滚子摇臂式配气机构凸轮型线改进设计_长城_孙小伟
配气机构凸轮型线优化设计参考资料
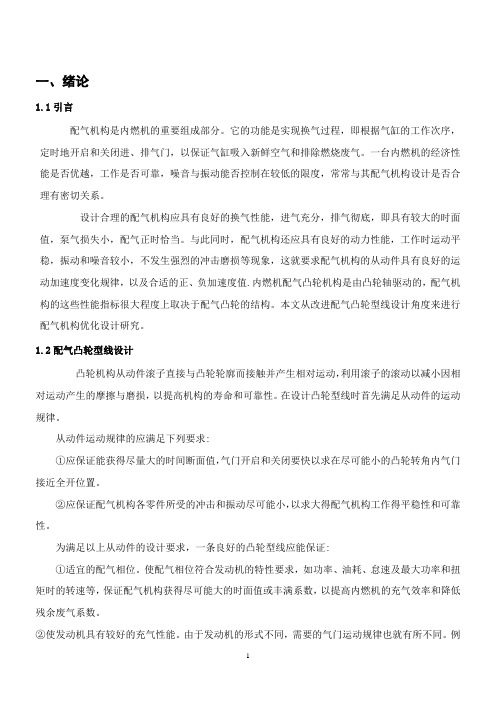
一、绪论1.1引言配气机构是内燃机的重要组成部分。
它的功能是实现换气过程,即根据气缸的工作次序,定时地开启和关闭进、排气门,以保证气缸吸入新鲜空气和排除燃烧废气。
一台内燃机的经济性能是否优越,工作是否可靠,噪音与振动能否控制在较低的限度,常常与其配气机构设计是否合理有密切关系。
设计合理的配气机构应具有良好的换气性能,进气充分,排气彻底,即具有较大的时面值,泵气损失小,配气正时恰当。
与此同时,配气机构还应具有良好的动力性能,工作时运动平稳,振动和噪音较小,不发生强烈的冲击磨损等现象,这就要求配气机构的从动件具有良好的运动加速度变化规律,以及合适的正、负加速度值.内燃机配气凸轮机构是由凸轮轴驱动的,配气机构的这些性能指标很大程度上取决于配气凸轮的结构。
本文从改进配气凸轮型线设计角度来进行配气机构优化设计研究。
1.2配气凸轮型线设计凸轮机构从动件滚子直接与凸轮轮廓而接触并产生相对运动,利用滚子的滚动以减小因相对运动产生的摩擦与磨损,以提高机构的寿命和可靠性。
在设计凸轮型线时首先满足从动件的运动规律。
从动件运动规律的应满足下列要求:①应保证能获得尽量大的时间断面值,气门开启和关闭要快以求在尽可能小的凸轮转角内气门接近全开位置。
②应保证配气机构各零件所受的冲击和振动尽可能小,以求大得配气机构工作得平稳性和可靠性。
为满足以上从动件的设计要求,一条良好的凸轮型线应能保证:①适宜的配气相位。
使配气相位符合发动机的特性要求,如功率、油耗、怠速及最大功率和扭矩时的转速等,保证配气机构获得尽可能大的时面值或丰满系数,以提高内燃机的充气效率和降低残余废气系数。
②使发动机具有较好的充气性能。
由于发动机的形式不同,需要的气门运动规律也就有所不同。
例如球形燃烧室内燃机希望进气门尽快开启使空气尽早流入;而高速汽油机希望进气开始时缓慢一些,以便更好的利用惯性充气。
③适宜的从动件加速度。
加速度不宜过大或者带突变,加速度曲线应尽可能连续。
天然气发动机配气凸轮型线的改进设计

天然气发动机配气凸轮型线的改进设计郑清平;张玲玲;张盼盼;黎明;王瑾【摘要】利用AEXCITE TIMING DRIVE软件,建立某四气门天然气发动机运动学和动力学模型,对原有发动机配气机构进行性能分析,发现了原机配气机构存在丰满系数小、落座冲击大、接触应力过大、有轻微反跳和飞脱问题.通过改进设计凸轮型线的缓冲段和工作段型线,模拟结果表明,进气门丰满系数从原机的0.56增加到0.58,排气门丰满系数从0.53增加到0.57,增加了发动机的充气性能,同时也解决了气门落座冲击大、反跳问题,减少了凸轮与挺柱间的接触应力.发动机性能试验结果表明,改进设计后的配气机构同时也改善了发动机的动力性能,提高了功率和转矩.【期刊名称】《河北工业大学学报》【年(卷),期】2015(044)005【总页数】5页(P55-59)【关键词】天然气;发动机;配气机构;气门;凸轮型线【作者】郑清平;张玲玲;张盼盼;黎明;王瑾【作者单位】河北工业大学能源与环境工程学院,天津300401;河北工业大学能源与环境工程学院,天津300401;河北工业大学能源与环境工程学院,天津300401;河北工业大学能源与环境工程学院,天津300401;河北工业大学能源与环境工程学院,天津300401【正文语种】中文【中图分类】TK413.40 前言配气机构是发动机的重要组成部分,其工作的好坏直接影响发动机的换气过程,与发动机的动力性、经济性以及排放性密切相关[1-3].配气机构研究包括两方面的内容:1)零部件的设计,包括凸轮型线、气门摇臂、气门弹簧及气门等零部件的设计,其中凸轮型线的设计尤为重要;2)机构的运动学和动力学问题[4-5].本文利用EXCITETIM INGDRIVE软件建立了某天然气发动机配气机构运动学和动力学计算模型,首先分析其是否存在落座冲击大、反跳、飞脱、接触应力过大等配气机构问题,然后通过改进设计凸轮缓冲段和工作段型线,解决存在的问题,最终使发动机性能得到一定的改善.1 配气机构模型的建立该天然气发动机采用下置式凸轮轴配气机构,其机构主要包括凸轮轴、挺柱、推杆、摇臂、气门桥、进、排气门以及气门内外弹簧.单阀系计算模型如图1所示.该发动机配气机构模型中,需要的参数包括各个零部件结构参数、单元的刚度、阻尼以及质量等.为了保证计算的准确性,单元的刚度通过有限元计算获得,其质量通过PROE软件获得.2 原进、排气凸轮型线的评价2.1 运动学结果在计算模型中导入原发动机的进排气凸轮升程曲线,进行运动学模拟.通过运动学模拟,得到配气机构的主要技术参数如表1所示,主要性能参数如表2所示.丰满系数反映了发动机充气效率,丰满系数较大能够提高发动机的充气性能,使发动机尽可能进气,但是过大的丰满系数会影响配气机构的可靠性和平稳性,为了获得良好的充气效率,一般要求丰满系数不低于0.55,原发动机排气门的丰满系数为0.53,有待提高.