渗碳工艺
渗碳工艺流程
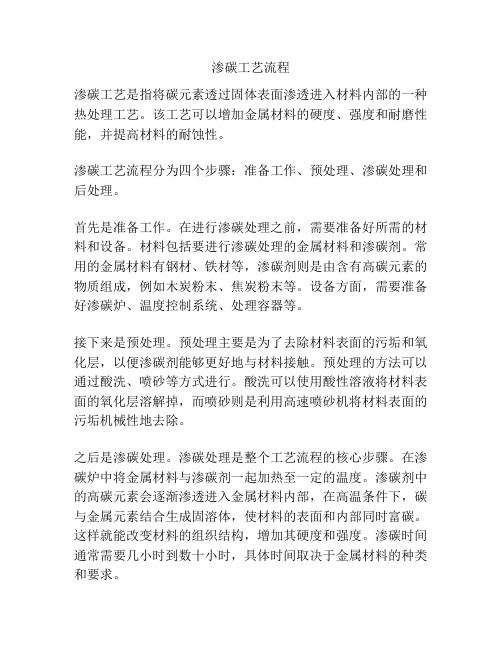
渗碳工艺流程渗碳工艺是指将碳元素透过固体表面渗透进入材料内部的一种热处理工艺。
该工艺可以增加金属材料的硬度、强度和耐磨性能,并提高材料的耐蚀性。
渗碳工艺流程分为四个步骤:准备工作、预处理、渗碳处理和后处理。
首先是准备工作。
在进行渗碳处理之前,需要准备好所需的材料和设备。
材料包括要进行渗碳处理的金属材料和渗碳剂。
常用的金属材料有钢材、铁材等,渗碳剂则是由含有高碳元素的物质组成,例如木炭粉末、焦炭粉末等。
设备方面,需要准备好渗碳炉、温度控制系统、处理容器等。
接下来是预处理。
预处理主要是为了去除材料表面的污垢和氧化层,以便渗碳剂能够更好地与材料接触。
预处理的方法可以通过酸洗、喷砂等方式进行。
酸洗可以使用酸性溶液将材料表面的氧化层溶解掉,而喷砂则是利用高速喷砂机将材料表面的污垢机械性地去除。
之后是渗碳处理。
渗碳处理是整个工艺流程的核心步骤。
在渗碳炉中将金属材料与渗碳剂一起加热至一定的温度。
渗碳剂中的高碳元素会逐渐渗透进入金属材料内部,在高温条件下,碳与金属元素结合生成固溶体,使材料的表面和内部同时富碳。
这样就能改变材料的组织结构,增加其硬度和强度。
渗碳时间通常需要几小时到数十小时,具体时间取决于金属材料的种类和要求。
最后是后处理。
后处理主要是对渗碳处理后的材料进行清洗和调质处理。
清洗是为了除去渗碳剂残留在材料表面的碳渣和污垢,通常可以通过酸洗或者喷砂等方式进行。
调质处理是为了改变材料的组织结构,使其达到所需的力学性能。
常用的调质方式有回火处理、淬火处理等。
总结起来,渗碳工艺流程包括准备工作、预处理、渗碳处理和后处理四个步骤。
通过这一工艺,可以提高金属材料的硬度、强度和耐磨性能,使得材料能够适用于各种高强度、高负荷的工程领域。
液体渗碳技术

液体渗碳技术液体渗碳技术是一种常用的表面强化方法,它通过在金属材料表面形成一层高碳含量的硬化层,从而提高材料的硬度、耐磨性和抗腐蚀性能。
本文将从渗碳原理、工艺流程、设备及应用等方面进行详细介绍。
一、渗碳原理液体渗碳技术主要是利用液态金属中的高浓度活性元素,如碳、氮等,在高温下向金属表面扩散,形成一定厚度的强化层。
其中,液体中的活性元素主要通过化学反应和扩散作用来实现。
在液体渗碳过程中,首先需要将金属件放入预热炉中进行加热处理,使其达到适宜的温度范围。
然后将含有活性元素的溶液(如盐酸、氰酸等)浸泡在金属件周围,并保持一定时间。
在此过程中,活性元素会逐渐扩散到金属表面,并与其发生反应,在表面形成一定厚度的硬化层。
最后将金属件取出冷却,即可完成渗碳处理。
