内螺纹粉末冶金成型模具的制作方法
粉末冶金注塑成型工艺流程
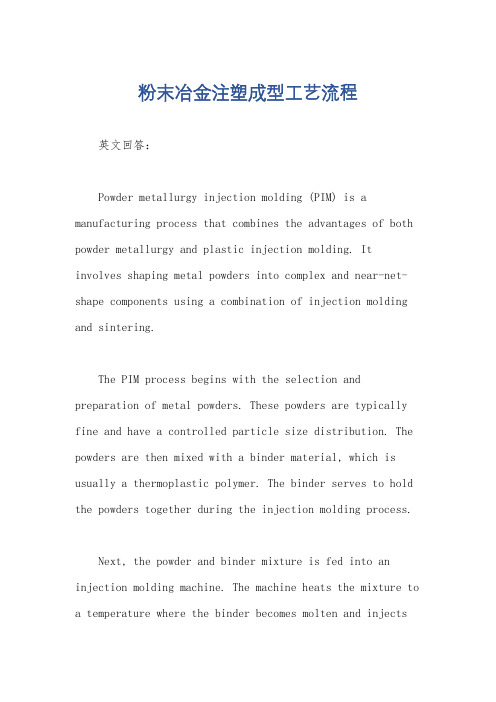
粉末冶金注塑成型工艺流程英文回答:Powder metallurgy injection molding (PIM) is a manufacturing process that combines the advantages of both powder metallurgy and plastic injection molding. It involves shaping metal powders into complex and near-net-shape components using a combination of injection molding and sintering.The PIM process begins with the selection and preparation of metal powders. These powders are typically fine and have a controlled particle size distribution. The powders are then mixed with a binder material, which is usually a thermoplastic polymer. The binder serves to hold the powders together during the injection molding process.Next, the powder and binder mixture is fed into an injection molding machine. The machine heats the mixture to a temperature where the binder becomes molten and injectsit into a mold cavity. The mold is typically made of steel and has the desired shape of the final component. The injection molding machine applies pressure to ensure thatthe mixture fills the mold completely.Once the mold is filled, it is cooled to solidify the binder material. The solidified component, known as a green part, is then ejected from the mold. The green part isstill fragile and cannot be used as a final product. It undergoes a debinding process to remove the binder material, usually through thermal or solvent extraction methods.After debinding, the green part is subjected to a sintering