凸轮与挺柱间的润滑系数反映了其润滑性能的好坏,一般要求最小润滑系数,即在凸轮桃尖附近,润滑系数为0.15~0.3.原发动机进、排气凸轮与挺柱之间润滑系数都在范围内,其润滑性能良好.凸轮与挺柱的材料分别是球墨铸铁和钢,其最大的许用应力为650 MPa,排气门凸轮与挺柱间接触力大于许用应力值,增加了零件间的磨损,缩短了零件的使用寿命.加速度跃度是反映从动件振动响应的重要指标,为了减少振动,一般要求最大跃度值不超过1000mm/rad3.图1 计算模型Fig.1 The calculationmodel表1 主要技术参数Tab.1 Themain technicalparameters技术参数凸轮升程/mm气门升程/mm基圆半径/mm凸轮轴标定转速/r m in 1提前开启相位角/°CA滞后关闭相位角/°C A进气 5.693 8.12 17 1 250 16 27排气 6.0 8.76 17 1 250 60 10表2 主要性能参数Tab.2 Themain performance parameters性能参数丰满系数最大接触应力/MPa最大跃度值/mm rad 3凸轮与挺柱间最小润滑系数进气0.56 640 1 188 0.18排气 0.53 670 912 0.172.2 原配气机构动力学结果分析该发动机在额定转速2 500 r/m in时,其气门升程、凸轮与挺柱间的接触应力以及落座情况如图2~图4所示.从图中可以看出,排气门存在早关的现象,其关闭不平稳.排气门的接触应力过大,超过许用范围,增加了凸轮桃尖处的磨损.在气门落座时,落座力突然增大,其落座不平稳,冲击力较大,在气门落座之后出现落座力为0的情况,说明气门存在反跳的现象.3 凸轮型线的改进设计配气凸轮由3段组成,其中包括:基圆、挺柱上升段和挺柱下降段,其中上升段和下降段又分别由缓冲段和工作段组成[6].根据原进、排气配气机构存在的问题,对凸轮型线的缓冲段和工作段进行改进设计.由于原气门落座冲击加大,考虑到配气机构运行平稳性以及配气机构的特点,选择梯形函数作为新凸轮型线缓冲段.气门间隙为0.3,气门缓冲段高度设置为0.32 mm,由于原发动机气门落座速度过大,需要降低缓冲段的末端速度,将其设置为1.5mm/rad3.多项式配气凸轮工作段函数得到的升程具有多阶导数连续,气门升程比较光滑,且能够适应多种类型的配气机构,使用比较广泛 [7-8].本文采用多项式工作段函数对凸轮型线改进设计,其气门升程为图2 原机进、排气门升程Fig.2 The originalvalve lift式中:h max为凸轮最大升程,mm;hr为缓冲段高度,mm;C2、C4、Cp、Cr、Cs为常数;p、q、r、s为偶数指数,一般取8~60.通过多次模拟对比,最终确定进、排气凸轮型线方案,其参数C4、p、q、r、s的取值分别为0.2、12、22、32、52;0.2、14、24、32、52.改进后的运动学性能如表3所示,从表中可以看出改进后进、排气气门升程丰满系数分别从原机的0.56增加到0.58,从0.53增加到0.57,增加了发动机的充气性能,改善了发动机的换气过程,加速度最大跃度值都小于1 000 mm/rad3,确保的配气机构运行的平稳性避免了机构发生振动.凸轮与挺柱间的润滑条件较好,减少了零部件间的磨损.最大接触应力都满足许用值要求,其值小于原发动机,降低了凸轮与挺柱间的磨损.改进后的凸轮型线,其动力学分析结果如图5~图7所示,从图中可以看出,改进后的气门升程曲线光滑,开启、关闭都比较良好,没有出现波动,在凸轮工作段,凸轮与挺柱间的接触力不存在零的现象,没有发生飞脱,且接触应力小于原发动机,都在允许范围之内,减少了对凸轮桃尖处的磨损.进、排气门落座都比较平稳,没有发生大的冲击,减少了气门与气门座之间的磨损,同时气门落座后,没有出现落座力为0的情况,说明气门没有发生反跳.表3 改进后主要性能参数Tab.3 Themain performance para metersafter improvement性能参数丰满系数最大接触最大跃度值/凸轮与挺柱间应力/MPa mm rad 3最小润滑系数进气 0.58 510 978 0.2排气 0.57 498 964 0.184 改进后发动机性能试验为了验证凸轮型线改进前后发动机的性能,在发动机试验台架进行了外特性试验,并测取了进气流量和充气效率.天然气发动机的试验台架,如图8所示.主要测试装置包括CW 150型电涡流测功机(洛阳南峰机电设备有限公司)、上海同圆环保科技有限公司生产TOCEIL-CMF02型天然气流量计,AVL1000型空气流量计.图9为凸轮型线改进前后不同转速下气缸的充气效率,从图中可以看出,改进后发动机充气效率有所提高,在转速为2200 r/min时,充气效率提高了1.51%,在转速为1400 r/m in时,充气效率增加了0.79%,在额定转速下充气效率提高了0.83%,改善了发动机充气性能.