年产1000吨的PVC生产工艺设计
年产万吨聚氯乙烯车间工艺设计

一、工艺流程概述1.原料准备:将乙烯气体通过氯化反应和氯化工艺制备成氯乙烯。
2.聚合反应:将制备好的氯乙烯与过氯化钴等催化剂进行聚合反应,生成聚氯乙烯。
3.精炼和提炼:通过卸料和提炼过程,除去聚合反应产生的杂质和残留催化剂。
4.融化加工:将精炼和提炼后的聚氯乙烯经过加热和融化,通过挤出、注塑、吹膜等加工工艺,制成各种产品。
5.产品检验:对融化加工后的产品进行物理性能和质量的检验。
6.包装和出库:将合格的产品进行包装,并出库销售。
二、关键设备的选择和工艺参数的确定1.氯化塔:采用液氯氯化法,选择高效的氯化塔设备,保证氯化反应的高效进行。
2.反应釜:选择适当规格的不锈钢反应釜,对聚合反应进行控制。
3.蒸馏塔:选择具有高效蒸馏性能的蒸馏塔,进行精炼和提炼过程。
4.挤出机、注塑机、吹膜机等加工设备:选择具有高效和稳定性能的加工设备,满足产品加工要求。
5.检测仪器:选择高精度的物理性能和质量检测仪器,确保产品符合标准要求。
三、安全措施和环保要求1.氯气泄漏报警和处理系统:设置氯气泄漏探测器,在发现泄漏情况时及时报警,并启动处理系统进行处理,保证车间人员的安全。
2.废气处理系统:设置废气处理设备,对产生的废气进行处理,减少对环境的污染。
3.废水处理设施:建立废水处理系统,对产生的废水进行处理,达到排放标准。
4.严格操作规程和个人防护措施:制定严格的操作规程,包括操作流程、操作要求等,并提供个人防护装备,提醒员工遵守相关安全规定。
5.废弃物处理:建立废弃物分类处理系统,对废弃物进行分类、包装和处理,减少对环境的影响。
四、能源消耗和优化1.合理规划车间布局和设备布置,减少能源输送、损耗和消耗。
2.对设备进行定期检修和维护,保持设备运行的稳定性和高效性,减少能源的浪费。
3.提高工艺参数的优化,减少生产过程中能源的消耗。
4.引入智能化管理系统,对能源消耗进行实时监控和调整,达到最佳的能效。
总结:年产万吨聚氯乙烯车间的工艺设计需要考虑原料准备、聚合反应、精炼和提炼、融化加工、产品检验以及包装和出库等环节。
年产万吨聚氯乙烯车间工艺设计

年产万吨聚氯乙烯车间工艺设计1. 引言本文档旨在对年产万吨聚氯乙烯(PVC)车间的工艺设计进行详细说明。
PVC是一种重要的合成树脂,广泛应用于建筑材料、电线电缆、塑料制品等领域。
设计一个高效、稳定和可持续发展的车间工艺对于确保产品质量和提高生产效率至关重要。
2. 工艺流程2.1 原料准备PVC的主要原料包括乙烯、氯乙烯和氢氯酸等。
原料准备阶段需要对原料进行储存、提供和混合。
储存区域应具备良好的通风和防火设施,确保原料的安全性和稳定性。
2.2 反应PVC的生产主要通过聚合反应完成。
聚合反应要求严格的温度控制、压力控制和触媒添加。
反应釜设备应具备高效的加热和冷却系统,以确保反应的可控性和高效性。
2.3 分离和磺化在聚合反应完成后,需对产物进行分离和磺化处理。
