大众汽车标准 _VW91104概要
大众标准中文版

大众汽车集团标准 TL 244 2010年12月版分类号:50223关键字:锌,镍,钝化处理,密封,无Cr(VI),防腐蚀,表面保护锌/镍-合金涂覆层表面保护要求旧版本TL 244: 1987-10, 1992-05, 1993-11, 1995-12, 2002-05, 2004-12, 2006-08, 2007-02变更相对于 TL244: 2007-02 版本,作了如下更改:--补充了热处理后零件的抗拉强度≦ 1200Mpa 部分;--添加了 Ofl-r647 和 Ofl-r648 两种涂覆方法;--原表 2 中关于含铬的表面保护类型已删除;--添加了图 1 和图 2;--添加了 PV 1209,PV 1200 和 PV1210 三种测试依据;--镀层表面形态的要求有所增加;--镍的上限值有所改变;--原第 4 条关于镀层厚度的测量的内容加入到部分;--原部分的要求有所改变;--参考标准有更新;--标准重组。
1 范围本标准规定了抗拉强度为 Rm≦ 1000Mpa(按 VW 137 50 的特征字母 r)的铁材料和钢制件上的电解离析和无Cr( VI)后处理的锌/镍合金涂覆层的要求。
此外还定义了抗拉强度值大于 1000Mpa时的应用极限。
本标准定义了合金涂覆不适用于抗拉强度 Rm>1200Mpa 和表面硬度>370HV 的钢制件。
而且适用于抗拉强度值在 1000Mpa 和 1200Mpa之间的钢制件时,必须按 DIN EN ISO4042 作热处理。
这些当作坚固防腐层(稳定等级为 6)的涂覆层,亦特别适用于除了腐蚀负荷增加和温度负荷增加至150°C(例如:发动机室和刹车系统)之外的部件以及螺栓拧紧系统。
银色涂覆层(例如:Ofl-r642,Ofl-r643,Ofl-r645和Ofl-r647)特别适用于导线连接(接地线连接)。
这些涂覆层特别适用于内部传动的紧固元件,以避免附加的施力作用。
vw线束标准

VW线束标准是指大众汽车集团(Volkswagen Group)在汽车线束领域的技术标准和规范。
该标准旨在确保线束在性能、质量和安全性方面达到一致标准,以保障车辆和乘客的安全。
以下是关于VW线束标准的一些要点:
1.线束是汽车电气系统的核心组成部分,负责将车辆各个电气元件连接起来,实现电力传输和信息
传递。
2.VW线束标准的制定旨在确保线束在性能、质量和安全性方面达到一致标准。
该标准涉及线束的
规格、材料、工艺、测试等方面的要求。
3.VW线束标准规定了线束的截面积、颜色、标识、连接方式等方面的要求,以确保线束的可靠性、
耐久性和安全性。
4.VW线束标准还规定了线束与其他汽车组件的兼容性和接口要求,以确保车辆的整体性能和可靠
性。
5.VW线束标准不仅适用于大众汽车集团旗下的品牌,也适用于其他汽车制造商的汽车线束领域。
该标准的推广和应用有助于提高整个汽车行业的电气系统性能和安全性。
总之,VW线束标准是一种技术标准和规范,旨在确保汽车电气系统的性能、质量和安全性达到一致标准。
该标准的推广和应用有助于提高整个汽车行业的电气系统性能和安全性。
大众汽车标准_VW 01055-Y
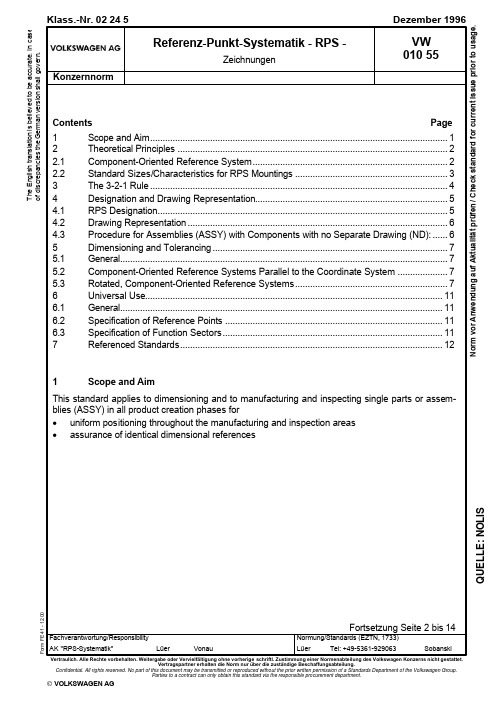
Vertragspartner erhalten die Norm nur über die zuständige Beschaffungsabteilung.Confidential. All rights reserved. No part of this document may be transmitted or reproduced without the prior written permission of a Standards Department of the Volkswagen Group.Parties to a contract can only obtain this standard via the responsible procurement department.© VOLKSWAGEN AGN o r m v o r A n w e n d u n g a u f A k t u a l i t ät p r üf e n / C h e c k s t a n d a r d f o r c u r r e n t i s s u e p r i o r t o u s a g e .T h e E n g l i s h t r a n s l a t i o n i s b e l i e v e d t o b e a c c u r a t e . I n c a s e o f d i s c r e p a n c i e s t h e G e r m a n v e r s i o n s h a l l g o v e r n .Q U E L L E : N O L I SSeite 2VW 010 55: 1996-122 Theoretical Principles2.1 Component-Oriented Reference SystemOne of the basic ideas forming the basis for the reference point system is the component-oriented coordinate system according to VW 010 52.A vehicle is dimensioned by means of a global coordinate system (mathematical vehicle coordinate system), the origin of which is defined to be in the center at the level of the front axle of a vehicle (see VW 010 59 Part 1; VW 010 52 is the binding reference for the vehicle coordinate system), Figure 1.A Vertical plane S Longitudinal center plane D Horizontal planeFigure 1. Global coordinate system for vehiclesStarting from the axes of this coordinate system, grid lines are spread out parallel to the axes. These grid lines, spaced 100 mm apart, theoretically penetrate the vehicle. These grid lines serve to find all points on the vehicle. In other words, they help to determine the position of each vehicle component. Dimensioning is also performed with the aid of these grid lines.The reference point system is based on a component-oriented reference system.The origin of the component reference system is defined by the intersection point of three refer-ence planes. The reference planes are formed via the RPS main mountings defined on the compo-nent.When several parts are assembled, these parts are toleranced with respect to each other.After the parts are joined, the ASSY is described by a combined component-oriented reference system. This is formedby adoption of one of the existing reference systems orby forming a new reference system using the existing reference points.The specification of the new reference system depends on the function of the ASSY.Seite 3VW 010 55: 1996-122.2 Standard Sizes/Characteristics for RPS MountingsMultiple-use location holes with high precision requirements must be adequately strong.In general, the standard sizes according to Table 1 and Table 2 shall be used. In case of holes in RPS surfaces, it must be ensured that the bearing surfaces are of adequate size and provide proc-ess assurance.The specified dimensions shall be projected – parallel to the axes – onto the component.Table 1.Recommended standard valuesFor further standard sizes see VW 010 77Designation Nominal dimen-sionTol.Graphical representationL o c at i o n h o l e s ,p l u g g a b l eRound hole see VW 01077101520Square25+16 x 2010 x 20Rectangle15 x 20+1Ø 15Ø 20S u r f a c e sCircleØ 25+11020E d g e sEdge length "a"25+1Table 2.Recommended standard valuesFor further standard sizes see VW 010 78Designation Nominal dimen-sion w x lTol.Graphical representationLong holeL o c a t i o n h o l e s ,p l u g g a b l eLong hole in angle positionsee VW 01078Seite 4VW 010 55: 1996-123 The 3-2-1 RuleEvery rigid body possesses six degrees of freedom in three-dimensional space: three translational degrees parallel to the axes of a reference system and three rotatory degrees around the axes, Figure 2.Figure 2. The degrees of freedom in three-dimensional spaceIn order to support a non-rotationally-symmetric body in a uniquely determinate manner, it must be fixed in all six possible directions of movement. The 3-2-1-rule provides for such unique fixing. It determines the following main-mounting distribution:E.g. 3 mountings in z direction2 mountings in y direction1 mounting in x directionImplementation of this rule is shown based on the following representation, Figure 3.Figure 3. Application of the 3-2-1 ruleThe three mountings in z direction restrict three degrees of freedom: translation in z direction and rotation around the x and y axes. The pin in the round hole prevents motion parallel to the axes in the x and y directions and, finally, the pin in the long hole prevents rotation around the z axis, Fig-ure 3.This rule applies equally to any other rigid component, even if its structure is much