热处理炉有效加热区测定方法
热处理炉有效加热区测定方法

热处理炉有效加热区测定方法热处理炉有效加热区测定方法导言:热处理炉是一种被广泛应用于金属材料处理的设备,其主要功能是通过加热和冷却控制,对金属材料进行结构调整和物理性能改善。
在进行热处理过程中,确保炉内加热区能够达到有效加热是非常关键的。
本文将探讨热处理炉有效加热区的测定方法,以帮助读者更好地理解和掌握该技术。
一、有效加热区的定义在热处理炉中,有效加热区是指能够达到所需温度范围并实现均匀加热的区域。
一般来说,如果炉内的温度分布能够在一定的误差范围内保持均匀,那么该区域就可以被认定为有效加热区。
在实际应用中,有效加热区的确定对于炉内金属材料的均匀加热非常重要,它直接影响到处理效果的质量。
二、传统方法1. 温度测量法传统的热处理炉有效加热区测定方法之一是通过在炉内不同位置布置温度传感器,测量这些位置处的温度值。
根据温度分布图来确定加热区的范围。
这种方法简单直接,可以提供炉内温度的整体情况。
然而,由于传感器的布置可能存在问题,比如不均匀或数量不足,因此可能会导致测量结果的不准确。
2. 金属试块法另一种常用的方法是使用金属试块来评估有效加热区的范围。
在炉内放置一系列具有相同材料和尺寸的金属试块,然后根据试块的质量变化来判断加热区的位置。
这种方法相对简单,但仍然存在一些局限性,比如试块的分布和数量问题,以及在实际加热过程中试块与工件之间的传热差异等。
三、改进方法为了克服传统方法存在的问题,近年来,一些新的测定方法被提出并得到了广泛应用。
下面介绍几种改进的方法:1. 热像仪法热像仪是一种能够显示物体表面温度分布的设备,通过红外线探测技术来测量物体的辐射能量并将其转化为图像。
热像仪可以将炉内的温度分布直观地展示出来,并能够在实时监测中提供精确的温度数据。
通过分析热图,可以快速确定有效加热区的位置和范围。
这种方法不仅操作简便,而且具有较高的测量精度,因此在炉内温度分布调整和优化过程中得到了广泛的应用。
2. 数值模拟法数值模拟方法是一种通过计算机仿真来预测热处理过程中加热区温度分布的技术。
热处理炉有效加热区检测规程
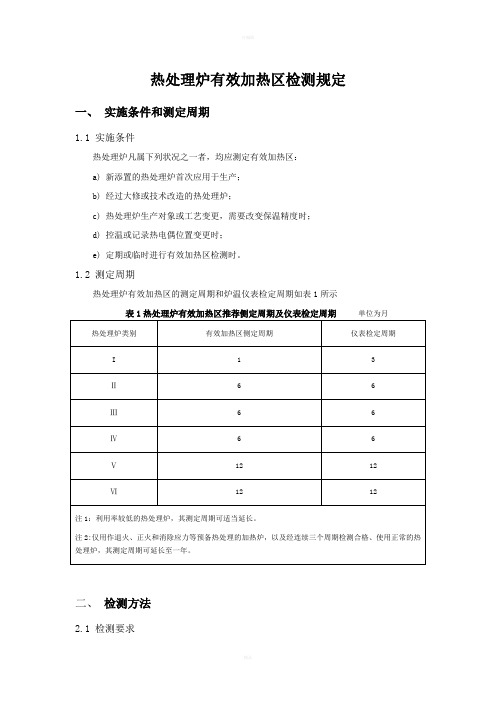
热处理炉有效加热区检测规定一、实施条件和测定周期1.1 实施条件热处理炉凡属下列状况之一者,均应测定有效加热区:a) 新添置的热处理炉首次应用于生产;b) 经过大修或技术改造的热处理炉;c) 热处理炉生产对象或工艺变更,需要改变保温精度时;d) 控温或记录热电偶位置变更时;e) 定期或临时进行有效加热区检测时。
1.2 测定周期热处理炉有效加热区的测定周期和炉温仪表检定周期如表1所示单位为月二、检测方法2.1 检测要求⑴热处理炉有效加热区的检测,一般情况下采用空载试验,特殊要求时可以装载试验(半载试验或满载试验)。
⑵测试时,热处理炉应以常用升温速度升温,真空炉采用常用真空度。