分离过程主要通过卸料和过滤等方式进行,确保分离效果良好。
磺化处理则需通过控制温度和添加磺化剂等手段,使产物获得所需的性质和品质。
2.4 硫化经过分离和磺化处理后的产物需要进行硫化反应,以提高PVC的机械性能和耐候性。
硫化过程需要控制温度、压力和硫化剂的添加量,确保硫化反应的完全性和一致性。
2.5 润滑和加工硫化后的PVC需要进行润滑处理,以增强其流动性和加工性。
润滑处理一般通过添加润滑剂,同时需要控制温度和混合速度,以确保润滑剂均匀分布。
之后,PVC可进行成型、挤出、注塑等加工方式,制成最终的产品。
3. 设备需求为了实现年产万吨聚氯乙烯的目标,车间需要配置以下主要设备:•反应釜:高效的反应釜能够提供良好的加热和冷却系统,满足反应过程的要求。
•分离设备:包括卸料和过滤设备,能够实现有效和高效的分离过程。
•磺化设备:具备精确的温度控制和添加磺化剂的能力,以实现良好的磺化效果。
•硫化设备:提供准确的温度和压力控制,确保硫化反应的完全性和一致性。
•润滑设备:包括润滑剂添加设备和混合设备,能够实现均匀的润滑处理。
4. 安全和环境考虑在设计车间工艺时,安全和环境因素是非常重要的考虑因素。
年产万吨聚氯乙烯生产工艺设计

安装调试阶段:按照设计要求,安装设备并进行调试,确保生产工艺流程顺畅
试生产阶段:进行试生产,对产品进行检测和评估,确保产品质量符合要求
正式生产阶段:正式投入生产,对生产过程进行监控和管理,确保生产效率和产品质量稳定可靠
主要设备及参数选择
反应器类型:根据工艺要求选择合适的反应器类型
反应温度:控制反应温度,保证反应效率
Part Three
年产万吨聚氯乙烯生产工艺方案
方案设计依据和原则
依据:市场需求、产品用途、生产工艺要求等
原则:经济性、可行性、环保性、安全性等
方案流程说明
准备阶段:确定生产工艺方案,进行市场调研和可行性分析
设计阶段:根据产品要求,设计生产工艺流程,进行设备选型和配置
采购阶段:根据设计方案,采购原材料和设备,确保质量合格
项目主要目标和意义
提高聚氯乙烯生产效率,降低成本
优化生产工艺,提高产品质量
推动聚氯乙烯产业升级,提高市场竞争力
促进地方经济发展,增加就业机会
Part Two
聚氯乙烯生产工艺流程及特点
聚氯乙烯生产工艺流程
单击此处输入你的正文,请阐述观点
聚合反应:在催化剂的作用下,氯乙烯单体发生聚合反应生成聚氯乙烯树脂
项目背景及介绍
项目背景介绍
项目名称:年产万吨聚氯乙烯生产工艺设计
项目背景:随着聚氯乙烯市场的不断扩大,市场需求量不断增加,为了满足市场需求,提高产品质量和降低成本,需要进行生产工艺设计
项目目标:设计一套高效、稳定、环保的聚氯乙烯生产工艺,提高产品质量和降低成本,满足市场需求
项目意义:提高聚氯乙烯生产效率,降低生产成本,提高产品质量和竞争力,促进聚氯乙烯行业的发展
,a click to unlimited possibilities
10000吨年硬聚氯乙烯管材生产车间工艺设计
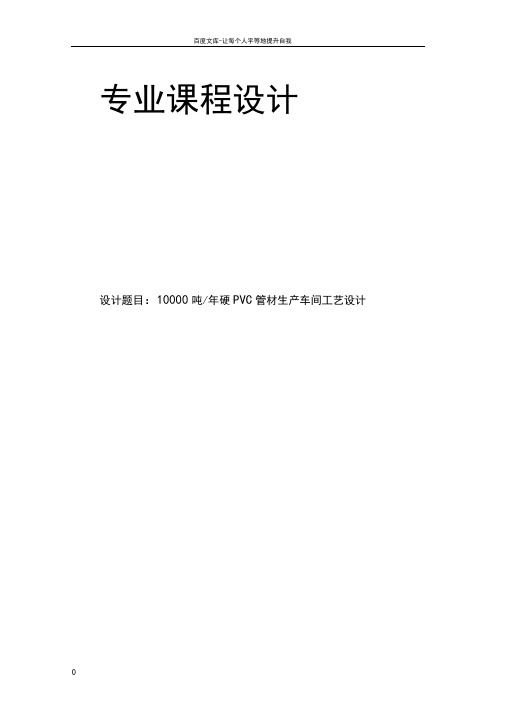
