如何填写5why表
五WHY分析法

02 5WHY的实施步骤
正确案例分析
正确案例分析
02 5WHY的实施步骤
案例1-杰弗逊纪念馆
杰弗逊纪念馆墙面破 损情况很严重
why
经常用化学性质很强烈 的清洗液对其进行清洗
why why
为了清除大量的鸟粪
被黄昏的灯光所吸引 why
3-why 为什么不知道手册规定?
依据上一年的报告为模板来写的
4-why 为什么模板与手册不符? 模板中没有手册依据和控制项
5-why 为什么没有手册依据和控制项?
模板的管理没有相应的规范
04 5WHY演示
步骤3、制定对策
短期措施: 修订2014年福州机务部安全质量分析“事件汇报材料,增加手册中的相关 要求内容。 长期措施: 制定模板管理规范,包括在模板中必须有填写手册依据及符合性的页面。
系统为什么 没防住?
为什么?
教训:
根源
为什么? 为什么? 为什么?
为什么? 为什么? 为什么?
为什么? 为什么? 为什么?
纠正措施
日期
A
A
B
B
CC
02 5WHY的实施步骤
第2步的要点
怎么问问题很重要! 原则:导向可控的解决方案
02 5WHY的实施步骤
错误案例分析
02 5WHY的实施步骤
案例:由一个人摔跤引出的故事
五WHY分析法
目录
: contents sub title : contents sub title
01 / 5WHY简介 02 / 实施步骤 03 / 5WHY练习 04 / 5WHY演示 05 / 5WHY注意事项
5why分析表格式
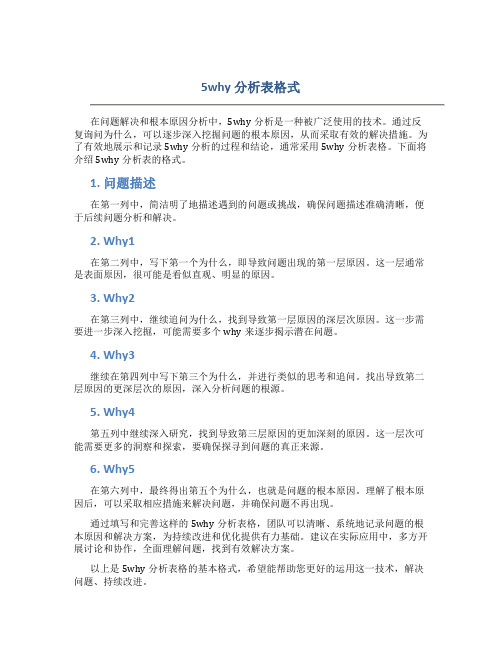
5why分析表格式在问题解决和根本原因分析中,5why分析是一种被广泛使用的技术。
通过反复询问为什么,可以逐步深入挖掘问题的根本原因,从而采取有效的解决措施。
为了有效地展示和记录5why分析的过程和结论,通常采用5why分析表格。
下面将介绍5why分析表的格式。
1. 问题描述在第一列中,简洁明了地描述遇到的问题或挑战,确保问题描述准确清晰,便于后续问题分析和解决。
2. Why1在第二列中,写下第一个为什么,即导致问题出现的第一层原因。
这一层通常是表面原因,很可能是看似直观、明显的原因。
3. Why2在第三列中,继续追问为什么,找到导致第一层原因的深层次原因。
这一步需要进一步深入挖掘,可能需要多个why来逐步揭示潜在问题。
4. Why3继续在第四列中写下第三个为什么,并进行类似的思考和追问。
找出导致第二层原因的更深层次的原因,深入分析问题的根源。
5. Why4第五列中继续深入研究,找到导致第三层原因的更加深刻的原因。
这一层次可能需要更多的洞察和探索,要确保探寻到问题的真正来源。
6. Why5在第六列中,最终得出第五个为什么,也就是问题的根本原因。
理解了根本原因后,可以采取相应措施来解决问题,并确保问题不再出现。
通过填写和完善这样的5why分析表格,团队可以清晰、系统地记录问题的根本原因和解决方案,为持续改进和优化提供有力基础。
建议在实际应用中,多方开展讨论和协作,全面理解问题,找到有效解决方案。
