模具常见问题分析及其解决方法
模具常见问题及解决方法

本次培训到此结束,谢谢!
8、产品不容易脱出ห้องสมุดไป่ตู้
通常在对部品进行排料时就应考虑部品的出料问题。一般情况下,我们采用以下几 种出料方式: ⑴:风吹出; 对于一些较小的产品,利用吹气销将其吹出。 ⑵:在重心作用下,产品自然滑落; 在下模铣一出料缺口,利用部品的自身重力滑落。 ⑶:零件推零件; 借助条料的传送力,将冲压完成后的部品推出模具。此时应注意模具的升料高度。 ⑷:零件由条料带出; 此方式一般运用在模具在最后工步对部品的外形进行整体落料的情况下采用,通过大力 弹簧将部品重新压入到条料中,在条料送出的同时将部品一同带出。 ⑸:零件整体落料; 在考虑运用此方式之前必须确认部品的毛刺方向是否允许? 为了避免部品粘附在卸料板或凹模板表面,通常会在最后工位的卸料板或凹模板上使用 小顶杆。
80
t
5° ~10°
°~
85
°
第 一 次 弯 曲
第 二 次 弯 曲
R
回弹抵消
回弹抵消
二次弯曲加工
7、模具容易磨损
影响因素:⑴:模具材料的选用; ⑵:模具润滑不够; ⑶:模具材质热处理不良; ⑷:模具间隙太小; 解决对策:⑴:选用合理优质的模具材料; ⑵:合理的润滑; ⑶:模具材料施以表面处理;(如镀钛) ⑷:选择合理的间隙;
5、冲头容易断裂
影响因素:⑴:由于模具间隙不均匀,冲头受到横向负荷而折断; ⑵:模具间隙小使冲头在脱料时受到横向负荷而折断; ⑶:冲头因导引不良使得冲头在冲切时有偏移现象; ⑷:冲头刃部长度过长; ⑸:冲头阶段部发生应力集中; ⑹:冲头所选用的材料; ⑺:冲屑堵塞造成冲头负荷增大; ⑻:卸料板因受到侧压而倾斜; 解决对策: ⑴:模具间隙要均匀; ⑵:模具间隙取大; ⑶:正确的冲头导引; ⑷:冲头刃部长度减短; ⑸:冲头阶段部施以R角; ⑹:使用高韧性的冲头材料; ⑺:凹模直段部取短及下模有确实的逃孔设计; ⑻:防止卸料板发生倾斜;
塑料模具设计常见问题及改进方法

塑料模具设计常见问题及改进方法塑料模具是塑料制品生产的关键工具,其设计质量直接影响着产品的成型质量和生产效率。
在塑料模具设计过程中,常会遇到一些常见问题,例如设计不合理、成型不良等。
本文将介绍塑料模具设计常见问题及改进方法。
一、常见问题1.设计不合理在塑料模具设计过程中,设计不合理是最常见的问题之一。
设计不合理会导致模具结构复杂、易损件过多、成本增加等问题。
这些问题都会影响模具的使用寿命和生产效率。
2.成型不良成型不良也是常见的问题之一。
成型不良可能是由于模具设计不合理、材料选择不当、成型参数设置不正确等原因导致的。
成型不良会影响产品的质量,甚至导致生产事故。
3.模具寿命短模具寿命短是塑料模具常见问题之一。
模具寿命短可能是由于材料选择不当、表面处理不到位、使用条件不合理等原因导致的。
模具寿命短会增加生产成本,降低生产效率。
4.技术水平低一些塑料模具设计人员技术水平低也是常见问题。
技术水平低会导致设计不合理、制造精度低、模具寿命短等问题。
5.应力集中在塑料模具设计中,应力集中也是一个常见问题。
应力集中可能导致模具开裂、损坏等问题,从而影响模具的使用寿命和生产效率。
二、改进方法为了解决设计不合理的问题,可以通过优化设计来改进。
优化设计可以减少模具结构复杂度、减少易损件、降低成本等。
优化设计可以采用CAD软件进行模拟分析,找出设计不合理的地方并进行改进。
