危废焚烧处理工艺及图片
工业固废物的焚烧处理课件
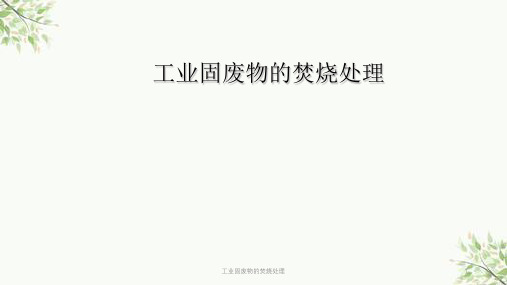
工业固废物的焚烧处理
9
回转式焚烧炉
工业固废物的焚烧处理
10
• 工作原理:
回转式焚烧炉是用 冷却水管或耐火材料沿 炉体排列,炉体水平放 置并略为倾斜。通过炉 身的不停运转,使炉体 内的垃圾充分燃烧,同 时向炉体倾斜的方向移 动,直至燃尽并排出炉 体。
• 特点:设备利用率高, 灰渣中含碳量低,过剩 空气量低,有害气体排 放量低。但燃烧不易控 制,垃圾热值低时燃烧 困难。
工业固废物的焚烧处理
7
• 2.流化床式焚烧炉系统,其特点是垃圾的悬浮燃烧,空气与垃圾 充分接触,燃烧效果好。但是流化床燃烧需要颗粒大小较均匀的 燃料,对垃圾的预处理要求严格。
工业固废物的焚烧处理
8
3.回转窑式焚烧炉系统,其特点是将垃圾投入连续、缓慢转动的筒 体内焚烧直到燃烬,故能够实现垃圾与空气的良好接触和均匀充 分的燃烧。西方国家多将该类焚烧炉用于有毒、有害工业垃圾的 处理。
火这一段,都认为是干燥阶段。 (2)焚烧阶段
焚烧过程的主阶段,即真正的燃烧过程。 (3)燃尽阶段
生成固体残渣的阶段。 三个阶段并非界限分明,尤其是对混合垃圾之类的焚烧过程更是如此。
工业固废物的焚烧处理
6
焚烧系统
1.垃圾层燃焚烧炉(机械炉排炉)系统,如采用滚 动炉排、水平往复推饲炉排和倾斜往复炉排(包括顺 推和逆推倾斜往复炉排)等。主要特点是垃圾无需严 格的预处理。
工业固废物的焚烧处理
11
工业固废物的焚烧处理
工业固废物的焚烧处理
1
一般工业废物(如高炉渣、
钢渣、赤泥、有色金属渣、
工
粉煤灰、煤渣、硫酸渣、废
业 固
石膏、盐泥等)
废
物
工业有害固体废物:有毒的、
危废焚烧烟气处理ppt课件

10
烟气上升过程中,颗粒一部分随烟气被带出脱硫塔,一 部分因自重回流到循环流化床内,进一步增加了流化床 的床层颗粒浓度和延长吸收剂的反应时间,小的颗粒经 旋风除尘器收集后部分返回到循环流化床脱酸塔中,塔 内烟气流速5m/s,使消石灰的循环倍率可达30~120倍, 停留时间可达30min左右,提高了消石灰的利用率。主 要化学反应如下:
9
1.4湿法脱酸系统工艺原理
采用NaOH溶液作为脱酸剂进行塔内脱酸,由于其碱性强, 吸收二氧化硫后反应产物溶解度大,不会造成过饱和结晶, 避免了结垢堵塞问题。主要化学反应如下:
2NaOH + SO2= Na2SO3+ H2O Na2SO3+ SO2+ H2O=2NaHSO3 Na2CO3+ SO2= Na2SO3+CO2 2Na2SO3+ O2=2Na2SO4 NaOH+HCl=NaCl+ H2O NaOH+HF=NaF+ H2O 影响湿法脱酸效率的主要因素是液气比,液气比决定了吸
表1-1 本项目危险废物焚烧炉大气污染物排放限值
序号 污染物
最高允许排放浓度限值(mg/m3)
1
烟气黑度
2
烟尘
3
一氧化碳(CO)
4
二氧化硫(SO2)
5
氟化氢(HF)
6
氯化氢(H林曼 I 级 10 50 50 1 10 500
危废焚烧处理工艺及图片