图5 改进后进、排气门升程Fig.5 Valve liftafter improvement图8 天然气发动机试验台架Fig.8 Naturalgasengine testbench图9 改进前后充气效率对比Fig.9 Comparison of charge coefficientbeforeand after improvement图10 和图11分别为凸轮型线改进前后转矩和功率随转速的变化,从图中可以看出凸轮型线改进设计后,由于发动机的进气量增加,从而使发动机功率和转矩也有所增加,其中在转速1200 r/m in时,转矩增加了12.56 N m,功率增加了5.25,在标定转速下,转矩和功率分别增加了7.2 N m、2.1 kW,由此可见,改进凸轮型线后使发动机性能得到一定改善.图10 改进前后功率对比Fig.10 Comparison of powerbeforeand after improvement图11 改进前后转矩对比Fig.11 Comparison of toquebeforeand after improvement5 小结1)利用EXCITETim ing Drive软件建立了天然气发动机配气机构的运动学、动力学计算模型,评价了原进、排气凸轮型线,并找出了原配气机构存在的问题.2)针对原配气机构存在的问题,改进了凸轮型线的缓冲段和工作段,提高了进、排气凸轮的丰满系数,解决了气门落座冲击大、反跳等问题,同时减少了凸轮与挺柱间的接触应力,减低了凸轮桃尖处的磨损.3)凸轮型线的改进设计使原发动机动力性能得到一定的改善.参考文献:[1]刘云,肖恩忠.高速柴油机配气凸轮优化设计综述 [J].拖拉机与农用运输车,2006,33(4):6-9.[2]焦运景,张惠明,杨志勇.配气相位对天然气发动机燃烧和排放的影响 [J].农业机械学报,2009,8(8):13-17.[3]肖红,苏强,骆葳.天然气发动机在不同喷射和点火时刻下的性能和优化设计研究 [J].内燃机,2014(2):25-29.[4]姜建华,王伟.CA4D柴油机配气机构设计 [J].汽车技术,2005(9):21-24.[5]TAkashi IRITANI,Akira SHOZAKI,Bencheng SHENG.Predicition of the dynam ic characteristics in valve train design of a diesel engine[J].SAE,2002,32:1839-1846.[6]郭磊,褚超美,陈家琪.高次多项式凸轮型线特性参数对配气机构性能的影响的研究 [J].内燃机工程,2005,26(1):20-23.[7]王小慧,彭海雄,周海涛.配气凸轮轴型线逆向优化设计 [J].铁道机车车辆,2011,10(31):177-188.[8]浦耿强,张云清.顶置凸轮配气机构仿真分析 [J].汽车科技.2001(1):8-11.。
06-某发动机凸轮型线的优化设计及分析_吉利汽车苏圣等

凸轮型线的设计及分析苏圣胡景彦李慧军刘云卿杜宝杰吴丰凯吴小飞(浙江吉利汽车技术中心有限公司,浙江杭州 311228)摘要:本文主要描述通过工程软件计算出来的分析结果来进行指导凸轮型线的设计,最后通过发动机试验验证了新设计的凸轮型线满足设计要求。
关键词:汽油机凸轮型线阀系动力学特性单阀系动力学正时机构动力学主要软件:A VL EXCITE Timing drive、A VL Boost1. 前言在发动机的配气机构中,凸轮的凸轮型线不仅对发动机的动力性能有影响,同时也对发动机的机械噪声和零部件的磨损情况都有直接的影响。
所以优化设计一个比较好的凸轮型线既要考虑发动机的热力学性能又要关注发动机的机械性能,同时还要满足凸轮型线的加工要求。
只有上述几个条件全部满足要求才能进行加工生产并且测试。
设计凸轮型线总共分成5个阶段。
第一阶段为热力学预测阶段,在该阶段中主要设计一条热力学性能最优的气门升程曲线。
第二阶段为凸轮型线设计阶段,在该阶段中参照热力学设计的气门升程曲线并且根据运动学原理设计一条满足动力学性能的凸轮型线。
第三阶段对设计完成的凸轮型线进行单阀系的动力学校核,如果不满足动力学要求,则返回第二阶段重新设计凸轮型线。
第四阶段进行多阀系动力学分析,观察各个指标是否满足设计要求,如果不满足要求返回第二阶段重新设计。
第五阶段就是将设计完成的凸轮型线移交给供应商进行加工。
下图为凸轮型线的设计流程。
图1 凸轮型线设计流程2. 设计过程2.1 热力学预测目前某款1.5升GDI发动机最大功率为78kW,要比预期的发动机功率小5kW,为了提高发动机功率,采取的措施为更改发动机的进排气凸轮。
首先根据某1.5升GDI发动机参数进行搭建热力学模型,并且反复调试该热力学模型直到热力学各个工况的计算结果与实际中测得相对应工况中的试验结果相吻合为止。
热力学模型如下图所示。
图2 热力学模型利用上述的热力学软件,计算4种进气门升程和4这种排气门升程,计算出相应的功率和扭矩。
配气机构凸轮型线改进设计

大的振动和磨损 。为了避免上述严重缺点 ,本文使 用多项高次方凸轮代替传统的几何凸轮 ,以实现配 气机构凸轮型线的优化 ,并且使用 A A S软件对 DM 采用 两种 凸轮 的 配气 系统分 别建 模 。最后 对 两个配 气 机构 的性 能进 行预测 并 对 比分 析 了计算 结 果 。
