注塑工艺及缺陷案例全解
注塑产品缺陷及图示
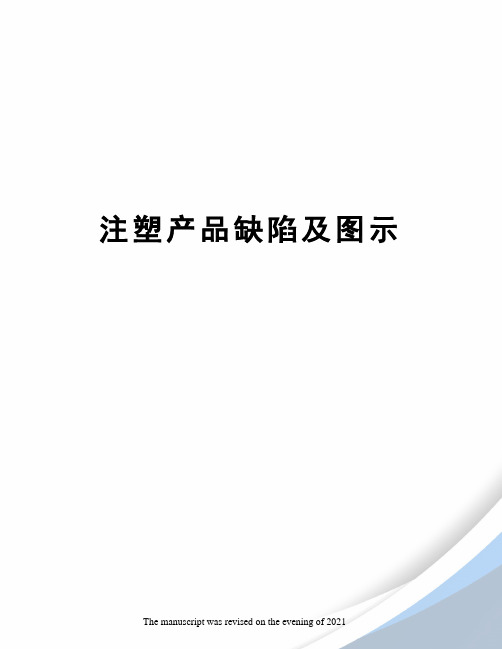
注塑产品缺陷及图示 The manuscript was revised on the evening of 2021第一节飞边飞边又称溢边,披锋,毛利等,大多发生在模具的分合位置上,如动模和定模分型面如图,滑块的滑配部位,镶件的缝隙,顶杆孔等处如下图:图2-1-1 图2-1-2我们常用的处理工具为毛利刀,对于不同部位的包毛刺将采取不同的处理方法:1、像底板等不影响外观的部位图1-1-3对于此类毛刺的方法为用手紧握刀柄、刀刃贴于产品边框(即毛刺根部)从上到下均匀用力移动刀柄,把毛刺处理干净。
2、对外观有一定影响但不影响装配的部位图2-1-4对于这种毛刺,我们一般的处理方法为:用手紧握刀柄、刀刃轻帖于产品边框从上到下或从左到右均匀用力移动刀柄把毛刺处理干净。
3、既影响装配又影响外观的部位图2-1-5对于处理这种毛刺大家一定要小心,因为这种处在与显像管配合面上的毛刺稍有处理不甚就会出现内框与显像管之间配合有较大的间隙,所以针对这种毛刺我们只能按如图方式,用浇口在有毛刺的内框上面,从前往后的擀。
4、另外对于小毛刺,可以用刀尖处理。
第二节银丝条纹(包括表面气泡和内部气孔)这是一种常见的毛病,是塑料在充模过程受到气体的干扰而出现在制件表面熔料流动方向的缺陷,气体成分包括水气、分解气以及空气,其中以水气和分解气为多见。
当这些气体在注射作用结束后,仍然滞留在制件表面,沿料流方向形成一连串在光照下闪烁的大大小小泡点,我们称之为“银丝”或“银纹”,当塑件表面出现“银丝”或“银纹”时,常见的处理工具为砂纸和刀片,标准处理方法为用把标准砂纸对折三次,然后沿折纹撕开如图所示:让砂纸蘸水砂银纹处,标准动作如图;直到银纹消失。
有的银丝较为严重,需要先用已磨好的刀片在银丝处刮,直到银丝消失,然后将砂纸裁成如图所示40*50毫米方块,蘸水后在待处理表面从左到右反复轻抹,直到待处理表面光滑平整。
第三节熔接痕图2-2-1熔接塑料在型腔中由于遇到嵌件,孔洞(包括栅格)流速不连贯的区域,充模料中断的区域而以多股形式汇合的,因不能完全熔合而产生的熔接逢,最常见还有,由于多浇口而造成的熔接痕,熔接痕熔接痕有些熔接痕极为微小,可不作处理,而有些熔接痕十分明显,严重影响成品外观质量,我们要对其处理,作为操作工对熔接痕的粗略判断方法为:用手指甲轻刮熔接痕处,如果感觉到熔接痕较深,那么要先用刀片刮,然后再用砂纸处理(如下图所示);如果熔接痕较浅只需用砂纸处理即可。
注塑缺陷的分析ppt
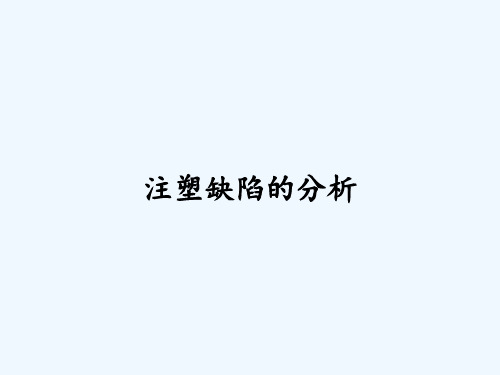
1、选择合理得浇口位置及 形式,将熔接线引导至不显
眼位置。
