新型干法水泥生产工艺
新型干法水泥生产工艺辅助设备

帆布层
帆布层
硫化接头的 阶梯长度
橡胶输送带的断面图
胶带端头硫化接头
➢ ⑵ 托棍
➢
输送带的支撑与约束装置。根据托辊装设部位和作用的
不同,右:平行托棍(支承输送带的承载段和空载段)、槽
形托辊(用于支承承载边的输送带和物料,角度30 º~45
º)、调心托辊(支承输送带和物料、调整跑偏的输送带,使
之复位)和缓冲托辊(在装载处减小物料对输送带的冲击作
A向
下托辊(平行)
(b) 槽形上托辊及平行下托辊
导向滚柱体
胶带(承载段) 托辊
托辊支架
υ移
υ带
υ辊
立辊
立轴
(c)平形调心托辊
导向滚柱体 胶带(承载段)
(e)调心托辊的调心作用原理
导向滚柱体
胶带运行方向
立轴
(d)槽形调心托辊
托辊 托辊支架
➢ ⑤ 托辊的辊子:辊子是托辊的主要部件,辊子由外 筒、轴承座、轴承、心轴和密封装置构成。外筒多用无缝 钢管制成,也可用增强尼龙代用,轴承座用铸铁车制或钢 板冲压制成。辊子轴承的润滑和密封效果对减小回转阻 力、延长轴承使用寿命等有重要作用。下图(a)为钢板 冲压密封装置,这种方式构造简单,便于装拆和修理,但 密封效果和可靠性较差;下图(b)为采用双道迷宫式塑 料密封装置,这种密封方式的密封效果和可靠性较好,为 了防止外筒内壁脱落的氧化物等进入轴承内,防止润滑脂 流出,装设了内密封圈。辊子轴承应采用滴点较高的不易 流失和变质的锂基润滑脂作润滑剂。
机三种:
➢
① 通用带式输送机(即TD型带式输送机)所用输送带的
带芯材料为棉帆布或化纤织物,外包橡胶或塑料。
➢
② 钢绳芯带式输送机(即DX型带式输送机)所用输送带
新型干法水泥生产工艺

新型干法水泥生产工艺新型干法水泥生产工艺是水泥生产工艺的一种新兴形式,具有节能、环保、高效等优点。
下面,我们将结合具体例子,详细介绍新型干法水泥生产工艺。
首先,新型干法水泥生产工艺相比传统湿法水泥生产工艺具有节能的特点。
传统湿法水泥生产工艺中,需要将石灰石等辅料用水浸泡后进行破碎、烧成。
而新型干法水泥生产工艺使用干燥和破碎设备,无需用水进行破碎,因此节约了大量的水资源。
此外,新型干法水泥烧成过程中,采用了高温炉的技术,使煅烧能耗大幅降低,进一步提高了能源利用效率,达到了节能的目的。
其次,新型干法水泥生产工艺具有环保的特点。
传统湿法水泥生产工艺中,由于需大量用水,导致废水排放量巨大,对水资源的浪费和环境的污染较为严重。
而新型干法水泥生产工艺不需要用水进行破碎和煅烧,避免了废水的产生,减少了对水环境的污染。
此外,新型干法水泥生产工艺在煅烧过程中,采用了环境友好的高温炉,使排放的废气中有害物质的含量大为降低,减少了大气污染的排放。
再次,新型干法水泥生产工艺具有高效的特点。
传统湿法水泥生产工艺中,由于需要进行水泥石灰石辅料的湿制主要过程,时间相对较长,在生产效率上有一定的限制。
而新型干法水泥生产工艺无需用水浸泡石灰石等辅料,导致生产时间大大缩短。
此外,煅烧过程中的高温生产技术,使得新型干法水泥生产工艺具有更高的煅烧温度和更长的停留时间,使得水泥熟料的物理和化学变化更完善,提高了水泥的质量和性能。
最后,新型干法水泥生产工艺还具有一定的适用范围限制。
传统湿法水泥生产工艺虽然耗能大、污染严重,但适用于水资源丰富的地区。
而新型干法水泥生产工艺适用于水资源相对匮乏的地区,尤其适用于干旱地区。
综上所述,新型干法水泥生产工艺是一种具有节能、环保、高效等优点的新兴生产工艺。