设计题目:10000吨/年硬PVC管材生产车间工艺设计
专业课程设计任务书
一、课程设计课题硬聚氯乙烯管生产车间工艺设计
二、课程设计工作自2011年12月26日起至2012年1月11日止
三、课程设计进行地点本校
四、设计原始数据:
7200小时;
PVC管材合格率
物料损耗系数
工序
造粒工段
挤出成型工段
74 〜73
1650〜1500
电绝缘材料,一般软制品
SG-3
53.0
135〜127
72 〜71
1500〜1350
电绝缘材料,农膜,塑料鞋
SG-4
56.5
126〜119
70 〜69
1250〜1150
薄膜,人造革,高强度硬管
SG-5
58.0
118 〜107
68 〜66
1100 〜1000
透明制品,硬管,型材
1.4
设计配方的原则是根据使用要求,根据我国已经制定了各类管材标准进行, 管材配方中包含:pv(W脂,抗冲击改性剂,稳定剂,加工改性剂,填充剂、色 料及外润滑剂等成分。
1.4.1ห้องสมุดไป่ตู้脂
塑料制品的物理机械性能取决于树脂的分子量,分子量愈高其物理机械性
能及耐热性能愈好。但分子量高,加工流动性能差。特别是硬质pvc它的加工
粒粒料单螺杆挤出机挤出管材冷却定型牵引切割管材。
硬管的成型方法很多,挤出〜牵引法生产的PVC硬管,产量高、成本低、收 效快,利用一台挤出机可以生产出多种规格的管材。
1.3
(1)依据硬聚氯乙烯管生产车间工艺设计任务书。及老师的要求。
(2)依据有关于硬聚氯乙烯管材的国标等要求,认真贯彻国家建设方针、政 策及有关规定,精心设计,保证设计质量。
PVC管材生产车间工艺设计
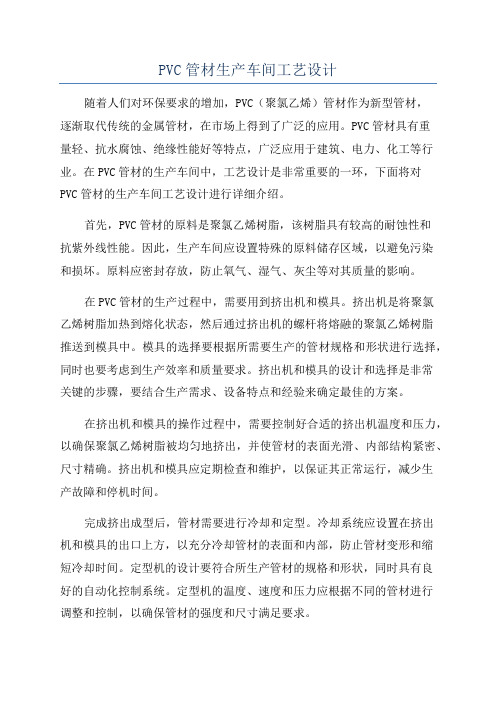
PVC管材生产车间工艺设计随着人们对环保要求的增加,PVC(聚氯乙烯)管材作为新型管材,逐渐取代传统的金属管材,在市场上得到了广泛的应用。
PVC管材具有重量轻、抗水腐蚀、绝缘性能好等特点,广泛应用于建筑、电力、化工等行业。
在PVC管材的生产车间中,工艺设计是非常重要的一环,下面将对PVC管材的生产车间工艺设计进行详细介绍。
首先,PVC管材的原料是聚氯乙烯树脂,该树脂具有较高的耐蚀性和抗紫外线性能。
因此,生产车间应设置特殊的原料储存区域,以避免污染和损坏。
原料应密封存放,防止氧气、湿气、灰尘等对其质量的影响。
在PVC管材的生产过程中,需要用到挤出机和模具。
挤出机是将聚氯乙烯树脂加热到熔化状态,然后通过挤出机的螺杆将熔融的聚氯乙烯树脂推送到模具中。
模具的选择要根据所需要生产的管材规格和形状进行选择,同时也要考虑到生产效率和质量要求。
挤出机和模具的设计和选择是非常关键的步骤,要结合生产需求、设备特点和经验来确定最佳的方案。
在挤出机和模具的操作过程中,需要控制好合适的挤出机温度和压力,以确保聚氯乙烯树脂被均匀地挤出,并使管材的表面光滑、内部结构紧密、尺寸精确。
挤出机和模具应定期检查和维护,以保证其正常运行,减少生产故障和停机时间。