以上是5why分析表格的基本格式,希望能帮助您更好的运用这一技术,解决问题、持续改进。
在实际使用5why分析表格时,请确保问题描述确切、逻辑清晰,每一步why 都要有有力合理的解释。
这样才能有效利用5why分析技术,找准问题根本,做出有效改进。
以上是5why分析表格格式的基本介绍,希望对您有所帮助。
祝您工作顺利!。
5Why分析表(案例)

XX电子有限公司5Why分析表(案例)产品名称A型针车型问题描述针变形分析日期2018.3.9 不良数量55000PCS/180PCS/4PCS 不良率 2.2000% 发生场所进料检验生产批号2018.3.2a.过程工艺、检验、零部件状况追踪检查说明1、是否遵循SOP的工艺条件、作业流程?☐是□否 4、是否使用了经验证合格的零件?☐是□否2、是否使用正确的设备(含条件)及工具?☐是□否 5、技术规范是否符合、验证且培训?☐是□否3、人员是否培训并鉴定?□是☐否6、生产期间的环境状况是否有区别?□是☐否7、运输包装是否符合标准书要求?☐是□否 8、其它,说明:说明:进行5WHY分析时,参与人员应尽量全面,如设计开发、工程(生产技术)、生产、品保、采购、业务、班组长、作业人员;过程中应采取开放式的以事实为原则,并结合采用脑力激荡法等方式进行。
b、根本原因分析(5个为什么):发生原因:第1个为什么?直接原因①为什么会发生电镀变形答:电镀卡槽内卡住撞击变形流出原因:第1个为什么?直接原因①为什么OQC没有管控到答:未尽职责第2个为什么?直接原因②为什么品质监控没有终止不良发生答:已发现不良实行全检,未能追踪第2个为什么?直接原因②为什么全检员工没有管控到答:技术培训不达标第3个为什么?直接原因③为什么电镀之后发现问题不能完全解决答全检过程中QC没能对全检之后的产品进行仔细抽检第3个为什么?直接原因③为什么发现不良没有严格管控答:监督不足第4个为什么?直接原因④为什么决定全检还不能控制不良答:控制不到位,OQC没能管控到第4个为什么?直接原因④为什么新进员工对产品认知不够规范答:经验不足第5个为什么?根本原因⑤为什么QC未跟踪追查不良答:不够细心第5个为什么?根本原因⑤为什么发现问题对策不够彻底答:包装人员不够认真负责c、问题点无法再现,根本原因查找1、现品分析(可采用环境试验、老化验证、模拟试验、客户或供应商场所验证、对手件上试验、实车验证等):机器运行正常,生产模具一次成型下落不会发生变形,电镀之后发现不良变形。
5 Why 标准模板
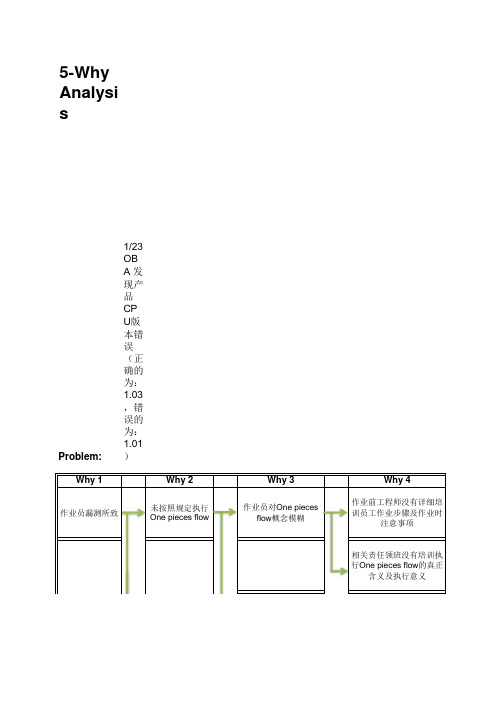
5-Why AnalysisProblem:1/23 OBA 发现产品CPU版本错误(正确的为:1.03,错误的为:1.01)Why 1Why 2Why 3Why 4作业员漏测所致未按照规定执行One pieces flow作业员对One piecesflow概念模糊作业前工程师没有详细培训员工作业步骤及作业时注意事项相关责任领班没有培训执行One pieces flow的真正含义及执行意义产品积压过多,导致升级OK产品与没有升级的产品混在了一起.临时接到客户通知,升级F/W。
