陶瓷工艺学第十讲 陶瓷成型(干法成型)2014
陶瓷粉末成型工艺
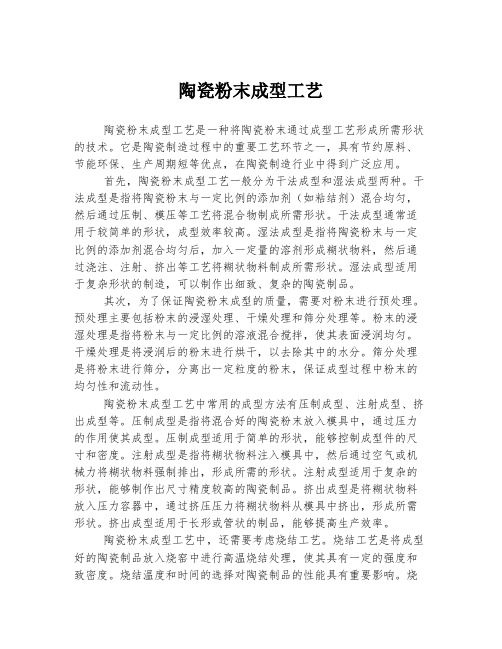
陶瓷粉末成型工艺陶瓷粉末成型工艺是一种将陶瓷粉末通过成型工艺形成所需形状的技术。
它是陶瓷制造过程中的重要工艺环节之一,具有节约原料、节能环保、生产周期短等优点,在陶瓷制造行业中得到广泛应用。
首先,陶瓷粉末成型工艺一般分为干法成型和湿法成型两种。
干法成型是指将陶瓷粉末与一定比例的添加剂(如粘结剂)混合均匀,然后通过压制、模压等工艺将混合物制成所需形状。
干法成型通常适用于较简单的形状,成型效率较高。
湿法成型是指将陶瓷粉末与一定比例的添加剂混合均匀后,加入一定量的溶剂形成糊状物料,然后通过浇注、注射、挤出等工艺将糊状物料制成所需形状。
湿法成型适用于复杂形状的制造,可以制作出细致、复杂的陶瓷制品。
其次,为了保证陶瓷粉末成型的质量,需要对粉末进行预处理。
预处理主要包括粉末的浸湿处理、干燥处理和筛分处理等。
粉末的浸湿处理是指将粉末与一定比例的溶液混合搅拌,使其表面浸润均匀。
干燥处理是将浸润后的粉末进行烘干,以去除其中的水分。
筛分处理是将粉末进行筛分,分离出一定粒度的粉末,保证成型过程中粉末的均匀性和流动性。
陶瓷粉末成型工艺中常用的成型方法有压制成型、注射成型、挤出成型等。
压制成型是指将混合好的陶瓷粉末放入模具中,通过压力的作用使其成型。
压制成型适用于简单的形状,能够控制成型件的尺寸和密度。
注射成型是指将糊状物料注入模具中,然后通过空气或机械力将糊状物料强制排出,形成所需的形状。
注射成型适用于复杂的形状,能够制作出尺寸精度较高的陶瓷制品。
挤出成型是将糊状物料放入压力容器中,通过挤压压力将糊状物料从模具中挤出,形成所需形状。
挤出成型适用于长形或管状的制品,能够提高生产效率。
陶瓷粉末成型工艺中,还需要考虑烧结工艺。
烧结工艺是将成型好的陶瓷制品放入烧窑中进行高温烧结处理,使其具有一定的强度和致密度。
烧结温度和时间的选择对陶瓷制品的性能具有重要影响。
烧结温度过高会使陶瓷制品变形或烧结不充分,烧结温度过低则会影响陶瓷制品的力学性能和致密度。
陶瓷工艺学第十章烧成与窑具

第四节 窑具
4.1 窑具种类 匣钵、棚板、支柱、各种耐火垫、
托板、辊棒和窑车材料等。
现代窑炉的重要标志之一,就是大幅度 减少了窑具的用量,采用多种高级耐火材料 窑具,满足快速烧成的需要。
4.2窑具的性能要求 (1)足够的结构强度
常温强度和高温强度
(2)良好的抗热震性能 破坏机理:裂纹不断扩展; 热膨胀系数小,产生应力小,不易破坏 熟料和基质的相互关系;相对量的多少 影响较大。
理论温度制度曲线
1400 1200 1000 800 600 400
200
脆性生坯
厚坯 薄坯
热塑性范围
中火保温
脆性瓷器
时间
1.2.2.3 釉烧方法
(1)一次烧成时,釉料的熔化温度与坯料的氧化分解 温度相适应,中火保温防止针孔、橘釉、黑心、鼓泡 等缺陷。 (2)冷却初期依据釉料要求确定冷却速度
