转炉设计
120T炼钢转炉设计 (2)
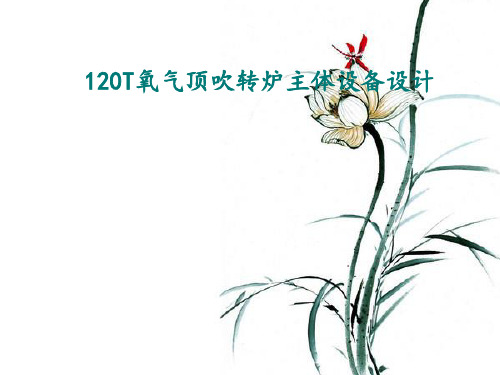
5.造渣制度
石灰加入量的计算公式 : Q=2.2([Si%]铁水+[P%])×R/(CaO%)有效 ×W铁水×1000 式中:Q—石灰加入量(㎏/炉);[Si%]铁水—为铁水硅成分;R—炉渣 碱度; W—铁水量(t);(CaO%)有效—石灰有效CaO含量;(CaO%)有 效=石灰CaO%-R×石灰SiO2%。 终渣碱度要求控制在2.6~3.5,具体数值取决于钢种对终点P、S含量的 要求、入炉铁水处理工艺、装入制度和操作工艺。碱度要求按照《钢种 生产技术操作标准》。 采用分批加入的操作工艺,一般第一批渣料在开吹的同时加入,加入量 为总量的2/3,第二批料在前期渣化好后分批加入,视化渣情况,在4~7 分钟内加完。
钢水
倒炉出钢 前
测温管
插入钢水 400~ 500mm,时 间 5s 均匀
MgO、P2O5、 FeO、TFe等
根据需要
渣
第一次倒 炉出钢前
样勺
CaO、SiO2、 根据需要
钢水
第一次倒 炉出钢前
样勺
稳、准、 快、满、 盖
C、S、P、 Mn
所有非用 副枪取样 的炉次
10.溅渣护炉示意图
溅渣护炉
吹炼前期随第一批料加入轻烧白云石
根据供氧压力、供氧流量、纯吹时间,
8.脱氧合金化
合金加入量(kg)=目
标成分%—钢水残余成 分%/合金成分%×合金 收得率% ×钢水量(㎏/ 炉) 出钢到1/4时开始陆续加 入合金,3/4时应加完 合金应加在钢流上。
脱氧合金示意图
9.测温取样
取样类型 取样时间 取样、测 温方式 取样、测 温要求 分析元素 取样频率
6.温度制度
① ②
转炉炉衬设计

炉炉型和炉衬设计转炉炉型和炉衬设计(design of conveter furnace outline and lining) 确定适合于转炉炉容量和操作条件的转炉炉型和各部位炉衬材质的设计。
是转炉炼钢车间设计的主要组成部分。
转炉炉型设计转炉炉型是指新砌成的转炉炉衬的内腔形状和尺寸。
氧气转炉的炉型通常是先用统计公式计算出转炉各部位的主要尺寸,然后再与炉容量相近、条件相似的实际生产转炉进行比较和调整后确定的。
氧气转炉炉型绝大多数是轴对称回转体结构,由截锥型炉帽(仅有少数转炉呈偏口形)、圆柱形炉身和不同形状的炉底三部分组成。
按转炉熔池形状不同,常见的炉型有筒球型、锥球型和截锥型三种(见图)。
筒球型炉型形状简单,砌筑方便,炉壳制造容易,大容量转炉采用较多。
锥球型炉型与相同容量的筒球型炉相比,在熔池深度相同的情况下,更有利于冶金反应;截锥型炉型的优点是炉底砌筑方便,这两种炉型在中小容量转炉炉型设计中采用较多。
对氧气转炉炉型的主要技术参数要求为:(1)炉容比(工作容积与公称容量之比)与铁水条件、冶炼操作转zhuan方法和转炉炉容量有关,通常每公称吨炉容比为0.80~1.00m3/t;(2)高宽比(炉子全高与炉壳直径之比)对转炉操作和建设费用有直接影响,一般取为1.25~1.65;(3)炉帽的倾角为60o±3。
;(4)炉口直径一般为熔池直径的0.43~0.53倍;(5)熔池直径系指转炉熔池在平静状态时金属液面的直径,它与转炉装入量和供氧强度有关,可按D=K(G/T)1/2进行计算,式中D为熔池直径,m;K为比例常数,一般为1.85~2.3;G为转炉装入量,t;T为转炉供氧时间,min。
炉衬耐火材料选择转炉炉衬分为工作层、填充层和永久层。