工程师要求off lineupdate F/W(测试OK,待包装状态的产品)TCN中没有明确作业流程PE未提供测试流程的TCNPE认为TE的TCN中已经对流程作出说明;TE认为作业流程需要PE提供;PD没有检查确认包装站别产品上传时没有发现版本错误产品上传时,只要求对比ATIS&CSM是否一致TE W/I中没有要求检查确认软件版本信息的内容Why 5Root Cause Recurrence Prevention Status工程师认为作业步骤简单,无需在做更加详尽的培训工程师的自我假定,导致同作业员的交流不充分。
相关部门工程师制订的TCN,备注或培训时,着重强调作业步骤及作业时的注意事项。
Owner:TomClose我们高估作业员的理解能力,认为全部掌握,无需解释执行的意义我们的自我意识,没有同作业员做更加详尽的交流。
班会或培训时,我们要站在作业员的角度去理解问题;并适时的提问,让作业员真正理解培训内容。
Owner:TomClose出货紧急,作业员偏向了产量,而未对品质要求上面注意作业分配上面不充足,先期策划没有做好。
制定计划,协调资源,实施《重工排配表》。
做好先期准备工作,明确分工后方可开始作业。
Owner:TomCloseTE的TCN中只是阐述了测试步骤,没有作业流程;我们认为TE已经提供TCN,PE无需再作提供部门之间缺乏交流,没有明确责任分工。
PSG(问题解决小组)5why分析标准表格

P D C A
A P C D
1 2 3 4 5 6 7
A P C D A P C DA P C DA P C D A P C D
A P C D
KPI 数据追踪
PSG
PROBLEM SOLVING GROUP
计划:问题定义,验证原因,确定解决方案(解决方案是什么,什 么时间做,谁来做) 检验:在实施后进行检验,如果问题点不在发生,则说明这个解决 方案是有效的
开始日期 : 机器 : Page 2
解决方案
做:行动执行,解决方案的执行
推行:及时生效执行(约2周内)将解决方案推广的其他区域
日期确认 N° 日期 原因 解决方案 /行动 预计完成时间 实际完成时间
备注
P D C A
A P C D
1
2
A P C D
3
A P C D
4
A P C D
5
A P C D
6
A P C D
7
A P C D
8
A P C D
9
A P C D
长期解决方案
日期确认 N° 日期 原因 解决方案 /行动 预计完成时间 实际完成时间
5WHY分析报告模板

品番
御中
MB80-13-C1251A
様
品名
5WHY分析报告书
拉杆螺母
)
发生日期
2月1日
现品区分
试作品
量产品
不 寸法 外观 性能 形状 不良分类 他( 良 信 不适合内容 息 拉杆配装后,MA寸法NG,低于15.3的下限,导致装配NG
在库品处理方案: 全数选别
1.工序步聚表述(对发生及流出工序用红色单独标出):
重新设计冲棒
冲棒未实施寿命管理
内牙纹端面2-3个牙磨损 严重