光泽釉——快速冷却 结晶釉——结晶温度保温处理 (3)二次烧成 高温素烧低温釉烧:釉烧时可以不考虑坯体的脱 结构水及 氧化分解排气,素烧 时不考虑与釉的关系。 低温素烧高温釉烧:釉烧时可以不考虑 坯体的脱结构 水,要考虑氧化分解,素 烧时不考虑与釉的关系。
不同烧结温度及高温保温时间对产品性能的影响
注:摘自《陶瓷研究》杨世源
烧成温度(℃) 保温时间(min) 平均吸水率(%)
1020
30
16.4
1040
30
15.7
1060
30
14.92
1080
30
14.10
1100
30
13.92
1080
5
14.96
1080
15
14.7
1080
30
陶瓷成型方式
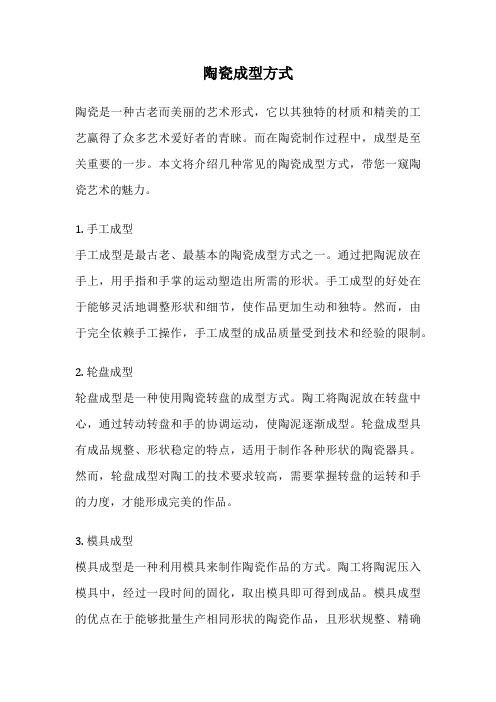
陶瓷成型方式陶瓷是一种古老而美丽的艺术形式,它以其独特的材质和精美的工艺赢得了众多艺术爱好者的青睐。
而在陶瓷制作过程中,成型是至关重要的一步。
本文将介绍几种常见的陶瓷成型方式,带您一窥陶瓷艺术的魅力。
1. 手工成型手工成型是最古老、最基本的陶瓷成型方式之一。
通过把陶泥放在手上,用手指和手掌的运动塑造出所需的形状。
手工成型的好处在于能够灵活地调整形状和细节,使作品更加生动和独特。
然而,由于完全依赖手工操作,手工成型的成品质量受到技术和经验的限制。
2. 轮盘成型轮盘成型是一种使用陶瓷转盘的成型方式。
陶工将陶泥放在转盘中心,通过转动转盘和手的协调运动,使陶泥逐渐成型。
轮盘成型具有成品规整、形状稳定的特点,适用于制作各种形状的陶瓷器具。
然而,轮盘成型对陶工的技术要求较高,需要掌握转盘的运转和手的力度,才能形成完美的作品。
3. 模具成型模具成型是一种利用模具来制作陶瓷作品的方式。
陶工将陶泥压入模具中,经过一段时间的固化,取出模具即可得到成品。
模具成型的优点在于能够批量生产相同形状的陶瓷作品,且形状规整、精确度高。
但是,模具成型的缺点是缺乏个性化和创新性,作品容易呈现出机械化的感觉。
4. 雕塑成型雕塑成型是一种将陶泥切割、雕刻和拼接成作品的方式。
陶工通过刀具和雕刻工具的运用,将陶泥打磨成所需的形状和纹理,然后通过拼接的方式组合成完整的作品。
雕塑成型的优点在于能够表达出更多的细节和艺术感,作品具有立体感和层次感。
然而,雕塑成型的过程较为复杂,需要陶工具备较高的技术和创意。
以上几种陶瓷成型方式各具特点,可以根据作品的需求和陶工的技术选择合适的成型方式。
无论是手工成型还是轮盘成型、模具成型或者雕塑成型,每一种方式都有其独特的魅力和挑战。
通过不同的成型方式,陶瓷作品才能展现出多样化的形态和风格,让人们在欣赏中体验到陶瓷艺术的无穷魅力。
陶瓷成型方式的选择是陶工艺术创作中不可或缺的一环,它直接关系到作品的形态和质量。
不同的成型方式在陶瓷作品的形成过程中各自发挥着重要的作用,也对陶工的技术和创意提出了不同的要求。
陶瓷成型工艺流程

陶瓷成型工艺流程
《陶瓷成型工艺流程》
