海勒加工中心参数调整
加工中心功能调试

加工中心功能调试一、数控系统参数设置数控系统正常运行的重要条件是必须保证各种参数的正确设定,不正确的参数设置与更改,可能造成严重的后果。
因此,必须理解参数的功能,熟悉设定值,详细内容参考《参数说明书》。
1. 显示参数的操作(1)按MDI面板上的【SYSTEM】功能键数次或者按【SYSTEM】功能键一次,再按〖参数〗软键,选择参数画面,见图3-1。
图3-1 参数画面(2)参数画面由多页组成,可用光标移动键或翻页键,寻找相应的参数画面,也可由键盘输入要显示的参数号,然后按下〖号搜索〗软健,显示指定参数所在的页面,此时光标位于指定参数的位置。
2.用MDI设定参数(1)在操作面板上选择MDI方式或急停状态。
(2)按下【OFS/SET】功能键,再按〖设定〗软键,可显示“设定”画面的第一页。
(3)将光标移动到“写参数”处,按〖操作〗软键,进入下一级画面。
(4)按〖NO:1〗软键或输入1,再按〖输入〗软键,将“写参数”设定为1,此时参数处于可以写入状态,同时CNC产生“SW0100 参数写入开关处于打开”报警,这时若同时按下【RESET】键和【CAN】键,可解除SW0100报警。
(5)按【SYSTEM】功能键,再按〖参数〗软键,进入参数画面。
找到需要设定的参数画面,将光标置于需要设定的参数上。
(6)输入设定值,按【INPUT】键,则输入的数据将被设置到光标指定的参数中。
(7)参数设定完毕,需要将“写参数”设置为0,即禁止参数设定,防止参数被无意更改。
注:有时在参数设定中会出现报警“PW0000必需关断电源”,此时需要重新启动数控系统,参数方能生效。
3.参数说明数据类型有效数据范围备注位型0或1位轴型字节型-128~1270~255 在一些参数中不使用符号字节轴型字型-32768~327670~65535 在一些参数中不使用符号字轴型双字型-99999999~99999999双字轴型注意:(1)对于位型和位轴型参数,每个数据由8位组成,每个位都有不同的意义。
加工中心三合一参数设置
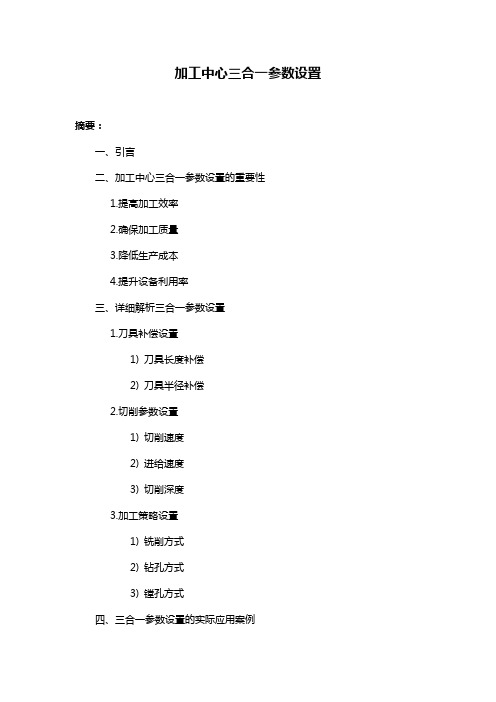
加工中心三合一参数设置摘要:一、引言二、加工中心三合一参数设置的重要性1.提高加工效率2.确保加工质量3.降低生产成本4.提升设备利用率三、详细解析三合一参数设置1.刀具补偿设置1) 刀具长度补偿2) 刀具半径补偿2.切削参数设置1) 切削速度2) 进给速度3) 切削深度3.加工策略设置1) 铣削方式2) 钻孔方式3) 镗孔方式四、三合一参数设置的实际应用案例1.案例一:叶片零件加工2.案例二:汽车发动机缸体加工3.案例三:航空发动机零件加工五、结论正文:一、引言随着现代制造业的发展,加工中心在生产中的地位越来越重要。
作为一种集多种加工功能于一身的设备,加工中心能够满足多种加工需求,提高生产效率。
而合理的三合一参数设置则是发挥加工中心潜能的关键。
本文将从加工中心三合一参数设置的重要性、详细解析以及实际应用案例等方面进行阐述,以期为大家提供有益的参考。
二、加工中心三合一参数设置的重要性1.提高加工效率合理的三合一参数设置能够充分发挥加工中心的性能,提高加工效率。
通过优化刀具补偿、切削参数和加工策略等设置,可以使加工过程更加稳定,减少加工时间,提高生产效率。
2.确保加工质量三合一参数设置直接影响到加工零件的质量。
合理的刀具补偿和加工策略可以降低加工误差,确保零件加工质量。