more complex. With a system of rigid bodies, the elements of which are interconnected by joints or guides, more than 6 degrees of freedom must be fixed using additional main mountings.For non-rigid components, additional support points must be defined for supporting the compo-nents according to RPS aspects.RPS 1 shall be the point that binds the most degrees of freedom.Seite 5VW 010 55: 1996-124 Designation and Drawing Representation4.1 RPS DesignationAll RPS points must be included in the part drawing.The designation is subdivided as follows:•Main mounting points=Capitals?H =Hole? F =Surface?T =Theoretical pointis the mean of two support points •Support points=Small letters?h =Hole? f =Surface?t =Theoretical pointis the mean of two support points •Mounting types?Location holes/pins=Code letter H,h?Surfaces/edges/ball/tip=Code letter F,f?Theoretical point=Code letter T,t •Fixing directions=Small letters?x, y, z for component-oriented reference systems parallelto the coordinate system?a, b, c for rotated, component-oriented reference systems Examples of designation:Fixing directionCode letter for surface as main mountingFixing directionsCode letter for hole as main mountingDesignation with numberingFixing directionCode letter for surface as main mountingDesignation with numberingFixing directionCode letter for surface as support pointDesignation with numberingNumbering begins with the RPS 1 point for each single part and for each assembly.Seite 6VW 010 55: 1996-124.2 Drawing RepresentationDrawing representation takes place according to the valid drawing guidelines.The RPS surfaces shall be identified by means of cross-hatching.If a part drawing does not exist yet, RPS Dimensions Sheet FE 515 1) shall be used.As soon as the part drawing exists, the specifications from the RPS Dimensions Sheet are adopted directly in the drawing or adopted in text macro NO-F23 2). Administration of these specifications in the text macro is mandatory.4.3 Procedure for Assemblies (ASSY) with Components with no Separate Drawing (ND): The RPS points for components with no drawing (ND) must be identified by specifying the item number or part number.A drawing exists for part 1; ND for parts 2 and 3, Figure 4.A RPS 1 Hxy; RPS 1 Hxy for Item 3S RPS 2 Hx only for Item 3D RPS 1 Hxy only for Item 2F RPS 2 Hy; RPS 2 Hy for Item 2Fig. 4ASSY with RPS pointsGraphical representation, not adopted in drawing1) Stored in design data administration system under FEO 000 5152) Stored in design data administration system under NOF 000 023Seite 7VW 010 55: 1996-12 5 Dimensioning and Tolerancing5.1 GeneralDimensions and tolerances can be entered directly in the drawing or via the table, Figure 5.The starting point for dimensioning the components is generally the origin of the reference system. Form and functional dimensions with tolerances shall always be referenced to the origin of the ref-erence system.Example: The holes within a hole group are dimensioned with respect to each other. The position of the hole group is dimensioned with respect to the reference planes.In the fixing direction, the main mountings are positioned without tolerance with respect to the vehi-cle coordinate system / reference system.The origin/reference point is shown in the drawing or table. If two or three fixing directions are bound at one point, tolerancing must be separated according to the hole or surface. In this case, the surface must be identified one line lower in the table. Here, the surface is set to zero in the tol-erance zone. In the line in which the hole is set to zero, the tolerance zone for the surface shall be identified with a horizontal line, see the table in Figure 5.The support-point tolerances shall be defined according to the requirements.5.2 Component-Oriented Reference Systems Parallel to the Coordinate SystemThe origin of the reference system is defined without tolerances in the global vehicle coordinate system by means of a translation, Figure 55.3 Rotated, Component-Oriented Reference SystemsWith rotated reference systems, the theoretical angles of rotation must be specified in RPS Dimen-sions Sheet FE 515 1) or in the drawing table text macro NO-F23 2).If there are several angles of rotation, the angle specification and thus the sequence of rotations shall be obtained from the drawing. "See drawing" must be added to the table instead of the angle entry.The position of the reference point is determined by means of its x, y and z coordinates in the global vehicle coordinate system.Angles of rotation around the x, y and z axes are entered using mathematically positive or negative values. Positive angles are specified counterclockwise and negative angles clockwise.In the coordinate system, the horizontal axis is assigned an angle of zero.Nominal dimensions and tolerances are specified in a, b and c values in the RPS table.The fixing directions of the RPS points are specified as a, b and c values in the table and/or draw-ing, e.g. RPS 1 HabFc, Figure 6 and Figure 7.1), 2)see page 6Seite 8VW 010 55: 1996-12A if necessaryFig. 5Dimensioning with text macro NO–F23Seite 9VW 010 55: 1996-12A Reference point S View RSeite 10VW 010 55: 1996-12A Reference point S View R6 Universal Use6.1 GeneralThe purpose of the RPS is to provide process assurance/capability and repeat accuracy for the procedures in order to make them independent of setting work performed by the worker.The reference points must be used in all manufacturing, assembly, inspection and installation pro-cesses.In case of self-contained function sectors such as the side panel tank flap, a reference change in combination with functional dimensions to RPS planes is permissible.Prior to the specification of RPS points, it is absolutely necessary to define the functions of the sin-gle part and the relevant assemblies with their required functional tolerances.Reference points that were established at the beginning of a process must be kept for as long as possible. In order