完成挤出成型后,管材需要进行冷却和定型。
冷却系统应设置在挤出机和模具的出口上方,以充分冷却管材的表面和内部,防止管材变形和缩短冷却时间。
定型机的设计要符合所生产管材的规格和形状,同时具有良好的自动化控制系统。
定型机的温度、速度和压力应根据不同的管材进行调整和控制,以确保管材的强度和尺寸满足要求。
最后,对于生产好的管材,还需要进行质量检查和包装。
质量检查应包括外观、尺寸和物理性能等方面的检验,以确保管材的质量符合标准要求。
包装应根据不同的管材规格和长度进行选择,以保护管材不受外界环境的影响,并方便运输和使用。
综上所述,PVC管材的生产车间工艺设计是一个复杂而细致的过程,需要考虑到原料储存、挤出机和模具的选择和设计、冷却和定型设备的安装和调试、质量检查和包装等方面的要求。
万吨聚氯乙烯车间工艺设计

万吨聚氯乙烯车间工艺设计1.工艺流程:PVC的生产工艺通常包括聚合、塑化、脱除不饱和气体、热稳定、挤出和制品成形等步骤。
聚合是PVC制备的关键步骤,通常采用悬浮聚合法,其中乙烯氯和稳定剂等原料在聚合釜中发生聚合反应。
塑化过程将聚合物颗粒加热成粘稠的熔体,以便后续处理。
脱除不饱和气体过程将熔融的PVC中的不饱和气体去除。
热稳定工艺用于防止PVC分解,在高温条件下添加热稳定剂。
挤出工艺将熔融的PVC通过模具挤出,形成所需的形状。
制品成形过程将挤出的PVC制品进行冷却、切割和包装。
2.设备布局:PVC车间的设备布局应考虑到安全、生产效率和操作便利性。
首先,应将不同的工艺步骤合理安排,以确保工序之间的流程顺畅。
例如,聚合反应器应位于PVC车间的中心位置,以便于原料的输入和产物的输出。
其次,应根据原料、中间产物和成品的特性进行合理的设备布置。
例如,塑化机、挤出机和制品成形设备应根据工艺流程的要求进行合理的布局,以方便操作和流程控制。
此外,应考虑设备的安全性和防火防爆要求,并合理布置安全设施和逃生通道。
3.能耗分析:在PVC车间中,能耗管理是至关重要的。
应进行能耗分析,找出能耗高的环节,并采取合理的措施降低能耗。
例如,在塑化过程中,采用高效的预热装置和加热系统,减少能量损耗。
在挤出过程中,采用高效的挤出机和冷却系统,减少能耗和水的浪费。
此外,应优化生产计划,避免设备空闲和停机时间,提高生产效率和能源利用率。
4.环保措施:PVC生产过程中会产生废水、废气和固体废物,对环境造成一定的影响。
为满足环保要求,应采取相应的环保措施。
首先,在废水处理方面,应安装废水处理设施,对生产废水进行处理,并达到排放标准。
其次,在废气处理方面,应安装废气处理设备,对排放的废气进行净化和回收利用。
最后,在固体废物处理方面,应实施废物分类和合理处置,减少对环境的负面影响。
综上所述,万吨级PVC车间的工艺设计应合理安排工艺流程,合理布局设备,进行能耗分析和实施环保措施,以确保生产的安全、高效和环保。
年产1000吨PVC波纹管材车间设计毕业设计 精品
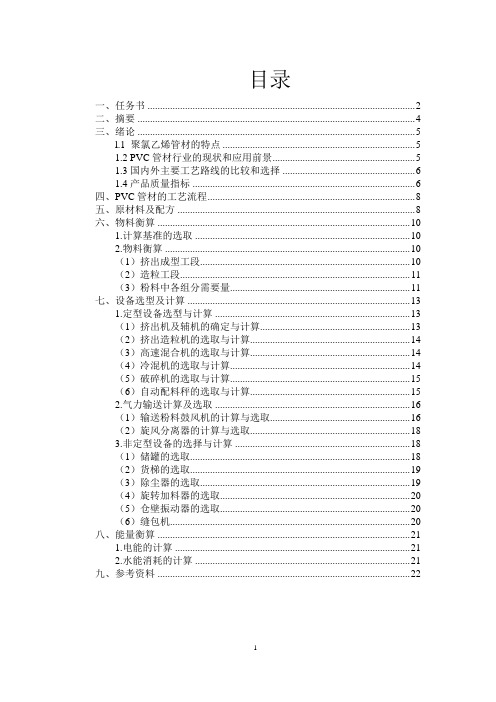