同时,通过优化切削参数,可以提高加工表面的粗糙度,满足产品质量要求。
3.降低生产成本合理的三合一参数设置有助于降低生产成本。
通过提高加工效率和保证加工质量,可以减少不良品率,降低返工、退货等额外成本。
此外,合理的切削参数设置还可以延长刀具寿命,降低刀具消耗成本。
4.提升设备利用率优化三合一参数设置有助于提高加工中心的设备利用率。
合理的加工策略和切削参数设置可以充分发挥设备的性能,使设备潜能得到充分利用。
同时,合理的刀具补偿设置可以降低因刀具磨损等原因导致的设备停机时间,提高设备利用率。
三、详细解析三合一参数设置1.刀具补偿设置1) 刀具长度补偿:根据刀具的实际长度和刀具补偿值进行设置,以消除刀具磨损和安装误差对加工长度的影响。
加工中心功能调试

加工中心功能调试一、数控系统参数设置数控系统正常运行的重要条件是必须保证各种参数的正确设定,不正确的参数设置与更改,可能造成严重的后果。
因此,必须理解参数的功能,熟悉设定值,详细内容参考《参数说明书》。
1. 显示参数的操作(1)按MDI面板上的【SYSTEM】功能键数次或者按【SYSTEM】功能键一次,再按〖参数〗软键,选择参数画面,见图3-1。
图3-1 参数画面(2)参数画面由多页组成,可用光标移动键或翻页键,寻找相应的参数画面,也可由键盘输入要显示的参数号,然后按下〖号搜索〗软健,显示指定参数所在的页面,此时光标位于指定参数的位置。
2.用MDI设定参数(1)在操作面板上选择MDI方式或急停状态。
(2)按下【OFS/SET】功能键,再按〖设定〗软键,可显示“设定”画面的第一页。
(3)将光标移动到“写参数”处,按〖操作〗软键,进入下一级画面。
(4)按〖NO:1〗软键或输入1,再按〖输入〗软键,将“写参数”设定为1,此时参数处于可以写入状态,同时CNC产生“SW0100 参数写入开关处于打开”报警,这时若同时按下【RESET】键和【CAN】键,可解除SW0100报警。
(5)按【SYSTEM】功能键,再按〖参数〗软键,进入参数画面。
找到需要设定的参数画面,将光标置于需要设定的参数上。
(6)输入设定值,按【INPUT】键,则输入的数据将被设置到光标指定的参数中。
(7)参数设定完毕,需要将“写参数”设置为0,即禁止参数设定,防止参数被无意更改。
注:有时在参数设定中会出现报警“PW0000必需关断电源”,此时需要重新启动数控系统,参数方能生效。
3.参数说明注意:(1)对于位型和位轴型参数,每个数据由8位组成,每个位都有不同的意义。
(2)轴型参数允许对每个轴分别设定参数。
(3)各参数类型的数据值范围为一般有效范围,具体的参数范围根据实际情况确定。
4.设定显示语言(1)本系统可使用CF存储卡来存储和恢复机床数据。
加工中心的数控系统参数设定和操作要点

加工中心的数控系统参数设定和操作要点一、参数设定参数的设定包括刀具参数及刀具补偿参数、零点偏置等参数的设定。
下面简单介绍参数的设定步骤。
(1) 刀具参数及刀具补偿参数打开软键功能中的参数栏后,按刀具补偿软键,屏幕上显示出刀具补偿数据。
按软键<<T或>>T选择刀具号,>>D或<<D选择刀沿号,离开此窗口后,所设定的状态不会改变。
刀具补偿分为刀具长度补偿和刀具半径补偿。
在设定时,移动光标到所要设定或修改的区域后输入数值,再按输入键确认。
(2) 零点偏置在回参考点之后,实际值存储器以及实际值的显示均以机床零点为基准,而工件的加工程序则是以工件零点为基准的,机床零点与工件零点之间所存在的差值就是零点的偏移量,这个偏移量就是我们要设定的零点偏置参数。