工作层衬砖与熔池钢水和熔渣接触工作条件十分恶劣,要求有良好的物理性能和化学稳定性,同时也要有较低的价格。
转炉工作层衬砖常采用焦油白云石砖、焦油镁砂砖、镁碳砖和二步煅烧砖,镁碳砖应用较广泛。
120t转炉尺寸设计
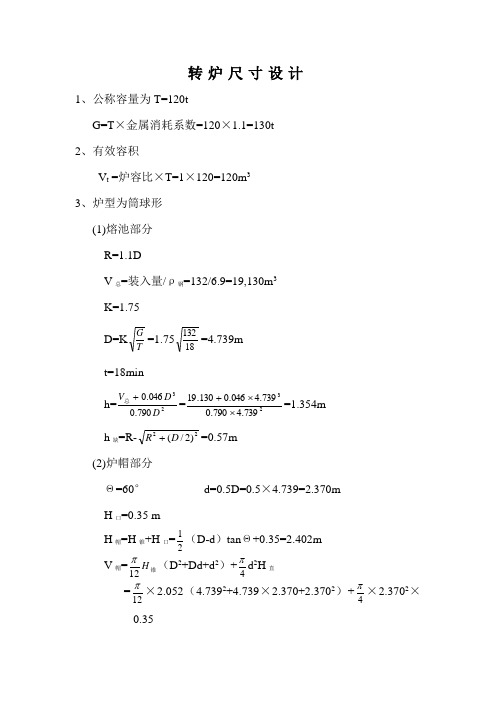
转炉尺寸设计1、公称容量为T=120tG=T ×金属消耗系数=120×1.1=130t 2、有效容积V t =炉容比×T=1×120=120m 3 3、炉型为筒球形 (1)熔池部分R=1.1DV 总=装入量/ρ钢=132/6.9=19,130m 3 K=1.75D=KT G =1.7518132=4.739m t=18min h=23790.0046.0D D V +总=23739.4790.0739.4046.0130.19⨯⨯+=1.354m h 缺=R-22)2/(D R +=0.57m (2)炉帽部分Θ=60° d=0.5D=0.5×4.739=2.370mH 口=0.35 mH 帽=H 锥+H 口=21(D-d )tan Θ+0.35=2.402mV 帽=锥H 12π(D 2+Dd+d 2)+4πd 2H 直 =12π×2.052(4.7392+4.739×2.370+2.3702)+4π×2.3702×0.35=22.646m 3 (3)炉身部分V 身=V 总-V 帽-V 池=120-22.646-19.130=78.224m 3 H 身=2D 4π身V =2739.414.3224.6784⨯⨯=4.437m 3(4)出钢口 α=20°d 出=T 75.163+=16.523cm (5)炉衬厚度H 总=H 帽+H 身+h+H 底=2.402+4.437+1.354+1.140 =9.333mD 壳=D+2×(炉身炉衬厚度)=4.739+2×(980/100)=6.699m H 总/D 壳=9.333/6.699=1.39氧气转炉车间设计一、 车间生产能力转炉座数为三座,采用三吹三。
根据客户要求产量选取为120t 。
(1)每座转炉年出钢炉数 N=121400T T =13651400T η⨯=368.03651400⨯⨯=11680炉T1—--平均每炉钢冶炼时间 T2—--一年有效作业天数 1400—一天的日历时间min η----转炉作业率,约75%-80% (2)年产钢量W=nNq=3×11680×120=4204800t W----车间年产钢水量t n----经常吹炼转炉数 N----每座转炉年出钢炉数 q----公称容量t 三、车间类型选择中型车间(由产量决定)高架式(为了节省劳动力,提高利用率) 多跨式二、 多跨车间的工艺布置依次为:加料跨、转炉跨、精炼及铁水接受跨、连铸跨、出坯跨,这样可保证物料运输距离短,物流顺畅,相互干扰少。
140T_转炉炉型设计

1 40T 转炉炉型设计序言现在钢铁联合企业包括炼铁,炼钢,轧钢三大主要生产厂。
炼钢厂那么起着承上启下的作用,它既是高炉所生产铁水的用户,又是供应轧钢厂坯料的基地,炼钢车间的成产正常与否,对整个钢铁联合企业有着重大影响。
目前,氧气转炉炼钢设备的大型化,生产的连续化和高速化,到达了很高的生产率,这就需要足够的设备来共同完成,而这些设备的布置和车间各种物料的运输流程必须合理,才能够使生产顺利进展。
转炉是炼钢车间的核心设备,设计一座炉型合理满足工艺需求的转炉是保证车间正常生产的前提,而炉型设计又是整个转炉设计的关键。
140T 转炉炉型设计1 炉型设计步骤(1) 列出原始条件:公称容量,铁水条件。