危废焚烧处理工艺及图片公司内部编号:(GOOD-TMMT-MMUT-UUPTY-UUYY-DTTI-资料整理一、危废处理工艺流程系统工艺主流程框图体积较大的废物经过破碎后与不需破碎的废物由抓斗混合后送至废物给料斗,经计量后从料斗经溜槽由推料机构送入回转窑内。
液态危险废物根据热值的不同并经过过滤后分别喷入回转窑和二燃室内焚烧。
固态废物和液态废物根据化验分析的成分和分析由技术部门制定配料单,进料量根据回转窑内温度等工况条件由控制室内的计算机进行调节和控制。
整个焚烧系统配备了自动控制和监测系统,在线显示运行工况和尾气排放监测,并能自动反馈,对有关的主要工艺参数进行自动调节。
焚烧系统还设有可靠的配风装置以保证回转窑、二燃室处于负压运行状态。
危险废物在回转窑内进行高温分解及燃烧反应,废物大幅减量,部分未燃尽的残渣从回转窑排出后直接掉落在二燃室下部的炉排上再次燃烧,燃尽后由出渣系统连续排出,回转窑焚烧产生的烟气进入二燃室内进一步燃烧,二燃室的出口烟气温度保证维持在1100℃以上,烟气停留时间超过2秒,使烟气中的有机物和二恶英彻底分解,达到无害化的目的。
二燃室产生的高温烟气进入余热锅炉回收部分能量产生蒸汽。
烟气经余热锅炉后温度降为500℃-600℃之间。
再经过烟气急冷中和塔将温度降低到200℃-180℃之间,避免二恶英等有毒气体的再合成。
经急冷后的烟气进入干式反应装置,在干式反应装置中喷入活性炭及Ca(OH)2对烟气进一步脱酸,并对重金属及可能再生产的二恶英等物质进行吸附,再进入布袋除尘器进行除尘。
然后烟气进入SCR脱氮装置脱除氮氧化物。
烟气净化的最后一道工序是湿式脱酸,在湿式脱酸塔中喷入碱液脱除SO2、HCl、HF等酸性气体,达到严格的烟气排放标准。
最后经过净化的烟气被加热以消去白烟后通过引风机的作用送入烟囱排入大气中。
(2)危险废物储存与预处理系统固体危险废物的预处理工艺流程及特点:固体按照化验室的分析,根据性状和成分不同,被分别送往废物储存区的各个贮池储存,即固体废物破碎池、高热值固体废物贮池、低热值固体废物贮池内。
包头危废处置中心危险废物处理技术PPT课件
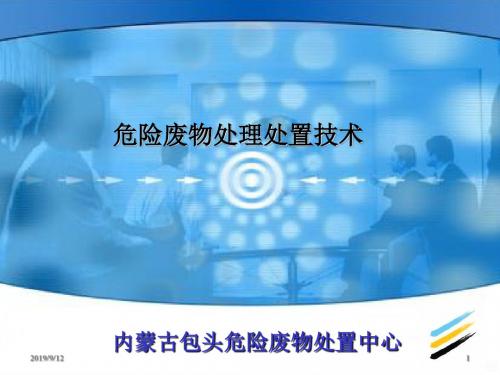
应急旁路 布袋除尘器
烟气
除雾 经 过 再
喷淋 热 器
填料
洗涤塔
烟囱
播放完毕
28
急冷塔
急冷1秒的降温保证措施:
选用美国喷雾公司双流体雾化喷头 雾化粒径在70~20μ M,1秒内完成 液体的汽化
急冷塔防腐 采用耐高温、耐腐蚀、耐烟气冲刷 的耐酸胶泥,高温烟道采用耐腐蚀的 耐火材料 防止湿壁和积水
2019/9/12
4
• 2.1、焚烧处理工艺
• 1、焚烧处理废物种类:医疗废物、可燃性 工业废物(固态、半固态、液态)。
2019/9/12
5
2.废物预处理
• 废物配伍原则:废物入炉前,依其成分、热值等参 数进行搭配,搭配的过程要注意废物之间的相容 性,避免不相容的废物混和后发生反应。
• 不能直接入炉焚烧的大尺寸废物,破碎后配伍入 炉焚烧。
理配伍。 5)回转窑采用独特的供风方式,使物料混合均匀,燃烧充分。 6)防窑体尾端结焦措施:减少回转窑长度、增加回转窑直径,
在窑尾罩设辅助熔渣喷枪。 7)考虑到设备要具有一定的超负荷运行能力,回转窑设计
φ 2.8×9m。 8)回转窑外表温度控制在180 ℃左右,即避免了酸性气体的