2.2 检测点数量和位置热处理炉有效加热区温度检测点的数量和位置按照热处理炉的形式和假定有效加热区的尺寸来确定。
2.3 检测温度以常用的工艺规定温度为检测温度范围,检测温度根据检测温度范围按表2规定确定。
2.4 检测顺序及方法⑴校正检测仪器、热电偶、补偿导线,热电偶应提供误差值。
⑵测量装置的接线a) 用适当的方法按需要将热电偶牢固地绑扎在测温架的每个测温位置上。
b) 将热电偶参考端引出炉外,在方便的位置通过补偿导线、切换开关、铜导线与检测仪器联接。
应防止由于引出线安装不当而影响炉温测量。
c) 装载试验时,热电偶测量端应尽可能和工件接近。
⑶温度测定a) 空载试验或装载试验时,不得升到高于检测温度后再降到检测温度。
b) 所有测定点的温度,在到达检测温度及其保温精度范围内的最低温度之后,以表3规定的时间间隔及测定次数测量各点温度。
c) 测温得到的读数进行修正后得到实际温度值,以这些值来判断各位置的保温精度是否满足要求。
d) 如果测温点的温度偏差超过保温精度范围,允许适当延长检测温度下的保温时间,但一个检测温度点的保温和检测总时间不得超过2 h。
表3 检测时间间隔和测量次数2.5 重复检测⑴按规定的方法所测得的数据,其中有一个测温点的保温精度不能满足要求时,应改变假定有效加热区或对热处理炉进行调整后再作重复检测。
温度均匀性测试报告

温度均匀性测试报告
1.测试依据
AMS 2750D —高温测量
GB/T 9452-2012 —热处理炉有效加热区测定方法
2.测试热电偶分布
温度均匀性测试采用九点测量法(图2.1)。
图2.1
3.温度均匀性数据采集
数据采集应在所有设备或TUS传感器达到测试温度下限后开始。
炉子应保持在测试温度直到所有测试
4.合格性判定
温度均匀性测试合格判定依据:
1、温度均匀性测试期间,TUS传感器、控制或检测传感器读数不超过设定温度的温度容差。
2、全部热电偶到温度稳定后的保温期间,TUS传感器、控制或检测传感器读数都在要求的温度容差内。
3、温度均匀性测试在规定的周期时间内进行。
温度均匀性测试报告
设备名称设备编号设备类别
测试地点测试开始时间测试结束时间
热电偶编号测试日期测温方式九点法测试温度点稳定后最高温度稳定后最低温度偏差范围/℃
~
~ 结论
有效加热区图示:
检测人日期
审核人日期。
热处理炉有效加热区测定方法
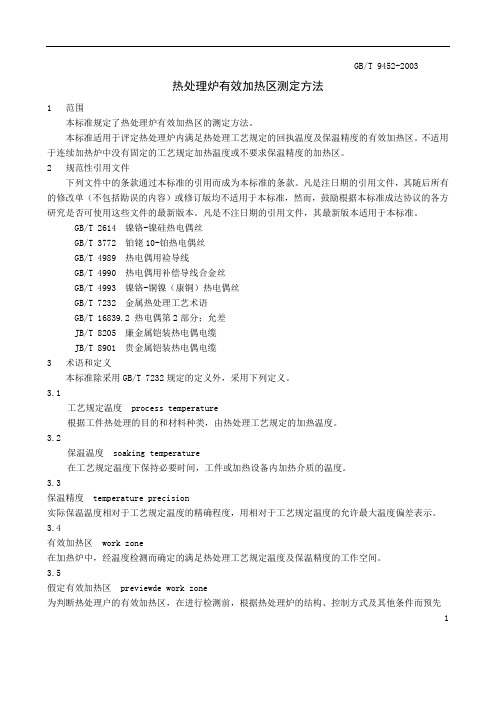
GB/T 9452-2003热处理炉有效加热区测定方法1 范围本标准规定了热处理炉有效加热区的测定方法。
本标准适用于评定热处理炉内满足热处理工艺规定的回执温度及保温精度的有效加热区。
不适用于连续加热炉中没有固定的工艺规定加热温度或不要求保温精度的加热区。
2 规范性引用文件下列文件中的条款通过本标准的引用而成为本标准的条款。
凡是注日期的引用文件,其随后所有的修改单(不包括勘误的内容)或修订版均不适用于本标准,然而,鼓励根据本标准成达协议的各方研究是否可使用这些文件的最新版本。