通过采用干燥和破碎设备,减少了用水量;通过采用高温炉和环境友好的技术,减少了废气的排放;同时,具有更高的生产效率。
然而,新型干法水泥生产工艺也有一定适用范围的局限性。
新型干法水泥工艺及设备概述
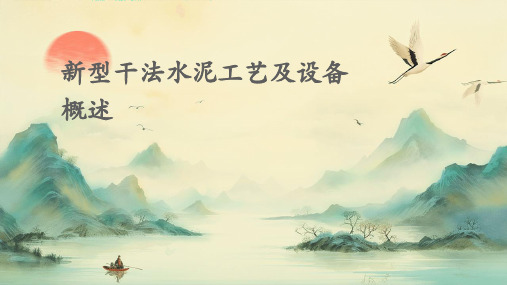
研究和应用新材料技术,开发新型水泥品种和性能,满足市场需求 和未来发展趋势。
04
新型干法水泥工艺及设备的环保与节
能
环保措施
废气处理
01
采用高效除尘器和脱硫脱硝技术,降低废气排放量,减少对大
气的污染。
废水处理
02
采用循环冷却水系统,实现废水零排放,同时对生产过程中产
生的废水进行深度处理,达到排放标准。
应急预案
制定应急预案,建立应急救援队伍,确保在发生突发事件 时能够迅速、有效地应对。
06
新型干法水泥工艺及设备的经济效益
分析
投资分析
投资规模
新型干法水泥工艺及设备的投资规模较大,涉及的设备种类繁多,包括原料破碎、生料制 备、熟料烧成、水泥粉磨等设备。
资金来源
投资新型干法水泥工艺及设备的资金来源主要包括企业自有资金、银行贷款、政府扶持资 金等。
原料预均化
通过堆取料机、均化库等设备,使原料混合均 匀,保证后续生产过程的稳定性。
配料与粉磨
根据生产需求,将原料按照一定比例配料,并通 过球磨机等设备将原料粉磨至一定细度。
熟料烧成
将粉磨后的原料送入回转窑中,在高温下进行烧制 ,形成熟料。
熟料冷却与破碎
将烧制后的熟料进行快速冷却,并破碎至一定粒 度,便于后续加工。
发展趋势
低碳化发展
在工艺和设备中加强低碳技术的研发和应用,降低水泥行业的碳 排放强度。
资源循环利用
加强固体废弃物的资源化利用,推动水泥行业循环经济的发展。
智能化升级
加强智能化技术在新型干法水泥工艺及设备中的应用,提高生产效 率和能源利用效率。
05
新型干法水泥工艺及设备的生产管理
新型干法水泥生产工艺

新型干法水泥生产工艺引言新型干法水泥生产工艺是近年来水泥行业的一项重要发展,通过采用干法工艺进行水泥生产,实现了对水泥生产过程的全面优化。
本文将介绍新型干法水泥生产工艺的原理、优势以及应用场景。
工艺原理新型干法水泥生产工艺相对于传统湿法生产工艺来说更加环保、节能。
其基本原理如下:1.原料处理:首先将石灰石、黏土、铁矿石等原料在原料破碎设备中进行粉碎和混合,使得原料能够满足烧成的要求。
2.烧成过程:将处理后的原料在旋转窑中煅烧,通过高温实现石灰石的分解,生成水泥熟料。
与传统湿法工艺不同的是,新型干法工艺中不需要使用大量的水分配合烧成过程。
3.磨矿和混合:将石灰石熟料经过磨矿设备磨碎,再与适量的石膏混合制成水泥。
4.脱硝和除尘:在工艺流程中加入了脱硝和除尘设备,有效减少了二氧化硫和氮氧化物等污染物的排放。
工艺优势相较于传统的湿法水泥生产工艺,新型干法水泥生产工艺具有以下几个优势:1.节能减排:新型干法工艺不需要用水,避免了大量水的消耗和废水排放问题。
同时,新工艺中增加了除尘和脱硝设备,能够有效减少污染物的排放,降低环境污染。
2.成本降低:由于节能减排所带来的成本优势,新型干法水泥生产工艺降低了生产成本,提高了企业的盈利能力。
3.产品质量提升:干法工艺在烧成和磨矿过程中的控制更加精细,可以得到更为均匀的产品颗粒度和化学成分,提高了水泥的品质。
4.工艺稳定性:干法工艺不受天气和供水限制,生产过程更加稳定可控,避免了湿法生产中可能出现的干扰因素。
