钢制车轮生产工艺
中国第二条辗钢整体车轮生产线及其工艺技术水平分析

中国第二条辗钢整体车轮生产线及其工艺技术水平分析3郭玉玺 杜国器 张 平(太原重型机械(集团)有限公司030024太原)摘 要 介绍了太原重型机械(集团)有限公司引进原加拿大钢轮厂(CS W )车轮生产主要设备,并发挥自己的优势,自行设计、再建成功的中国第二条辗钢整体车轮生产线。
对新建的生产线装备和工艺技术水平作了客观地分析和评价。
关键词 辗钢车轮 生产线 技术水平 分析 太钢车轮厂(T S W )1 引言加拿大钢轮厂(CS W )于1994年关闭一年后,其主要设备被太原重型机械(集团)有限公司购进。
1997年,在中国太原诞生了一座新钢轮厂,这就是具有47年设计制造重型机器产品历史的太原重型机械(集团)有限公司新组建的太重钢轮厂(T S W )。
太重正是移植和利用了原CS W 车轮生产的主要设备,自行设计、再建成功了继马钢车轮轮箍系统之后的中国第二条辗钢整体车轮生产线。
整个生产工艺与设备从冶炼到锻造、轧制、热处理、机加工、在线检验(无损检测)和性能试验自成体系,能够满足AA R 标准、中国铁道行业标准和其他先进标准对现代车轮制造工艺技术的要求,可制造直径为 610mm ~ 1300mm 的各类铁道车辆用辗钢整体车轮和各种工业用钢轮。
车轮的设计年产量为6×104t ,约16×104个。
1997年12月,铁道部组织专家对T S W 按铁道部四方车辆研究所设计的具有更高结构强度的低应力S形辐板车轮( 840HD S )图纸试生产的产品,进行了质量检验、抽样解剖试验和生产实地考察认证,认为生产线具备了生产铁道车辆用辗钢整体车轮的条件,产品的理化性能指标、表面质量和形位公差均达到了TB T 2817—1997和设计图纸要求,正式批准T S W 于1998年1月1日起投入批量生产。
2 生产工艺技术水平分析2.1 执行较为严格的技术标准和规范收稿日期:1998203227。
郭玉玺:男,1949年生,高级工程师。
钢制车轮的内容
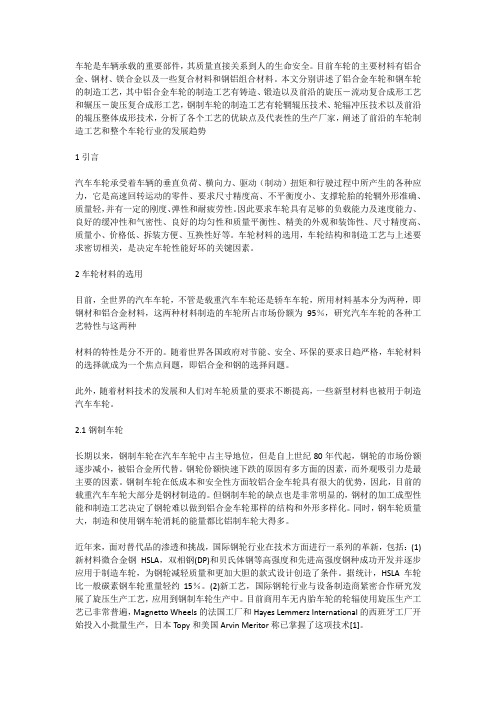
车轮是车辆承载的重要部件,其质量直接关系到人的生命安全。
目前车轮的主要材料有铝合金、钢材、镁合金以及一些复合材料和钢铝组合材料。
本文分别讲述了铝合金车轮和钢车轮的制造工艺,其中铝合金车轮的制造工艺有铸造、锻造以及前沿的旋压-流动复合成形工艺和辗压-旋压复合成形工艺,钢制车轮的制造工艺有轮辋辊压技术、轮辐冲压技术以及前沿的辊压整体成形技术,分析了各个工艺的优缺点及代表性的生产厂家,阐述了前沿的车轮制造工艺和整个车轮行业的发展趋势1引言汽车车轮承受着车辆的垂直负荷、横向力、驱动(制动)扭矩和行驶过程中所产生的各种应力,它是高速回转运动的零件、要求尺寸精度高、不平衡度小、支撑轮胎的轮辋外形准确、质量轻,并有一定的刚度、弹性和耐疲劳性。
因此要求车轮具有足够的负载能力及速度能力、良好的缓冲性和气密性、良好的均匀性和质量平衡性、精美的外观和装饰性、尺寸精度高、质量小、价格低、拆装方便、互换性好等。
车轮材料的选用,车轮结构和制造工艺与上述要求密切相关,是决定车轮性能好坏的关键因素。