废钢比,氧枪类型以及吹氧时间等。
(2) 根据条件选炉型(3) 确定炉容比(4) 计算熔池直径,熔池深度等尺寸(5) 计算炉帽尺寸(6) 计算炉身尺寸(7) 计算出钢口尺寸(8) 确定炉衬厚度(9) 确定炉壳厚度(10) 校核H/D(11) 绘制炉型图2 炉型设计与计算2.1 本次设计任务:设计140T 转炉炉型(1) 原始条件炉子平均出钢量为140t , 钢水收得率为92% ,最大废钢比取20% ,采用废钢矿石法冷却。
铁水采用低磷生铁[W(si)≤0.85%,W(F)≤0.2% W(5)≤0.05%] ; 氧枪采用三孔拉瓦尔型喷头,设计氧压为1.0mpa(2) 炉型选择根据原始条件采用筒球形炉型作为此次设计的转炉炉型(3) 炉容比,取V/T=0.9892.2 炉型尺寸的计算(1) 熔池尺寸的计算①熔池直径计算:计算公式: D=k (G/t) 1/2熔池直径式中:K—常数,取1.57 ;G—金属装入量,t ;T—吹氧时间,min 。
a: 确定初期金属装入量为GG=2T/2+B*1/2式中:T——平均出钢量为,140t ;B——常数,取15% ;η金——金属收得率为92% ;G=2×140/2+15%*1/92%=141.557(t)V金=G/ρ金=141.557/6.8=20.817(m3)B: 确定吹氧时间:根据生产实践,吨钢耗氧量一般低磷铁水约为50~57 那么供氧强度=吨钢耗氧量/吹氧时间=57/14=14[m3/(t*min)] D=1.57(141.557/14)1/2=4.99m熔炉深度计算筒球型熔池深度的计算公式为:h熔=V金+0.046D3/0.79D2=20.817+0.046*4.993/0.79*4.992=1.35m 熔池其他尺寸确实定球冠的弓形高度:h1=0.15D=0.15×4.99=4.54m球冠的曲率半径:R=0.91×D=0.15×4.99=4.54m2.3 炉帽尺寸确实定(1) 炉口直径d0:d0=0.48D=0.48×4.99=2.4m(2) 炉帽倾角θ 取64° ;(3) 炉帽高度(H 帽)式中:H o——炉口高度,取0.4m在炉口设置水箱式水冷炉口2.4 炉身尺寸确定(1) 炉膛直径( 无加厚段)(2) 根据选定的炉容比为0.989 ,可求出炉子总容积为炉身高度:那么炉型高:2.5 出钢口尺寸计算(1) 出钢口直径:(2) 出钢口衬砖外径d r=63+1.7571/2=(6+1.75*140)1/2=17.5CM=0.175m(3) 出钢口长度d T' =6d T=6*17.5=105cm=1.05m(4) 出钢口倾角β取18°L T=T dT=7×17.5=122.5cm=1.225m符合高宽比的推荐值,因此认为所涉及的炉子尺寸是根本适宜的。
出钢量为60t转炉设计

转炉设计冶金工程课程设计任务书1 设计题目:转炉设计2已知条件:炉子平均出钢量为60t,钢水收得率取94%,最大废钢比取18%,采用废钢矿石法冷却:铁水采用P08低磷生铁[ω(Si)≦0.85%]ω(P)≦0.2%ω(S)≦0.05%],氧枪采用四孔拉瓦尔喷头,设计氧压为1.0MPa。
3设计内容及要求:(1)确定炉型和炉容比(2)计算熔池尺寸、炉帽尺寸、炉身尺寸、出钢口尺寸、炉衬厚度及炉壳厚度(3)绘制转炉炉型图(4)其它要求:①在课程设计期间要努力工作,勤于思考,仔细检索文献和分析设计过程的问题。
②设计说明书必须认真编写,字迹清楚、图表规范、符合制图要求。
