强力双齿辊破碎机堵料的原因分析及改进措施
双齿辊破碎机物料粘结分析及改进

图 1 改进前两齿轮相对位置
பைடு நூலகம்
( ) 据 原有 结 构 , 齿 辊有 相 对 圆周 运动 , 3根 两 齿 辊 结构 强度大 ,利用 改进齿辊 齿形 大小 、齿数 的 多
们 称之 为“ 暖煤 ”而破碎机 在露 天使用 , , 工作齿 辊 的
温度 与 室 外 温度 相 同 , 一般 在 一 5 C—一0 C, 样 2。 3。 这 物 料与 工作装 置 的温差非 常大 , 出现冻粘 现象 。 () 4 两齿辊 间距离 小 , 密度过 大 。 齿
1 引 言
文献标识码: B
文 章编号: 6 1— 9 1 20 ) 1—0 4 17 8 6( 0 8 0 0 3—0 2 扫 机构 , 结果未 能成 功 。原 因是 , 齿辊 转 动惯量 非 常 大 , 间夹杂 的煤矸坚 硬 , 齿 没有 相应 的材质 和结 构能 应对 , 而使清 扫机构 或机架损 坏 。 从 ( ) 过反 复的思考 与研究 , 2经 最终 决定对 齿辊 的
物料 不能 破碎 , 使上 一级输送机 构物 料堆 积 , 能停 只
过 密是易 粘结物 料原 因之一 ,原机器 的结 构是 每个 辊上 有 3柱 圆形齿 圈 ,每 一柱 齿 圈轴 向均部 1 5行 齿 , 向 2 齿 , 间齿顶部 留有 间隙 。改进前两 齿 周 4 2辊 辊齿 间相对 位置示 意如 图 1 。
在 3%以上 , 0 由于层理发育有夹矸层 , 夹矸现象 。 故呈
( ) 周 边水 文地 质 条件 的限制 , 表 , 下 水 2受 地 地
发达 , 使煤 中含水 量增加 。
() 3 开采工 艺及气 温 的原 因 。 在冬 季用 电铲进行
采 煤作 业 , 层厚度 在 6 一 次采全 高 。 季 冻 煤 —7 m, 冬 层 厚度 1 . 在冻 层 以 内的煤 , 温 0 o , 7—2m, 煤 —5 c 我
破碎机故障原因分析及处理方法

7、拆下破碎壁并重新正确安装。
8、最长空载时间为30分钟。
9、破碎壁的磨损量不要超过其厚度的2/3。
10、给楔块加垫片或拧紧轧臼壁螺栓。
11、过铁太多,会使支承套受冲击并导致定锥衬板松动。
12、把配合面恢复到厂家尺寸。
破碎机失速
1、三角皮带太松。
2、驱动电机出现电气故障。
8、割掉轧臼壁或破碎壁底部阻碍排料的凸边部分。
9、换用不同腔形的轧臼壁及破碎壁,向制造厂咨询。
定锥松动
1、支承套与调整环的螺纹磨损。
2、运转过程中锁紧压力过低。
3、破碎机排料口太小。
4、所用破碎壁或轧臼壁过厚。
5、破碎机排料口太大。
6、检查液压站到锁紧缸的软管连接是否正常。
7、锁紧环螺栓防止锁紧环在定锥拆出过程中意外抬起。由于振动而引起此螺栓向下拧紧,将锁紧环限制在非锁紧位置。
3、破碎部件薄弱断面弯曲,加速了动锥或定锥与衬板配合面的磨损。
4、破碎部件弯曲,加速了动锥或定锥与衬板配合面的磨损。
润滑池进水
平衡圈顶部积水