收稿 日期 :20 460 0 6 )-5
见 ,取凸轮上升段进行讨论。假设工作段挺柱最大 升 程为 一 。 ( ) 当 = 1 。时 ,h = 一 。 ( ) 当 =0时 ,h( )= 2 。1 0 ( ) 当 = 3 0时 ,假 设气 门开启 ( 落 座 ) 速 或 度为 ,因为 :
1 前
言
几 何 凸轮 的主要 缺点 是运 动规 律不 连续 ,在 高 速 发动 机 中将会 引起 配气 机构 的强 烈振 动 ,造成 很
包角 ) ,挺柱工作段始点卢= ;挺柱最大升程处 = 1 0 ;工作段终点处 = , 2 对应/=一 。 3 1 下 面 以 五项 式 为 例 ,说 明其 升 程 曲 线 的 表 达 式:
2 函数 凸轮 设 计 原 理
多项 高次 方 凸轮 系 有 多项 式 高 次 方 曲线 组 成 , 它的升程 曲线二 阶导数 为连 续 函数 ,即保 证 正 负加
速度连续圆滑过渡。以基本工作段起点作为计算起
点,对应 = ,挺柱升程 h = ;为 了计算方便 , 0 。0
以无因次量 卢=1 作为 自变量 ( 为工作段半 一
: .
望 . :
d d i t
d
维普资讯
・
2 O・
I r v me to m t n sg srb t n M e h n s mp o e n fCa Ou l e De in i Diti u i c a im i n o
WD618.42柴油机配气凸轮型线的改进设计

l. 5 5
WD 1. 2柴ቤተ መጻሕፍቲ ባይዱ油机是 潍 柴 动力 新 投 放 市 场 的功 68 4 率 较 大 的车 用 发 动机 , 在试 验 阶段 发 现 该 机 型存 在
缸 径 × 行 程/ m a r 标 定 功 率 / W k
文 章 编 号 :00 02(06 0 -00 0 10 - 9520) 5 5 - 4
2 0 9 7 0 6
WD 1 . 2柴 油机 配气 凸轮 型线 的 改进 设 计 6 4 8
乔 军 ’ 国祥 。李
( . 柴 动力股 份 有限公 司 , 1潍 潍坊 2 1 0 ;. 6 0 1 2 山东 大学 能源 与 动力 T程 学 院)
pr s u e d c e s d a lt l. e s r e r a e ite
摘 要 :利用 B X S ( )T和 T C N软件 对 WD 1. 2柴油机及 其配 气机 构建 立仿 真计算模 型 , Y O 684
进 行 了联合计 算。对 配气相位进行 了重新选择 , 大凸轮 升程 和轮廓 线 函数 也进行 了优 化 , 高 最 提 了充 气效率 降低 了进排 气凸轮 最大接触 应 力。通过 台架试验 结 果对 比证 明 , 柴油机 采 用改进 后
发 火 顺 序 最 高燃 烧 压 力 / a MP 冷 态 气 门 间 隙/ m a r
l53624 ———— l. 5 3 进 . 5 排 . 气0 3 , t0 4
进 气 广 开 3 . 。 A I ) J 6 5 【 j 【 ’ TI ’
Ab t a t I h ril,t esmu ain m o eso D6 8 4 is le gn n t av r i r e sr c : n t ea tce h i lt d l f o W 1 . 2 de e n i ea d isv letan we es t
凸轮泵转子型线优化设计及模拟计算

凸轮泵转子型线优化设计及模拟计算沈浩;贾琨;黎义斌;孟庆武;桑小虎【摘要】针对渐开线转子型线进行优化设计,在转子型线为渐开线-圆弧的基础上,引入一段高阶曲线,衔接渐开线与圆弧之间的过渡曲线,有效的消除曲线连接处所形成的“尖点”现象.通过对高阶曲线的边界限制和计算机软件的实施得出高阶曲线的方程,并根据几何方法及渐开线的性质从而得到整个转子型线的参数方程,并建立其三维模型.采用动网格技术对凸轮泵三维模型数值模拟计算,结果表明:优化后的模型出口处的“脉动”现象有很大的改善,有效的降低了工作噪音.随着转速的提升,介质在出口处的平均速度也随之升高.通过对比流场的模拟计算和实验结果,验证了模拟计算方法的可行性.【期刊名称】《兰州理工大学学报》【年(卷),期】2014(040)003【总页数】5页(P44-48)【关键词】凸轮泵;转子型线;动网格;脉动现象【作者】沈浩;贾琨;黎义斌;孟庆武;桑小虎【作者单位】兰州理工大学机电工程学院,甘肃兰州730050;兰州理工大学机电工程学院,甘肃兰州730050;兰州理工大学能源与动力工程学院,甘肃兰州730050;济南优科精流机械设备有限公司,山东济南250021;兰州理工大学机电工程学院,甘肃兰州730050【正文语种】中文【中图分类】TH326随着海洋、边远油田的开发利用和污水输送的发展,工作方式有效且经济效益好的凸轮泵成为研究的热点.凸轮泵中,转子在传动轴的带动下进行同步反向旋转,从而构成了较高的真空度和排放压力,特别适合医药介质和腐蚀性高黏度介质的输送.