2.增加冷却系统成型不良的问题可以通过增加冷却系统来改进。
增加冷却系统可以有效降低成型温度、缩短成型周期、提高产品质量。
合理的冷却系统设计可以通过有限元分析和实验验证。
3.优化材料选择模具寿命短的问题可以通过优化材料选择来改进。
优化材料选择可以选择抗磨损、抗腐蚀、高强度的材料,从而提高模具的使用寿命。
还可以采用表面处理技术来提高模具的使用寿命。
为了解决技术水平低的问题,可以通过提高技术水平来改进。
提高技术水平可以通过培训、学习、实践等方式来进行。
提高技术水平可以提高设计水平、精度水平、制造工艺水平等。
模具注塑常见问题及解决方法

模具注塑常见问题及解决方法模具注塑是一种常见的制造工艺,广泛应用于汽车、电子、家电等行业。
然而,在注塑过程中常会遇到一些问题,例如产品质量不合格、生产效率低下等。
本文将针对这些常见问题进行分析,并提出相应的解决方法。
1. 产品尺寸不准确产品尺寸不准确是模具注塑过程中常见的问题之一。
造成尺寸不准确的原因可能有很多,例如模具设计不合理、注塑机调试不当等。
解决这个问题的方法是对模具进行优化设计,确保模具的尺寸精度和稳定性;同时,对注塑机进行精确调试,保证注塑过程的准确性。
2. 产品表面缺陷产品表面缺陷是另一个常见的问题,例如气泡、痕迹、烧焦等。
这些表面缺陷会影响产品的外观和质量。
要解决这个问题,可以从以下几个方面入手:优化模具通气系统,确保注塑过程中的气体能够顺利排出;调整注塑参数,控制注塑温度和压力,避免过高或过低造成烧焦或气泡;定期清洁模具,防止灰尘和杂质对产品表面造成影响。
3. 模具磨损严重模具在长期使用过程中会出现磨损,导致产品尺寸不准确或者产生其他问题。
要解决这个问题,可以采取以下几种措施:定期对模具进行保养和维护,及时更换磨损严重的零部件;使用高质量的模具材料,提高模具的耐磨性;注塑过程中控制好注塑温度和压力,避免过高过低造成模具磨损。
4. 注塑机故障注塑机故障是导致生产效率低下的主要原因之一。
为了避免注塑机故障,可以采取以下几个措施:定期对注塑机进行维护和保养,清洁注塑机内部的杂质和积聚物;使用高质量的注塑机零部件,避免因零部件质量差导致故障;培训操作人员,提高其对注塑机的操作技能和维修能力。
5. 塑料材料选择不当塑料材料的选择对注塑产品的质量和性能有很大影响。
如果选择的塑料材料不合适,可能会导致产品强度不足、耐热性差等问题。
因此,在进行模具注塑之前,应仔细选择合适的塑料材料,根据产品的要求和使用环境来进行选择。
6. 生产成本过高生产成本过高是许多企业关注的问题。
要降低生产成本,可以从以下几个方面入手:优化模具设计,减少材料的浪费;提高注塑机的效率,减少能耗;采用高效的生产工艺,提高生产效率。
塑料模具设计常见问题及改进方法

塑料模具设计常见问题及改进方法塑料模具设计在实际应用中,常常会遇到一些问题,影响生产效率和产品质量。
下面将介绍一些常见的问题,并提出改进的方法。
1. 精度不够:在塑料模具的设计和制造过程中,如果精度不够,会导致产品尺寸和形状的不一致,影响产品的质量。
改进方法可以通过使用高精度加工设备和工艺,并进行严格的质量控制来提高精度。
2. 成型件表面质量不良:塑料模具中常常会出现成型件表面出现纹痕、气泡、疤痕等问题,影响产品的外观和质量。
改进方法可以选择适合的模具材料,提高模具表面光洁度,调整模具温度和冷却系统等。