process. Sintering involves heating the part in a controlled atmosphere to a temperature below its melting point. During sintering, the metal powders bond together, resulting in a denser and stronger final component. The sintering process also helps to eliminate any remaining porosity in the part.Finally, the sintered part undergoes any necessary secondary operations, such as machining or surfacefinishing, to achieve the desired final shape and properties. The finished part can have complex geometries, high precision, and excellent mechanical properties.中文回答:粉末冶金注塑成型(PIM)是一种将粉末冶金和塑料注塑成型的优点结合起来的制造工艺。
粉末冶金模具的设计与制造

粉末冶金模具的设计与制造1. 引言粉末冶金是一种重要的金属制造工艺,广泛应用于汽车、航空航天、电子、能源等领域。
在粉末冶金工艺中,模具的设计与制造是关键环节,直接影响产品的质量和性能。
本文将介绍粉末冶金模具的设计与制造过程,包括模具材料的选择、模具的结构设计、加工工艺等内容,以帮助读者全面了解粉末冶金模具的制造方法和技术要点。
2. 模具材料的选择模具材料的选择是粉末冶金模具设计的第一步。
模具材料需要具备一定的硬度、耐磨性和耐各种腐蚀介质的能力。
常用的模具材料有以下几种:•工具钢:具有较高的硬度和韧性,适用于大部分粉末冶金模具的制造。
•高速钢:具有更高的硬度和耐磨性,适用于对模具耐磨性要求较高的情况。
•硬质合金:具有较高的硬度和耐磨性,适用于对模具耐磨性要求极高的情况。
在选择模具材料时,需要根据具体应用场景和成本考虑,综合各种性能指标做出合理选择。
3. 模具的结构设计模具的结构设计是粉末冶金模具制造中的核心环节。
良好的模具结构设计可以提高产品的制造效率和质量,降低生产成本。
以下是模具结构设计的几个要点:•模具的整体结构应该合理,易于安装和拆卸。
模具的结构应简洁、牢固,能够承受制造过程中的力和压力。
•模具的导向和定位系统要设计到位,以确保模具在制造过程中的稳定性和精度。
•模具的开合系统要灵活可靠,能够实现快速开合和调节。
对于大型模具,可以考虑采用液压或气动开合系统。
•模具的冷却系统要充分考虑,以保证模具在制造过程中能够及时散热,提高产品质量和生产效率。
4. 模具的制造过程粉末冶金模具的制造过程主要包括以下几个步骤:4.1 模具设计在模具设计阶段,根据产品的形状和尺寸要求,通过CAD软件进行三维建模。
在设计过程中,要充分考虑模具的可行性和制造工艺,以确保模具的质量和可生产性。
4.2 模具加工模具加工是模具制造的关键环节。
常用的模具加工方法包括数控加工、线切割、铣削等。
在加工过程中,需要根据模具材料和结构要求选择合适的加工工艺,精确控制加工尺寸和表面质量。
粉末冶金材料模具设计