二、工艺流程液体渗碳技术的工艺流程主要包括预处理、渗碳处理和后处理三个环节。
1. 预处理预处理是指在进行液体渗碳前对金属件进行必要的准备工作。
首先需要对金属件进行清洗,去除表面的油污、锈蚀等杂质。
然后将其放入预热炉中进行加热处理,使其达到适宜的温度范围。
2. 渗碳处理渗碳处理是指将含有活性元素的溶液浸泡在金属件周围,并保持一定时间,使活性元素逐渐扩散到金属表面形成硬化层的过程。
具体操作步骤如下:(1)将含有活性元素的溶液倒入渗碳炉中;(2)将预热好的金属件放入渗碳炉中,并确保其表面与溶液充分接触;(3)启动加热系统,使温度逐步升高到设定值,并保持一定时间;(4)关闭加热系统,等待金属件自然冷却至室温。
3. 后处理后处理是指将渗碳处理后的金属件进行必要的加工和表面处理。
主要包括退火、研磨、抛光等环节,以保证其表面质量和性能。
三、设备液体渗碳技术的设备主要包括预热炉、渗碳炉和冷却设备等。
其中,预热炉用于对金属件进行加热处理,使其达到适宜的温度范围;渗碳炉用于浸泡含有活性元素的溶液,并将其扩散到金属表面形成硬化层;冷却设备则用于将金属件冷却至室温。
四、应用液体渗碳技术广泛应用于机械制造、航空航天、汽车制造等领域。
渗碳工艺的原理过程及应用
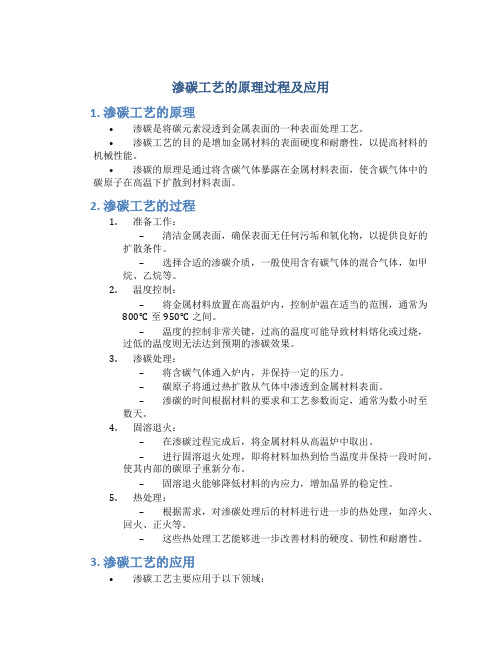
渗碳工艺的原理过程及应用1. 渗碳工艺的原理•渗碳是将碳元素浸透到金属表面的一种表面处理工艺。
•渗碳工艺的目的是增加金属材料的表面硬度和耐磨性,以提高材料的机械性能。
•渗碳的原理是通过将含碳气体暴露在金属材料表面,使含碳气体中的碳原子在高温下扩散到材料表面。
2. 渗碳工艺的过程1.准备工作:–清洁金属表面,确保表面无任何污垢和氧化物,以提供良好的扩散条件。
–选择合适的渗碳介质,一般使用含有碳气体的混合气体,如甲烷、乙烷等。
2.温度控制:–将金属材料放置在高温炉内,控制炉温在适当的范围,通常为800°C至950°C之间。
–温度的控制非常关键,过高的温度可能导致材料熔化或过烧,过低的温度则无法达到预期的渗碳效果。
3.渗碳处理:–将含碳气体通入炉内,并保持一定的压力。
–碳原子将通过热扩散从气体中渗透到金属材料表面。
–渗碳的时间根据材料的要求和工艺参数而定,通常为数小时至数天。
4.固溶退火:–在渗碳过程完成后,将金属材料从高温炉中取出。
–进行固溶退火处理,即将材料加热到恰当温度并保持一段时间,使其内部的碳原子重新分布。
–固溶退火能够降低材料的内应力,增加晶界的稳定性。
5.热处理:–根据需求,对渗碳处理后的材料进行进一步的热处理,如淬火、回火、正火等。
–这些热处理工艺能够进一步改善材料的硬度、韧性和耐磨性。