凡是不注日期的引用文件,其最新版本适用于本标准。
GB/T 2614 镍铬-镍硅热电偶丝GB/T 3772 铂铑10-铂热电偶丝GB/T 4989 热电偶用裣导线GB/T 4990 热电偶用补偿导线合金丝GB/T 4993 镍铬-铜镍(康铜)热电偶丝GB/T 7232 金属热处理工艺术语GB/T 16839.2 热电偶第2部分;允差JB/T 8205 廉金属铠装热电偶电缆JB/T 8901 贵金属铠装热电偶电缆3 术语和定义本标准除采用GB/T 7232规定的定义外,采用下列定义。
3.1工艺规定温度 process temperature根据工件热处理的目的和材料种类,由热处理工艺规定的加热温度。
3.2保温温度 soaking temperature在工艺规定温度下保持必要时间,工件或加热设备内加热介质的温度。
3.3保温精度 temperature precision实际保温温度相对于工艺规定温度的精确程度,用相对于工艺规定温度的允许最大温度偏差表示。
3.4有效加热区 work zone在加热炉中,经温度检测而确定的满足热处理工艺规定温度及保温精度的工作空间。
3.5假定有效加热区 previewde work zone为判断热处理户的有效加热区,在进行检测前,根据热处理炉的结构、控制方式及其他条件而预先1GB/T 9452-2003假定的测温空间,一般为热处理炉制造厂或有关标准规定的工作空间。
热处理炉炉温均匀性检测操作规程

7.相关记录
炉温均匀性检测计划表 《RCLL-001》
炉温均性检测记录表 《RCLL-002》
编制
日期
审核
日期
批准
日期
标记
处数
更改文件号
签字
日期
炉温均匀性测量记录表
炉子名称
设备 编号 设备 型号
车间
检测日期
假定有效加热区尺寸 /mm
装载量及气氛
设定温度/℃
测量结果
时间
温度传感器真实温度/℃ 1# 2# 3# 4# 5# 6# 7# 8# 9# 10#
实施条件
最大值 最小值 最大偏差 结论 检测者 备注
审核者
批准者
6.3.5 准备 TUS 炉温均匀性检测表按照热电偶排布进行排列记录,进行准备。
编ቤተ መጻሕፍቲ ባይዱ 审核 批准
日期 日期 日期
标记 处数
更改文件号
签字
日期
热处理炉温均匀性测试作业规程
共2页
第2页
6.3.6 准备工作就绪,依据产品的热处理工艺设置仪表的工作参数,热处理炉开始工作,当控温仪仪表或 TUS 热电偶中任意一个测量 点温度达到测试温度公差下限前,数字记录仪开始记录数据,每 5 分钟记录一 次,所有热电偶测量的数据(测量间隔最大不超过 5 分钟),应至少连续记录 6 组数据。数字记录仪的数据记 录格式如附件炉温均匀性检测记录表。
实施条件
编号:
最大值
最小值
最大偏差
结论
合格
检测者
备注
标准(偏差): ±10℃
审核者
批准者
炉温均匀性测量记录表
编号:
炉子名称
炉子 编号 设备 型号
车间
热处理炉高温测量解析