2车轮材料的选用目前,全世界的汽车车轮,不管是载重汽车车轮还是轿车车轮,所用材料基本分为两种,即钢材和铝合金材料,这两种材料制造的车轮所占市场份额为95%,研究汽车车轮的各种工艺特性与这两种材料的特性是分不开的。
随着世界各国政府对节能、安全、环保的要求日趋严格,车轮材料的选择就成为一个焦点问题,即铝合金和钢的选择问题。
此外,随着材料技术的发展和人们对车轮质量的要求不断提高,一些新型材料也被用于制造汽车车轮。
2.1钢制车轮长期以来,钢制车轮在汽车车轮中占主导地位,但是自上世纪80年代起,钢轮的市场份额逐步减小,被铝合金所代替。
钢轮份额快速下跌的原因有多方面的因素,而外观吸引力是最主要的因素。
钢制车轮在低成本和安全性方面较铝合金车轮具有很大的优势,因此,目前的载重汽车车轮大部分是钢材制造的。
但钢制车轮的缺点也是非常明显的,钢材的加工成型性能和制造工艺决定了钢轮难以做到铝合金车轮那样的结构和外形多样化。
浅谈车轮的生产技术的发展现状

AUTO PARTS | 汽车零部件浅谈车轮的生产技术的发展现状袁水俊大亚车轮制造有限公司 江苏省镇江市 212300摘 要: 随着新一轮汽车科技工业革命和汽车产业结构变革的发展浪潮正在迅速席卷整个全球,汽车行业新一代材料、新工程技术广泛应用,新模式、新服务业态不断涌现,为了有效应对这种新发展浪潮,各大型汽车部件制造商和企业分别提出了产品轻量化、智能化、网络化、共享自动化等五大发展战略方向,其中,轻量化发展是不断改善现代汽车动力燃料利用经济性的一个有效途径。
而车轮作为现代汽车非常重要的汽车零部件之一,不但要求外形美观,还要努力实现产品轻量化,保证工作可靠性。
目前我国汽车铝合金车轮制造产业的经济发展只有十几年的发展历史,是一个新兴的大型汽车专用零部件制造产业,但发展迅猛。
这种车轮是由一个轮辋和各种形状的轮辐部件组成,介于汽车车轮和传动车轴之间,是能够承受汽车负荷的一种旋转传动组件。
车轮产业是现代汽车当中的一个重要的零部件,不但直接影响着我国汽车的驾驶安全性和运动操控性,同时也对我国汽车的安全节能、环保发展具有重要的战略影响。
关键词:铝合金车轮 生产技术 现状 发展车轮作为汽车整车行驶部分的主要承载件,是左右整车性能最重要的安全部件。
它不仅要承受静态时车辆本身垂直方向的自重载荷,更需要经受车辆行驶中来自各个方向因起动、制动、转弯、石块冲击、路面凹凸不平等各种动态载荷所产生的不规则应力的考验。
作为汽车最为重要的部件之一,车轮可以说是衡量整车质量和档次的最主要象征之一。
1 汽车车轮生产技术的现状1.1 车轮的材料类别随着经济的发展,材料工艺也在不断进步,目前市场上车轮使用的材料主要有:钢圈、铝合金车轮、镁合金车轮、碳纤维等。
1.1.1 钢轮:钢轮主要材料为合金钢,分体式轮辐和轮辋,采用拼接、焊接、挤压等工序进行装配,1.1.2 铝合金车轮:采用牌号A356的铸造铝合金或者牌号为6061的锻造铝合金车轮,铝合金材料工艺可塑性强,外观花样多,加工精度高,消费者使用起来有很强的观赏性和舒适性。
轮胎基础知识及生产工艺(半钢)
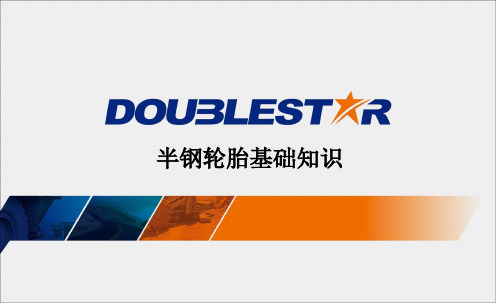
三角胶: 填充于胎圈钢丝及胎侧部位的橡胶提供胎圈钢丝到胎侧硬度(刚性)过渡、加强胎圈强度 耐磨胶: 一层硬质橡胶,用来防止胎圈与轮圈突缘的摩擦、腐蚀