陶瓷成型工艺是指将原料经过一系列的加工工序,最终成为陶瓷制品的过程。
其中,成型工艺是整个陶瓷制作过程中的重要一环,直接影响着陶瓷制品的成型质量和外观。
首先,成型工艺的第一步是原料的准备。
一般陶瓷的原料包括粘土、石英砂、长石等,这些原料要经过混合、过筛等工序,确保原料的均匀性和杂质的去除。
接下来是成型工艺的制胚工序。
这一步通常包括挤压成型、注塑成型、手工成型等工艺。
其中,挤压成型是利用成型机将原料挤压成一定形状的坯体,注塑成型是将原料注入成型模具中进行成型,而手工成型则是通过手工操作将原料成型为所需的形状。
不同的成型方式会直接影响到陶瓷制品的成型质量和成本。
成型工艺的下一步是干燥工序。
这一步是为了将成型后的坯体中的水分蒸发干净,使得坯体可以进一步进行烧制工序。
通常会采用自然晾晒或者利用烘干设备进行干燥处理。
最后,成型工艺的最后一步是修整工序。
这一步包括修整坯体表面、刻花、打磨等工序,使得坯体表面更加光滑,符合设计要求。
总的来说,《陶瓷成型工艺流程》是一个包括原料准备、制胚、
干燥和修整工序的系统工艺流程。
通过严谨的工艺流程和精细的操作,可以制作出高质量的陶瓷制品。
陶瓷成型原理
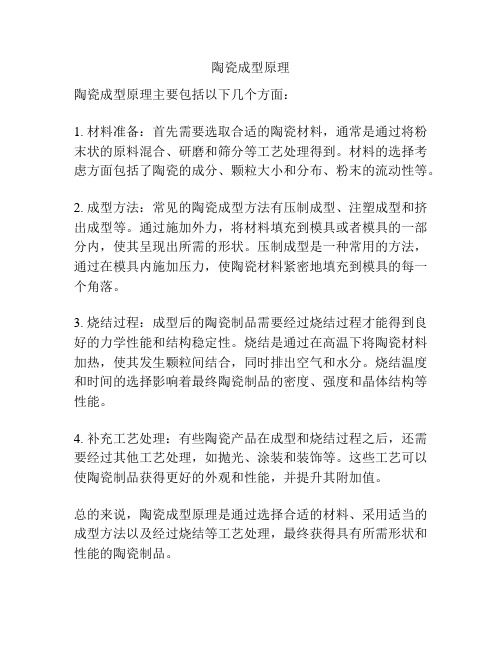
陶瓷成型原理
陶瓷成型原理主要包括以下几个方面:
1. 材料准备:首先需要选取合适的陶瓷材料,通常是通过将粉末状的原料混合、研磨和筛分等工艺处理得到。
材料的选择考虑方面包括了陶瓷的成分、颗粒大小和分布、粉末的流动性等。
2. 成型方法:常见的陶瓷成型方法有压制成型、注塑成型和挤出成型等。
通过施加外力,将材料填充到模具或者模具的一部分内,使其呈现出所需的形状。
压制成型是一种常用的方法,通过在模具内施加压力,使陶瓷材料紧密地填充到模具的每一个角落。
3. 烧结过程:成型后的陶瓷制品需要经过烧结过程才能得到良好的力学性能和结构稳定性。
烧结是通过在高温下将陶瓷材料加热,使其发生颗粒间结合,同时排出空气和水分。
烧结温度和时间的选择影响着最终陶瓷制品的密度、强度和晶体结构等性能。
4. 补充工艺处理:有些陶瓷产品在成型和烧结过程之后,还需要经过其他工艺处理,如抛光、涂装和装饰等。
这些工艺可以使陶瓷制品获得更好的外观和性能,并提升其附加值。
总的来说,陶瓷成型原理是通过选择合适的材料、采用适当的成型方法以及经过烧结等工艺处理,最终获得具有所需形状和性能的陶瓷制品。
陶瓷成型技术

项目1:注浆成型技术
一、注浆成型 传统的定义:在石膏模的毛细管力作用下,含有一 定水分的粘土泥浆脱水硬化、成型的过程。 目前:将所有基于坯料具有一定液态流动性的成型 方法统归为注浆成型。 工艺特点: (1)适于成型各种产品,形状复杂、不规则、薄、 体积较大而且尺寸要求不严的器物,如花瓶、汤碗、 椭圆形盘、茶壶等。 (2)坯体结构均匀,但含水量大且不均匀,干燥 与烧成收缩大。