3. 模具寿命短:塑料模具在长时间使用过程中容易出现磨损、疲劳断裂等问题,导致模具寿命较短。
改进方法可以选择耐磨性好的材料制作模具,增加模具的强度和硬度,正确使用和维护模具等。
4. 模具结构复杂:一些塑料模具的结构比较复杂,设计和制造难度大,容易出现问题。
改进方法可以使用先进的设计软件和CAD/CAM技术,优化模具结构,简化模具制造过程,提高生产效率和产品质量。
5. 生产周期长:一些塑料模具的设计和制造周期较长,影响生产进度和交货时间。
改进方法可以使用模具快速制造技术,如快速加工和快速制造等,缩短模具的设计和制造周期。
6. 模具排气不畅:在塑料模具制造过程中,如果模具的排气不畅,容易产生气泡等缺陷,影响产品质量。
改进方法可以优化模具的设计和加工过程,设置合适的排气口和排气系统,并通过模具试验和调整来改善排气效果。
7. 模具变形:一些大尺寸或复杂结构的塑料模具在使用中容易发生变形,影响产品的尺寸精度和外观。
改进方法可以通过增加模具的刚性和稳定性,使用优质的模具材料,控制模具温度和冷却系统等来减少模具变形。
塑料模具设计常见问题的改进方法主要包括提高精度、改善表面质量、增加模具寿命、简化结构、缩短生产周期、优化排气系统和控制模具变形等。
通过不断改进和优化,可以提高塑料模具的生产效率和产品质量。
模具常见问题分析及其解决方法

模具常见问题分析及其解决方法概述模具是工业生产中常用的一种工具,它在各个行业中被广泛应用。
然而,随着使用时间的增加,模具也会出现各种问题。
本文将详细分析模具常见问题,并提供相应的解决方法,以帮助读者更好地应对模具问题。
问题一:模具磨损严重模具磨损是使用寿命过程中常见的问题之一。
其主要表现为模具表面磨损或凹陷。
磨损的原因可能是: - 使用材料硬度较高 - 使用时间较长 - 模具润滑不足 - 模具设计不合理解决方法: - 使用耐磨性能更好的模具材料,如优质钢材 - 定期进行模具保养和维护,及时更换磨损严重的部件 - 在使用过程中保持适当的模具润滑,减少磨损 - 对模具进行优化设计,减少出现磨损的可能性问题二:模具尺寸偏差大模具尺寸偏差大是另一个常见问题。
这可能导致生产出的产品尺寸不准确,影响产品质量。
尺寸偏差大的原因包括: - 模具制造过程中的测量误差 - 模具材料膨胀或收缩不均匀 - 模具结构设计不合理解决方法: - 提高模具制造过程中的测量精度,并进行多次验证 - 选择合适的模具材料,控制材料膨胀或收缩的影响 - 对模具结构进行优化设计,避免尺寸偏差的产生问题三:模具易生锈模具易生锈是模具在使用过程中常见的问题之一。
模具生锈不仅影响外观,还可能导致模具损坏。
模具易生锈的原因可能是: - 环境湿度较高 - 模具存放不当 - 模具润滑不足解决方法: - 控制使用环境湿度,尽量保持干燥 - 对模具进行正确的存放,避免受潮或受酸碱腐蚀 - 在使用过程中,保持模具的适度润滑,防止生锈问题四:模具易断裂模具易断裂是一种严重的问题,可能导致模具报废,造成生产线停机。
模具易断裂的原因包括: - 模具结构设计不合理 - 模具材料不合格或强度低 - 模具使用过程中发生过载解决方法: - 对模具结构进行优化设计,提高其受力性能 - 选择合适的模具材料,确保其强度和韧性满足要求 - 在使用过程中,避免过载操作,及时发现并处理异常情况问题五:模具易堵塞模具易堵塞是模具在使用过程中常见的问题,特别是对于塑料注塑模具。