工艺应用场景新型干法水泥生产工艺广泛应用于水泥行业中,适用于各类水泥生产企业。
特别适合以下场景:1.水资源匮乏地区:对于水资源匮乏的地区,干法工艺无需使用水,能够解决传统湿法生产中的水资源问题。
2.排放限制严格的地区:新型干法水泥生产工艺增加了脱硝和除尘等设备,能够有效降低排放的二氧化硫和氮氧化物等污染物,满足环保要求。
3.快速响应能力要求高的场景:传统湿法生产水泥需要较长时间的反应周期,而干法生产工艺响应速度快,可根据市场需求进行灵活的调整。
新型干法水泥生产工艺

新型干法水泥生产工艺引言随着社会的发展和环境保护意识的增强,传统湿法水泥生产工艺面临着越来越多的限制和挑战。
为了减少水泥生产中的能耗和环境污染,新型干法水泥生产工艺应运而生。
本文将介绍新型干法水泥生产工艺的原理、特点以及在实际应用中的效果。
原理新型干法水泥生产工艺通过在水泥生产过程中,尽量减少或避免使用水的方式,实现水泥的干燥混合、煅烧和磨矿等工序。
其原理主要包括以下几个方面:1.干燥混合:传统湿法水泥生产中,需要将原料与水混合形成石膏浆液,然后通过热风干燥将其干燥成粉末状。
而新型干法水泥生产工艺中,通过粉煤灰、煤粉等辅助燃料的燃烧产生的热能进行干燥,使原料直接成为粉末状,从而避免了水的使用。
2.煅烧过程:在传统湿法水泥生产中,石膏浆液需要在高温煅烧窑中进行煅烧,新型干法水泥生产工艺中为了替代石膏浆液,通常使用高硅石灰石、煤粉等作为原料,在高温下进行煅烧。
通过干燥处理的原料可以更有效地进行煅烧,提高煅烧效率和产量。
3.磨矿过程:在传统湿法水泥生产中,石膏浆液需要经过磨矿过程制成水泥,而新型干法水泥生产工艺中,在干燥混合和煅烧过程后获得的干粉状原料直接经过磨矿设备进行细磨,制成干法水泥。
这种省略了石膏浆液制备过程的干法生产工艺,不仅减少了水的使用,还可以提高水泥的品质。
特点新型干法水泥生产工艺相比传统湿法水泥生产工艺具有以下特点:1.节能环保:由于新型干法水泥生产工艺避免了水的使用,减少了水泥生产中的能耗和水资源的消耗。
同时,在干燥混合和煅烧过程中,通过合理利用辅助燃料燃烧产生的热能,可以达到节能环保的目的,减少了环境污染的排放。
2.降低成本:相比传统湿法水泥生产工艺,新型干法水泥生产工艺无需使用大量的水资源,节约了水泥生产过程中的用水成本。
同时,通过利用辅助燃料进行干燥、煅烧和磨矿,减少了传统水泥生产中所需的煤炭等能源消耗,可以有效降低生产成本。
3.提高水泥品质:由于新型干法水泥生产过程中避免了石膏浆液的使用,直接将干燥、煅烧后的原料进行磨矿,可以获得质量更稳定、品质更高的水泥产品。
新型干法水泥的生产工艺

新型干法水泥的生产工艺
新型干法水泥是一种新型的水泥生产工艺,相较于传统的湿法生产工艺,具有更高的能源效率和环境友好性。
以下是一般的新型干法水泥生产工艺的步骤:
1. 原材料准备:将石灰石、黏土、铁矿石等原材料按照一定比例混合,并粉碎成适当大小的颗粒。
2. 煅烧:将混合好的原材料送入炉内进行煅烧。
在高温下,原材料中的水分和有机物会被蒸发和分解,同时化学反应会发生,形成熟料。
3. 熟料磨矿:将煅烧后的熟料冷却,并通过磨矿设备将其细磨成适当的粉末。
4. 熟料混合:将磨矿后的熟料与适量的矿物掺合料(如石膏、矿渣等)进行混合,以调整水泥的性能。
5. 粉煤灰处理:如果使用粉煤灰作为掺合料,需要对其进行处理,去除其中的杂质,以保证水泥质量。
6. 包装与储存:将最终生产好的水泥通过包装设备进行包装,并储存到适当的仓库中,以待销售和使用。