防止粉化的方法有: ①适当降低模型的干燥速度,使水分能够从模型四 周均匀地蒸发; ②采取提前合模的办法,夜间让模型整体干燥,因 模型湿不宜提前合模的,可在芯子上部盖塑料布, 以防止大量的水分从顶点蒸发; ③待模型的外吃浆面刮去一层,增加透气性,使水 分向外吃浆面蒸发。
5、延长石膏模型的使用寿命 1)石膏模型有一定的使用寿命,一般可塑成型用 模型的使用寿命约100-250次,注浆成型用模型只 有50-150次。其损坏原因主要有以下三方面:其 一是模型本身强度不高,易被碰裂或压裂;其二是 模型工作面被坯料中泥粒磨损而报废;其三是注桨 用模型由于模型与坯料桨中电解质起休化学反应造 成模型的毛细孔中与表面上产生硫酸钠析晶,而降 低吸水能力。
石膏模的寿命不但取决于合理的使用,还与制模的 石膏质量和操作工艺过程有关。如石膏粉炒温度过 高或过低,石膏粉颗粒粗大,浇注时加水过多,混 合不均匀,制备好的石膏粉放在潮湿的地方等情况 均会影响模型使用寿命。 2)为了延长石膏模的使用寿命,应正确掌握制造 模型的工艺操作和合理使用外,还可从提高石膏模 的机械强度入手。
各类产品尽管加工方法不同,但是坯体修整是必要 的,不可忽视的,否则就不能保证瓷器半成品质量。 在修坯中也要防止坯体产生缺陷,并修整那些能修 整的带缺陷的坯体。 修坯分为干修和湿修两种方式。 湿修:坯体的水分16~19%。 干修:坯体的水分 < 2%。
工艺学实验报告 - 干压成型制作陶瓷片
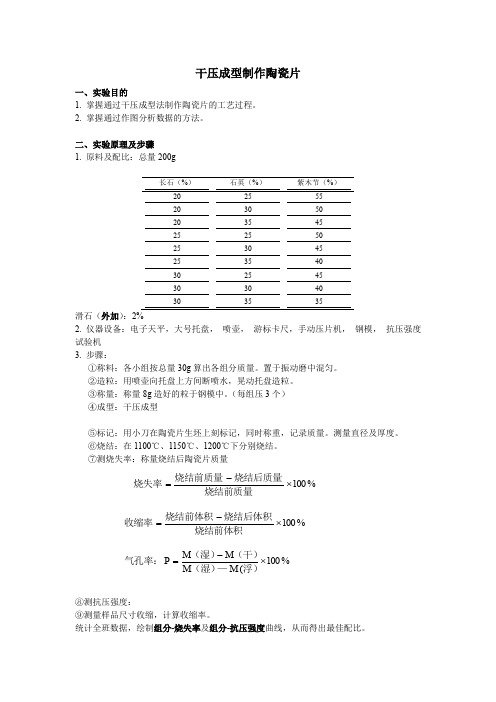
干压成型制作陶瓷片一、实验目的1. 掌握通过干压成型法制作陶瓷片的工艺过程。
2. 掌握通过作图分析数据的方法。
二、实验原理及步骤1. 原料及配比:总量200g长石(%)石英(%) 紫木节(%) 20 25 55 20 30 50 20 35 45 25 25 50 25 30 45 25 35 40 30 25 45 30 30 40 滑石(外加):2%2. 仪器设备:电子天平,大号托盘, 喷壶, 游标卡尺,手动压片机, 钢模, 抗压强度试验机3. 步骤:①称料:各小组按总量30g 算出各组分质量。
置于振动磨中混匀。
②造粒:用喷壶向托盘上方间断喷水,晃动托盘造粒。
③称量:称量8g 造好的粒于钢模中。
(每组压3个)④成型:干压成型⑤标记:用小刀在陶瓷片生坯上刻标记,同时称重,记录质量。
测量直径及厚度。
⑥烧结:在1100℃、1150℃、1200℃下分别烧结。
⑦测烧失率:称量烧结后陶瓷片质量%100⨯-=烧结前质量烧结后质量烧结前质量烧失率 %100⨯-=烧结前体积烧结后体积烧结前体积收缩率 %100(⨯-=浮)—(湿)(干)(湿)气孔率:M M M M P⑧测抗压强度:⑨测量样品尺寸收缩,计算收缩率。
统计全班数据,绘制组分-烧失率及组分-抗压强度曲线,从而得出最佳配比。
三、实验总结实验数据记录如下:在1000℃下烧结得到的数据及图形在1150℃下烧结的数据及图形在1200℃下烧结的数据及图形结论:通过以上数据分析可得出:当在1000摄氏度时,8—1配比下所得的样品抗压强度较好,烧失率和收缩率比较低;在1150摄氏度下,5—2配比时所得的配比好;在1200摄氏度时,7—3下配比好。