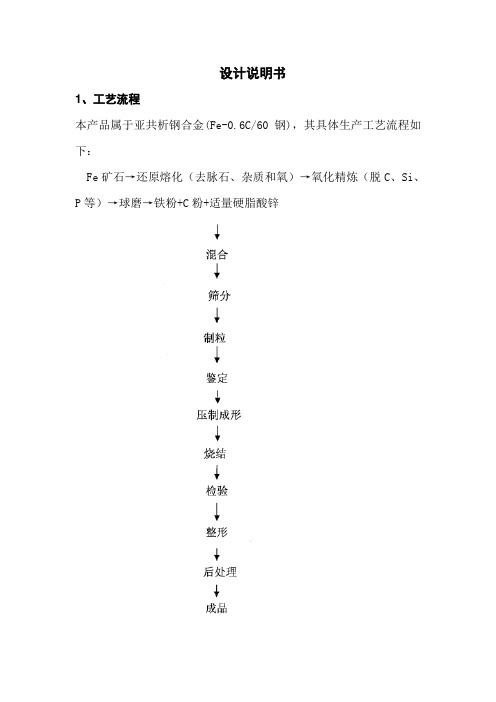
设计说明书1、工艺流程本产品属于亚共析钢合金(Fe-0.6C/60钢),其具体生产工艺流程如下:Fe矿石→还原熔化(去脉石、杂质和氧)→氧化精炼(脱C、Si、P等)→球磨→铁粉+C粉+适量硬脂酸锌2、压坯设计2.1产品零件分析该产品采用Fe-0.6C(60钢),属于铁基制品,其制品密度依靠较高的压坯密度来达到,因此,在压制成形时需要采用较高的单位压力(一般在400-500MPa)。
由于该产品零件形状比较简单,带一个外台阶,采用简单的单上双下模冲即可成形,并使其密度分布均匀。
有配合、定位、相对运动要求的零部件,产品尺寸精度和形位精度及表面粗糙度要求较高,因此,该产品的的尺寸精度定义为IT8、形位精度如图所示为7级,表面粗糙度精度要求为7级。
2.2压坯精度设计由模具设计任务书的零件成品图可得知该产品压坯同轴度需控制在0.08mm,相当于IT10级;压坯垂直度控制为0.1mm,相当于IT11级;压坯侧面平行度为0.15mm,相当于IT12级。
2.3压坯密度和单重的确定由于已知压坯密度ρ=6.6g/cm3,因此压坯单重W=ρ×V ,由成品图给数据计算其压坯体V=h×S,算的V=166.8cm3 ,所以求的压坯单重W=6.6×166.8=1100.8g。
3、压机与压制方式选择3.1压机压力选择铁基制品一般采用固相烧结,其制品密度除了依靠烧结温度、保温时间之外,在一定程度上还依靠较高的压坯密度来达到,因此该产品采用500MPa的单位压力。
根据任务书要求,截面积S=74.0cm2 ,所以F=P×S=5×74=370t脱模压力,根据实际生产经验,铁基压坯的脱模压力P脱模≈0.13P=0.13×500MPa=65MPa3.2压制类型的选择年生产量为50万件,假设每年的工作时间为300天,每天工作时间为8小时,则p=500000/300/8/60=3.47=4件/min,所以选择自动压制。
粉末冶金整形模具设计步骤
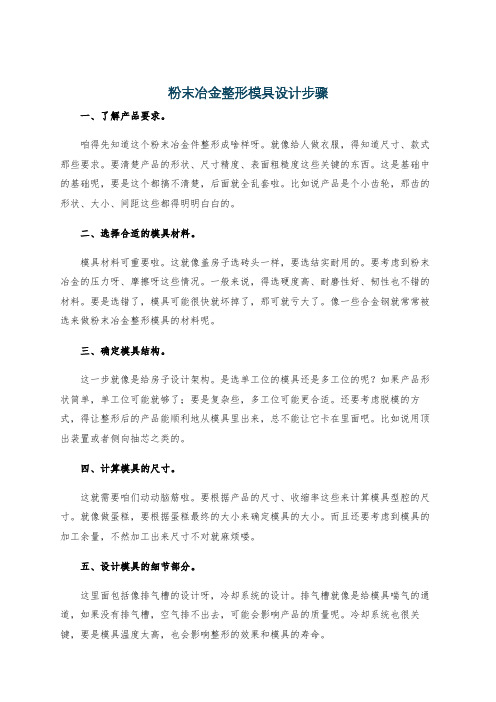
粉末冶金整形模具设计步骤一、了解产品要求。
咱得先知道这个粉末冶金件整形成啥样呀。
就像给人做衣服,得知道尺寸、款式那些要求。
要清楚产品的形状、尺寸精度、表面粗糙度这些关键的东西。
这是基础中的基础呢,要是这个都搞不清楚,后面就全乱套啦。
比如说产品是个小齿轮,那齿的形状、大小、间距这些都得明明白白的。
二、选择合适的模具材料。
模具材料可重要啦。
这就像盖房子选砖头一样,要选结实耐用的。
要考虑到粉末冶金的压力呀、摩擦呀这些情况。
一般来说,得选硬度高、耐磨性好、韧性也不错的材料。
要是选错了,模具可能很快就坏掉了,那可就亏大了。
像一些合金钢就常常被选来做粉末冶金整形模具的材料呢。
三、确定模具结构。
这一步就像是给房子设计架构。
是选单工位的模具还是多工位的呢?如果产品形状简单,单工位可能就够了;要是复杂些,多工位可能更合适。
还要考虑脱模的方式,得让整形后的产品能顺利地从模具里出来,总不能让它卡在里面吧。
比如说用顶出装置或者侧向抽芯之类的。
四、计算模具的尺寸。
这就需要咱们动动脑筋啦。
要根据产品的尺寸、收缩率这些来计算模具型腔的尺寸。
就像做蛋糕,要根据蛋糕最终的大小来确定模具的大小。
而且还要考虑到模具的加工余量,不然加工出来尺寸不对就麻烦喽。
五、设计模具的细节部分。
这里面包括像排气槽的设计呀,冷却系统的设计。