3 设计工作量:设计说明书1份;转炉炉型图1份;参考文献列表1份1.1转炉炉型设计1.1.1转炉炉型设计概述(1)公称容量及其表示方法公称容量(T),对转炉容量大小的称谓。
即平时所说的转炉的吨位。
(2)炉型的定义转炉炉型是指转炉炉膛的几何形状,亦即指由耐火材料切成的炉衬内形。
炉型设计内容包括:炉型种类的选择;炉型主要参数的确定;炉型尺寸设计计算;炉衬和炉壳厚度的确定;顶底复吹转炉设计。
1.1.2炉型种类及其选择(1)炉型种类根据熔池(容纳金属液的那部分容积)的形状不同来区分,炉帽、炉身部位都相同,大体上归纳为以下三种炉型:筒球形、锥球形和截锥形。
①筒球形炉型:该炉型的熔池由一个圆筒体和一个球冠体两部分组成,炉帽为截锥体,炉身为圆筒形。
其特点是形状简单,砌砖简便,炉壳容易制造。
在相同的熔池直径D和熔池深度h的情况下,与其他两种炉型相比,这种炉型熔池的容积大,金属装入量大,其形状接近于金属液的循环运动轨迹,适用于大型转炉。
②锥球形炉型(国外又叫橄榄形):该炉型的熔池由一个倒置截锥体和一个球冠体两部分组成,炉帽和炉身与圆筒形形炉相同。
其特点是,与同容量的其他炉膛相比,在相同熔池深度h下,其反应面积大,有利于钢、渣之间的反应,适用于吹炼高磷铁水。
③截锥体炉型:该炉型的熔池有一个倒置的截锥体组成。
转炉基础设计方案

转炉基础设计方案介绍本文档将详细描述转炉的基础设计方案。
转炉是一种重要的冶金设备,用于炼钢过程中的转炉炼钢。
在设计转炉基础时,需要考虑到结构的稳定性、耐火材料的选用以及温度和压力的控制等因素。
设计一个合理的转炉基础能够保证转炉的正常运行,并提高生产效率和产品质量。
结构设计转炉基础的结构设计是确保转炉稳定运行的关键。
基础通常由混凝土浇筑而成,可以根据转炉的尺寸和重量来确定基础的尺寸。
考虑到转炉运行过程中的振动和冲击载荷,基础结构应具有足够的强度和刚度。
为了增加基础的稳定性,可以在基础的周围设置反冲墙或桩基。
基础的设计还包括转炉的支撑方式。
支撑方式可以采用直接支撑或间接支撑。
直接支撑是将转炉直接放置在基础上,采用铸铁座或钢座来支撑。
间接支撑则是通过支承架将转炉悬浮在基础上,可以减小振动影响。
耐火材料的选用在转炉的基础设计中,耐火材料的选择至关重要。
耐火材料主要用于转炉的内衬和底部。
常用的耐火材料有矽砖、高铝砖和镁碳砖等。
在选择耐火材料时,需要考虑其耐温、耐压和耐火碱性的性能。
同时,还需要考虑耐火材料的粘结性和耐久性,以保证其能够在高温和高压环境下长时间稳定运行。
温度和压力控制转炉基础设计中的另一个重要考虑因素是温度和压力控制。
转炉在运行过程中会产生高温和高压的环境,因此需要采取措施来控制温度和压力,以避免设备损坏和生产事故的发生。
温度控制可以通过给转炉设置冷却设备来实现。
冷却设备可以通过循环水或其他冷却介质来降低转炉的温度。
需要注意的是,在选择冷却方式时,要考虑冷却介质的稳定性和廉价性。
对于压力控制,可以在转炉上设置压力传感器来监测压力变化,并及时采取措施来调节压力。
在设计基础时,还可以考虑设置泄压装置,以防止超压情况的发生。
安全性考虑在转炉基础设计中,安全性是不可忽视的因素。
转炉的运行过程中存在较高的温度和压力,因此需要考虑到操作人员和设备的安全。
为了保证操作人员的安全,可以在转炉周围设置安全栏杆和标识,提供明确的操作指导,以避免意外事故的发生。
第二章 转炉炉型设计
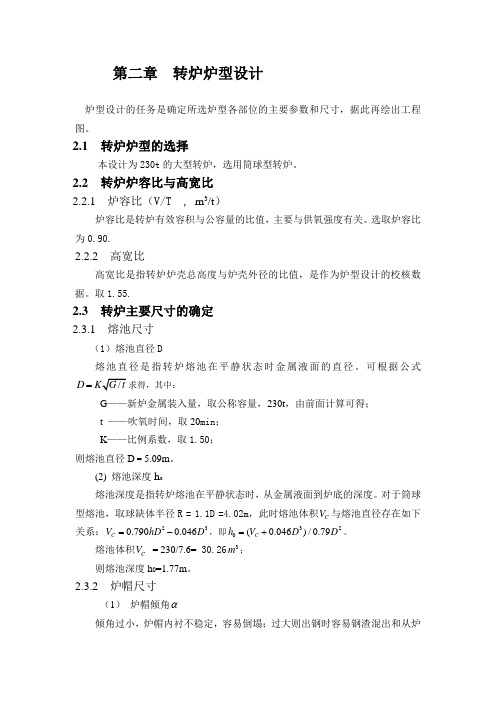