低温腐蚀。 9)回转窑采用美国WEBBCO公司的揉性密封块和密封片组件。
余热锅炉采用耐腐蚀材料,设置在高温区,露点温 度以上,防止结露腐蚀。
蒸发热管采用耐高温、耐腐蚀合金材料316L,该材 料能够抵抗NO2、SO2、HCL的腐蚀。
2019/9/12
25
8 烟气净化及排烟系统
该系统设备包括烟气急冷塔、干法增湿脱酸反应器、 活性炭喷射器、布袋除尘器、洗涤除雾塔、烟气再加热器、 引风机、烟囱、急冷水输送、活性炭粉贮存及输送、洗涤 水循环系统、碱液制备等附属设备。
固废焚烧处理全套PPT
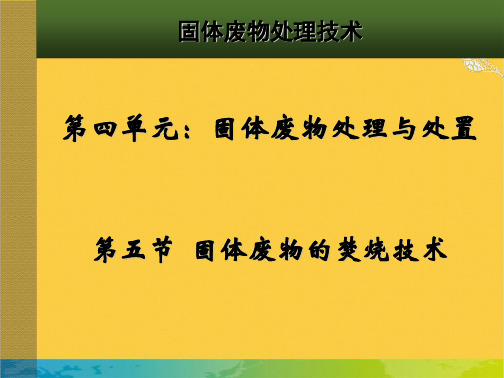
Second
Combustion
Chamber
Second
Combustion
1,000℃
Slush
Waste Liquid
Rotary Kiln 1,100~1,300℃
1,200℃ Slag
A 控制燃烧温度和停
PCDDs:
TCDDs
留时间;
B 减少烟气 200~500℃ 停 留 时
气 停留时间:越长越彻底,通常要在1.
洗涤塔 吸附塔
系 (的R层o3燃燃ta)烧 焚ry回。烧K转i方ln窑式式的焚主烧要炉特系点统是,垃其重圾特无金点需是属严将格垃的圾预投处入理连。续、缓慢转动的筒体内焚烧直到燃烬袋静离,故式电心能除 过分够实尘离滤现垃圾与空静布气电袋的良除除好尘尘接触器器和均匀充分
二、垃圾焚烧技术的特点
利用燃烧过程对垃圾进行高温处理,垃圾中病原体破坏十分 彻底,无害化效果好、减少占地,还可以进行能量回收,如用于 发电。(西山大浦沟垃圾发电厂)
通过焚烧处理,可以基本实现固体废物的“三化” 。 ➢ 大气污染问题,特别是二噁英、重金属污染问题; ➢ 投资运行成本高,管理水平要求高。
除尘在危险温度下运行(150-450 ℃ ) 存在有利于二恶英催化形成的含金属颗粒 垃圾与燃料中含有复杂的有机污染物存在
有足够的氯
二噁英控制的技术途径
烟气冷却塔(急冷塔)
袋式除尘器
洗烟塔
活性炭吸附塔
三、焚烧法处置垃圾的原理:
固体辰废物能否燃烧?取决于热值和可燃性,只要热
值大于3350kJ/Kg,易自燃(不加助燃剂) 通常可将焚烧分为3个阶段: (1)干燥:水分蒸发 (2)热分解:多数为放热反应 (3)燃烧:快速分解及高温氧化
危废焚烧处理工艺与图片
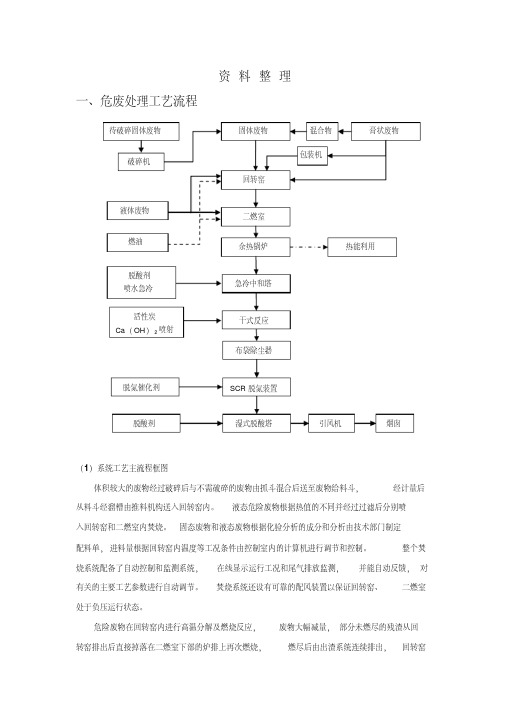
资料整理一、危废处理工艺流程(1)系统工艺主流程框图体积较大的废物经过破碎后与不需破碎的废物由抓斗混合后送至废物给料斗,经计量后从料斗经溜槽由推料机构送入回转窑内。
液态危险废物根据热值的不同并经过过滤后分别喷入回转窑和二燃室内焚烧。
固态废物和液态废物根据化验分析的成分和分析由技术部门制定配料单,进料量根据回转窑内温度等工况条件由控制室内的计算机进行调节和控制。
整个焚烧系统配备了自动控制和监测系统,在线显示运行工况和尾气排放监测,并能自动反馈,对有关的主要工艺参数进行自动调节。
焚烧系统还设有可靠的配风装置以保证回转窑、二燃室处于负压运行状态。