钻孔并焊接排水管
动锥转不动
支承套与调整环的螺纹之间积聚了污物或生锈。原因如下:
1、给料过热炉渣。
2、螺纹润滑不足。
3、防尘圈或防尘密封磨损。
4、无防雨设施。
5、在某一固定排料口位置运行时间太长。
7、给料分布不好,给料偏析引起物料给向破碎腔的一侧。
8、破碎壁和轧臼壁的平行带发生碰撞。
9、轧臼壁或破碎壁的平行带磨损过快。
1、更换轧臼壁或割大给料口。
2、检查传动轴转速是否正确。
3、减小给料粒度。
4、此类物料应自由给入,不能挤满给料。
辊压机常见故障及处理方法
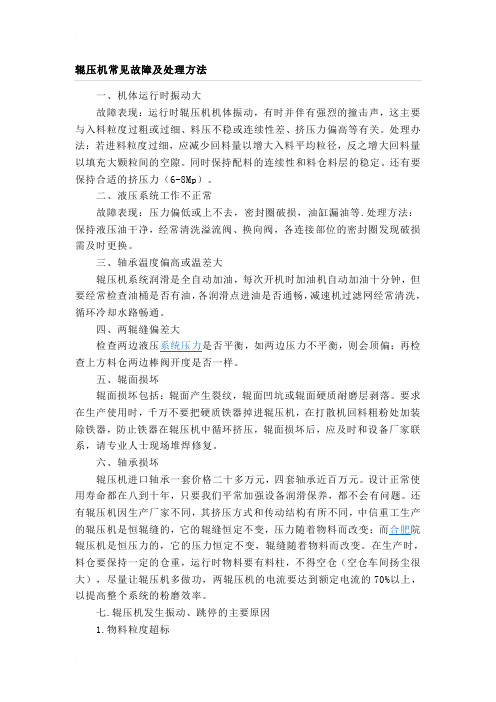
一、机体运行时振动大故障表现:运行时辊压机机体振动,有时并伴有强烈的撞击声,这主要与入料粒度过粗或过细、料压不稳或连续性差、挤压力偏高等有关。
处理办法:若进料粒度过细,应减少回料量以增大入料平均粒径,反之增大回料量以填充大颗粒间的空隙。
同时保持配料的连续性和料仓料层的稳定。
还有要保持合适的挤压力(6-8Mp)。
二、液压系统工作不正常故障表现:压力偏低或上不去,密封圈破损,油缸漏油等.处理方法:保持液压油干净,经常清洗溢流阀、换向阀,各连接部位的密封圈发现破损需及时更换。
三、轴承温度偏高或温差大辊压机系统润滑是全自动加油,每次开机时加油机自动加油十分钟,但要经常检查油桶是否有油,各润滑点进油是否通畅,减速机过滤网经常清洗,循环冷却水路畅通。
四、两辊缝偏差大检查两边液压系统压力是否平衡,如两边压力不平衡,则会顶偏;再检查上方料仓两边棒阀开度是否一样。
五、辊面损坏辊面损坏包括:辊面产生裂纹,辊面凹坑或辊面硬质耐磨层剥落。
要求在生产使用时,千万不要把硬质铁器掉进辊压机,在打散机回料粗粉处加装除铁器,防止铁器在辊压机中循环挤压,辊面损坏后,应及时和设备厂家联系,请专业人士现场堆焊修复。
六、轴承损坏辊压机进口轴承一套价格二十多万元,四套轴承近百万元。
设计正常使用寿命都在八到十年,只要我们平常加强设备润滑保养,都不会有问题。
还有辊压机因生产厂家不同,其挤压方式和传动结构有所不同,中信重工生产的辊压机是恒辊缝的,它的辊缝恒定不变,压力随着物料而改变;而合肥院辊压机是恒压力的,它的压力恒定不变,辊缝随着物料而改变。
在生产时,料仓要保持一定的仓重,运行时物料要有料柱,不得空仓(空仓车间扬尘很大),尽量让辊压机多做功,两辊压机的电流要达到额定电流的70%以上,以提高整个系统的粉磨效率。
七.辊压机发生振动、跳停的主要原因1.物料粒度超标按照科本公司辊压机操作手册要求,入辊压机物料平均粒度要小于30mm,最大不能超过50mm。
辊压机、打散机和磨机常见故障及分析处理

一、辊压机常见故障及分析处理辊压机是利用高压料层粉碎的机理,采用单颗粒粉碎群体化的工作方式进行连续工作。
常见故障有:两辊异常振动,动、静辊电流不稳,挤压效果不佳,出辊压机斗提负荷过重,甚至压死斗提等,我们主要从入磨物料的性质和辊压机的操作参数以及设备三个方面进行分析,并采取措施,具体如下:1)配料中(特别是熟料中)含有大量的细粉,熟料飞砂量较多,这是引起辊压机异常振动的主要原因。
对此从两方面进行调整;一是减少配料库中熟料的离析现象。
原来两台水泥磨熟料配料共使用一个配料库,因库顶熟料进料口稍微偏离中心位置,库内熟料离析严重,对此将原设计而未用的石灰石库启用改为熟料库,库下的配料秤作相应调整,实现水泥磨双系统分别单独配料,减小了熟料的离析;二是当熟料中细粉较多时,可增加混合材中沸石掺量,达到调整物料平均粒径的目的。
根据经验,入辊压机物料平均粒径在20mm以上,最好在35mm-45mm之间,辊压机不易振动且挤压效果好,如物料太细,可将动、定辊之间的垫铁加厚,由原来的10mm加为12mm,液压压力也可适当降低,以减小振动。
2)打散分级机分级能力降低,回粉中细粉太多,循环负荷加大,导致总配料量降低,辊压机缓冲小仓中含有较大颗粒的新鲜物料减少。
3)入辊压机小仓皮带处漏风严重,或者系统收尘风机风量过小,造成布料器通风少,收尘效果差,细粉不能被及时抽走,进入小仓内细料较多。
4)入磨物料中综合水分太小。
如物料中平均粒径偏低,含水分也偏低,物料通过辊压机时,两辊之间的啮合角就小,物料很容易顺辊隙冲下,不易形成稳定的料饼,造成辊压机振动和挤压效果差。
根据经验,入辊压机物料综合水分控制在0.8%-1.3%之间比较理想,我们采取在熟料配料秤上增加淋水装置,来控制适宜的物料水分,改善了挤压效果。
5)入辊压机物料粒径不均,夹有较大的颗粒,在两辊挤压过程中,较细的物料下泻过快,容易造成辊压机两端辊缝偏差大,不能形成稳定的料层,从而引起振动或跳停。
辊磨系统操作中常见故障的原因及处理措施
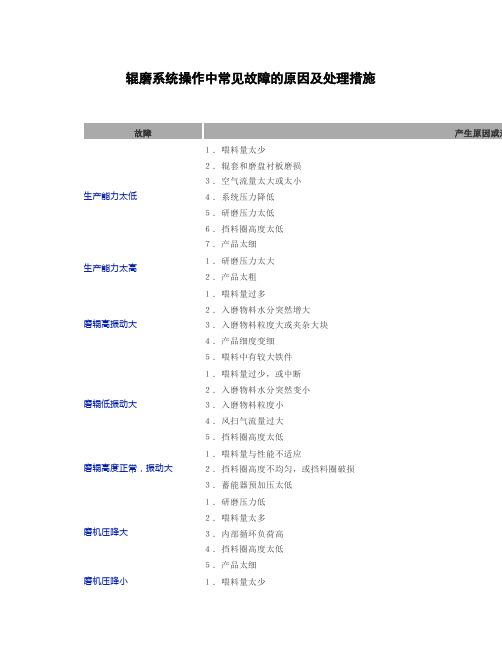
(1)加强对轴承的润滑,并定期检查磨辊油质;
(2)改进润滑油质和轴端整体密封结构,防止粉尘从轴承压紧透盖处进入轴承内部
2.辊套和衬板选用高耐磨材料
3.加强密封,减少漏风
4.力争喂料量稳定,磨盘上始终保持一定厚度的料层
油液中侵入空气,致油
液变质
液压系统振动,有噪音;液压元件工作不稳定,运动部件爬行;换向冲击大
更换不良密封件;检查管接头及液压元件连接处,并拧紧松动的螺栓
油液中混入水分
油液呈乳白色,导致液压元件生锈,磨损加快
增加研磨压力,并重调蓄能器压力
挡料圈太高
1.磨机电机电流高
2.磨机ΔP较低
降低挡料圈高度
挡料圈太低
1.磨机电机电流低
2.通过进风环的ΔP较高
3.尾料量较大
4.产量较低
5.磨辊振动大
增大挡料圈高度
入磨物料过于干燥
1.出磨气流温度高
2.物料在磨盘上的摩擦力减小
3.气流扫过磨盘,降低了磨辊的作用
4.产品变粗
3.控制入磨物料的水分含量
4.增大研磨压力,并重调蓄能器压力
5.提高挡料圈高度
6.检查给定气流下的进风环截面面积
研磨压力高
1.磨机电机电流高
2.止推轴承压力增大
3.磨机压降低
4.内部循环负荷变小
降低研磨压力,并重调蓄能器压力
研磨压力低
1.磨机电机电流低
2.气流量和ΔP一定时,产量低
3.尾料量增大
4.进风环和分离器ΔP较高
液压泵故障
泵轴Байду номын сангаас间隙大;输油量不足;泵内铜套、齿轮等元件损坏或精度差;压力板磨损大
输煤系统齿辊破碎机粘煤分析及处理方法
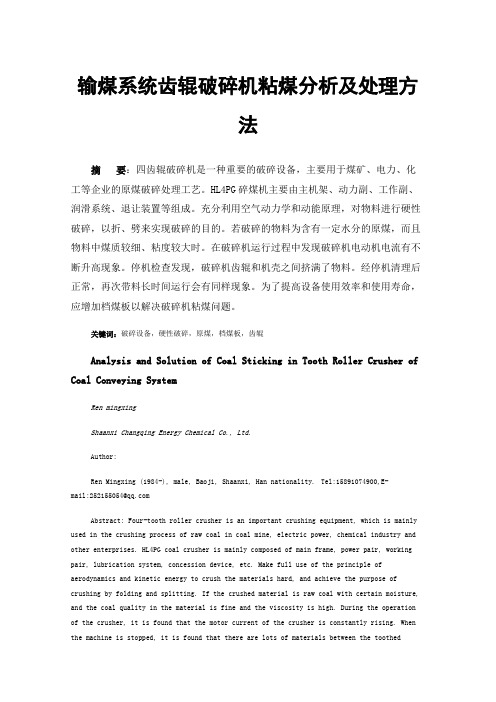
输煤系统齿辊破碎机粘煤分析及处理方法摘要:四齿辊破碎机是一种重要的破碎设备,主要用于煤矿、电力、化工等企业的原煤破碎处理工艺。
HL4PG碎煤机主要由主机架、动力副、工作副、润滑系统、退让装置等组成。
充分利用空气动力学和动能原理,对物料进行硬性破碎,以折、劈来实现破碎的目的。
若破碎的物料为含有一定水分的原煤,而且物料中煤质较细、粘度较大时。
在破碎机运行过程中发现破碎机电动机电流有不断升高现象。
停机检查发现,破碎机齿辊和机壳之间挤满了物料。
经停机清理后正常,再次带料长时间运行会有同样现象。
为了提高设备使用效率和使用寿命,应增加档煤板以解决破碎机粘煤问题。
关键词:破碎设备,硬性破碎,原煤,档煤板,齿辊Analysis and Solution of Coal Sticking in Tooth Roller Crusher of Coal Conveying SystemRen mingxingShaanxi Changqing Energy Chemical Co., Ltd.Author:Ren Mingxing (1984-), male, Baoji, Shaanxi, Han nationality.Tel:158****4900,E-mail:****************Abstract: Four-tooth roller crusher is an important crushing equipment, which is mainly used in the crushing process of raw coal in coal mine, electric power, chemical industry and other enterprises. HL4PG coal crusher is mainly composed of main frame, power pair, working pair, lubrication system, concession device, etc. Make full use of the principle of aerodynamics and kinetic energy to crush the materials hard, and achieve the purpose of crushing by folding and splitting. If the crushed material is raw coal with certain moisture, and the coal quality in the material is fine and the viscosity is high. During the operation of the crusher, it is found that the motor current of the crusher is constantly rising. When the machine is stopped, it is found that there are lots of materials between the toothedroller and the casing of the crusher. After shutdown and cleaning, it is normal, and the same phenomenon will occur when the material is taken again for a long time. In order to improvethe efficiency and service life of the equipment, the coal retaining plate should be added to solve the problem of coal sticking in the crusher. Key words: crushing equipment, hard crushing, raw coal, coal retaining plate, toothed roller1.引言陕西长青能源化工有限公司是一家煤制甲醇企业,生产工艺需将原煤破碎至合适粒度,以满足后续锅炉制粉及煤气化制浆对媒粒要求,公司选用了江油黄龙破碎输送设备制造有限公司制造的HL4PG.5-500B型,额定生产能力500t/h四齿辊破碎机。
破碎机堵料的原因和解决方法
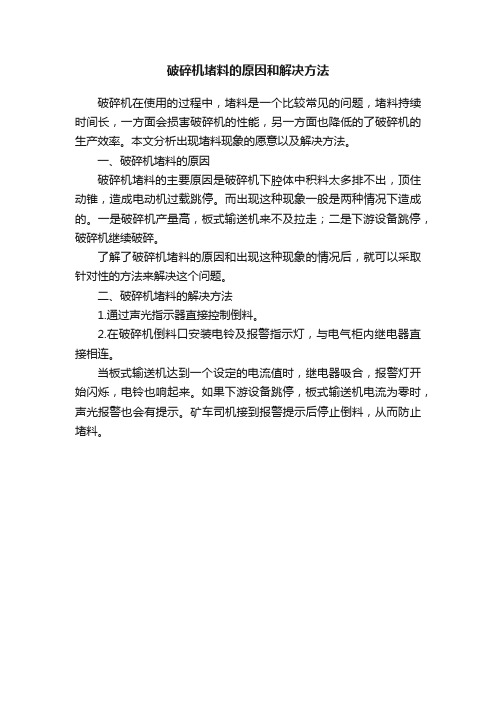
破碎机堵料的原因和解决方法
破碎机在使用的过程中,堵料是一个比较常见的问题,堵料持续时间长,一方面会损害破碎机的性能,另一方面也降低的了破碎机的生产效率。
本文分析出现堵料现象的愿意以及解决方法。
一、破碎机堵料的原因
破碎机堵料的主要原因是破碎机下腔体中积料太多排不出,顶住动锥,造成电动机过载跳停。
而出现这种现象一般是两种情况下造成的。
一是破碎机产量高,板式输送机来不及拉走;二是下游设备跳停,破碎机继续破碎。
了解了破碎机堵料的原因和出现这种现象的情况后,就可以采取针对性的方法来解决这个问题。
二、破碎机堵料的解决方法
1.通过声光指示器直接控制倒料。
2.在破碎机倒料口安装电铃及报警指示灯,与电气柜内继电器直接相连。
当板式输送机达到一个设定的电流值时,继电器吸合,报警灯开始闪烁,电铃也响起来。
如果下游设备跳停,板式输送机电流为零时,声光报警也会有提示。
矿车司机接到报警提示后停止倒料,从而防止堵料。
辊压机故障分析
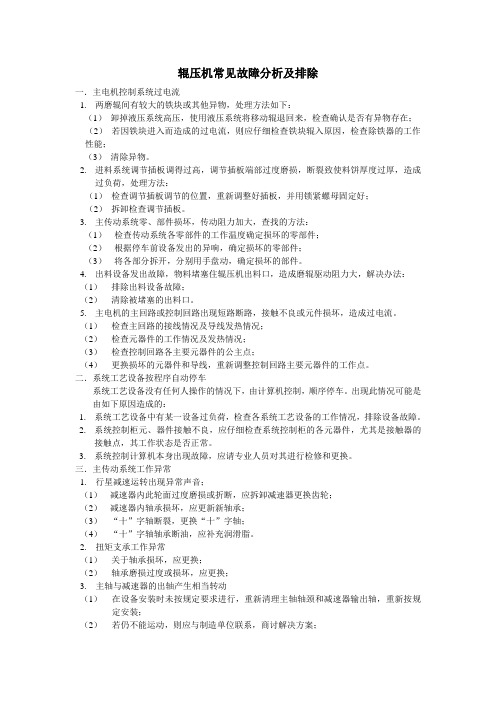
辊压机常见故障分析及排除一.主电机控制系统过电流1.两磨辊间有较大的铁块或其他异物,处理方法如下:(1)卸掉液压系统高压,使用液压系统将移动辊退回来,检查确认是否有异物存在;(2)若因铁块进入而造成的过电流,则应仔细检查铁块辊入原因,检查除铁器的工作性能;(3)清除异物。
2.进料系统调节插板调得过高,调节插板端部过度磨损,断裂致使料饼厚度过厚,造成过负荷,处理方法:(1)检查调节插板调节的位置,重新调整好插板,并用锁紧螺母固定好;(2)拆卸检查调节插板。
3.主传动系统零、部件损坏,传动阻力加大,查找的方法:(1)检查传动系统各零部件的工作温度确定损坏的零部件;(2)根据停车前设备发出的异响,确定损坏的零部件;(3)将各部分拆开,分别用手盘动,确定损坏的部件。
4.出料设备发出故障,物料堵塞住辊压机出料口,造成磨辊驱动阻力大,解决办法:(1)排除出料设备故障;(2)清除被堵塞的出料口。
5.主电机的主回路或控制回路出现短路断路,接触不良或元件损坏,造成过电流。
(1)检查主回路的接线情况及导线发热情况;(2)检查元器件的工作情况及发热情况;(3)检查控制回路各主要元器件的公主点;(4)更换损坏的元器件和导线,重新调整控制回路主要元器件的工作点。
二.系统工艺设备按程序自动停车系统工艺设备没有任何人操作的情况下,由计算机控制,顺序停车。
出现此情况可能是由如下原因造成的:1.系统工艺设备中有某一设备过负荷,检查各系统工艺设备的工作情况,排除设备故障。
2.系统控制柜元、器件接触不良,应仔细检查系统控制柜的各元器件,尤其是接触器的接触点,其工作状态是否正常。
3.系统控制计算机本身出现故障,应请专业人员对其进行检修和更换。
三.主传动系统工作异常1.行星减速运转出现异常声音;(1)减速器内此轮面过度磨损或折断,应拆卸减速器更换齿轮;(2)减速器内轴承损坏,应更新新轴承;(3)“十”字轴断裂,更换“十”字轴;(4)“十”字轴轴承断油,应补充润滑脂。
- 1、下载文档前请自行甄别文档内容的完整性,平台不提供额外的编辑、内容补充、找答案等附加服务。
- 2、"仅部分预览"的文档,不可在线预览部分如存在完整性等问题,可反馈申请退款(可完整预览的文档不适用该条件!)。
- 3、如文档侵犯您的权益,请联系客服反馈,我们会尽快为您处理(人工客服工作时间:9:00-18:30)。
经 验料在磨盘上停留的时间;使用可调式喷口环以调整风速,达到合适的喷口环风速;控制选粉机回粉量以减少料床上的细粉;配备喷水装置,必要时进行磨内喷水;采用具有减振功能的磨辊限位装置,避免磨辊和磨盘由于料层不稳定而导致的直接接触。
在多种手段综合作用下,单辊脱硫立磨的运行非常平稳。
1.4 立磨调试
在设计过程中,通过工艺平衡计算和对立磨进行工艺试验等手段,初步确定了最佳脱硫立磨工艺参数,特别是风量、局部风速、压力与磨机产量、成品细度以及分离器转速等的匹配关系。
在立磨调试时发现,如果磨机内粉磨过的物料不能及时排出,致使磨机内部物料过多,磨机负荷增大,料层不稳定,会导致立磨振动过大。
单辊加载的磨机在调试时,几乎不必考虑加载力的稳定情况,仅通过调整风料配比就可在很短的时间内使立磨正常运转。
粉磨系统中与立磨相关的其他设备对磨机工作影响较大的是收尘器。
立磨运转时,如果袋式收尘器压差过大,将导致细粉不能排出,磨机内过饱和,最后振动停机。
在条件具备的前提下,单辊加载的立磨调试时间仅为 5~7 d。
单辊加载立磨与相近规格集中加载立磨相比,磨机的产量得到了大幅度的提高。
表 2 表明单辊加载立磨完全实现了小规格、大产量的突破。
表 2 MLT2650 和 MLT2619 主要参数对比
磨机型号MLT2250MLT2650MLT2619
研磨轨道直径/mm225026502650
电动机功率/kW9001250710
产量/(t・h-1)406030
磨辊直径/mm170020201900
磨辊数量/个333
加载方式单辊加载单辊加载集中加载2 应用成果
某公司于 2009 年购买了 2 台 MLT2650 型脱硫立磨,于 2010 年投产,设备运行稳定,达产达标。
在
图 3 运转于某公司的 MLT2650 脱硫立磨
143
经 验
本栏目编辑 李文民 安秀清
第 41 卷 2013 年第 2 期
破碎机负荷增加。
因此,首先清除了破碎机上面的物料,结果发现破碎机内并无异物。
再次带料试车,同样的情况在次发生,并且下料溜槽被堵塞。
2 原因分析
经检查发现,破碎机齿板的齿牙与齿牙之间粘满了物料,几乎成为“光辊”。
主要原因为齿牙与齿牙啮合不深,齿根部的物料难以清除,使得破碎机咬料困难,物料不能被及时破碎,造成物料堆积,使破碎机负荷增加。
同时在清理溜槽时发现,与破碎机相连的出料溜槽为斜面 (见图 1),当物料落下时,由于物料湿黏,有很多小颗粒黏附在溜槽斜面上,越积越
多,最后把两边的齿辊“抱住”,增加电动机负荷。
1. 壳体
2. 齿辊
3. 出料溜槽
4. 带式输送机
图 1 改进前的破碎机及溜槽
3 改进措施
经过认真分析,提出以下改进措施。
(1) 增加清理齿牙根部物料的装置 在破碎机壳体下部安装刮刀 (见图 2),刮刀的刀片节距与齿板相同,每个刀片嵌入在两个齿牙之间,在齿辊旋转过程中清理齿牙根部的物料,保证在运行过程中齿辊齿牙
咬住物料。
1. 壳体
2. 齿辊
3. 刮刀
4. 出料溜槽
5. 带式输送机
图 2 改进后的破碎机及溜槽
(2) 改变出料溜槽的结构形式 将与破碎机相连
的溜槽斜槽改为直槽 (见图 2),物料下落时不会造成堆积,减少了细粒物料的黏附概率,同时也减小了破碎机的额外负荷。
4 改进效果
通过以上改进措施,破碎机运行平稳,成功地解决了堵料问题。
整个选煤系统运行正常,降低了停机概率,减少了经济损失。
□
(收稿日期:2012-09-07)(修订日期:2012-10-15)。