第二章 转炉炉型设计炉型设计的任务是确定所选炉型各部位的主要参数和尺寸,据此再绘出工程图。
2.1 转炉炉型的选择本设计为230t 的大型转炉,选用筒球型转炉。
2.2 转炉炉容比与高宽比2.2.1 炉容比(V/T , m 3/t )炉容比是转炉有效容积与公容量的比值,主要与供氧强度有关。
选取炉容比为0.90.2.2.2 高宽比高宽比是指转炉炉壳总高度与炉壳外径的比值,是作为炉型设计的校核数据。
取1.55.2.3 转炉主要尺寸的确定 2.3.1 熔池尺寸(1)熔池直径D熔池直径是指转炉熔池在平静状态时金属液面的直径。
可根据公式/D K G t =求得,其中:G ——新炉金属装入量,取公称容量,230t ,由前面计算可得; t ——吹氧时间,取20min ; K ——比例系数,取1.50; 则熔池直径D = 5.09m 。
(2) 熔池深度h 0熔池深度是指转炉熔池在平静状态时,从金属液面到炉底的深度。
对于筒球型熔池,取球缺体半径R = 1.1D =4.02m ,此时熔池体积C V 与熔池直径存在如下关系:230.7900.046C V hD D =-,即320(0.046)/0.79C h V D D =+。
熔池体积C V = 230/7.6= 30.263m ; 则熔池深度h 0=1.77m 。
2.3.2 炉帽尺寸(1) 炉帽倾角α倾角过小,炉帽内衬不稳定,容易倒塌;过大则出钢时容易钢渣混出和从炉口大量流渣。
在本设计中取α = 62°。
(2) 炉口直径d 0本设计中取取炉口直径为熔池直径的45%,即d 0 = 5.09×45% =2.29m(3) 炉帽高度H帽取炉口上部直线段高度H口 =350mm ,则炉帽高度为:H 帽 =1/200()tan D d H α-+= 1/2(5.09—2.29)tan62°+ 0.35 = 2.98m 2.3.3 炉身尺寸(1) 炉身直径转炉炉帽以下,熔池面以上的圆柱体部分称为炉身。
转炉工作原理及结构设计.
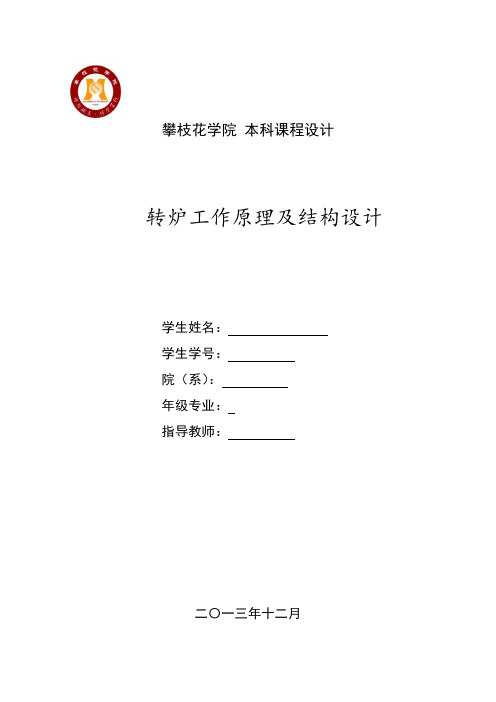
攀枝花学院本科课程设计转炉工作原理及结构设计学生姓名:学生学号:院(系):年级专业:指导教师:二〇一三年十二月转炉工作原理及结构设计1.1 前言1964年,我国第一座30t氧气顶吹转炉炼钢车间在首钢建成投产。
其后,上钢一厂三转炉车间、上钢三厂二转炉车间等相继将原侧吹转炉改为氧气顶吹转炉。
20世纪60年代中后期,我国又自行设计、建设了攀枝花120t大型氧气顶吹转炉炼钢厂,并于1971年建成投产。
进入20世纪80年代后,在改革开放方针策的指引下,我国氧气转炉炼钢进入大发展时期,由于氧气转炉炼钢和连铸的迅速发展,至1996年我国钢产量首次突破1亿t,成为世界第一产钢大国。
1.2 转炉概述转炉(converter)炉体可转动,用于吹炼钢或吹炼锍的冶金炉。
转炉炉体用钢板制成,呈圆筒形,内衬耐火材料,吹炼时靠化学反应热加热,不需外加热源,是最重要的炼钢设备,也可用于铜、镍冶炼。
转炉按炉衬的耐火材料性质分为碱性(用镁砂或白云石为内衬)和酸性(用硅质材料为内衬)转炉;按气体吹入炉内的部位分为底吹、顶吹和侧吹转炉;按吹炼采用的气体,分为空气转炉和氧气转炉。
转炉炼钢主要是以液态生铁为原料的炼钢方法。
其主要特点是:靠转炉内液态生铁的物理热和生铁内各组分(如碳、锰、硅、磷等)与送入炉内的氧进行化学反应所产生的热量,使金属达到出钢要求的成分和温度。
炉料主要为铁水和造渣料(如石灰、石英、萤石等),为调整温度,可加入废钢及少量的冷生铁块和矿石等。