危险废物在回转窑内进行高温分解及燃烧反应,废物大幅减量,部分未燃尽的残渣从回转窑排出后直接掉落在二燃室下部的炉排上再次燃烧,燃尽后由出渣系统连续排出,回转窑固体废物回转窑二燃室余热锅炉急冷中和塔干式反应待破碎固体废物膏状废物液体废物破碎机燃油布袋除尘器SCR 脱氮装置湿式脱酸塔烟囱引风机脱酸剂脱氮催化剂活性炭Ca (OH )2喷射脱酸剂喷水急冷热能利用包装机混合物焚烧产生的烟气进入二燃室内进一步燃烧,二燃室的出口烟气温度保证维持在1100℃以上,烟气停留时间超过2秒,使烟气中的有机物和二恶英彻底分解,达到无害化的目的。
二燃室产生的高温烟气进入余热锅炉回收部分能量产生蒸汽。
烟气经余热锅炉后温度降为500℃-600℃之间。
再经过烟气急冷中和塔将温度降低到200℃-180℃之间,避免二恶英等有毒气体的再合成。
经急冷后的烟气进入干式反应装置,在干式反应装置中喷入活性炭及Ca(OH)2对烟气进一步脱酸,并对重金属及可能再生产的二恶英等物质进行吸附,再进入布袋除尘器进行除尘。
然后烟气进入SCR脱氮装置脱除氮氧化物。
烟气净化的最后一道工序是湿式脱酸,在湿式脱酸塔中喷入碱液脱除SO2、HCl、HF等酸性气体,达到严格的烟气排放标准。
最后经过净化的烟气被加热以消去白烟后通过引风机的作用送入烟囱排入大气中。
危险废物处理工艺流程图及细分工艺流程图详细解释

危险废物处理工艺流程图及细分工艺流程图详细解释一、危废处理工艺流程1、系统工艺主流程框图体积较大的废物经过破碎后与不需破碎的废物由抓斗混合后送至废物给料斗,经计量后从料斗经溜槽由推料机构送入回转窑内。
液态危险废物根据热值的不同并经过过滤后分别喷入回转窑和二燃室内焚烧。
固态废物和液态废物根据化验分析的成分和分析由技术部门制定配料单,进料量根据回转窑内温度等工况条件由控制室内的计算机进行调节和控制。
整个焚烧系统配备了自动控制和监测系统,在线显示运行工况和尾气排放监测,并能自动反馈,对有关的主要工艺参数进行自动调节。
焚烧系统还设有可靠的配风装置以保证回转窑、二燃室处于负压运行状态。
危险废物在回转窑内进行高温分解及燃烧反应,废物大幅减量,部分未燃尽的残渣从回转窑排出后直接掉落在二燃室下部的炉排上再次燃烧,燃尽后由出渣系统连续排出,回转窑焚烧产生的烟气进入二燃室内进一步燃烧,二燃室的出口烟气温度保证维持在1100℃以上,烟气停留时间超过2 秒,使烟气中的有机物和二恶英彻底分解,达到无害化的目的。
二燃室产生的高温烟气进入余热锅炉回收部分能量产生蒸汽。
烟气经余热锅炉后温度降为500℃-600℃之间。
再经过烟气急冷中和塔将温度降低到200℃ -180℃之间,避免二恶英等有毒气体的再合成。
经急冷后的烟气进入干式反应装置,在干式反应装置中喷入活性炭及Ca( OH)2 对烟气进一步脱酸,并对重金属及可能再生产的二恶英等物质进行吸附,再进入布袋除尘器进行除尘。
然后烟气进入SCR脱氮装置脱除氮氧化物。
烟气净化的最后一道工序是湿式脱酸,在湿式脱酸塔中喷入碱液脱除SO2、HCl、HF 等酸性气体,达到严格的烟气排放标准。
最后经过净化的烟气被加热以消去白烟后通过引风机的作用送入烟囱排入大气中。
2、危险废物储存与预处理系统2.1、固体危险废物的预处理工艺流程及特点:固体按照化验室的分析,根据性状和成分不同,被分别送往废物储存区的各个贮池储存,即固体废物破碎池、高热值固体废物贮池、低热值固体废物贮池内。