目前,在食品加工、油脂生产、日用化学、油田运输、污水处理等领域已经有广泛的应用. 凸轮泵具有结构简单,对产品的剪切力小以及稳定运输等优点,成为近年来研究的焦点.张铁柱[1]等针对于摆线叶型的转子型线方程进行推导,并对转子型线提出了参数优化设计方法和实例的论证.很多研究人员在此基础上,应用复极矢量函数等方法建立了渐开线转子理论型线模型[2-3].S.H.Tong [4]等应用偏差函数(DF)方法对渐开线转子型线进行修正,并研究了凸轮泵在工作过程中产生的振幅变化周期.随着计算机软件的发展,对泵的模拟计算越来越完整、精确[5-7],特别是张锴等[8]应用动网格技术对泵内流场全面的展示.在国外,凸轮泵的型线设计的研究是前沿课题之一[9-10],而在国内这方面的研究较少.本文是以外啮合的两叶凸轮泵作为研究对象,在转子型线为渐开线-圆弧的基础上提出了一种渐开线-高阶曲线-圆弧的优化方案,通过计算得到转子型线方程,应用相关的软件建立其凸轮泵的三维模型.Fluent计算中,采用K-Epsilon湍流模型和动网格技术,对凸轮泵全流场进行三维非定常湍流计算.1 理论计算凸轮泵的核心就是一对共轭的且形状相同的转子,现阶段转子型线主要以渐开线为代表,齿顶和齿根处一般都是采用圆弧.凸轮泵型线不是一条光滑的曲线,在两段曲线的衔接处会出现“尖点”,如图1a所示,从而使介质运输过程中产生很大“脉动”现象,既产生了噪声又不能保证介质的平稳恒量的输送.故在此基础上引入了高阶曲线,如图1b所示,高阶曲线是连接渐开线和圆弧之间一段过渡曲线,保证转子型线连续并且光滑.图1 两种转子型线Fig.1 Two kinds of rotor profiles转子理论型线除满足共轭条件外,转子的叶形应有良好的几何对称性、连续性.以下是对端面为渐开线的转子模型的建立.转子的型线由渐开线、高阶曲线、齿根圆弧和齿顶圆弧组成.1.1 基圆半径和齿根、齿顶圆半径如图2所示,过A点作基圆的切线交于F点,压力角为α.根据三角关系可知:rj=Rcos α(1)式中:R为节圆半径,rj为基圆半径,α为压力角.由渐开线啮合特性知,啮合点在啮合线上移动的距离等于基圆上任意点在基圆上移动的弧线距离.当啮合点由E移到P点,节圆上的C点必移至P点,即节圆转动了1/8周,继而得到:(2)式中:r0为齿顶和齿根圆弧半径.由式(2)可见,齿顶圆弧和齿根圆弧半径r0与压力角α无关,只随基圆半径rj改变. 图2 优化后的转子型线Fig.2 Optimized profile of rotor1.2 渐开线方程在渐开线上的任意取一点Z(x,y),从Z点做基圆的切线ZD,切点为D.θ角随Z点在渐开线BCE上的移动而变化,Z(x,y)点的坐标方程为(3)依据渐开线性质可知:由于(4)根据图2几何关系则有从而得(5)将上式代入式(3)得(6)1.3 压力角为了使两转子啮合时不产生干涉,应使两转子啮合的啮合点不超过公法线与基圆的切点,即也就是π/4rj≤rjtan α从而有α≥38°8′46″(7)在模拟计算和实际加工中,渐开线转子的压力角一般选用α=40°~50° .1.4 高阶曲线为了保证整个凸轮泵转子型线连续、光滑,如图2所示,在渐开线和圆弧衔接处引入高阶曲线(MB和EH两端曲线),其初始表达式为ρ(φ)=a0+a1φ+a2φ2+a3φ3+…+anφn(8)为了使ρ(φ)的三阶导数存在而且连续光滑,变化方程(8)的次数至少不低于5次,即要求n≥5.但是,随着方程次数的增高,曲线ρ(φ)的二阶、三阶导数的最大值vmax、amax将增大,因此方程次数也不宜太高,一般取n≤8.这里取n=6,所求的过渡高阶曲线应是六次多项式:(9)定义:为度速度,体现叶片的径向速度;为度加速度,影响叶片的径向惯性力;为度跳动,主要反映曲线振动作用以及影响噪音大小.在方程(9)中,a0~a6为设计变量.为了能够使曲线光滑且度跳动指标趋于极小,同时兼顾加速度等指标,给出以下优化方程:minW1|Jmax|+maxW2|amax|(10)式中:W1、W2为加权因子.因为凸轮泵转子的长短轴可知,从尽可能使最大度跳动值Jmax的角度出发,选取较大的W2和较小的W1值.根据图2的几何性质,给出以下的边界约束条件:依据式(11~13)边界条件通过计算机软件编程计算,得到最优解并导入到MATLAB 软件中,最终获得高阶曲线的理论曲线表达式.2 凸轮泵的数值模拟2.1 建立模型及划分网格因为压力角是转子型线方程的主要参数,此时选取压力角为45°,由于凸轮泵在实际工作过程中,两个转子间和转子与腔壁间是非接触的,在此所有模型间隙都设定为0.4 mm,各对应的参数见表1.表1 凸轮泵型线的参数Tab.1 Parameters of rotor profile of cam pump节圆半径R/mm压力角α/(°)基圆半径rj/mm齿顶、齿根圆半径r0/mm范围角β/(°)404524.3022.205在Pro/E中针对参数方程建立凸轮泵模型,并对进出口相应的延长处理,建立其三维模型后导入划分网格软件Gambit中.