热处理炉高温测量解析
热处理炉高温测量是指在炉内进行高温处理过程中对温度进行测量和控制的技术。
高温测量在热处理炉中具有重要的作用,可以保证炉内温度达到设定要求,从而保证热处理效果。
高温测量的方法有多种,常用的方法包括热电偶、红外测温仪和光纤测温仪等。
1.热电偶:热电偶是一种利用热电效应测量温度的传感器。
它
由两种不同金属线材组成的热电对连接成一端,另一端与测量设备相连。
当热电对的一端暴露在高温环境中时,热电对产生的温差会产生电动势,通过测量电动势的大小来确定温度。
热电偶具有响应速度快、测量范围广、稳定性好等优点,广泛应用于炉温测量。
2.红外测温仪:红外测温仪利用物体的红外辐射来测量温度。
物体在高温下会辐射出红外光,红外测温仪通过接收物体发出的红外光,并将其转换成温度值。
红外测温仪具有接触测温、非接触测温等优点,适用于对炉内物体表面温度进行快速测量。
3.光纤测温仪:光纤测温仪是利用光纤的光学特性来测量温度的。
光纤测温原理基于光纤内部的光学信号和温度的关系,通过测量光纤热效应和热光学特性来确定温度。
光纤测温仪具有高温测量范围广、精度高、抗电磁干扰等优点,适用于炉温测量的特殊环境。
在实际应用中,根据具体的热处理工艺需求和测量要求选择合
适的高温测量方法,并进行相应的装置安装和材料选型,以确保热处理炉温度的准确测量和控制。
热处理炉有效加热区测定方法
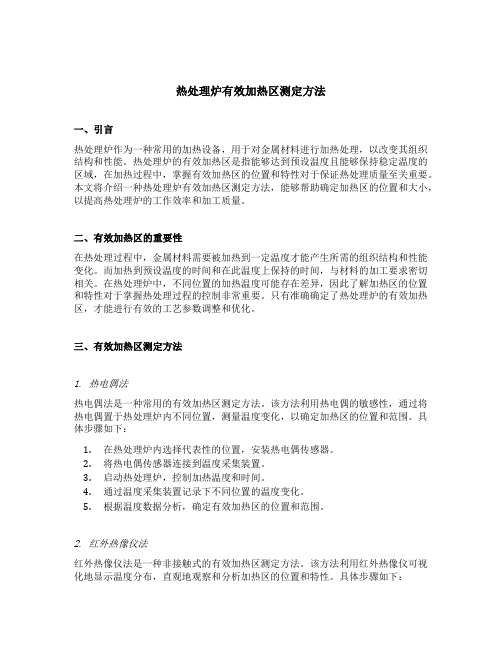
热处理炉有效加热区测定方法一、引言热处理炉作为一种常用的加热设备,用于对金属材料进行加热处理,以改变其组织结构和性能。
热处理炉的有效加热区是指能够达到预设温度且能够保持稳定温度的区域,在加热过程中,掌握有效加热区的位置和特性对于保证热处理质量至关重要。
本文将介绍一种热处理炉有效加热区测定方法,能够帮助确定加热区的位置和大小,以提高热处理炉的工作效率和加工质量。
二、有效加热区的重要性在热处理过程中,金属材料需要被加热到一定温度才能产生所需的组织结构和性能变化。
而加热到预设温度的时间和在此温度上保持的时间,与材料的加工要求密切相关。
在热处理炉中,不同位置的加热温度可能存在差异,因此了解加热区的位置和特性对于掌握热处理过程的控制非常重要。
只有准确确定了热处理炉的有效加热区,才能进行有效的工艺参数调整和优化。
三、有效加热区测定方法1. 热电偶法热电偶法是一种常用的有效加热区测定方法。
该方法利用热电偶的敏感性,通过将热电偶置于热处理炉内不同位置,测量温度变化,以确定加热区的位置和范围。
具体步骤如下:1.在热处理炉内选择代表性的位置,安装热电偶传感器。
2.将热电偶传感器连接到温度采集装置。
3.启动热处理炉,控制加热温度和时间。
4.通过温度采集装置记录下不同位置的温度变化。
5.根据温度数据分析,确定有效加热区的位置和范围。
2. 红外热像仪法红外热像仪法是一种非接触式的有效加热区测定方法。
该方法利用红外热像仪可视化地显示温度分布,直观地观察和分析加热区的位置和特性。