需要注意的是,具体的生产工艺可能会因厂商和地区而有所不同,上述仅为一般
的步骤概述。
另外,新型干法水泥的生产工艺相对传统的湿法工艺来说更加节能环保,可以减少能源消耗和废气排放,具有较好的发展前景。
新型干法水泥生产简介
新型干法水泥生产简介一.新型干法水泥生产方法及工艺流程1. 新型干法水泥生产方法凡是以悬浮预热和预分解技术为核心,并把现代科学技术如,矿山计算机控制网络化开采,原料预均化,生料均化,高效多功能挤压粉末新技术、新型机械粉体输送装置、新型耐热、耐磨、耐火、隔热材料以及IT技术等广泛应用于水泥干法生产全过程,是水泥生产具有高效、优质、节约资源、清洁生产、符合环境保护要求和工艺设备大型化、生产控制自动化、实行科学管理的现代化水泥生产方法,称为新型干法水泥生产方法。
2.新型干法水泥生产工艺流程生产工艺流程示意图二.水泥生产工艺流程简介1.破碎系统生产水泥的原料种类繁多,属于钙质原料的石灰石、泥灰岩、白垩、大理岩等。
属于硅铝原料的有黏土、页岩、粉砂岩、砂岩等。
而破碎车间的主要作用就是将各种粒度不符合生产要求的原材料进行破碎,使其达到符合生产要求的粒度。
破碎作业可以通过不同的破碎系统来完成。
根据原料的物理机械性质、来料粒度、要求的破碎比,生产规模以及使用的破碎机等,可能会需要多个破碎系统。
破碎系统包括破碎级数和每级中的流程。
破碎四通的级数主要取决于工厂对该种原料要求的破碎比与所用破碎机的破碎比。
高破碎比的破碎机已达到要求的破碎比,只要一次破碎即可。
如果达不到要求就需要二级甚至三级破碎。
目前新型干法水泥生产线普遍使用的破碎设备是单段锤式破碎机和反击式破碎机。
1.1 单段锤式破碎机单段锤式破碎机是20世纪50年代才出现的新机型。
单段锤式破碎机的主要特点就是能将很大的矿石一次破碎成磨机需要的粒度。
它除具有一般锤式破碎机的基本特点外,还有为了破碎大块物料所特有的结构特点,使得进机最大粒度可以达到转子直径的2/3,而出料粒度可达25mm,因此它被广泛的用于破碎石灰石原料和粘土。
1.2 反击式破碎机反击式破碎机也是20世纪中期才出现的新机型,由于反击式破碎机的结构特点,使它更适应破碎含水量过大物料、硬度较高的物料。
因此它主要被用于破碎粉砂岩、页岩、硅质板岩等硬度较高的物料。
新型干法水泥生产工艺流程
新型干法水泥生产工艺流程
《新型干法水泥生产工艺流程》
随着工业技术的不断发展,新型干法水泥生产工艺流程也逐渐成熟并得到广泛应用。
干法水泥生产工艺以其节能、环保、高效的特点,逐渐替代了传统湿法生产工艺,成为水泥行业的主流生产方式。
新型干法水泥生产工艺流程主要包括原料破碎、燃料预处理、石灰石煅烧、煤粉预处理、磨料、熟料制备等环节。
首先,通过颚式破碎机将原料破碎成一定粒度的粉末。
然后,对煤粉和石灰石进行预处理,以保证燃料和原料的质量稳定。
接下来,石灰石经过煅烧过程,将石灰石中的二氧化碳释放出来,形成石灰石熟料。
随后,将煤粉和石灰石熟料混合后进行研磨,得到水泥熟料。
最后,水泥熟料经过熟料制备,即通过回转窑进行煅烧,形成成品水泥。
新型干法水泥生产工艺流程比传统湿法生产工艺具有很多优势。
首先,干法生产消耗的能源更少,能够大幅度降低生产成本。
其次,由于干法生产过程中不需要大量的水,因此生产过程中的废水排放量减少,对环境造成的污染也较小。
此外,新型干法水泥生产工艺流程生产出的水泥具有更好的品质和性能,可以满足更高要求的建筑需求。