对整个凸轮泵模型划为三个部分,分别为凸轮泵的工作区、入口流道和出口流道.网格类型选用大部分为六面体(hex/wedge),划分方法选用非结构性网格(cooper),如图3所示.介质输入、输出端设定压力进出口,两个转子设定为墙壁(wall),为导入UDF后使两转子旋转做铺垫.图3 模型的网格图Fig.3 Model grid graph2.2 计算模型[11]根据凸轮泵的原理做出假设:流体是恒温的牛顿流体,具有不可压缩性,流体初始状态是静止的.基于上述假设,采用标准的k-ε模型,由于凸轮泵中的两个转子是随时间变化而进行同步转动,故在计算中采用的是动网格模型,动网格模型可以用来模拟由于流域边界运动引起流域形状随时间变化的流动情况,很适合此模型计算.2.3 数值计算方法根据凸轮泵的工作原理可知,泵内有两个相同的转子旋转而产生压力使介质运输到目的地.在Fluent中,应用湍流模型及动网格技术,并导入相对应的UDF使两个凸轮泵做同步反向旋转运动.设置泵的输入、输出端为压力进出口,初始条件都设定为一个标准大气压,保持出口压力不变.在计算过程中,采用非定常、隐式求解器,并应用标准的k-ε模型,对于求解器的控制采用PISO的压力-速度耦合形式,并使用二阶迎风格式,时间步长设为0.000 1.使用监测器对进出口的压力及流量进行监测,出口流量和入口压力都呈现稳定的周期性波动视为计算收敛.3 模拟计算结果在模拟计算中,针对优化后的凸轮泵模型(转子型线由渐开线-高阶曲线-圆弧组成)与初始模型(转子型线由渐开线-圆弧组成)进行比较分析.如图4所示,两种模型在达到稳定后,由于凸轮泵的结构限制,输出流量都出现周期性的“脉动”现象,但优化后的模型明显比初始模型“脉动”现象有所改善.这说明在转子型线中插入高阶曲线的方法可以提高凸轮泵的工作性能.图4 两种模型出口的流量脉动图Fig.4 Flow pulsation diagram at pump outlet for two models由于凸轮泵模型符合完全对称原则,随着两个转子的转动,压力分布会呈现瞬时相同,故在此只选用两个时间点进行分析.图5是50%叶片厚度的压力分布图,由图可以看出,在两个转子啮合的间隙处都产生较大的压力,并且在t=0.4 s时右转子与右侧的腔壁也产生较大的压力,这会使介质通过间隙发生泄漏现象,降低凸轮泵的工作效率. 针对优化后的模型在不同的转速的工况下进行分析,如图6所示.大约在0.2 s时,其出口平均流速达到基本稳定状态,随着凸轮泵转子转速的提高,出口的平均速度也随之上升,当转速高于14rad/s时,其出口的平均速度会呈现小波动现象.图5 不同时刻50%叶片厚度的压力分布图Fig.5 Pressure distribution diagram 50% blade from inlet to outlet along thickness at different times图6 不同转速在出口的平均输出速度Fig.6 Mean outlet velocity at different pump speeds4 试验4.1 试验原理与方法凸轮泵的动力源是由电机提供,并通过变速箱传递到转动轴上,叶片通过花键与转动轴连接,从而使两个转子进行同步反向的旋转.当两个转子做持续的旋转运动过程中,泵腔内会出现局部真空,这种现象的产生将在入口端把介质吸入到泵腔内,随着两转子的转动将介质增压并从出口处排出.根据在Pro/E软件中建立的三维模型生成数控加工程序,在工厂内加工出试验样机,并把试验样机安装在试验台上进行测试.由于凸轮泵在工作过程中有回流现象,故在介质的入口和出口的管道上都安装有单向阀,如图7所示.在出口端安装了压力表,可以监测输出介质的压力情况,而流量计可以对输出流量进行监测.图7 试验台原理图Fig.7 Schematic diagram of test rig4.2 试验结果对比监测结果如图8所示,由于模拟计算中没有考虑密封等因素,模拟值高于实验值也属于正常现象,也说明了模拟计算的正确性.图8 实验值与模拟值的对比Fig.8 Comparison between experimental and simulation results5 结论1) 在原有的渐开线-圆弧组成的凸轮泵转子型线的基础上提出了一种插入高阶曲线的优化方法,使高阶曲线衔接在渐开线和圆弧之间,有效的消除了“尖点”现象. 2) 优化后的模型在输出端所产生的流量“脉动”现象有所改善,并且在不同转速的工况下,随着转速的增大,凸轮泵的输出介质的平均速度也随之增大.3) 对优化后的凸轮泵进行样机试验,由于模拟过程中没有考虑到密封等因素,与实验结果产生一定的偏差,但变化趋势是相一致的,因此,建立模型和计算方法是可信的. 参考文献:[1] 张铁柱,张洪信,赵红.非接触式转子泵理论型线与实际型线设计 [J].机械工程学报,2002,38(11):152-155.[2] 唐善华.凸轮泵转子型线设计与性能分析 [J].武汉大学学报:工学版,2007,40(3):76-79.[3] 史庭足.罗茨鼓风机叶轮数学模型的建立 [J].