3. 渗碳工艺的应用•渗碳工艺主要应用于以下领域:1.汽车工业:–渗碳可以提高发动机零部件的硬度和耐磨性,延长零部件的使用寿命。
–例如,曲轴、凸轮轴、齿轮等关键零部件常采用渗碳工艺进行处理。
2.机械制造:–渗碳可以提高机械零部件的表面硬度,减少磨损和疲劳断裂。
–例如,齿轮、轴承、齿条等机械组件可通过渗碳工艺增加其耐磨性和使用寿命。
3.冶金行业:–渗碳可以改善冶金材料的性能,提高其硬度和耐磨性。
–例如,渗碳处理可以将普通碳钢转化为高碳钢,提高钢材的强度和硬度。
4.制造业:–渗碳工艺广泛应用于各种制造业,包括航空航天、船舶、电子、家电等行业。
渗碳的名词解释
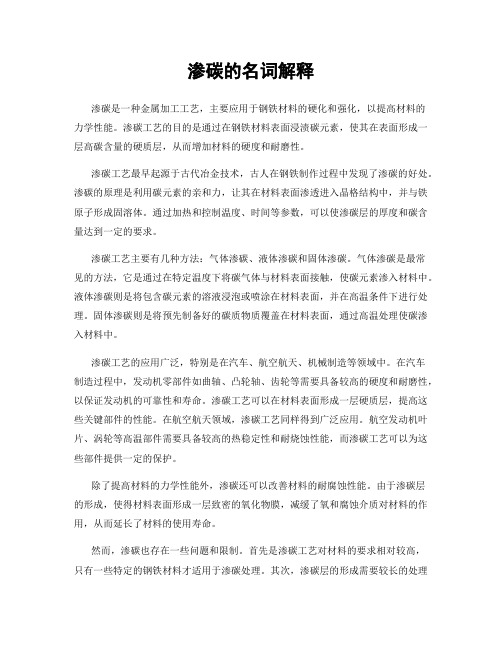
渗碳的名词解释渗碳是一种金属加工工艺,主要应用于钢铁材料的硬化和强化,以提高材料的力学性能。
渗碳工艺的目的是通过在钢铁材料表面浸渍碳元素,使其在表面形成一层高碳含量的硬质层,从而增加材料的硬度和耐磨性。
渗碳工艺最早起源于古代冶金技术,古人在钢铁制作过程中发现了渗碳的好处。
渗碳的原理是利用碳元素的亲和力,让其在材料表面渗透进入晶格结构中,并与铁原子形成固溶体。
通过加热和控制温度、时间等参数,可以使渗碳层的厚度和碳含量达到一定的要求。
渗碳工艺主要有几种方法:气体渗碳、液体渗碳和固体渗碳。
气体渗碳是最常见的方法,它是通过在特定温度下将碳气体与材料表面接触,使碳元素渗入材料中。
液体渗碳则是将包含碳元素的溶液浸泡或喷涂在材料表面,并在高温条件下进行处理。
固体渗碳则是将预先制备好的碳质物质覆盖在材料表面,通过高温处理使碳渗入材料中。
渗碳工艺的应用广泛,特别是在汽车、航空航天、机械制造等领域中。
在汽车制造过程中,发动机零部件如曲轴、凸轮轴、齿轮等需要具备较高的硬度和耐磨性,以保证发动机的可靠性和寿命。
渗碳工艺可以在材料表面形成一层硬质层,提高这些关键部件的性能。
在航空航天领域,渗碳工艺同样得到广泛应用。
航空发动机叶片、涡轮等高温部件需要具备较高的热稳定性和耐烧蚀性能,而渗碳工艺可以为这些部件提供一定的保护。
除了提高材料的力学性能外,渗碳还可以改善材料的耐腐蚀性能。
由于渗碳层的形成,使得材料表面形成一层致密的氧化物膜,减缓了氧和腐蚀介质对材料的作用,从而延长了材料的使用寿命。
然而,渗碳也存在一些问题和限制。
首先是渗碳工艺对材料的要求相对较高,只有一些特定的钢铁材料才适用于渗碳处理。
其次,渗碳层的形成需要较长的处理时间,特别是对于较厚的渗碳层,处理时间更长。
此外,渗碳过程中材料内部会产生应力,可能会导致变形和破裂,因此处理过程需要严格控制。
总之,渗碳是一种重要的金属加工工艺,可以通过在材料表面形成一层高碳含量的硬质层,提高材料的硬度、耐磨性和耐腐蚀性能。