1、增加模温;2、加高熔体温度;3、优化注射速度 及注射压力。
六、湿气痕; 湿气痕由模壁上得冷凝水汽造成,就是顺着塑流得方向出现得灰白色喷射
线段,一些个案表现为表面气泡及粗糙。
故障件图片
成形原因:塑料粒子在存储或注塑过程中吸入了空气中得水分,当这种潮湿得 粒子在注塑熔化时,水分便变为水蒸气泡。由于熔料得模壁流动速度慢于中心 部位,这样这些水蒸气泡就被推向了塑件得表层,受压得气泡因为补偿压力而 爆破,随之被熔胶得流动波峰压至变形,并在模壁上固化。
度缺陷
1、选择合理得浇口位置(将熔接线放在不影响 产品处或将料流改为75°以上得汇流);2、模具 水路要合理,让有熔接线得模具对应处温度能调
得更高些;3、要有充分得排气。
1、加大保压;2、优化注射速度;3、增加熔胶温度 ;5、增加模具温度。
三、喷射纹; 喷射纹就是像蛇形般蜿蜒得粗糙得编织纹,出现在注塑件表面上, 极大得影响着零件得外观质量。 喷射纹一般均从浇口处开始,有时也可以从塑件得狭窄处开始。
1、选择合理得浇口大小及形式,需保证能 充分得补压;2、模具水路要合理,通过模 温得控制使其更好补压;3、要有充分得
排气。
1、料筒得储料行程就是否足够;2、保压及保压 时间就是否太小;3、注射速度就是否太小;4、增
加熔胶温度;5、增加模具温度。
二、熔接线; 熔接线一般均以线形方式显现。熔接线得出现会直接影响零件得 外观质量及零件强度。
得出现。
直接对着空腔得细小得浇 口最易形成喷射纹
优化后得浇口,料流通过上侧 壁模腔得阻挡,使前锋料与后 面得料流能很好得融合在一
注塑工艺及常见缺陷分析

模具扣位斜度不 夠
射膠壓力過高 注 塑 成 型 不 良
e.彎曲,翹曲
f.批峰
g.破裂
h.頂白
注塑工艺及常见缺陷分析
缩水
缩水(缩孔)+ 变形(翘曲) 变形
翘曲方向
现象:表面出现收缩凹印,容易出现在骨位柱子背面,胶 厚处,侧壁
原因:注塑射速射压低,保压小,料温低;产品肉厚不均; 模具排气不良,浇口太小;
改善对策:注塑提高射压射速,加大射胶量,提高保压及 保压时间;提高料筒温度;模具加大浇口,改善排气。
注塑工艺及常见缺陷分析
黑点
黑点(异色) +结合线(熔接痕、夹线) 结合线
现象:表面出现与产品颜色不同的点,常见的有黑点;容 易出现在白色产品
原因:注塑料筒温度偏高,背压偏高,螺杆转速偏快;原 料不洁;没有清干净炮筒;
现象:表面呈波纹状;一般出现浇口处
原因:注塑射速、射压、保压偏小,炮筒温度过低,模具 浇口太小;
改善对策:注塑提高射速射压、保压,提高炮筒温度,提 高模温;
注塑工艺及常见缺陷分析
蛇纹
蛇纹(冷料凹痕) +顶白(顶凸) 顶白
现象:表面呈蛇形纹理,通常出现在浇口位置
现象:表面有白色印记。一般是顶针的背面。
发生了何种缺陷?何时发生?频次如何?不良数/ 不良率是多少?
