成铜刺 来自延扎过程中,修边机未调整好,或扎轮间隙调整不当,导致 刮伤等。
1、 中央爆裂的种类 1)、铜杆中含氧量过高(大于6000PPM)引起的中央爆裂; 2)、夹杂物引起的中央爆裂; 3)、拉丝设备不良导致的中央爆裂(如不恰当的眼模进角);
• 2、 中央爆裂的形成过程 观察中央爆裂断线的纵剖面的金相照片,我们发现原先排列整齐的氧化亚ቤተ መጻሕፍቲ ባይዱ
铜颗粒因受应力影响而呈现扭曲变形及参次不齐的状况,从金相图来 观察断线的形成过程(图中显示:氧化亚铜粒子已明显扭曲集中,并 有微小裂纹产生,此时还未断线),若在大拉时造成此现象,虽有足 够的强度维持不断线,但在后续中拉过程中只要再施加外力,则必然 造成断线,同理若在中拉时造成内伤,细拉时必然有问题。(发生断 线时,拉成的铜线硬而脆,一弯就断,常被误认为铜质不佳。)
• 一般来讲,铜刺或长条裂片与铸造或延扎时所发生的氧化亚铜粒 子有关,因为氧化亚铜的存在阻止铜杆在加工时裂痕闭合,因此 在拉伸后铜线表面产生刺或长条裂片,严重时造成断线。
• F、 张力断线
• 张力断线是拉伸过程中常见的一种断线,其断线特征是断头呈杯 锥状或尖锥状,由于拉力大于铜线本身的抗拉强度,造成断线。
2 热管式退火炉
热管式退火炉 也是比较传统的 退火工艺,其设 备的结构示意图 如图2所示。它 主要有:不锈钢 管、加热棒、测 温热电偶、冷却
水及导轮组成。
导轮 放线盘
加热棒
退火不锈钢管 导轮
收线盘
冷却水
图2 管道式退火炉结构示意 图
2 热管式退火炉
• 2.1 优点:技术简单,设备简陋,设备投资低,对 操作人员要求低,能够实现多头退火。
拉丝过程中线径的变化
一、拉丝工艺工序流程图
8.000mm铜杆 2.600mm加工铜
检验①
合格
大拉机
退火线 过程线
检验②
不合格(评审) 规格线(不退火)
退货
让步接收
检验③
A+B类
C类
返拉
检验①
合格
不合格
评审 让步接收
退货
中拉机
规格线(不退火)
退火线 过程线
检验③
小拉机
过程线
检验③
规格线(不退火)
微拉机
• 产生原因:铜线拉伸过程中润滑不良,眼模角度不当,眼模前堆 积铜粉,减面率过大及速度匹配不当均可能造成张力断线。