渗碳工艺的六种常见方法

书山有路勤为径,学海无涯苦作舟
渗碳工艺的六种常见方法
1、一次加热淬火低温回火,渗碳温度820~850o C 或
780~810o C
特点:对心部强度要求高者,采用820~850o C 淬火,心部组织为
低碳马氏体;表面要求硬度高者,采用780~810o C 加热淬火可以细化晶
粒。
适用范围:适用于固体渗碳后的碳钢和低合金钢工件。
气体、液体渗碳后的粗晶粒钢,某些渗碳后不宜直接淬火的工件及渗碳后需机械加工的零件。
2、渗碳、高温回火,一次加热淬火、低温回火,渗碳温度840~860o C
特点:高温回火使马氏体和残留奥氏体分解,渗层中碳和合金元素以碳化物形式析出,便于工削加工及淬火后渗层残留奥氏体减少。
适用范围:主要用于Cr-Ni 合金钢渗碳工件。
3、二次淬火低温回火
特点:第一次淬火(或正火),可以消除渗层网状碳化物及细化心部组织。
第二次淬火主要改善渗层组织,但对心部性能要求较高时应在心部Ac3 以上淬火。
适用范围:主要用于对力学性能要求很高的重要渗碳工件,特别是对粗晶粒钢。
但在渗碳后需进行两次高温加热,使工件变形及氧化脱碳增加,热处理过程较复杂。
4、二次淬火冷处理低温回火
特点:高于Ac1 或Ac3(心部)的温度淬火,高合金钢表层残留奥氏体较多,经冷处理(-70~80ºC)促使奥氏体转变,从而提高表面硬度和耐磨性。
渗碳处理工艺

渗碳处理工艺
1渗碳处理技术
渗碳处理技术已经在化学行业和铸造行业中得到了广泛的应用,它是一种改善金属材料性能的热处理方法。
渗碳工艺是把铁和钢熔点中的碳移入金属材料的边界处,从而提高金属材料的抗疲劳和耐磨性的工艺。
渗碳处理可以改善金属的拉伸强度,抗压强度和塑性,延长金属材料的使用寿命。
渗碳处理是指使用受热炉中的碳吸收到金属材料表面,形成不同厚度的碳化膜而达到其他目的的一种处理工艺。
优势
渗碳处理主要有以下几个优势:
1.渗碳处理的加工周期短,不需要外部的操作介入,只需要一定的温度和时间,即可实现金属材料的改性,简化了工艺流程。
2.渗碳处理的原料便宜,由于不需要使用复杂的元素,因此经济特别是能源压力比较小。
3.渗碳处理能够提高金属材料的热强度,减少金属材料的疲劳损坏,延长金属材料的使用寿命。
应用
渗碳处理主要应用在机械制造、汽车制造等行业,如铸件、管件、压力容器、螺栓螺母和销芯等。
渗碳处理的热处理工艺还可以用于装配件的生产,这样可以改善机械装配件本身的外观性能,延长其使用寿命,提高机械装配件的耐久性,从而提高使用效率。
2结论
渗碳处理是一种改善金属材料性能的热处理方法,具有加工周期短、原料便宜、热强度高、耐久性好等优点,可以应用在机械制造、汽车制造等行业,如铸件、管件、压力容器、螺栓螺母和销芯等,能够为金属材料的改性提供一种有效的方法。