通过选择软键“参数”和“零点偏移”后,在屏幕上出现零点偏置窗口。
使用光标移动键将光标移动到待修改的范围后输入数值,零点偏置就设定好了。
利用“测量”软键功能还可以根据机床坐标系的原点计算出零点偏移量。
具体方法是把刀具运行到所选择的零点位置,按软键“计算”键计算出偏移量,数控系统会将计算出的偏移量登记到操作者所选定的相应的区域中。
按软键“确认”键可以关闭此窗口。
二、操作要点·开机通电后,必须执行手动返回参考点的操作。
否则机床不执行任何指令动作。
·在操作时,首先选择机床的工作方式。
再根据所选择的工作方式,确定下一步的操作内容。
·在调试加工程序进行试切时,一般选择比较小的进给倍率。
如5%,10%等。
·在进行加工之前,必须在NC上通过参数的输入和修改对机床、刀具进行调整。
如输入刀具参数及刀具补偿参数、输入或修改零点偏置、输入设定数据。
加工中心调平

加工中心使用一段时间后,会出现精度下降的情况,原因有可能是设备水平扭曲发生变动(尤其是底部八点支撑卧式加工中心),因此需要定期对设备水平扭曲进行检查,校准。
设备工具示意图如下:工具1.检棒(BT40,BT50等,与主轴锥形孔规格一致)、2.水平仪(高精度0.02mm/m,选择质量好一点的,测量结果准确,使用寿命长)过程1.设备整体分工作台和主轴两部分,见示意图。
而工作台又可分为两部分看(左右两部分或者前后两部分)。
测量扭曲,即测量工作台两部分的平行度。
2.1-8点代表设备的8个地脚螺栓(可调整),一般情况下,优先调整1,2点和7,8点,而3,4点和5,6点位于中间连接处,易影响工作台与主轴的位置度,尽量不调,可微调。
33.将2个水平仪如图分别沿X,Z方向放置工装平面上,中间气泡在有效范围内。
将工作台用手轮从Z轴原点位置,前进一点,然后开始平缓的前进到Z轴终点,分别记录开始位置,中间位置(中间可停顿看格数变化)和终点位置,这个3个位置的气泡格数变化(至少操作两次,分别记录2个水平仪的气泡位置的变化)若变化在0.5-1格以内,则扭曲没问题,若超过1格,则需调整。
64.例如:1号水平仪在沿向X+方向(自南向北)移动时,气泡往X-方向(西侧)偏移2格,说明西侧西北角高,调整2号地脚,扭紧床身螺母,使床身下压。
如果螺母紧到极限位置,则调整下端斜铁,顺时针拧斜铁螺栓,使床身下压。
直至测量是气泡偏移格数在1格以内。
注意事项1.扭曲测量是可以带工装测量的,水平测量不能带工装,必须在设备自身的平台面上;2.有的卧加较小,是三点定位的,设备本身无扭曲,不需测量;3.尽量不要调整3,4,5,6这四个点,微调可以;4.扭曲调整是建立在设备水平已经调整完的前提下;5.水平仪测量的实际倾斜值=标称分度值×L×偏差格数,例如:标称分度值为0.02mm/m,L=200mm,偏差格数为2格则:实际倾斜值0.02/1000×200×2=0.008mm。
加工中心三合一参数设置

加工中心三合一参数设置摘要:一、引言二、加工中心三合一参数设置的必要性三、加工中心三合一参数设置的具体步骤1.选择合适的切削刀具2.设置加工工艺参数3.设定刀具路径四、参数设置中应注意的问题五、总结正文:在现代机械加工领域,加工中心已经成为一种不可或缺的设备。
而加工中心的三合一参数设置,更是决定了加工效率和加工质量的关键因素。
本文将详细介绍加工中心三合一参数设置的相关内容。