排气槽就像是给模具喘气的通道,如果没有排气槽,空气排不出去,可能会影响产品的质量呢。
冷却系统也很关键,要是模具温度太高,也会影响整形的效果和模具的寿命。
六、校对审核。
这就像是检查作业一样。
自己先检查一遍,看看有没有哪里设计得不合理。
也可以找同事或者经验丰富的人帮忙看看,多一双眼睛就多一份保障嘛。
可不能让有问题的设计进入生产环节,不然到时候出了问题就不好收拾啦。
粉末冶金整形模具设计虽然有点复杂,但只要一步一步来,把每个环节都考虑周到,就一定能设计出好用的模具啦。
粉末冶金模具介绍

粉末冶金模具介绍一、MIM概念及工艺流程金属粉末注射成形是传统粉末冶金技术与塑料注射成形技术相结合的高新技术,是小型复杂零部件成形工艺的一场革命。
它将适用的技术粉末与粘合剂均匀混合成具有流变性的喂料,在注射机上注射成形,获得的毛坯经脱脂处理后烧结致密化为成品,必要时还可以进行后处理生产工艺流程如下配料→混炼→造粒→注射成形→化学萃取→高温脱粘→烧结→后处理→成品二、MIM技术特点金属粉末注射成形结合了粉末冶金与塑料注射成形两大技术的优点,突破了传统金属粉末模压成形工艺在产品形状上的限制,同时利用塑料注射成形技术能大批量、高效率生产具有复杂形状的零件:如各种外部切槽、外螺纹、锥形外表面、交叉通孔、盲孔、凹台、键销、加强筋板,表面滚花等·MIM技术的优点a.直接成形几何形状复杂的零件,通常重量0.1~200gb.表面光洁度好、精度高,典型公差为±0.05mmc.合金化灵活性好,材料适用范围广,制品致密度达95%~99%,内部组织均匀,无内应力和偏析d.生产自动化程度高,无污染,可实现连续大批量清洁生产·MIM与精密铸造成形能力的比较特点精密铸造MIM最小孔直径2mm0.4mm2mm直径盲孔最大深度2mm20mm最小壁厚2mm<1mm最大壁厚无限制10mm4mm直径公差±0.2mm±0.05mm表面粗糙度(Ra)5μm1μm·MIM与其他成形工艺的比较项目 MIM粉末冶金精密铸造机加工密度98%86%98%100%拉伸强度高低高>高光洁度高中中高微小化能力高中低中薄壁能力高中低复杂程度高低中高设计宽容度高中中中材质范围高高中高三、MIM常用材质材料体系合成成分低合金钢Fe-2Ni、F-8Ni不锈钢316L、430L、17-4PH工具钢42Cr2Mo4、M2硬质合金WC-CO(6%)重合金W-Ni-Fe、W-Ni-Cu、W-Cu 四、几种MIM材料的基本性能材料密度(103kg/cm3)硬度拉伸强度Mpa延伸率铁基合金PIM46007.6885HRB40025PIM46507.68100HRB60015不锈钢316L7.9452HRB58045钨合金95%W18.131HRC93010五、MIM产品典型应用领域航空航天业:机翼铰链、火箭喷嘴、导弹尾翼、涡轮叶片芯子等汽车业:安全气囊组件、点火控制锁部件、涡轮增压器转子、座椅部件、刹车装置部件等电子业:磁盘驱动器部件、电缆连接器、电子封装件、手机振子、计算机打印头等军工业:地雷转子、枪扳机、穿甲弹心、准星座、集束箭弹小弹等日用品:表壳、表带、表扣、高尔夫球头和球座、缝纫机零件、电动玩具零件等机械行业:异形铣刀、切削工具、电动工具部件、微型齿轮、铰链等医疗器械:牙矫形架、剪刀、镊子、手术刀等。
粉末冶金一模四件模具加工工艺流程

粉末冶金一模四件模具加工工艺流程
以下每一道工序单独完成后,均须品质部严格检测;
模芯采用材质为YG15外协加工成型;
芯棒为外协加工成型至图示尺寸;
所有工件均须淬火处理、雕刻字码。
一:备料