渗碳工艺的工艺流程
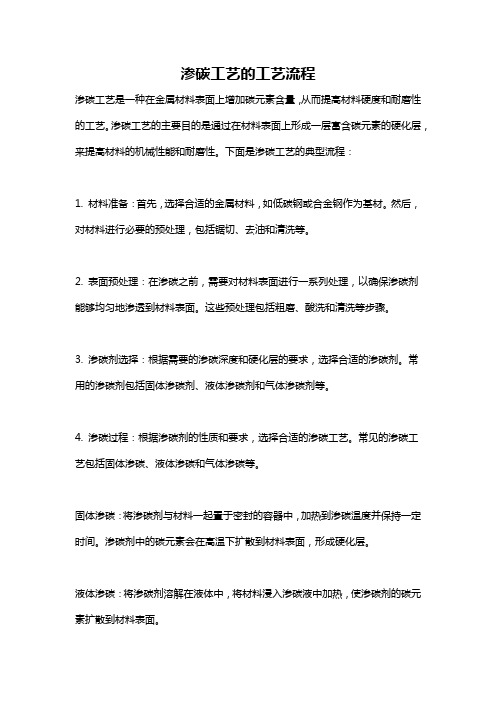
渗碳工艺的工艺流程渗碳工艺是一种在金属材料表面上增加碳元素含量,从而提高材料硬度和耐磨性的工艺。
渗碳工艺的主要目的是通过在材料表面上形成一层富含碳元素的硬化层,来提高材料的机械性能和耐磨性。
下面是渗碳工艺的典型流程:1. 材料准备:首先,选择合适的金属材料,如低碳钢或合金钢作为基材。
然后,对材料进行必要的预处理,包括锯切、去油和清洗等。
2. 表面预处理:在渗碳之前,需要对材料表面进行一系列处理,以确保渗碳剂能够均匀地渗透到材料表面。
这些预处理包括粗磨、酸洗和清洗等步骤。
3. 渗碳剂选择:根据需要的渗碳深度和硬化层的要求,选择合适的渗碳剂。
常用的渗碳剂包括固体渗碳剂、液体渗碳剂和气体渗碳剂等。
4. 渗碳过程:根据渗碳剂的性质和要求,选择合适的渗碳工艺。
常见的渗碳工艺包括固体渗碳、液体渗碳和气体渗碳等。
固体渗碳:将渗碳剂与材料一起置于密封的容器中,加热到渗碳温度并保持一定时间。
渗碳剂中的碳元素会在高温下扩散到材料表面,形成硬化层。
液体渗碳:将渗碳剂溶解在液体中,将材料浸入渗碳液中加热,使渗碳剂的碳元素扩散到材料表面。
气体渗碳:将含碳气体(如一氧化碳)直接与材料接触,在高温下使碳元素扩散到材料表面。
5. 渗碳时间和温度控制:根据材料和渗碳剂的性质,控制渗碳的时间和温度。
渗碳时间和温度的选择对于形成理想的硬化层非常重要。
6. 渗碳后处理:在渗碳完成后,需要对材料进行后处理,以去除渗碳剂的残留物和减小变形风险。
后处理步骤包括冷却、清洗和淬火等。
7. 检测和评估:最后,对渗碳后的材料进行检测和评估,以确保渗碳的效果满足要求。
常见的检测方法包括金相检测、硬度测试和耐磨性测试等。
总结起来,渗碳工艺是一种通过在金属材料表面上增加碳元素含量来提高硬度和耐磨性的工艺。
其工艺流程包括材料准备、表面预处理、渗碳剂选择、渗碳过程、渗碳时间和温度控制、渗碳后处理以及检测和评估等步骤。
只有在每个步骤都严格控制和操作的情况下,才能获得理想的渗碳效果。
渗碳

• (2)装箱:零件的固体渗碳时在渗碳箱中进行 ,渗碳箱 一般用钢板焊成或铸铁铸成,渗碳箱不宜过大,其外形尺 寸应尽可能适合工件的要求,箱子最好与炉底板架空,受 热均匀 。 • (3) 装炉与升温:零件可在低温入炉并用分段升温的方 法。但对于连续生产,这种方法不经济,故通常采用高温 入炉的方法。 • (4) 保温时间:零件在渗碳温度下需要保温时间视渗碳 层深度要求而定。 • (5) 出炉前的试棒检查:保温完毕大约半小时抽检试 棒,可把试棒淬于水中,折断后观察断口,或将断面抛光 后用4%硝酸酒精腐蚀,以检查渗碳层所达到的深度,渗 碳深度达到了技术要求则可出炉。如还未达到渗碳层深 度,应适当延长保温时间。