具体步骤如下:1.在热处理炉内启动加热过程。
2.将红外热像仪对准热处理炉内部,观察温度分布图像。
3.根据红外热像仪显示的图像,确定加热区的位置和大小。
3. 涂料膜法涂料膜法是一种简单易行的有效加热区测定方法。
该方法利用涂料对热处理炉内的温度变化敏感,通过涂料膜的变色来反映加热区的位置和特性。
具体步骤如下:1.选择适合的涂料,如温度变色油漆。
2.在热处理炉内不同位置涂上一层涂料膜。
第五章 热处理炉温温度测量技术
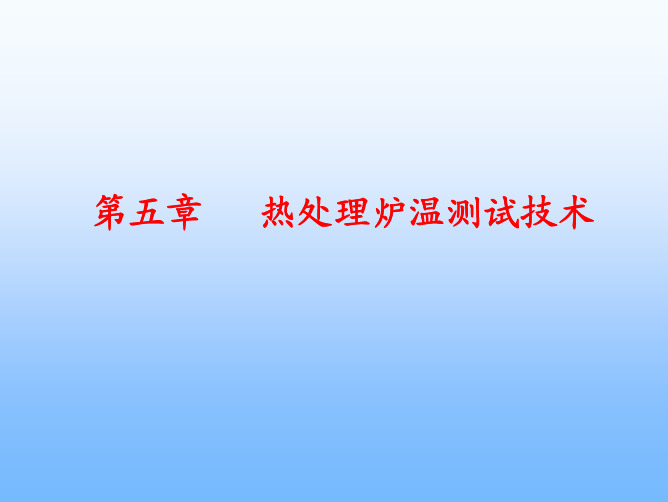
一、箱式炉温度的测量方法
1. 炉内温度分布,一般是炉门处温 度最低,电热元件附近温度最高,感 温元件一般采用热电偶。 2.中温箱式电炉,热电偶的插入位置,一般 都垂直安装在炉顶上,位于中心偏后的位置。 使其处于炉膛温度的均匀区。插入深度一般不 小于保护管外径的8~10倍。 3. 高温炉热电偶插入孔位于后墙,热 电偶需水平安装,如果插入炉内部分过长 时,需要耐火材料或耐热钢支架支撑。使 用一段时间后需转动180度。
感温元件所代表的炉温,实质上是炉膛中感温元件所 感温元件所代表的炉温,实质上是炉膛中感温元件所 在区域的介质温度,所以,炉膛温度分布的均匀性以及感 在区域的介质温度,所以,炉膛温度分布的均匀性以及感 温元件在炉膛中安装的位置是否适当,就成为感温元件是 温元件在炉膛中安装的位置是否适当,就成为感温元件是 否真却反映炉温或工件温度的重要条件。 否真却反映炉温或工件温度的重要条件。
图5-7
光导棒探头
1-光导棒 2-光导棒与光纤接头 3-光纤 4-吹气引入口
光纤比色高温计原理系统图,探头可用光导棒或透射 镜。光纤所传递的辐射光没有选择性,在通过调制盘2时, 由于调制盘上两半圆上的红外滤波片不同,在一个半周内通 过的波长为λ1,在另一个半周内通过的波长为λ2。两束波 长交替投射到光敏元件上,产生不同的光电流I1和I2,交替 送入比值放大器,在同步信号驱动下,分别进行放大后,进 行比值计算,运算后的比值信号经线性化处理、A/D转换后 送入数字显示仪显示。
图5-3 全辐射高温计示意图 1-物镜 2-热电偶 3-目镜 4-温度显示仪表
图5-4 瞄准时的图像
实际上,辐射高温计的热敏感元件不只是一只热电 偶,而是一组(8对或16对)直径为0.05~0.07mm的镍铬- 考铜热电偶串联组成的热电堆,热电偶的热接点焊在涂有 铂黑的瓣形镍箔上(图5-4中的8片对称排列的黑色扇形 片,又称为靶心)。热电偶的冷端由考铜箔串连起来。为 了自动补上环境温度变化带来的误差,采用了双金属片补 偿光栅(图5-4中右下方遮住瓣形镍箔的黑影即光栅), 其位置可根据输出值的高低进行调整。
- 1、下载文档前请自行甄别文档内容的完整性,平台不提供额外的编辑、内容补充、找答案等附加服务。
- 2、"仅部分预览"的文档,不可在线预览部分如存在完整性等问题,可反馈申请退款(可完整预览的文档不适用该条件!)。