模具失效及解决方法实例

模具失效及解决方法实例一、引言模具是工业生产中必不可少的工具,它能够成型出各种形状和尺寸的产品。
然而,模具在使用过程中会受到各种因素的影响,导致失效。
模具失效不仅会影响生产效率,增加生产成本,还会影响产品的质量。
因此,了解模具失效的原因和解决方法非常重要。
本文将介绍模具失效的类型、原因以及一些常见的解决方法实例。
二、模具失效类型1. 磨损:模具在使用过程中,其工作表面会与材料不断接触,导致工作表面磨损。
2. 腐蚀:模具受到化学或电化学作用,导致腐蚀损坏。
3. 塑性变形:材料在模具内塑性变形,导致模具变形。
4. 热疲劳:模具在工作过程中频繁冷热交替,导致热疲劳损坏。
5. 裂纹扩展:由于制造、使用过程中产生的裂纹在交变应力作用下扩展导致破坏。
三、模具失效原因1. 操作不当:如超负荷生产、材料硬度过高、材料中有杂质等都会导致模具过早磨损或腐蚀。
2. 维护不当:润滑不足、冷却系统不良等都会导致模具过热或腐蚀。
3. 材料问题:模具材料的选择不当,如硬度、耐腐蚀性、耐磨性等都会影响模具的使用寿命。
4. 制造问题:制造过程中的缺陷,如铸造缺陷、热处理不当等都会导致模具产生裂纹或塑性变形。
四、解决方法实例1. 磨损修复:对于磨损的模具,可以采用堆焊、喷涂等方法进行修复。
例如,对于磨损的凸轮表面,可以采用堆焊的方式进行修复,选择耐磨性好、焊前流动性好的合金堆焊焊条。
在修复过程中,需要注意控制热输入,避免热影响扩大。
同时,对于一些磨损严重的模具,还可以采用喷涂的方法进行修复,选择耐磨性好、耐腐蚀的涂层材料,如金属陶瓷、镍基涂层等。
2. 腐蚀防护:对于腐蚀的模具,可以采用镀层、表面处理等方法进行防护。
例如,对于受腐蚀的模具钢表面,可以采用镀铬或镀锌等防腐方法进行防护。
此外,还可以采用表面处理的方法提高模具表面的抗腐蚀性能,如采用氧化处理、磷化处理等。
3. 温度控制:对于塑性变形的模具,可以通过调整生产工艺、选择合适的材料等方法来降低模具工作时的温度。
模具设计中的故障分析与维修措施推荐
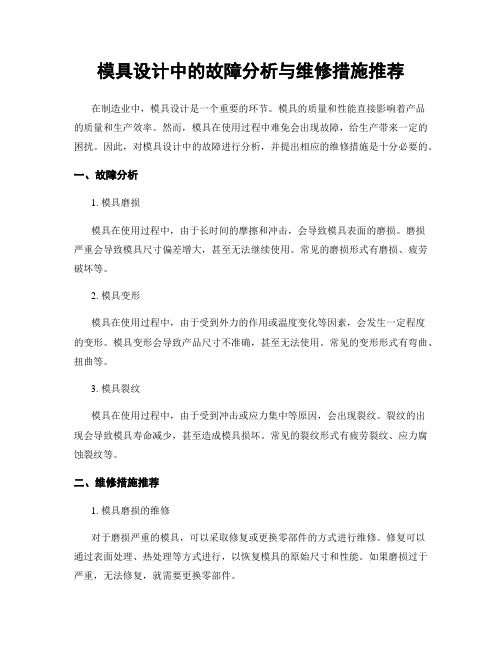
模具设计中的故障分析与维修措施推荐在制造业中,模具设计是一个重要的环节。
模具的质量和性能直接影响着产品的质量和生产效率。
然而,模具在使用过程中难免会出现故障,给生产带来一定的困扰。
因此,对模具设计中的故障进行分析,并提出相应的维修措施是十分必要的。
一、故障分析1. 模具磨损模具在使用过程中,由于长时间的摩擦和冲击,会导致模具表面的磨损。
磨损严重会导致模具尺寸偏差增大,甚至无法继续使用。
常见的磨损形式有磨损、疲劳破坏等。
2. 模具变形模具在使用过程中,由于受到外力的作用或温度变化等因素,会发生一定程度的变形。
模具变形会导致产品尺寸不准确,甚至无法使用。
常见的变形形式有弯曲、扭曲等。
3. 模具裂纹模具在使用过程中,由于受到冲击或应力集中等原因,会出现裂纹。
裂纹的出现会导致模具寿命减少,甚至造成模具损坏。
常见的裂纹形式有疲劳裂纹、应力腐蚀裂纹等。
二、维修措施推荐1. 模具磨损的维修对于磨损严重的模具,可以采取修复或更换零部件的方式进行维修。
修复可以通过表面处理、热处理等方式进行,以恢复模具的原始尺寸和性能。
如果磨损过于严重,无法修复,就需要更换零部件。
2. 模具变形的维修对于模具的变形问题,可以通过热处理或机械加工等方式进行维修。