林业机械与木工设备,2011,29(5):31-33.[4] TONG S H,YANG D C H.Rotor profiles synthesis for lobe pumps with given flow rate functions [J].Journal of Mechanical Design,2005,127:287-294.[5] 韩伟,朱登魁,敏政,等.离心式心脏内部流场数值模拟与分析 [J].兰州理工大学学报,2012,38(5):53-57.[6] 余志毅,刘影.叶片式混流泵气液两相非定常流动特性分析 [J].农业机械学报,2013,44(5):66-69.[7] 齐学义,汪玮华,郝连松.轴流泵水力模型内部流场数值模拟 [J].兰州理工大学学报,2012,38(4):51-54.[8] 张锴,翟俊霞,陈嘉南,等.微型齿轮泵内流场的动网格模拟和分析 [J].兰州理工大学学报,2011,37(1):45-49.[9] LITVIN F L,FENG P puterized design and generation of cycloidal gearings [J].Mech Mach Theory,1996,31(7):891-911.[10] LIU H C,TONG S H,YANG D C H.Trapping-free rotors for high-swalling lobe pumps [J].Journal of Mechanical Design,2000,122:536-542.[11] 江帆,黄鹏.Fluent高级应用与实例分析 [M].北京:清华大学出版社,2008:205-208.。
404_Excite TD扩展功能在滚子摇臂式配气机构分析中的应用_长城汽车_孙小伟等

Excite TD 扩展功能在滚子摇臂式配气机构分析中的应用孙小伟 陈孝培 高宏伟 关莹 刘刚(长城汽车股份有限公司动力研究院,河北 保定)摘 要:本文应用TD 软件的扩展功能分析滚子摇臂与气门的滑动速度、摇臂与气门接触应力以及液压间隙调节器支撑力角度,使滚子摇臂式配气机构的分析更加全面,避免出现设计风险。
关键词:配气机构;滚子摇臂;气门;相对滑动 主要软件:A VL EXCITE Timing Drive1. 前言Excite TD 在配气机构的设计分析中应用十分广泛,带有液压间隙调节器的滚子摇臂式配气机构在国内轿车发动机上的应用越来越多,每年都有运用TD 分析滚子摇臂式配气机构的论文发表,而应用TD 软件的扩展功能分析滚子摇臂与气门的滑动速度、摇臂与气门接触应力以及液压间隙调节器支撑力角度却没有论文提到。
2. 进、排气单阀系模型依据发动机的配气机构建立进、排气机构TD 单阀系模型,见图1。
图1 滚子摇臂式配气机构和TD 单阀系模型3.运用扩展功能进行配气机构布置的运动学分析图2 进、排气凸轮型线运动学进、排气凸轮型线和运动学速度、加速度如图2所示。
图7 液压间隙调节器支撑力从图6和图7可以看出,液压间隙调节器支撑力方向在允许范围以内,不会出现滚子摇臂脱离液压间隙调节器的问题,液压间隙调节器的侧向力和轴向力大小也满足要求,液压间隙调节器不会浮起。
4. 结语综上所述,通过TD 扩展功能分析,能避免出现滚子摇臂、气门及气门导管过度磨损、滚子摇臂脱离液压间隙调节器和液压间隙调节器浮起等问题。
参考文献[1] Excite TD 用户培训教程[2] Wang Chunshan, "Vavletrain Design", SAE paper 2005-01-1834r e s u l t a n t s u p .f o r c e F I F O (N)angle(deg)angle(deg)。
微型汽车发动机凸轮型线仿真优化设计及应用研究
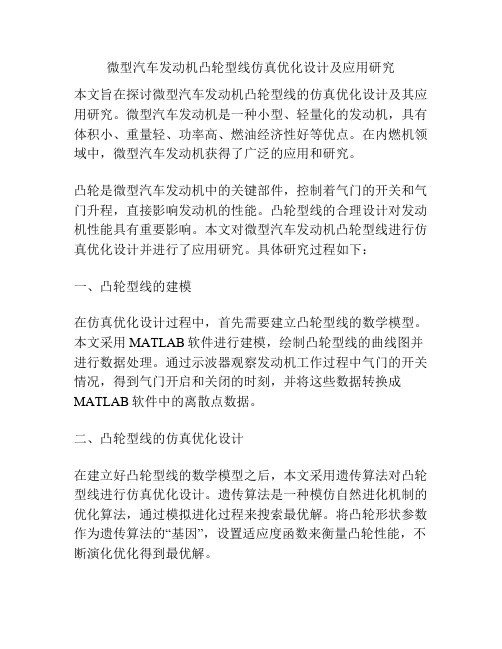
微型汽车发动机凸轮型线仿真优化设计及应用研究本文旨在探讨微型汽车发动机凸轮型线的仿真优化设计及其应用研究。
微型汽车发动机是一种小型、轻量化的发动机,具有体积小、重量轻、功率高、燃油经济性好等优点。
在内燃机领域中,微型汽车发动机获得了广泛的应用和研究。
凸轮是微型汽车发动机中的关键部件,控制着气门的开关和气门升程,直接影响发动机的性能。
凸轮型线的合理设计对发动机性能具有重要影响。
本文对微型汽车发动机凸轮型线进行仿真优化设计并进行了应用研究。
具体研究过程如下:一、凸轮型线的建模在仿真优化设计过程中,首先需要建立凸轮型线的数学模型。
本文采用MATLAB软件进行建模,绘制凸轮型线的曲线图并进行数据处理。
通过示波器观察发动机工作过程中气门的开关情况,得到气门开启和关闭的时刻,并将这些数据转换成MATLAB软件中的离散点数据。
二、凸轮型线的仿真优化设计在建立好凸轮型线的数学模型之后,本文采用遗传算法对凸轮型线进行仿真优化设计。
遗传算法是一种模仿自然进化机制的优化算法,通过模拟进化过程来搜索最优解。
将凸轮形状参数作为遗传算法的“基因”,设置适应度函数来衡量凸轮性能,不断演化优化得到最优解。