to avoid changes to arranged reference points, they are jointly defined – as early as possible in the design and development process – in consultation with all departments partici-pating in the production process.Reference points must be positioned at stable areas of a component that will remain unchanged even in further development and/or production processes.Reference points on components that move relative to the body during driving operation can be considered according to the 3-2-1 rule only in the actual design position.The RPS points on components that are used several times in vehicles and thus have multiple ref-erences to the global coordinate system can be shown without a global coordinate reference in the technical drawing.The reference point system is equally oriented toward the production process, toward the function sectors and toward the strategic quality goals, e.g. audit, process capability.6.2 Specification of Reference PointsParallelism to the coordinate system (holes and surfaces) must be observed when entering the reference points. In the case of rotated systems, parallelism to the reference planes must be o b-served.The RPS points must be produced in the tool sequence in which the greatest dimensional stability is attained.Whenever possible, reference points must be produced with a standardized shape (hole, surface), which must be defined in detail.If holes cannot be made in a component, surfaces or edges must be used to specify reference points.In the case of COP parts (transfer parts), the respective reference-point positions arise in the ASSY.6.3 Specification of Function SectorsUse of the RPS on a complex portion of the vehicle such as the dashboard requires a structure that addresses the development and design engineering systems and includes all parts, single parts and assemblies.A function sector includes all components in the visible and covered areas that directly affect their surroundings with their function points.The specification of reference planes depends on the spatial and geometric position relationship of a component with its surroundings.The reference planes are identical for a function sector. In other words, components or component groups and the surroundings have the same starting basis, Figure 8.A Dashboard ASSY function sector S Airbag function sectorD Center-vent function sector F Air outlet vent function sector FS Fig. 87 Referenced StandardsVW 010 52VW 010 59 T1VW 010 77VW 010 78。
VW91101_汽车环境标准: 汽车零件,生产材料,运行材料 避免有害物质
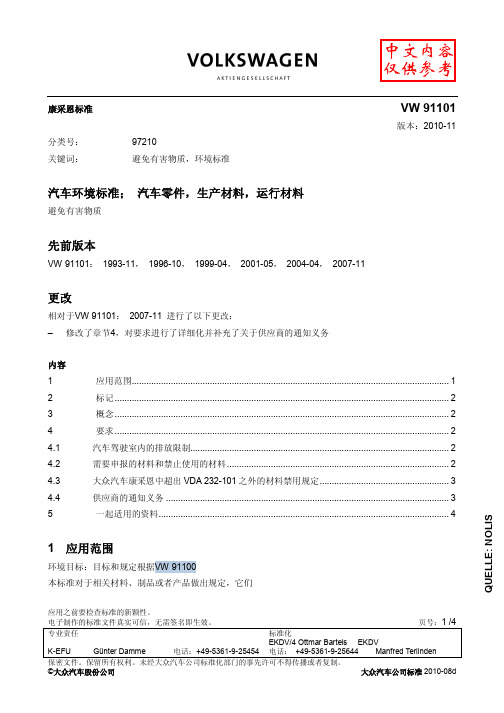
Q U E L L E : N O L I S应用之前要检查标准的新颖性。
电子制作的标准文件真实可信,无需签名即生效。
页号:1 /4 专业责任标准化 EKDV/4 Ottmar Bartels EKDV K-EFU Günter Damme 电话:+49-5361-9-25454 电话: +49-5361-9-25644 Manfred Terlinden 保密文件。
保留所有权利。
未经大众汽车公司标准化部门的事先许可不得传播或者复制。
康采恩标准VW 91101版本:2010-11分类号: 97210关键词: 避免有害物质,环境标准汽车环境标准; 汽车零件,生产材料,运行材料避免有害物质先前版本VW 91101: 1993-11, 1996-10, 1999-04, 2001-05, 2004-04, 2007-11更改相对于VW 91101: 2007-11 进行了以下更改: – 修改了章节4,对要求进行了详细化并补充了关于供应商的通知义务内容 1 应用范围 .................................................................................................................................. 1 2 标记 ......................................................................................................................................... 2 3 概念 ......................................................................................................................................... 2 4 要求 ......................................................................................................................................... 2 4.1 汽车驾驶室内的排放限制.......................................................................................................... 2 4.2 需要申报的材料和禁止使用的材料 ........................................................................................... 2 4.3 大众汽车康采恩中超出VDA 232-101之外的材料禁用规定 ..................................................... 3 4.4 供应商的通知义务 .................................................................................................................... 3 5 一起适用的资料 .. (4)1 应用范围环境目标:目标和规定根据VW 91100本标准对于相关材料、制品或者产品做出规定,它们中文内容仅供参考页号:2VW 91101: 2010-11– 通过大众汽车康采恩汽车销售国法律,或者– 与法律规范和使用地点无关而是通过大众公司康采恩内部决定禁止使用、限制使用或者服从其他管理规定。
大众标准中文版

大众汽车集团标准TL 2442010年12月版分类号:50223关键字:锌,镍,钝化处理,密封,无Cr(VI),防腐蚀,表面保护锌/镍-合金涂覆层表面保护要求旧版本TL 244: 1987-10, 1992-05, 1993-11, 1995-12, 2002-05, 2004-12, 2006-08, 2007-02变更相对于 TL244: 2007-02 版本,作了如下更改:--补充了热处理后零件的抗拉强度≦ 1200Mpa 部分;--添加了 Ofl-r647 和 Ofl-r648 两种涂覆方法;--原表 2 中关于含铬的表面保护类型已删除;--添加了图 1 和图 2;--添加了 PV 1209,PV 1200 和 PV1210 三种测试依据;--镀层表面形态的要求有所增加;--镍的上限值有所改变;--原第 4 条关于镀层厚度的测量的内容加入到部分;--原部分的要求有所改变;--参考标准有更新;--标准重组。
1 范围本标准规定了抗拉强度为 Rm≦ 1000Mpa(按 VW 137 50 的特征字母 r)的铁材料和钢制件上的电解离析和无Cr( VI)后处理的锌/镍合金涂覆层的要求。
此外还定义了抗拉强度值大于 1000Mpa时的应用极限。
本标准定义了合金涂覆不适用于抗拉强度 Rm>1200Mpa 和表面硬度>370HV 的钢制件。
而且适用于抗拉强度值在 1000Mpa 和 1200Mpa之间的钢制件时,必须按 DIN EN ISO4042 作热处理。
这些当作坚固防腐层(稳定等级为 6)的涂覆层,亦特别适用于除了腐蚀负荷增加和温度负荷增加至150°C(例如:发动机室和刹车系统)之外的部件以及螺栓拧紧系统。
银色涂覆层(例如:Ofl-r642,Ofl-r643,Ofl-r645和Ofl-r647)特别适用于导线连接(接地线连接)。
这些涂覆层特别适用于内部传动的紧固元件,以避免附加的施力作用。
大众汽车标准_VW 01106-1_EN_2004-07-01

Gas-Shielded Arc WeldingThe English translation is believed to be accurate. In case of discrepancies the German version shall govern.Sheet Steel Joints Design, Type, Quality AssuranceVW 011 06-1Konzernnorm Descriptors: welding, gas-shielded arc welding, steel, MIG welding, MAG welding, TIG welding, sheet steel, sheet steel joint, sheet metal ContentsPage1 2 2.1 2.2 3 3.1 3.2 4 4.1 4.2 4.3 5 5.1 5.2 5.3 5.4 5.5 6 7Scope .................................................................................................................................. 2 Abbreviations and definitions .............................................................................................. 2 Abbreviations ...................................................................................................................... 2 Definitions ........................................................................................................................... 