对冲棒实施寿命 管理 重新设计冲棒
设计不合理
——
——
禁止二次回牙
完成日期 3月25日 3月25日 3月25日 3-1始
担当部门 安拓 安拓 高岛+安拓 高岛+安拓
改善确认 已完成 已完成 已完成 实施继续
备注
改 善 对 策
1 2 3 4
进料——冷打成型——攻牙——电镀——外观检查——包装——出货
2.5WHY分析 序号 原 因 分 析 拉杆组装后, MA寸法NG 不适合现象 1WHY 2WHY 根本原因 3WHY 4WHY 的冲棒直径设计 打导角的冲棒外径偏大 超出上限 不合理 组装后,拉杆拧入螺母 部分过深 1 产品在冷打成型时,打 导角的冲棒磨损 攻牙时排铁屑不顺畅 端面倒角角度过小 先前为镀镍,改为镀锌 内牙纹磨损,导致小径 该批次产品实施了2次回 而实施了退镀,酸洗时 偏大 牙 选成牙损伤 序号 改善对策 修正冲棒设计图纸,将冲棒直径由¢11.0修改为¢10.5 修正冲棒设计图纸,将冲棒角度由100°修改为 110°。 指导供应商对冲棒模具、攻牙用的丝锥实施使用寿命管理。建立使用寿命管理的规范。 绝对禁止2次回牙
有效的管理工具之一----5WHY
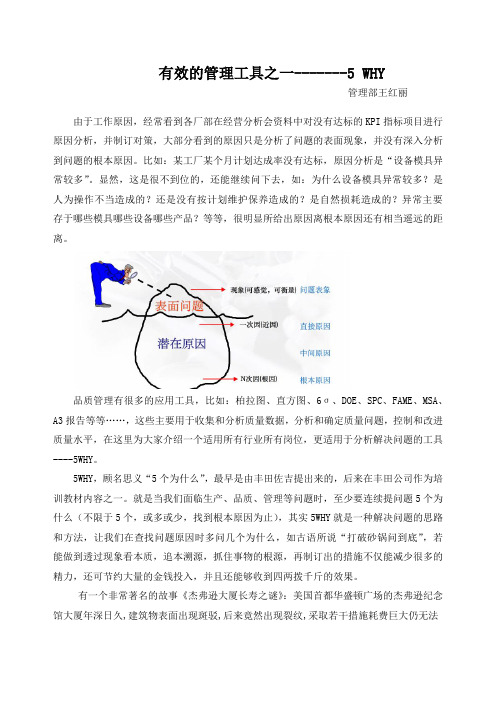
有效的管理工具之一-------5 WHY管理部王红丽由于工作原因,经常看到各厂部在经营分析会资料中对没有达标的KPI指标项目进行原因分析,并制订对策,大部分看到的原因只是分析了问题的表面现象,并没有深入分析到问题的根本原因。
比如:某工厂某个月计划达成率没有达标,原因分析是“设备模具异常较多”。
显然,这是很不到位的,还能继续问下去,如:为什么设备模具异常较多?是人为操作不当造成的?还是没有按计划维护保养造成的?是自然损耗造成的?异常主要存于哪些模具哪些设备哪些产品?等等,很明显所给出原因离根本原因还有相当遥远的距离。
品质管理有很多的应用工具,比如:柏拉图、直方图、6σ、DOE、SPC、FAME、MSA、A3报告等等……,这些主要用于收集和分析质量数据,分析和确定质量问题,控制和改进质量水平,在这里为大家介绍一个适用所有行业所有岗位,更适用于分析解决问题的工具----5WHY。
5WHY,顾名思义“5个为什么”,最早是由丰田佐吉提出来的,后来在丰田公司作为培训教材内容之一。
就是当我们面临生产、品质、管理等问题时,至少要连续提问题5个为什么(不限于5个,或多或少,找到根本原因为止),其实5WHY就是一种解决问题的思路和方法,让我们在查找问题原因时多问几个为什么,如古语所说“打破砂锅问到底”,若能做到透过现象看本质,追本溯源,抓住事物的根源,再制订出的措施不仅能减少很多的精力,还可节约大量的金钱投入,并且还能够收到四两拨千斤的效果。
有一个非常著名的故事《杰弗逊大厦长寿之谜》:美国首都华盛顿广场的杰弗逊纪念馆大厦年深日久,建筑物表面出现斑驳,后来竟然出现裂纹,采取若干措施耗费巨大仍无法遏止。
政府非常担忧,派专家们调查原因,拿出办法。
后来报告交上来写明调查结果:最初以为蚀损建筑物的原因是酸雨。