三、凸轮型线的应用研究通过仿真优化设计,本文得到了一组优化后的凸轮型线参数,再将这些参数应用于实际微型汽车发动机中,进行燃烧室压力测量和性能测试。
实验结果显示,优化后的凸轮型线可以明显提升发动机的输出功率和燃油经济性。
综上所述,通过对微型汽车发动机凸轮型线的仿真优化设计及应用研究,本文取得了一定的研究成果。
在未来的研究中,可以进一步探究凸轮型线的优化方案,并将其应用于更广泛的内燃机领域中,为内燃机的发展提供有价值的参考。
进一步探究凸轮型线的优化方案,可以从以下几个方面进行研究:一、不同工况下的凸轮型线优化不同工况下发动机对凸轮型线的要求不同,因此凸轮型线的优化也需要根据不同工况进行制定。
比如,在高速运转状态下,发动机需要更高的输出功率,因此凸轮型线的参数需要针对高负荷、高转速的要求进行优化。
- 1、下载文档前请自行甄别文档内容的完整性,平台不提供额外的编辑、内容补充、找答案等附加服务。
- 2、"仅部分预览"的文档,不可在线预览部分如存在完整性等问题,可反馈申请退款(可完整预览的文档不适用该条件!)。
- 3、如文档侵犯您的权益,请联系客服反馈,我们会尽快为您处理(人工客服工作时间:9:00-18:30)。
滚子摇臂式配气机构凸轮型线的改进设计
孙小伟
(长城汽车股份有限公司动力研究院,河北保定)
摘要:某款发动机在NVH测试中发现气门咔哒声明显,通过对原凸轮型线进行动力学分析,查出气门提前落座,通过改进缓冲段设计,避免了气门提前落座,减小了气门落座速度和落座力,改善了发动机的声品质。
关键词:凸轮型线;缓冲段
主要软件:A VL EXCITE Timing Drive
1. 前言
凸轮型线的设计不仅影响发动机热力学性能,也关系到配气机构工作的可靠性,更对配气机构的振动噪声起到重要影响。
带有液压间隙调节器的滚子摇臂式配气机构在国内轿车发动机上的应用越来越广泛,分析该配气机构的特点设计合理的凸轮型线十分必要。
2. 进、排气单阀系模型
依据发动机的配气机构建立进、排气机构TD单阀系模型,见图1。
图1 滚子摇臂式配气机构和TD单阀系模型
3. 原凸轮型线设计校对
图2 原设计的进气门动力学计算结果
图2的气门升程对比图中绿色的线是气门静升程曲线,红色的线是动升程曲线,从放大的气门升程图可以看出在理论升程0.109mm时进气门关闭,而原设计的关闭侧缓冲段高度只有0.05mm,说明进气门提前落座。
气门落座速度为0.73m/s,气门落座力为1200N。
图3原设计的排气门动力学计算结果
图3的气门升程对比图中绿色的线是气门静升程曲线,红色的线是动升程曲线,从放大的气门升程图可以看出在理论升程0.147mm时排气门关闭,而原设计的关闭侧缓冲段高度只有0.05mm,说明排气门提前落座。
气门落座速度为0.83m/s,气门落座力为1634N。
3.改进凸轮型线的运动学及动力学分析
3.1运动学分析
新设计的进、排气凸轮型线和运动学速度、加速度如图4和图5所示,图中的Curve1(虚线)为原设计的气门升程曲线。
图4 进气凸轮运动学
图5 排气凸轮运动学
经运动学分析,弹簧裕度、跃度、丰满度和K系数均满足要求。
3.2 动力学分析
图6和图7中图片左侧是6000rpm的动力学结果,右侧是6600rpm的动力学结果。
上面的图红色的线是动力学气门升程曲线,从中可以看出气门均无反跳发生;绿色的线是气门运动速度曲线,从中可以看出气门的落座速度均小于0.3m/s;蓝色的线是气门落座力曲线,从中可以看出气门落座力均小于500N,小于六倍的气门弹簧预紧力。
下面的图红色的线是凸轮接触力曲线,从中可以看出凸轮接触力始终大于零,说明没有出现气门飞脱现象;绿色的线是气门加速度曲线,从中可以看出气门加速度没有出现太大的阶跃。
图6 进气动力学
图7 排气动力学
4. 试验验证
图8 噪声测试结果
经过对凸轮型线改进前后噪声测试对比发现,优化凸轮型线后,发动机顶面噪声明显降低,主要为500Hz~2000Hz 中心频率降低明显,发动机顶面咔哒声有明显改善,降低了整机噪声。
5. 结语
通过EXCITE TD分析出原凸轮型线设计不能满足NVH要求,优化设计的凸轮型线改善了发动机声品质,降低了整机噪声。
参考文献
[1] Excite TD用户培训教程
[2] Seon-Yang Hwang, Koo-Tae Kang, Byung-Soo Lim and Yoon-Soo Lim, "Noise Reduction and Sound Quality Improvement of Valve Train in V6 Gasoline Engine", SAE paper 2005-01-1834
[3] Robert L. Norton, David Eovaldi, James Westbrook III and Ronald L. Stene, "Effect of Valve-Cam Ramps on Valve Train Dynamics", SAE paper 1999-01-0801。