首先,我们需要明确加工中心三合一参数设置的必要性。
三合一参数设置,即切削刀具的选择、加工工艺参数的设置以及刀具路径的设定。
这三个环节相辅相成,缺一不可。
只有做好三合一参数设置,才能确保加工过程的顺利进行,达到预期的加工效果。
接下来,我们将详细介绍加工中心三合一参数设置的具体步骤。
第一步,选择合适的切削刀具。
切削刀具的选择应根据加工材料的性质、加工精度要求以及刀具的成本等因素综合考虑。
此外,还要注意刀具的耐用性和可更换性,以降低刀具的更换频率,提高加工效率。
第二步,设置加工工艺参数。
加工工艺参数包括主轴转速、进给速度、切削深度等。
这些参数的设置要根据加工材料、刀具类型以及加工目标等因素来调整。
合理的加工工艺参数可以保证加工过程的顺利进行,提高加工质量。
第三步,设定刀具路径。
刀具路径的设定要充分考虑加工过程中刀具的运动轨迹,以尽可能减少刀具的空行程,提高加工效率。
同时,还要避免刀具在加工过程中与工件或夹具发生干涉,确保加工过程的安全性。
在参数设置过程中,还应注意以下问题:首先,要确保参数设置的合理性,避免因参数设置不当导致的加工过程出现问题;其次,要注重数据的记录和备份,以便在出现问题时,可以快速找到原因并进行调整;最后,要定期对设备进行检查和维护,确保设备的正常运行。
总之,加工中心三合一参数设置是影响加工效率和加工质量的重要因素。
只有做好三合一参数设置,才能确保加工过程的顺利进行,满足生产需求。
机床加工加工中心运行参数优化
机床加工加工中心运行参数优化现代机床加工加工中心在制造业中发挥着至关重要的作用。
为了提高机床的加工效率和加工质量,优化运行参数成为了必要的措施之一。
本文将介绍机床加工加工中心运行参数优化的一些方法和策略。
一、机床加工加工中心运行参数的重要性机床加工加工中心的运行参数对加工效率和加工质量有着直接的影响。
合理调整和优化运行参数可以提高加工速度、降低能耗,并且减少加工中的误差和品质问题。
因此,合理的运行参数是保证加工中心正常高效运行的关键。
二、运行参数的种类机床加工加工中心的运行参数主要包括进给速度、主轴转速、切削速度、切削深度等。
这些参数的选择和设置需要根据不同的零件和加工要求进行调整。
一般来说,根据不同材料的硬度、切削性能和要求的表面精度等因素,选取适合的运行参数可以达到最佳的加工效果。
三、参数优化的方法和策略1. 实验法:通过反复试验和测试来寻找最佳的运行参数。
这种方法需要进行大量的实验,不仅耗时耗力,还需要具备一定的实验设备和技能。
2. 模拟仿真法:通过计算机模拟和仿真来评估不同运行参数的效果。
这种方法可以节省时间和成本,同时还可以避免实验带来的一些安全隐患。
3. 专家系统法:利用专家系统和人工智能技术来建立优化模型,通过对历史数据和专家知识的分析,得出最佳的运行参数。
这种方法具有较高的准确性和效率。
四、参数优化的注意事项在进行参数优化时,需要注意以下几个方面:1. 数据采集的准确性:确保采集到的数据准确可靠,避免人为或仪器误差对结果的影响。
2. 参数范围的合理性:根据机床的性能和制造要求,合理选取参数的范围。
过小的参数范围可能导致性能不足,过大的参数范围则可能导致加工质量下降。
3. 参数间的关联性:不同参数之间存在一定的关联性,需要综合考虑其对加工过程的影响。
单独优化某个参数可能会导致其他参数的失衡。
4. 实时监测与调整:机床加工加工中心运行参数的优化是一个动态过程,需要实时监测加工状态和参数调整,使得加工过程能够保持在最佳状态。