3 Gas-shielded arc welding procedure................................................................................... 4 Tungsten inert-gas welding (TIG)........................................................................................ 4 Gas-shielded metal arc welding (MIG/MAG)....................................................................... 4 General requirements ......................................................................................................... 5 Materials.............................................................................................................................. 5 Design ................................................................................................................................. 8 Weld dimensions............................................................................................................... 10 Requirements for welds and quality assurance of welds .................................................. 12 Weld quality....................................................................................................................... 12 Penetration depths ............................................................................................................ 12 Weld types ........................................................................................................................ 13 Special weld types ............................................................................................................ 18 Evaluation of imperfections ............................................................................................... 23 Drawing entries ................................................................................................................. 23 Referenced standards....................................................................................................... 24Changes The following changes have been made as compared to VW 011 06-1, 2003-05: Referenced standards updated Standard edited Section 5.1 shortened Section 5.4 extended by special weld types (multiple front weld; corner joint) Section 5.4.1: requirements revised Previous issues 1997-01; 2003-05Preface The following basic regulations are based on experience gained with partially and fully mechanized equipment and implemented tests and also on accepted engineering standards such as DIN standards and DVS specifications.Form FE 41 - 01.03Page 1 of 25Fachverantwortung/Responsibility K-QS-32 Herr Dr. Witt Tel.: 7 36 23 Normung/Standards (EZTD, 1733) Fischer Tel.: +49-5361-9-2 79 95 Sobanski© VOLKSWAGEN AGConfidential. All rights reserved. No part of this document may be transmitted or reproduced without the prior written permission of a Standards Department of the Volkswagen Group. Parties to a contract can only obtain this standard via the responsible procurement department.Check standard for current issue prior to usage.Klass.-Nr./Class. No. 04 81 7July 2004Page 2 VW 011 06-1: 2004-07 1 ScopeThis standard applies to the design, layout and quality assurance of arc-welded sheet steel joints which are predominantly subject to dynamic loads. It comprises the following procedures according to DIN EN ISO 4063: Reference no. 131 135 141 for: of: Method Metal inert-gas welding Metal active-gas welding Tungsten inert-gas welding Code MIG MAG TIGbutt and fillet welds, lap welds, plug welds and special weld types bright uncoated and coated sheet steel as well as of both high-alloyed steels and premium steels; for examples see Section 4.1; Workpiece thickness 0.5 mm to 6 mm test characteristics of quality level B (high requirement) according to DIN EN ISO 5817, see also DVS specification 0705.with:All fusion-welded joints to which this scope is not applicable require the clarification of the responsible engineering departments. Special measures made necessary because of the component, e.g. change to the quality level for specific imperfections, are permissible and shall be entered in the drawing. 2 2.1 a f1,2 fL fSt Fi h l L s s1,2 sN t1 t2 HAZ Σt ∅ Abbreviations and definitions Abbreviations Calculated throat thickness Penetrations on sheets 1 and 2 Penetration length Penetration at the face surface Joining plane Gap size Throat length Length Throat thickness Throat thickness with respect to sheets 1 and 2 smallest common throat thickness Thickness of sheet 1 Thickness of sheet 2 Heat-affected zone Sum total of sheet thicknesses Diameter mm mm mm mm or % (of face surface) mm mm mm mm mm mm mm mm mm mmPage 3 VW 011 06-1: 2004-072.2DefinitionsFüThe following definitions are valid for the application of this standard: 2.2.1 Weld jointJoint created by fusion welding. It comprises the weld, fusion line, heat-affected zone and unaffected base material (Figure 1).1 2Legend: 1 = weld 2 = heat-affected zone 3 = fusion line, fusion zone344 = unaffected base material Figure 1 – Fusion weld jointNOTE Weld and fusion line may be identical. 2.2.1.1 Weld The area where the workpiece(s) is/are joined at the weld joint. The weld comprises the base material and/or the filler metal. 2.2.1.2 Fusion line Borderline between the base metal and/or filler material melted during welding and the metal that remains solid. 2.2.1.3 Weld metal Material that solidified after welding, comprising either the base material or filler metal and base material. Some elements in the weld metal can come from casings and/or accessory materials (DIN ISO 857-1). 2.2.1.4 Heat-affected zone HAZ Area of the base material that remained solid, but, due to the energy applied during welding, experienced microstructural changes related to temperature.Page 4 VW 011 06-1: 2004-072.2.1.5 Unaffected base material Area of the base material that experienced no evident microstructural changes as a result of the energy applied during welding. 2.2.2 Same types of materialMaterials which do not differ significantly in terms of their chemical composition and their suitability for welding (DIN 8528-1). 