分析 Analysis
改善 Improve
相关因素有哪些?主要因素是什么?根本原 因是什么?必要时通过测量得出数据。
制定改进计划并实施.并将此种改善方法应用到类似 的产品上进行改善。
注塑工艺及常见缺陷分析
注塑件缺陷原因及对策
a.缺膠
b.縮水
对策:依限度区分无需加工与待加工;
注塑成型类产品常见不良分析案例

注塑成型不良的案例分析一、飞边(披锋)系指从模具分型面拼出熔融树脂的现象,在成形作业当中属于最恶劣的情况,特别是当飞边粘在模具面上,残留下来,直接锁模的话,则损伤模具分型面。
一旦出现这种情况,该损伤部分又会导致产生新的飞边,怎么也没办法,所以需特别注意不要出现飞边,1、不得施加过高的射出压力熔融粘度低的树脂,如尼龙、聚丙烯、聚乙烯、聚苯乙烯等,流动性好,往往从模具缝隙出现“边缘鼓出”现象,因此,不得施加过高的射出压力和保压压力。
当有出现飞边的倾向时,应尽早让保压转换用限位开关动作,减少计量。
降低射出压力。
另外,保压压力也有过高的时候,对于这些流动好的树脂,不要从一开始就施加高保压压力。
应边观察成形品的状况,边一点一点提高压力。
2、最初锁模力不足时,当然会产生飞边,不了解所用模具所需锁模力究竟有多大,就不可能作出断。
先利用锁模力调整手柄,增加锁模力试试看。
上图为在模具接触面(分型面)形成的飞边。
飞边主要是发生在分型面,但其它如在小顶杆周围、抽芯周围有时也出现飞边。
所谓纵向飞边,几乎均起因于模具精度不够。
象尼龙之类熔融粘度低的树脂,特别容易产生飞边,如聚碳酸酯之类粘度高的树脂则难于产生飞边。
以最大锁模力锁模,仍然出现飞边时,则应考虑是否是机械能力不足。
此时的判断方法是,当模腔内的压力乘以模腔、流道的投影面积所得的数值未超过机械是大锁模力的话,则不属于机械能力不足。
但需正确估计模腔内压力,然而不能把产品目录所列出的射出压力看作是模腔压力。
射出压力充其量是料筒内的理论压力,树脂流入模具,即被冷却,压力急剧下降。
平均压力从低粘度部件250kg/cm2到高粘度工业部件800kg/cm2左右,这种压力很难估计,虽然大体上有个基准,但要想保证估计精度,还需要凭经验。
3、在模具接触面产生了伤痕、夹有脏东西或是模具平行度差,当然会产生飞边,模具保管不善,则会使安装面打上伤痕,或是生锈,这样都会导致产生飞边。
所以应该养成习惯妥善保管模具。
图文解说最常见的11例注塑成型缺陷
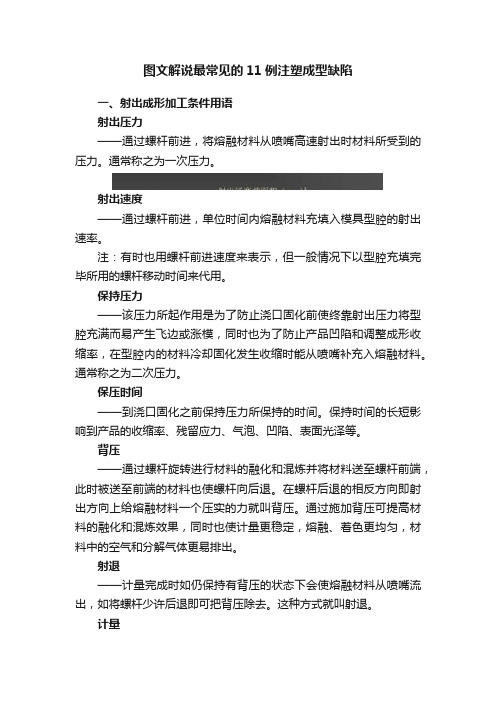
图文解说最常见的11例注塑成型缺陷一、射出成形加工条件用语射出压力——通过螺杆前进,将熔融材料从喷嘴高速射出时材料所受到的压力。
通常称之为一次压力。
射出速度——通过螺杆前进,单位时间内熔融材料充填入模具型腔的射出速率。
注:有时也用螺杆前进速度来表示,但一般情况下以型腔充填完毕所用的螺杆移动时间来代用。
保持压力——该压力所起作用是为了防止浇口固化前使终靠射出压力将型腔充满而易产生飞边或涨模,同时也为了防止产品凹陷和调整成形收缩率,在型腔内的材料冷却固化发生收缩时能从喷嘴补充入熔融材料。