加工中心产品调试基本步骤
加工中心产品件调试基本步骤
1.确认图纸找出其中的加工内容重要尺寸关键点
2.确认加工图档对比图纸毛坯成品活三者尺寸关系(是否
改版)
3.确定产品件本序的装夹方式分析X Y Z 三轴的极限位置(工
件的装夹方向是否容易出错)做定位装置
4.明确工序的分中方式压表位置点(确认分中的类型和坐标
序号)
5.选择刀具并对刀仔细检查一一对应(确定刀具的材质类
型长度刃数直径磨损程度)(了解每把的加工内容是什么,明确主要易磨损刀具)
6.准备好本工序所用的量具和工装(游标卡尺千分尺等)
7.后处理,1将Q1替换成Q0 2是否添加M0 3工序号名称是
否填写正确
8.开始调试加工1启动单步(对比刀具高度值和机床坐标是
否合理)2打开手轮模拟(验证程序和加工参数调机操作是否正确)
9.测量测量图纸所标注的所有尺寸值(是否需要更改程序或
者刀具补偿值)。
加工中心调水平技巧
加工中心调水平技巧加工中心可是机械加工领域的“大拿”,它要想好好干活,调水平那可是关键中的关键,就如同盖房子得先打好地基一样重要。
咱先说说为啥加工中心得调水平。
这加工中心就像一个超级精密的大厨,它加工出来的零件那得是“色香味”俱全,精度要求高得很。
要是它站得歪歪扭扭,就像人走路不稳似的,加工出来的零件肯定也会“走样”。
比如说,本来要做一个方方正正的零件,结果因为加工中心没调平,可能就变成了个梯形,这可咋行?所以调水平就是要让加工中心稳稳当当,确保每一刀下去都精准无误。
那怎么开始调呢?这就好比给一个巨人找平衡,得有合适的工具。
水平仪可是必不可少的家伙,它就像加工中心的“体检医生”,能精准地测出加工中心的“身体状况”。
把水平仪放在加工中心的工作台或者导轨上,就像给它把脉一样,看看哪里高哪里低。
要是水平仪的气泡偏向左边,那就说明左边低右边高,这时候就得想办法调整了。
调整的时候啊,加工中心底部的地脚螺栓就派上用场了。
这螺栓就像巨人的脚指头,可以通过旋转它们来改变加工中心的高度。
如果发现某个角落低了,就把对应的地脚螺栓拧紧一点,慢慢地把它抬高,就像把陷下去的脚指头往上抬一抬,让身体重新平衡。
不过这过程可得小心翼翼,不能太猛,不然就像人突然用力过猛会摔倒一样,加工中心也会“受伤”,精度可能就被破坏了。
在调的过程中,还有个小窍门。
可以从加工中心的不同位置测量,就像给人全身检查一样,不能只看一个地方。
因为有时候某个局部看起来平了,但整体可能还是有偏差。
就像看一个人,只看脸觉得挺好看,一看身材比例不协调,那也不行啊。
多测几个点,取个平均值,这样才能让加工中心真正达到平衡状态。
还有哦,环境因素也不能忽视。
加工中心就像个娇弱的宝宝,温度、湿度的变化都会影响它。
如果车间里温度忽高忽低,就像人一会儿在蒸笼里一会儿在冰窖里,加工中心也会“不舒服”,精度可能就会跟着“闹脾气”。
所以尽量保持车间温度稳定,给加工中心创造一个舒适的“家”。
加工中心精度参数设置
加工中心精度参数设置加工中心是一种高精度、高效率的数控机床,广泛应用于航空、汽车、电子、模具等行业中。
加工中心的精度参数设置对加工效果和产品质量有着非常重要的影响。
本文将就加工中心的精度参数设置进行详细介绍,希望能够对相关工作者有所帮助。
一、加工中心的精度参数包括:1. 位置精度:位置精度是指在一定时间和温度条件下,加工中心在规定的工作空间内,不同位置上定位误差的精度。