误差分析:(1)由于在制料的过程中操作错误而导致误差(2)在烧结的过程中由于不同温度下导致受热不均匀程度不同导致误差(3)在称量读数时不准确导致误差体会:本次试验中,通过干压成型法制作陶瓷片加深了我对这一制作工艺流程了解与认识,在实验过程中,经历了配料、造粒、成型和烧结这几个步骤,每个步骤都需要仔细准确操作,对于不懂的地方时刻向学长请教,其中,喷水量的多少一定要掌握好,否则,对成型颗粒结果影响很大;除此之外,在压片过程中也要把我好压力适度,压力过大或者过小都会影响成形结果,当压好从模具里脱模时也要小心,因为陶瓷片还没经过烧结,强度很低,不小心就容易损坏;最后,我明白了要作为一个合格的研究科研人员,必须具备细心、耐心等态度,对待科学是需要严谨的,只有这样才能在将来的学术上出很好的成果。
陶瓷材料成型
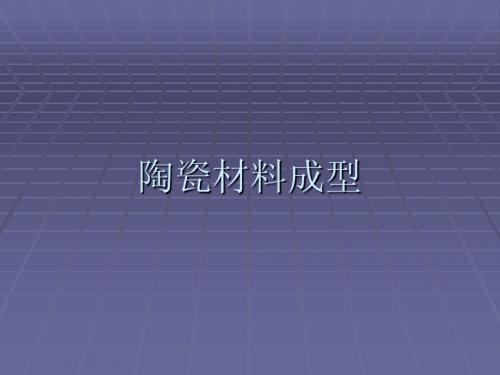
干燥基本理论知识
干燥基本原理 干燥定义:排出坯体中水分的工艺过程称为干燥。 坯体中所含水分的类型及其结合形式 1、化学结合水:物料矿物分子组成内的水分。又 称结构水。干燥过程中不能除去。 2、吸附水:物料内存在很多毛细管,存在其内的 即为吸附水。 3、自由水:存在于物料表面的润湿水分以及孔隙 中的水分。
排除吸附水时,不发生收缩,不产生应力。
干燥基本理论知识
干燥的过程 干燥可以分为四个阶段: 升温阶段:含水率下降、干燥速度上升、坯体表
面温度上升。 等速干燥阶段:含水率下降、干燥速度不变、坯 体表面温度不变。 降速干燥阶段:含水率下降、干燥速度下降、坯 体表面温度上升。 平衡阶段:含水率不变、干燥速度为零。
一车间压制工段部分技术参数
1、粉料过筛:10目 2、粉料水分:6.3~6.8% 两个仓以上混合使用 3、压制参数 3.1平面立体:凹凸面 坯重:1160±20g 厚度:8.1~8.2 mm 压力:280bar 3.2文化石: 坯重:1420±20g 厚度:5.5 mm 压力:250bar 3.3树皮纹: 坯重:1500±20g 厚度:10.3~10.颗粒之间以及颗粒与模壁 之间产生摩擦力,摩擦力的不均匀分布导致坯体 中压力分布不均匀。
陶瓷材料成型
影响坯体致密度的因素
一、成型压力 施加于粉料上的压力主要消耗在克服粉料的阻 力以及克服颗粒对模壁的摩擦力,所以成型压力 的确定要依据粉料的组成和性质以及坯体的大小 和形状。 二、加压方式 2.1 加压有单面加压、双面同时加压、双面先后 加压和六面加压等几种方式。在墙地砖生产中应 用前三种方式。
坯体强度的变化
在坯体压制过程中坯体强度与压制力呈现规 律变化。压制力较小会使坯体强度不够,压制力 过大会造成动力浪费。
- 1、下载文档前请自行甄别文档内容的完整性,平台不提供额外的编辑、内容补充、找答案等附加服务。