热处理可以通过加热和冷却等方式,使模具恢复原始形状。
机械加工可以通过切削、磨削等方式,修复模具的尺寸和形状。
3. 模具裂纹的维修对于模具的裂纹问题,可以采取焊接、热处理等方式进行维修。
焊接可以通过填充和熔化等方式,修复模具的裂纹。
热处理可以通过加热和冷却等方式,消除模具的应力,防止裂纹扩展。
维修措施的选择要根据具体情况进行。
在进行维修之前,需要对模具的故障原因进行分析,确定维修的方式和方法。
同时,维修过程中需要注意保护模具的表面,避免二次损坏。
除了维修措施,预防措施也是非常重要的。
在模具设计和使用过程中,应注意以下几点:1. 合理设计模具结构,减少应力集中和磨损。
2. 选择适当的材料,提高模具的耐磨性和耐腐蚀性。
注塑模具各类问题原因分析及解决办法
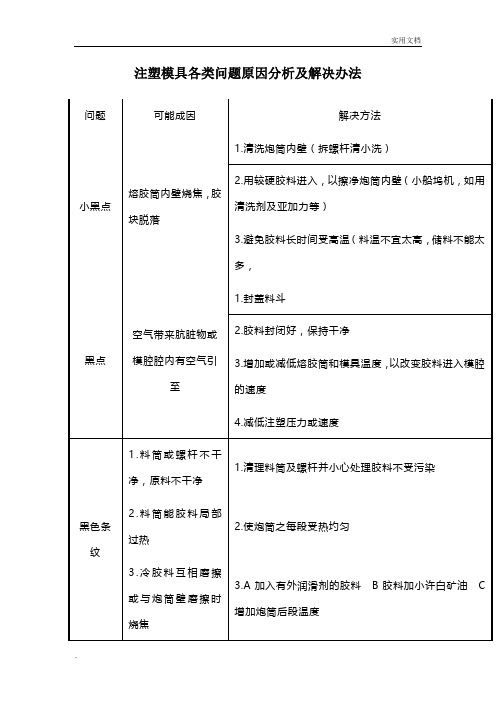
注塑模具各类问题原因分析及解决办法1注塑件收缩凹陷的原因分析注塑成型过程中,制品收缩凹陷是比较常见的现象。
造成这种情况的主要原因有:机台方面(1)射嘴孔太大造成融料回流而出现收缩,太小时阻力大料量不足出现收缩。
(2)锁模力不足造成飞边也会出现收缩,应检查锁模系统是否有问题。
(3)塑化量不足应选用塑化量大的机台,检查螺杆与料筒是否磨损。
模具方面(1)制件设计要使壁厚均匀,保证收缩一致。
(2)模具的冷却、加温系统要保证各部份的温度一致。
(3)浇注系统要保证通畅,阻力不能过大,如主流道、分流道、浇口的尺寸要适当,光洁度要足够,过渡区要圆弧过渡。
(4)对薄件应提高温度,保证料流畅顺,对厚壁制件应降低模温。
(5)浇口要对称开设,尽量开设在制件厚壁部位,应增加冷料井容积。
塑料方面结晶性的塑料比非结晶性塑料收缩历害,加工时要适当增加料量,或在塑料中加成换剂,以加快结晶,减少收缩凹陷。
加工方面(1)料筒温度过高,容积变化大,特别是前炉温度,对流动性差的塑料应适当提高温度、保证畅顺。
(2)注射压力、速度、背压过低、注射时间过短,使料量或密度不足而收缩压力、速度、背压过大、时间过长造成飞边而出现收缩。
(3)加料量即缓冲垫过大时消耗注射压力,过小时,料量不足。
(4)对于不要求精度的制件,在注射保压完毕,外层基本冷凝硬化而夹心部份尚柔软又能顶出的制件,及早出模,让其在空气或热水中缓慢冷却,可以使收缩凹陷平缓而不那么显眼又不影响使用。
2注塑件震纹的原因分析PS等刚性塑料制件在其浇口附近的表面,以浇口为中心的形成密集的波纹,有时称为震纹。
产生原因是熔体粘度过大而以滞流形式充模时,前端的料一接触到型腔表面便很快冷凝收缩起来,而后来的熔料又胀开已收缩的冷料继续前进过程的不断交替使料流在前进中形成了表面震纹。
解决办法(1)提高料筒温度特别是射嘴温度,还应提高模具温度。
(2)提高注射压力与速度,使其快速充模型腔。
(3)改善流道、浇口尺寸,防止阻力过大。
- 1、下载文档前请自行甄别文档内容的完整性,平台不提供额外的编辑、内容补充、找答案等附加服务。
- 2、"仅部分预览"的文档,不可在线预览部分如存在完整性等问题,可反馈申请退款(可完整预览的文档不适用该条件!)。
- 3、如文档侵犯您的权益,请联系客服反馈,我们会尽快为您处理(人工客服工作时间:9:00-18:30)。
對 策一﹕
a.加大壓料力. b.降低仿形入塊美工線. c.氬焊修復或更換備品.