目录一、任务书 (2)二、摘要 (4)三、绪论 (5)l.1 聚氯乙烯管材的特点 (5)1.2 PVC管材行业的现状和应用前景 (5)1.3 国内外主要工艺路线的比较和选择 (6)1.4 产品质量指标 (6)四、PVC管材的工艺流程 (8)五、原材料及配方 (8)六、物料衡算 (10)1.计算基准的选取 (10)2.物料衡算 (10)(1)挤出成型工段 (10)(2)造粒工段 (11)(3)粉料中各组分需要量 (11)七、设备选型及计算 (13)1.定型设备选型与计算 (13)(1)挤出机及辅机的确定与计算 (13)(2)挤出造粒机的选取与计算 (14)(3)高速混合机的选取与计算 (14)(4)冷混机的选取与计算 (14)(5)破碎机的选取与计算 (15)(6)自动配料秤的选取与计算 (15)2.气力输送计算及选取 (16)(1)输送粉料鼓风机的计算与选取 (16)(2)旋风分离器的计算与选取 (18)3.非定型设备的选择与计算 (18)(1)储罐的选取 (18)(2)货梯的选取 (19)(3)除尘器的选取 (19)(4)旋转加料器的选取 (20)(5)仓壁振动器的选取 (20)(6)缝包机 (20)八、能量衡算 (21)1.电能的计算 (21)2.水能消耗的计算 (21)九、参考资料 (22)一、任务书PVC制品加工厂课程设计任务书一、设计名称年产1000吨PVC波纹管材车间设计二、课题条件学生已学过相关课程,可利用图书馆资料,进行必要的文献调研和数据查询,可提供计算机进行相关计算和辅助设计。
三、设计任务按扩大初步设计要求进行设计。
1.查阅资料,进行文献综述。
2.工艺流程设计3.选择原材料、确定配方4.物料平衡计算绘制物料流程草图。
确定各种物料的年、约、日、时消耗量。
完成物料平衡表。
5.设备选型及设计对定型设备进行选型并计算所需设备的台数,对非定型设备进行计算。
编制设备一览表。
6.能量衡算计算电能的消耗量、冷却剂的消耗量。
年产万吨聚氯乙烯生产工艺设计

年产万吨聚氯乙烯生产工艺设计引言聚氯乙烯(Polyvinyl Chloride,简称PVC)是一种重要的合成材料,广泛应用于建筑、汽车、电子、食品包装等领域。
年产万吨聚氯乙烯的生产工艺设计对于提高生产效率、降低成本具有重要意义。
本文将详细介绍年产万吨聚氯乙烯生产工艺的设计方案。
工艺流程年产万吨聚氯乙烯的生产工艺流程主要包括以下几个步骤:1. 原料准备聚氯乙烯的主要原料是乙烯和氯气。
乙烯是由石油和天然气中的轻烃类物质经过裂解、脱氢等加工步骤得到的。
氯气可以通过电解食盐水或者氯化氢与氧气反应得到。
2. 乙烯氯化将乙烯与氯气进行氯化反应,生成乙烯氯化物。
乙烯氯化反应一般在高温高压下进行,使用催化剂促进反应速度。
3. 聚合反应将乙烯氯化物进行聚合反应,生成聚氯乙烯。
聚合反应通常在聚合釜中进行,同时加入引发剂和调节剂来控制聚合反应的速率和分子结构。
4. 分离与精制将聚合物溶液进行分离,得到聚氯乙烯的粗品。