上冲料、下冲料、中模模套、中模模芯料(外协)、上冲垫板料、上冲压盖料、下冲垫板料、下冲压盖料、芯棒压盖料、芯棒座料、芯棒(外协)
二:粗车
上冲、下冲、中模套、上冲垫板、上冲压盖、下冲垫板、下冲压盖、芯棒压盖、芯棒座
三:铣床
中模套、上下冲垫板、上下冲压盖、芯棒压盖、芯棒压盖铣基准、钻子及沉头
四:热处理
上冲、下冲材质为SLD材质,热处理后硬度为HRC56-58;
中模芯为YG15材质与中模套热配;
上下冲压盖、芯棒压盖、上下冲垫板材质均为Cr12材质,热理硬度为HRC30-40;
芯棒座材质为45#钢,热处理后硬度为HRC23-28。
五:平磨
上下冲外形、外形避空段、两端面、挂台高度尺寸、中模两端面、上下冲垫板、上下冲压盖、芯棒压盖、芯棒座两端面
六:车床精车
中模外圆及台阶、上下冲垫板、上下冲压盖、芯棒压盖、芯棒座、外圆
七:CNC精铣
上下冲压盖沉头、芯棒压盖沉头、上下冲电极
八:慢丝线割
上下冲芯棒孔、中模产品成型孔
九:钳工装配
上下冲与芯棒实配、上下冲与中模实配、模具整体装配
十:放电
上下冲面区、芯棒孔避空段放电、上冲芯棒孔排气孔
十一:抛光
上下冲面区放电后抛光。
粉末冶金高速钢模具工艺流程

粉末冶金高速钢模具工艺流程
1.原材料制备:粉末冶金高速钢模具材料的原料包括金属粉末和其他添加剂。
金属粉末一般由高速钢的主要成分,如铁、碳、铬、钼、钴等金属制成。
其他添加剂可能包括增强剂、增湿剂等。
2.粉末混合:将金属粉末和其他添加剂按一定比例混合均匀,可以采用机械搅拌或者其他方法进行混合。
3.压制成型:将混合好的粉末放入模具中进行冷压成型,一般采用注射成型、压制成型等方法。
冷压成型可以使粉末呈固态状态,便于后续烧结。
4.烧结:将冷压成型的模具进行烧结,提高模具的密实度和强度。
烧结一般在高温下进行,使金属粉末颗粒相互连结成型。
5.热处理:对烧结好的模具进行热处理,改善其力学性能。
热处理可以包括淬火、回火等工艺,使模具达到适应工作环境的要求。
6.加工:热处理后的模具可以进行粗加工和精加工。
粗加工可以包括车削、铣削等工艺,将模具的形状和尺寸加工到接近最终要求。
精加工可以包括打磨、抛光等工艺,提高模具的表面质量。
粉末冶金成型技术

粉末冶金成型技术Ⅰ、粉末冶金成型技术1、粉末冶金成型技术(Powder Metallurgy)是一种较新的金属制造工艺,它通过将金属粉末或粉体团结成模具内所需形状,从而生产出广泛应用的金属零件。
其原理是金属粉末经高压热压成型而形成零件。
2、粉末冶金成型技术能够制造出具有较高精度、更小体积的零件,是传统金属制造技术无法达到的高精度和大精度的紧凑零件。
同时,由于具有良好的耐磨性,它还可以制造可耐高速摩擦的零件。
3、粉末冶金成型技术使用金属粉末来制造零件,因此可以制造出大规模和复杂零件。
它制造出的产品可以达到更高的均匀度、更高的精度和更强的密度,这些特点比其他技术都有优势。
II、工艺流程1、把金属粉末混合成易流动的糊状物:在粉末冶金成型过程中,首先将金属粉末混合成易流动的糊状物,然后将其成型成所需的各类结构。
2、金属流成型:将调制好的金属流放入到模具中,然后将其投射成型,采用精确的高压成型,以形成模具内期望的形状。
3、表面处理:一些金属零件可能需要再进行表面处理,比如镀铬、电镀和热处理,以满足零件性能的需求,增强其耐蚀性、耐磨性等。
4、热处理:热处理是利用复杂的热处理技术,通过改变零件的温度来改变其组织和性能,以获得期望的性能和表面光洁度。