总的来说,新型干法水泥生产工艺流程在节能环保、质量稳定等方面具有明显优势,是未来水泥行业生产方式的趋势。
随着
技术的不断提升和发展,相信新型干法水泥生产工艺流程将会在未来得到更广泛的应用。
新型干法水泥生产工艺
新型干法水泥生产工艺摘要:通过预分解窑干法水泥生产来了解了新型干法水泥生产工艺的工艺流程,熟悉新型干法水泥生产工艺的特点,知道新型干法水泥生产客观规律以及“均衡稳定”的重要关键词:新型干法水泥,原料预分化,预分解,均衡稳定。
悬浮预热器窑和预分解窑工艺是当代水泥工业用于生产水泥的最新技术,通常称为新型干法水泥技术。
新型干法水泥生产,就是以悬浮预热和预分解技术为核心,把现代科学技术和工业生产最新成就,例如原料矿山计算机控制网络化开采、原料预均化、生料均化、挤压粉磨、IT技术,及新型耐热、耐磨、耐火、隔热材料等广泛应用于干法水泥生产全过程,使水泥生产具有高效、优质、节能、环保和大型化、自动化及科学管理等特征的现代化水泥生产方法。
1.新型干法水泥生产工艺流预分解窑干法水泥生产是新型于法水泥生产技术的典型代1.1.1生料制备来自矿山的石灰石由自卸卡车运入破碎喂料仓,经石灰石破碎系统的破碎后由皮带输送机定量地送往预配料的预均化堆场。
黏土用自卸汽车运入或者从工厂的黏土堆棚中用铲斗车卸入黏土喂料仓,经喂料机喂人≠1200mm×1080mm双辊破碎机,在双辊破碎机中破碎到85%的黏土小于25mm后,经计量设备送入预配料的预均化堆场。
破碎后的石灰石、黏土和其他辅助原料各自从堆场由皮带输送机送往磨头喂料仓,经配料计量后,定量喂入原料磨进行烘干并粉磨。
烘干磨的热气体由悬浮预热器排出的废气供给,开启时则借助热风炉供热风。
粉磨后的生料用气力提升泵送人两个连续性空气均化库,进一步用空气搅拌均化生料和储存生料量地送往预配料的预均化堆场1.1.2熟料煅烧均化库中的生料经卸料、计量、提升、定量喂料后由气力泵送至窑尾悬浮预热器和分解窑水泥生产过程解炉中,经预热和分解后的物料进入回转窑煅烧成熟料。
回转窑和分解炉所用燃料煤由原煤经烘干兼粉磨后,制成煤粉并储存在煤粉仓中供给。
熟料经冷却机后,由裙板输送机、计量秤、斗式提升机分别送入熟料库内储存。
新型干法水泥生产工艺流程
新型干法水泥生产工艺流程新型干法水泥生产工艺是指在水泥生产过程中采用先进的干法工艺,通过破碎、磨矿、煅烧等环节,生产出高质量的水泥产品。
相比传统湿法水泥生产工艺,新型干法水泥生产工艺具有节能、环保、高效等优点,受到了越来越多水泥生产企业的青睐。
下面将介绍新型干法水泥生产工艺的具体流程。
原料准备新型干法水泥生产工艺的第一步是原料准备。
水泥的主要原料包括石灰石、粘土、铁矿石等。
这些原料首先需要经过破碎、研磨等工艺处理,使其达到适合进入煅烧系统的粒度和化学成分要求。
在原料准备过程中,需要确保原料的质量稳定,以保证水泥产品的品质。
原料研磨经过原料准备的原料进入研磨系统,进行进一步的研磨处理。
研磨系统通常采用立磨或者辊压机进行研磨,将原料研磨成细粉,以提高煅烧系统的燃烧效率和水泥品质。
煅烧煅烧是新型干法水泥生产工艺的关键环节。
经过研磨的原料进入旋窑或者立窑进行煅烧。
在煅烧过程中,原料经过高温煅烧,发生化学反应,形成水泥熟料。
煅烧系统通常采用先进的燃烧技术和热工控制技术,以提高煅烧系统的热能利用率和水泥熟料的品质。
熟料磨磨经过煅烧的水泥熟料需要进行熟料磨磨,将其磨成水泥粉。
熟料磨磨系统通常采用水泥立磨或者滚筒磨进行磨磨,以满足水泥产品的粒度要求。