2.2.3 Different types of materialMaterials which differ significantly in terms of their chemical composition and their suitability for welding. 3 Gas-shielded arc welding procedureGas-shielded arc welding is a form of fusion welding. An electrical arc is used as the heat source. It burns between the electrode and the workpiece. In this process, the arc and the weld pool are protected from the atmosphere by a shield of protective gas. The classification into the following procedures depends on the electrode type: 3.1 Tungsten inert-gas welding (TIG)In this procedure, an arc is ignited between a non-consumable tungsten electrode and the workpiece. Argon, helium, mixtures of both and sometimes added active gases, are used to form the protective atmosphere. The filler metal is (as in the case of gas welding) fed from the side. 3.2 Gas-shielded metal arc welding (MIG/MAG)In this procedure, an arc is ignited between the melting end of the wire electrode (filler metal) and the workpiece. The welding current flows via sliding contacts in the electric current guide of the gun to the wire electrode. When inert gases (low-activity gases, e.g. noble gases such as argon, helium or mixtures of both) are used as protective atmosphere, this is called metal inert-gas welding (MIG). When active gases are used (e.g. CO2, or mixtures containing CO2, or, in some cases, mixtures of CO2 and oxygen), this is called metal active-gas welding (MAG). This procedure is used to weld unalloyed and low-alloy steels.Page 5 VW 011 06-1: 2004-074General requirementsWelds that are subject to mandatory documentation shall be evaluated according to the relevant type-specific and/or component-specific test specifications (PV). Deviations with respect to the specified weld geometries and weld layouts shall be detailed in the drawing and verified by testing. They shall be described in test specifications (PV). Further requirements with respect to gas-shielded arc welding are contained in the following documents: VW 011 06-2 VW 011 06-3 VW 011 42 Shielded Arc Welding - Rework on Sheet Metal Connections Gas-Shielded Arc Welding – Part 3: Al Welded Joints Welded Seam Repairs on Aluminum Structures – Product Evaluation and Notes on ProcedureWhen creating arc-welded sheet steel joints, the greatest possible design strength in accordance with the design goal must be realized while also ensuring sufficient reliability and a favorable cost/quality ratio. For this purpose, every weld joint must be suitable for welding, i.e. the dimensions of the welding equipment and the accessibility of the weld according to DVS 0929 must be taken into consideration for design. Weldability for service of a sheet steel joint is given if the component, on the basis of its design (Section 4.2) and with the material used (Section 4.1), remains functional (Section 4.3) under the intended operating stresses (Figure 2).Material Welding suitabilityWeldability of the partWelding capability ManufacturingWeldability for service DesignFigure 2 – Representation of weldability according to DIN 8528-1 4.1 MaterialsThe following list is not complete. The following products and materials have good welding properties: a) Cold-rolled flat products made from soft steels for cold forming: DIN 1623-1 (02.83)1) DIN EN 10130 Material no. St 12 DC01 1.0330 St 13 DC03 1.0347 St 14 DC04 1.0338 1) DIN 1623-1 was replaced in October 1991 by DIN EN 10130.Page 6 VW 011 06-1: 2004-07b) c) d)Cold-rolled strips DC01 to DC04 with the surface finishes BK, RP, RPG according to DIN EN 10139. Hot-rolled strips with ≤ 0.20% C content, e.g. according to TL 1111. Hot-rolled products of structural carbon steels DIN 17100 (01.80)2) DIN EN 10025 Material no. St 37-2 -1.0037 St 37-2 R St37-2 S 235 JR 1.0114 St 37-3 S 235 JO 1.0116 St 52-3 S 355 J2G3 1.0570 Conditionally weldable: St 50-2 E295 1.0050 2) DIN 17100 was replaced in March 1994 by DIN EN 10025.The following products and materials are also weldable:e) f)g)Cold-rolled strip and sheet with higher yield point for cold working made from micro-alloyed steels (SEW 093 of March 1987) Isotropic micro-alloyed cold-rolled strip (according to VW 500 17) is a further development of the traditional micro-alloyed cold-rolled strip ZStE260 to ZStE420 (formerly SEW 093). NOTE VW 500 17 defines the material requirements of isotropic micro-alloyed steels, placing particular emphasis on the mechanical properties. Cold-rolled flat products with high yield point for cold working made from micro-alloyed steels: DIN EN 10268 Material no. H240LA 1.0480 H280LA 1.0489 H320LA 1.0548 H360LA 1.0550 H400LA 1.0556 DIN EN 10292 Material No. H260LAD+Z, +ZF 1.0929 H300LAD+Z, +ZF 1.0932 H340LAD+Z, +ZF 1.0933 H380LAD+Z, +ZF 1.0934 H420LAD+Z, +ZF 1.0935 Hot-rolled flat products made from steels with a high yield point for cold working: DIN EN 10149-2 Material no. S315MC 1.0972 S355MC 1.0976 S420MC 1.0980 S460MC 1.0982 S500MC 1.0984 S550MC 1.0986 S600MC 1.8969 S650MC 1.8976 S700MC 1.8974h)Page 7 VW 011 06-1: 2004-07i)Cold-rolled strip and sheet with higher yield point for cold working made from phosphorus-alloy steels SEW 094 Material no. ZStE220P 1.0397 ZStE260P 1.0417 ZStE300P 1.0448 DIN EN 10 292 Material no. H220PD+Z, +ZF 1.0358 H260PD+Z, +ZF 1.0431 H300PD+Z, +ZF 1.0443 Strip and sheet from stainless steels (DIN EN 10088-2): e.g. austenitic steels X5CrNi18-10 1.4301 or ferritic steels X2CrTi12 1.4512j)Page 8 VW 011 06-1: 2004-074.2DesignFüThe following specifications and the notes on design from the DVS 0929 Specification are used as the basis for the production-friendly design of arc-welded sheet-steel joints. 