III、优点1、体积小:由于采用精密模具来进行流体压力成型,可以制造出具有较小体积和精确尺寸的部件;2、准确精度:粉末冶金成型可以根据模具进行长宽比、曲率与折弯处理,以达到较高的精度,组装时也相对容易;3、节能降耗:比传统金属加工手段更加节省能源耗费,而且粉末冶金可以减少冶炼及清理成本,从而降低成本;4、结构复杂:粉末冶金制造的零件可以根据设计形状进行复杂的结构设计,可在一个工件上制造气隙空间及护套,从而更加省时。
IV、缺点1、成本高:粉末冶金技术的设备耗费较高,使得生产成本比其他工艺高很多;2、尺寸大小限制:模具的设计尺寸受生产设备的尺寸限制,影响着大小尺寸和深度尺寸的生产;3、生产周期长:由于加工方法比其他工艺复杂,因此所需的生产周期也变得更长;4、表面光洁度差:因为运用压力成型,而非切削加工,因此物件的表面光洁度不是非常理想。
- 1、下载文档前请自行甄别文档内容的完整性,平台不提供额外的编辑、内容补充、找答案等附加服务。
- 2、"仅部分预览"的文档,不可在线预览部分如存在完整性等问题,可反馈申请退款(可完整预览的文档不适用该条件!)。
- 3、如文档侵犯您的权益,请联系客服反馈,我们会尽快为您处理(人工客服工作时间:9:00-18:30)。
内螺纹粉末冶金成型模具的制作方法
以内螺纹粉末冶金成型模具的制作方法为标题
一、引言
内螺纹粉末冶金成型模具是一种用于生产内螺纹零件的工具,它能够将粉末冶金材料压制成具有内螺纹形状的工件。
本文将介绍内螺纹粉末冶金成型模具的制作方法。
二、模具设计
在制作内螺纹粉末冶金成型模具之前,首先需要进行模具设计。
模具设计是整个制作过程的基础,它包括模具的形状、尺寸、结构等方面的考虑。
设计师需要根据产品要求和工艺要求,确定模具的具体参数。
三、材料选择
模具的材料选择对于模具的使用寿命和生产效率有着重要的影响。
一般而言,模具材料需要具备高硬度、高耐磨性和高强度等特点。
常用的模具材料有高速钢、硬质合金等。
根据具体的工件要求,选择合适的模具材料。
四、加工工艺
1. 加工模具的毛坯:根据模具的形状和尺寸要求,选择合适的毛坯材料,然后进行粗加工,将毛坯加工成大致形状和尺寸。
2. 精密加工:进行模具的精密加工,包括车削、铣削、钻孔等工艺。
通过精密加工,将模具加工成最终的形状和尺寸。
3. 热处理:对加工好的模具进行热处理,以提高模具的硬度和耐磨性。
常用的热处理方法有淬火、回火等。
4. 表面处理:对模具进行表面处理,以提高模具的表面光洁度和耐腐蚀性。
常用的表面处理方法有电镀、喷涂等。
五、模具装配
模具装配是将各个零部件组装成完整的模具的过程。
在模具装配过程中,需要保证各个零部件的精度和配合度,以确保模具的正常使用。
同时,还需要进行模具的调试和测试,以验证模具的性能和精度。
六、模具调试
模具装配完成后,需要进行模具的调试。
调试的目的是检查模具的各个部分是否正常工作,是否符合设计要求。
在调试过程中,需要进行模具的试模和调整,以确保模具能够正常运行。
七、模具使用与维护
模具制作完成后,需要进行模具的使用与维护。
在使用模具时,需要注意避免过度加载和过度磨损,以延长模具的使用寿命。
同时,还需要进行模具的定期维护和保养,包括清洁、润滑等,以确保模具的正常使用。
八、总结
内螺纹粉末冶金成型模具的制作方法包括模具设计、材料选择、加工工艺、模具装配、模具调试等多个环节。
通过合理的制作方法和技术手段,可以制作出高质量的内螺纹粉末冶金成型模具。
在模具的使用过程中,需要进行定期维护和保养,以延长模具的使用寿命。