半钢胎规格标示方法
冠带条(CAPPLY):
冠带条是提升轮胎动平衡以及均匀性性能、保证轮胎行驶舒适性的主要部件,本设计采 用高密度改性尼龙材料,起到箍紧带束层,减少钢丝之间剪切力,降低生热的目的。从 而提高轮胎的高速性能,减少滚动阻力。并且采用先进螺旋缠绕技术,显著提高了轮胎 的动平衡和均匀性
轮胎各部件作用
带束层(BELT):
品牌名称 均匀性点
通过与车轮振动的最小位 置(用白色圆圈表示)进 行比照,防止车体的振动。
DOUBLESTAR
动平衡点
该标识指示轮胎的滚动方向
制造编号/制造记号
生产的批次号 例如“1811”表示于2011年的 第18个星期制造 “ 0810” 表 示 于 2010 年 的 第08个星期制造
轮胎的规格
更重要的是取决于轮胎的缓冲性能。缓冲性能就是轮胎在负荷下的径
向变形量。
• 行驶的安全性能: 对于汽车而言,轮胎是一个安全部件。为保证汽车
轮胎结构
轮胎结构
• 轿车胎构成 – 胎面 • 冠带层、带束层
– 胎侧、子口耐磨胶
– 胎体 – 气密层 – 胎圈、三角胶 – 子口护布
半钢轮胎结构特点
• 轿车胎结构特点 – 胎面一般采用单一胶料,可不做分层设计 – 在带束层上增加一至两层纤维冠带层,提高轮胎高速性能
A1 A2 A3 A4
5 10 15 20
B C D E
轮式工程机械车轮用型钢技术条件
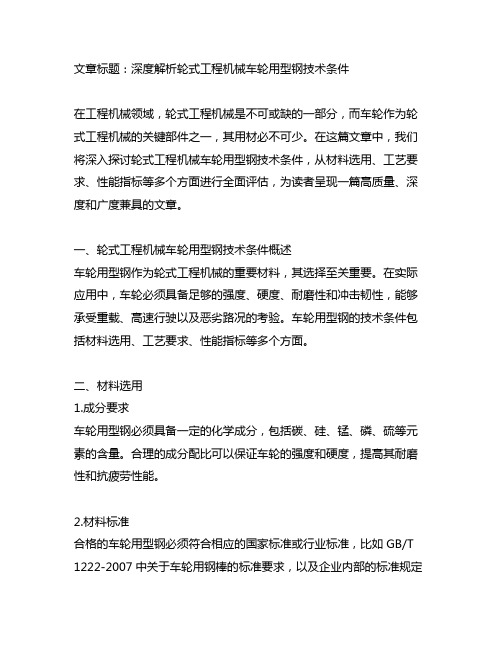
文章标题:深度解析轮式工程机械车轮用型钢技术条件在工程机械领域,轮式工程机械是不可或缺的一部分,而车轮作为轮式工程机械的关键部件之一,其用材必不可少。
在这篇文章中,我们将深入探讨轮式工程机械车轮用型钢技术条件,从材料选用、工艺要求、性能指标等多个方面进行全面评估,为读者呈现一篇高质量、深度和广度兼具的文章。
一、轮式工程机械车轮用型钢技术条件概述车轮用型钢作为轮式工程机械的重要材料,其选择至关重要。
在实际应用中,车轮必须具备足够的强度、硬度、耐磨性和冲击韧性,能够承受重载、高速行驶以及恶劣路况的考验。
车轮用型钢的技术条件包括材料选用、工艺要求、性能指标等多个方面。
二、材料选用1.成分要求车轮用型钢必须具备一定的化学成分,包括碳、硅、锰、磷、硫等元素的含量。
合理的成分配比可以保证车轮的强度和硬度,提高其耐磨性和抗疲劳性能。
2.材料标准合格的车轮用型钢必须符合相应的国家标准或行业标准,比如GB/T 1222-2007中关于车轮用钢棒的标准要求,以及企业内部的标准规定等。
三、工艺要求1.工艺流程车轮用型钢的生产工艺包括钢水冶炼、连铸、轧制、热处理等多个环节,每个环节的工艺参数都需严格控制,以确保最终产品的质量。
2.热处理工艺热处理是影响车轮用型钢性能的关键环节,包括淬火、回火、正火等工艺,其中淬火温度、保温时间、冷却介质等参数的选择对最终的车轮性能有着重要影响。
四、性能指标1.强度指标车轮用型钢的抗拉强度、屈服强度、硬度等都是重要的性能指标,与车轮的承载能力和使用寿命密切相关。
2.耐磨性车轮在使用过程中会受到不同程度的磨损,因此其耐磨性能是衡量其质量好坏的重要标准之一。