- 2、"仅部分预览"的文档,不可在线预览部分如存在完整性等问题,可反馈申请退款(可完整预览的文档不适用该条件!)。
- 3、如文档侵犯您的权益,请联系客服反馈,我们会尽快为您处理(人工客服工作时间:9:00-18:30)。
4. 分散剂
❖ 分散剂的作用
也叫抗絮凝剂、减水剂或解凝剂,用于 使陶瓷粉体在液体系统中均匀分布而不 产生絮凝,增强流动性。
4. 分散剂
❖ 分散剂的分类 ➢无机盐:无机磷酸盐、硅酸盐及硼酸盐等。 ➢表面活性剂:阴离子、阳离子、两性离子
及非离子表面活性剂。
➢中低分子量的聚合物:聚环氧乙烷、聚
乙二醇及聚乙烯 醇等。
混合一般采用机械混合法,即采用球磨或搅拌的方 法,在原料粉碎的同时进行混合,有时还采用化学混合 法,即将化合物粉末与添加组分的盐溶液进行混合或者 各组分全部以盐溶液的形式进行混合。
配料混合时必须注意加料的次序和加料的方法,以 保证配料的准确性和混合的均匀性。
(Ba0.85Sr0.15)TiO3配料计算
1. 粘结剂(binders) 2. 塑性剂(plasticizers) 3. 溶剂(solvents) 4. 分散剂(dispersants)
1. 粘结剂
❖ 粘结剂的作用
通过包裹粉料颗粒,自身固化形成表面 和产生三维相互连接的强的树脂构架, 赋予素坯一定的强度和韧性。
1. 粘结剂
❖ 粘结剂的种类
2. 塑性剂
❖ 塑性剂的作用
➢降低粘结剂的塑限温度Tg,使Tg达到室温 或室温以下,从而确保粘结剂在室温时具有 好的流动性和不发生凝结; ➢对粉体颗粒还起润滑和桥联作用,有利于 料浆的分散稳定。
2. 塑性剂
加入塑性剂会使素坯膜的强度降低
2. 塑性剂
❖ 塑性剂的种类 中低分子量的高分子。
最常用的塑性剂有聚乙二醇、邻苯二 甲酸脂、乙二醇等。
3. 溶剂(solvents)
❖ 常用溶剂的物理性质
3. 溶剂(solvents)
❖ 选择溶剂主要考虑的因素:
a) 溶解分散剂、粘结剂和塑性剂; b) 分散陶瓷粉料; c) 在浆料中保持化学稳定性,不与粉料发生化
学反应; d) 提供浆料合适的粘度; e) 在适当的温度蒸发与烧除; f) 保证素坯无缺陷的固化; g) 使用安全卫生和对环境污染少且价格便宜。
4) 塑性剂
3.溶剂(solvents)
❖ 溶剂的作用 ➢ 在混合或成型过程中提供流动性; ➢ 溶解其它的添加剂。
3.溶剂(solvents)
❖ 溶剂分类 ➢ 通用分类
✓ 有机:乙醇、丙酮及二元共聚的有机物。 ✓ 无机: 水。
➢ 按极性分类
✓ 极性(Polar) ✓ 非极性或弱极性(Nonpolar or Weakly Polar) ✓ 氢键结合(Hydrogen Bonding)
4.2 陶瓷成型
(Forming of Ceramics)
日用瓷
建筑瓷
卫生瓷
艺术瓷
结构陶瓷
蜂窝陶瓷
1.陶瓷制备工艺
陶瓷刀具
电真空陶瓷管
热敏陶瓷
陶瓷种类众多,形态也多种多样。 如何制备的呢? 制备工艺与性能的关系又如何呢?