凹陷對策二
解決方法 修整銅仁 改進加工工藝 人工修整3D
產品拉裂,裂紋.
原因分析:模腔表面 不夠光滑. 模具方面﹕
a.拉伸間隙太小或不均,位抻受阻. b.定位偏移,胚料置單邊. c.模具硬度低導到金屬粘附現象. d.凹模圓角過小拉伸力變大.
3. 下模薄殼壓料塊兩球形孔起歸位作用,損壞后易暴模, 故不能磨薄殼底面;
4. 參考模具:
M305后蓋
M433后蓋
2 典型3D模具結構與原理圖
D. 3D直切模示意圖
3D直切模與平面上的沖孔 模在模具結構上並無太大 區別,隻因3D直切模在沖 切方向上產品料厚的非均 勻性,常常因為設計不當 容易產生較大毛刺;故3D 直切模沖頭刀口一般為仿 形結構
4, 2003年600T大型連續衝模開發成功
5, 2000年成功開發出旋切模具結構
6, 2000年兄弟單位成功開發了NOKIA鈦合金手
機8910外殼模具
7, 2001年成功開發MOTOROLA V60手機外殼模具
沖件展示 NOKIA 8910
NOKIA NICKEL
MOTOROLA M225/M325
b. 3D旋切模工作原理
導軌
導 板
左右反向
前后方向
b. 3D旋切運動示意圖
運作示意圖
典型3D模具結構與原理圖
c. 3D旋切模修模注意事項
1. 旋切模切料間隙一般是由上下限位柱與上下刀口之 差,調節切料間隙只需調整上下限位柱長度;
2. 0.6mm鋁材切料間隙為0.05~0.07mm(待定)
0.4mm不鏽鋼間隙為0.04~0.06mm (待定) ;
沖子固定在脫料板的快拆結構 .
3
典型模具結構
3D斜切結構:沖子及刀口都在下模.
典型模具結構
內法蘭切邊:沖子及刀口都在下模.
內法蘭切邊產品
連續模排樣示例
三.3D件常見問題分析及解決
問題點:壓印.壓傷.模痕.
旋切
毛邊毛刺大,切料不斷
分 析:
a.上下模的限位柱高度發生變化導致間隙 不合理.
b.沖頭與凹模刀口磨損. c.氣頂杆壓力不夠或不穩定. d.氣頂杆高度不一致. e.導板導軌損壞或螺絲松脫.
3D模具維修難點
1. 3D工件模具極難找到定位基準,尺寸不 易保証
2.拉伸件外觀不易掌控 3.工件拉伸后切邊平面度不易保証 4.3D面上沖切,模具刀口易拉傷,並難以
維護 5.沖壓產生粉屑多,沖件表面易產生壓傷
典型3D模具結構與原理圖
a. 3D旋切模結構示意圖
旋切結構
典型3D模具結構與原理圖
MOTOROLA M324/M310
其它
二.典型模具結構介紹
1.3D模具概論
3D模具即生產3D(三維 Three Dimension)產品的模具.因產品外觀 精美,結構復雜,故需下料,拉伸,整形, 直沖,斜沖,側切,旋切,翻邊,推邊等多 個工序才能成型.模仁多為三維球曲 面 工作時由3D定位產品對外觀及尺 寸要求較為嚴格需用三次元檢測。
產品拉裂,裂紋.