- 3、如文档侵犯您的权益,请联系客服反馈,我们会尽快为您处理(人工客服工作时间:9:00-18:30)。
热处理炉有效加热区测定方法
1、适用范围
本规程规定了铸钢件用热处理炉有效加热区的测定方法。
本规程适用于铸钢件退火、正火、淬火、回火热处理炉工况的空载测试及有效加热区的评定。
2、引用标准:
GB/T16923 钢件的正火与退火
GB/T16924 钢件的淬火与回火
GB/T9425 热处理炉有效加热区测定方法
GB/T2614 镍铬—镍硅热电偶丝
GB/T4989 热电偶用补偿导线
GB/T4990 热电偶用补偿导线合金丝
GB/T7232 金属热处理工艺术语
GB/T16839.2 热电偶第2部分:允差
GB/T18404 铠装热电偶电缆及铠装热电偶
3、术语
本规程引用的术语为GB/T9425、GB/T7232中的术语。
3.1 工艺规定温度
根据工件热处理的目的和材料种类,由热处理工艺规定的加热温度。
3.2 保温温度
在工艺规定温度下保持必要的时间,工件或加热设备内加热介质的温度。
3.3 保温精度
实际保温温度相对于工艺规定温度的精确程度,用相对于工艺规定温度的允许最大温度偏差表示。
3.4 有效加热区
经温度检测而确定的满足热处理工艺规定的温度计保温精度的工作空间。
4、铸钢厂热处理炉的保温精度
表1 热处理炉保温精度
炉子名称 热处理炉类别 有效加热区保温精度℃ 仪表指示精度不低于%
1#热处理炉 Ⅲ ±10℃ 0.5
2#热处理炉 Ⅲ ±10℃ 0.5
3#热处理炉 Ⅲ ±10℃ 0.5
4#热处理炉 Ⅲ ±10℃ 0.5
5#热处理炉 Ⅲ ±10℃ 0.5
6#热处理炉 Ⅲ ±10℃ 0.5
7#热处理炉 Ⅲ ±10℃ 0.5
5、测温装置
5.1 热电偶及补偿导线
根据检测温度计要求的保温精度,按表3选择热电偶,热电偶应符合GB/T2614。
补偿导线应符合GB4989、GB4990、GB/T18404的规定。
表2检测用热电偶
热电偶名称 分度号 等级 使用温度℃ 允许偏差℃ 检定周期
镍铬—镍硅 K Ⅱ 0-1200 ±0.75%t 半年
注:t为被测温度
表3检测用补偿导线
热电偶分度号 补偿导线型号 补偿导线名称 代号 温度范围℃ 允差℃
K KX 镍铬10-镍硅3延长型导线 KX-GS -20—100 ±1.5
5.2 检测仪器
检测仪器用精度不低于0.5级,使用有纸记录仪—富士PHA88004-EA0YV 记录仪。
5.3 测温架
检测用测温架用不锈钢钢管焊接而成,用来固定热电偶,为确保其不变形,测温架需增加焊接加强筋。
6、检测方法 6.1 检测要求
6.1.1 热处理炉有效加热区的检测,一般采用空载试验,特殊要求时可以进行装载试验(半装载试验或满载试验)。
6.1.2 测试时,热处理炉应以常用升温速度升温。
6.2 检测点的数量和位置
铸钢厂热处理炉有效加热区温度检测点的数量和位置示意图详见图1—图6.