成品包装经过熟料磨磨的水泥粉通过输送系统进入成品库,然后进行包装。
包装系统通常采用自动化包装设备,将水泥粉装入袋中,并进行称重、封口等操作,最终形成成品水泥产品。
除尘处理在新型干法水泥生产工艺中,除尘处理是非常重要的环节。
煅烧系统和熟料磨磨系统产生的烟气中含有大量粉尘和有害气体,需要通过除尘设备进行处理,以保护环境和改善工作环境。
总结新型干法水泥生产工艺流程包括原料准备、原料研磨、煅烧、熟料磨磨、成品包装和除尘处理等环节。
通过先进的设备和工艺技术,新型干法水泥生产工艺具有节能、环保、高效等优点,是水泥生产企业实现可持续发展的重要途径。
希望本文对新型干法水泥生产工艺流程有所帮助。
- 1、下载文档前请自行甄别文档内容的完整性,平台不提供额外的编辑、内容补充、找答案等附加服务。
- 2、"仅部分预览"的文档,不可在线预览部分如存在完整性等问题,可反馈申请退款(可完整预览的文档不适用该条件!)。
- 3、如文档侵犯您的权益,请联系客服反馈,我们会尽快为您处理(人工客服工作时间:9:00-18:30)。
浅谈新型干法水泥的生产工艺
摘要:随着我国“绿色低碳、节能减排”的呼声越来越高。
一些传统水泥生产工艺方法已经不符合新时期生产发展的需要,因此,对于生产工艺的更新已经刻不容缓,本文结合作者的工作实践经验,探讨了新型干法水泥生产的工艺。
关键词:悬浮预热器窑预分解窑工艺水泥生产工艺
悬浮预热器和预分解窑工艺是当代水泥工业用于生产水泥的最新技术,通常称为新型干法水泥技术。
新型干法水泥生产,就是以悬浮预热和预分解技术为核心,把现代科学技术和工业生产最新成就,例如,原料矿山计算机控制网络化开采、原料预均化、生料均化、挤压粉磨、it技术,及新型耐热、耐磨、耐火、隔热材料等广泛应用于干法水泥生产全过程,使水泥生产具有高效、优质、节能、环保和大型化、自动化及科学管理等特征的现代化水泥生产方法。
因此,新型干法水泥生产是一种新时期比较符合环保要求、符合高生产率要求的生产技术,以下是对新型干法水泥生产的特点、生产工艺流程、生产工序进行的介绍。
1 新型干法水泥生产的特点
1.1 优良的品质
生料设备全过程广泛采用现代均化技术,矿山开采、原料预均化、原料配料及粉磨、生料空气搅拌均化四个关键环节互相衔接,紧密配合,形成生料制备全过程的均化控制保证体系即“均化链”,从而满足了悬浮预热、预分解窑新技术对生料质量提出的严格要
求,产品质量可以与湿法媲美,使干法生产的熟料质量得到了保证,熟料28天抗压强度≥60-63 mpa。
1.2 低消耗
采用高效多功能挤压粉磨、新型粉体输送装置大大节约了粉磨和输送能耗;悬浮预热及预分解技术改变传统回转窑内物料堆积态的预热和分解方法,熟料的煅烧所需要的能耗下降。
总体来说,熟料热耗低,烧成热耗可降到 3000 kj/kg(718kcal/kg)以下,熟料综合电耗≤58 kwh/t,水泥综合电耗降低到了95kwh/t以下。
1.3 生产效率的大幅度提高
悬浮预热、预分解窑技术从根本上改变了物料预热、分解过程的传热状态,传热、传质迅速,大幅度提高了热效率和生产效率。
操作基本自动化,单位容积产量达150 ~180kg/(m3,h),劳动生产率可高达3000~6000t/(人年)。
1.4 减少污染,清洁环保
由于“均化链”技术的采用,可以有效地利用在传统开采方式下必须丢弃的石灰石资源;悬浮、预分解技术及新型多通道燃烧器的应用,有利于低质燃料及再生燃料的利用,同时可降低系统废气排放量、排放温度和还原窑气中产生的no2含量,减少了对环境的污染,为“清洁生产”和广泛利用废渣、废料、再生燃料及降解有害危险废弃物创造了有利条件。