然后对粗品进行洗涤、脱水、干燥等工艺步骤,以获得高纯度的聚氯乙烯产品。
设计要点年产万吨聚氯乙烯生产工艺的设计要点包括以下几个方面:1. 工艺流程的稳定性与安全性工艺流程应具备良好的稳定性和安全性,确保生产过程的连续稳定运行。
在设计中应考虑到原料的质量波动、设备的故障停机等因素,合理设计反应釜和分离设备的容量和数量。
2. 能源消耗与环境保护在工艺流程设计中应考虑到能源消耗和环境保护的问题。
采用先进的能源回收技术和废气处理技术,降低生产过程中的能源消耗和排污量,提高资源利用效率。
3. 产品质量与生产效率在工艺设计中应注重产品质量和生产效率的提高。
选择合适的催化剂和控制剂,优化聚合反应条件,控制产品的分子量和分子量分布,以及产品的溶解度和熔点等性能。
4. 辅助设施与管理系统除了主要的生产设备外,还需考虑到辅助设施和管理系统的设计。
包括原料仓储系统、废水处理系统、工艺控制系统等,以提高生产效率和管理水平。
结论年产万吨聚氯乙烯生产工艺设计是一个复杂的工程问题,需要综合考虑工艺流程的稳定性、安全性、能源消耗、环境保护、产品质量和生产效率等因素。
- 1、下载文档前请自行甄别文档内容的完整性,平台不提供额外的编辑、内容补充、找答案等附加服务。
- 2、"仅部分预览"的文档,不可在线预览部分如存在完整性等问题,可反馈申请退款(可完整预览的文档不适用该条件!)。
- 3、如文档侵犯您的权益,请联系客服反馈,我们会尽快为您处理(人工客服工作时间:9:00-18:30)。
物料衡算
该反应中物流变量有3个,加一个反应速率变量,共有4 个变量,有2种组分,赋值年产量PVC1000吨,转化率 为90%,自由度分析为:4-2-2=0。 本次设计目标为年产量1000吨的PVC片材,查阅资料 知,可假定物料自然消耗率为0.1%,产品合格率为94%, 回收率为90%。每年生产296天,二班轮流全天24小时 生产。物料衡算如下
年产1000吨的PVC生产工艺设计
指导老师:AAA 设 计 者:BBBB 报告时间:2018年11月26日
目
录
•PVC的简介
•工艺流程 •物料衡算
•设备选择
PVC的简介
聚氯乙烯(Polyvinyl Chloride, 简称PVC)是五大通用合成树脂之一,世界产 量和消费量仅次于聚乙烯和聚丙烯,列第三位。世界聚氯乙烯树脂消费以硬 制品为主,占总消费量的59.31%,软制品占33.08%,其它占7.61%。聚氯 乙烯的生产是通过氯乙烯单体聚合而成。 近年来,我国PVC表观消费量以年均10%—15%的速度增长,PVC在各领 域的应用比例正在不断变化,软制品消费比例逐年下降,而异型材、管材、 板材等主要用作建筑材料的硬制品的消费比例不断提高。此外,包装、农业、 汽车、医疗、日常生活用品等领域对PVC的需求量也将不断增长。
设备选择
搅拌装置的设计
根据搅拌物料的性质、搅拌要求选用平直叶桨式搅拌器,由于料液层比较高, 为了将物料搅拌均匀,故本设计采用三层两叶平桨。
离心机的选择