3.冲击韧性在恶劣路况下,车轮经常会受到来自路面的冲击负荷,因此其冲击韧性也是需要重点考虑的性能指标。
五、总结与展望在本文中,我们对车轮用型钢技术条件进行了全面评估,从材料选用、工艺要求、性能指标等多个方面进行了深入探讨。
通过本文的阐述,相信读者对车轮用型钢的相关知识有了更深入的了解,更能够在实际应用中选择合适的车轮材料。
车轮制作经验谈

通过近36年的研发工作,笔者学习了许多不同领域的知识,不仅仅是在学校学的书本里的知识,还包括工作中得来的。
这些知识的积累,使得笔者对创新有了更深的体会,那就是不论是做技术,还是管理,都需要将这许多知识揉搓、磨合,擦出火花,让这些想法再雕琢、打磨,生成创意,最后经过实践锤炼,转化为生产力,这样才能产生出有价值的方案。
当然,知识需要积累,需要回顾,更需要总结。
本文是笔者结合工作设计关于车轮制作的一些经验之谈,供同行参考借鉴。
合理利用塑性变形,消除弹性变形车轮制作工艺就是一个不断与弹性变形、塑性变形作斗争的过程,有时要想方设法消除弹性变形,合理实现塑性变形,有时则要有效利用弹性变形,顺势而为。
案例1 在开发13.5×4.5B滚型车轮时,轮辋轮辐压装后,胎圈座(控制轮胎径向圆跳动的轮廓)径向圆跳动公差值不大于1.2mm,合格;而轮缘(控制轮胎轴向窜动的轮廓)端面圆跳动公差值为1.5mm,超差0.3mm,达不到质量要求。
通过设计两半式收缩模,将不合格轮辋轮缘撑宽近1mm,如图1所示,再复压,返修合格率达95%。
剩余5%的不合格件,首先在车床上将轮缘撑宽,再次复压,如图2所示,全部返修合格。
通过这些手段,可将不合格品全部返修合格。
但如果其他规格车轮也照葫芦画瓢,还是有问题的。
如现有的12×4.0B车轮与正在开发的13.5×4.5B车轮是有区别的,材料厚度不同、直径不同、宽度不同、发生的塑性变形量也不同,13.5×4.5B车轮就刚好处在塑性变形与弹性变形之间,设计时将冷滚模宽度比产品的设计宽度宽0.5mm,也就是让轮辋成形时加宽,压配时加大塑性变形量,消除弹性变形,经过验证,一次交检合格率达100%。
这就是一个消除弹性变形,合理实现塑性变形工艺突破的典型案例。
图1 撑轮辋受力图2 压配案例2 轮辐零件图如图3所示,使用从500t油压机到1600t油压机对轮辐压形,轮辐平面度总是大于0.3mm,达不到工艺要求,主要原因是原材料本身平面度差。
浅谈钢制车轮的生产及质量改进
浅谈钢制车轮的生产及质量改进摘要:据行业内粗略估计,钢制车轮的市场份额从20世纪80年代初期的90%以上逐步萎缩到90年代后期的不足50%。
快速下滑的销售业绩引起了国际钢轮制造业、钢铁制造业和钢制车轮设备制造商的高度重视,其紧密合作的结果推动了钢轮制造技术的革新和市场份额的理性恢复。
本文对钢制车轮的生产及质量改进进行分析,以供参考。
关键词:钢制车轮;生产;质量改进引言近年来,随着铝轮产品的出现,便以质量轻、更好的圆度和均质性、美观的优势取得市场的认可,致使传统的钢轮产品出现了份额萎缩。
尽管铝车轮具有众多优点,但是由于其价格较贵,所以在大批量生产的轿车和轻型商用车中,还是采用钢制车轮。
1车轮改进的重要性车轮作为列车行走系统关键零部件之一,其运行环境复杂,在服役过程中承受着侧向力及径向垂直力共同作用,需要较高的力学性能和抗疲劳性能方能满足运行要求。