通常称之为二次压力。
保压时间——到浇口固化之前保持压力所保持的时间。
保持时间的长短影响到产品的收缩率、残留应力、气泡、凹陷、表面光泽等。
背压——通过螺杆旋转进行材料的融化和混炼并将材料送至螺杆前端,此时被送至前端的材料也使螺杆向后退。
在螺杆后退的相反方向即射出方向上给熔融材料一个压实的力就叫背压。
通过施加背压可提高材料的融化和混炼效果,同时也使计量更稳定,熔融、着色更均匀,材料中的空气和分解气体更易排出。
射退——计量完成时如仍保持有背压的状态下会使熔融材料从喷嘴流出,如将螺杆少许后退即可把背压除去。
这种方式就叫射退。
计量——射出保压时螺杆前进把材料充满型腔并留有2~5mm的螺杆行程位置(残量)的储料设定量。
如果射出时螺杆位置押到零则会使型腔内的材料冷却固化发生收缩时不能从喷嘴补充入熔融材料而使保压不起作用。
螺杆回转数——单位时间内螺杆回转储料的转数。
螺杆回转的快慢影响到计量储料时间,计量应在冷却时间内完成,如超过冷却时间则要加快回转数。
保压切换——射出压力向保压切换时的时间(螺杆位置)对于成形条件是非常重要的。
通常以充入型腔材料的90~95%作为切换点。
二、射出成形不良原因和对策1. 充填不足--树脂未完全充满型腔使制品有缺损的现象。
[1] 成形品的体积过大i)要使用成形能力大的成形机。
ii)使用成形多腔模具时,关闭部分型腔。
常见注塑件缺陷及解决的方法
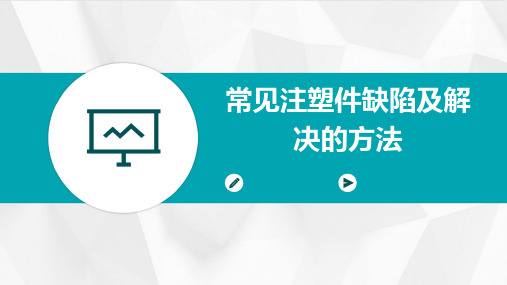
充填不足
01
总结词
充填不足是指注塑件在成型过程中未能完全填满 模具型腔,导致部分区域出现缺料或凹陷。
02
详细描述
充填不足通常是由于注射速度慢、注射压力不足、 模具温度过高或塑料流动性差等原因引起的。
缩痕
总结词
缩痕是指注塑件表面出现凹陷或收缩痕迹,影响 外观和尺寸精度。
详细描述
缩痕通常是由于塑料冷却过程中收缩率不均、模 具温度不均匀或注射压力不足等原因引起的。
常见注塑件缺陷及解 决的方法
目录
• 常见注塑件缺陷 • 注塑件缺陷原因分析 • 解决注塑件缺陷的方法 • 案例分析
01
常见注塑件缺陷
翘曲与扭曲
总结词
翘曲与扭曲是指注塑件形状发生扭曲或弯曲,不符合设 计要求。
详细描述
翘曲与扭曲通常是由于模具设计不合理、塑料收缩率差 异、注射温度和压力不适当等原因引起的。
环境条件的控制Байду номын сангаас
总结词
保持稳定的环境条件对注塑件的质量至关重 要,包括温度、湿度和清洁度等。
详细描述
确保注塑车间温度、湿度稳定,保持环境清 洁、无尘。定期对设备和环境进行清理和消 毒,防止污染和细菌滋生。同时,要关注天 气变化和季节性温差对注塑件质量的影响,
采取相应的措施进行调节。
04
案例分析
案例一:翘曲与扭曲缺陷的解决
材料选择与控制
总结词
选择合适的材料,控制材料质量是解决注塑件缺陷的重要步骤。
详细描述