对于加工中心来说,位置精度是一个非常重要的指标,包括定位精度、重复定位精度、圆跳动误差等。
2. 加工精度:加工精度是指加工中心在加工过程中,所能达到的工件尺寸和形位公差的精确度。
这主要与机床自身的精度、刀具选择、刀具磨损、切削参数等因素有关。
3. 重复定位精度:重复定位精度是指机床在多次加工同一工件时,各个定位点的偏差范围。
重复定位精度直接影响加工中心的加工稳定性和一致性。
4. 声压级:声压级是指加工中心在工作时产生的噪音水平。
高精度的加工中心通常能够降低噪音水平,提高工作环境的舒适度。
5. 表面粗糙度:表面粗糙度是指工件在加工中心上加工后的表面质量。
精度高的加工中心可以实现更高的表面光洁度和精度。
二、加工中心的精度参数设置方法1. 机床维护保养:定期对加工中心进行维护保养,包括润滑、除尘、检查传动系统、检查机床精度部件等。
2. 确定切削参数:在进行加工过程中,要根据工件的材料、形状和要求,确定合适的切削参数。
这包括进给速度、主轴转速、切削深度、切削速度等。
3. 选择合适的刀具:刀具的选择对加工精度有着直接的影响,需要根据工件材料和形状选择合适的刀具,并根据加工参数进行合理的刀具安装和调试。
4. 清洁工作环境:保持加工中心的工作环境清洁整洁,减少灰尘和杂质的干扰,确保加工精度参数的稳定性。
5. 定期检查校正:定期对加工中心的精度参数进行检查和校正,及时发现并修正精度偏差。
三、加工中心的精度参数设置的重要性1. 影响产品质量:加工中心的精度参数设置直接关系到加工出来的工件质量,尤其是在一些对精度要求较高的行业,如航空航天、医疗器械等,良好的精度参数设置是保证产品质量的重要保障。
- 1、下载文档前请自行甄别文档内容的完整性,平台不提供额外的编辑、内容补充、找答案等附加服务。
- 2、"仅部分预览"的文档,不可在线预览部分如存在完整性等问题,可反馈申请退款(可完整预览的文档不适用该条件!)。
- 3、如文档侵犯您的权益,请联系客服反馈,我们会尽快为您处理(人工客服工作时间:9:00-18:30)。
西门子840D重写数据前的总清方法
1.NC全清步骤
(1)将NC启动开关S3拨到“1”的位置
(2)启动NC,如NC已启动,可按一下复位按钮S1
(3)待NC启动成功,七段显示器显示“6”,将S3拨到“0”的位置,NC 全清执行完成。
2.PLC全清步骤
(1)将PLC启动开关S4–>“2”,PS灯会亮。
(2)S4–>“3”并保持约3秒等到PS灯在次亮;PS灯灭了又再亮。
(3)在3秒之内,快速的执行下述操作S4:“2”–>“3”–>“2”;PS灯先闪,后又亮,PF灯亮。
(有时PF灯不亮)
(4)等PS和PF灯亮了,S4–>“0”;PS等和PF灯灭而PR灯亮。
(”–>”表示拨到开关至某位置)
3.完成以上步骤PLC和NC应处于运行模式,NC上的两排LED的最上面的两个绿灯亮,七段数码管显示数字“6”。
海勒加工中心常用参数
1.光栅尺屏蔽参数30200(1)编码器数量,30240(1)编码器类型【4代表增量式编码器,0代表没有】
2.丝杠螺距参数30310
3.主轴夹紧力检测DB190.DBW40,参数14510(40.41.42)
4.JOG快速进给调整32010
5.参考点偏置34090(X.Y.Z修改1号位,C轴主轴角度0号位代表低速,1号
位代表高速)
6.线性尺分隔时段31010(LB0.04、LS0.02)
7.机械手原点检测DB190.DBW12、DB190.DBW14、DB190.DBW18.。