4.2.1 Joint typesThe weld joint is the area in which the parts are joined by welding. The respective type of joint is determined by the arrangement of the parts with respect to each other (extension, reinforcement, branching), see Table 1. Table 1 – Joint types (DIN EN 12345) Position of parts Description The parts lie in the same plane and touch against each other end to end The parts lie on top of one another in parallel, e.g. in explosive cladding The parts lie in parallel on top of one another and overlap. The parts meet at right angles (Tshaped) and lie on top of one another Two parts lying in the same plane meet on a third part that lies between them at right angles (forming a double T shape) One part meets the other at an angle. The edges of two parts meet at an angle of more than 30° (corner)No. 1 2 3Type of joint Butt joint Edge joint Lap joint4T-joint5Double T-joint6Bevel joint7Corner joint8Front jointThe edges of two parts meet at an angle of 0° to 30°9Multiple jointThree or more parts meet at any angle Two parts, e.g. wires, lie on top of one another in a cross shape10Cross jointPage 9 VW 011 06-1: 2004-074.2.2Weld typesThe weld type is determined by the following: Type of weld joint Type and scope of preparation, e.g. gap optimization (see DIN EN ISO 5817 and DIN EN ISO 9692-1) Material Welding method. 4.2.2.1 Fillet weld The parts lie in two planes with respect to one another, form a fillet joint and are joined by welding. It is possible to differentiate between a fillet weld (Figures 3 and 5) and a double fillet weld (Figure 4) with and without edge preparationFigure 3 - Fillet weld on T-jointFigure 4 – Double fillet weld on T-jointFigure 5 - Fillet weld on bevel joint without edge preparation4.2.2.2 Square butt weld on butt joint, flanged weld The parts lie in one plane, form a gap and are joined by welding, see Figures 6 and 7.Figure 6 - Square butt weld 4.2.2.3 Lap weldFigure 7 – Flanged weldThe parts lie in parallel on top of one another. The face surface of the top sheet and the bottom sheet form a fillet. Both parts are joined by welding. This is termed lap weld (see Figure 8). Variant 1 Variant 2Figure 8 – Lap weldPage 10 VW 011 06-1: 2004-074.2.2.4 Front weld See Figure 9.Figure 9 – Front weld 4.2.2.5 Plug weld See Figure 10.Figure 10 – Plug weld 4.3 4.3.1 Weld dimensions Throat thicknessThe calculated throat thickness a is required for the calculation of the forces acting on a weld joint. For example, the following applies to the design of a fillet weld: a ≤ 0.7 tmin. In production, the actually measured throat thickness s must always be greater than or the same as the calculated throat thickness a. If the throat thickness s (Figure 11) cannot be determined directly, the smallest common throat thickness sN (Figure 12) can be used for an alternative criterion. The smallest common throat thickness sN is the shortest distance between the contact surfaces of component edge and weld metal and the surface of the weld (see also Figures 13 and 14).sN saaFigure 11 - Fillet weldFigure 12 - Fillet weld with deep penetrationPage 11 VW 011 06-1: 2004-07sNsNFigure 13 – Concave weldFigure 14 – Convex weldThe shortest (common) distance between both components of the weld joint shall be measured in order to determine the shortest common throat thickness sN. Excess weld metal must not be considered for convex welds (see Figure 14). 4.3.2 Weld lengthThe calculated weld length l is the weld length defined for the specific design by the designer. Both the starting and end areas (end crater) are used to determine the weld length. In order to improve the dynamic load capacity, the weld length can exceed the component length (Figure 15).l1 = Calculated weld length e.g. component length l2 = Weld seam length Figure 15 – Magnified weld length Proof of sufficient strength is provided by the component-specific strength tests.Page 12 VW 011 06-1: 2004-075Requirements for welds and quality assurance of weldsIn general, the welding quality requirements according to DIN EN 729-1 shall be taken into consideration together with the comprehensive quality requirements set out in DIN EN 729-2. The design of a weld shall be described clearly by indicating the weld’s length, thickness and quality. These requirements are part of the drawing specifications (also see Section 6). Unless other specifications are noted in the drawing, the requirements of Sections 5.1 to 5.5 shall apply. 5.1 Weld qualityIf there is no component-specific test specification, quality level B, high, specified in DIN EN ISO 5817, shall apply. The imperfections specified there are represented for square butt welds and fillet welds on a T-joint. The limit values for imperfections apply to other weld types, too (e.g., flanged weld, fillet weld on lap joint). Unequal weld leg lengths as an imperfection according to DIN EN ISO 5817 must not be evaluated for the fillet weld in joints of sheet metal in the body-in-white and in exhaust systems. 5.2 Penetration depthsThe weld joint is sufficient once a continuous crystalline joint with a measurable penetration depth of f ≥ 0.2 mm is created between the sheets involved. For certain weld types – e.g. fillet weld on lap joint or flanged weld – the penetrations f cannot always be determined if 100% of the face surfaces is included in the weld. Permissible penetration depths f < 0.2 mm shall be indicated in the drawing or specified in a component-specific test specification. The weld quality and/or strength must be verified by means of a dynamic strength test and a microscopic examination. NOTE: Due to the smaller “welding window” the test intervals for f < 0.2 mm (e.g. using microsections) shall be conducted at shorter time intervals or on smaller batch sizes. The processes shall be coordinated with all the departments involved (Design, Quality Assurance, Production).Page 13 VW 011 06-1: 2004-075.3 5.3.1Weld types Square butt weld on butt jointt1sFigure 16 - Square butt weld on butt joint s = throat thickness fSt = penetration The face surfaces (fSt ) shall be 100% melted. Design as flanged weld: s ≥ tmin. (see Figure 16) fSt ≥ 100 %SNt1Figure 17 – Flanged weld sN = smallest common throat thickness The face surfaces (fSt ) shall be 100% melted. sN ≥ tmin. (see Figure 