1.2.1 转炉分类1.2.1.1 炼钢转炉早期的贝塞麦转炉炼钢法和托马斯转炉炼钢法都用空气通过底部风嘴鼓入钢水进行吹炼。
侧吹转炉容量一般较小,从炉墙侧面吹入空气。
炼钢转炉按不同需要用酸性或碱性耐火材料作炉衬。
直立式圆筒形的炉体,通过托圈、耳轴架置于支座轴承上,操作时用机械倾动装置使炉体围绕横轴转动。
50年代发展起来的氧气转炉仍保持直立式圆筒形,随着技术改进,发展成顶吹喷氧枪供氧,因而得名氧气顶吹转炉,即L-D转炉(见氧气顶吹转炉炼钢);用带吹冷却剂的炉底喷嘴的,称为氧气底吹转炉(见氧气底吹转炉炼钢)。
- 1、下载文档前请自行甄别文档内容的完整性,平台不提供额外的编辑、内容补充、找答案等附加服务。
- 2、"仅部分预览"的文档,不可在线预览部分如存在完整性等问题,可反馈申请退款(可完整预览的文档不适用该条件!)。
- 3、如文档侵犯您的权益,请联系客服反馈,我们会尽快为您处理(人工客服工作时间:9:00-18:30)。
氧气顶吹转炉设计姓名XXX学号XXX冶金工程XXXX材料科学与工程学院目录1.原始条件2.炉型选择3.炉容比的确定4.熔池直径的计算5.炉帽尺寸的确定6.炉身尺寸的确定7.出钢口尺寸的确定8.炉衬厚度确定9.炉壳厚度的确定10.验算高宽比序言现在钢铁联合企业包括炼铁,炼钢,轧钢三大主要生产厂。
炼钢厂则起着承上启下的作用,它既是高炉所生产铁水的用户,又是供给轧钢厂坯料的基地,炼钢车间的成产正常与否,对整个钢铁联合企业有着重大影响。
目前,氧气转炉炼钢设备的大型化,生产的连续化和高速化,达到了很高的生产率,这就需要足够的设备来共同完成,而这些设备的布置和车间内各种物料的运输流程必须合理,才能够使生产顺利进行。
转炉是炼钢车间的核心设备,设计一座炉型合理满足工艺需求的转炉是保证车间正常生产的前提,而炉型设计又是整个转炉设计的关键。
炉衬简介1 炉衬组成转炉炉衬由永久层,填充层和工作层组成。
永久层紧贴着炉壳钢板,通常是用一层镁砖或铝砖侧砌而成,其作用是保护炉壳。
修炉时一般不拆除炉壳永久层填充层介于永久层和工作层之间,一般用焦油镁砂或焦油白云石料捣打而成。
工作层直接与钢水,炉渣和炉气接触,不断受到物理的,机械的和化学的冲刷,撞击和侵蚀作用,另外还要受到工艺操作因素的影响,所以其质量直接诶关系到炉龄的高低。
国内外中小型转炉普遍采用焦油白云石或焦油镁砂质大砖砌筑炉衬。
为提高炉衬寿命,目前已广泛使用镁质白云石为原料的烧成油浸砖。
我国大中型转炉多采用镁碳砖。
2 炉衬砌筑(1) 砌筑顺序:转炉炉衬砌筑顺序是先测定炉底中心线,然后进行炉底砌筑,在进行炉身,炉帽和炉口的砌筑,最后进行出钢口炉内和炉外部分的砌筑。
(2) 砌筑要求①背紧,靠实,填满找平,尽量减少砖缝;②工作层实行干砌,砖缝之间用不定型耐火材料填充,捣打结实;③要注意留有一定的膨胀缝.3 提高炉衬寿命的措施(1) 提高耐火材料的质量;(2) 采用均衡炉衬提高砌炉质量;(3) 改进操作工艺;(4) 转炉热态喷补;(5) 激光监测;(6) 采用溅渣护炉技术;120吨氧气顶吹转炉设计1. 原始条件炉子平均出钢量为120吨 铁水采用P08低磷生铁;氧枪采用六孔拉瓦尔型喷头,设计氧压为1.0MPa 。
2. 炉型选择根据初始条件采用锥球型作为设计炉型。
转炉由炉帽、炉身、炉底三部分组成,转炉炉型是指由上述三部分组成的炉衬内部空间的几何形状。
有于炉帽和炉身的形状没有变化,所以通常按熔池形状将转炉炉型分为筒球型、锥球型和截锥型三种。