干货 危险废物处理工艺流程图及细分工艺流程图详解

危险废物处理工艺流程图及细分工艺流程图详解一、危废处理工艺流程(1)系统工艺主流程框图体积较大的废物经过破碎后与不需破碎的废物由抓斗混合后送至废物给料斗,经计量后从料斗经溜槽由推料机构送入回转窑内。
液态危险废物根据热值的不同并经过过滤后分别喷入回转窑和二燃室内焚烧。
固态废物和液态废物根据化验分析的成分和分析由技术部门制定配料单,进料量根据回转窑内温度等工况条件由控制室内的计算机进行调节和控制。
整个焚烧系统配备了自动控制和监测系统,在线显示运行工况和尾气排放监测,并能自动反馈,对有关的主要工艺参数进行自动调节。
焚烧系统还设有可靠的配风装置以保证回转窑、二燃室处于负压运行状态。
危险废物在回转窑内进行高温分解及燃烧反应,废物大幅减量,部分未燃尽的残渣从回转窑排出后直接掉落在二燃室下部的炉排上再次燃烧,燃尽后由出渣系统连续排出,回转窑焚烧产生的烟气进入二燃室内进一步燃烧,二燃室的出口烟气温度保证维持在1100℃以上,烟气停留时间超过2 秒,使烟气中的有机物和二恶英彻底分解,达到无害化的目的。
二燃室产生的高温烟气进入余热锅炉回收部分能量产生蒸汽。
烟气经余热锅炉后温度降为500℃-600℃之间。
再经过烟气急冷中和塔将温度降低到200℃-180℃之间,避免二恶英等有毒气体的再合成。
经急冷后的烟气进入干式反应装置,在干式反应装置中喷入活性炭及Ca(OH)2 对烟气进一步脱酸,并对重金属及可能再生产的二恶英等物质进行吸附,再进入布袋除尘器进行除尘。
然后烟气进入SCR脱氮装置脱除氮氧化物。
烟气净化的最后一道工序是湿式脱酸,在湿式脱酸塔中喷入碱液脱除SO2、HCl、HF 等酸性气体,达到严格的烟气排放标准。
最后经过净化的烟气被加热以消去白烟后通过引风机的作用送入烟囱排入大气中。
(2)危险废物储存与预处理系统。
- 1、下载文档前请自行甄别文档内容的完整性,平台不提供额外的编辑、内容补充、找答案等附加服务。
- 2、"仅部分预览"的文档,不可在线预览部分如存在完整性等问题,可反馈申请退款(可完整预览的文档不适用该条件!)。
- 3、如文档侵犯您的权益,请联系客服反馈,我们会尽快为您处理(人工客服工作时间:9:00-18:30)。
资料整理一、危废处理工艺流程(1)系统工艺主流程框图体积较大的废物经过破碎后与不需破碎的废物由抓斗混合后送至废物给料斗,经计量后从料斗经溜槽由推料机构送入回转窑内。
液态危险废物根据热值的不同并经过过滤后分别喷入回转窑与二燃室内焚烧。
固态废物与液态废物根据化验分析的成分与分析由技术部门制定配料单,进料量根据回转窑内温度等工况条件由控制室内的计算机进行调节与控制。
整个焚烧系统配备了自动控制与监测系统,在线显示运行工况与尾气排放监测,并能自动反馈,对有关的主要工艺参数进行自动调节。
焚烧系统还设有可靠的配风装置以保证回转窑、二燃室处于负压运行状态。
危险废物在回转窑内进行高温分解及燃烧反应,废物大幅减量,部分未燃尽的残渣从回转窑排出后直接掉落在二燃室下部的炉排上再次燃烧,燃尽后由出渣系统连续排出,回转窑焚烧产生的烟气进入二燃室内进一步燃烧,二燃室的出口烟气温度保证维持在1100℃以上,烟气停留时间超过2秒,使烟气中的有机物与二恶英彻底分解,达到无害化的目的。