17)t2t2Page 14 VW 011 06-1: 2004-075.3.2Front weldSNf1 SN fL2sNf2t1t2 t1a) b) Figure 18 – Front weld sN fL2. f1,2 tmin. t1 0.2 mmt2t1c)t2sN = smallest common throat thickness fL2 = penetration length f1,2 = penetration 5.3.3 Fillet weld on lap joints1 sN N af2t1hs2Figure 19 - Lap weld s1,2 sN a f2 h = throat thickness = smallest common throat thickness = calculated throat thickness = side wall penetration on the component t2: = gap size s1,2 0.7 tmin. sN f2 s1,2 and sN 0.7 tmin. a ≤ 0.7 tmin. (design recommendation) 0.2mm (see Figure 19)NOTE: If the throat thicknesses s1,2 cannot be determined directly, the smallest common throat thickness sN may be chosen as an alternative criterion.t2Page 15 VW 011 06-1: 2004-075.3.4Fillet weld with deep penetrationt1 f1 s1 sNt2aTheoretical root pointFigure 20 - Fillet weld with deep penetration s1,2 sN a f1,2 = throat thickness (with deep penetration) = smallest common throat thickness = calculated throat thickness = side wall penetration on component t1,2 s1,2 0.7 tmin. sN s1,2 and sN 0,7 tmin. a ≤ 0.7 tmin. f1,2 0.2 mm (see Figure 20)NOTE: If the throat thicknesses s1,2 cannot be determined on the microsection directly, the smallest common throat thickness sN may be chosen as an alternative criterion. 5.3.5 Fillet weld on bevel jointt1sN≤ 30°Figure 21 - Fillet weld on bevel joint sN = throat thickness f2 = penetration sN f2 tmin. 0.2 mm (see Figure 21)The face surface of the upper sheet must be 100 % melted.f2t2f2 s2Page 16 VW 011 06-1: 2004-075.3.6Multiple jointf1f2lt1t3Figure 22 – Three-sheet-T-joint f1,2,3 = penetration fSt1,2 = face surface penetration of t1,2 fSt3 = face surface penetration of t3 5.3.7 Corner joint f1,2,3 > 0.2 mm fSt1,2 ≥ insertion depth l fSt3 = 100% meltedsNt1t2Figure 23 – Corner joint The face surfaces of both sheets must be 100 % melted. Smallest common throat thickness sN ≥ tmin.t2Page 17 VW 011 06-1: 2004-075.3.8Plug weldFor plug weld see Figure 24. The values in Table 2 serve as reference values for the ratio of the sheet thickness to the hole diameter. Table 2 – Hole diameter and sheet thickness Sheet thickness used t (mm) up to 1.0 > 1.00 to 1.25 > 1.25 to 1.50 > 1.50 to 2.00 > 2.0 to 3.00 > 3.00 to 3.50 Hole diameter ∅ or L (mm) ≥6 ≥7 ≥8 ≥9 ≥ 10 ≥ 14 Optionally, long holes for narrow flanges W x L (mm) 6 x 10 6 x 12 8 x 12 -When there are gaps between the sheets, the length of the penetration fL must be equivalent to the length L or to the diameter of the hole, or exceed it. ∅ or L x Bt1 t2 fLf2fSt1,2 = face surface penetration of t1,2 fL = penetration length, width and/or diameter f2 = penetration depthfSt1,2 = 100 % melted fL ≥ ∅ or L or W f2 ≥ 0.2 mm Figure 24 – Plug weldThe face surfaces of the hole must be 100 % melted.Page 18 VW 011 06-1: 2004-075.4Special weld typesAdequate evaluation criteria shall be used to evaluate any special weld types that are not listed here. 5.4.1 Fillet weld on multiple lap jointS1t1 t2 t3 f3S2Figure 25 - Three-sheet lap weld The cross-sections of the upper sheets t1 and t2 must be 100 % melted and the throat thickness a of t1 and t2 must be met. If no specifications are made in the drawing, the following applies as reference value: a = 0.7 tmin2,3 The penetration depth f3 in sheet t3 shall be minimum 0.2 mm.Page 19 VW 011 06-1: 2004-075.4.2Multiple front weld sN2 sN1 sN3 F1 F2 Fi = joining plane i F3 *1) If it is clear that one sheet arrangement in a multiple-sheet arrangement is to be considered as a single sheet, then this sheet shall not be included in the overall evaluation when determining the throat thickness sN. t1 t2 t3 t4*1)Figure 26 – Four-sheet front weld In the case of multiple-sheet joints, the smallest common throat thickness sN of the relevant joining planes is used to determine the throat thickness s, as is the case for a multiple lap joint. Here the following applies: In the relevant joining plane (in Figure 26 - four-fold front weld with the joining planes F1, F2 and F3) the throat thickness sN must be ≥ Σ of the sheet thicknesses on the right and = Σ of the sheet thicknesses on the left of the joining plane. The following applies to Figure 26 as an example: sN1 ≥ t 1 sN2 ≥ ? t(3+4) sN3 ≥ ? t4 fSt = face surfaces t1 t4 < (t2 + t3 + t4 ) < (t1 + t2 + t3 ) t3 + t4 < (t1 + t2 ) fSt 1,2,3,4 = 100% meltedPage 20 VW 011 06-1: 2004-07sN4sN3sN 2 s N1t1 t t34t2Figure 27 – Multiple front weld For multiple front welds in exhaust systems (e.g., sheet layers on the exhaust pipe, Figure 27) the factor 0.7 applies in the determination of the smallest common throat thickness sN: sN1 ≥ 0.7 t1 sN2 ≥ 0.7 (t1 + t2) sN3 ≥ 0.7 (t1 + t2 + t3) sN4 ≥ 0.7 tpipe or or sN2 ≥ 0.7 (t3 + t4) sN3 ≥ 0.7 t4Page 21 VW 011 06-1: 2004-075.4.3Fillet welds on components with round cross sectionsf1 sNtaFigure 28 - Fillet weldt f1 = = t2 f2Figure 29 - Fillet weld with deep penetrationsFigure 30 – Concave fillet weld For Figures 28 and 30 determine the throat thickness s approximately: On workpieces with different geometrical shapes, the shortest distance of the median line between the two workpieces shall be selected as the dimension s. s = throat thickness s ≥ 0.7 tminFor fillet welds on components with a round cross section it is recommended to determine the smallest common throat thickness sN as shown in Figure 29. sN = smallest common throat thickness sN ≥ a. NOTE: In the event of imperfections, e.g. undercuts, DIN EN ISO 5817 shall apply.f2Page 22 VW 011 06-1: 2004-075.4.4Square butt weld on flanged jointf1 f2 t1 sN t2Figure 31 - Fillet weld on specially shaped workpieces sN = smallest common throat thickness f1,2 = penetration depth sN ≥ tmin. (see Figure 31) f1,2 ≥ 0.2 mmPage 23 VW 011 06-1: 2004-075.5 5.5.1Evaluation of imperfections Weld spatterWeld spatter must be avoided as far as possible. Any globules or welding residues that remain stuck to the parts and which could lead to an impairment of function are not permitted. Spatter-free areas shall be defined in the drawing or in a test specification. 