研究表明,原因是冲洗墙壁所含的清洁剂对建筑物有酸蚀的作用,而该大厦墙壁每日被冲洗,大大频于其他建筑,受酸蚀损害严重。
5W(5个为什么)分析报告表 模板
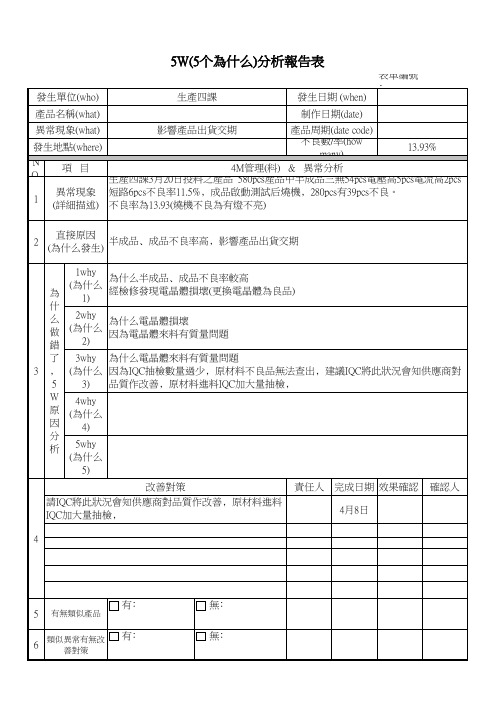
什
么 做 錯
2why (為什么
2)
為什么電晶體損壞 因為電晶體來料有質量問題
了 3why 為什么電晶體來料有質量問題
3 ﹐ (為什么 因為IQC抽檢數量過少﹐原材料不良品無法查出﹐建議IQC將此狀況會知供應商對
5
3) 品質作改善﹐原材料進料IQC加大量抽檢﹐
W 4why 原 (為什么 因 4) 分 析 5why
1
異常現象 短路6pcs不良率11.5%﹐成品啟動測試后燒機﹐280pcs有39pcs不良。 (詳細描述) 不良率為13.93(燒機不良為有燈不亮)
2
直接原因 (為什么發生)
半成品﹑成品不良率高﹐影響產品出貨交期
為
1why (為什么
1)
為什么半成品﹑成品不良率較高 經檢修發現電晶體損壞(更換電晶體為良品)
(為什么
5)
改善對策
責任人 完成日期 效果確認 確認人
請IQC將此狀況會知供應商對品質作改善﹐原材料進料 IQC加大量抽檢﹐
4月8日
4
5 有無類似產品
6
類似異常有無改 善對策
有﹕ 有﹕
無﹕ 無﹕
核准﹕
審核﹕
制表﹕
發生單位(who)
5W(5个為什么)分析報告表
生產四課
發生日期 (when)
表單編號 ﹕
產品名稱(what)
制作日期(date)
異常現象(what)
影響產品出貨交期
產品周期(date code)
發生地點(where)
不良數/率(how many)
13.93%
N
項目
4M管理(料) & 異常分析
生產四課3月20日投料之產品 580pcs產品中半成品三無54pcs電壓高5pcs電流高2pcs
- 1、下载文档前请自行甄别文档内容的完整性,平台不提供额外的编辑、内容补充、找答案等附加服务。
- 2、"仅部分预览"的文档,不可在线预览部分如存在完整性等问题,可反馈申请退款(可完整预览的文档不适用该条件!)。
- 3、如文档侵犯您的权益,请联系客服反馈,我们会尽快为您处理(人工客服工作时间:9:00-18:30)。
第二步:测量- 信息与相关数据
测量注意遵循“3个真 实”— 真实地点 真实事物 真实事情
如何使用鱼骨图展开分析
1.召集相关人员,采用头脑风暴法列出所有可能的人、机、物、环(以及方法) 等方面的因素; 2.通过测量的数据逐个排除问题原因,使用×或√来注释非问题原因和可能的问题
文件编号:FM-WCM-FI-001/A 最新生效日期:2011/05/31
认识5why表
1.表格是否是文控中心的正式表格: 文件编号和生效日期. 2.表格包含内容: a. 日期、 b. 生产线 c. 岗位 d. 参加人员、 e. 问题定义、 f. 测量数据、 g. 鱼骨图分析、 h. 根本原因分析、 i. 根本问题解决方案、 j. 控制、 k. 行动措施表、 l. 输出的控制措施、 m. 最后的团队领导审核 n. 确认合格表格的确认人签名。
解决措施和方案是什么 ?