二燃室产生的高温烟气进入余热锅炉回收部分能量产生蒸汽。
烟气经余热锅炉后温度降为500℃-600℃之间。
再经过烟气急冷中与塔将温度降低到200℃-180℃之间,避免二恶英等有毒气体的再合成。
经急冷后的烟气进入干式反应装置,在干式反应装置中喷入活性炭及Ca(OH)2对烟气进一步脱酸,并对重金属及可能再生产的二恶英等物质进行吸附,再进入布袋除尘器进行除尘。
然后烟气进入SCR脱氮装置脱除氮氧化物。
烟气净化的最后一道工序就是湿式脱酸,在湿式脱酸塔中喷入碱液脱除SO2、HCl、HF等酸性气体,达到严格的烟气排放标准。
最后经过净化的烟气被加热以消去白烟后通过引风机的作用送入烟囱排入大气中。
(2)危险废物储存与预处理系统2、1固体危险废物的预处理工艺流程及特点:固体按照化验室的分析,根据性状与成分不同,被分别送往废物储存区的各个贮池储存,即固体废物破碎池、高热值固体废物贮池、低热值固体废物贮池内。
由于危险废物形状的复杂性,有的外形尺寸较大,或不规则,为了有利于焚烧处理,因此设置固体废物破碎池用于此类固体废物破碎。
固体危险废物预处理工艺的特点:A 、固体废物储存池进料门采用由红外线控制的自动控制密封门系统,在输送车进入储存区时密封门自动打开以便卸料,卸料完成则密封门自动关闭,确保储存池保持全密封的负压状态工作;B 、固体废物储存池采用钢砼混凝土结构,内覆多层防腐蚀材料,储存池的最低点设置渗沥水坑及泵;C 、在储存池内实现固体危险废物的储存、配伍及控制调节的过程2、2液态危险废物的预处理 固体废物破碎池废物储存区固体废物待破碎固体废高热值固体废物贮低热值固体废物贮混合池 破碎机 回转窑进料斗破碎固体废物渗沥液泵再生纸袋(桶)桶装废液与罐车废液通过真空系统与泵送系统输送至废液储罐中贮存。
低热值废液焚烧前需通过配伍混匀,调整热值与酸碱性。
废液的配伍混匀在中与均质槽中进行。
均质槽设置两个,带防爆搅拌器及夹套伴热,低热值废液储罐可通过管道自流至均质槽中。
液体危险废物预处理工艺特点:A、整个液体危险废物储存系统采用全自动的操作系统,有独立的操作室,与总控制室联网,实现总控制室人机界面的集中控制,液体危险废物储存区域的卸料口及专用罐区均设置氮气保护装置,确保整个系统的安全;B、系统设有均质槽以调节废液热值及酸碱度,可根据需要将液体危险废物送入焚烧系统;C、桶装液体危险废物的储存设有专区,按照甲、乙类危险废物分开储存堆放,并就类别的不同区别存放,输送采用真空输送系统,只需将真空输送枪放入桶内,桶内的液体危险废物将立即被吸入真空罐再由泵送往废液储罐。
废液储罐采用热水夹套及保温,并装有搅拌器。
2、3膏状废物的预处理桶装废液与罐车废液通过真空系统与泵送系统输送至废液储罐中贮存。
低热值废液焚烧前需通过配伍混匀,调整热值与酸碱性。
废液的配伍混匀在中与均质槽中进行。
均质槽设置两个,带防爆搅拌器及夹套伴热,低热值废液储罐可通过管道自流至均质槽中。
液体危险废物预处理工艺特点:A、整个液体危险废物储存系统采用全自动的操作系统,有独立的操作室,与总控制室联网,实现总控制室人机界面的集中控制,液体危险废物储存区域的卸料口及专用罐区均设置氮气保护装置,确保整个系统的安全;B、系统设有均质槽以调节废液热值及酸碱度,可根据需要将液体危险废物送入焚烧系统;C、桶装液体危险废物的储存设有专区,按照甲、乙类危险废物分开储存堆放,并就类别的不同区别存放,输送采用真空输送系统,只需将真空输送枪放入桶内,桶内的液体危险废物将立即被吸入真空罐再由泵送往废液储罐。
废液储罐采用热水夹套及保温,并装有搅拌器。
3、危险废物进料系统进料系统流程及特点(固状、膏状、液状)(1) 固体废物进料流程:A、固体废物经起重机抓斗搅拌后,抓送至进料斗上方准备投料。
B、确定翻板处于全关状态,用抓斗将废物抓至翻板上部。
C、确定推料机处于全退状态、锁风装置处于全关状态,首先开启翻板,使固体废物落至推料机前端;关闭翻板,然后开动推料机,使固体废物进入回转窑前端,而后推料机退后,根据实际情况确定往复操作的次数与频率,确保形成一定长度的窑前料封。
D、进入下一个固体废物进料流程,反复第(1)条至第(3)条的操作。
(2)膏状废物进料流程:A、膏状废物、木糠混合固态物进料流程:膏状废物、木糠经混合机出来的固态物的进料方式与固体废物进料方式相同,参瞧固体废物进料流程。
B、包装膏状废物进料流程:包装好的膏状废物通过滚柱传送装置运送到提升机上料搁板上,由提升机提升至回转窑进料斗处,然后由推料机将纸袋(筒)推入回转窑,完成包装膏状废物的进料操作。
C、采用柱塞泵、喷枪进料流程:回转窑前端设浆液喷枪,利用柱塞泵的压力经喷枪喷入回转窑前端,完成膏状废物的进料操作。
(3)、废液进料流程:回转窑前端及二燃室设废液喷枪,利用废液加压泵的压力实现废液雾化后经喷枪喷入回转窑前端或二燃室,完成废液的进料操作。
(4)焚烧系统焚烧系统流程及特点A、危险废物均由回转窑前端进入回转窑,固体废物进料口、液态废物及混合料进料口喷枪均布置在回转窑窑头部位;B、回转窑前端设有燃烧器与一次风,危险废物随着回转窑的转动不断翻滚,与一次风混合,迅速被干燥并着火燃烧。
同时在欠氧条件下分解出可燃气体,焚烧产生的烟气进入二燃室;C、回转窑中未燃烬的危险废物,从回转窑尾部落至设于二燃室下部的专用炉排上继续燃烧直至燃烬,炉排的运行时间为可控,(根据排渣情况调整废物在炉排上的时间)。
产生的烟气进入二燃室,燃烬的炉渣落至水封式出渣机,炉渣经水冷却后,由炉渣运输车外运;D、二燃室中设有两台喷油燃烧器、两个高热值喷枪与一组专门设计的二次风喷口,来自回转窑中未充分燃烧的气体进入二燃室继续燃烧,二燃室布置了高速二次风,它能有力地混搅烟气,并且在>1100-1200℃的情况下,停留>2秒的行程时间,满足有害物质的充分燃烧与分界;E、二燃室燃烧产生的烟气进入余热锅炉。
本方案采用带尾部炉排的回转窑+二燃室组合式焚烧炉。
该组合式焚烧炉具有下列适合危险废物焚烧的特点:A、回转窑+二燃室结构就是目前各国用于各种废物焚烧处置的最常用设备,有大量的使用业绩与较悠久的历史。