1.5 装备大型化
装备大型化、单机生产能力大,使水泥工业向集约化方向发展。
水泥熟料烧成系统单机生产能力最高可达10000t/d,从而有可能建成年产数百万吨规模的大型水泥厂,大大的提高了水泥生产的效率。
1.6 生产控制自动化
利用各种检测仪表、控制装置、可靠的dcs集散型计算机控制系统及执行机构等对全厂生产线进行自动测量、检验、计算、控制、监测,以保证生产“均衡稳定”与设备的安全运行,使生产过程经常处于最优状态,达到优质、高效、低消耗的目的。
1.7 管理科学化
应用it技术进行有效管理,采用科学的、现代化的方法对所获取的信息进行分析和处理。
1.8 投资大,建设周期较长
新型干法水泥生产技术要求的生产设备科技含量高,所占资源、地质、交通运输等条件都要求比较高,而且耐火材料的消耗亦较大,因此整体投资比较大,目前吨水泥投资在300-350元左右;新建一条新型干法水泥生产线从“三通一平”到“竣工投产”的建设周期为12个月左右。
2 新型干法水泥生产工艺流程
预分解窑干法水泥生产是新型干法水泥生产技术的典型代表,图1为我国某日生产5000t熟料的预分解窑水泥生产线的生产全过程:
图一
2.1 生料制备
原料粉磨采用1台立磨系统,该系统的生产能力为400t/h,生料细度为80μm筛筛余<18%,入磨物料综合水份<8%,出磨物料综合水份<0.5%。
来自矿山的石灰石由自卸卡车运入破碎喂料仓,经石灰石破碎系统的破碎后由皮带输送机定量的送往预配料的预均化堆场。
黏土等辅助原料用自卸汽车运入或者从工厂的黏土堆棚中用铲斗车卸
入黏土等配料库,经喂料机喂人双辊破碎机,在双辊破碎机中破碎到85%的黏土小于25 mm后,经计量设备送入预配料的预均化堆场。
破碎后的石灰石、黏土和其他辅助原料各自从堆场由皮带输送机送往配料库。
由配料站来的原料经皮带输送机、入磨锁风阀送至原料立式磨内进行烘干、粉磨,粗粉返回磨内再次粉磨,合格生料随出磨气流进入旋风收尘器,细粉作为成品与从大布袋袋式收尘器(或电除尘器)、增湿塔收下的窑灰一起经提升机、空气输送斜槽送入1座φ22.5×52m有效储量为17000t的生料均化库内。
当原料磨停磨时,窑灰可另行输送至生料入窑系统中。
原料粉磨系统设有自动连续取样装置,试样经过x—荧光分析仪检测并由计算机自动控制和调整各种原料的配合比例,从而调整生料配比,保证出磨生料化学成份的合格与稳定。
2.2 预热分解
预热分解就是利用预热器和分解炉把生料的预热和进行部分的分解,从而代替回转窑部分功能,以达到缩短回窑长度,同时使窑内以堆积状态进行气料换热的一个过程,移到预热器内在悬浮状态下进行,可以使生料与同窑内排出的炽热气体充分混合,因此,可以增大气料接触面积,使得传热速度加快,热交换效率大大提高,达到提高窑系统生产效率、降低熟料烧成热耗的目的。
预分解技术的出现是水泥煅烧工艺的一次技术飞跃。
它是在预热器和回转窑之间增设分解炉和利用窑尾上升烟道,设燃料喷人装置,使燃料燃烧的放热过程与生料的碳酸盐分解的吸热过程,在分解炉内以悬浮态或流化态下迅速进行,使入窑生料的分解率提高到90%以上。
将原来在回转窑内进行的碳酸盐分解任务,移到分解炉内进行;燃料大部分(60%左右)从分解炉内加入,少部分(40%左右)由窑头加入,减轻了窑内煅烧带的热负荷,有利于生产大型化;由于燃料与生料混合均匀,燃料燃烧热及时传递给物料,使燃烧、换热及碳酸盐分解过程得到优化。
因而具有优质、高效、低耗等一系列优良性能及特点。
2.3 熟料煅烧
熟料烧成系统由回转窑、双系列5级低压损旋风预热器和ttf
分解炉或ndf分解炉组成,日产熟料5000吨,熟料热耗710*4.18 kj/(kg.熟料)。
均化库中的生料经卸料、计量、提升、定量喂料后由提升机送至窑尾悬浮预热器和分预分解炉中,经预热和分解后的物料进入进
入1台φ4.8×72(或74)m,三档支撑,斜度为3.5%,转速0.396~3.96r/min的回转窑煅烧成熟料。
窑头及分解炉均配有多通道的煤粉燃烧器。
回转窑和分解炉所用燃料煤由原煤经烘干兼粉磨后,制成煤粉并储存在煤粉仓中供给。
熟料通过1台128.6m2能力5500t/h第三代高效控制流推动篦式冷却机,篦冷机出口处设有一台锤式破碎机保证出冷却机熟料粒度≤25mm,熟料出冷却机的温度为环境温度+65℃。
冷却后熟料经链斗输送机或斗式提升机送至1座φ45m熟料帐蓬库,其储存量为52500t,库的有效储存量为45000t,有效储期10天。
2.4 水泥制成
水泥粉磨选用2台φ1700×1200mm辊压机+2台φ4.2×13m球磨机系统,配用2台v型选粉机和2台n-3000的改进型o-sepa选粉机。
当入磨物料粒度≤25mm,水泥比表面积为320-350m2/kg(粉磨p.042.5普通硅酸盐水泥)时,系统生产能力为320-360t/h。
水泥粉磨是水泥制造的最后工序,也是耗电最多的工序。
其主要功能在于将水泥熟料(及胶凝剂、性能调节材料等)粉磨至适宜的粒度(以细度、比表面积等表示),形成一定的颗粒级配,增大其水化面积,加速水化速度,满足水泥浆体凝结、硬化要求。
熟料、石膏经定量喂料机送入水泥磨中粉磨。
水泥磨与选粉机一起构成所谓的圈流水泥磨,粉磨时也可根据产品要求加入适量的混合材料与熟料、石膏一同粉磨生产不同种类或标号的水泥品种。
粉磨后的水泥经斜槽和提升机等送至8座φ16×22m的圆库,水泥总储量为:8×7000=56000吨,总储期7天的水泥圆库储存。
水泥储库的一部分水泥经包装机包装为袋装水泥,经火车或汽车运输出厂,另一部分由散装专用车散装出厂。
其他不同规模的预分解窑水泥生产线、同规模而不同生产厂家的预分解窑水泥生产线的工艺流程大体上与前述相似,不同之处主要是生产过程中的某些工序和设备不尽相同。
3 新型干法水泥生产工序
从上述的日产5000t熟料的预分解窑水泥生产线的工艺流程不难看出,新型干法水泥生产可以概括成生料制备、熟料煅烧、水泥制成这三大生产过程,但具体生产工序之多,远不只是“两磨一烧”三个工序。
一般而言,具体生产主要包括以下几大工序:①原料、燃料、材料的选择及入厂;②原料、燃料、材料的加工处理与预均化;③原材料的配合;④生料粉磨及废气处理;⑤生料的调配、均化与储存及入窑喂料系统;⑥熟料煅烧及冷却;⑦熟料、石膏、混合材料的储存与准备;⑧熟料、石膏、混合材料的在水泥配料站配合及粉磨(即水泥粉磨);⑨水泥储存、包散装及成品发运。
4 结束语
总之,在整个生产过程中,为确保原料、燃料、材料及生料、熟料、水泥符合要求,生产过程的各个工序必须进行生产控制与质量监控,应由具备较高专业技能水平的人员进行规范化操作,这样才能确保水平生产成品达到硅酸盐水泥限定的各项技术指标,保证
水泥生产质量,提高生产效率与技术水平。
注:文章内所有公式及图表请用pdf形式查看。