炉型的选择往往与转炉的容量有关。
所选120吨转炉属中型故用锥球型。
和相同体积的筒球型相比,锥球型熔池比较深,有利于保护炉底。
在同样熔池深度的情况下,熔池直径可以比筒球型大,增加了熔池反应面积,有利于去P ,S 。
我国的中小型转炉普遍采用这种炉型3. 炉容比的确定炉容比是指转炉有效容积V t 与公称容量G 的比值V t /G(m 3/t)。
V t 系炉帽、炉身和熔池三个内腔容积之和。
公称容量以转炉炉役期的平均出钢量来表示。
确定炉容比应综合考虑。
通常,铁水比增大,贴水中Si 、S 、P 行两高,用矿石作冷却剂以及供氧强度提高时,为了减少喷溅或溢渣损失,提高金属收得率和操作稳定性,炉容比要适当增大。
但过大的炉容比又会使基建和设备投资增加。
对于大型转炉,由于采用多孔喷枪和顶底复吹,操作比较稳定,因此在其他条件相同的情况下,炉容比有所减少。
转炉新砌炉衬的炉容比推荐值为0.90~0.95m 3/t ,大转炉取下限,小转炉取上限。
本题中,取炉容比为90.0 GV t4. 熔池直径的计算① 熔池直径的计算 熔池直径的计算公式tG KD = 式中D 熔池直径,m ; G 新炉金属装入量,t ; t 吹氧时间,min ; K 比例系数,如表1所示。
表1不同吨位下的K 值A . 确定初期金属装入量G :则3143.170.7120m GV ===金金ρ (钢液的密度取t m /0.73)B . 确定吹氧时间:根据生产实践,吨钢耗氧量,一般低磷铁水约为50~57m 3/t 钢,高磷铁水为62~69m 3/t 钢,本设计采用低磷铁水,取吨钢耗氧量为50m 3/t 钢,并取吹氧时间为18min (参见表2)。
则()[]min /78.21850)/332⋅===t m t m q O 吹氧时间吨钢耗氧量(供氧强度取7.1=K则氧气射流穿透深度mD 39.418120*7.1==m nTq H O 007.1678.212036.036.0256.0256.02=⎪⎭⎫⎝⎛⨯⨯=⎪⎪⎭⎫ ⎝⎛=穿② 熔池深度的计算筒球型熔池深度的计算公式为:m D D V h 555.139.4665.039.4033.0143.17665.0033.02323=⨯⨯+=+=金 W 为防止炉底直接接受氧气射流冲击,氧气射流穿透深度应小于熔池深度,一般应使h H 7.0<穿本题中:m h m H 0885.17.0555.17.0007.1=⨯=⨯<=穿符合要求。
所以确定m h m D 555.1,39.4==即D=4390mm, h=1555mm ③ 熔池其他尺寸的确定。
球冠的弓形高度:m D h 395.039.409.009.01=⨯===395mm炉底球冠曲率半径:m D R 829.439.41.11.1=⨯==取整R=4830mm 锥度的确定:()()329.0395.0555.15.0tan 212=-⎪⎭⎫ ⎝⎛---=h R R D α2.18=α符合倒锥度推荐值( 12~ 30)5. 炉帽尺寸的确定① 炉口直径d取m D d 11.239.448.048.0=⨯===2110mm② 炉帽倾角θ(选取原则:便于炉气逐渐收缩逸出,减少炉气对炉帽衬砖的冲刷侵蚀;使帽锥各层砖逐渐收缩,缩短砌砖的错台长度,增加砌砖的稳定性。
如果角度值过大,砌砖错台太长容易脱落。
取︒=60θ.③ 炉帽高度H 帽;取H 口=350mm ,则整个炉帽高度为:m H d D H 317.235.060tan 211.239.4tan 2=+︒-=+-=口帽θ 取整H=2315mm 在炉口设置水冷管水冷炉口。