陶瓷材料学家比较重视烧结工艺,而成型 工艺一直是个薄弱环节,不被人们所重视。 现在,人们已经逐渐认识到,除了烧结过 程之外,成型过程也是一个重要环节,是 陶瓷生产过程的一个重要步骤。在成型过 程中形成的某些缺陷(如不均匀性等) 仅 靠烧结工艺的改进是难以克服的。
破坏滑石的层状结构, 预烧温度一般在1300~1500ºC之间,
避免定向排列,降低 加矿化剂(如苏州土、硼酸、碳酸钡
收缩,减少瓷件开裂, 等)可降低预烧温度,含Fe2O3时,可
同时也有利于粉磨
采用还原气氛
二 配料与混合
配料就是按照瓷料的组成,将所需要的各种原料进 行称量,称量务必精确。配料是陶瓷工艺中最基本的一 环。
粉料堆积的拱桥效应
Bimodal mixing of spheres
14
四 陶瓷成型用添加剂 (Additives)
陶瓷粉料绝大多数为脊性料,因此如果想获得 足够强度的素坯常需要一些添加剂。
主要包括: • 溶剂 • 分散剂 • 粘结剂 • 塑性剂等
常用的添加剂分有机和无机两大类,在新型陶 瓷中以有机添加剂为主。
➢配料制备 ➢混合 加料的次序 加料的方式 湿法混合时的分层 球磨筒的使用
三 颗粒的堆积 (Packing of Particles)
Particles on Packing density
12
颗粒的形态与拱桥效应
柱状、针状、片状、 球状、多面体状等。 拱桥效应:粉料堆积空隙率>理论值
• 热塑性:聚乙烯(PE)、无规聚丙烯 (APP)、 EVA、 PS、 PMMA。 • 热固性: 环氧树脂, 酚醛树脂等 • 水溶性: 纤维素醚等
❖ 粘结剂的种类
1. 粘结剂
❖选择粘结剂需要考虑的因素
➢ 素坯的厚度; ➢ 选溶剂类型及其匹配性,要不妨碍溶剂挥发和不产 生气泡; ➢ 易于排除,不留残余物; ➢能起到稳定浆料和抑制颗粒沉降作用; ➢要有较低的塑性转变温度,以确保在室温下不发生 凝结; ➢考虑所用衬垫材料的性质,要不相粘和易于分离。
疏松、气孔
开裂
成型工艺已经成为制备高性能陶瓷材料部 件的关键技术,它对提高陶瓷材料的均匀 性、重复性和成品率,降低陶瓷制造成本 具有十分重要的意义。
2.陶瓷成型过程及分类
❖ 成型过程
就是将分散体系(粉料、塑性物料、浆料) 转变成为具有一定几何形状和强度的块 体(素坯)的过程。
2.陶瓷成型过程及分类
❖ 成型技术分类
陶瓷是一门粉体科学技术,按照粉末原 料在成型前的状态可以将陶瓷粉末的成型 技术分为三类:
I. 干法成型 II. 塑性成型 III. 浆料成型 IV. 自由实体制造或快速无模成型
原料
预烧目的
预烧条件
Al2O3 MgO
使γ-Al2O3转化为α-
采用H3BO3作添加剂时,预烧温度
Al2O3,提高原料纯度, 1400~1450ºC左右,保温2~3h。采
改善产品性能
用NH4F作添加剂时,预烧温度1250ºC,
保温1~2h
提高MgO的活性,改 预烧温度在1400ºC以上 善水化性能
滑石
第三部分 陶瓷的成型
一、 陶瓷粉体预处理
1 酸洗与磁选 酸洗主要是将一定浓度(30%)的盐溶液注入原料中,加热
以除掉其中有害的铁杂质。 磁洗是利用铁的磁性质,使物料通过强大的磁场,铁质杂
质等被磁场吸引而从原料中。分离出来。
2 预烧 预烧工艺的关键是预烧温度、预烧气氛及外加剂的选择。
常用原料的预烧目的与预烧条件