根据产品使用要求和工艺特性,选择具有良好流动性和成型性的材料。同时, 要确保材料干燥、清洁,无杂质和污染。定期对材料进行质量检查,确保其性 能稳定。
模具优化与维护
精密注塑工艺与产品缺陷解决方案100例PPT模板课件

c
案例21 断 裂
f
案例24 通 水孔位披
锋
9
a
案例25 顶 针印明显
d
案 例 28 镜 片长度尺 寸偏大
2 案例分析
b
案例26 困 气烧焦
e
案 例 29 中 间孔位边 侧夹水线
c
案 例 27 表 面夹线及 内柱少胶
f
案例30 困 气调整困
难
10
2案例分 析
案例31 变形
案例36 进胶口气
纹圈
案例32 面壳底部 行位拉模
a
案例67 顶 白(二)
d
案例70 骨 位困气发
白
2 案例分析
b
案 例 68 侧 边多胶( 披锋)
e
案例71 水 口位气纹
(一)
c
案例69 表 面凹凸不
平
f
案例72 水 口位气纹
(二)
17
2案例分 析
01
案 例 7 3 进胶 点位气纹、
缺胶
04
案例76发 白(二)
02
案例74表 面拉高
05
案 例 7 7 电池 框水口位拖
05
案 例 9 5 内侧 拉伤(二)
03
案例93水 口拉胶粉
06
案例96表 面流纹
21
2案例分析
案例97变形 案例98两侧面顶出变形 案例99外观色差 案例100料流结合处容易断裂
22
感谢聆听
23
7
2案例分 析
01
案例13u形 位夹水线
04
案例16烧 焦
02
案例14困 气烧白
05
案例17内 行位易断
03
注塑缺陷原因和案例分析(培训教材)课件

44.8
0.9
89.6
1.3
156.8
1.8
291.2
3.0
448
4.3
627.2
5.8
828.8
7.5
注塑缺陷原因和案例分析(培训教材)课件
21
5.3.保压时间(Ti)=0.6D2+0.3D
Ti:保压时间(sec),D:产品最大厚度(mm)
产品最大厚度(mm)
保压时间(sec)
0.8
0.6
1.0
注塑缺陷原因和案例分析(培训教材)课件
16
应用举例: 有一种产品,是用PC材料生产的,其最大胶厚t
为2mm,成型温度Tm为270 ℃,所用模温Tw为120 ℃, 计算其冷却时间。
注塑缺陷原因和案例分析(培训教材)课件
17
计算:
从材料手册上可查到PC材料的热传导系数 a=0.105 mm2/sec, 热变形温度Ts =135℃;
0.9
1.5
1.8
2.0
3.0
3.0
6.3
4.0
10.8
6.0
23.4
注塑缺陷原因和案例分析(培训教材)课件
22
6)如何对模具进行有效冷却?
应根据产品结构、塑料种类、品质要求适当选择冷却方式, 不能所有模具都用常温水: 模温机:加玻纤(GF)、流动性差、尺寸精度要求高、薄壁胶件、 易弯曲变形、易应力开裂、外观要求高的产品;
1.3.使用玻纤、防火,或较脆的工程材料时,原则上选用 中低速、中低压;
1.4.以上1.1、 1.3.类容易粘模的产品,其注射时间应尽量 短。
注塑缺陷原因和案例分析(培训教材)课件
12
2)冷却时间长短的选择