炉帽部分容积为:()()32222202.1835.011.225.011.211.239.439.435.0315.21225.0)1222m H d d Dd D H H V =⨯⨯++⨯+-=+++-=ππππ口口帽帽)((6. 炉身尺寸的确定① 炉膛直径D 膛=D (无加厚段)② 根据选定的炉容比为0.90,可求出炉子总容积为310812090.0m V =⨯=总3652.72143.17202.18108m V V V V t =--=--=池帽身③ 炉身高度m D V H 802.439.44652.72422===ππ身身取整H=4800mm7. 出钢口尺寸的确定出钢口尺寸一般都设在炉帽与炉身的交界处,以使转炉出钢时其位置最低,便于钢水全部出净。
出钢口的主要尺寸是中心线的水平倾角和直径。
① 出钢口直径出钢口直径决定出钢时间,随炉子容量不同而异。
出钢时间通常为2至8分钟。
时间缩短(即出钢口过大),难以控制下渣,且钢包内钢液静压力增长过快,脱氧产物不易上浮。
时间过长(即出钢口过小),钢液容易二次氧化和吸气,散热也达。
通常按下面的公式来确定:cm T d T 523.1675.163=+=取整d=165mm ② 出钢口衬砖外径()cm d d T ST 14.9961.8265——==cm d ST 95=取=950mm ③ 出钢口长度()cm d L T T 18.13266.11587——==取cm L T 125==1250mm④ 出钢口倾角θ:为了缩短出钢口长度以利于维修和减少钢液二次氧化及热损失,大型转炉θ趋于减小。
取︒=20θ8. 炉衬厚度确定通常炉衬由永久层、填充层、工作层组成。
有些转炉则在永久层和炉壳钢板之间夹有一层石棉板绝热层。
永久层紧贴炉壳(无绝热层时),修炉时一般不予拆除。
其主要作用是保护炉壳。
该层用黏土砖砌筑。
填充层介于永久层和工作层之间,一般用焦油镁砂捣打而成。
其主要作用是减轻炉衬受热膨胀时对炉壳产生挤压和便于拆除工作层。
炉帽可用二步煅烧镁砖,也可根据具体条件选用其他材质。
转炉各部位的炉衬厚度设计参考值如表3所示。
表3 转炉炉衬厚度设计参考值:炉衬选择应遵循以下原则:① 耐火度高;② 高温下机械强度高,耐极冷极热性能好; ③ 化学性质稳定;④ 资源广泛,价格便宜。
根据如上120吨 转炉炉衬厚度选取选填充层100mm 选用焦油镁砂填料。
工作层材质全部采用镁碳砖。
永久层选取三层黏土砖。
每层黏土砖厚为120mm.9. 炉壳厚度确定炉身部分选=2δ70mm 厚的钢板,炉帽mm 501=δ和炉底=3δ70mm 厚的钢板,则mmH H h H 98605010061036070480023151555501006103603=+++++++=+++++++=δ身帽总mmD D 633020070216004390100226201307201302=+⨯++=⨯++++++=δ壳 取整D=6330mm10. 验算高宽比增大高宽比有利于减少喷溅和溢渣、提高金属收得率。
但是高宽比过大,在炉膛体积一定时,反应面积过小,氧气流股易冲刷炉壁,对炉衬寿命不利;而且导致厂房高,基建费用大;转炉倾动力矩大,耗电大。
转炉高宽比推荐值为1.35-1.65。
56.163309860==壳总D H符合转炉高宽比推荐值(1.35~1.65),因此认为所设计的炉子尺寸基本上是合适的。
能够保证转炉的正常冶炼进行。
11。