450m m ;约350m m ;
图1:1#热处理炉有效加热区示意图
6
450m m ;膛约300m m ;
图2:2#热处理炉有效加热区示意图
6
450m m ;
膛约350m m ;
图3:3#热处理炉有效加热区示意图
6
450m m ;膛约300m m ;
图4:4#、5#热处理炉有效加热区示意图
6
400m m ;膛约350m m ;
图5:6#热处理炉有效加热区示意图
450m m ;约350m m ;
图6:7#热处理炉有效加热区示意图
6.3 检测温度
结合铸钢厂热处理炉的实际使用情况,各台热处理炉的检测温度如下表所示。
设备名称 主要用途 常用工艺温度
空炉检测温度
实炉检测温度
1#热处理炉
铸件的退火、正火及回火
910±10℃、880±10℃、650±10℃、560±10℃
910±10℃、650±10℃ 根据工艺执行
2#热处理炉 铸件的退火、
正火、回火及
淬火 910±10℃、880±10℃、
560±10℃、650±10℃
910±10℃、650±10℃ 根据工艺执行
3#热处理炉 铸件的退火、
正火、回火及
淬火 1100±10℃、910±10℃
880±10℃、560±10℃
650±10℃
1100±10℃、
650±10℃
根据工艺执行
4#热处理炉 铸件的退火、
正火、回火 910±10℃、880±10℃、
560±10℃
910±10℃、650±10℃ 根据工艺执行
5#热处理炉 铸件的退火、
回火 910±10℃、880±10℃、
650±10℃、560±10℃
910±10℃、650±10℃ 根据工艺执行
6#热处理炉 铸件的退火、
正火及回火 910±10℃、880±10℃、
650±10℃、560±10℃
910±10℃、650±10℃ 根据工艺执行
7#热处理炉 铸件的退火、
正火及回火 910±10℃、880±10℃、
650±10℃、560±10℃
910±10℃、650±10℃ 根据工艺执行
6.4、检测顺序及方法
6.4.1 所用的检测仪器、热电偶、补偿导线必须在检定周期内。
6.4.2 测量装置的接线
6.4.2.1 用铁丝将铠装热电偶牢固的绑扎在测温架的每个测温位置上。
6.4.2.2 将铠装热电偶参考端引出炉外,在方便的位置通过补偿导线、铜导线与检测仪器连接,安装时应防止由于引出线安装不当而影响炉温测量。
6.4.2.3 装载试验时,热电偶测量端应尽可能和铸件接近。
6.4.3 温度测定
6.4.3.1 空载试验或装载试验时,不得升到高于检测温度后在降到检测温度。
6.4.3.2 所有测温点的温度,在到达检测温度及其保温精度范围内的最低温度之后,均温0.5小时后,以10分钟每次的频率记录各点的温度。
次数≥8次。
6.4.3.3 如果测温点的温度偏差超过保温精度范围,允许适当延长检测温度下的保温时间,但是一个检测温度点的保温和检测总时间不得超过2小时,
7、有效加热区的评定
通过上述方法检测,假定有效加热区各点的温度均在工艺规定的保温精度范围内时,则该空间为该热处理炉的有效加热区。
8、记录
有关检测结果包含如下内容:
a、实施的条件及空载或装载情况;
b、热处理炉的名称、型号、类别、主要技术参数、制造单位及日期;
c、常用温度、检测温度及保温精度;
d、测温装置的名称、型号、类别、精度及检定日期;
e、假定有效加热区的尺寸及检测点示意图;
f、使用的燃气种类;
g、装载试验的装载量、铸件特性(材料、尺寸及重量等);
h、各检测点测温时间及温度显示值,数据处理;
i、有效加热区判定结果及检验合格证;
j、检测日期;
k、责任者(检测者、审核者、批准者姓名)
(详见测试报告)
9、判定
9.1 检测结果符合表1的要求,合格后由设备科填写合格证,装载试验由技术科根据检测结果及实物检
测情况进行综合评价。
9.2 若经检测炉况不符合要求时,则不可投入使用,对其进行修理、调整后,再对其进行检测,直到满足要求为止。
10、检测周期
检测周期为六个月,连续三个周期检测合格、使用正常的热处理炉,其测定周期可延长至一年。
11、管理
11.1 热处理炉炉况的测试由设备科统一组织实施,判定结果并出具合格证;生产科按测试周期的需要,合理安排测试时间;技术科提供工艺要求并监督实施、综合评价;清铲工部负责支架、铠装热电偶的安装,并按技术科提供的工艺要求进行操作;机修负责支架的制作及记录仪的记录。
11.2 测定结果须经技术主管领导签字确认。
11.3 热处理炉炉况测定的全部原始记录,按技术管理制度存入档案。
11.4 设备操作人员发现热处理炉运行中有如下影响炉温均匀性不稳定因素,及时通知相关部门进行处理,同时通知技术部门该热处理炉的状况,由技术部门判定该台热处理炉是继续运行,还是重新按工艺点炉。
a、某一点温度同超出设定温度要求的±10℃;
b、某个烧嘴点不着火;
c、某个烧嘴上位机上显示点火,但对应该点的温度远远低于设定温度;
d、某个烧嘴一直熄火;
e、助燃空气及煤气压力低于设定值压力;
f、炉压超出设定压力值;
g、某个烧嘴火焰上漂或者无力;。