B、对危险废物的品种与热值均具有较好的适应性;C、整个焚烧过程,在密闭的条件下进行,正常工作下为负压运行,无任何外泄情况发生,有效防止有害物质与恶臭对周围操作环境的污染;D、在回转窑与二燃室内均布置燃烧器与助燃空气,确保危险废物在所要求的温度下进行燃烧;可以确保烟气在要求温度(≥1100℃)以上具有不小于2秒的停留时间,使有毒有害气体彻底分解;E、为了满足渣热灼减率<5%的规定,在回转窑后续设一只专有技术的小炉排,未燃尽的物料可在炉排上继续焚烧一段时间。
炉排就是可调的,可以按实际情况加速或减速、(我们康博危废处理未采用炉排结构)(5)热能利用系统热能利用系统流程:A、二燃室出口高温烟气进入余热锅炉,在烟气降温的同时产生蒸汽,蒸汽从锅炉汽包排出,部分经过热器过热后进入高温分汽缸进行蒸汽的分配使用,另一部分即从汽包引出饱与汽进入低温分汽缸以供使用。
B、经余热锅炉降温后的烟气(约500~600℃)进入烟气净化系统。
余热锅炉特点:为了大幅度降低运行成本,工程采用一台特殊的全辐射式余热锅炉,该锅炉就是在总结了国内、外以焚烧危险废物余热锅炉的应用实践中,不断改进而开发的全辐射式余热锅炉,它具有以下特点:A、根据工程的特点,为了有效降低运行成本,锅炉的供汽采用两种参数,即:设计压力为1、6MPa,饱与蒸汽温度为203℃;系统中设计了两种分汽缸,即:低温分汽缸及高温分汽缸(详见:工艺流程图);高温分汽缸出来的蒸汽设计压力就是1、5MPa,过热蒸汽温度为:360℃,并利用该过热蒸汽对炉排风及二燃室二次风均加温至:200~300℃,提高了系统的燃烧热效率;并利用该过热蒸汽把烟气处理系统SCR系统的进口烟气温度加热到:240℃-250℃,克服了如用饱与蒸汽加热须加电热带进行再升温,大幅度降低了运行成本。
B、该锅炉特别适应烟气温度向更高化的变化,即使烟气温度超过1100℃或更高,锅炉出口温度的变化也不会太大。
C、锅炉不会出现因积灰与堵灰而导致的影响运行状况,所以锅炉能长期稳定运行,确保降低烟气温度与连续供应工艺生产系统与生活用蒸汽。
(6)烟气净化系统烟气净化系统工艺流程及特点固废处置烟气净化工艺,包括:A 、烟气冷却:将烟气通入急冷塔进行冷却,利用喷液在高温气流中的蒸发达到使气流降温的目的,将炉气温度由500-600℃降到200℃以下,所用的喷液就是来自于喷淋吸收塔排出的废碱液,其中所含碱液能对气体中酸性成份起中与脱酸作用,效率可达到60-80%。
B 、干式脱酸:为了除去烟气中汞等金属及其蒸汽与二恶英的有害物质,在急冷中与塔与布袋除尘器之间的烟道上设置有活性炭粉喷射系统。
活性炭粉经容积给料机,输送至特别设计的喷射吸收器。
同时,还配置了活性消石灰(Ca(OH)2)的喷射系统,与活性碳混合后喷入吸收器,通过特制的文丘里烟气管道,能达到50%除SO2效率与70%以上除HCL 、HF 效率。
碱性物与烟气反应产物的回收利用,继续用于对烟气处理。
C 、除尘:将经过b 步骤处理的烟气通入袋式除尘器,确保了灰尘颗粒在10mg/m3以下的烟气排出药剂危废焚烧处理工艺及图片除尘要求。
D、脱硝:将经过c步骤处理的烟气先经过加热器加热后通入设有喷氨装置的脱硝器,采用SCR(选择性催化剂脱硝工艺)。
依靠催化剂的作用,加强氨(NH3)对NOx的吸收,达到脱NOx 的目的,效率可以达到85%。
E、湿式脱酸:将经过d步骤处理的烟气通入设有碱液喷淋装置的湿式吸收塔,使SO2,HCl、HF的去除率都可以达到99%。