在机车、客车及高铁用车轮制造标准中规定所用车轮必须使用辗钢整体车轮。
在车轮的锻造过程中,目前采用分步锻造+辐板轮辋轧制的工艺,其优点是通过轧制保证各部位拥有较好的金属流线,产品受力区域经轧制后金属更加致密,各部位余量能够精准控制,分布均匀,提高材料利用率等。
但是轧制成形过程也是整个车轮成形的关键,参数调整及优化对车轮热成形形状影响较大。
2车轮行业发展把握“一带一路”机会,促进车轮企业融入全球配套。
车轮产品以其极具优势的国际竞争力,出口市场逐年增加,其中铝车轮出口增幅达到10%左右,整体车轮出口占总产量的40%左右,随着车轮产业的快速发展,产业垂直分工加速,车轮产品利润空间越来越小,造成产业盈亏平衡点逐渐上移,规模化发展势在必行。
由于售后市场需求的大幅提升,车轮企业的新增产能和过剩产能从前端OEM配套逐步延伸到AM售后服务市场,推进以市场为导向的区域市场拓展和扩张。
企业为最大限度地减少生产所占用的资源、降低管理运营成本,提高生产效率,注重信息化水平,追求零库存和对市场的快速反应,零部件企业逐步引入6S、精益生产、TQM、TPM与生产流程再造,加强生产管理的过程控制、提高制造系统的灵活性、合理布局生产系统运行过程,生产方式从粗犷式向精益化发展转型。
动车组车轮的制造工艺与质量控制
动车组车轮的制造工艺与质量控制摘要:高速铁路的安全运输是关系到国计民生的重大问题。
车轮是高速列车的关键安全部件之一,技术标准高,生产难度大。
文章介绍了动车组车轮的质量标准、工艺设计和优化,以及坯料冶炼和热处理的工艺方法。
研制的车轮具有内部质量好、物理机械性能高的优点,从而保证了产品的安全性和可靠性。
从产品工艺设计、工艺控制、质量体系等方面保证标准车轮质量的动态稳定性。
关键词:动车组;制造工艺;质量控制中图分类号:RT987文献标识码;A1动车组车轮制造工艺1.1钢坯冶炼工艺钢坯的冶金质量是影响车轮安全可靠的关键因素。
近年来,马钢在方坯无氧化防护铸造技术和结晶器电磁搅拌技术方面取得了很大进展,效果明显。
(1)采用小型电动搅拌与大型电动搅拌相结合的控制方法,有效地防止了碳偏析和枝晶偏析。
(2)采用清洁度控制技术,实现夹杂物的细小分散分布。
(3)加强连铸的保护浇注作业,特别是加强二次氧化的控制,优化覆盖剂和保护渣的操作。
.(4)设置合理的成分控制范围,在标准中允许精确控制硫和铝的含量。
1.2车轮热成型工艺采用数值模拟的方法对380mm车轮加热用圆坯的温度变化进行了模拟分析。
图1钢坯加热过程温度分布由图1可见,当加热时间达到5h时,钢坯温度总体较均匀。
图2车轮用Φ380mm圆坯加热过程数值模拟与实测结果对比1.3热处理工艺热处理工艺的关键是如何有效地发挥v的强化作用和晶粒细化作用,从而提高车轮的强韧性匹配,提高车轮的质量。
用formastor热模拟试验机测定了d2和er8的cct曲线,用金相显微镜观察了显微组织,并测定了5kg维氏硬度。
为热处理工艺参数的设计提供了参考。
Cct曲线如图3所示。