渗碳零件的材料
渗碳用钢:合金渗碳 钢含碳量0.15~0.25 %之间。 例15、20、20Cr、 20CrMnTi、20SiMnVB 等
• 发展历史:渗碳工艺在中国可以上溯2000 年以前。最早是用固体渗碳介质渗碳。液 体和气体渗碳是在20世纪出现并得到广泛 应用的。美国在20年代开始采用转筒炉进 行气体渗碳。30年代﹐连续式气体渗碳炉 开始在工业上应用。60年代高温(960~ 1100℃)气体渗碳得到发展。至70年代﹐出 现了真空渗碳和离子渗碳。
由渗剂直接滴入炉内进行渗碳时,由于热裂 分解出的活性碳原子过多,不能全部为零件表面所 吸收而以炭黑、焦油等形式沉积于零件表面,阻碍 渗碳过程,而且渗碳气氛的碳势也不易控制。因此 发展了滴注可控气氛渗碳,即向高温炉中同时滴入 两种有机液体,一种液体(如甲醇)产生的气体碳 势较低,作为稀释气体;另一种液体(如醋酸乙酯) 产生的气体碳势较高,作为富化气。通过改变两种 液体的滴入比例,利用露点仪和红外分析仪控制碳 势,是零件表面的含碳量控制在要求的范围内。
气体渗碳通过下述反应使原子扩散渗透到钢 中:2CO=〔C〕+CO2 • 滴注式的CO是通过C一H一O系有机剂在炉中 直接热分解而获得的。但液体有机剂的品种 很多,并不是都可以用于滴注。作为滴注用 的有机剂一般可分为下列三类: (1)C>O时,如CH3·COOCH(醋酸甲脂) 2CO+3H2+〔C〕 (2)C=O时,如CH3OH(甲醇) CO+2H2 (3)C<O时,如HCOOH(甲酸) CO+H2+〔O〕
- 1、下载文档前请自行甄别文档内容的完整性,平台不提供额外的编辑、内容补充、找答案等附加服务。
- 2、"仅部分预览"的文档,不可在线预览部分如存在完整性等问题,可反馈申请退款(可完整预览的文档不适用该条件!)。
- 3、如文档侵犯您的权益,请联系客服反馈,我们会尽快为您处理(人工客服工作时间:9:00-18:30)。
渗碳工艺如下:
电炉到870°后,打开炉盖,放置零件到炉内,拧紧盖子螺丝,盖子的缝隙绝对不能有气体排出(用点火检查),开始放甲醇到保温60分钟的正常流量,后同时放三乙醇胺2时30分钟,打开炉盖,取出零件到保温桶内自然冷却到空气温度(注意绝不能整体放入到油中或水中冷却)然后就可以对有要求做硬度部分加热到850°左右,快速放入到流动的冷水中冷却,就可以了。
2. 如果表面渗碳厚度在0.3-0.4mm之间
延长放三乙醇胺的时间30分钟就可以,其它一样。
只做参考
祝永华。