在实际工业生产存在有进料泵、回流泵、塔底泵、循环泵、产品泵等不同泵种, 其中石油化工泵的选择应满足其工艺所需的流量、扬程、压力、温度、气蚀余 量等工艺参数指标,满足介质特性要求以及现场安装要求。
1—纯水贮槽;2—纯水计量 泵;3—纯水计量槽;4—纯 水入料泵;5—氯乙烯单体计 量槽;6—加料小罐;7— PVA贮槽;8—HPMC贮槽; 9—PVA循环泵;10—HPMC 循环泵;11—PVA计量罐; 12—HPMC计量罐;13—分 散剂入料泵;14—夹套水循 环泵;15—聚合釜;16—出 料槽;17—泡沫捕集器; 18—洗涤塔;19—洗涤塔受 水槽;20—喷淋水循环泵; 21—回收单体过滤器;22— 压缩机;23—气水分离器; 24—一段冷凝器;25—二段 冷凝器;26—中间槽;27— 回收单体贮槽。
谢 谢
国内近几年产能及价格图表
工艺流程
聚氯乙烯是由氯乙烯通过自由基聚合而成的。有悬浮聚合法、乳液聚合法和 本体聚合法,以悬浮聚合法为主,约占PVC总产量的80%左右。 悬浮聚合法 使单体呈微滴状悬浮分散于水相中,选用的油溶性引发剂则溶 于单体中,聚合反应就在这些微滴中进行,聚合反应热及时被水吸收,为了 保证这些微滴在水中呈珠状分散,需要加入悬浮稳定剂,如明胶、聚乙烯醇、 甲基纤维素、羟乙基纤维素等。引发剂多采用有机过氧化物和偶氮化合物, 如过氧化二碳酸二异丙酯过氧化二碳酸二环己酯、过氧化二碳酸二乙基己酯 和偶氮二异庚腈、偶氮二异丁腈等。聚合是在带有搅拌器的聚合釜中进行的。 聚合后,物料流入单体回收罐或汽提塔内回收单体。然后流入混合釜,水洗 再离心脱水、干燥即得树脂成品。
每小时车间处理物料量 M5=1063.83/296/24h≈0.15t 年40t 新料量 M7=M2-M6=1064.89-58.40=1006.49t
设备选择
聚合釜的选择
制备高分子化合物的主要设备。一般是立式圆柱形高压釜,带有夹套,以便通 入蒸汽或冷水来加热或冷却。用于乳液聚合的,内有不锈钢的水平桨式搅拌器, 由电动机通过传动装置和减速器传动。釜的外壁常用碳钢制成,内衬不锈钢, 也有衬搪瓷的。聚合时可以间歇生产,也可以多釜串联连续生产。
物料衡算
年需要物料量 M1=合格产品量/合格率=1000/0.94≈1063.83t 年车间进料量 M2= M1/(1-物料自然消耗率)=1063.83t /(1-0.1%)≈1064.89t 年自然消耗量 M3=M2-M1=1064.89-1063.83=1.06t 年废品量
M4=M1-合格产品量=1063.83-1000=63.83t
对于连续反应釜:
在55℃下,水的密度是985.65kg/m³ ,PVC 密度是1400kg/m³ , VCM进料9.264×105kg/B ,脱盐水进料 8.769×105/B, 可知每批的最大体积V=1629m³ 反应釜实际个数:nt=V/(Vt×α) Vt为 135m³ ,α为0.8 nt=1629/(135×0.8)=15.08≈16 为确保维修不影响生产,多设一台备用机, 所以本次设计采用2个搅拌式聚合釜