图3D2/ER8的CCT曲线3质量控制3.1标准动车组质量管理体系的构建针对标准动车组认证后的大批量生产,根据零缺陷管理体系和产品实现过程中的要求,以iris和iso9001标准体系为依据,从标准车轮的技术条件入手,根据目前的生产条件、管理水平和员工的业务素质,提出了一种基于iso9001标准体系的车轮零缺陷管理系统,针对高速高风险的特点,注重预防,准确识别产品安全特征,全面识别产品和工艺生产模式,明确工艺参数和产品特征值控制要求,明确设备精度参数要求,加强工艺控制,实施生产过程各要素跟踪,加强工艺监督,明确工作责任,实施严格的质量追溯制度。
车轮螺母生产工艺流程
车轮螺母生产工艺流程下载温馨提示:该文档是我店铺精心编制而成,希望大家下载以后,能够帮助大家解决实际的问题。
文档下载后可定制随意修改,请根据实际需要进行相应的调整和使用,谢谢!并且,本店铺为大家提供各种各样类型的实用资料,如教育随笔、日记赏析、句子摘抄、古诗大全、经典美文、话题作文、工作总结、词语解析、文案摘录、其他资料等等,如想了解不同资料格式和写法,敬请关注!Download tips: This document is carefully compiled by theeditor. I hope that after you download them,they can help yousolve practical problems. The document can be customized andmodified after downloading,please adjust and use it according toactual needs, thank you!In addition, our shop provides you with various types ofpractical materials,such as educational essays, diaryappreciation,sentence excerpts,ancient poems,classic articles,topic composition,work summary,word parsing,copy excerpts,other materials and so on,want to know different data formats andwriting methods,please pay attention!车轮螺母生产工艺流程一、原材料准备阶段。
在进行车轮螺母的生产之前,首先需要准备好所需的原材料和设备。
钢铁锻造法
钢铁锻造法钢铁锻造法是指通过施加大力量的压力和冲击,使金属材料在金属变形的过程中改变其形状和外观的一种加工工艺。
钢铁锻造法是金属加工领域中最古老、最基础的工艺之一,被广泛用于制造汽车、飞机、桥梁、导弹、军工等领域。
本文将就钢铁锻造法进行详细介绍。
(1)按照加工方式划分钢铁锻造法可以分为自由锤锻和机械锤锻两大类。
自由锤锻是指人力或动物力通过锤子撞击金属工件,使其产生塑性变形的过程。
机械锤锻是指利用锤头在锻模上的撞击作用,使金属逐渐变形的过程。
一般来说,大型工件采用自由锻造,中小型工件采用机械锻造。
(2)按照锻模类型划分钢铁锻造法可以分为自由锻模和闭式锻模两大类。
自由锻模是指金属在锤击下自由变形的锻模。
闭式锻模是指金属在锻模内形成所需形状的锻模。