模具與沖床﹕
a.合理的沖床速度. b.合理的壓座壓力. c.合理的拔模力. d.合理的保壓時間.
產品拉裂,裂紋.
材料方面
a.前后批次材料厚檢測. b.前后批次材料試模對比. c.客戶提供的材料規格. d.華南檢測的材料指標.
產品拉裂
分 析:
a.壓料力小--角底起皺—角部材料受 阻. b.模仁棱角尖銳—材料受阻切斷材料. c.直邊壓料力太大—拉伸不均—角部 破裂. d.下料外形尺寸不合理—拉伸力增大 —角度破裂.
沖孔
切邊
.典型3D模具結構
3D側切模 從外向內沖切,沖頭及刀口均在下模
1
2
模具結構參考
3
后蓋
典型3D模具結構與原理圖
3D側切模
. 從內向外沖切,沖頭及刀口均在下模.
模具結構參考: M305后蓋
典型3D模具結構與原理圖
從內向外沖切,沖頭在下模,刀口在上模
模具結 構參考 M5104 后蓋
典型模具結構
毛邊毛刺大,切料不斷
對 策:
a.定期改善,確保限位柱與沖頭,凹模間隙 吻合.
b.對沖頭,凹模刀口進行點檢和定期保養. c.確保頂杆壓力穩定均衡,壓力在2.0-
2.5kg/cm平方米. d.確保頂杆高度不一致合理,定期檢查. e.導板導軌保持良好的潤滑狀態.
壓印.壓傷.模痕
原因分析:
a.沖頭刀口磨損或崩缺. b.下模入塊刀口磨損或崩缺. c.沖頭刀口有反毛刺帶出粉屑. d.刀口入塊成型入塊滑塊3D仿形入塊高 度不合理. e.沖孔跳廢料.
手机沖件模典型結構介紹
模 修:龍捷
講義目錄
一.產品介紹 二.典型模具結構介紹 三.模具常見問題分析及其解決方法
一.AP1沖壓廠發展歷程回顧
1. 1996年成立沖壓廠,進軍電腦機殼市場
2, 1997年衝壓自動生產線ROBOT模具成功導入
3, 1999年成功開發APPLE之大型3D鐵件法大壓料力. b.清除拋光模仁利角. c.減小直邊壓料力. d.改變下料外形.
產品平面度不良
分 析﹕
a.凹模入塊3D面壓料力不夠(指側切 刀口). b.沖頭與凹模刀口間隙大. c.3 D仿形美工線工步高度不合理. d.3D面的整形工步調整不合理. e.3D仿形入塊壓料力不夠鄉或圓弧面 與產品R面不吻合.
對 策:
a.調整刀口間隙,翻新沖頭或更換備品. b.翻新刀口或更換備品. c.清除刀口反面毛邊.
產品Z折斷差及變形
原 因:
a.整形插刀或滑塊斜面磨損. b.折塊入塊崩缺或松動. c.Z折入塊螺絲松動或入塊有廢料. d.Z折入塊,滑塊不脫料. e.滑塊脫料不順或帶料.
壓印.壓傷.模痕
預防措施:
a.沖頭刀口研磨或更換(補焊研磨) b.入塊刀口研磨或更換新品(補焊研磨 ) c.沖頭刀口修整0.10mm以下R.防止 帶出粉屑. d.調整相關部位的入塊,滑塊,仿形入塊 高度. e.修整沖頭刀口切料結構,盡量使用吹
產品拉伸變形,凹陷,塌角.
原因分析﹕
a.壓料力不夠.
c.模仁崩缺.
產品平面度不良
預防對策﹕
a.保持一定的模高和沖壓速度. b.合理的沖壓力或3D仿形壓料深度. c.保持合理的沖孔間隙. d.每次研磨3D面刀口時,保持原形R不變. e.3D面的整形力度要均勻.
毛邊大及毛刺大
原 因:
a.刀口間隙大或沖頭刀口磨損. b.沖頭刀口崩缺,磨損嚴重. c.沖頭刀口反面毛邊.