跟进行动 序号 1 任务描述 更新维修策略 责任人 张工 完成时间 6 月15 日 结果
注意紧凑的3步:根本原因→设定问题解决方案→现场未 能解决的问题设定跟进行动表-改善效果。
如何输出控制?
步骤五:控制措施
详细描述预防故 障再次发生的预 防措施 必须附上OPL或 培训记录, SOP,WI文件, Troble shooting, 防呆装置照片
原因,对可能的原因需要进一步测量得出更多的信息后再次排出非问题原因。 3.一般情况下最后的根本原因会有1~3项,如果过多原因则建议不要使用5why形式来 分析解决问题,可以需求更多资源解决。 4.将选出的1~3个原因使用5why法分析!
如何问5个why?
1 ,原因一 M512 轴承磨损 为什么:轴承内没油了。 为什么:轴封已破损。 为什么:轴封已使用3 年未进行检查。 为什么:维修策略未要求检查此轴封。 为什么:
FI Champion审核合 格后提交文控中心登 记后返还给TF FI负责 人。
常见使用5why表的问题
使用非正式受控格式的表格! 问题定义不清晰! 测量数据太简单,导致无法后续分析! 鱼骨图分析的原因太简单,甚至个别出现直接跳 到结论! 5个why的上下层逻辑不对,根本原因分析错误。 根本原因已分析出来但未有相应的控制改善措施 最后没有输出的预防控制措施,或只是简单的培 训来应付!
1.每个原因均需要逐层问到根本的原因是什么? 2.下一个“为什么”应当是上个“为什么”的直接原因。 3.注意避免上下层的逻辑性不合理,和根本原因未分析出来就直接定 论了!
跟进改善!
根本原因:维修策略未要求检查此轴封。 步骤四:问题解决方案: (图或者描述) 1. 更新维修策略,增加对此类轴封每2 月检查的要求
日期:
a
5WHY问题解决表
生产线:
1
b
岗位:
c
参加人员: 根本原因代码:
d
故障MSI代码: 第一步:问题定义 事情描述: 发生地点: 发生时间: 相关人员: 趋势情况: 严重性: 第三步:分析和找到根本原因
第二步:测量-信息与相关数据
e
测量
f
机器
人员
g
物料
1,原因一 为什么: 为什么: 为什么: 为什么: 为什么: 根本原因: 步骤四:问题解决方案: (图表或者描述) 步骤五:控制-确认 (改善结果)
PM工程师必须要 确认,必须填入 “维修计划号”。
预防重复性发生的措施(附正式措施文件): 吃一堑,长一智OPL SOP 培训 防呆措施 Pokayoke 文件修订
最终检查在设定的完 成期限内是否按照 “跟进行动表”要求 输出了控制的有效措 施!
故障维修图示 维修策略 此项目关闭
最后的审核和确认
区域TF FI负责人对此改 善的措施进行审核,确认 以上全部工作按要求执行。 然后提交纸质版材料给工 厂FI Champion进行确认。
5Why触发
按照各区域设定的5WHY出发 值,触发5why 出发值就需写 5WHY分析.
每个班超过各机台每班 触发时间如左图所示, 需要书写5Why表 每个机台每小时超过触 发值如右图所示时间, 需要写5Why表
可口可乐装瓶商生产(佛山)有限公司 Coca-Cola Bottlers Manufacturing(Foshan)Company 为什么:
h
为什么: 为什么: 为什么:
i
跟进行动 序号 任务描述 责任人 完成时间 结果
j
预防重复性发生的措施: 吃一堑,长一智O P L 培训 防呆措施 Pokayoke 文件修订 SOP 故障维修图示 维修策略
k
复核人:
l n
m
此项目关闭 审批人:
如何定义和测量?
第一步:问题定义 事情描述: 发生地点: 当什么时候发生: 相关人员: 趋势情况: 严重性: