化工优化计算基础知识
4.3 化工过程系统最优化问题的类型

实际生产操作必须根据环境和条件的变化来调节决策变量 (即操作变量),从而使整个过程系统处于最佳状态,也就 是目标函数达到最优。这就是操作参数优化问题
如:通过操作参数优化计算,可以找到对应于系统下的精馏
塔最佳回流比、操作压力、反应器最佳反应温度和再循环流 量等等。
如果操作参数与生产装置的测试系统连接在一起,随时根据
检测仪表送来的信息进行优化计算,然后将计算结果信息直 接送往控制系统,则称为“在线操作优化”
过程系统的设计参数优化和操作参数优化的区别 在于优化对象不同,前者优化的是设计变量,后 者优化的是操作变量,
但就应其数学本质而言并什么本质上的区别,优 化的对象都是决策变量
当用机理模型描述过程系统的参数优化问题时, 模型方程分为稳态优化模型和动态优化模型
例4-2 间歇式理想混合反应器的最优操作, 假设反应器内进 行的是可逆放热反应,通过改变其冷却衬套内冷却剂的温度 对反应器实现最优控制
解:描述该反应器内过程进行的 T (t )] dt dT qr F r[ xA (t ), T (t )] (T Tc ) dt C p VC p
最优化问题可分为
过程系统参数的优化 过程系统结构的优化 过程系统管理的优化
4.3.1 过程系统参数优化
包括设计参数优化和操作参数优化
设计参数优化,就是把最优化技术应用于过程系统
模型,寻求一组使目标函数达到最优,同时又满足
各项设计规定要求的决策变量(即设计变量)。
根据最优设计方案可计算单元设备的尺寸
化工过程分析与合成
第四章 化工过程系统的优化
目 录
4.1 概述 4.2 化工过程系统优化问题基本概念 4.3 化工过程系统最优化问题的类型 4.4 化工过程中的线性规划问题
化工计算绪论及第一章

0.252 kcal
6q 266.9kgf m / s 1lbf 3.2808 ft
0.4536kgf 1m 1929.6lbf ft s
1-6 20%蔗糖溶液,20ºC粘度为1.967cp,换算 成:(1)kg/m·h(2)kgf·S/m2;(3)N·S/m2;(4)mPa·S; (5)lb/ft·S;(6)lbf·S/ft2。(1cp=0.01p)
例1-1 25℃时水的粘度为0.8937厘泊,换算成千 克/米·时及帕·秒。(1厘泊=0.01泊,1泊=1克/厘 米·秒)
解:1、找出比例形式(熟了后该步可忽略)
1k g 1000 g
100cm 1m
3600s 1h
2. 0.8937cp 0.8937102. g 1kg 100cm 3600s
第二节
单位换算
1— 4单位换算的方法
单位换算,是用不同单位制表示同一物理量。
连接单位法:将所有单位(原单位及所需换算 成单位)写出来,根据量与量间关系及单位间关 系写成数字与单位连乘连除式。
连接单位法步骤:
1、先查出同一因次不同单位制的换算系数,写 成比例形式(其比例 实质为1 )
2、将需换成的量和单位根据其间关系写成数字 附带单位连乘连除的式子进行运算。
每个比值间垂直线相当于乘号,注意所乘比例
与要求单位间换算关系。
例2 将R=0.08205 atm.l.mol-1.K-1→SI单位
解:
R 0.08205 atm.l mol.K
101325Pa 1atm
1N 1Pa m 2
1m3 1000l
8.314N m mol1 K 1 8.314J mol1 K 1
化工系统知识点总结

化工系统知识点总结一、化工系统概述化工系统是指通过一系列化学和物理过程,将原材料转化为最终产品的系统。
化工系统包括原材料的处理、反应、分离、纯化等一系列过程。
化工系统广泛应用于石油化工、制药、食品、化肥、化纤等各个领域。
化工系统的设计、运行和控制都需要深入了解化学工程原理、设备操作和系统优化。
二、化工系统组成1. 原材料处理:原材料处理包括原材料的输送、储存和预处理。
原材料通常是液体、气体或固体,在化工系统中需要进行输送和储存。
预处理包括杂质去除、浓缩、稀释等操作,以满足反应和分离过程的要求。
2. 反应过程:反应过程是化工系统的核心部分,通过一系列化学反应将原材料转化为最终产品。
反应过程需要控制反应温度、压力、物料配比等因素,以保证产品质量和产率。
3. 分离过程:分离过程是将反应产物中的目标成分分离出来的过程,包括蒸馏、结晶、萃取、吸附等操作。
分离过程需要根据目标成分的性质选择合适的分离方法,并进行设备的设计和操作。
4. 纯化过程:纯化过程是将分离后的目标成分进一步提纯的过程,包括结晶、结晶、析出等操作。
纯化过程需要根据产品的要求选择合适的方法,并进行设备操作和控制。
5. 设备与仪表:化工系统涉及大量的设备和仪表,包括反应釜、分离塔、换热器、泵、阀门、传感器、控制系统等。
这些设备和仪表需要进行选择、设计、安装和维护,以保证系统的正常运行。
6. 控制与优化:化工系统需要进行控制和优化,以保证产品质量和产率。
控制包括过程控制、设备控制、安全控制等,需要采用自动化系统和仪表控制。
优化包括生产方案优化、能源消耗优化、资源利用优化等,需要进行系统分析和调整。
三、化工系统的设计1. 工艺设计:化工系统的设计从工艺设计开始,即确定原料、反应路线、分离方法和产品规格。
工艺设计需要考虑产品质量、产率、设备投资和运行成本等因素,进行方案比选和优化。
2. 设备设计:设备设计是化工系统设计的重要环节,需要根据工艺要求选择合适的设备类型、规格和数量。
化工设计设计基础

化工设计设计基础1. 引言化工设计是化学工程领域的核心任务之一,它涉及到从实验室到工业生产的过程中的化学反应、物质传递和能量转化等方面的设计和优化。
本文将介绍化工设计的基础知识,包括设计的目标、设计流程和设计方法等。
2. 设计目标化工设计的主要目标是将实验室中的研究成果转化为可行的、高效的工业生产过程。
具体来说,设计目标可以包括以下几个方面:•生产成本:通过优化设计来降低生产成本是化工设计的一个重要目标。
这涉及到最小化原材料和能源的消耗,同时提高生产效率和产品质量。
•安全性:化工设计还需要考虑工艺过程中的安全性,防止事故的发生。
这包括设计合适的控制措施和应急预案,以及考虑到可能出现的风险因素。
•环境友好:在设计化工过程时,还需要考虑到对环境的影响,并寻找减少废弃物和排放物的方法。
•可持续发展:化工设计还应该考虑到可持续发展的要求,选择符合环保要求和资源可持续利用的工艺和材料。
化工设计的一般流程通常分为几个主要阶段,包括前期调研、方案设计、详细设计和实施等。
具体流程如下:3.1 前期调研前期调研阶段是对项目进行全面了解和分析的过程。
在这个阶段,设计人员需要收集相关的信息和数据,了解产品的要求和目标。
方案设计阶段是根据前期调研阶段的结果,制定一个初步的设计方案。
在这个阶段,设计人员需要确定适用的反应工艺、材料和设备等。
3.3 详细设计在详细设计阶段,设计人员将对方案进行进一步完善和优化。
这个阶段的重点是确定工艺参数、选取最适合的设备和材料,以及设计相关的控制系统。
3.4 实施实施阶段是将设计方案付诸实施的过程。
在这个阶段,设计人员需要协调各个部门和人员,确保设计方案的顺利运行。
4. 设计方法化工设计涉及到复杂的化学反应和物质流动等过程,因此需要运用一系列的设计方法和工具来帮助设计人员完成任务。
4.1 模拟和模型模拟和模型是化工设计中常用的工具。
通过建立数学模型和模拟计算,设计人员可以预测和优化工艺参数、能量转化效率等。
化工过程模拟与优化

02
化工过程模拟的原理与技术
单元操作模拟
总结词
单元操作模拟是针对化工过程中单个操作单元的模拟,通过 数学模型描述单元内部物料和能量的传递、转化和平衡。
详细描述
单元操作模拟基于物理化学原理,通过建立数学模型来描述 单元设备的内部过程,如流体流动、传热、传质等。通过单 元操作模拟,可以预测设备性能、优化操作参数和提高设备 效率。
04
化工过程模拟的挑战与解决方案
数据缺失与不确定性
总结词
数据缺失和不确定性是化工过程模拟中的常见问题,需要采用数据填充、概率建模和蒙特卡洛模拟等 方法进行处理。
详细描述
在化工过程中,由于实验成本高昂或历史数据不足等原因,常常存在数据缺失的情况。为了减小数据 缺失对模拟结果的影响,可以采用插值、回归等方法对缺失数据进行填充。同时,可以采用概率建模 和蒙特卡洛模拟等方法来处理不确定性问题,为决策提供更全面的信息。
目的
优化化工过程,提高产品质量、降低 能耗和减少环境污染,实现经济效益 和环境效益的双重提升。
模拟的重要性
提高生产效率
通过模拟,可以预测和优化化工过程 的操作条件,提高生产效率。
降低实验成本
通过模拟,可以在实验室内进行大量 虚拟实验,避免了实际生产中的高昂 成本和安全风险。
优化产品设计
通过模拟,可以对新产品的设计和开 发进行预测和优化,缩短产品开发周 期。
总结词
优化算法用于寻找化工过程的最优操作 参数和配置,以提高生产效率和降低能 耗。
VS
详细描述
优化算法基于数学规划、梯度下降等方法 ,通过迭代搜索最优解。常见的化工过程 优化算法包括线性规划、非线性规划、遗 传算法等。通过优化算法的应用,可以找 到最优的操作参数和配置,提高生产效率 和降低能耗,实现化工过程的节能减排和 可持续发展。
化工基础知识

化工基础知识化工基础知识是指化工学科最基本的理论、原理、方法和技术,是化工工程师必须掌握的基本内容。
下面将介绍一些重要的化工基础知识。
1. 化学反应原理:化学反应是化学变化的过程,是化学反应工程的基础。
化学反应原理包括反应热力学、反应动力学和化学平衡等内容。
热力学研究反应系统的能量变化,动力学研究反应速率和反应机理,平衡研究反应系统达到最终状态时的状态。
2. 物质平衡:物质平衡是化工过程设计的基础,涉及物质在化工过程中的输入、输出和转化。
物质平衡可以用质量平衡和物质计量来计算,常用的方法包括物料的输入输出检测和流程图的绘制。
3. 能量平衡:能量平衡是热力学系统中能量变化的描述,涉及热力学图表、热平衡计算和热力学过程分析。
能量平衡通常通过测量传热和计算热量的输入和输出来进行。
4. 流体力学:流体力学是研究流体力学特性和其运动规律的学科,包括流体的密度、压力、粘度以及流体运动的速度和方向等。
化工过程中的流体力学计算可以用来优化管道设计、分离设备和混合设备的选型和运行。
5. 传质过程:传质过程是物质在物理和化学过程中通过不同相界面的传递和转化。
传质过程包括扩散、对流和传质平衡等,常用传质模型包括菲克定律、斯特拉维安定律和质量对数平衡。
6. 反应器设计:反应器设计是化工工程中的重要环节,涉及到反应器的选择、尺寸和运行条件的确定。
反应器设计需要考虑反应物的转化率、反应速率、反应温度和压力等因素。
7. 分离过程:分离过程是将混合物中的组分物质分离出来的过程。
常用的分离过程包括蒸馏、萃取、吸附和结晶等。
分离过程的选型需要考虑分离效果、能耗和操作难度等因素。
8. 化工安全:化工安全是化工工作中最重要的因素之一,涉及到化工过程中的安全生产、事故预防和紧急救援等。
化工安全需要遵循国家相关的安全法律法规和标准,采取合理的工艺措施和安全控制措施。
以上是一些重要的化工基础知识,化工工程师必须了解和掌握这些基础知识才能够进行化工过程的设计、运行和优化。
化工原理中的化工过程集成与优化

化工原理中的化工过程集成与优化化工工程中的过程集成与优化是一项重要的技术,旨在通过优化化工过程中的各个单元操作,提高生产效率、降低能耗以及减少对环境的污染。
本文将介绍化工原理中的化工过程集成与优化的基本概念、方法和应用案例,并探讨其在化工工程中的重要性和前景。
一、化工过程集成与优化的基本概念化工过程集成与优化旨在通过将化工过程中的各个单元操作进行整合和优化,以实现整体性能的提升。
过程集成是指将不同的单元操作相互结合,形成一个具有相互关联和协同作用的整体系统;过程优化则是通过对该整体系统进行综合分析和调整,以实现最佳的生产效果。
化工过程集成与优化的目标包括降低能耗、提高产量和质量、降低成本和减少对环境的影响。
二、化工过程集成与优化的方法1. Pinch Analysis(突破分析)Pinch分析是一种常用的化工过程集成与优化方法,主要用于能量系统的优化。
该方法通过对热量的流动进行分析,确定热量交换装置的最佳配置,以最大程度地降低能量消耗和损失。
2. Mathematical Programming(数学规划)数学规划是一种利用数学模型和计算方法来优化化工过程的方法。
它通过建立数学模型,将目标函数和约束条件进行数学描述,然后使用优化算法求解最优解。
常用的数学规划方法包括线性规划、整数规划、动态规划等。
3. Process Simulation(过程模拟)过程模拟是一种将化工过程进行数字化描述和仿真的方法,旨在通过对过程进行模拟和分析,找出优化的空间和改进的方向。
过程模拟常用的软件工具包括ASPEN Plus、HYSYS等。
三、化工过程集成与优化的应用案例1. 炼油厂的能量优化炼油厂是一个典型的能耗较高的化工过程,其中能量系统的优化对于提高能源利用效率和降低成本至关重要。
通过应用Pinch Analysis方法,可以确定热量交换网络的最佳配置,实现能量的最大回收和利用。
2. 化肥生产过程的排放控制化肥生产过程中,大量的废气和废水会对环境造成严重的污染。
化工工艺计算说明书
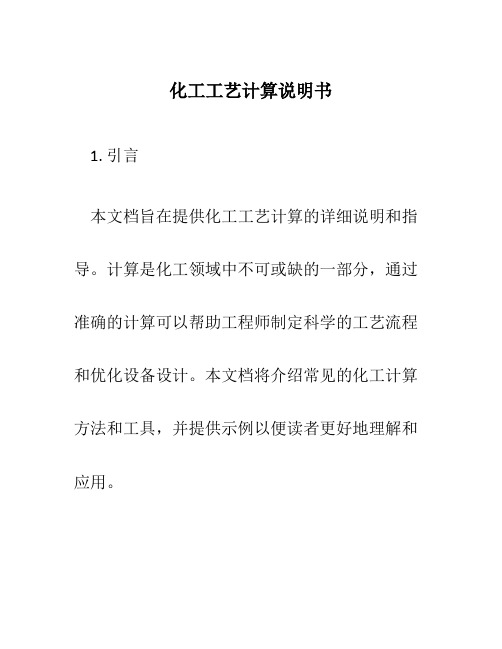
化工工艺计算说明书1. 引言本文档旨在提供化工工艺计算的详细说明和指导。
计算是化工领域中不可或缺的一部分,通过准确的计算可以帮助工程师制定科学的工艺流程和优化设备设计。
本文档将介绍常见的化工计算方法和工具,并提供示例以便读者更好地理解和应用。
2. 常见化工计算方法2.1 流体力学计算流体力学计算是化工工艺中最常见的计算之一。
它包括液体和气体在管道中流动的速度、流量、压力损失等参数的计算。
常用的流体力学计算方法有:•流速计算:通过引入质量和体积流量的定义,可以计算出流体在管道中的速度。
•压力损失计算:通过考虑流体的粘度、密度和管道长度等因素,可以计算出流体流动过程中的压力损失。
2.2 热力学计算热力学计算是研究能量转化和传递的关键计算方法。
在化工领域中,热力学计算被广泛应用于热传导、物质变化和能量平衡等方面。
常用的热力学计算方法有:•温度计算:通过考虑材料的热导率和热容量,可以计算出物体在不同条件下的温度分布。
•相变计算:通过考虑物质的相变热和变化过程中的能量平衡,可以计算出相变过程中的温度和物质的变化量。
2.3 反应工程计算反应工程计算是研究化学反应过程的一种重要方法。
它可以用于确定反应方程式、估计反应速率以及分析反应过程中的各种参数。
常用的反应工程计算方法有:•反应平衡计算:通过考虑反应物和生成物之间的化学平衡关系,可以计算出反应物的转化率和生成物的浓度。
•反应速率计算:通过实验数据,可以建立反应速率方程,并通过该方程计算出反应的速率常数和反应物的消耗速率。
3. 常见化工计算工具3.1 ExcelExcel是一种功能强大的电子表格软件,广泛应用于各个领域的计算和数据分析。
在化工领域中,可以利用Excel进行各种化工计算,例如流体力学计算、热力学计算和反应工程计算。
Excel具有易用性和灵活性,可以通过公式和函数进行复杂的计算和数据处理。
3.2 MATLABMATLAB是一种专业的数值计算和科学数据可视化软件,被广泛应用于化工领域的计算和分析。
- 1、下载文档前请自行甄别文档内容的完整性,平台不提供额外的编辑、内容补充、找答案等附加服务。
- 2、"仅部分预览"的文档,不可在线预览部分如存在完整性等问题,可反馈申请退款(可完整预览的文档不适用该条件!)。
- 3、如文档侵犯您的权益,请联系客服反馈,我们会尽快为您处理(人工客服工作时间:9:00-18:30)。
卜1 •技术经济数据・▲ 2 •几个化工单元操作优化实例卜3•过程系统的优化优化问题的由来优化方法和理论来源于军事,管理和经济。
我国古代军事天才孙武所著《孙子兵法》把军事运筹学的思想,理论和方法阐述得淋漓尽致,其中包含大量的优化思想和方法。
两次世界大战,尤其是二战中提出的很多均是优化问题,诸如搜索潜艇问题;护航问题;布雷问题;轰炸问题以及运输问题等等。
二战后,优化方法的应用由军事问题转入民用问题,提出了现代管理的理论和方法,如工程设计,计划管理等等。
现阶段,生产规模日益庞大,生产技术日益复杂,商业经营日趋国际程技术和管理人员人员优化的意义和可行性在工业决策中,优化技术是主要的定量分析工具。
针对复杂的化工设计和工厂操作问题,通过优化方法做出的决策比直接决策更为可靠、有效。
•在化工厂以及许多其他工业工程的设计、操作和分析中所涉及的大部分问题都可使用优化方法进行求解。
如初始设计、优化现有设备以强化其操作性能,达到产量最大、成本最小、能耗最低等目的。
奁计算机及其相关软件的发展使得优化问题的计算不仅可行而且高效(二战后兴起,近几十年来普及)O每个优化问题都包含三个基本方面:-至少有一个要优化的目标函数(利润函数、费用函数等);・等式约束;■不等式约束。
所谓化工优化设计就是采用优化方法使化工过程满足最优的目标函数和约束条件。
这一最优目标函数通常是指设备或装置的年费用为最小。
在化工设计中确定某些参数时,需要考虑对设备费用和操作费用的影响。
•化工装置的年费用=设备费用+操作费用。
设备费用:一般指设备的购置费用、安装费用、维修费用按折旧年限分摊到每年的成本。
操作费用:指每小时生产所需的水、电、蒸汽等费用乘以年开工小时数为每年的成本。
由于优化设计涉及技术经济参数,因此可靠的定量计算需了解国家的技术经济政策和市场的价格走势。
进行化工的优化设计计算,必须要有技术经济数据或相应的数据库。
由于物资的价格特别是钢材和能源的价格随市场变化很大,所以技术经济数据不像物性数据是固定不变的,需要根据市场的发展不断修正。
•设备费用(1)按设备有固定的单价Cs=fS「Dj.ZjCs-设备的年费用,元;S L一设备的数量,m2(或m3或kg);Dj一设备的单价,7C/m2(或元/nP或元/kg);Zj —设备折旧费,1/年; /—相关的校正系数。
•:・设备费用(2)按系列设备公式计算卩一设备尺寸的函数。
根据不同的设备有不同的函数形式。
如管壳式换热器的计算公式为:Cs = • 了2' a^L • S如一换热器的传热面积,m2;°、〃一设备的回归系数。
•:・设备费用(2)按系列设备公式计算C s=13f r f2-aA^Zj表6J管壳式换热器回归系数和校正系数表心设备费用(2)按系列设备公式计算碳钢塔板的精憾塔计算公式为:Cs = 278.38办・左丁3 • exp(0.57D)N • Z j齐一美元对人民币的汇率;九一塔板因子系数,浮阀塔板取1,筛板塔板取0・85,泡罩塔板取1・59;厶一板数因子,N>20时取1, Nv20时由厶=2.25/1.0414N计算; N—实际塔板数;D—塔径,nio操作费用Cc = (^sQw +Dz% +D D E)TQ—操作的年费用,元;»s —水的单价,7C/m3;q w一水的耗量,m3/h;血一蒸汽的单价,7U/kg;坠一蒸汽的耗量,kg/h;巧一电的单价,元/(kW・h); E —设备的动力消耗,kW;—年开工小时,ho 求解优化问题的方法往往根据条件的不同而各有差异。
如目标函数只涉及一个变量,称为单变量优化问题,否则为多变量问题。
这里介绍的化工单元操作的优化,都是单变量的优化问题。
•:•最佳管径的设计管路的优化设计是指设计出使整个管路的设备费和操作费的年成本最小的管径,对高压管路和远距离管线的设计尤其重要。
管路特性方程H = AZ+ —+Pg泵的电机输入功率pgqvH最佳管径的设计管路质量:jr jrm = (l + F)p m L~[(d+2^2-d2]=(l + F)p nt L-[2d6 + 62]加一管材质量,kg;》一管壁厚度,m;kg/m3最佳管径的设计 费用方程:C. =D r mZj+D D P a T= D J Z J (l + F)p m L^[2d3 + 32]c 一皆幽李结生吁帝田.力一管路単爲质备的价毎(包括安装和维修等费用)O 因此:管路系统的年总费用Cz 是管径〃的函数。
•最佳管径的设计dC z "(I )极值法:目标函数的一阶导数等于0。
需=0+D DT ^^rjAZ+眷贬龙40殆+ 32$2 耳—兀d g可以通过迭代上述方程求解管径〃,即为最佳管径,但该管径需根据管材规格进行圆整。
(2)穷举法:把不同的管径(按管材的规格)逐一代入费用方程,可以得到〃的列表函数,即可方便地得到最佳的管径。
换热器冷却水出口温度的优化用冷却水冷却某工艺热流体,当换热器的传热量为已知,水的进口温度一定时,根据传热计算可知:冷却水出口温度的高低即影响设备费用;同时冷却水的出口温度又影响冷却水的用量即操作费用。
所谓最佳冷却水出口温度就是在此温度换热器冷却水出口温度的优化 由热量衡算和传热速率:Q =^0qn,cp(t2~tl)=KA^InA = ^- 口一 n)—d)=KA(珀 一(2)一(卩2 一'J36000Cp((2 — ‘1 )换热器冷却水出口温度的优化费用方程:C Z =D J Z J A + D S ^Q t nIn —JG—换热器年总费用;D/ —换热器单位面积的费用(包括安装和维修等费用)。
Ds —每千克冷却水费用(包括动力费用)。
Z/ —换热器的折旧率,1/年;貳一换热器年工作小时,ho因此:管路系统的年总费用G是管径$的函数。
换热器冷却水出口温度的优化月厂些=0(I)极值法:目标函数的一阶导数等于0。
少2」^「(珀-t2)-(T2—(i)]Tn 三二^D J Z J Q珀一2丿卩」丁2-片 + 36OO0V = 0K [(T1-t2)-(T2-t1)']2c p{t2-t^~可以通过迭代上述方程求解切即为最佳冷却水出口温度。
(2)穷举法:把不同的岀口温度代入费用方程,可以得到Cz-『2的列表函数,即可方便地得到最佳冷却水出口温度。
计算对K作为常数考虑,如把K也作为5的函数,则计算难度将增加。
•:•精馆塔最佳回流比的确定回流比是精馅塔设计和操作的重要参数,回流比的大小直接影响精馅塔的能耗及塔板的直径和数量。
以常规精馆塔(泡点加料)为例。
塔顶全凝器的冷凝热负荷为:Qc =/c V = /c (7? + l)Z> = ^w e Pc Ar塔底再沸器的汽化热负荷为:Q R == /R (R +1)D= WzX比,加一塔顶蒸气、塔底蒸气的摩尔汽化热, Wz —饱和水蒸气用量,kg/h ; V —加热蒸气的汽化热,kj/kg o精馆塔最 【佳回流比的确定 kj/kmol ;精馅塔最佳回流比的确定Gilliland 关联方程取:N -N—1——= 0.75 - 0.75 1 + N TV 0.75 - 0.75(R - R min V 56681 + R 丿 0.5668+ N Tmg1 一 0.75 + 0.75I 1 + R 丿 r /?-1? min V 5668< 1+R >精馆塔最【佳回流比的确定塔板直径应为气液负荷的复杂函数,现采用一种简单的精馅塔最佳回流比的确定 费用方程:NC z =278.38^/^3 exp(0.57D)-^Z y +q wD s T + W z D z t/? —Rmin)1 + R ‘__________________ 7・ exp(0・0114V(273 + T)CR + DPp^)二 + (R + 1)D E TD z 一蒸汽的单价,元/kg ; D s 一水的单价,7U/m 3;0.5668+ N〒 2 vTmin0.75 — 0.75=278・38//人1 一 0.75 + 0.75R_ R min1 + R精馆塔最【佳回流比的确定当D、心、Ng p和卩等为已知值,其他的物性和经济参数也为已知值时,精馅塔的年费用G是的函数,最佳操作人同样可以通过极值法和穷举法求得o技术的发展使人们认识到,要把一个装置作为整体来考虑,使之能耗最小.年费用最小和环境污染最小,达到整体设计的优化,称为过程的集成。
通常在同一装置内有多股物料需要加热,另有多股物料需要冷却。
如果把这些物料相互匹配,使热流体放出的热量提供给冷流体加热,这样可以大大减少加热蒸汽和冷却水的耗量,使能量利用率大为提高。
过程集成中目前最实用的方法是夹点技术。
•:•温焙图和复合曲线根据热量衡算可知,温度上升即流体的焙值增加, 当流体的比热容为常数时可写为:Q=q/p(t2 - =夹点和换热系统的集成Company name夹点和换热系统的集成(b)Company name承夹点和换热系统的集成夹点/II I系统热集成的目标函数热复合曲线和冷复合曲线的相互位置决定了夹点温差,同时也确定了需要换热器的个数、传热面积的大小及冷却水和加热蒸汽的耗量。
系统热集成的目标函数有多种选择。
其中以年费用为目标函数的形式如下:Cz =6为堺沁 +(q/s +Wz2"■I。