5.5.2 General imperfectionsImperfections such as cracks, pores, lack of fusion, gap sizes shall be evaluated, unless otherwise indicated in the drawing, according to DIN EN ISO 5817, quality level B “high”. Unequal weld leg lengths shall not be evaluated for fillet welds on lap joint. For exhaust systems the gap size must not exceed 1.0 mm. 6 Drawing entriesThe graphical representation (for example see Figure 32), dimensioning and symbols for the welding procedures named in Section 1 shall be carried out according to DIN EN 22553.s8a6n x l (e)131/ VW01106-1/h Legend: s8 = actual throat penetration) 8 mm thickness (with deepva6 = design throat thickness (without deep penetration) 6 mm n = number of welds l = minimum weld length; tolerance +5 mm, unless otherwise indicated e = distance between the welds v = initial dimensionExplanation: Weld produced by means of metal inert-gas welding (code number 131 according to DIN EN ISO 4063); evaluation according to VW 011 06-1; horizontal position h according to DIN EN ISO 6947. Figure 32 - Example of application for interrupted fillet weld with initial dimension; symbolic representationPage 24 VW 011 06-1: 2004-077Referenced standards1 Steel Flat Products; Cold Rolled Sheet and Strip; Technical Delivery Conditions; Mild Unalloyed Steels for Cold Forming Weldability; Metallic Materials, Definitions Steels for General Structural Purposes; Quality Standard Quality Requirements for Welding - Fusion Welding of Metallic Materials – Part 1: Guidelines for Selection and Use Quality Requirements for Welding - Fusion Welding of Metallic Materials – Part 2: Comprehensive Quality Requirements Hot Rolled Products of Non-Alloy Structural Steels; Technical Delivery Conditions Stainless Steels - Part 2: Technical Delivery Conditions for Sheet/Plate and Strip of Corrosion-Resisting Steels for General and Construction Purposes Cold Rolled Low Carbon Steel Flat Products for Cold Forming – Technical Delivery Conditions Cold Rolled Uncoated Mild Steel Narrow Steel Strip for Cold Forming Technical Delivery Conditions Hot Rolled Flat Products Made of High Yield Strength Steels for Cold Forming – Part 1: General Delivery Conditions Hot Rolled Flat Products Made of High Yield Strength Steels for Cold Forming – Part 2: Delivery Conditions for Thermomechanically Rolled Steels Cold-Rolled Flat Products Made of High Yield Strength Micro-Alloyed Steels for Cold Forming - General Delivery Conditions Continuously Hot-Dip Coated Strip and Sheet of Steels with Higher Yield Strength for Cold Forming – Technical Delivery Conditions Welding - Multilingual Terms for Welded Joints with Illustrations Welded, Brazed and Soldered Joints - Symbolic Representation on Drawings Welding – Fusion-Welded Joints in Steel, Nickel, Titanium and Their Alloys (Beam Welding Excluded) – Quality Levels for Imperfections Welding and Allied Processes - Nomenclature of Processes and Reference Numbers Welds - Working Positions - Definitions of Angles of Slope and Rotation Welding and Allied Processes – Recommendations for Joint Preparation Part 1: Manual Metal-Arc Welding, Gas-shielded Metal-Arc Welding, Gas Welding, TIG Welding and Beam Welding of Steels Welding and Allied Processes – Vocabulary - Part 1: Metal Welding Processes Recommendations for Selection of Acceptance Levels according to DIN EN 25 817; Butt Welds and Fillet Welds on Steel Notes on Design for MIG/MAG Welding using Industrial Robots Cold-Rolled Strip and Sheet of Micro-Alloyed Steels with Higher Yield Point for Cold Forming – Technical Supply SpecificationsThe last publication date of withdrawn standards is provided in parentheses. DIN 1623-1 (02.83) DIN 8528-1 DIN 17100 (01.80) DIN EN 729-1 DIN EN 729-2 DIN EN 10025 DIN EN 10088-2 DIN EN 10130 DIN EN 10139 DIN EN 10149-1 DIN EN 10149-2 DIN EN 10268 DIN EN 10292 DIN EN 12345 DIN EN 22553 DIN EN ISO 5817 DIN EN ISO 4063 DIN EN ISO 6947 DIN EN ISO 9692-1 DIN ISO 857-1 DVS 0705 DVS 0929 SEW 093 (03.87)1In this section terminological inconsistencies may occur as the original titles are used.。
大众汽车标准_VW_10540-3

汽车零件
制造厂代码 用于国外工厂及其承制厂
1999 年6月 VW
105 40-3
01 15 5 共 3 页第1页
资料
同1983年10月版比较,作了如下修改:
─ 删除了菲律宾,葡萄牙,萨拉热窝 TAS (培斯),泰国,印度尼西亚, 乌拉圭,委内瑞拉
─ 增补了长春FAW(奥迪),台湾,Skoda(斯科达)公司,Seat(西雅特)公司, 上海大众
自己生产 供应商
卡门荷大众
自己生产
供应商 4
长春FAW(奥迪)
长春FAW(大众)
5 上海大众(SVW) 自己生产 供应商
布鲁克西尔大众 自己生产
供应商
6 台湾
自己生产
供应商
空位
代码 2BR
3ME
2VZ
5FA 5FV 5SV
6BE
6CC
范围1) 1AA ~ 2ZZ2) 3AA ~ 3ZZ 4AA ~ 4DZ 4JA ~ 4ZZ
audiag资料资料资料资料抄抄抄抄写写写写李李李李莉日日日日期010907期期期4821696576制造厂代码制造厂代码制造厂代码制造厂代码共共共共3页页页页第第第第1页页页页日期日期日期日期日日日日期020401期期期译译译译校校校校日日日日期270401期期期011551054032br3me1999年年年年6月月月月vw莉莉莉代码代码代码代码2vz国外工厂国外工厂国外工厂国外工厂43125fv5sv6be5技技技技校校校校66cc6ca6zz6ma6pz1aa2zz23aa3zz4aa4dz5aa5zz6aa6bz4ja4zz5fa1925761151384代码数代码数代码数代码数汽车零件汽车零件汽车零件汽车零件用于国外工厂及其承制厂用于国外工厂及其承制厂用于国外工厂及其承制厂用于国外工厂及其承制厂南非大众南非大众南非大众南非大众自己生产自己生产自己生产自己生产7上海大众上海大众上海大众上海大众svw自己生产自己生产自己生产自己生产供应商供应商供应商供应商1i和2剔除剔除剔除剔除2zv3剔除剔除剔除剔除va8和4剔除剔除剔除剔除za2和5剔除剔除剔除剔除zabzaezalzaozbrzdozfozfpzfszguzjjzpczstzwwzwnzzw和和和q两个字母不用因为这两个字母有混淆的危险两个字母不用因为这两个字母有混淆的危险两个字母不用因为这两个字母有混淆的危险两个字母不用因为这两个字母有混淆的危险和和和va9和和和zb2空位空位空位空位自己生产自己生产自己生产自己生产供应商供应商供应商供应商空位空位空位空位自己生产自己生产自己生产自己生产供应商供应商供应商供应商自己生产自己生产自己生产自己生产供应商供应商供应商供应商空位空位空位空位自己生产自己生产自己生产自己生产供应商供应商供应商供应商b至至至至西雅图西雅图西雅图西雅图h自己生产自己生产自己生产自己生产共共共共3页页页页第第第第2页页页页105403vw范围范围范围范围18aa国外工厂国外工厂国外工厂国外工厂尼日利亚大众尼日利亚大众尼日利亚大众尼日利亚大众秘鲁秘鲁秘鲁秘鲁8nz8va8zz代码代码代码代码98制造厂代码制造厂代码制造厂代码制造厂代码6za312供应商供应商供应商供应商4806ra6zz7aa7lz7ma7zz5sv312488oa8ra8pz8uz961204321449aa9ua9tz9zz8ha9arsetba7ca7da7e
大众标准目录(中文)

录2 附
2006.12
5
VW 010 59-6
录3 附
EN
2007.07
5 5 6 7 8 9 10 11 12 13 13 14
VW 010 59-6
录4 附 VW 010 59-2 VW 010 66 VW 010 88 VW 010 98 VW 011 10 VW 011 27 VW 011 54 VW 011 55 VW 101 26-1 VW 101 26-2 VW 105 00
2000.06 2000.06 2002.12 2005.11 2005.11 2005.11 2005.11 2002.1 2002.12 2003.12
1974.11 1975.06 1975.06
1976.02 2005.05 1985.08 2005.09 1991.11 1995.02 2004.08 1991.11
CN/EN/DE 2004.07 EN EN/DE EN/DE EN CN/EN DE DE EN/DE 2006.01
2004.07 2007.04 2001.1 1977.12 2007.08 2006.01
2004.07