闭式锻造是通过锻模的制作和加工来实现的。
(3)按照材料状态划分钢铁锻造法可以分为热锻和冷锻两大类。
热锻是指在金属达到一定热度时进行的锻造;冷锻则是指在室温下进行的锻造。
一般来说,热锻可以更好地改善金属的塑性和延展性,但是因为需要进行加热和冷却等工序,热锻的加工难度更大,成本也更高。
2. 钢铁锻造法的工艺流程(1)选材:选择适合锻造工艺的金属材料。
(2)加热:将金属材料加热至适当的温度,使其塑性达到最佳状态。
(3)锻造:在加热的状态下,利用自由锤或机械锤等设备进行金属变形。
(4)退火:在锻造完成后,将金属材料加热至一定温度,使其内部应力得到释放和分散,从而增加材料的延展性和韧性。
(5)表面处理:对金属工件表面进行打磨、切削、清洗等处理,使其表面平整、光滑,提高其外观质量。
钢铁锻造法是一种重要的加工工艺,其应用范围非常广泛。
(1)汽车制造业:例如汽车发动机、转向架、车轮等。
(2)机械制造业:例如钢材结构件、机床导轨、行星齿轮等。
(3)航空、航天和国防工业:例如航空发动机、导弹、火箭等。
(4)能源领域:例如核电设备、原油钻探机械等。
(5)交通运输领域:例如火车车轮、碾压道路机等。
- 1、下载文档前请自行甄别文档内容的完整性,平台不提供额外的编辑、内容补充、找答案等附加服务。
- 2、"仅部分预览"的文档,不可在线预览部分如存在完整性等问题,可反馈申请退款(可完整预览的文档不适用该条件!)。
- 3、如文档侵犯您的权益,请联系客服反馈,我们会尽快为您处理(人工客服工作时间:9:00-18:30)。
钢制车轮生产工艺
钢制车轮生产工艺是指将钢材经过一系列的工艺流程加工成最终的车轮产品的过程。
下面将详细介绍一下钢制车轮的生产工艺。
首先是原材料的准备。
钢制车轮的主要原材料是高强度钢材,通过对钢材进行化学成分分析,以及进行金相分析,确定其质量。
然后根据车轮的设计要求,确定钢材的硬度和强度等机械性能。
第二步是钢材的预处理。
首先,对钢材进行退火处理,以消除应力和改善塑性。
然后进行锻造处理,将钢材加热到一定的温度,然后用锻压机将其锻造成具有一定形状和尺寸的车轮毛坯。
第三步是车轮的成型和加工。
首先,将锻造好的车轮毛坯进行热处理,以提高其显微组织和力学性能。
然后进行车轮的精整,通过专用的机床对车轮进行车削、铣削、钻孔等加工操作,将车轮毛坯加工成具有一定精度和表面质量的车轮毛胚。
第四步是车轮的组装。
将车轮毛胚上的轮缘和轮辐进行组装,并进行校验和调整,以确保车轮的几何尺寸和轮轴孔位的精度和间隙符合要求。
然后进行焊接等加工,将车轮的各个部件焊接在一起。
第五步是车轮的表面处理。
对车轮进行表面喷砂或喷丸处理,以去除车轮表面的氧化物等污染物。
然后对车轮进行酸洗处理,以去除车轮表面的氧化层,提高车轮的表面质量和附着力。
最后一步是车轮的检验和质量控制。
对车轮的各项技术指标进行检测,包括轮缘直径、轮缘高度、轮辐的刚度和强度等。
对车轮进行质量控制,确保产品的合格率和质量稳定性。
综上所述,钢制车轮的生产工艺包括原材料准备、钢材的预处理、车轮的成型和加工、车轮的组装、车轮的表面处理和车轮的检验和质量控制等环节。
通过这些工艺步骤,可以生产出具有高强度、高精度和表面质量稳定的钢制车轮产品。